
ТПУ май 2012
.pdfСписок литературы
1.Демидович Б.К. Пеностекло / Б. К. Демидович. − Минск: Наука и техника, 1975. 247 с.
2.Вакалова Т.В., Хабас Т.А., Эрдман С.В., Верещагин В.И. Практикум по основам технологии тугоплавких неметаллических и силикатных материалов. – Томск: Изд. ТПУ, 1999. 160 с.
ИССЛЕДОВАНИЕ ВОЗМОЖНОСТИ ИСПОЛЬЗОВАНИЯ СЫРЬЯ УРАЛЬСКОГО РЕГИОНА В СТЕКОЛЬНОМ ПРОИЗВОДСТВЕ
Альбаева И.И., Ковязина И.С., Лагунова Е.Ю., Саетова Н.С.
Уральский Федеральный университет имени первого Президента России Б.Н. Ельцина, г.Екатеринбург
В последнее время остро стоит проблема ресурсо- и энергосбережения. Любая отрасль промышленности заинтересована в том, чтобы получать высококачественный продукт при минимальных затратах.
Использование в стекольном производстве материалов Уральского региона позволит значительно сократить затраты на транспортировку материалов, и, следовательно, снизить себестоимость сырья не отразившись при этом на качестве конечного продукта.
Нами было взято 5 навесок с разным составом шихты: от необогащенного кварцевого песка до обогащенного с добавками осветлителя и обесцвечивателей. Варка производилась в силитовой печи в корундовых тиглях при температурах 1400 – 1500 °С в течение 6 часов, отлив – в металлические подогретые формы, затем отжиг в муфельной печи при 560-580 °С. Полученные стекла обладали неплохими варочными свойствами, не имели включений, не отличались повышенной тугоплавкостью.
Таблица. Характеристика сырьевых материалов месторождений Уральского региона (мас.%) представлена в таблице.
Сырье |
|
SiO2 |
Al2O3 |
CaO |
MgO |
Fe2O3 |
Na2O |
К2О |
TiO2 |
Необогащ. |
кварцевый |
96,16 |
1,42 |
0,29 |
0,07 |
0,71 |
0,15 |
0,25 |
0,24 |
песок, Каменское м/р |
|
|
|
|
|
|
|
|
|
Обогащенный песок |
98,52 |
0,61 |
0,17 |
0,04 |
0,19 |
0,05 |
0,14 |
0,05 |
|
Доломит Первоуральск |
1,50 |
1,00 |
33,60 |
18,20 |
0,20 |
|
|
|
|
Известняк Сосновское м/р |
0,70 |
1,03 |
54,20 |
0,80 |
0,12 |
0,07 |
0,07 |
0,05 |
|
ПШК Вишневогорск ГОК |
59,50 |
21,80 |
|
|
0,19 |
15,10 |
|
|
Все образцы светопрозрачны, но образец №1 обладает светопропусканием всего 83 %, имеет самый заметный зеленый оттенок, что связано с наличием Fe2O3 и примесей в песке. В образцах №2 и №3 светопропускание составляет 87 и 91 % соответственно. Образец №4, с добавлением осветлителя селитры, и образец №5, с добавкой селитры и оксида церия, обладают самым высоким светопропусканием 93 и 94 %, что удовлетворяет ГОСТ 111-90 (светопропускание стекол марок М3-М6 должно быть не меньше 85 %).
Использование местных сырьевых материалов поможет значительно ускорить производственный процесс, т.к. не нужно будет подолгу ждать подвода сырья и, конечно, снизит затраты на производственный процесс.
Поэтому мы предлагаем использовать указанное местное сырье в качестве шихты для изготовления листового стекла, тарного и других изделий, не требующих особо высокой степени чистоты исходных материалов.
При условии дальнейшего обогащения кварцевого песка можно рекомендовать получение из него термополированного (флоат) стекла.
ЭЛЕКТРОХИМИЧЕСКОЕ ОКИСЛЕНИЕ МЕДИ ПОД ДЕЙСТВИЕМ ПЕРЕМЕННОГО ТОКА ПРОМЫШЛЕННОЙ ЧАСТОТЫ
Андреева С.В., Лежнина М.И.
Национальный исследовательский Томский политехнический университет
Рассмотрено влияние состава и концентрации электролита на скорость электрохимического окисления металлической меди под действием переменного тока промышленной частоты.
Ранее была показана возможность электрохимического синтеза ряда оксидов металлов с помощью переменного тока промышленной частоты. Установлено, что наибольшее влияние на скорость процесса образования фазовых оксидов металлов оказывают следующие факторы: состав
61

и концентрация электролита, температура электролиза и плотность переменного тока [1–3]. Электрохимический синтез имеет ряд преимуществ перед известными технологиями. Во-первых, он позволяет получить нанопорошки высокой чистоты. Во-вторых, обеспечивает экологически чистое и практически безотходное производство [4].
