
water quality and system
.pdf
< previous page page_185
Table 11-1. Minimum plumbing facilities for office and public buildings. Source: International Association of Plumbing And Mechanical Officials, ANSI 40-1996 (pending) Safety Requirements for Plumbing, Uniform Plumbing Code. Note that other provisions and restrictions apply; check the Code for details or refer to your local code
"Each person shall be provided with sanitary facilities, including provisions for the physically handicapped as prescribed by the Department having jurisdiction. For requirements for the handicapped, ANSI A117.1-1992, Accessible And Usable Buildings And Facilities, may be used.
"The total occupant load shall be determined by minimum existing requirements. The minimum number of fixtures shall be calculated at fifty (50) percent male and fifty (50) percent female based on the total
occupant load." |
|
Urinals |
Lavatories |
Drinkirng |
||
Type Of |
Water Closets |
|||||
Building Or |
(Fixtures/Person) |
(Fixtures/Person) |
(Fixtures/Person) |
Fountains |
||
Occupancy |
|
|
|
|
|
(Fixtures/Person) |
Office or |
Male |
Female |
Male |
Male |
Female |
1 per 150 |
public |
||||||
buildings |
1:1-100 |
3:1-50 |
1:1-100 |
1:1-200 1:1-200 |
|
|
|
|
|||||
|
2:101-200 |
4:51-100 |
2:101-200 |
2:201-400 2:201-400 |
|
|
|
3:201-400 |
8:101-200 |
3:201-400 |
3:401-750 3:401-750 |
|
|
|
|
11:201-400 |
4:401-600 |
Over 750, add one |
|
|
|
|
|
|
fixture for each |
|
|
|
|
|
|
additional 500 |
|
|
|
Over 400, add one fixture Over 600, add one |
persons |
|
|
||
|
|
|
|
|||
|
for each additional 500 |
fixture for each |
|
|
|
|
|
males and one for each |
additional 300 males |
|
|
|
|
Office or |
additional 150 females |
|
|
|
|
|
|
|
|
|
|
|
|
public |
Male |
Female |
Male |
Male |
Female |
|
buildings (for |
|
|||||
employee use) |
1:1-15 |
1:1-15 |
0:1-9 |
1 per 40 |
1 per 40 |
|
|
|
|||||
|
2:16-35 |
3:16-35 |
1:10-50 |
|
|
|
|
3:36-55 |
4:36-55 |
Add one fixture for |
|
|
|
|
|
|
each additional 50 |
|
|
|
males
Over 55, add one fixture for each additional 40 persons
< previous page page_185
next page >
Page 185
next page >
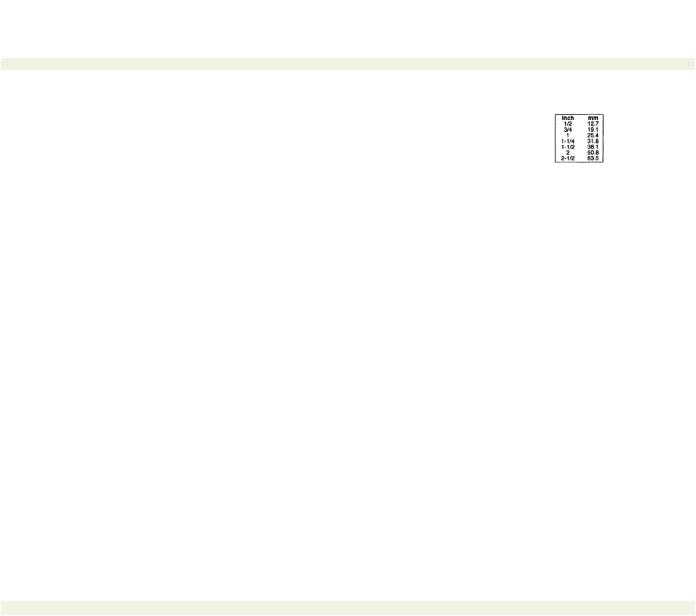
< previous page |
page_186 |
next page > |
Page 186
Table 11-2. Fixture design method, showing data for calculating pipe and meter sizing. Source: International Association of Plumbing And Mechanical Officials, ANSI 40-1996 (pending) Safety Requirements for Plumbing, Uniform Plumbing Code.
