
технология литейного производства
.pdf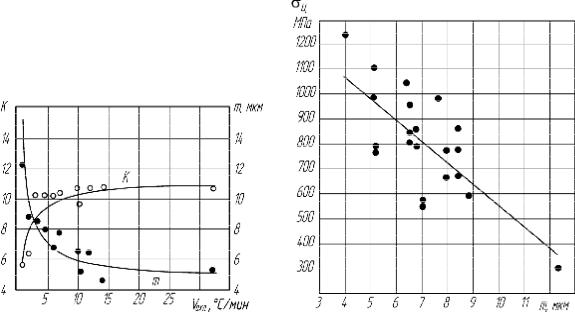
формы через 5-6 ч после заливки, и при этом трещины отсутствовали. Тонко- стенные отливки рабочих колес насосов 10УВЛХ2М диаметром 650 мм (мас- са 150 кг) необходимо выдерживать в форме не менее 12 ч; выбивка этих от- ливок через 6 ч после заливки привела к образованию холодных трещин на дисках колес. Крупные и сложные рабочие колеса насосов 20ГР-8 и 20Р-11 выдерживают в форме около 72 ч. Отливки типа бронеплит мельниц следует выдерживать в форме 8-24 ч, в зависимости от толщины и массы отливки.
Рис. 208. Износостойкость К и величина |
Рис. 209. Влияние величины карбидов m |
карбидов m чугуна ИЧХ12М в зависимости |
на прочность чугуна ИЧХ12М |
от скорости охлаждения при кристаллиза- |
|
ции |
|
Особенности литья деталей из высокопрочного чугуна в песчаные формы. Основными вопросами, которые приходится решать при литье дета- лей в песчаные формы являются: выбор и приготовление исходных формо- вочных материалов, приготовление формовочных и стержневых смесей, изго- товление форм и стержней, заливка форм, остывание отливок в формах и уда- ление прибылей литников от отливок.
При литье деталей из высокопрочного чугуна применяются те же ис- ходные формовочные материалы, а также формовочные и стержневые смеси, что и при литье из серого чугуна. Процесс изготовления форм и стержней, предназначенных для чугуна с шаровидным графитом, также не отличается от процесса изготовления форм и стержней для отливок из чугуна с пластин- чатым графитом.
Исключительно большое значение при производстве отливок из чугуна с шаровидным графитом имеют вопросы разливки металла в формы после
341
обработки чугуна магнием. Дело в том, что при выдержке чугуна после обра-
ботки его магнием в жидком состоянии происходит непрерывное испарение магния и чем длительнее выдержка, тем больше теряется магния непроизво- дительно. При очень длительной выдержке чугуна в ковше остаточное со- держание магния, может уменьшиться настолько, что вместо шаровидного графита образуется графит пластинчатой формы, и чугун в этом случае будет иметь низкие механические свойства. Длительная выдержка чугуна после об- работки его магнием приводит к понижению температуры чугуна, что связано с понижением жидкотекучести чугуна и с образованием значительного коли- чества усадочных раковин, спаев и других литейных дефектов.
Исходя из этого, необходимо по возможности сокращать время вы- держки чугуна в ковше после ввода магния. Точно так же должно быть ми- нимальным время заливки литейной формы, во избежание повышенного окисления металла, что связано с возможностью попадания окисных плен в отливку.
Процесс разливки чугуна зависит от способа обработки чугуна магни- ем. При обработке чугуна магнием в открытых ковшах разливка чугуна про- изводится из тех же ковшей, в которых производилась обработка его магни- ем. При обработке чугуна магнием в копильниках вагранок разливка чугуна производится либо мелкими ковшами, наполняемыми из вагранки, либо из ковшей большой емкости, равной емкости копильника. Разливка чугуна после
обработки его магнием в герметизированных ковшах или автоклавах может производиться непосредственно из тех же ковшей, в которых производилась обработка чугуна магнием. При необходимости доливки чугуна с целью его разбавления чугун переливается в ковш большей емкости, в него добавляется чугун из вагранки и после этого производится заливка форм.
