
технология литейного производства
.pdf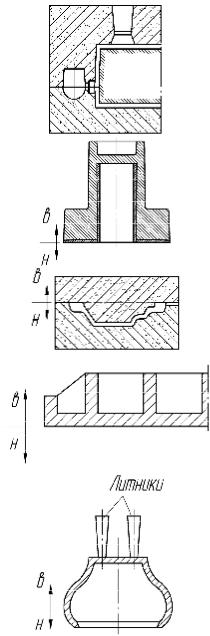
Таблица 47
Основные требования к выбору положения отливки в форме
Эскиз |
Основные требования |
1 |
2 |
|
При повышенной склонности сплавов к |
|
образованию усадочных раковин. Следует от- |
|
ливки располагать так, чтобы толстые части |
|
были сверху или с боку по разъему, что позво- |
|
ляет удобно устанавливать прибыли |
|
|
|
Наиболее ответственные части отливок |
|
следует располагать в нижней части формы или, |
|
в крайнем случае, вертикально, что уменьшает |
|
дефекты по неметаллическим включениям, уса- |
|
дочным и газовым раковинам |
|
|
|
При подводе металла по разъему формы |
|
горизонтальные тонкие стенки отливки следует |
|
располагать в нижней части формы, что обеспе- |
|
чивает лучшее заполнение формы и устраняет |
|
недолив и спай |
|
Массивные части отливок из серого чу- |
|
гуна следует располагать в нижней полуформе, |
|
а при формовки в одной полуформе – внизу; |
|
направленная кристаллизация для крупных от- |
|
ливок при этом обеспечивается применением |
|
металлических холодильников или смесей с по- |
|
вышенной теплопроводностью |
|
Основную часть отливок с малой и рав- |
|
номерной толщиной стенок (посудное литье, |
|
ванны) следует располагать в верхней части |
|
формы, обеспечивая тем самым хорошее ее за- |
|
полнение клиновыми щелевыми или дождевы- |
|
ми питателями, подводимыми в верхнюю часть |
|
отливки |
|
|
241
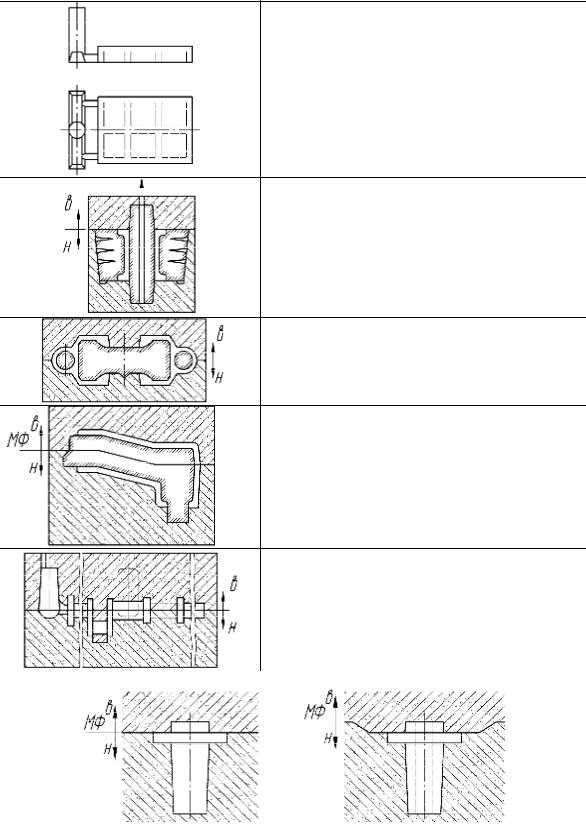
Отливку необходимо располагать так, чтобы обеспечить спокойное заполнение фор- мы, исключающее разрушение струей металла
отдельных участков формы и стержней
Для устранения образования газовых ра-
ковин отливки при заливке следует располагать так, чтобы был обеспечен преимущественно
верхний отвод газов из стержней
Отливку в форме следует располагать по возможности так, чтобы можно было объеди-
нить несколько стержней в один для двух или более отливок
При изготовлении форм под высоким давлением, особенно на автоматических лини- ях, а также для деталей, подвергающихся испы- танию на герметичность, отливки в форме сле- дует располагать так, чтобы обеспечить крепле- ние стержней без жеребеек, а закрепление уве- личенной нижней части знака – плоскостью
разъема верхней полуформы
Отливку в форме следует располагать так, чтобы общая высота формы была наи- меньшей, а полуформы имели примерно одина-
ковую высоту
Рис. 130. Пример выбора поверхности разъема формы
242
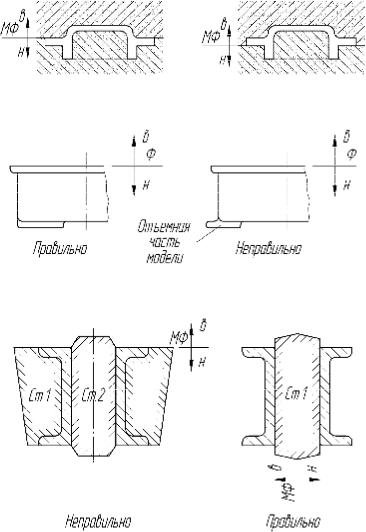
Основные поверхности детали располагать в одной желательно нижней, полуформе (рис. 131).
