
water quality and system
.pdf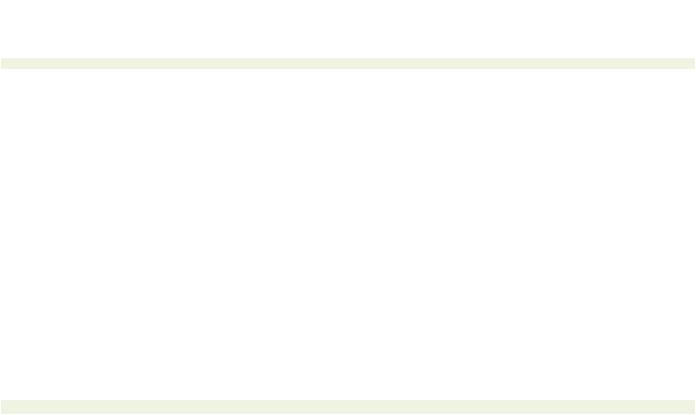
< previous page |
page_225 |
next page > |
Page 225
the time to perform the job. If the job takes six months to perform, the facility can pay 1/6 of the job each month.
Finally, contract payment can be based on a portion of the work completed as shown by the progress curve in Figure 12-2 earlier in this chapter. If the progress curve indicates that 25 percent of the work is complete, and this percentage is confirmed by field inspector reports, then payment of 25 percent of the job can be made. Use of the progress curve for payment and job tracking has many sophisticated uses for payment and performance as well.
As shown in the attached figure, the contractor's performance fee could be based upon how well he follows the curve. If he exceeds the curve by good performance, he might be offered a bonus, and if his progress lags behind the curve, perhaps additional funding should be retained as an incentive to accelerate.
Shop Inspection
Perhaps pipe is being fabricated in a shop, or one of the equipment items such as a large water softener is being put together at a factory. In these cases, if the facility manager has elected to make a partial payment to the contractor for this type of work, the facility should arrange to have it inspected at the factory or shop. In addition, the inspector should verify the materials are slated for the facility manager's jobsite.
More than once, a contractor has been tempted by an urgent order from another project to ship the equipment to a different direction. On one project, the U.S. Government urgently needed a large pump a subcontractor was putting together for another job. It was shipped to the government job much to the facility manager's dismay. Later, the Government reimbursed the facility and the contractor for the delay. The Government need was that urgent.
This kind of incident is rare, but it can happen. The facility manager should exercise care to protect his funds and budget when making partial payments.
Bonds and Bonding
Bonds are a way of assuring the facility manager that the contractor will complete his work within the required budget and scope. The bond is, in effect, insurance that the contractor's work will be done. There are several types of bonds, but not every type of bond
< previous page |
page_225 |
next page > |

< previous page |
page_226 |
next page > |
Page 226
applies to every construction project. The bond costs the contractor money and ultimately, this cost is passed along to the facility in the contractor's proposal.
Before any discussion on bonds, the facility manager should know that a recent trend is to eliminate bonds in construction projects since many bonding companies fail to take over the project when it comes time to do so. In fact, on one project the bonding company hired the original contractor to complete the work! If the facility manager is confident that the contractor is honest, reliable and has the resources to get the job done, it may be worthwhile to eliminate bonding altogether.
For those facility managers who require bonds, the three main types of bonds are bid bonds, payment bonds and performance bonds.
Bid Bonds
In a bid bond, the contractor guarantees that he will complete the project for his bid price. The bid bond then accompanies the bid and is the contractor's ''deposit" that he will perform the work for the bid price, plus any changes, of course.
Bid bonds cost 5-10 percent of the bid price and are forfeited if the contractor fails to start work if his company is the low bidder. Bid bonds are often eliminated from the process, but the advantage of the bid bond is to keep the contractors from submitting courtesy or frivolous bids. It also encourages the contractor to keep from making mistakes since the bond can be held by the facility until mistake is proved and this ties up some capital the construction company could use on other projects.
Performance Bonds
A performance bond is a commitment by the bonding company that the contractor will perform the work of the contract. In contrast to a bid bond, which is a commitment to the bid, a performance bond is a commitment to the project or to the entire job. Usually, the performance bond is submitted after the bids and before the construction work starts. It is evidence that financial backing is present should the contractor fail in performance of the work.