В данной работе проводились исследования скорости разрушения меди при электролизе переменным током в растворах NH4NO3 и KCl. Эксперименты проводились при постоянной темпе-
ратуре (90оС) и плотности тока 1 А/см2, концентрация растворов электролитов изменялась от 3 до 25%. Скорость разрушения меди определялась по убыли массы электродов весовым методом [5]. По результатам экспериментов были получены следующие значения:
Таблица 1. Влияние природы и концентрации электролита на скорость разрушения меди при плотности тока 1 А/см2 и температуре 90 °С
Электролит |
|
Концентрация электролита, % мас. |
|
|
|
|||||
|
|
3 |
|
5 |
|
10 |
|
15 |
20 |
25 |
|
|
Скорость разрушения меди, г/см2∙ч |
|
|
|
|||||
KCl |
|
0,0 |
|
0,0 |
|
0,0 |
|
0,0 |
0,0 |
0,0 |
|
226 |
|
119 |
|
129 |
|
09 |
|
093 |
109 |
NH4NO3 |
|
0,0 |
|
0,0 |
|
0,0 |
|
0,0 |
0,0 |
0,0 |
|
062 |
|
218 |
|
922 |
|
233 |
|
143 |
624 |
По данным таблицы 1 была построена зависимость скорости разрушения меди от концентрации электролита при постоянной температуре и плотности тока представленная на рис. 1.
Рис. 1. Зависимость скорости разрушения меди от концентрации электролитов при постоянной
температуре (90 °С) и плотности тока (1 А/см2)
Из рис. 1 видно, что с ростом концентрации KCl в интервале 3–25% масс. скорость окисления меди уменьшается. Максимальная скорость окисления наблюдается в 3 %-ном растворе KCl, и
составляет 0,0226 г/см2∙ч. При использовании растворов нитрата аммония скорость разрушения меди в интервале 3 – 10% масс. возрастает, в интервале 10 – 20% минимальна, а затем вновь воз-
растает. Для раствора NH4NO3 максимальная скорость разрушения составила 0,0922 г/см2∙ч при 10 %-ной концентрации электролита.
Список литературы:
1.Коновалов Д.В., Коробочкин В.В., Ханова Е.А. Электрохимический синтез оксида цинка на переменном токе // Известия ТПУ. 2003. Т. 306. № 5. С. 67–71.
2.Коробочкин В.В., Косинцев В.И., Быстрицкий Л.Д., Ковалевский Е.П. Получение геля гидроксида алюминия электролизом на переменном токе // Неорганические материалы. 2002. Т. 38. № 9. С. 1087–1090.
3.Коробочкин В.В., Усольцева Н.В., Горлушко Д.А., Балмашнов М.А. Закономерности синтеза нанодисперсных оксидов меди электролизом на переменном токе в растворе щелочи // Известия ТПУ. 2010. Т. 317. № 3. С. 13–16.
4.Коробочкин В.В. Процессы получения нанодисперсных оксидов с использованием
62
электрохимического окисления металлов при действии переменного тока. Томский политехнический университет. Томск 2004. 273 с.
5. Ускоренные методы коррозионных испытаний. / Розенфельд И.Л., Жиганова К.А. М.: Металлургия, 1966. 347 с.
ИССЛЕДОВАНИЕ ВЛИЯНИЯ КОНЦЕНТРАЦИИ НИТРАТА АММОНИЯ И ПЛОТНОСТИ ТОКА НА ЭЛЕКТРОХИМИЧЕСКОЕ ОКИСЛЕНИЕ МЕДИ
Андреева С.В., студент Национальный исследовательский Томский политехнический университет
Рассмотрено влияние концентрации электролита на скорость электрохимического окисления металлической меди под действием переменного тока промышленной частоты.
Ранее была показана возможность электрохимического синтеза ряда оксидов металлов с помощью переменного тока промышленной частоты. Скорость разрушения металла зависит от химической природы образующихся на поверхности электрода оксидов. В результате протекания процесса часть образующегося оксида меди переходит в объем раствора электролита, а часть остается на поверхности электрода. Установлено, что наибольшее влияние на скорость процесса образования фазовых оксидов металлов оказывают следующие факторы: состав и концентрация электролита, температура электролиза и плотность переменного тока [1–3]. Электрохимический синтез имеет ряд преимуществ перед известными технологиями. Во-первых, он позволяет получить нанопорошки высокой чистоты. Во-вторых, обеспечивает экологически чистое и практически безотходное производство [4].
Изучение электрохимического окисления металлов с использованием переменного тока приобретает актуальность не только для синтеза чистых нанопорошков оксидов металлов, но и в связи с получением экспериментальных данных по коррозионной стойкости металлов под действием токов промышленной частоты. Коррозионная стойкость меди зависит от технологических условий ее производства (плавки и отливки), механической и термической обработки и наличия примесей. Использование переменного тока позволяет дополнительно упростить аппаратурное обеспечение процесса и снизить энергетические затраты на его проведение [5].
В данной работе проводились исследования скорости разрушения меди при электролизе переменным током в растворах NH4NO3. Исследования кинетики электрохимического синтеза оксидов меди с использованием переменного тока промышленной частоты проводились согласно методике, изложенной в [6]. Эксперименты проводились при постоянной температуре (90оС) и плотности тока 1 А/см2 и 2 А/см2 концентрация раствора электролита изменялась от 3 до 25%. Скорость разрушения меди определялась по убыли массы электродов весовым методом [7]. По результатам экспериментов были получены следующие значения:
Табл.1. Влияние концентрации электролита на скорость разрушения меди при различных плотностях тока и температуре 90 0С
Концентрация электро- |
|
|
|
|
|
|
|
|
|
лита NH4NO3, |
|
3% |
|
5% |
10% |
15% |
20% |
25% |
|
% масс. |
|
|
|
|
|
|
|
|
|
Скорость |
разрушения |
|
|
|
|
|
|
|
|
меди при плотности тока |
0,0062 |
|
0,0218 |
|
0,0785 |
0,0233 |
0,0143 |
0,0624 |
|
1 А/см2 , в г/см2∙ч |
|
|
|
|
|
|
|
|
|
Скорость |
разрушения |
|
|
|
|
|
|
|
|
меди при плотности тока |
0,0089 |
|
0,0284 |
|
0,2320 |
0,1808 |
0,0453 |
0,2017 |
|
2 А/см2, в г/см2∙ч |
|
|
|
|
|
|
|
|
По данным таблицы 1 была построена зависимость скорости разрушения меди от концентрации электролита при постоянной температуре и плотности тока (1 А/см2) представленная на рис.1.