Практика работы с герметизированными ковшами показала, что при вводе 0,7 % магния в чугун последний можно вдвое разбавить и при этом ос- таточное содержание магния в отливках составляет 0,04-0,05 %.
При отливке крупных деталей с большими прибылями после заливки форм рекомендуется производить доливку прибылей горячим металлом. При невозможности доливки металла в прибыли открытые поверхности послед- них присыпаются сухим песком или экзотермической смесью.
Охлаждение отливок в формах, залитых чугуном, обработанным магни- ем, должно производиться медленно. Температура по всему сечению отливки выравнится и не будет возникать остаточных литейных напряжений. Прежде- временная выбивка отливок может привести к короблению их, а при неблаго- приятных условиях даже к полному разрушению.
При выбивке отливок из форм следует учитывать, что в отливках из чу- гуна с шаровидным графитом возникают повышенные напряжения, и при не-
осторожной выбивке тонкостенных отливок могут образоваться в отливках трещины. Вследствие того, что чугун с шаровидным графитом имеет боль- шую прочность и значительное удлинение в литом состоянии, не рекоменду-
342
ется отбивать прибыли и литниковую систему молотком, так как даже при достаточно тонких сечениях литников они отламываются вместе с частью от- ливки. Поэтому, прежде чем удалять прибыли и литниковую систему, необ- ходимо сделать надрез на них зубилом или фасонным отрезным кругом. В крупных отливках прибыли лучше всего отрезать автогеном, как это делается на стальных отливках.
В большинстве случаев прибыли удаляются до термической обработки отливок огневой резкой, которую производят в несколько приемов с переры- вами, чтобы не допускать перегрева металла и возникновения напряжений. Исключение составляют некоторые детали сложной конфигурации, склонные к образованию трещин при огневой резке. Такие детали подвергаются терми- ческой обработке вместе с прибылями.
Благодаря предварительной обрезке литников и прибылей детали мож- но укладывать в печь плотно, без больших зазоров, а, следовательно, можно в значительной степени предотвратить коробление отливок в процессе терми- ческой обработки.
При обрезке прибылей оставляют припуски на механическую обработ- ку до 12 мм, которые удаляют после термической обработки механическим путем.
Обрезку прибылей у крупных отливок, не подвергающихся тер- мической обработке, а также заварку литейных дефектов производят после предварительного отпуска по следующему режиму: загрузка деталей в печь, предварительно нагретую до 350 °С; нагрев до 550 °С со скоростью 50 °С в час; выдержка при этой температуре в течение 8-10 ч, охлаждение до 350 °С со скоростью 50 °С в час с дальнейшим охлаждением на воздухе.
Вследствие того что в отливках из чугуна с шаровидным графитом воз- никают повышенные напряжения, все отливки, за исключением отливок с равномерными толщинами стенок и простой конфигурацией, подвергаются термической обработке для снятия напряжений.
Особенности литейной формы для алюминиевых сплавов. Алюминие-
вые сплавы можно заливать в сырые, сухие и металлические формы.
Многие алюминиевые сплавы обладают склонностью к образованию га- зовой и усадочной пористости в отливках. Поэтому при выборе состава фор- мовочных и стержневых смесей следует обращать особое внимание на их га- зотворную способность.
Для отливок из алюминиевых сплавов применяют мелкозернистые пес- ки с добавкой глинистых песков вместо глины. Стержневые смеси должны обладать большой податливостью, а крепители выгорать при сравнительно низкой температуре. При изготовлении отливок в песчаных формах для уве- личения скорости охлаждения сплава и получения отливки с меньшей порис- тостью в большинстве случаев применяется формовка по сырому.
При заливке в форму алюминиевые сплавы окисляются, и окисные пленки могут захватываться струей жидкого металла и попадать в отливку.