Число отъемных частей модели должно быть минимальным. При ма- шинной формовке отъемные части заменять стержнями или изменять конст- рукцию отливки (рис. 132).
Поверхность разъема должна обеспечить формовку с применением наименьшего количества стержней (рис. 133).
Рис. 131. Пример выбора поверхности разъема формы
Рис. 132. Конструкция отъемных частей модели
Рис. 133. Выбор поверхности разъема
Для предупреждения смещения верхней части отливки относительно нижней и утечки металла в разъем формы отливку следует, по возможности, располагать в нижней полуформе (рис. 134).
243
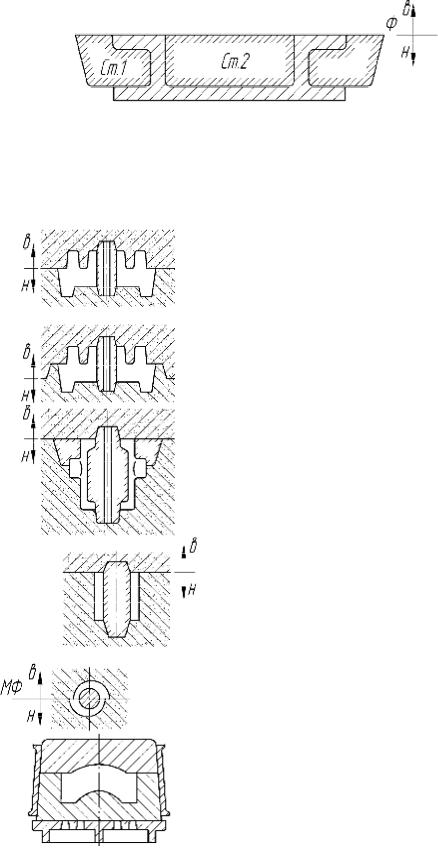
|
Рис. 134. Выбор поверхности разъема |
||
|
|
Таблица 48 |
|
Основные требования к выбору разъема формы |
|||
Эскиз |
|
Основные требования |
|
1 |
|
2 |
|
|
|
Число разъемов формы должно быть |
|
|
|
минимальным, а поверхности разъемов – |
|
|
|
плоскими; при фасонной поверхности разъе- |
|
|
|
ма его построение должно выполняться ли- |
|
|
|
ниями, имеющими определенную геометри- |
|
|
|
ческую форму, что упрощает процесс изго- |
|
|
|
товления, доводки и контроля модельных |
|
|
|
плит |
|
|
|
|
|
|
|
Число отъемных частей должно быть |
|
|
|
минимальным; при массовом и серийном |
|
|
|
производстве, если нельзя изменить конст- |
|
|
|
рукцию отливки, их следует заменять стерж- |
|
|
|
нями |
|
|
|
|
|
|
|
Разъем формы должен обеспечить |
|
|
|
наименьшее количество дефектов по переко- |
|
|
|
сам, а также минимальную протяженность |
|
|
|
литейных швов по поверхностям отливок и |
|
|
|
соответственно заливов; если же заливов не |
|
|
|
избежать, то обработка их не должна вызы- |
|
|
|
вать затруднений; на базовых поверхностях |
|
|
|
отливок литейные швы и заусенцы не допус- |
|
|
|
каются |
|
|
|
|
|
|
|
При безопочной формовке в нижней |
|
|
|
части полуформы; в этом в случае съем верх- |
|
|
|
ней формы и нижней, находящейся под воз- |
|
|
|
действием вибратора, не вызывает затрудне- |
|
|
|
ний |
|
|
|
|
|
244
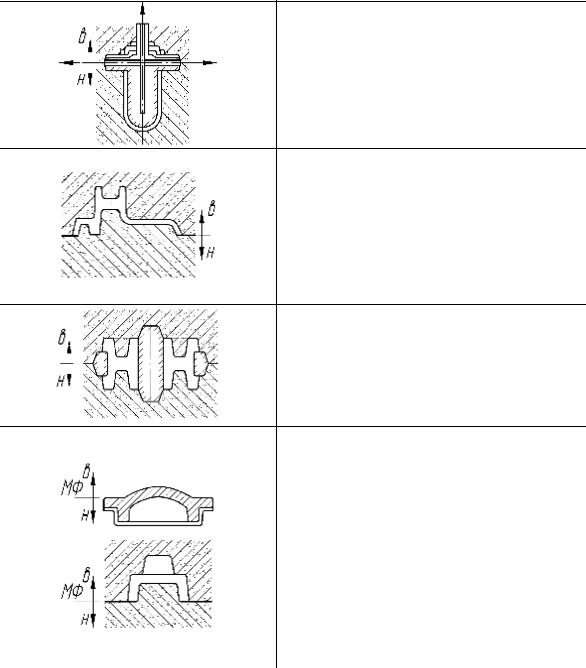