Pressure Range - 30 to 45 psi (207 to 310 kPa)***
Meter |
Building Supply and |
|
|
|
Maximum Allowable Length in Feet (meters) |
|
|
|
|
|||||||
Branches, Inches |
|
|
|
|
|
|
|
|
|
|
|
|
|
|
|
|
and Street |
|
|
|
|
|
|
|
|
|
|
|
|
|
|
|
|
Service, |
|
40 |
60 |
80 |
100 |
150 |
200 |
250 |
300 |
400 |
500 |
600 |
700 |
800 |
900 |
1000 |
Inches |
|
|||||||||||||||
1/2** |
(12) |
(18) |
(24) |
(30) |
(46) |
(61) |
(76) |
(91) |
(122) |
(152) |
(183) |
(213) |
(244) |
(274) |
(305) |
|
¾ |
6 |
5 |
4 |
3 |
2 |
1 |
1 |
I |
0 |
0 |
0 |
0 |
0 |
0 |
0 |
|
¾ |
¾ |
16 |
16 |
14 |
12 |
9 |
6 |
5 |
5 |
4 |
4 |
3 |
2 |
2 |
2 |
1 |
¾ |
I |
29 |
25 |
23 |
21 |
17 |
15 |
13 |
12 |
10 |
8 |
6 |
6 |
6 |
6 |
6 |
1 |
1 |
36 |
31 |
27 |
25 |
20 |
17 |
15 |
13 |
12 |
10 |
8 |
6 |
6 |
6 |
6 |
¾ |
1-1/4 |
36 |
33 |
31 |
28 |
24 |
23 |
21 |
19 |
17 |
16 |
13 |
12 |
12 |
11 |
11 |
1 |
1-1/4 |
54 |
47 |
42 |
38 |
32 |
28 |
25 |
23 |
19 |
17 |
14 |
12 |
12 |
11 |
11 |
1-1/2 |
1-1/4 |
78 |
68 |
57 |
48 |
38 |
32 |
28 |
25 |
21 |
18 |
15 |
12 |
12 |
11 |
11 |
1 |
1-1/2 |
85 |
84 |
7g |
65 |
56 |
48 |
43 |
38 |
32 |
28 |
26 |
22 |
21 |
20 |
20 |
1-1/2 |
1-1/2 |
150 |
124 |
105 |
91 |
70 |
57 |
49 |
45 |
36 |
31 |
26 |
23 |
21 |
20 |
20 |
2 |
1-1/2 |
151 |
129 |
129 |
110 |
80 |
64 |
53 |
46 |
38 |
32 |
27 |
23 |
21 |
20 |
20 |
1 |
2 |
85 |
85 |
85 |
85 |
85 |
85 |
82 |
80 |
66 |
61 |
57 |
52 |
49 |
46 |
43 |
1-1/2 |
2 |
220 |
205 |
190 |
176 |
155 |
138 |
127 |
120 |
104 |
85 |
70 |
61 |
57 |
54 |
51 |
2 |
2 |
370 |
327 |
292 |
265 |
217 |
185 |
164 |
147 |
124 |
96 |
70 |
61 |
57 |
54 |
51 |
2 |
2-1/2 |
445 |
418 |
390 |
370 |
330 |
300 |
280 |
265 |
240 |
220 |
198 |
175 |
158 |
143 |
133 |
Pressure Range - 46 to 60 psi (317 to 414 kPa)*** |
|
|
|
Maximum Allowable Length in Feet (meters) |
|
|
|
|||||||||
Meter and Street |
Building Supply and |
|
|
|
|
|
|
|
|
|||||||
Branches, Inches |
40 |
60 |
80 |
100 |
150 |
200 |
250 |
300 |
400 |
500 |
600 |
700 |
800 |
900 |
1000 |
|
Service, Inches |
|
|||||||||||||||
¾ |
1/2'* |
(12) |
(18) |
(24) |
(30) |
(46) |
(61) |
(76) |
(91) |
(122) |
(152) |
(183) |
(213) |
(244) |
(274) |
(305) |
7 |
7 |
6 |
5 |
4 |
3 |
2 |
2 |
1 |
1 |
1 |
0 |
0 |
0 |
0 |
||
¾ |
¾ |
20 |
20 |
19 |
17 |
14 |
11 |
9 |
8 |
6 |
5 |
4 |
4 |
3 |
3 |
3 |
¾ |
1 |
39 |
39 |
36 |
33 |
28 |
23 |
21 |
19 |
17 |
14 |
12 |
10 |
9 |
8 |
8 |
1 |
1 |
39 |
39 |
39 |
36 |
30 |
25 |
23 |
20 |
18 |
15 |
12 |
10 |
9 |
8 |
8 |
¾ |
1-1/4 |
39 |
39 |
39 |
39 |
39 |
39 |
34 |
32 |
27 |
25 |
22 |
19 |
19 |
17 |
16 |
1 |
1-1/4 |
78 |
78 |
76 |
67 |
52 |
44 |
39 |
36 |
30 |
27 |
24 |
20 |
19 |
17 |
16 |
1-1/2 |
1-1/4 |
78 |
78 |
78 |
78 |
66 |
52 |
44 |
39 |
33 |
29 |
24 |
20 |
19 |
17 |
16 |
1 |
1-1/2 |
85 |
85 |
85 |
85 |
85 |
85 |
80 |
67 |
55 |
49 |
41 |
37 |
34 |
32 |
30 |
1-1/2 |
1-1/2 |
151 |
151 |
151 |
151 |
128 |
105 |
90 |
78 |
62 |
52 |
42 |
38 |
35 |
32 |
30 |
2 |
1-1/2 |
151 |
151 |
151 |
151 |
150 |
117 |
98 |
84 |
67 |
55 |
42 |
38 |
35 |
32 |
30 |
1 |
2 |
85 |
85 |
85 |
85 |
85 |
85 |
85 |
85 |
85 |
85 |
85 |