Payment Bonds
A payment bond is a guarantee that the prime contractor will pay his subcontractors. On some contracts, the main (prime)
< previous page |
page_226 |
next page > |
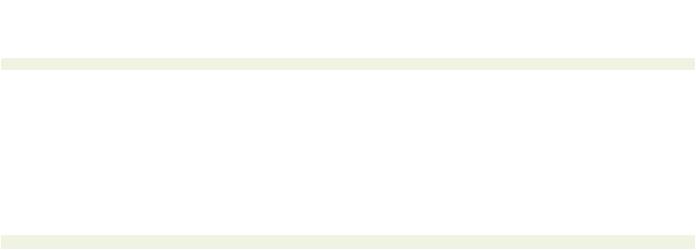
< previous page |
page_227 |
next page > |
Page 227
contractor bills the facility but then, for some reason, does not pay his subcontractors with that money. Under law, since the subcontractor's labor and materials are in the facility, the subcontractor has the right to sue the facility for payments he has not received from the prime contractor. The fact that the facility has paid someone else does not relieve the facility of the obligation to the subcontractor. Therefore, the payment bond is the prime contractor's guarantee that he will pay the subcontractors. For most facilities that use bonds, this is the most important bond to have on the job.
A Final Word About Bonds
Facility managers should realize that bonds and insurance are generally handled by attorneys and lawyers. And this text does not pretend to give the facility manager any legal advice. In the event decisions are made to include bonds or that bonds are in question, it is wise to seek the advice of counsel in this area.
Finally, the bulk of the work is complete, the crews are released and testing can begin.
< previous page |
page_227 |
next page > |
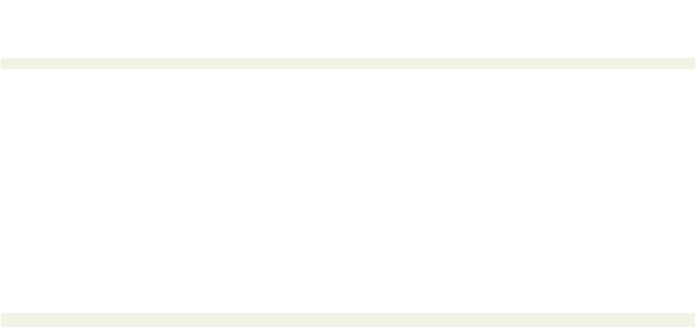
< previous page |
page_229 |
next page > |
Page 229
Chapter 13
Performance Testing
A successful construct/on project will include testing. The facility manager wants to hold the construction contractor responsible for testing since the contractor is installing the pipe and equipment. In addition, the facility will often conduct its own tests after maintenance work has been completed. Field testing ensures that the installed system operates as designed and intended.
Field Testing
The facility manager wants to be assured that the finished water system product performs as it is intended. For piping systems, there are two types of testspressure and flow tests. For equipment, the facility manager wants to make sure the system is tested to make sure that it does what it is intended to do. If the facility has a new water softener, it needs to be tested to verify that it removes the hardness, and that it removes the hardness from the specified amount of gallons before it has to be regenerated. Chlorinators, pumps, valves all need tests to make sure they work. In short, water systems, like other building systems, must be commissioned. Pressure Leakage Tests In Pipes
Pipelines that leak do not do anyone much good. Inside buildings, leaks will eventually be identified because the water will show up somewhere. Underground lines can leak, but the facility may never know it because the water drains underground to the water
< previous page |
page_229 |
next page > |

< previous page |
page_230 |
next page > |
Page 230
table. Leak tests make sure the system is free of leaks.
Usually, leak tests are a two-stage operation with a gross leak test performed to make sure all the equipment has been installed correctly and a design pressure test to make sure the pipes will hold design pressures.
To perform a leak test, pipelines are pumped up to test pressure with either air or water. The pressure is held for one, two or, for some systems, 24 hours. The pipe is then inspected for leaks and if no leaks are found, the test is accepted and the pipeline is complete.
Records of the test should be taken and signed by both the contractor and facility. The results of the tests are included with the final documents.