Разъем формы должен быть таким,
чтобы обеспечить удобный вывод газов из всех стержней, болванов и углубленных (при почвенной формовке) участков формы
Количество стержней должно быть минимальным; по возможности – стержни следует заменять болванами, особенно на ав- томатических линиях формовки, или не-
сколько отдельных стержней заменять одним общим; в единичном производстве для воз- можности замены стержней болванами сле-
дует применять парные модельные плиты по типу машинной формовки
Разъем формы должен быть таким, чтобы все или основные стержни устанавли-
вались в нижней полуформе и обеспечивали тем самым максимально удобнее процессы сборки формы, ее отделки, окраски и просу- шивания, а также контроль установки стерж-
ней
Базовые поверхности отливок долины быть расположены в одной полуформе с об- рабатываемыми поверхностями, а. также с фланцами и приливами, связанными с базо- выми жесткими размерами; части детали, не
допускающие относительного взаимного смещения, должны также располагаться в од- ной полуформе, если же разъем формы не допускает их расположения в одной полу- форме, то ответственные поверхности долж-
ны занимать в форме строго определенное положение по отношению к базовым, что достигается применением специальной осна-
стки и средств контроля
Выбор вида формовки. Под видом формовки подразумевается состоя- ние литейной формы, в котором она допускается к сборке и заливке метал- лом. Различают два вида формовки: «по-сырому» и «по-сухому».
Формы, прошедшие тепловую сушку, независимо от глубины просу- шенного слоя, считаются изготовленными «по-сухому».
Методом формовки «по-сухому» рекомендуется изготовлять крупные и толстостенные отливки, а также отливки, к качеству которых предъявляются повышенные требования.
Формы из песчано-глинистых смесей, не прошедшие тепловую сушку,
245
и формы из жидкоподвижных смесей и смесей на жидком стекле, подвергае- мые провяливанию или химическому твердению, считаются изготовленными «по-сырому».
