
Конспект лекций
.pdfрахунок сил тертя. Характеристика правильної машини визначається розмірами та механічними властивостями листового прокату.
Правка здійснюється за 3÷5 або більше проходів за рахунок пластичної деформації в поверхневих шарах листового прокату. Кількість роликів машини впливає на якість правки. Для правки товстолистового прокату (S>4 мм) застосовуються машини з числом роликів від 5 до 11 (частіше 7). Ролики виготовляють із сталі і піддають поверхневому загартуванню до HRC 50÷60, або з чавуну з вибіленою поверхнею. Розмір діаметрів роликів складає
|
Dрол = (0,9÷0,95)t, |
(4.38) |
де |
t – крок між роликами (мм) вибирають в залежності від зусиль Р які |
|
діють на ролики. |
|
|
Зі |
зменшенням t точність правки зростає. |
Крок роликів один з |
розрахункових параметрів.
Випускаються правильні машини з гідроприводом. На них можна здійснювати правку листового прокату з товщиною листа до 45 мм і шириною до 3600 мм [4].
Для вибору машини необхідно знати потужність правки яка визначається
по формулі: |
|
||
N = |
2МкрV |
квт, |
(4.39) |
102D η |
|||
|
рол |
|
де – Мкр - сумарний крутний момент, кГм; V – швидкість правки, м/хв.;
Dрол – діаметр роликів, мм;
η – коефіцієнт корисної дії (η =0,8).
. Для цього потрібно розрахувати крутні моменти які діють у процесі
правки. |
|
|
Сумарний крутний момент визначається по формулі: |
|
|
|
Мк = М1 + М2 + М3 , |
(4.40) |
де М1- момент деформації листа; |
|
|
М2 |
– момент від сил тертя кочення роликів по листу; |
|
М3 |
– момент від сил тертя у підшипниках роликів. |
|
81

Момент М1 визначається з визначення роботи деформації листового
прокату по формулі: |
|
М1 = σ т24bsDE (к1 + 0,33к −1) , |
(4.41) |
де – σт – межа текучості матеріалу; Е – модуль пружності; к – коефіцієнт пружної зони.
Коефіцієнт пружної зони визначається з відношення:
к = 2Z0/s, |
(4.42) |
де - Z0 – ширина пружної зони (рис. 4.11).
Рис. 4.11. Епюра напружень при згинанні у перетині
Коефіцієнт пружної зони для кожного ролика визначається з використанням експериментальної діаграми (рис. 4.12) по формулі:
кі = к3 +{(1 - к3)/(n – 4)}(і – 3). (4.43) Коефіцієнт пружної для третього ролика визначають експериментально в
залежності від властивостей матеріалу заготовки та числа роликів правильної машини.
Коефіцієнт пружної зони для другого ролика визначають з вираження к2 = 2к3.
82
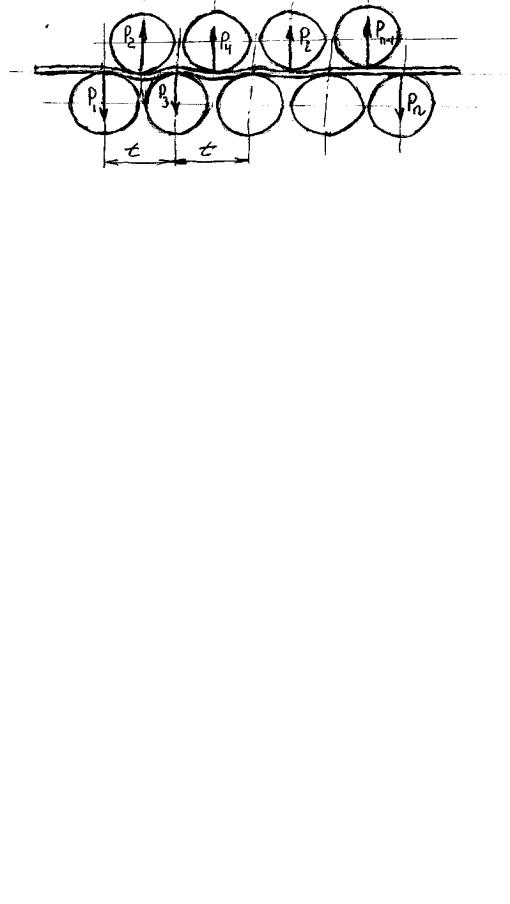
Рис. 4.12. Залежність коефіцієнту пружної зони від числа роликів
Значення крутних моментів М2 та М3 визначають по формулам:
М2 = 0,5DРf; М3 = 0,5Рdµ, |
(4.44) |
де – Р – сили які діють на ролики; |
|
D – діаметр роликів; |
|
f - коефіцієнт тертя котіння роликів по листу (f |
≈ 0,1); |
d = діаметр цапфи роликів; |
|
µ = коефіцієнт тертя у підшипниках опор роликів: (котіння µ = 0,003÷0,005; ковзання µ = 0,08÷0,1).