Pressure Test Methods And Safety - Pressure tests are most safely conducted with water. Air tests require the pipes to be pumped up using pressurized cylinders or air compressors and if the pipe fails during the test, expanding air can hurl pieces of the pipe in many directions. A water test does not cause this sudden expansion. On a large job, the contractor may do an initial leak test with air, looking for gross leaks in a large system, then go back and do a demonstration test for the facility manager with water. For a gross leakage test, the pipe is not pumped up to full pressure. Just a small portion of the test pressure is applied to confirm any gross leaks.
It is a good idea to use air for the gross leak test since gross leaks are fairly obvious. Most are the result of a valve not being closed, or a flange left out of place. On some pipe systems, the fittings may not have been tightened or perhaps one of the plumbers forgot to glue a joint together. If the gross test is done with water, this can cause a large mess that can be avoided by using air.
Once the contractor is satisfied that there are no major leaks, the pipe is then filled with water and pressurized to the design amount for the specified time. Often, a contractor is tempted to continue using the air pressure method since he has already set up the equipment. This decision should be up to the facility. The issue is whether to accept the risk of the air test, should it fail, versus the extra costs of setup for filling the pipes with water, pressure testing with water, and disposing of the water afterward. The decision depends upon the size of the pipe since it takes a small air compressor a long time to pump up a large pipe system.
A pressure test with air also requires the use of a soap bubble solution to look for small leaks where leaking water would be
< previous page |
page_230 |
next page > |

< previous page |
page_231 |
next page > |
Page 231
obvious. The other parameter to consider in deciding whether to test with air or water is obtaining the necessary water, and where to waste it after the tests have been run. If the drains are completed, the drains can be used.
Finally, with both air and water tests, inspectors can sometimes become confused if it is a long test because of atmospheric pressure and temperature changes throughout the day. These ambient changes will affect the test. If the pipe is filled with warm water on a hot day and later that night the pressure is read again, the pressure will have decreased slightly because of the cooler temperature of the water and the water contracting as it cools.
The American National Standards Institute has specified an amount of allowed pressure change as a function of temperature and volume. This information is sometimes included with the specifications. However, it becomes important if the pressure changes over a long timed test as to whether the thermometers have been calibrated correctly, and whether the volume in the pipes has been correctly calculated. All this kind of information can become confusing during the test and should be spelled out beforehand. The results should be included with the test report.
Of course, if the test fails, the facility manager should insist the entire test be repeated. The contractor, while locating and repairing a leak in one spot, may cause a leak at the next joint while fixing the first leak. If the test is not repeated, the facility manager would not know the pipe was leaking at the new location.
Furthermore, the manager should insist that the test be repeated until the system passes the test. On one job, a contractor performed the required test, identified the leaks and said that to fix the leaks was extra work, since a test was specified but passing the test was not a contract requirement.
One last thing about pressure tests. They are intended to be non-destructive tests. This means the facility does not want the contractor to break the pipes while testing them. However, the system should be tested enough until there is confidence the pipe will withstand the operating conditions. A test that does not represent true operational conditions is of little value.
Flow Tests
After the pressure tests, the contractor may be directed to conduct a flow test. Not only is it the intent of the pipeline not to leak, but the pipes should deliver the correct flow to the right locations. An obstruction in the pipe can limit the flow which, of course, is not
< previous page |
page_231 |
next page > |
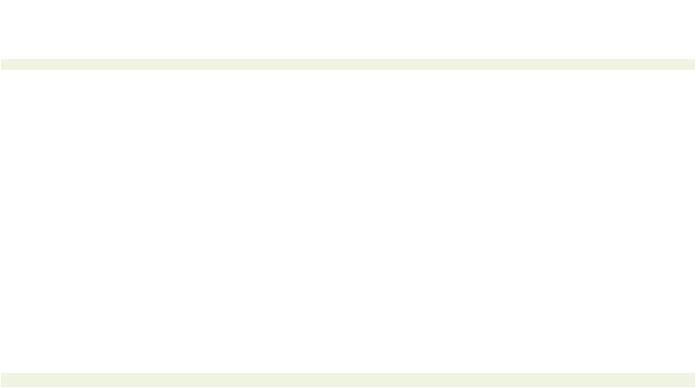
< previous page |
page_232 |
next page > |
Page 232
the intent of the pipe system. An excellent example of a flow test requirement is included in the National Fire Protection Association's Fire Sprinkler Codes.