63
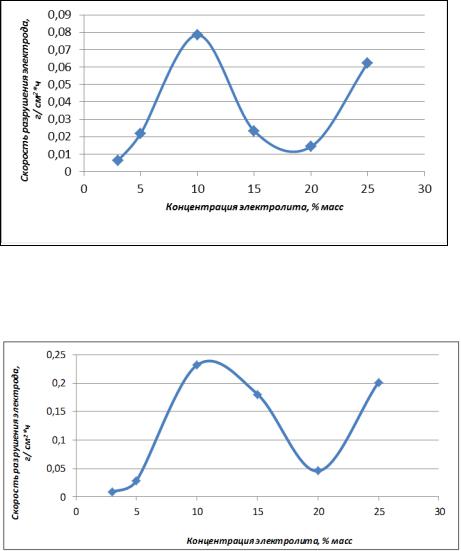
Рис.1. Зависимость скорости разрушения меди от концентрации NH4NO3 при постоянной температуре (900С) и плотности тока (1 А/см2)
Также по данным таблицы 1 была построена зависимость скорости разрушения меди от концентрации электролита при постоянной температуре и плотности тока (2 А/см2) представленная на рис.2.
Рис.2. Зависимость скорости разрушения меди от концентрации NH4NO3 при постоянной температуре (900С) и плотности тока (2 А/см2)
Из рис. 1 и 2 видно, при использовании растворов нитрата аммония скорость разрушения меди в интервале 3 – 10% масс. возрастает, в интервале 10 – 20% минимальна, а затем вновь возрастает. Анализ таблицы 1 показывает, что максимальное разрушение медных электродов под действием электрохимической коррозии происходит в растворах 10%-ной концентрации NH4NO3. Для плотности тока 1 А/см2 максимальная скорость разрушения составила 0,0785 г/см2∙ч, а для плотности тока 2 А/см2 максимальная скорость разрушения электродов составила 0,2320 г/см2∙ч. При использовании раствора нитрата аммония концентрацией 3%масс. и плотности тока 1 А/см2 скорость разрушения меди минимальна. Следовательно, минимальной коррозионной устойчивостью медь обладает в растворах 10%-ной концентрации NH4NO3 и при плотности тока 2 А/см2.
Список литературы:
1.Коновалов Д.В., Коробочкин В.В., Ханова Е.А. Электрохимический синтез оксида цинка на переменном токе // Известия ТПУ. – Томск, 2003. – Т. 306. – № 5. – С. 67–71.
2.Коробочкин В.В., Косинцев В.И., Быстрицкий Л.Д., Ковалевский Е.П. Получение геля гидроксида алюминия электролизом на переменном токе // Неорганические материалы. – 2002. – Т. 38. – № 9. – С. 1087–1090.
3.Коробочкин В.В., Усольцева Н.В., Горлушко Д.А., Балмашнов М.А. Закономерности синтеза нанодисперсных оксидов меди электролизом на переменном токе в растворе щелочи //Известия ТПУ. – 2010 – Т. 317. – № 3. – С. 13-16.
4.Коробочкин В.В. Процессы получения нанодисперсных оксидов с использованием электрохимического окисления металлов при действии переменного тока. Томский политехнический университет. Томск 2004. - 273л.
64
5.Богодяж Ю.Е., Репина Д.А. Коррозионная стойкость меди в растворах хлоридов при действии переменного тока //Химия и химическая технология в XXI веке: материалы XI Всероссийской научно-практической конференции студентов и аспирантов - Томск, ТПУ, 12-14 мая 2010.
-Томск: Изд. ТПУ, 2010 - т. 1. - c. 7-9
6.Коробочкин В.В., Ханова Е.А. Определение количества окисленных титана, кадмия и меди при электролизе на переменном токе // Заводская лаборатория. Диагностика материалов. – 2005. – Т.71. – №6. – С. 20–23.
7.Ускоренные методы коррозионных испытаний. / Розенфельд И.Л., Жиганова К.А. – М.: Металлургия, 1966. – 347 с.
