
ТПУ май 2012
.pdfТаблица 1 – Значения растворимости образцов ГА, МГА до и после прокаливания при T = 800 °C в воде (рН 7, Т = 25 °С)
Образец |
ПР |
рПР |
ГА незам. |
3,56∙10-33 |
33,12 |
МГА, х=0,1 |
2,07∙10-30 |
29,76 |
ГА незам., прокал. |
9,70∙10-38 |
37,19 |
МГА, х=0,1, прокал. |
5,32∙10-33 |
32,30 |
ГА аллогенный |
3,06∙10-33 |
33,80 |
Выводы:
1.Методом жидкофазного осаждения получены образцы незамещенного гидроксиапатита и магнийзамещенного ГА.
2.Показано, что в случае незамещенного ГА термическая обработка приводит к увеличению размера частиц практически в 2 раза, в то время как на размеры частиц МГА она не влияет.
3.Дополнительная термообработка образцов при Т = 800 °С в течение 1 часа позволяет увеличить растворимость порошков в воде при рН 7 на несколько порядков.
Список литературы:
1. Фадеева И.В., Шворнева Л.И., Баринов С.М., Орловский В.П. Синтез и структура магнийсодержащих гидроксиапатитов // Журн. Неорган. материалы. 2003. Т. 39. № 9. С. 1102-1105
2.Баринов С.М., Комлев В.С. Биокерамика на основе фосфатов кальция. М.: Наука, 2005.
204 с.
ВЛИЯНИЕ КАРБАМИДА НА РЕОЛОГИЧЕСКИЕ СВОЙСТВА МАЗЕВОЙ ОСНОВЫ ИЗ ГЕЛЯ ГИДРОКСИДА АЛЮМИНИЯ
Рюмина Е.М., Рюмина О.М.
Национальный исследовательский Томский политехнический университет
Впоследние годы наметилась тенденция более широкого использования лекарств в форме мазей в различных областях медицины.
Всостав мази входят лекарственные вещества и вспомогательные вещества (мазевая основа). Мазевая основа придает мази определенную консистенцию, объем и требуемые физические свойства (вязкость, плавкость и т. п.).
Гель гидроксида алюминия в качестве мазевой основы обладает хорошими иммобилизационными свойствами, что дает высокую стабильность мази [3].
Для стабилизации мазей и мазевых основ широко используют различные вещества, разрешённые к медицинскому применению. В качестве таких веществ могут применяться водорастворимые поверхностно-активные вещества (ПАВ), которые повышают вязкость, седиментационную и агрегативную устойчивость мазей и мазевых основ [1]. Карбамид применяется в качестве смягчителей в производстве косметических кремов, входит в состав некоторых зубных паст, позволяет снизить использование других стабилизаторов (консервантов), т.к. он обладает антимикробными свойствами, благодаря своей способности препятствовать росту микроорганизмов [2].
Целью нашей работы являлось исследования влияния некоторых добавок карбамида на реологические свойства мазевой основы из геля гидроксида алюминия (ГГА).
Объектами реологических исследований служили образцы мазевой основы из ГГА и ГГА с добавлением карбамида (8% мас.).
Реологические исследования приготовленных мазевых основ проводили на ротационном вискозиметре «Реотест - 2» в диапазоне градиентов скоростей сдвига от 1,0 до 145,8 с-1, при температуре в интервале от 25°С.
121

D, скорость сдвига, с-1
200,00
150,00
100,00
50,00
0,00 0,00 10,00 20,00 30,00
r, напряжение сдвига, Па ГГА
D,скорость сдвига, с-1
200
150
100
50
0
0 |
5 |
10 |
r, напряжение сдвига, Па ГГА+карбамид
Реограммы мазевых основ при 25 °С
а) б)
Рисунок 1. Зависимость динамической вязкости от скорости сдвига для образцов мазевой основы из ГГА(а) и ГГА с добавлением карбамида(б).