85 |
85 |
83 |
80 |
1-1/2 |
2 |
370 |
370 |
340 |
318 |
272 |
240 |
220 |
198 |
170 |
150 |
135 |
123 |
110 |
102 |
94 |
2 |
2 |
370 |
370 |
370 |
370 |
368 |
318 |
280 |
250 |
205 |
165 |
142 |
123 |
110 |
102 |
94 |
2 |
2-1/2 |
654 |
640 |
610 |
580 |
535 |
500 |
470 |
440 |
400 |
365 |
335 |
315 |
285 |
267 |
250 |
**Building supply, three-quarter (¾) inch (19.1 mm) nominal size minimum.
***Available static pressure after head loss.
< previous page page_186 next page >

< previous page |
page_187 |
next page > |
Page 187
after using the restroom. The sink should provide both hot and cold water. When the number of water closets, urinals, and sinks has been estimated, room dimensions are established.
Sinks - Restroom sinks can be free-standing, recessed in a counter or the pedestal type. A hot and cold water faucet along with a drain is provided. Codes specify the distance from the sink drain to the trap and from the trap to the vent. The height of the sink is standardized in the U.S. as is the height for the water closet (see Figure 11 - 1).
Along with the sink will be a soap and paper towel dispenser, but the trend in recent years has been to locate the paper towel dispenser more than a hand's reach away from the sink to prevent the paper towels from falling into the sink and plugging it. A warm air dryer is still popularly used for drying hands but a dryer requires electrical wiring power to the units.
Layout - As the architect lays out the facility, the restrooms will be strategically located to provide optimum location. In a large multistory building, for example, a restroom is provided on each floor. Given the size of the floor, there may be more than one restroom on each floor. For some designs, executives may insist on their own private washroom.
The sizes and layouts of these facilities is a matter of design. Knowing what works and what does not is a matter to be determined by architects. While the plumbing codes will provide recommendations for the number of users per water closet and/or sink, general guidance is needed to determine a practical distance to the rest room from the patron's station or the worker's desk, no one standard governs all situations.
Once the restroom has been roughly laid out by the architect, the details of the physical dimensions can be finalized. The wall panels that surround the water closets come in fixed dimensions in increments of two inches. Both the minimum width of the cubicles and the recommended width are also defined by architectural standards. Space should be provided outside of the cubicles for movement and to prevent the patron from becoming trapped at one end of a long narrow corridor.
In 1990, Congress passed the Americans with Disabilities Act (ADA), which mandated requirements to provide restroom facilities for those of us who use a wheelchair or have to use other assistance for walking. Access, grab rails, toilet and sink fixtures are
< previous page |
page_187 |
next page > |

< previous page |
page_188 |
next page > |
Page 188
Figure 11-1.