МАТЕМАТИЧЕСКОЕ МОДЕЛИРОВАНИЕ АГЛОМЕРАЦИИ ФОСФОРИТНОЙ МЕЛОЧИ С ИСПОЛЬЗОВАНИЕМ КРЕМНЕЗЕМСОДЕРЖАЩИХ МАТЕРИАЛОВ
Атаханова Р.А., Тлеуова С.Т., Бестереков У. Южно-Казахстанский Государственный Университет им. М. Ауезова, г. Шымкент, Республика
Казахстан, 160000, rozochka_888@mail.ru
В процессе термической подготовки сырья до 20–25% товарного кускового фосфорита превращается в мелочь фракций 10–0 мм, которая является отходом. В отвалах фосфорных заводов юга Казахстана накоплено более 5 млн. т фосфоритной мелочи, при эффективной переработке которой возможно получение значительного количество желтого фосфора. При этом количество фосфоритной мелочи, вывозимой в отвалы, постоянно увеличивается в связи с недостаточной механической прочностью перерабатываемого кускового фосфорита. Накопленная фосфоритная мелочь по содержанию Р2О5 не уступает кондиционной руде и может стать основным сырьевым источником для фосфорных предприятий. Одним из эффективных методов переработки фосфоритной мелочи агломерация [1].
Один из главных показателей качества агломерата – его прочность, которая имеет важное значение как для процесса спекания, так и при переработке продукта в руднотермической печи. Низкая прочность агломерата приводит к росту количества возврата, увеличению энергетических, сырьевых и эксплуатационных расходов, то есть к ухудшению всех технико-экономических показателей аглопроцесса.
Прочность агломерата, зависящая от его вещественного состава и текстуры, определяется физико-химическими свойствами компонентов агломерируемой шихты и технологическими параметрами процесса.
Вещественный состав агломерата в основном определяется исходным составом минеральных компонентов аглошихты и отражает взаимодействие этих компонентов в процессе спекания при высокой температуре.
Для определения оптимальных технологических параметров агломерации и состава шихты, с использованием фосфоритной мелочи, кремнеземсодержащих материалов и коксовой мелочи нами выполнено математическое моделирование с использованием матрицы симплексрешетчатого метода планирования эксперимента по плану Шеффе [2], состоящим из шести экспериментальных точек. Для проведения линии задаваемого уровня расчеты были выполнены с использованием ПЭВМ.
На основании результатов проведенных экспериментов были рассчитаны уравнения регрессии, характеризующие зависимости показателей процесса спекания от составов агломерируемых шихт.
yC = 13,6 x1 –12x2 – 21x3 –0,8x1x2 –5,6x1x3 –0,8x2x3; |
(1) |
|
yQ = 0,43x1 – 0,55x2 – 0,31x3 –0.44x1x2 –1,48x1x3 –1,4x2x3; |
(2) |
|
y = 560x1 – 595x2 – 450x3 –10x1x2 –180x1x3 –50x2x3; |
(3) |
|
yR = 1,7x1 – 2,3x2 – 0,8x3 – 0,4x1x2 – 0,6x1x3 – 0,2x2x3, |
(4) |
|
где |
yC – вертикальная скорость спекания; yQ – удельная производительность агломе- |
рационной установки; y – насыпная плотность агломерата из фосфоритной мелочи; yR – прочность на сжатие в цилиндре агломерата.
Полученные уравнения позволяют оценить влияние первоначального состояния двух углеродсодержащих материалов на технологические свойства агломерации.
На основе анализа полученных результатов математического планирования экспериментов агломерации фосфоритной мелочи с добавкой фосфатно-глинисто-кремнистый сланец (ФГКС) и кремнеземсодержащего сырья установлены следующие оптимальные технологические параметры:
-удельная производительность 0,21 м3/м2час;
-вертикальная скорость спекания шихты 13-20 мм/мин;
-механическая прочность агломерата 1,5-2,5 мПа;
65
- насыпная плотность 500-540 кг/м3.
Список литературы:
1.Бержанов Д.С., Джусипбеков У.Д., Казова А.М., Турлыгазиев С. Химическая и термическая подготовка фосфоритного сырья для электротермии. Алматы: Гылым, 1997. 176 с.
2.Ахназаров С.Л., Кафаров В.В. Методы оптимизации экспериментов в химической технологии. М.: Высшая школа, 1985.
ТЕРМОПАРООБРАБОТКА КАК МЕТОД ПЕРЕРАБОТКИ ЦИНКОВЫХ КЕКОВ Ахтамов Ф.Э., Хамраев Р.Б., Адылова Н.А.
Навоийский государственный горный институт,п/и 210100, Узбекистан, Навоийская область, г.Навои, ул.Южная 27а, savollar@mail.ru
Цинковый кек – нерастворённый остаток после выщелачивания цинкового огарка, содержит
%: Zn – 18-23; Pb – 4,8-11,7; Cu – 0,25-1,28; Cd – 0,08-0,2; Ag – 170-425г/т; Fe – 23-32; Sобщ. – 4,7-10
[1]. Для доизвлечения цинка кеки подвергают вельцеванию (восстановительно-возгоночный обжиг) – при температуре 1000-1200 °С с добавкой кокса в количестве 35-45 % от массы перерабатываемого материала. При этом получают цинковые возгоны и клинкер – остаток от вельцевания, который содержит много ценных компонентов. Цинковые возгоны отправляются обратно на процесс сернокислотного выщелачивания.
Недостатками вельцпроцесса являются:
-большой расход кокса;
-необходимость высоких температур для прохождения процесса;
-нерешенность вопросов извлечения других ценных компонентов, таких, как Au, Ag, Pb, Cu, Fe и др. из-за отсутствия рациональной технологии переработки медного клинкера [2].
В связи с этим были проведены исследования возможности переработки цинковых кеков способом термопарообработки с последующим сернокислотным выщелачиванием огарка.