Уобразца, полученного из ГГА без добавок, наблюдается кривая течения, характерная для твердообразных систем. Особенностью поведения этой системы в твердообразном состоянии является то, что при небольших скоростях деформации происходит спад напряжения сдвига, далее наблюдается обычное увеличение его с повышением скорости.
Уобразца, полученного с добавлением карбамида, четко видно, что аналогичный излом реологической кривой отсутствует, это вероятно связано с предотвращением разрывов сплошности
иобразования слоистости, вследствие чего с увеличением скорости сдвига происходит более равномерное разрушение структуры, что несет положительный характер.
Список литературы:
1.Семкина О.А., Джавахян М.А., Левчук Т.А. и др. Вспомогательные вещества, используемые в технологии мягких лекарственных форм (мазей, гелей, линиментов, кремов) (обзор) // Химико-фармацевтический журнал. 2005. № 9. Т. 39. С. 45-48.
2.Зотов А.Т. Мочевина. Государственное научно-техническое издательство химической литературы. М. 1963.
3.Название изобретения: пат. 2159609 С2 МПК Россия. А61К9/06. Противовирусное средство в мазевой форме на основе интерферона-альфа-2. Опубл. 27.11.2000, Бюл. № 33.
ПОЛУЧЕНИЕ ГРАНУЛИРОВАННОГО ПЕНОСТЕКЛА ТЕРМОХИМИЧЕСКИМ СПОСОБОМ Сеник Н.А.
Национальный исследовательский Томский политехнический университет
Наиболее перспективным теплоизоляционным материалом в настоящее время представляется пеностекло, обладающее высокими тепло и звукоизоляционными свойствами, негорючестью, влагонепроницаемостью, огне- и биостойкостью, высокой механической прочностью.
Но, несмотря на все неоспоримые достоинства пеностекла, в России нет ни одного крупного завода выпускающего этот материал. Причиной является отсутствие надежной технологии, обеспечивающей получение пеностекла с заданными и стабильными свойствами. К тому же отсутствует дешевое и недефицитное сырьё. Поэтому вопросы создания сырьевой базы для производства такого высокоэффективного теплоизоляционного строительного материала как пеностекло являются актуальными.
Набирает тенденцию возможность использования и введения в оборот распространенных источников природного кремнеземсодержащего сырья, а именно высококремнистых аморфных пород, путем замены дорогостоящих высококачественных стекольных песков. А так же разработка низкотемпературного способа получения гранулята без применения энергозатратных стекловарочных агрегатов, что позволит значительно удешевить процесс получения продукта.
122
Наиболее перспективным сырьем является диатомит, поскольку он имеет более стабильный химико-минералогический состав. Колебания SiO2 в диатомите составляет 77,7-83,1 %, против 35,3-86,7 % для трепелов и 52,1-91,4 % для опок.
Основными компонентами шихты для получения гранулированного пеностекла являются диатомит Инзенского месторождения и каустическая сода. Для возможности дополнительного управления пористостью в качестве газообразователя опробованы сажа, алюминиевая пудра, глицерин, жидкое стекло и смесь глицерина с жидким стеклом. Вода используется как компонент, позволяющий провести процесс грануляции и как регулятор пористости.
Необходимая дисперсность диатомита ограничивается следующими параметрами: размер частиц сырья должен быть менее 80 мкм, а пик (d50) приходиться на 6-8 мкм, при этом влажность готового продукта составляет не более 6,0-7,0 %.
Получение гранулированного материала проводилось по схеме, включающей стадии сушки и помола исходного сырья (диатомитовой породы), смешивания продукта измельчения с жидкой порообразующей смесью и каустической содой в интенсивном-смесителе грануляторе, формование гранул, их сушка при температуре 125оС и вспенивание при температуре 800 °С.
Полученные результаты представлены в таблице 1.