343
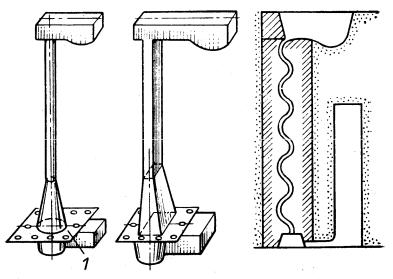
Поэтому литниковые системы для алюминиевых сплавов должны конструи- роваться так, чтобы движение расплава при заливке в форму было по воз- можности плавным, без завихрений. Это достигается уменьшением скорости движения металла от чаши к полости формы. Для этого делают незаполнен- ные ситниковые системы с сечениями элементов, постепенно расширяющи-
мися от стояка к питателю: Fпит : Fшл : Fст = 1 : 2 : 4.
Для обеспечения плавного поступления расплава в форму и исключения попадания окислов и шлака в отливку устанавливают металлические фильт- ровальные сетки. Чаще всего применяют обычный цилиндрический или призматический стояк, а при большой высоте для ослабления ударного дей- ствия струи металла делают ступенчатую литниковую систему и зигзагооб- разные (змеевидные) стояки (рис. 210).
а |
б |
в |
Рис. 210. Типы стояков:
а– цилиндрический; б – призматический,
в– зигзагообразный; 1 – сетка; 2 – металлоприемник
Контрольные вопросы.
1.Каким требованиям должны отвечать формы для стальных отливок?
2.Укажите предел влажности при формовке по-сырому, установленно- го для стального литья?
3.Для чего в стальных отливках в подприбыльной части устанавливают холодильники?
4.Почему для отливок из ковкого чугуна при расчете литниковой сис- темы скорость заливки принимается меньшей, чем для серого чугу- на?
5.Для чего в отливках из ковкого чугуна стержни изготавливаются из
344
более податливой смеси?
6.Какие особенности алюминиевых сплавов учитывают при конструи- ровании литниковых систем?
7.Для каких целей при заливке алюминиевых сплавов применяют фильтровальные сетки?
8.Для чего литниковая система для отливок из алюминиевых сплавов принимается с соотношением Fпит : Fшл : Fст = 1 : 2 : 4?
9.Что надо иметь в виду при выбивке отливок из высокопрочного чу- гуна?
10.Чем объяснить склонность белых чугунов к образованию холодных трещин?
ЛЕКЦИЯ 33.
ТЕМА: ТЕХНОЛОГИЯ И ОСНОВНЫЕ ПРИНЦИПЫ СПЕЦИАЛЬНЫХ СПОСОБОВ ЛИТЬЯ
План лекции
1.Сущность способов литья и области их применения.
2.Литье в постоянные формы: кокиль, под давлением, центробежное.
3.Литье в разовые формы: оболочковые, по выплавляемым моделям.
Повышенные требования к качеству выпускаемых машин, стремление к облегчению конструкций с целью экономии металла за последние годы за- метно изменили вид отливок: вместо простых по конфигурации, толстостен- ных заготовок производят сложные тонкостенные, более легкие отливки, прочность которых обеспечивает коробчатое сечение, ребра жесткости и дру- гие конструктивные элементы. Изготовление отливок в разовых песчано-
глинистых формах при машинной и особенно при ручной формовке имеет ряд существенных недостатков: невысокая точность и недостаточная чистота поверхности отливок; необходимость оставлять значительные припуски на механическую обработку; образование крупнозернистой литой структуры и др. Повышение точности и чистоты поверхности отливок достигают, исполь- зуя специальные методы литья, к которым относят: кокильное, под давлени- ем, под низким давлением, по выплавляемым (выжигаемым) моделям, в обо- лочковые формы, центробежное, электрошлаковое и некоторые другие, здесь не рассматриваемые методы получения отливок (вакуумным всасыванием, выжиманием, жидкой штамповкой).
Изготовление отливок в металлических формах.