Схема процесу правки приведена на рис. .
Рис. 4.13. Схема правки на багато валковій листоправильній машині
83
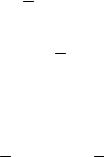
Користуючись епюрою напружень (рис. 4.11) визначаємо згинальні моменти, які виникають у процесі правки за форулою
z0 |
S / 2 |
(4.45) |
M = 2∫σzdF + 2 ∫σT zdF |
0z0
Виразимо σ через межу текучості σt по формулі |
σ = σt |
z |
, а площу |
||||||||||||||||||||||||
|
|||||||||||||||||||||||||||
|
|
|
|
|
|
|
|
|
|
|
|
|
|
|
|
|
|
|
|
|
|
|
|
|
|
z0 |
|
поперечного перетину через dF = b dz , |
|
|
|
||||||||||||||||||||||||
|
|
|
|
|
|
|
|
2 |
|
|
z0 |
|
|
|
|
|
|
|
|
S / 2 |
(4.46) |
||||||
|
|
M = |
|
b |
∫ |
σT z2dz + 2b |
∫ |
σT zdz |
|||||||||||||||||||
|
|
|
|||||||||||||||||||||||||
|
|
|
|
|
|
|
|
z |
0 |
|
|
|
|
|
|
|
|
|
|
|
|
|
|||||
|
|
|
|
|
|
|
|
|
|
0 |
|
|
|
|
|
|
|
|
|
z0 |
|
|
|
|
|||
Тоді отримаємо після підстановки та інтегрування |
|
|
|
||||||||||||||||||||||||
|
|
|
|
|
|
|
|
|
|
|
|
|
2 |
|
|
|
1 |
2 |
|
|
|
|
|
|
|
||
М = σtb(0,25s |
|
|
|
- |
|
z0 ), |
|
|
(4.47) |
||||||||||||||||||
|
|
|
3 |
|
|
||||||||||||||||||||||
|
|
|
|
|
|
|
|
|
|
|
|
|
|
|
|
|
|
|
|
|
|
|
|
|
|
|
|
M = |
|
|
|
S 2 |
− |
z2 |
|
|
|
|
|
|
|
|
|
(4.48) |
|||||||||||
σT b |
|
|
|
|
|
|
|
0 |
|
|
|
|
|
|
|
|
|
||||||||||
|
|
|
|
|
|
4 |
|
|
|
|
3 |
|
|
|
|
|
|
|
|
|
|
|
|
||||
|
|
|
|
|
|
|
|
|
|
|
|
|
|
|
|
|
|
|
|
|
|||||||
Підставляючи у цю формулу значення коефіцієнту пружної зони |
|||||||||||||||||||||||||||
K = |
|
2z0 |
|
|
|
|
|
|
|
|
|
|
|
|
|
|
|
|
|
|
(4.49) |
||||||
|
S |
/ |
|
|
|
|
|
|
|
|
|
|
|
|
|
|
|
|
|
|
|
|
|||||
|
|
|
|
|
|
|
|
|
|
|
|
|
|
|
|
|
|
|
|
|
|
|
|
|
|
||
отримаємо: |
|
|
|
|
|
|
|
|
|
|
|
|
|
|
|
|
|
|
|
|
|
|
|
|
|
|
|
М = 0,25σtbs2(1 - |
1 |
к2). |
|
(4.50) |
|
||||||||||||||||||||||
3 |
|
|