При формовке «по-сырому» сокращается цикл изготовления форм, уве- личивается оборачиваемость опок, сокращаются грузопотоки. Все это увели- чивает производительность труда и снижает себестоимость литья. Однако, формовка «по-сырому» имеет ряд существенных недостатков, которые необ- ходимо учитывать при назначении вида формовки:
-следует избегать изготовления форм «по-сырому», где металлостати- ческое давление и динамический напор достигают значительных величин. Это может вызвать деформацию и разрушение сырых форм и повлечет за со- бой раздутие форм и песчаные включения;
-в сырую форму нежелательно устанавливать холодильники, так как на их поверхности конденсируется влага, что приведет к образованию в отливке газовых раковин. При применении холодильников в сырых формах, послед- ние должны заливаться не более чем через 3-4 часа после сборки;
-следует избегать изготовления крупных форм «по-сырому», так как по
условиям формовки и сборки они простаивают длительное время до момента сборки и заливки форм.
-при продолжительном времени заливки сырой формы на поверхности отливки могут образовываться плены, ужимины и другие дефекты;
-выступающие части форм при формовке «по-сырому», ввиду малой их прочности, могут быть разрушены потоком металла.
Контрольные вопросы.
1.Какие принципы лежат в основе выбора оптимального положения от- ливки в форме?
2.Сформулируйте условия обеспечения направленного затвердевания.
3.Назовите принципы, на основании которых выбирается положение полости разъема модели и формы.
4.Назовите этапы конструирования литых деталей.
5.Каким должен быть разъем формы при машинной формовке?
6.Что такое вид формовки?
7.Чем отличается формовка по-сухому от формовки по-сырому?
8.Как следует располагать в форме отливку, чтобы предупредить сме- щение верхней части отливки?
9.Как следует располагать в форме наиболее ответственные поверхно- сти?
10.Как обеспечить надежность крепления стержней при сборке форм и возможность проверки правильности их установки?
246

ЛЕКЦИЯ 23.
ТЕМА: ПОЛУЧЕНИЕ ОТЛИВОК, ТРЕБУЕМЫХ РАЗМЕРОВ И ФОРМ
План лекции
1.Определение припусков на усадку, механическую обработку.
2.Формовочные уклоны, технологические пополнения.
Определение величины усадки отливок. Усадкой называется уменьше-
ние объема металла при охлаждении. Изменение линейных размеров отливки, вызванное усадкой, называется линейной усадкой. Величина усадки зависит от марки сплава, конфигурации отливки, ее размеров, формовочных материа- лов, вида формовки, температуры металла при заливке формы и других фак- торов. Наибольшую усадку имеют отливки простой конфигурации, так как нет препятствий усадке. В отливках, имеющих стенки разной толщины, усад- ка получается неравномерной из-за неодновременного затвердевания и осты- вания. Более толстые части затвердевают позднее, чем тонкие. Отливки с большим числом стержней также не имеют равномерной усадки, так как стержни препятствуют свободной усадке. Наличие большого количества пе-
ременных факторов затрудняет точное определение величины линейной усадки отливок. Для уточнения фактической величины усадки необходимо
проводить многочисленные замеры готовых отливок и их сопоставление с размерами модели.
Величина линейной усадки εл может быть определена по формуле
εл = lмодl − lотл ×100% ,
отл
где lмод – размер модели, мм; lотл – размер отливки по чертежу, мм.
Отливка соответствует размерам чертежа в тех случаях, когда при изго- товлении модели правильно учитывается линейная усадка металла. На осно- вании анализа многочисленных замеров рекомендуется пользоваться данны- ми табл. 49.
Определение припусков на механическую обработку. Припуском на ме-
ханическую обработку называется слой металла, предусмотренный для сня- тия в процессе механической обработки. Величина припусков зависит от ма- териала литой детали, характера производства, положения обрабатываемой поверхности в форме (при заливке). Припуски устанавливаются в зависимо- сти от класса точности отливки.
Точность отливки – степень приближения размеров, формы, располо- жения элементов и параметров качества и поверхностей отливки к соответст- вующим заданным параметрам детали.
