
технология литейного производства
.pdf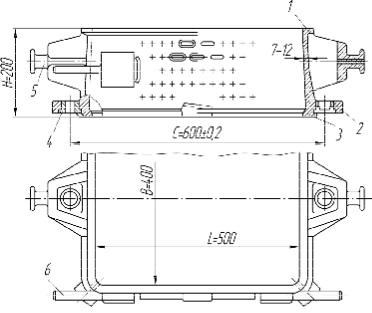
К опочной оснастке относят, опоки, штыри, крепежные приспособле- ния, литейные жакеты, подопочные плиты.
Классификация опок. Опока – приспособление для удержания формо- вочной смеси при изготовлении литейной формы, транспортировании ее и при заливке жидким металлом. Опоки классифицируют по геометрии, назна- чению. Различают опоки для ручной и машинной формовки, для формовки методом прессования под высоким удельным давлением, специальные опоки для безопочной формовки.
Материалом для опок служат чугун, сталь или алюминиевые сплавы. Опоки изготавливаются в соответствии с требованиями ГОСТ 17819-84.
Для удаления из формы газов, образующихся при заливке, в стенках опок выполняются вентиляционные отверстия. Удержание земли в форме и увеличение жесткости опок обеспечивается внутренними ребрами (крестови- нами).
Перемещение опок осуществляется при помощи ручек или цапф. Точность центровки опок при их сборке обеспечивается обычно специ-
альными втулками, закрепленными в отверстиях центрирующих ушков или самими точно обработанными отверстиями в ушках (рис. 93).
Рис. 93. Цельнолитая стальная опока
Наиболее широко применяются литые опоки из стали или чугуна.
Мелкие и средние формы изготавливаются в сварных опоках из проката специального профиля. Сварные опоки имеют достаточную жесткость при меньшем весе, чем литые. На рис. 93 показана цельнолитая стальная опока с размером в свету 500×400 мм. Боковая стенка опоки имеет в верхней части выступ 1 для увеличения прочности, а в нижней части – буртик 3 для удержа-
201
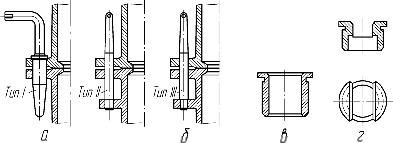
ния формовочной смеси. Для соединения с другой опокой (при помощи шты- рей) имеются приливы для направляющей 2 и центрирующей 4 втулок.
Для подъема при помощи крана служат цапфы 5, а для ручного подъема съемные ручки 6.
Металлические подопочные плиты имеют форму, соответствующую форме устанавливаемых на них опок.
Они изготавливаются из алюминиевых сплавов и снизу имеют сетку ребер жесткости.
Для удаления газов из форм при заливке в плитах делаются конические отверстия.
Транспортировка подопочных плит может осуществляться вручную (при помощи приливов ручек), электромостовым краном или кран-балкой (при помощи цапф).
Элементы центрирования. Спариваемые опоки всегда должны центри- роваться в двух диаметрально-противоположных точках.
Центрирующие отверстия располагаются на торцевых стенках, диамет- ры центрирующих отверстий и размеры центрирующих и направляющих вту- лок с учетом габаритов опок по ГОСТ 15019-69.
Центрирование при спаривании опок производят с помощью сборочных штырей через центрирующие и направляющие втулки (рис. 94).
Рис. 94. Способы спаривания (а, б) и элементы центрирования (в, г): а – штырем; б – на штырь; в – центрирующая; г – направляющие втулки
Контрольные вопросы.
1.Что такое модельный комплект?
2.Какие материалы применяют для изготовления моделей?
3.Металлические модели и стержневые ящики, их назначение, приме- няемые сплавы, процесс изготовления?
4.Классификация моделей по точности изготовления?
5.Классификация опок?
6.Назовите элементы центрирования опок?
7.Что такое драйер?
8.Какими способами осуществляют спаривание опок?
202
9.Почему необходимо применять элементы центрирования при сборке форм?
10.В чем отличие опок для ручной и машинной формовки?
ЛЕКЦИЯ 19.
ТЕМА: МАТЕРИАЛЫ ДЛЯ ИЗГОТОВЛЕНИЯ МОДЕЛЬНОГО КОМПЛЕКТА. КОНСТРУИРОВАНИЕ МОДЕЛЕЙ
План лекции
1.Техническое обоснование выбора материала моделей.
2.Конструирование деревянных и металлических моделей.
3.Конструирование стержневых ящиков.