Таблица 1. Характеристики гранулированного пеностекла, полученного термохимическим способом
№ |
Состав ших- |
Фракционный |
Наименование характеристик |
|
|
п/п |
ты |
состав, мм |
Насыпная |
Механическая |
Теплопро- |
|
|
|
плотность, |
прочность, МПа |
водность, |
|
|
|
кг/м3 |
|
Вт/м·К |
|
Д/Щ |
4,0-8,0 |
225 |
1,2 |
0,079 |
|
|
2,0-4,0 |
261 |
1,7 |
0,081 |
|
|
1,0-2,0 |
305 |
1,8 |
0,084 |
|
Д/Щ |
4,0-8,0 |
180 |
0,8 |
0,075 |
|
+Al пудра |
2,0-4,0 |
240 |
1,3 |
0,079 |
|
|
1,0-2,0 |
286 |
1,6 |
0,084 |
|
Д/Щ |
4,0-8,0 |
197 |
1,0 |
0,073 |
|
+сажа |
2,0-4,0 |
233 |
1,4 |
0,085 |
|
|
1,0-2,0 |
295 |
1,9 |
0,089 |
|
Д/Щ |
4,0-8,0 |
204 |
1,0 |
0,079 |
|
+ж.ст |
2,0-4,0 |
238 |
1,4 |
0,080 |
|
|
1,0-2,0 |
313 |
1,8 |
0,092 |
|
Д/Щ |
4,0-8,0 |
180 |
1,2 |
0,068 |
|
+глицерин |
2,0-4,0 |
190 |
1,4 |
0,070 |
|
|
1,0-2,0 |
230 |
1,6 |
0,073 |
|
Д/Щ |
4,0-8,0 |
186 |
1,2 |
0,077 |
|
+глицерин и |
2,0-4,0 |
210 |
1,5 |
0,079 |
|
ж.ст |
1,0-2,0 |
230 |
1,6 |
0,080 |
Показана возможность получения гранулированного пеностекла термохимическим способом – непосредственным воздействием гидроксида натрия на диатомит (аморфный кремнезем) при температуре 70-80 °С с образованием гидрозоля силиката натрия, а затем вспениванием при температуре 800 °С.
СПОСОБ КОНДУКТОМЕТРИЧЕСКОГО КОНТРОЛЯ КОНЦЕНТРАЦИИ РАСТВОРЕННЫХ ВЕЩЕСТВ В ПРОМЫШЛЕННЫХ РАСТВОРАХ Сесь К.В.
Национальный исследовательский Томский политехнический университет
Кондуктометрия как метод электрохимического контроля широко используется для анализа технологических растворов в химической, нефтехимической, пищевых и других областях промышленности, а также для анализа природных и сточных вод [1].
Методы измерения электрической проводимости растворов электролитов на переменном токе низкой частоты с контактными кондуктометрическими датчиками отличаются высокой точностью, и детально разработаны как методически, так и схемотехнически [2, 3]. В большинстве серийных производств измерения проводимости жидкости, в том числе для мониторинга экологи-
123
ческого состояния водных бассейнов, обычно используются двухэлектродные кондуктометрические ячейки.
Существует ряд способов повышения точности и расширения диапазона измерения удельной электропроводности растворов, которые могут быть реализованы при создании кондуктометров высокой точности, однако, при этом появляются факторы, ограничивающие применимость того, или иного метода [4, 5]:
1.Увеличение себестоимости прибора за счет увеличения содержания драгоценных металлов (увеличение поверхности электродов, четырехэлектродная схема, ячейка разборного типа).
2.Увеличение времени обработки аналитического сигнала, что невозможно при исследовании кинетики реакций в растворах (градуировочный график, измерение на различных частотах).
3.Химическое взаимодействие электрода с раствором электролита (платинирование).
В табл. 1 приведены результаты измерения удельной электрической проводимости растворов хлорида калия разной концентрации при температуре 25 °С. Измерение проводимости проводили четыре раза для каждого раствора. В качестве кондуктометрического датчика использовали проволоку из платины диаметром 1.00 мм впаянную в стеклянную пробирку. Калибровку кондук-
тометрической ячейки проводили по стандартным растворам КС1 с концентрацией 1 моль/дм3, 0,1 моль/дм3 и 0,01 моль/дм3 при 25 °С.