Flushing lanes - The line should be flushed, then filled with clear water. The flow should be allowed to flow through the valves, or the pumps are turned on. Flushing the line is always a good idea since the author has seen rocks, gloves, welding rod, soda cans, sticks, weeds and a number of other types of debris come running out of a pipe while it is being flushed.
Setting Up The Flow Tests - Before flow tests can be conducted, a couple of items should be resolved. A decision should be made as to the disposal of water. If the water is treated and chlorinated, it may be necessary to reduce the free chlorine before disposing of the water since too much chlorine could affect fish or microorganisms in a nearby stream.
Since the flows are going to be measured during a flow test, the meters should be checked to make sure they will accurately record the correct amounts of flow. The tests should also be conducted with calibrated meters and the dates and records of the tests noted in the test reports. As always, a representative of the facility manager should witness the flow test.
Facility management staff should keep in mind that the test is conducted by the contractor and no action should be taken by the facility manager's staff during a test since a pipe failure resulting from action by the facility manager will result in extra payment to the contractor. Flow tests can sometimes be affected by the outside weather conditions, but not to the extent that pressure tests are affected. Since Chapter 4 presented a discussion of the relationship between flow and pressure, it will not be repeated here other than to say that the flow test is a measurement of system performance based upon theoretical calculations that are similar to the real flow conditions. If there are problems reaching the required flows, there is potentially an object in the pipe or air bubbles that are obstructing flows.
Failing The Test - If the system does not meet the required flows, the facility manager is faced with a classic dilemma faced by all facility managers involved in construction.
The installers will argue that the system was not designed correctly, and therefore the construction contractor cannot make the
< previous page |
page_232 |
next page > |

< previous page |
page_233 |
next page > |
Page 233
system perform as intended because the flaw is in the design, not in the construction. Therefore, the contractor has no obligation to the facility since the design was done by someone else who worked for the facility manager and hence, failing the test is not his fault.
The issue here is one of whether there is an object inside the pipe blocking the flow. First, the facility manager wants to consult with the designer. It may be that there is an error in the calculations or that the design assumptions were incorrect.
Keep in mind that even the most accurate of flow calculations are only within five percent of the true flow. Usually, the decision to select the "next larger size" or pipe diameters gives enough extra capacity so that this problem is solved in planning.
If the decision is reached that there is an object in the flow, the contractor is expected to locate and fix it. It is part of the job because the contractor has agreed to install a system that meets the flows. Use of an inspection camera may help to locate the problem (see Chapter 14).
Pump Tests
Pump tests can be conducted in conjunction with the overall flow test, or a loop can be installed simply for testing pump flows. The pump test should check the performance of the pump according to the curve data shown in Figure 3-4. Usually, a pump test seeks to verify the pump curve by measuring flows at three points and plotting the pump curve for the installation. The three points are connected and the curve is presented as the final pump curve for that system. The tested pump curve should be turned over to the facility and saved for future reference. If the facility has to be remodeled at some future date, the new designer can use the pump curve for design calculations.
Electric Motor Tests - In conjunction with the pump test, the electric motors are tested to confirm their performance in the installation.
Some facilities delete the high pot test since the wire insulation can be degraded by this type of test. For an existing facility, a high
< previous page |
page_233 |
next page > |
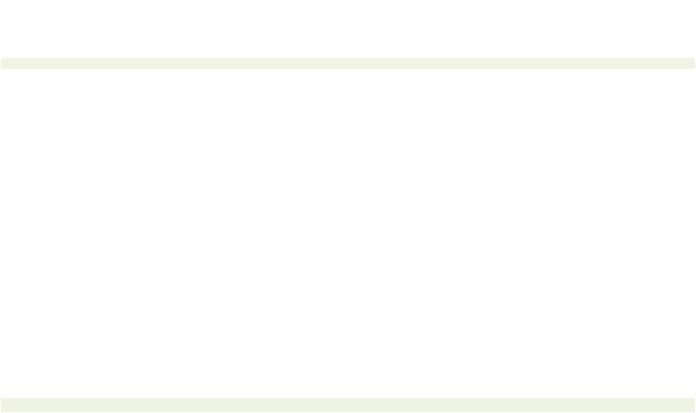
< previous page |
page_234 |
next page > |
Page 234
pot test carries some risk. The powerline could fail as a result of a shortage. If the line fails, it has to be replaced and the equipment is down while the power is being repaired. For a high pot test in an existing facility, the manager should have a backup plan in event the powerlines short out.