Все модели по типу применяемого материала можно разделить на три группы: деревянные, металлические и неметаллические.
В производстве моделей наиболее широко используемыми породами дерева являются сосна, ель, пихта, липа, бук, клен, береза. Древесину заго- товляют зимой, и она проходит естественную или искусственную сушку; за- тем из нее готовят пиломатериалы – доски, брусья, бруски, которые и исполь- зуют для изготовления моделей. Каждая из пород дерева характеризуется оп- ределенными физико-механическими свойствами: имеет предел прочности на растяжение, сжатие, изгиб, твердость и вязкость (способность древесины по- лучать относительно большую остаточную деформацию при изгибе, не про- являя при этом признаков разрушения). Эти характеристики являются осно-
вополагающими при выборе той или иной породы дерева для изготовления моделей.
Металлические модели применяют в серийном производстве для отли- вок с высоким классом точности, низкой шероховатостью поверхности, при большом количестве съемов форм с одной модели. В качестве сплавов для моделей используют чугун, сталь, алюминиевые сплавы, реже – бронзы или латуни. Сплавы должны не только обладать высокими механическими свой- ствами, твердостью, но и хорошо обрабатываться, а после соответствующей механической обработки давать гладкую рабочую поверхность моделей.
Неметаллические модели предназначаются, как правило, для спе- циальных целей. Например, восковые (парафиностеариновые и др.) – для ли- тья по выплавляемым моделям, гипсовые – для художественного литья, це- ментные – для формовки с фальшивой опокой, пенополистироловые – для формовки по выжигаемым или газифицируемым моделям и т.д. Получают распространение и пластмассовые модели. Они прочнее деревянных, легче некоторых сплавов (чугун, сталь, бронза), хорошо шлифуются, дешевле ме- таллических моделей и т.д. Однако химические методы упрочнения пласт-
203
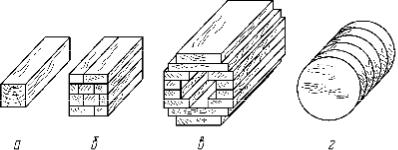
масс делают производство моделей вредным и требуют проведения специ- альных мероприятий по охране труда.
Выбор того или иного материала для изготовления моделей оп- ределяется рядом требований, предъявляемых к отливкам, а также тех- нологическими и техническими особенностями производства. Это класс точ- ности отливок, сложность, размерные характеристики отливок, серийность производства, способ изготовления форм, материал отливок. Отливки высо- кого класса точности, серийного производства, при машинной формовке, с размерами до 500 мм из всех видов сплавов экономически выгодно получать в формах по металлическим или пластмассовым моделям.
Конструирование деревянных и металлических моделей. Независимо от конструктивных признаков процесс изготовления моделей начинают с дере- вянных заготовок, используемых в качестве полуфабриката для выточки мо- делей заданной геометрической формы. Заготовки получают путем склеива- ния отдельных частей пиломатериалов, подготовленных из древесины.
Пиломатериалы, имеющие влажность 8-12 % и выдержанные после сушки, разрезают на мерные части. Широкие доски распиливают на узкие, шириной 110-150 мм, а затем склеивают в щиты, чтобы предупредить короб- ление. Рамные, кольцевые, дисковые заготовки, а также заготовки для круг- лых болванок делают не менее чем из трех слоев (рис. 95). При склеивании
учитывается расположение годовых колец древесины для предупреждения коробления.
Рис. 95. Заготовки для круглых болванок:
а – цельная; б – сплошная клееная; в – клееная полая; г – клееная из дисков
При изготовлении модели из заготовки мелкие формообразующие части (бобышки, платики, ребра и т.д.) крепят дюбелями, шурупами, гвоздями с предварительной врезкой в основное тело модели и посадкой на клей. Галте- ли (закругления) выполняют за счет основного тела модели или посредством врезки в нее (рис. 96). Галтели радиусом до 3 мм допускается выполнять из замазки. Отъемные и другие быстроизнашивающиеся части изготовляют из твердых пород древесины или из металла и пластмассы. Выступающие части моделей и стержневых ящиков, а также формовочные шаблоны, подвергае- мые особенно быстрому взносу (ребра, кромки, углы), армируют, т.е. оканто-
204
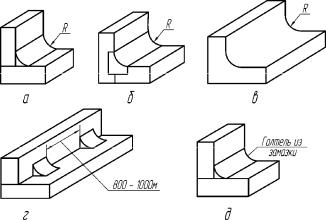
вывают пластинами из полосовой стали толщиной 1-3 мм.