|||||||||||||||||||||||||
|
σ |
|
bS |
2 |
|
|
|
|
K |
2 |
|
|
|
|
|
(4.51) |
|||||||||||
M = |
|
|
T |
|
|
|
|
1− |
|
|
|
|
|
|
|
|
|
|
|
|
|||||||
|
|
|
|
|
|
|
|
|
|
|
|
|
|
|
|
|
|
||||||||||
|
|
|
|
4 |
|
|
|
|
|
|
|
|
3 |
|
|
|
|
|
|
|
|
|
|||||
|
|
|
|
|
|
|
|
|
|
|
|
|
|
|
|
|
|
|
|
|
Визначимо згинальні моменти, які діють проти кожного ролика (рис. 4.13): М2 = Р1 2t ;
- М3 = Р1t – Р2 2t ;
М4 |
= Р1 |
3 |
t – Р2t + Р3 |
t |
; |
(4.52) |
|
2 |
2 |
||||||
|
|
|
|
|
-М5 =P12t - Р2 32 t + Р3t - Р4 2t ;
84
Mi = P1 |
(i −1) |
t − P |
|
(i − 2) |
t + P |
|
(i − 3) |
t − |
..... + P |
1 |
t ? |
||||||
2 |
2 |
2 |
|
|
|||||||||||||
|
|
2 |
|
3 |
|
|
|
i−1 2 |
|||||||||
відкіля |
|
|
|
|
|
|
|
|
|
|
|
|
|
|
|
|
|
|
|
|
|
|
|
Р1 = |
2М 2 |
; |
|
|
|
|
|
|
|||
|
|
|
|
|
t |
|
|
|
|
|
|||||||
|
|
|
|
|
|
|
|
|
|
|
|
|
|
|
|
|
|
|
|
Р2 |
= |
2(2М 2 + М3 ) |
; |
|
|
|
|
||||||||
|
|
|
|
|
|
||||||||||||
|
|
|
|
|
|
|
|
|
t |
|
|
|
|
|
|
|
|
|
|
Р3 = |
2(2М3 + М 4 + М 2 ) |
; |
|
(4.53) |
|||||||||||
|
|
|
|
||||||||||||||
|
|
|
|
|
|
|
|
|
t |
|
|
|
|
|
|
|
|
|
|
Рi |
= |
|
2(2Mi |
+ Mi−1 + Mi+1 ) |
|
|
|
||||||||
|
|
|
|
|
|
|
t |
|
|
|
|
|
|
|
|
||
|
|
|
|
|
|
|
|
|
|
|
|
|
|
|
|
|
Pn-1 |
= |
2(2M n−1 + M n−2 ) |
, |
||
|
|
|
|||
|
|
|
t |
||
|
Pn = |
2M n−1 |
. |
||
|
|
||||
|
|
|
t |
Таким чином знаючи моменти та визначивши сили, які діють на ролики можна підрахувати крутні моменти та потужність процесу правки.
4.2.3.2.Способи очищення та розмічання листового прокату
Очищення листового прокату в першу чергу необхідне для того щоб шкідливі речовини не попадали у склад зварювального шву і не знижували його фізико-механічні властивості. Основними видами забруднень являються окалина, іржа, різні органічні та неорганічні забруднення.
Окалина (Fe3O4) утворюється в процесі прокатки і термічної обробки.