Next, the pump motor needs to be checked to make sure the coils are correctly wound and there has not been any damage in the motor windings. For this test, a meggering meter is used to measure the electrical resistance of the windings. Meggering is usually an excellent method to ensure the motor will perform as designed.
Electrical Safety - Water and electricity do not mix, so the facility manager must exercise caution when conducting power tests or risk harmful, and potentially fatal, electrical shock to personnel. In general, leaks should have been eliminated before the power tests are started but sometimes, and this is especially true in the case of pumps, a leak springs from the operating equipment during testing.
The best thing to do when a piece of electrical equipment gets wet it to turn it off immediately. Most pumps have an emergency stop switch and many types of equipment have an on/off button. Staff should be encouraged to take the safe course of action and shut the power off to the equipment whenever necessary.
It also helps to know the locations of the electrical circuit breakers in case the room where the emergency stop switches are flooded.
Equipment Tests
For most of the equipment mentioned in Chapter 10, the facility manager should conduct a test when it is first installed to make sure it is operating correctly.
Equipment tests are performed according to the standards by which they are purchased. If a water softener is supposed to make 6,000 gallons of soft water between regenerations, a test needs to be conducted to confirm that 6,000 gallons are produced before the water starts to get hard again. If the water softener is supposed to regenerate automatically, the facility manager should check this out as well.
Equipment tests should be specified in the contract and are the responsibility of the construction contractor. The facility manager
< previous page |
page_234 |
next page > |
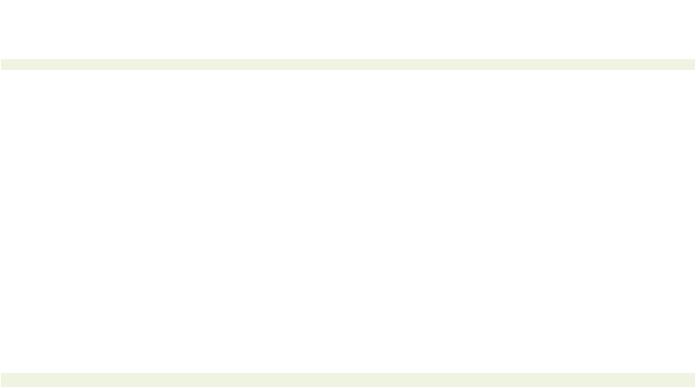
< previous page |
page_235 |
next page > |
Page 235
should be aware that the construction contractor will subcontract the purchase of a piece of equipment from a supplier. The supplier represents a manufacturer who designs and sells the equipment.
When an equipment test is conducted, the supplier usually has a representative of the manufacturer come out to the facility and conduct the test. The facility manager does not want to become entangled in any disputes between the various subcontractors, suppliers or middlemen but this may be unavoidable if there are problems with the equipment. Recalling the previous chapter's discussion on payment, the facility manager does not want to pay for equipment that does not work and consequently steps should be taken by the facility manager to assure that the tests are completed before the equipment is paid for.
Startups - When it comes to starting up new equipment, the facility manager benefits greatly from having his maintenance staff witness the performance tests. In this way, the maintenance personnel can meet with the manufacturer's representative and learn all they can in the short span of time available while the startup and performance tests are done.
In addition, most equipment comes from the factory with an operations and maintenance (O&M) manual which is turned over to the facility upon completion. This manual is the manufacturer's instruction manual on how to operate its equipment. Care should be taken with the O&M manuals because they are one of the most important pieces of information for operations personnel after the contractors and manufacturers representatives go home. The O&M provides valuable information in setting up a preventive maintenance program for the equipment (see Chapter 14).
It is also beneficial for the maintenance staff to be able to contact the manufacturer directly since spare parts or accessories will have to be purchased later on.
In most cases, equipment also has to be subjected to leak testing. Often, the manufacturer performs a leak test at the factory before shipping it, but sometimes during installation vessels and pipes get out of line and small leaks appear. These, of course, should be fixed before field testing.
Almost every piece of equipment has some type of control mechanism that makes the equipment self-regulating. The controls mean that staff only has to check on the equipment once in a while to make sure it is working correctly. The controls have to be set up
< previous page |
page_235 |
next page > |