Рис. 96. Выполнение галтелей в моделях и стержневых ящиках:
а – вклеиванием; б – врезанием; в – в теле модели (ящика); г – вклейкой частей галтелей (маяков); д – замазкой
Рабочую поверхность модельного комплекта тщательно шлифуют, она должна быть совершенно гладкой. Для выравнивания стыкуемых поверхно- стей допускается шпатлевание. После грунтования рабочие поверхности ок- рашивают не менее двух раз модельным лаком.
Взависимости от класса прочности или точности модели в технологию
ееизготовления могут быть внесены какие-то коррективы, устанавливаемые технологом. Эти данные заносят в технологическую карту, прикладываемую к чертежу детали с указанием технологии изготовления модельного комплек- та и отливки.
Как было отмечено выше, металлические модели получают из литой за- готовки, для изготовления которой применяют промодель. К деревянной промодели не предъявляется высоких требований по прочности, твердости, так как она используется один или несколько раз при формовке, но основные
технологические указания по изготовлению деревянных моделей относятся и к промоделям. Размеры промодели учитывают двойную усадку сплавов мо- дели и отливки и двойной припуск на механическую обработку.
Заготовка на модель должна быть плотной, без усадочных, газовых, песчаных дефектов, не иметь перекосов, коробления и трещин. Металличе-
ские модельные комплекты должны иметь соответствующий класс точности и шероховатости рабочей поверхности. Конструкция металлических моделей и стержневых ящиков должна обеспечить жесткость и прочность при мини- мальной массе. Модели допускается изготовлять сплошными только при мел- ких и средних габаритных размерах. Крепление отъемных частей моделей и крепление моделей к модельным плитам осуществляется с помощью шуру- пов, болтов и т.д.; при этом на рабочих поверхностях не должно быть следов крепежных изделий. Головка шурупа или болта утапливается внутрь рабочей
205
поверхности на некоторую глубину и сверху тщательно заделывается замаз- кой с соответствующей обработкой поверхности до гладкой.
Конструирование стержневых ящиков. Стержневые ящики по конст-
рукции подразделяют на два типа: неразъемные вытряхные и разъемные. Вы-
бор типа стержневого ящика определяется его габаритными размерами и конфигурацией.
Вытряхные стержневые ящики широко применяют в серийном произ- водстве отливок. Такой ящик состоит из коробки, донышка и вкладышей, ко-
торые после набивки полости ящика стержневой смесью извлекают вместе со стержнем. Заготовкой для таких стержневых ящиков является обычно короб- ка с дном, сделанная из досок или щитов. Коробку стержневого ящика изго- тавливают на шипах из досок толщиной 40-50 мм. Она расширяется от до- нышка вверх, чтобы удобнее было вытряхивать внутренние части ящика; ук- лон боковых стенок делается 1:10. Для облегчения удаления вкладышей к их наружным плоскостям клеем или шурупами крепят клинья, которые при пе- реворачивании ящика скользят по стенке коробки. Уклоны стенок корпуса при высоте вкладыша до 150 мм принимается 6°, от 151 до 250 мм – 5°, свы- ше 250 мм – 3°. Не следует делать лишних разъемов и вкладышей в ящике.
Для транспортировки ящика предусматриваются деревянные ручки, располагаемые на боковых стенках корпуса. Деревянные стержневые ящики, предназначенные для машинной формовки, оснащаются приспособлениями для крепления ящика к столу машины. Стержневым ящикам, предназначен- ным для изготовления стержней из ХТС или ЖСС, делают увеличенные ук- лоны боковых стенок.
Разъемные стержневые ящики могут иметь один, два и более разъема. Части ящика соединяют стяжками, скобами, дюбелями, втулками и др. Ме- таллические ящики выполняют тонкостенными. Их изготовляют так же, как и модели. На рис. 97 показана конструкция алюминиевого стержневого ящика (ГОСТ 19370-74) для изготовления песчаных стержней машинным, ручным и пескодувным способом.
Стержневые ящики для пескодувной и пескострельной формовки име- ют воздухоотводные и вдувные отверстия. Отношение площадей воздухоот- водного и вдувного отверстий составляет 0,2-0,3. При массовом производстве стержней это отношение увеличивают до 0,4-0,5. Вентиляцию стержневого
ящика осуществляют с помощью вент специальных щелей шириной
0,15-0,20 мм.