При попаданні у розплавлену зону зварного шву може визвати утворення пористості і зміну хімічного складу і фізичних властивостей шлаку, а, отже, і властивостей металу шва. Попадає у розплав зварного шва окалина перетворюється в інше з’єднання FeО (Fe3O4+Fe=4FeО), яке розчиняється ,
в розплавах шлаку і металу, підвищуючи зміст О2 у металі шва. При цьому ковкість і ударна в'язкість погіршуються (ан=1,9 5,3 кГм/см2).
85
Іржа являється продуктом корозії заліза у присутності води та кисня навколишнього середовища: 4Fe+2Н2O+3О2=2(Fe2O3 Н2O).
Як правило іржа не має міцного зв’язку з основним металом.
При високій температурі дуги молекула води розкладається на кисень і водень: 2H2O↔2H2+O2±Q кал.
У шві з'являються пори в результаті виділення водня а кисень розчиняється у металі шва знижуючи його властивості. Ударна в’язкість ан знижується до 2÷3 3 кГм/см2 при нормальному значенні ан=8 кГм/см2.
Інші забруднення такі як пісок, глинозем, органічні тощо теж можуть впливати на якість зварного шва.
Існують різноманітні способи очищення листового прокату від забруднень. Металургійний спосіб полягає в застосуванні флюсів, електродного дроту й електродів зі зниженою чутливістю до іржі й окалини (флюси з MnО, електроди
з покриттям до якого входять CaF2 і Ca).
Технологічний спосіб це застосування постійного струму або, двох дугового процесу та ін.
При хімічному способі очищення заготовку занурюють у травильну ванну з 20÷25% розчином соляної або сірчаної кислот. Після очищенням травленням поверхню заготовки нейтралізують лужними розчинами, промивають водою та сушать.
Термічний спосіб полягає у різкому нагріванні поверхні заготовки відкритим полум’ям до температури 150 0С ÷200 0С. Окалина та метал мають різні коефіцієнти лінійного розширення і тому окалина відділяється від металу.
Механічні способи існують різноманітні. До них відносяться наступні способи: очищення металічними щітками, очищення абразивними кругами, шрото-струменеве очищення, шротометальне очищення.
Очищення металічними щітками, які обертаються. Для виготовлення щіток використовують металічний дріт діаметром 0,2÷0,8 мм. Швидкість обертання щіток складає 15÷45 м/с;
86
Очищення абразивними кругами та голко-фрезами. Робочою поверхнею голкофрези служить дротовий ворс, який розташований як паралельно осі обертання голкофрези так і під кутом до неї.
Шротоструменеве очищення це обдування поверхні за допомогою стислого повітря в якому знаходиться шрот;
Шротометальне очищення в якому замість пневматичних розпилюючи устроїв застосовують шротометальні установки в яких струмінь абразивного матеріалу зі швидкістю до 60 м/с утворюється за рахунок відцентрової сили при обертанні турбінки;
Розмічанням називають операцію в результаті якої здійснюють нанесення на поверхню заготовки ліній або точок відповідно до розмірів розрахованого контуру розгортки деталі. Нанесення контуру розгортки виконується методами планометрії. Криволінійні контури будуються по координатним точкам. При цьому не рекомендується вести розмічання від точки до точки, тому що це приводить до накопичення похибки. Поверхню заготовки перед розмічанням покривають тонким шаром крейдового розчину змішаного з льняним маслом, клеєм або водним розчином мідного купоросу. Розмічальні лінії накернюють або визначають рисувалкою. Ширина та глибина ліній не більше 0,3 мм, Відстань між точками накернювання по контуру повинна бути 20 мм.
Розрізняють два метода розмічання: камеральний і плазовий.
Камеральний метод полягає в переносі розмірів на матеріал по попередньо розроблених ескізах розгорток. Розміри в ескізах розгорток одержують на основі робочих креслень деталей і виконують в технологічному або конструкторському бюро.
Плазовий метод полягає у виконанні розгортки у натуральну величину на спеціальній площині (плазі) або безпосередньо на металі. Попередні ескізи розгорток не розробляють.