Эксперимент проводился в следующей последовательности: измельченный до крупностью - 0,074 мм цинковый кек массой 100 грамм подвергался сушке при температуре 105 °С до постоянного веса, после чего проба помещалась в трубчатую вращающуюся печь. Когда температура печи достигала 250 °С, в печь подавался сухой пар от парогенератора. После окончания эксперимента установку охлаждали, навеску извлекали и взвешивали, определяя разницу между исходной и конечной массой. Обработанный таким образом продукт далее подвергался гидрометаллургической переработке. Одним из наиболее эффективных способов переработки термопарообработанного цинкового кека является выщелачивание сернокислыми растворами в заводских условиях. В ходе эксперимента все продукты подвергались химическому анализу. Результаты эксперимента приведены в табл. 1.
Условия опытов:
термопарообработка: t=500 °С, обработки=1 час, скорость подачи водяного пара 15-20 мл/мин,
гогарка=92%;
выщелачивание: СH2SO4=100 г/л, т:ж=1:8, выщелачивание=1 ч, t=60-70 °C, гкека=66%.
Таблица 1. Результаты прямого сернокислотного выщелачивания термопарообработанного цинкового кека.
Название |
Содержание в |
Содержание |
в |
Содержание в кеке после сер- |
Степень |
извле- |
|
нокислотного выщелачивания, |
чения в |
рас- |
|||||
металла. |
огарке, %. |
растворе, г/л. |
|
||||
|
%. |
твор, %. |
|
||||
|
|
|
|
|
|||
Zn |
22,2 |
21,3 |
|
7,8 |
76,6 |
||
Cu |
2,79 |
2,27 |
|
1,46 |
65,2 |
||
Pb |
4,47 |
0,0015 |
|
6,74 |
<1 |
|
|
Fe+2 |
1,19 |
следы |
|
1,8 |
- |
|
|
Fe+3 |
19,8 |
5,29 |
|
23,58 |
21,37 |
||
Au |
1,09 |
следы |
|
1,65** |
- |
|
|
Ag |
220,7 |
12,3* |
|
235,7** |
22,39 |
*Примечание: содержание Ag в растворе в мг/л.
**Примечание: содержание Au и Ag в кеке в г/т.
Предварительные результаты исследования свидетельствуют о возможности эффективной переработки цинковых кеков с последующим сернокислотным выщелачиванием. Достаточное
66
содержание золота и серебра в кеках выщелачивания даёт возможность извлекать благородные металлы.
Список литературы:
1. Лакерник М.М., Пахомова Г.Н. Металлургия цинка и кадмия. – М.: Металлургия, 1969.
275 с.
2. Ахтамов Ф.Э., Абдурахмонов С.А., Хужакулов Н.Б. // Научно-технический журн. «Горный вестник Узбекистана». 2009. Вып. 1. С. 77–78.
ТЕРМОДИНАМИЧЕСКОЕ МОДЕЛИРОВАНИЕ ХЛОРИРОВАНИЯ ОКСИДА УРАНА ХЛОРУГЛЕВОДОРОДАМИ
Байбосынов Ж.Ж., Родина Н. Южно-Казахстанский государтвенный университет
имени М. Ауезова, г. Шымкент, Республика Казахстан, 160000, zhubandyk-1209@mail.ru
Производство урана в настоящее время предусматривает в качестве промежуточной стадии получение фторидов урана посредствам взаимодействия диоксида урана с плавиковой кислотой, затем фториды урана подвергают металлотермическому восстановлению кальцием или магнием. Для уменьшения себестоимости получения промежуточных соединений урана необходимо увеличить скорость образования этих соединений. В этой связи актуальным является получение более дешевого хлорида урана, что возможно на основе хлоридовозгоночного метода. Несмотря на возможность получения тетрахлорида урана с использованием элементарного хлора, четыреххлористого углерода, этот метод имеет недостатки, основным из которых является высокая стоимость хлорагентов, что обуславливается высокой себестоимостью получения металлического урана. Поэтому необходим поиск более дешевых хлорирующих отходов для производства тетрахлорида урана.
В данной статье приведены результаты термодинамических исследований возможности окисления хлоруглеводородов с выделением элементарного хлора для непосредственного хлорирования диоксида урана. Для определения теоретических закономерностей возможности хлорирования оксида урана хлоруглеводородными соединениями использована программа «АСТРА-4», на основе энтропийного метода. Теоретические закономерности возможности хлорирования оксида урана рабочей системы UO2–C12H4Cl4–5O2 изучали в температурном в интервале 1000-2000К по предполагаемой реакции:
UO2 + C12H4Cl4 + 12O2 = UCl4 + 12CO2 + 2H2O
Равновесное распределение урана исследуемой системе характеризуется образованием таких соединений, как UCl2, UCl4, UCl3, UCl5 в интервале температур 700-2000К, конденсированный UO2 изменяется от 99,99% до 94,33%. В этом интервале температур 1300-2000К идет образование UCI3 от 0,00036 до 1,081%. UCI4 в интервале температур 1000-2000К увеличивается его образование до 4,37%.
Равновесное распределение углерода характеризуется конденсированным углеродом, образованным при Т=700К в количестве 49,49%, который заметно уменьшается до 1,07% при Т=1200К. Образование СО резко увеличивается в интервале температур 700К-1300К от 1,01% до 99,3%. Уменьшение образования СО2 от 49,49% до 5,49% наблюдается в интервале температур 7001100К, а в интервале 1200-2000К плавное уменьшение СО2 от 1,36 до 0,84%. В интервале температур 700-2000К так же идет попутное образование некоторых соединений углерода, как СН4 при Т=1200-1300К от 1,05 до 1,41%; СНО при Т=2000К до 1,33%; С1СО при Т=2000К от 0,36 до2,06% (Таб. 1).