Табл. 1. Результаты кондуктометрических измерений, N = 10, R = 0,95.
cKCl, |
|
ϰ , |
ϰ , |
|
|
|
|
RE, Ом |
изм |
спр |
д, % |
K, м–1 |
|
моль/дм3 |
См/м |
См/м |
||||
|
|
|
||||
0,01 |
4674 |
0,141 |
0,1412 |
–0,1 |
659 |
|
0,02 |
2371 |
0,278 |
0,2768 |
0,4 |
|
|
0,05 |
1002 |
0,658 |
0,6669 |
–1,3 |
|
|
0,1 |
503,1 |
1,31 |
1,289 |
1,6 |
|
|
1 |
59,37 |
11,1 |
11,18 |
–0,7 |
|
Из табл. 1 видно, что максимальная погрешность измерения удельной электропроводности не превышает 2 %, что соответствует точности широко распространенных промышленных и лабораторных кондуктометров, реализующих четырехэлектродные и бесконтактные способы измерения электропроводности растворов. При использовании миниатюрных датчиков можно значительно снизить содержание драгоценного металла в кондуктометрической ячейке до нескольких миллиграмм.
Сделан вывод о том, что при использовании импульсного напряжения с высокой скважностью импульса и высокой скоростью нарастания позволяет разработчикам кондуктометров уменьшить размер первичного измерительного преобразователя, заменить драгоценный металл (Pt, Pd) на нержавеющую сталь или графит, исключив погрешность кондуктометра, связанную с поляризацией электродов. Сокращение времени воздействия импульса напряжения уменьшает среднее за период значение действующего напряжения до единиц нановольт, что соответствует заряду, протекающему за период следования одиночных, импульсов не более десятков нанокулон.
Список литературы:
1.Бронникова О.В., Холостов С.Б. // Химия и экология. 2003. № 2. С. 3.
2.Латышенко К.П. // Вестник Тамбовского государственного технического университета. 2006. Т. 12. № 3. С. 647-653.
3.Грилихес М.С., Филановский Б.К. Контактная кондуктометрия: Теория и практика метода. Л: Химия, 1980. 176 с.
4.Шелохвостов В.П., Чернышев В.Н., Шелохвостов Р.В., Макарчук М.В. // Контроль. Диагностика. 2008. № 3. С. 36-45
5.Лыгач В.Н., Семенов Ю.В. // Горный информационно-аналитический бюллетень. 2004.
№7. С. 320-323.
БАЗА ДАННЫХ И РАСЧЕТ ДОПУСКАЕМЫХ НАПРЯЖЕНИЙ ДЛЯ УГЛЕРОДИСТЫХ И НИЗКОЛЕГИРОВАННЫХ СТАЛЕЙ В MATHCAD
Скляр М.С., Лосевской С.А.