Сущность метода и область применения. Сущность заключается в том,
что вместо разовой песчано-глинистой используют металлическую форму, называемую кокилем (рис. 211). Обладая по сравнению с песчано-
345
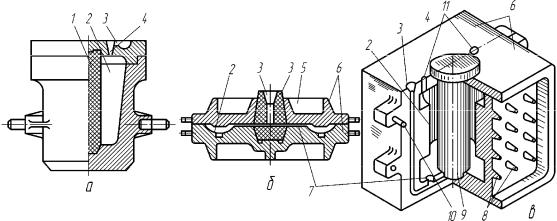
глинистыми формами приблизительно в 60 раз более высокой теплопровод- ностью, кокили обеспечивают мелкозерниструю структуру отливок, что по- вышает их прочность. При кокильном литье отпадает необходимость в мо- дельно-опочной оснастке, в формовочных и стержневых смесях, что не толь- ко дает большую экономию, но и снижает количество пыли и улучшает сани- тарные условия труда; повышается точность и чистота поверхности отливки; обслуживание кокилей не требует рабочих высокой квалификации; значи- тельно повышается производительность и уменьшаются необходимые произ- водственные площади. Технологический процесс кокильного литья можно легко механизировать. Механизированные кокили имеют устройство, позво-
ляющее закрывать и раскрывать их от пневматического или гидравлического привода. При массовом производстве несколько кокильных машин устанав- ливают на вращающиеся карусели, поворачивающиеся на необходимый угол через определенное время, за которое производится заливка кокиля.
Рис. 211. Металлические формы (кокили)
Наряду с преимуществами у кокильного литья есть и недостатки: высо- кая стоимость кокилей позволяет использовать их только в серийном и мас- совом производствах; опасность образования трещин в отливках из-за непо- датливости металлического кокиля; чугунные отливки в кокиле получают от- беленными и требуют длительного отжига, что удорожает их производство.
Кокильное литье применяют в условиях крупносерийного и массового производств при изготовлении несложных по конфигурации отливок с тол- щиной стенок от 3 до 100 мм из чугуна, стали и цветных металлов.
Конструкция кокиля. По конструкции кокили различают неразъемные вытряхные (рис. 211, а) и разъемные с горизонтальным (рис. 211, б) и верти- кальным (рис. 211, в) разъемами. Разъемные кокили (б, в) состоят из двух по- ловин 6, центрирующихся направляющими штырями 10. Чтобы избежать ко- робления, кокиль снабжают ребрами жесткости 6 (б) либо делают коробчатой формы (в). На наружной стенке кокиля для его ускоренного охлаждения ино-
346
гда отливают пальцы 8 (в). Отверстие или внутреннюю полость в отливке об- разует песчаный стержень 1 (а) либо металлический – 9 (в). Металл заливают в литниковую чашу 3, и по стояку 4 и питателям 7 он заполняет полость фор- мы 2. Так как металлические стержни неподатливы, то во избежание образо- вания в отливке трещин их удаляют из формы до начала усадки металла. Если внутренняя конфигурация отливки очень сложна, то металлические стержни делают из нескольких частей или заменяют песчаными. Литниковая система размещается в плоскости разъема кокиля. Для выхода воздуха из формы во время ее заливки, кроме выпоров 11 (в), в плоскости разъема по всей высоте кокиля прорезают щели глубиной 0,3-0,5 мм (на рисунке не показаны).
Изготавливают кокили из серого чугуна, стали, а также из цветных сплавов литьем с последующей механической обработкой.
Особенности технологии изготовления отливок в кокилях. Изго-
товление отливок в кокиле состоит из таких операций: очистка кокиля от ста- рой облицовки; нанесение огнеупорного защитного покрытия или покраска рабочей поверхности кокиля; сборка формы с установкой стержней; заливка кокиля; выдержка отливки в форме; раскрытие кокиля и удаление из него от- ливки.
Во избежание отбеливания чугунных отливок подбирают химический состав чугуна, обеспечивающий графитизацию в условиях повышенной ско- рости охлаждения. С этой же целью перед заливкой чугуна кокиль нагревают до 250-300 °С и время выдержки отливок в кокиле сокращают до минимума.
Если в кокиле получают отливки из силумина (сплав алюминия с крем- нием), то отпадает необходимость вводить натрий в сплав перед заливкой формы для измельчения структуры, так как быстрое охлаждение измельчает кремний в образующейся эвтектике.