Нагреваемые стержневые ящики изготовляют из стали и чугуна. Отли-
чительной особенностью нагреваемых стержневых ящиков является наличие системы механизированных толкателей, которые монтируют индивидуально или на специальной плите. Толкатели устанавливают против знаков и других нерабочих частей стержня. Для простых стержневых ящиков расстояние ме- жду толкателями 100-130 мм, а для более сложных 50-70 мм. Зазор между толкателем и отверстием для него в стержневом ящике равен 0,15-0,25 мм.
206
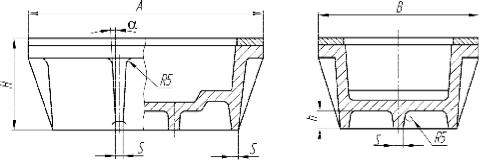
Пример изготовления модельного комплекта для отливки «Корпус вен- тиля» приведен на рис. 98 (изготовление модели) и на рис. 99 (изготовление стержня).
Рис. 97. Конструкция алюминиевого стержневого ящика
Перед установкой на токарный станок спаренных заготовок острые уг- лы древесины срубают или сострагивают. Подготовленная и закрепленная в
центрах токарного станка заготовка для корпуса вентиля показана на рис. 98, а.
При обработке на токарном станке сначала вытачивают знаки 1 (рис. 98, б). Затем обрабатывают наружную поверхность модели в соответст- вии с формой и размерами, указанными в модельном чертеже. Правильность
овальной формы обтачиваемой поверхности проверяют прикладыванием шаблона 4 (рис. 98, б). После окончательной обработки шаблон должен пол- ностью прилегать к обработанной поверхности, а его горизонтальные участки при этом должны касаться цилиндрических поверхностей знаков. Затем выта- чивают углубления 3 (рис. 98, б) для последующей установки фланцев.
Снятая с центров обточенная заготовка освобождается от метал- лических планок. Посредством легкого удара молотком по ручке плоской стамески, лезвие которой установлено на границе разъема на торце одного из концов заготовки, заготовка легко разъединяется на две части по плоскости разъема. Оставшиеся концы около стержневых знаков удаляют пилой, а бу-
магу с клеем на поверхности обеих частей заготовки сострагивают маленьким рубанком, рабочую поверхность которого смазывают машинным маслом. По-
сле этого на обеих частях заготовки на соответствующем расстоянии от оси вращения выстрагивают плоские поверхности под прямым углом к плоскости разъема. К этим поверхностям приклеивают две предварительно выстроган-
ные дощечки для изготовления галтели по линии пересечения поверхностей двух тел (рис. 98, б). Толщина дощечек определяется по модельному чертежу. Фланцы 5 (рис. 98, г, д, е) для модели вытачивают на токарном станке (на планшайбе) из заготовок, выпиленных из досок соответствующей толщины
(см. рис. 98, г, д, е).
Цилиндрическую часть модели патрубка изготовляют аналогично ос-
207
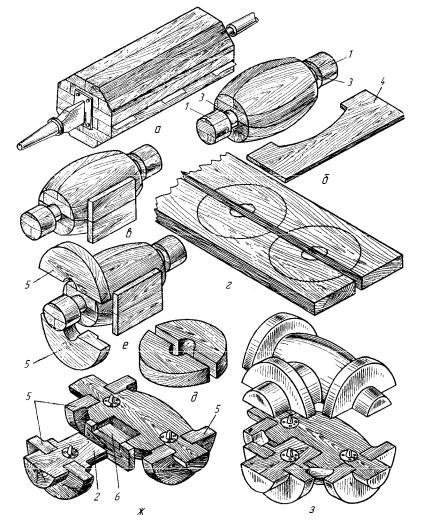
новной части модели. При этом цилиндрическую часть патрубка вытачивают такой длины, чтобы из нее можно было затем изготовить вручную шип 2 (рис. 98, ж) для крепления патрубка к основной части модели, в которой предварительно изготовляют углубление 6 (рис. 98, ж).
Рис. 98. Процесс изготовления модели «Корпуса вентиля»
После соединения патрубка с основной частью модели с помощью ши- па 5, клея и шурупов, из приклеенных ранее дощечек (рис. 98, в) изготовляют галтель путем ручной обработки этих дощечек полукруглой стамеской. Затем
к модели приклеивают фланцы и окончательно отделывают модель
(рис. 98, з).
Технология изготовления стержневого ящика к модели «Корпус венти- ля» изображена на рис. 99.