Анологично изучены равновесное распределение хлора и кислорода по элементам и соединениям в исследуемом интервале температур, которые характеризуются максимальным образованием Н2-99% при Т=700К и СО2-85,20% при Т=1300К.
Таблица №1. Равновесное распределение урана и углерода
Соеди- |
Распределение урана Т,К |
|
|
|
|
|
|
|
|
|||
нения |
|
|
|
|
|
|
|
|
||||
|
|
|
|
|
|
|
|
|
|
|
|
|
|
1000 |
1100 |
1200 |
|
1300 |
1400 |
1500 |
1600 |
1700 |
1800 |
1900 |
2000 |
UCl2 |
0 |
0 |
0 |
|
0 |
0 |
0 |
0 |
0 |
0 |
0 |
0 |
UO2 |
0 |
0 |
0 |
|
0 |
0 |
0 |
0 |
0 |
0 |
0 |
0,0002 |
k·UO2 |
99,8 |
99,43 |
98,19 |
|
96,32 |
95,95 |
95,59 |
95,27 |
94,97 |
94,7 |
94,5 |
94,4 |
67
UO3 |
0 |
0 |
|
0 |
|
0 |
|
0 |
|
|
0 |
|
0 |
|
0 |
|
0 |
|
0 |
0,0003 |
UCl3 |
0 |
0 |
|
0 |
|
0,0005 |
|
0,002 |
|
|
0,007 |
|
0,02 |
|
0,05 |
|
0,1 |
|
0,2 |
0,4 |
UCl4 |
0,17 |
0,56 |
|
1,8 |
|
3,67 |
|
4,04 |
|
|
4,39 |
|
4,7 |
|
4,97 |
|
5,16 |
|
5,2 |
5,14 |
UCl5 |
0,0002 |
0,0003 |
|
0,0006 |
|
0,0009 |
|
0,0009 |
|
0,001 |
|
0,001 |
|
0,001 |
|
0,001 |
|
0,001 |
0,001 |
|
|
|
|
Распределение углерода Т,К |
|
|
|
|
|
|
|
|
|
|
|
||||||
k·C |
19,04 |
5,407 |
|
1,07 |
|
0 |
0 |
|
0 |
0 |
0 |
|
0 |
|
0 |
0 |
||||
CO |
61,88 |
89,09 |
|
97,56 |
|
99,39 |
99,33 |
|
99,28 |
99,23 |
99,18 |
|
99,15 |
|
99,13 |
99,12 |
||||
CO2 |
19,06 |
5,49 |
|
1,36 |
|
0,602 |
0,66 |
|
0,716 |
0,766 |
0,81 |
|
0,84 |
|
0,86 |
0,878 |
||||
CHO |
0 |
0 |
|
0 |
|
0 |
0 |
|
0 |
0 |
0 |
|
0 |
|
0 |
0 |
||||
ClCO |
0 |
0 |
|
0 |
|
0 |
0 |
|
0 |
0 |
0 |
|
0 |
|
0 |
0 |
||||
CH4 |
0 |
0 |
|
0 |
|
0 |
0 |
|
0 |
0 |
0 |
|
0 |
|
0 |
0 |
Таким образом результаты термодинамического моделирования системы UO2–C12H4Cl4– 5O2. в интервале 1000-2000К характеризуется максимальным образованием UCI4 до 5,23% при Т=1900К.
Список литературы:
1.Шевченко В.Б., Судариков Б.Н. // Технология урана М., 1984.
2.Самсонов Д.П., Кирюхин В.П., Кирюхина Н.П., Первунина Р.И. определение содержания полихлорированных дибензо-п-диоксинов, дибензофуранов, бифенилов и полиароматических соединений в продуктах сгорания твердого ракетного топливо // Журн. аналит. химии. 1996. Т. 51.
№11. С. 1218–1221.
ПЛАЗМОХИМИЧЕСКАЯ ОБРАБОТКА УГЛЕРОДНЫХ НАНОТРУБОК ДЛЯ УЛУЧШЕНИЯ ИХ СВОЙСТВ
Балыков Д.В., Бервено А.В., Бервено В.П., Пенцак Е.О. Кемеровский государственный университет, г. Кемерово
Благодаря широкому спектру демонстрируемых свойств, углеродные нанотрубки (УНТ) применяются в микро- и наноэлектронике (полевые транзисторы, электронные схемы, дисплеи, автокатоды), приборостроении (сканирующие туннельные или атомные силовые микроскопы, вакуумная и сорбционная техника, фильтры), материаловедении (сорбенты, гетероструктуры), медицине, композиционных материалах и других перспективных областях науки и техники.
Предлагаемая разработка направлена на создание новой технологии плазмохимической модификации однослойных и многослойных углеродных нанотрубок (УНТ) путём их функционализации кислородом для целенаправленного изменения свойств УНТ и расширения областей их применения в промышленных масштабах.