При получении в кокиле отливок из сплавов на медной основе полость формы покрывают жирными красками. Между расплавом и кокилем образу- ется газовая прослойка, которая устраняет образование пригара на поверхно- сти отливки.
Изготовление отливок литьем под давлением.
Сущность метода и область применения. Сущность состоит в том, что жидким металлом принудительно заполняют металлическую пресс-форму под давлением, которое поддерживают до полной кристаллизации отливки. Давление обеспечивает быстрое и хорошее заполнение формы, высокую точ- ность и малую шероховатость поверхности отливки. Принудительное пита- ние отливки жидким металлом исключает, возможность образования усадоч- ных раковин, пористости и не требует установки прибылей. Ускоренная кри- сталлизация металла в металлической пресс-форме под давлением обуслов- ливает образование мелкозернистой структуры. Благодаря внешнему давле- нию растворенные в металле газы остаются в твердом растворе, что снижает газовую пористость металла. Отливки, полученные этим методом, как прави- ло, не имеют припусков на механическую обработку и после удаления из
347
формы являются готовыми деталями. Литьем под давлением можно получать отливки с толщиной стенки до 0,5 мм, сложной конфигурации и с отверстия- ми диаметром до 1 мм.
Высокая стоимость пресс-форм, имеющих сложную конфигурацию и требующих высокой точности изготовления, обусловливает целесообразность применения литья под давлением только в крупносерийном и массовом про-
изводствах тонкостенных отливок достаточно сложной конфигурации из сплавов цветных металлов массой до 50 кг.
Оборудование и технология литья под давлением. Литье под давлением осуществляют на компрессорных и поршневых машинах высокой производи- тельности, дающих 200-460 отливок в час. Поршневые машины (рис. 212) выпускают с горячей или холодной камерой сжатия, расположенной горизон- тально или вертикально. Машины с горячей камерой сжатия, в которых каме- ра находится непосредственно в расплаве, применяют для получения отливок из сплавов с низкой температурой плавления на основе цинка, олова и свин- ца. Машины с холодной камерой сжатия, в которых камера вынесена за пре- делы расплава, используют для получения отливок из более тугоплавких цветных сплавов на основе меди, алюминия и магния.
На машинах с вертикальной холодной камерой сжатия (рис. 212, а) рас- плав 4 заливают в камеру сжатия 5 (положение I). Верхний поршень 1, опус- каясь, давит на расплав и на нижний поршень 10, который при движении вниз открывает литниковый канал 3. Металл заполняет полость 2 пресс-формы, состоящей из двух половин 6 и 7 (положение II). Объем жидкого металла должен быть больше объема полости формы, чтобы между верхним и ниж- ним поршнем оставался избыток металла. Давление верхнего поршня под- держивают до полной кристаллизации отливки, после чего пресс-форму рас- крывают и отливку 9 вместе с литником 12 выталкивают из формы толкате- лями 5. Нижний поршень выталкивает наружу избыток металла 11 (положе- ние III) и его отправляют в переплав.
На рис. 212, б показана работа машины с горизонтальной холодной ка- мерой сжатия. Все операции на ней выполняются в той же последова- тельности.
На рис. 212, в приведена схема работы поршневой машины с горячей камерой сжатия. Чугунный тигель 13 с жидким металлом все время по- догревают снизу газом через форсунку 21. Перед заливкой пресс-форму 19 закрывают, и мундштук 18 соединяется с каналом 17. При верхнем положе- нии поршня 16 через отверстие 14 сплав заполняет камеру сжатия 15 и канал. При движении вниз поршень впрессовывает жидкий металл в полость формы. После затвердевания металла давление снимают, поршень движется вверх, форму раскрывают и отливку выталкивают толкателями 20. Машины с горя-
чей камерой сжатия более производительны и расходуют меньше жидкого металла, однако их нельзя применять для литья сплавов с температурой плав- ления более 500 °С из-за быстрого изнашивания поршня.