247
Точность отливки определяется значениями допусков на ее размеры, коробления, смещения по плоскости разъема, массы и припусков на механи- ческую обработку ее поверхностей.
|
|
Таблица 49 |
|
Группа отливок |
Усадка, % |
|
|
|
затрудненная |
свободная |
|
Серый чугун |
|
|
|
Мелкие и средние отливки |
0,9 |
1,0 |
|
Средние и крупные отливки |
0,8 |
0,9 |
|
Очень крупные отливки |
0,7 |
0,8 |
|
Специальные цилиндрические отливки: |
|
|
|
по длине |
0,8 |
0,9 |
|
по диаметру |
0,5 |
0,7 |
|
Стальное литье |
|
|
|
Отливки из углеродистых и низколегированных |
1,3-1,7 |
1,6-2,0 |
|
конструкционных сталей |
|
||
|
|
|
|
Отливки из высоколегированных хромистых сталей |
1,0-1,4 |
1,3-1,7 |
|
Отливки из феррито-аустенитных сталей |
1,5-1,9 |
1,8-2,2 |
|
Отливки из чисто-аустенитных сталей |
1,7-2,0 |
2,0-2,3 |
|
Цветное литье |
|
|
|
Оловянные бронзы |
1,2 |
1,4 |
|
Безоловянные бронзы |
1,6-1,8 |
2,0-2,2 |
|
Латуни цинковые |
1,5-1,7 |
1,8-2,0 |
|
Латуни кремнистые |
1,6-1,7 |
1,7-1,8 |
|
Латуни марганцовые |
1,8-2,0 |
2,0-2,3 |
|
Силумин |
0,8-1,0 |
1,0-1,2 |
|
Сплав алюминия с медью |
1,4 |
1,6 |
|
Классы точности размеров отливок – характеристика точности изго-
товления отливок, определяемая значениями допусков в мм (ГОСТ 26645-85). Установлено 16 классов точности и шесть дополнительных с индексами «Т» для номинальных размеров до 10000 мм.
В ГОСТе 26645-85 классы точности указаны для размеров элементов отливки образованной двумя полуформами и расположенной перпендикуляр- но к плоскости разъема. Допуски размеров элементов отливки, образованной одной частью формы или одним стержнем, устанавливают на один два класса выше приведенных в ГОСТе 26645-85, образованной тремя и более частями формы, несколькими стержнями, а также на толщины стенок, ребер и флан- цев – на 1-2 класса ниже. ГОСТ 26645-85 предусматривает предельные от- клонения, смещения от номинального положения элементов отливки на плос- кости разъема.
Допуск размера отливки (допускаемые отклонения) – разность между
наибольшим и наименьшим значениями размера отливки или между верхним и нижним предельным отклонениями.
При конструировании отливок на чертежах показывают допускаемые
248
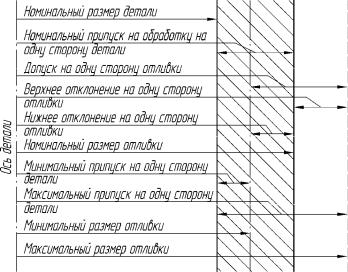
отклонения (допуски на размер).
Величина допуска на размеры отливок включает обычно погрешности по всем признакам, кроме погрешностей по точности взаимного расположе- ния поверхностей. Последние оговариваются на чертежах особо.
Правильное назначение величины допусков имеет большое значение с точки зрения экономики и организации производства. Отливку с большими допусками проще изготовить, но увеличение допусков приводит к большему расходу металла и в конечном итоге повышению себестоимости отливки. На рис. 135 показаны графическое объяснение припусков и допусков и их взаи- мосвязь.
Рис. 135.
Под номинальным размером отливки подразумевается основной рас- четный размер, который задается чертежом. Размер, получаемый непосредст- венным измерением, называется действительным размером. Действительный размер ограничивается предельными размерами – наибольшим или наимень- шим. Допуск, или отклонение, является разностью между номинальным и ка- ким-либо из предельных размеров. При этом различают верхние и нижние (отклонения в плюс и в минус).
Величина припусков зависит от наибольшего габаритного и номиналь- ного размеров отливки. Для установления припусков на механическую обра-
ботку под номинальным размером понимается наибольшее расстояние между противоположными обрабатываемыми поверхностями или расстояние от ба- зисной поверхности или оси до обрабатываемой поверхности (рис. 136).
Припуски на механическую обработку отливок устанавливаются по ГОСТ 26645-85 в соответствии с классами точности их изготовления:
I класс – для отливок массового производства;
II класс – для отливок серийного производства;
249

III класс – для отливок индивидуального производства.