Height from floor to surface for water closets and sinks. Reprinted from Step by Step Guide Book on Home Plumbing with permission of Step By Step Guide Book Co., West Valley City, Utah.
required to accommodate the handicapped under the ADA requirements. For more information about the ADA, see Interiors Management: A Guide For Facility Managers by Maggie Smith and Safety Management: A Guide For Facility Managers by Joseph Gustin, companion volumes in The Facilities Management Library.
Accessories - In most restroom facilities, the hand dryer is located on a wall at least 8 ft. from the sink. This way, it is physically impossible to touch the sink and the electric dryer element at the same time, reducing the potential for electric shock and reducing the requirement for power and plumbing to be in the same wall.
In women's restrooms, in addition to the paper towel dispenser a sanitary napkin dispenser is provided and restocked by the cleaning personnel.
On urinals, an infrared position sensor can be fitted. The urinal will automatically flush when the user steps away from the fixture.
< previous page |
page_188 |
next page > |

< previous page |
page_189 |
next page > |
Page 189
The advantage of the infrared device is that it enhances cleanliness because the urinal is flushed each time it is used.
After the decisions have been made about the number of water closets and sinks, decisions should be made about a few other human factors as well. In many areas, a mirror is placed in front of the sink for people who wish to check their appearance after washing. The mirror has to be placed strategically. Many is the facility manager who is embarrassed when discovering that other restroom patrons can clearly be seen relieving themselves by looking at the mirror on the restroom wall!
Lighting is a factor to consider carefully. Lighting should be placed over the mirrors and over the water closets as well. In some facilities, the architect, to save lighting costs, provides light fixtures over the general area and at the sinks, but nothing over the water closets. This mistake leads to dark cubicles around the water closets and prevents the housekeeping staff from seeing clearly enough to assure complete cleaning. This in turn creates doubt about the cleanliness of the water closet, and in general reflects poorly upon the entire complex.
While the extra lighting is a little more costly, it is well worth the expense in cleanliness and the resulting positive attitude it reflects upon the restroom and hence the manager of the facility.
Construction Materials - The walls and floor should be made of water-resistant material that is readily cleaned and does not allow for growth of molds or stains. Ceramic tile has been one of the more attractive choices for the past 50 years. Tile, if it is kept clean and maintained, will last a long time, up to 100 years, and certainly outlasts the life of the facility. Flooring can be ceramic tile as well however, floor tiles usually have sand or other granular material embedded in it to prevent slips and falls. Clay tiles work well along with vinyl flooring. The sink counter tops can be tile or Formica.
Color of the tiles, flooring and ceiling is usually coordinated. A good designer or contractor will prepare a color board for the owner. Here, instead of just passing out a chain with color chips for selection, a board is prepared that shows the different types of tiles, flooring, wall panels, soap, towel and paper dispenser. The owner/ facility manager can look over the combinations of colors and textures and make selections based upon the known color chips and tile components. In restrooms, light colors work best because they reflect light and reveal stains. This allows easy inspection for cleanliness. Black, dark brown or dark gray colors should be avoided.
< previous page |
page_189 |
next page > |
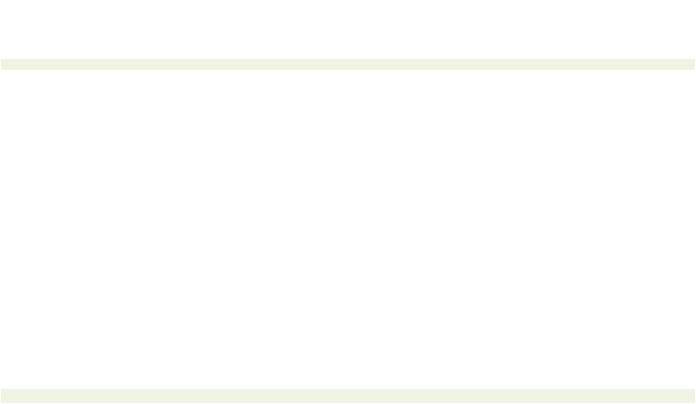
< previous page |
page_190 |
next page > |
Page 190
Since the plumbing and vent lines are in the walls, a cleanout should be located in a readily accessible spot, and depending upon the frequency of cleaning, a floor drain might not be a bad idea.