Допускаемое напряжение для углеродистых и низколегированных сталей при расчете по предельным нагрузкам сосудов, работающих в химической, нефтехимической и нефтеперерабатывающей промышленностях при статических однократных нагрузках, определяют таблице, приведенной в приложении ГОСТ Р 52857.1-2007 [1]:
124

Расчетная температу- |
Допускаемое напряжение [о], МПа, для сталей марок |
|
|
|
||||
ра стенки сосуда или |
|
|
|
|
|
|
|
|
СтЗ |
|
09Г2С, 16ГС |
20, 20К |
|
|
|
||
аппарата, °С |
|
|
|
|
||||
|
|
|
|
|
|
|
17ГС, |
|
толщина, мм |
|
|
|
|
10Г2, |
|||
|
|
|
|
|
||||
|
|
|
|
10 |
17Г1С, |
|||
|
|
свыше |
|
свыше |
|
09Г2 |
||
|
до 20 |
до 32 |
до 160 |
|
10Г2С1 |
|||
|
|
|
||||||
|
20 |
32 |
|
|
||||
|
|
|
|
|||||
|
|
|
|
|
|
|
||
|
|
|
|
|
|
|
|
|
20 |
154 |
140 |
196 |
183 |
147 |
130 |
180 |
183 |
100 |
149 |
134 |
177 |
160 |
142 |
125 |
160 |
160 |
150 |
145 |
131 |
171 |
154 |
139 |
122 |
154 |
154 |
200 |
142 |
126 |
165 |
148 |
136 |
118 |
148 |
148 |
250 |
131 |
120 |
162 |
145 |
132 |
112 |
145 |
145 |
300 |
115 |
108 |
151 |
134 |
119 |
100 |
134 |
134 |
350 |
105 |
98 |
140 |
123 |
106 |
88 |
123 |
123 |
375 |
93 |
93 |
133 |
116 |
98 |
82 |
108 |
116 |
400 |
|
|
|
|
|
|
|
|
85 |
85 |
122 |
105 |
92 |
77 |
92 |
105 |
|
410 |
81 |
81 |
104 |
104 |
86 |
75 |
86 |
104 |
420 |
75 |
75 |
92 |
92 |
80 |
72 |
80 |
92 |
430 |
71* |
71* |
86 |
86 |
75 |
68 |
75 |
86 |
440 |
— |
— |
78 |
78 |
67 |
60 |
67 |
78 |
450 |
— |
— |
71 |
71 |
61 |
53 |
61 |
71 |
460 |
— |
— |
64 |
64 |
55 |
47 |
55 |
64 |
470 |
— |
— |
56 |
56 |
49 |
42 |
49 |
56 |
480 |
— |
— |
53 |
53 |
46** |
37 |
46** |
53 |
|
|
|
|
|
|
|
|
|
*Для расчетной температуры стенки 425 °С.
**Для расчетной температуры стенки 475 °С.
При определении величины допускаемого напряжения по этой таблице необходимо соблюдать следующие требования ГОСТ:
1.При расчетных температурах ниже 20 °С допускаемые напряжения принимают такими же, как при 20 °С, при условии допустимого применения материала при данной температуре.
2.Для промежуточных расчетных температур стенки допускаемое напряжение определяют линейной интерполяцией с округлением результатов до 0,5 МПа в сторону меньшего значения.
3.Для стали марки 20 при Re/20 < 220 МПа допускаемые напряжения, указанные в настоящей таблице, умножают на отношение Re/20/220.
4.Для стали марки 10Г2 при Rp0,2/20 < 270 МПа допускаемые напряжения, указанные в настоящей таблице, умножают на отношение Rp0,2/20 /270.
5.Для стали марок 09Г2С, 16ГС классов прочности 265 и 296 по ГОСТ 19281 допускаемые напряжения, независимо от толщины листа, принимают равными указанным в графе, соответствующей толщине свыше 32 мм.
6.Допускаемые напряжения, расположенные ниже горизонтальной черты, действительны при ресурсе не более 105 ч.
7.Для расчетного срока эксплуатации до 2 105 ч допускаемое напряжение, расположенное ниже горизонтальной черты, умножают на коэффициенты: для углеродистой стали на 0,8; для марганцовистой стали на 0,85 при температуре < 450 °С и на 0,8 при температуре от
450 °С до 500 °С включительно.
Для облегчения работы при проектировании сосудов и аппаратов нами разработан алгоритм и программа определения допускаемого напряжения для рабочих условий, выполненная в среде MathCAD. В программе пользователем задаются только расчетная температура, марка стали, класс прочности и расчетный срок эксплуатации. По этим параметрам программа выбирает из базы данных, представленных в текстовых файлах, требуемые значения переменных, вычисляет допускаемое напряжение с учетом всех требований, округляет его в соответствии с требованиями ГОСТ и выдает пользователю результаты расчета. Таким образом, разработанная нами программа значительно снизит затраты времени проектировщика при выполнении данной рутинной работы.