348
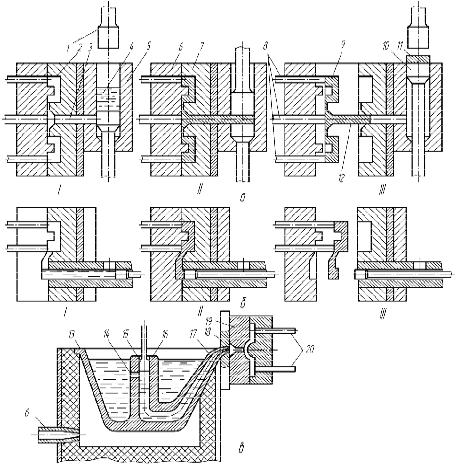
В машинах с холодной камерой сжатия поршень контактирует с рас- плавом в течение короткого промежутка времени и поэтому мало изнаши- вается. Здесь можно значительно повысить давление, что гарантирует высо- кую плотность и прочность отливок. Если в машинах с горячей камерой сжа- тия давление достигает 20 МПа, то в машинах с холодной камерой сжатия
при литье алюминиевых и медных сплавов давление может достигать
100-300 МПа.
Рис. 212. Схема поршневых машин для литья под давлением
Компрессорные машины, работающие на сжатом воздухе, применяются редко и поэтому здесь не рассматриваются.
Изготовление отливок литьем по выплавляемым моделям.
Сущность метода и область применения. Сущность состоит в том, что
по неразъемной легкоплавкой модели изготавливают неразъемную разовую форму. Модели из этой формы выплавляют, а образовавшуюся полость зали- вают жидким металлом. При этом способе получаемые отливки настолько точны, что объем механической обработки уменьшается на 80-100 % и в 1,5- 2,0 раза сокращается расход жидкого металла. Высокая точность и чистота
349
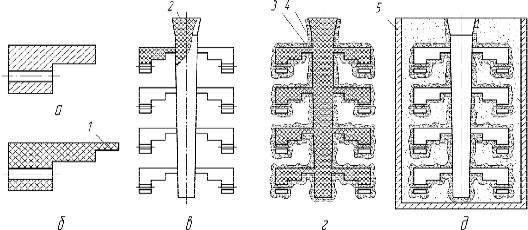
поверхности отливки обеспечиваются: применением неразъемных моделей (модели выплавляют и не требуется их расталкивать); отсутствием формо- вочных уклонов; изготовлением стержней в процессе формовки, а не отдель- но в стержневых разъемных ящиках; использованием маршалита (кварцевая мука) в качестве наполнителя в формовочной смеси, что обеспечивает полу- чение гладкой поверхности отливки.
Литье по выплавляемым моделям (рис. 213) применяют при производ- стве отливок очень сложной конфигурации из любых литейных сплавов, в том числе из высоколегированных сталей, имеющих высокую температуру плавления и трудно поддающихся механической обработке и ковке. Этим способом можно получать отливки массой от 0,02 до 100 кг, с толщиной сте- нок до 0,5 мм и отверстиями диаметром до 2 мм.
Рис. 213. Литье по выплавляемым моделям
Технология получения отливок литьем по выплавляемым моделям включает следующие этапы: изготовление разъемных пресс-форм; получение неразъемных легкоплавких моделей в пресс-формах; изготовление неразъем- ной разовой формы по легкоплавким моделям; выплавление моделей из фор- мы; обжиг формы; заливка формы металлом и выбивка готовых отливок.
Разъемные пресс-формы изготовляют из стали или алюминиевых спла- вов. Полость пресс-формы точно повторяет конфигурацию и размеры буду- щей детали с учетом усадки модельного состава.
Неразъемные легкоплавкие модели получают запрессовкой в пресс- форму модельного состава, нагретого до тестообразного состояния. Для его изготовления широко используют легкоплавкие материалы: парафин, стеа- рин, воск, церезин, канифоль и др. Легкоплавкая модель в отличие от обыч- ной является точной копией изготовляемой детали: она неразъемна, имеет все внутренние полости, отверстия, резьбу и не имеет стержневых знаков.
На рис. 213 приведен чертеж отливаемой детали (а) и неразъемной мо- дели (б), отличающейся от нее наличием питателя. Модели питателями «при-
350