У виробництві апаратури як правило використовують камеральний метод. Плазовий застосовується для виконання складних деталей апаратів.
87
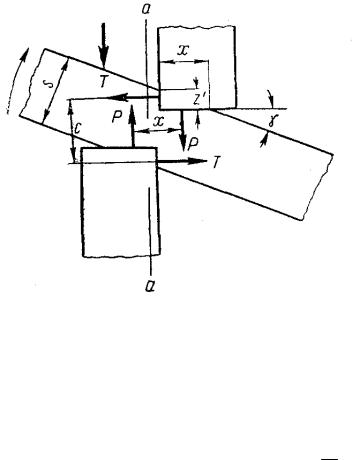
4.2.3.3.Способи розрізання листового прокату
Існують два основних метода розрізання листового прокату: холодна різка і термічна різка.
Холодне різання здійснюється без зняття стружки на ножицях для листового або сортового прокату та має саму високу продуктивність. Але застосування цього виду розрізання можливе тільки до товщини заготовки 60 мм. Крім того вартість обладнання джля холодного розрізання зростає з товщиною прокату. Схема розрізання приведена на рис. 4.14.
Рис. 4.14. Схема холодного розрізання листового прокату
Процес розрізання полягає в тому що ножі при переміщенні створюють силу розрізання Р, яка визиває напруження зсуву. З ростом сили Р зростає
величина зминання матеріалу z′ і відносна деформація ε = Z′ .
S
Силу розрізання можна визначити по формулі
|
S |
′ |
(4.54) |
|
P = τB(cosγ |
||||
− 2Z ) , |
||||
|
|
88 |
|
де τ - напруження зсуву (опір розрізанню); В – ширина листа;
S – товщина листа;
В залежності від зазору між ножами і збільшенням сили розрізування по причині зносу ножів необхідну силу розрізування вибирають у 1,5÷1,8 разів більшою за розрахунковою.
Вибір типу ножиців залежить від товщини заготовки S. Цей же параметр визначає зазор між ножами: при S до 10 мм в = 0,07 мм; при S 10÷20 мм в = 0,08 мм; при S 20÷24 мм в = 0,1 мм.
При розрізанні виникає момент Рх (рис. 4.14), який повертає заготовку в процесі різання та йому протилежний момент Тс, де Т рівнодіюча сила, нормальна до площини розрізання. Момент Рх значно більший за момент Тс і тому заготовка може повертатися утворюючи кут γ . Це може привести до поломки ножів. Для безпечної роботи ножиців необхідно застосовувати спеціальні упори.
У зоні розрізання змінюється мікроструктура матеріалу і можуть виникати тріщини. Тому після розрізання рекомендується обробка кромок. Якщо область матеріалу у зоні розрізання попадає у зону зварного шву, то обробка після розрізання не обов’язкова.
Холодне розрізання листового прокату здійснюється на ножицях двох типів: ножицях з призматичними ножами з нахилом та дискових ножицях.
Ножиці з призматичними ножами з нахилом називаються гільйотинними ножицями. Рух ножу в них передається системою важелів, кривошипношатунним механізмом або від гідравлічного привода. У гільйотинних ножиців закритого типу Рис. 4.15) нижній ніж 3 горизонтальний а верхній 4 з нахилом. Різання здійснюється рухом верхнього ножа. Лист 6 подається до упора 7 і затискається устроєм 2.
89

Рис. 4.15. Схема роботи гільйотинних ножиців.
На рис. 4.16 представлена кінематична схема кривошипно-шатунних гільйотинних ножиців. Нерухомий ніж 3 установлений на станіні, а рухомий 2 з нахилом 2÷60 на балці, яка приводиться у рух кривошипно-шатунним механізмом. Ножиці мають стіл з притискним устроєм та регулюючий упор. Маховик-шків 1 створює запас енергії, яка необхідна для розрізання. Довжина гільйотинних ножиців може доходити до 4 м.
Рис. 4.16. Кінематична схема кривошипно-шатунних ножиців.
90