125

Допускаемое напряжение для углеродистых и низколегированных сталей при расчете по предельным нагрузкам сосудов, работающих в химической, нефтехимической и нефтеперерабатывающей промышленностях при статических однократных нагрузках, определяют таблице, приведенной в приложении ГОСТ Р 52857.1-2007 [1]:
Список литературы:
1. ГОСТ Р 52857.1 -2007 «Сосуды и аппараты. Нормы и методы расчета на прочность. Общие требования».
МЕТОД МОЛЕКУЛЯРНОЙ ДИНАМИКИ КАК ИНСТРУМЕНТ ДЛЯ КОМПЬЮТЕРНОГО МОДЕЛИРОВАНИЯ УГЛЕРОДНЫХ НАНОСТРУКТУР
Татарников Д. А., студент, Ткачева В.В., студентка Национальный исследовательский Томский политехнический университет
Введение. За последние годы компьютерное моделирование стало неоценимым и важным инструментом для исследования и предсказания физических и химических процессов. Компьютерное моделирование означает математическое предсказание технических или физических процессов на современных компьютерах. Более того, компьютерное моделирование позволяет избежать дорогих экспериментальных затрат. Например, это в том случае, если трудно или невозможно создать необходимые условия в лаборатории, если измерения могут быть только произведены с очень большими сложностями или совсем не могут быть произведены, если эксперимент занимает очень долгое время или протекает слишком быстро, чтобы его можно было наблюдать человеческим глазом, или если результаты очень сложно интерпретировать.
В нанотехнологии такой подход позволяет предсказывать свойства новых материалов, которые до этого не существовали совсем в реальности. Также помогает идентифицировать наиболее обещающие и подходящие материалы. Тенденция в направлении виртуальных лабораторий, в которых материалы разрабатываются и изучаются на компьютере. Более того, моделирование позволяет определять средние или приблизительные значения макроскопических характеристик для таких материалов. В общем и целом, компьютерные эксперименты – это связующее звено между лабораторными экспериментами и физико-математической теорией.
Молекулярная динамика. Метод молекулярной динамики позволяет моделировать детальную микроскопическую картину внутренней подвижности макромолекулы. Суть метода МД за-
ключается в решении уравнений движения атомов, полученных из второго закона Ньютона:
|
|
d 2 r |
V |
|
|
m |
|
n |
|
|
|
|
|
|
|
||
|
n |
dt 2 |
n |
, |
(1) |
где mn и rn - масса и пространственные координаты атома n, V – потенциал системы, а n - знак пространственного градиента. Все частицы, находящиеся в выделенном объеме (МД ячейке), взаимодействуют друг с другом посредством заданного потенциала взаимодействия. Метод молекулярной динамики успешно используется в теоретических исследованиях структуры и динамики биологических макромолекул, жидкостей, газов и других молекулярных систем.
Ключевым фактором в молекулярной динамике является выбор потенциала межатомного взаимодействия. В качестве потенциала использовался эмпирический многочастичный потенциал Бреннера (рис.1) в модификации с включенным в него ван-дер-ваальсовым взаимодействием. Наш выбор потенциала был обусловлен тем, что согласно утверждению авторов и уже имеющейся информации по его применению, этот потенциал является реактивным, т.е. позволяет описывать процессы, сопровождающиеся образованием новых ковалентных связей и разрывом уже существующих связей.
Полная потенциальная энергия системы есть сумма энергий всех химических связей атомов
[1]
U f (rij )[VR (rij ) Bij VA (rij )]
i j ( i) |
(2) |
где VR(rij) - парный потенциал, учитывающий отталкивание между атомами (ядро-ядро), VA(rij) - парный потенциал, учитывающий притяжение валентных электронов и ядер.