Finally, the facility manager has to work with the architect to decide if the restroom will be on an outside wall. The advantage is for windows and exhaust fans or ducts to be located on the outside wall with a reduction in the amount of air conditioning ducts required. Bathrooms, restrooms and other bathing facilities need a greater exchange of air than rooms like sleeping rooms or offices. The increased air vents noxious fumes associated with restroom facilities. Needless to say, the outside wall that has a fan in it directly to the outside should not be over the business front sidewalk or an outside eating, picnic or rest area.
If a window is used in a bathroom with an outside wall, the glass should be frosted, of course, and only on upper floors. Open windows provide viewing by casual observers. If windows are not provided, emergency lighting should be installed somewhere inside the restroom since, if the power is lost, restrooms without windows become quite dark. The lighting can be a plug-in unit or the light fixtures themselves can have batteries inside them that take over and provide minimal light when the power fails.
Figure 11-2 shows a layout of a restroom fitted with sinks, counter tops, mirrors and lighting.
Kitchens
There are many similarities between construction of restrooms and kitchens, but there are also some large differences. Since the kitchen is the center of a facility for food preparation, its design varies from bathrooms. Most of the water management facilities are essentially the same.
Both hot and cold water supplies are plumbed into the kitchen for washing and preparing food. Drains are provided to carry waste away. In addition, kitchens have heating equipment, such as ovens, grills and stoves for cooking the various dishes. Finally, there is a dishwasher or other types of equipment items for washing and cleaning the dishes themselves. Provision is made for cold storage of foods in the form of a refrigerator or even a walk-in cold storage room.
Central elements of design in a kitchen are the use of non-combustible materials in construction of the shelves, counters, furniture and the use of ceramic or stainless steel to aid in cleaning and sterilizing the food preparation surfaces.
< previous page |
page_190 |
next page > |

< previous page |
page_191 |
next page > |
Page 191
Water is never used over grills, fat fryers or barbecues as water dumped on these types of cooking devices will cause injury from splashing hot grease. Fire protection for grills is a dry chemical system that dumps a coating over the burning material and smothers any fire.
Figure 11-2.
A typical restroom layout.
Water fixtures used for cleaning include large, deep sinks for washing pots or pans too large for the dishwasher, and wide shallow sinks for cleaning vegetables and fruits.
The dishwasher is usually integral with the countertops in the area reserved for cleaning dirty dishes and a warm water nozzle is piped over-head for general overall spray and washdown. A large garbage disposer grinds garbage, allowing it to wash down into the sewer system. Most restaurants will have a grease trap in the drain line designed specifically to capture grease which will solidify when combined with the cooler water in the main sewer line (see Figure 11-3).
The grease trap is usually located near the facility, but it is not in the kitchen because cleaning a grease trap is a dirty, messy operation and it cannot be done while meals are being prepared.
Dishwasher - A dishwasher for a large facility is usually hard plumbed into the kitchen. It is supplied with either hot and cold water or it has its own heating unit which heats cold water directly and uses it in the wash cycles. Commercial dishwashers also have a large garbage disposer integral with the drain for grinding any leftover food materials or other small items.
Other types of water management devices found in or near kitchens include a mop sink. A mop sink is a large square sink that mounts on the floor in a janitor closet. The sink has a drain and a plug. The mop can be rinsed easily in the mop sink without having to spill from the wet mop onto the floor (see Figure 3-1 1).
< previous page |
page_191 |
next page > |
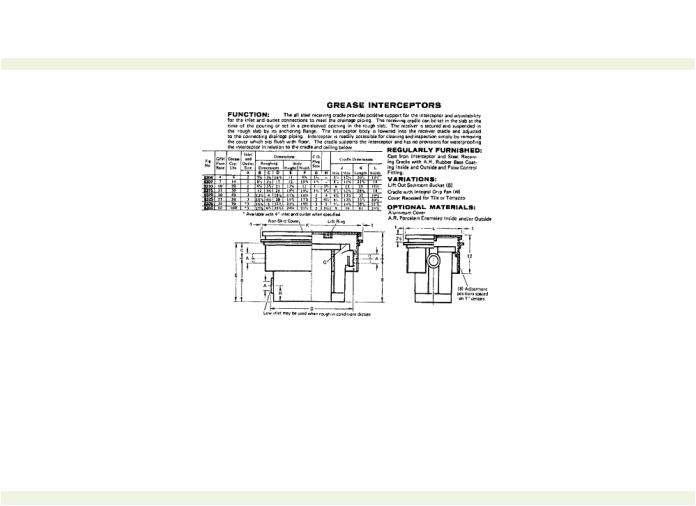
< previous page |
page_192 |
next page > |
Page 192
Figure 11-3.