Для улучшения свойств УНТ необходимо раскрыть (срезать верхнюю часть) УНТ путём удаления их «крышечек», функционализировать поверхность УНТ различными группами. Это достигается высокотемпературным нагревом (600-850°С) в потоке углекислого газа, в результате чего около 10% всех УНТ оказываются открытыми. Раскрыть 80% из всех УНТ можно путём выдерживания УНТ в течении 4,5 часов в азотной кислоте при температуре 240°С. Были попытки и механического удаления «крышечек», которые не привели к успеху.
Эти методы являются достаточно энергозатратными и трудно масштабируемыми. Недостатков лишён метод плазмохимической обработки УНТ при низкой температуре (70-120°С), разрабатываемый в лаборатории углеродных наноструктурированных материалов Института углехимии и химического материаловедения СО РАН, при участии магистрантов и студентов химического факультета Кемеровского государственного университета.
Общемировая потребность в нанотрубках в 2010 году оценена в 10 тысяч тонн. Их производит более 40 компаний. Немецкая Bayer планирует к 2012 году расширить производственные мощности до 3000 т/г, французская Arkema имеет завод с годовой производительностью 400 т, китайская CNano — 500 т/г, а бельгийская Nanocyl — 400 т/г. До 500 т/г увеличивает производство углеродных нановолокон японская Showa Denko. Согласно аналитическому отчету, опубликованному в апреле 2011 года компанией MarketsandMarkets, рынок нанотрубок в 2016 году достигнет $3,3 млрд, а его ежегодный рост — 12,4%. [Э.Раков, д.х.н, зав.каф. нанотехнологии и наноматериалов РХТУ им. Д.И. Менделеева, Журнал "Коммерсантъ Наука", №4 (4), 25.07.2011]
68
Заказчиками и потребителями выступают компании, работающие в области медицины, электроники, строительства, машиностроения - НТЦ «Гранат», «НаноТехЦентр», Холдинг Композит, ОАО "Энергия", Центр автоэмиссионных технологий, РКК Энергия им. Королева (имеются договоренности) и ещё около 90 компаний РФ, занимающиеся получением и/или применением УНЧ.
Прибыль проекта будет формироваться от продаж: установок плазмохимической активации УНТ, партий УНТ обработанных в плазме, оказанию услуг по исследованию свойств УНТ используемыми методами, оказанию услуг по активации УНТ.
Уникальные преимущества метода и его продуктов: энергетически выгодный, низкотемпературный метод активации УНТ (Т=70-120°С, у конкурентов 600-850°С), легко масштабируемый, экологически чистый, использование дешевых окислителей – газов, постоянство свойств УНТ после обработки (благодаря конструкции вращающегося реактора), доказанная эффективность обработанных УНТ (по сравнению с исходными), безопасность персонала (не используются высокие температуры и смеси кислот).
Личный вклад и оценка личностных качеств Балыков Данил Вениаминович – лаборант-исследователь, автор проекта, информационный
поиск, участие в разработке методики плазмохимической функционализации УНТ, осуществление экспериментальной работы и анализа, тестовые испытания образцов.
Активно участвовал в создании инновационного предприятия ООО «Сорбенты Кузбасса» специализирующегося в области углеродных сорбентов.
ТИОКАРБАМИДНОЕ ВЫЩЕЛАЧИВАНИЕ ЗОЛОТА ИЗ УПОРНЫХ ЗОЛОТОМЫШЬЯКОВЫХ РУД МЕСТОРОЖДЕНИЯ ИШТАМБЕРДЫ (КР)
Баткибекова М.Б. , Джунушалиева Т.Ш. , Борбиева Д.Б., Сыдыкова Ш.С. , Жамангулова Г.А.
Кыргызского государственного технического университета им. И. Раззакова, г. Бишкек
Золотосодержащие руды разведанных месторождений Кыргызстана весьма разнообразны по минеральному составу. В эксплуатацию вовлекаются руды со все более низким содержанием золота и более сложные по вещественному составу, который иногда значительно изменяется качественно и количественно в пределах одного месторождения.
Основным фактором, определяющим технологическую сложность или "упорность" золотосодержащего сырья является наличие в рудах тонко- и дисперсно вкрапленного золота в сульфидах, из которых прямым цианированием оно практически не извлекается [1-2]. Переработка труднообогатимого мышьяксодержащего сырья влечет за собой необходимость решения проблем удаления, обезвреживания, захоронения или использования мышьяка.
Цель работы – извлечение золота из упорных золотомышьяксодержащих руд тиокарбамидным выщелачиванием после удаления мышьяка.
Общая характеристика объекта исследования - упорных руд месторождения Иштамберды. Ведущий минеральный тип – золото – пирит – арсенопиритовый. Промышленный компонент - золото, его содержание в пробах – 11,2 – 15,6 г/т., попутный – серебро (до 27 г/т). Имеется самородное золото – 20%. Компонентом, осложняющим технологию переработки руд, является мышьяк (0,6%). Процессы цианирования и гравитационные к данной руде неприемлемы.