Припуски, компенсирующие коробление, сглаживающие местные уг- лубления и выступы, а также напуски, создающие направленное затвердева- ние металла, устанавливаются технологом-литейщиком при разработке тех- нологии.
Рис. 136. Примеры определения номинального размера отливок
Для оценки точности с некоторыми приближениями можно применять квалитеты, приведенные в табл. 50.
Таблица 50
Допуски размеров отливок
Интервалы |
|
|
|
|
Обозначение |
|
|
|
||
номиналь- |
|
|
|
|
|
|
|
|
|
|
ных разме- |
IT11 |
IT12 |
IT13 |
IT14 |
IT15 |
IT16 |
IT17 |
IT18 |
IT19 |
IT20 |
ров, мм |
|
|
|
|
|
|
|
|
|
|
до 6 |
0,075 |
0,120 |
0,180 |
0,300 |
0,480 |
0,750 |
1,200 |
1,800 |
3,000 |
4,800 |
6-10 |
0,090 |
0,150 |
0,220 |
0,360 |
0,580 |
0,900 |
1,500 |
2,200 |
3,600 |
5,800 |
10-18 |
0,110 |
0,180 |
0,270 |
0,430 |
0,700 |
1,100 |
1,800 |
2,700 |
4,300 |
7,000 |
18-30 |
0,130 |
0,210 |
0,330 |
0,520 |
0,840 |
1,300 |
2,100 |
3,300 |
5,200 |
8,400 |
30-50 |
0,160 |
0,250 |
0,390 |
0,620 |
1,00 |
1,600 |
2,500 |
3,900 |
6,200 |
10,000 |
50-80 |
0,190 |
0,300 |
0,460 |
0,740 |
1,200 |
1,900 |
3,000 |
4,600 |
7,400 |
12,000 |
80-120 |
0,220 |
0,350 |
0,540 |
0,870 |
1,400 |
2,200 |
3,500 |
5,400 |
8,700 |
14,000 |
120-180 |
0,250 |
0,400 |
0,630 |
1,000 |
1,600 |
2,500 |
4,000 |
6,300 |
10,000 |
16,000 |
180-250 |
0,290 |
0,460 |
0,720 |
1,150 |
1,850 |
2,900 |
4,600 |
7,200 |
11,500 |
18,500 |
250-315 |
0,320 |
0,520 |
0,810 |
1,300 |
2,100 |
3,200 |
5,200 |
8,100 |
13,000 |
21,000 |
315-400 |
0,360 |
0,570 |
0,890 |
1,400 |
2,300 |
3,600 |
5,700 |
8,900 |
14,000 |
23,000 |
400-500 |
0,400 |
0,630 |
0,970 |
1,550 |
2,500 |
4,000 |
6,300 |
9,700 |
15,500 |
25,000 |
500-630 |
0,440 |
0,700 |
1,100 |
1,750 |
2,800 |
4,400 |
7,000 |
11,000 |
17,500 |
28,000 |
630-800 |
0,500 |
0,800 |
1,250 |
2,000 |
3,200 |
5,000 |
8,000 |
12,500 |
20,000 |
32,000 |
800-1000 |
0,560 |
0,900 |
1,400 |
2,300 |
3,600 |
5,600 |
9,000 |
14,000 |
23,000 |
36,000 |
1000-1250 |
0,660 |
1,050 |
1,650 |
2,600 |
4,200 |
6,600 |
10,500 |
16,500 |
26,000 |
42,000 |
1250-1600 |
0,780 |
1,250 |
1,950 |
3,100 |
5,000 |
7,800 |
12,500 |
19,500 |
31,000 |
- |
1600-2000 |
0,920 |
1,500 |
2,300 |
3,700 |
6,000 |
9,200 |
15,000 |
23,000 |
- |
- |
2000-2500 |
1,100 |
1,750 |
2,800 |
4,400 |
7,000 |
11,000 |
17,500 |
- |
- |
- |
2500-3150 |
1,350 |
2,100 |
3,300 |
5,400 |
8,600 |
13,500 |
- |
- |
- |
- |
Ориентировочные данные о требуемой точности размеров отливок в за- висимости от эксплуатационного назначения деталей приведены в табл. 51.
250