A grease trap. Courtesy: J.R. Smith Co., 1995.
Construction Materials - The construction materials used in kitchens are designed to be compatible with the use. Usually, because of the large amounts of heating elements and flame sources, construction materials in kitchens are non-flammable. Non-flammable materials include stainless steel, porcelain, ceramic tile and clay tiles. Wood is sometimes used for cutting boards and counters because of its non-slip quality while cutting and food preparation activities take place. The wood is left unfinished, since paints and stains should not come into contact with foods. Occasionally, plastics such as Formica or vinyl tile are used but do not provide the service life of metals and tile. The floor is clay tile with a non-slip finish, but vinyl and Formica floor tiles can also be used. Walls are block, tile or sheetrock. Sheetrock walls can be punctured and if so, punctured sheetrock walls become a source of potential disease and can result in health department fines.
The ceiling should be solid with surface mount light fixtures. T-grid or drop ceilings should not be used in kitchen areas as dust from this type of ceiling can affect the food preparation. Recessed fixtures will result in dust that can settle on food products when the bulbs in the fixtures are changed. In all, devices should be selected
< previous page |
page_192 |
next page > |

< previous page |
page_193 |
next page > |
Page 193
that are smooth and water resistant and that can be washed with wet soapy solutions.
Ventilation - As with bathrooms, kitchens should be well-ventilated to carry away smoke and odors from cooking and humidity from dishwashing, cleaning and washing down. Grills should be ventilated as well to carry away cooking fumes.
Mechanical Room
A mechanical room in a facility has limited access, usually only by staff and sometimes only special persons on the staff. As such, mechanical rooms are kept locked and are keyed only to those staff who need to have access to the rooms. Mechanical rooms will contain water treatment equipment (Chapter 10); heating, ventilating and air conditioning equipment; solar or hot water heating equipment (Chapter 6); boilers; hot water tanks; pumps; air compressors; and/or fire protection equipment.
A mechanical room, since it is not used by the public, needs not be architecturally fancy. Usually, a simple concrete floor, unfinished walls of block or sheet rock, open joist or beam ceilings and light fixtures to illuminate any maintenance activity are all that are provided. A mechanical room will have floor drains and some mechanical rooms will have dikes on the floor around the various pieces of equipment to keep a spill from one item from going onto another item. The floor, usually of plain concrete, will be sloped to the floor drains to aid in speeding draining. And depending upon the equipment in the room, a hose bib and hose will be provided to wash down and rinse equipment that has been serviced.
Mechanical rooms sometimes will be insulated to prevent noise from the mechanical equipment from spreading throughout the building. Insulation can be sprayed, batts or loose. However, if the insulation is not compatible with water used in the room, it should be covered to prevent moisture from water and wash down operations from saturating the insulation.
Swimming and Bathing Pools
Perhaps nowhere in the world does water and a facility come together more beautifully and functionally than at a large outdoor pool or combination swimming and bathing facility (see Figure 11 -4). Here, the combination of cool sparkling water; ramps, walkways, and grassy areas; and people of all sizes, ages, and colors combines for pleasure, peace, comfort, exercise and recreation.
< previous page |
page_193 |
next page > |

< previous page |
page_194 |
next page > |
Page 194
Figure 11-4.
A large outdoor pool complex, a center of fun, relaxation and recreation.
The plumbing and piping details for pools are discussed in Chapters 3 and 4, and water chemistry and treatment are covered in Chapters 8 and 10. In this segment, the details of water/people interface are discussed.
Fence - A swimming pool is designed to be attractive. The plaster, vinyl or tile pool lining is a light blue or green aquamarine color that has been carefully chosen and selected to provide an image of safe, warm bathing. This design is intended to entice the user into the water for pleasure, health and relaxation. This expectation will be realized for adults.
Every summer, it seems, however, a small child inadvertently gets into somebody's backyard pool and drowns. After many lawsuits, a legal precedent has determined the presence of a pool as an ''attractive nuisance." This means that a normal person is enticed into the pool by its presence. Because of the attractive nuisance interpretation, the codes require that a barrier be erected about the pool to protect somebody idly passing by from being attracted into the pool to their own injury.
Most codes define the that a pool must be fenced. The fence
< previous page |
page_194 |
next page > |