Экспериментальная часть. Тиокарбамидное выщелачивание золота из концентратов упорных золотомышьяксодержащих руд Иштамберды (КР) [3]. Тиокарбамидное выщелачивание золота проводилось из средних проб концентратов золотомышьяковых руд месторождения Иштамберды после удаления из них мышьяка методами окислительного обжига, кислотного и щелочного разложения по схеме: отобранные пробы концентрата после удаления из них мышьяка были тщательно растерты в агатовой ступке в просеяны через сито (0,068 мм), перенесены в эксикаторы и залиты Х%-раствором H2SO4 в соотношении Т:Ж = 1:5 (для растворения двухвалентных металлов Ca, Mg, Sr, и т.д. и перевода их в раствор), после энергичного перемешивания (2 ч) были оставлены на сутки. Смесь проб с серной кислотой была отфильтрована через воронку Бюхнера и промыта 2-3 раза водой. Осадки после фильтрации были перенесены в конические колбы, в которые была добавлена серная кислота (Х%-раствор) в соотношении Т:Ж=Х:Z и выщелачивающие компоненты – сухой растертый тиокарбамид CS(NH2)2 и сухой растертый сульфат железа (III). При постепенном прибавлении тиомочевины к сернокислотному раствору концентрата образующийся оранжево-желтый осадок, который растворяется в избытке реагента:
CS(NH2)2 + AuCI3+ Н2О = AuCI + S + 2HCI + CО(NH2)2.
В нашем случае осадок не выпал. Колбы со смесью были поставлены на механическое перемешивание (6-8 часов). После перемешивания – смесь концентрата с выщелачивающими компонентами была отфильтрована через воронку Бюхнера и промыта водой. В фильтраты добавлен
69
порошок алюминия для цементации (восстановления) золота. Количество алюминиевого порошка зависело от количества исходной пробы. Осадок на фильтре далее не использовался. Фильтраты с добавленным порошком алюминия поставлены для перемешивания на магнитную мешалку (2-3 часа). Золото (I, III) при этом должно восстановиться до элементного состояния.
Растворы отфильтрованы через фильтры Шота (№4). Осадки на фильтрах обработаны концентрированной соляной кислотой для растворения избытка алюминия. Соляную кислоту удалили фильтрованием. Фильтраты для дальнейшего анализа не использовались. Нагретой до кипения «царской водкой» осадки на фильтрах были растворены и перенесены в фарфоровые чашки для выпаривания. Растворение проводилось в 2 этапа: добавили «царской водки», дали отстояться и отфильтровали. Повторили процедуру еще раз. Промыли фильтр Шотта небольшим количеством соляной кислоты и отфильтровали насухо. Выпаривание фильтратов проводилось на песчаной бане. В процессе выпаривания остаток в чашке 2 раза обрабатывался концентрированной соляной кислотой для удаления азотной кислоты. Выпаривание проводилось до состояния влажного остатка на дне чашки, затем в фарфоровые чашки было добавлено немного HCl и дистиллированной воды. Полученные растворы были отфильтрованы через фильтры (синяя лента) в мерные колбы на 50мл и доведены до метки дистиллированной водой. Тиосульфат взаимодействует с Au (III) по реакции:
Na[AuCI4]+4Na2S2O3 = Na3[Au(S2O3)2]+Na2S4O6 + 4NaCI,
т.е. отношение Au: S2O3 =1:4
Образовавшееся соединение взаимодействует с тиомочевинным комплексом золота:
Na3[Au(S2O3)2]+3[Au(SCNN2H4)] CI= [Au(S2O3)2]∙[Au(CSN2H4)2]3+3NaCI
Результаты исследований по тиокарбамидному выщелачиванию золота из концентратов упорных золотомышьяксодержащих руд месторождения Иштамберды (КР) после удаления из них мышьяка приведены в табл. 1.
Данные тиокарбамидного выщелачивания золота из концентрата упорных золотомышьяксодержащих руд месторождения Иштамберды после удаления из него мышьяка.
Таблица 1
№ п/п |
Наименование пробы |
масса |
Извлечено |
Среднее |
% извлечения |
||
|
|
|
|
пробы, г |
золота, г/т |
содер. Au в |
золота |
|
|
|
|
|
|
конц. г/т |
|
1 |
Концентрат |
после |
удаления |
125,2 |
35,17 |
|
69,5 |
|
мышьяка окислительным об- |
|
|
|
|
||
|
жигом |
|
|
|
|
|
|
2 |
Концентрат |
после |
удаления |
32 |
41,68 |
|
82,37 |
|
мышьяка кислотным разло- |
|
|
|
|
||
|
жение в р-ре HNO3 |
|
|
|
|
|
|
3 |
Концентрат |
после |
удаления |
72 |
11,15 |
50,6 |
22,03 |
|
мышьяка щелочным разложе- |
|
|
|
|
||
|
нием (в р-ре NaOH) |
|
|
|
|
|
По данным табл. 1 следует, что наиболее эффективно (82,37%) золото тиокарбамидным выщелачиванием извлекается из концентрата, мышьяк которого был удален кислотным разложением.
Вывод. Наибольшее извлечение золота из концентрата золотомышьяковых руд ~ 82,4 % достигается после удаления из него мышьяка путем кислотного разложения в растворе азотной кислоты.
Список литературы:
1.Техника и технология извлечения золота из руд за рубежом/ Лодейщиков В.В., Стахеев И.С., Василькова Н.А. и др. Под общ. ред. Лодейщикова В.В. М.: Металлургия,1973-288с.
2.Баткибекова М.Б., Джунушалиева Т.Ш., Борбиева Д.Б., Сыдыкова Ш.С. Тиокарбамидное извлечение золота из упорных золотосодержащих руд Долпрана (КР) // Материалы I Международной Росс.-Казахст. конференции по химии и химической технологии, Томск, 26-29 апр. 2011 г.
70