Стержневой ящик состоит из двух симметричных половинок. Однако
следует отметить некоторые особенности в изготовлении этого стержневого
208
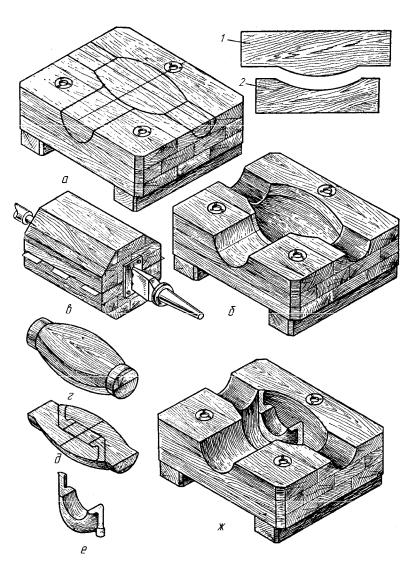
ящика. После разметки обеих половинок ящика, как указано на рис. 99, а, де- лают полости в них. Сначала вырезают полукруглой стамеской или выстраги- вают в каждой половине ящика специальным рубанком-галтельником сквоз- ное полуцилиндрическое отверстие диаметром 40 мм. Затем вырезают по- лость овальной формы. Для обеспечения правильной формы полости приме- няют шаблон 1 (рис. 99), выступающая овальная часть которого натирается цветным карандашом. Далее вырезают цилиндрическое отверстие диаметром 54 мм, расположенное перпендикулярно долевой оси ящика. После этого по- лость ящика приобретает вид, указанный на рис. 99, б.
Рис. 99. Процесс изготовления стержневого ящика для модели «Корпуса вентиля»
Перегородки для части ящика овальной формы изготовляют из заготов- ки, склеенной через бумагу из двух брусков. Заготовку устанавливают для
209
обработки на токарном станке, как показано на рис. 99, в; из заготовки выта- чивают вставку в соответствии с размерами и формой овальной полости ящи- ка. Правильность кривизны поверхности вытачиваемой вставки проверяют шаблоном 2 (рис. 99). После обработки вставка приобретает вид, указанный на рис. 99, г. Вставку разъединяют по плоскости разъема на две части и каж-
дую из них вставляют в полость половинок стержневого ящика и производят разметку перегородки на плоской поверхности каждой части вставки. После разметки вставки вынимают из полостей ящика (рис. 99, д) и подвергают ручной обработке стамесками. Для облегчения работы при извлечении стержня из ящика на перегородке делают формовочные уклоны, которые из- меряют при изготовлении малкой.
Обработанную по размерам перегородку (рис. 99, е) устанавливают в полость ящика и приклеивают. Затем между вставкой и основной полостью ящика выполняют галтели из замазки, ящик зачищают и окрашивают. На рис. 99, ж показана одна из половин готового ящика.
Изготовление модельной оснастки из пластмасс. Модельные комплек-
ты из пластмасс обладают лучшими свойствами, чем деревянные и металли- ческие комплекты. Пластмассовые модели имеют высокую механическую прочность и точность, не подвергаются короблению, разбуханию, усушке, коррозии. При изготовлении модельной оснастки широко применяют пласт- массы на основе эпоксидных смол. Формовочные уклоны, точность и шеро- ховатость поверхности пластмассовых модельных комплектов должны соот- ветствовать требованиям к модельным комплектам, изготовленным из алю- миниевых сплавов.
Процесс изготовления модельных комплектов из пластмасс на основе эпоксидных смол состоит из следующих основных операций: изготовление мастер-модели, изготовление форм, изготовление пластмассовой модели, стержневого ящика, монтаж модели на модельную плиту. Мастер-модель можно изготовить из древесины, гипса или алебастра.
Существует два способа изготовления модельных комплектов из пласт- масс: литьевой и контактный. Литьевой способ применяют при изготовлении модельных комплектов небольших габаритных размеров. Контактный способ применяют в тех случаях, когда модель (стержневой ящик) должна иметь вы- сокие прочностные свойства, или когда ее конструкция имеет сложные гео- метрические формы и выступающие тонкие части.
При этом способе используют армирующий стеклонаполнитель (стек- лоткань, стеклоленту, стекложгут), который в комплекте с пропиточными эпоксидными составами образует прочный конструкционный материал стек- лопластик. После изготовления модели неровности, шероховатости на по- верхности сухой гипсовой формы, зачищают шлифовальной шкуркой, а затем наносят разделительный состав. После этого приготовляют эпоксидную ком- позицию для облицовочного слоя и наносят ее кистью равномерно на всю по- верхность. Кистью проводят по поверхности формы 4-5 раз до начала жела-
210