Для потенциалов, описывающих межатомное взаимодействие, наиболее удачной оказалась запись в виде функций Морзе: [2]
126

|
|
|
|
|
|
De |
|
|
|
|
|
|
|
|
|
|
||||||
V (r ) |
|
|
e |
|
|
2S (rij Re) |
|
|||||||||||||||
|
R |
ij |
|
|
|
|
|
S 1 |
|
|
|
|
|
|
|
|
|
|||||
|
|
|
|
|
|
|
|
|
|
|
|
|
|
|
|
|
|
(3) |
||||
|
|
|
|
|
|
|
|
|
|
|
|
|
|
|
|
|
|
|
||||
|
|
|
|
|
|
|
|
|
De S |
|
|
2 |
|
(rij Re) |
|
|||||||
VA (rij ) |
|
|
|
|
|
|||||||||||||||||
|
|
|
|
|
|
e |
S |
|
||||||||||||||
|
|
S 1 |
|
|
|
|
|
|
|
|
(4) |
|||||||||||
|
|
|
|
|
|
|
|
|
|
|
|
|
|
|
|
|
|
|
|
|||
Функция f(rij) - функция обрезания потенциалов, которая позволяет учитывать взаимодейст- |
||||||||||||||||||||||
вие лишь ближайших соседей и имеет вид: |
|
|||||||||||||||||||||
|
|
|
|
|
|
|
1 |
|
|
|
|
|
|
|
, rij R1 |
|
||||||
|
|
|
|
|
|
|
|
|
|
|
rij |
R1 |
|
|
|
|
|
|
||||
|
|
|
|
|
1 |
|
|
|
|
|
|
|
|
|
|
|
|
|||||
|
f (rij ) |
|
[1 cos( |
|
|
|
|
|
)], R1 rij R2 |
|
||||||||||||
|
R2 |
R1 |
|
|
||||||||||||||||||
|
|
|
|
|
2 |
|
|
|
|
|
|
|
|
|
|
, rij R1 |
|
|||||
|
|
|
|
|
|
|
0 |
|
|
|
|
|
|
|
|
|||||||
|
|
|
|
|
|
|
|
|
|
|
|
|
|
(5) |
||||||||
|
|
|
|
|
|
|
|
|
|
|
|
|
|
|
|
|
|
|
|
|
||
Согласно Бреннеру величина поправки Bij рассчитывается по формуле: |
||||||||||||||||||||||
|
|
|
|
|
Bij Bji |
|
|
|
|
|
|
|
|
|
|
|
||||||
|
Bij |
|
|
|
|
|
|
|
|
|
|
|
|
|||||||||
|
|
|
|
|
2 |
|
|
|
|
|
|
|
|
|
|
|
(6) |
|||||
|
|
|
|
|
|
|
|
|
|
|
|
|
|
|
|
|
|
|
||||
|
|
|
|
|
|
|
|
|
|
N |
|
|
|
|
|
|
|
|
|
|
|
|
|
Bij |
[1 |
|
|
GC ( ijk ) f (rik )] |
|
||||||||||||||||
|
|
|
|
|
|
|
|
k ( i, j ) |
|
|
|
|
, |
(7) |
где Bij – функция, описывающее связанное состояние атома i по отношению к атому j; GC(Ѳijk) - функция, зависящая от угла между двумя линиями, соединяющими частицы i и j и частицы i и k.
Функция GC(Ѳijk) для углерода C определяется следующим образом:
G ( |
|
) a (1 |
c2 |
|
|
c2 |
|
|
|
|
|
0 |
|
0 |
|
|
) |
|
|||
|
d 2 |
d 2 |
(1 cos |
|
)2 |
|
||||
C |
ijk |
0 |
|
ijk |
|
|
||||
|
|
|
0 |
0 |
|
|
, |
(8) |
||
|
|
|
|
|
|
|
|
|
где a0 = 0.011304, c0 = 19, d0 = 2.5.
Рис. 1 Потенциал Бреннера Потенциал Бреннера описывает взаимодействие между атомами на расстояниях меньших,
чем R2=2.0Å, вследствие того, что ограничивающая функция f(r) обращается в 0 при r> R2. Поэтому для описания взаимодействия на больших расстояниях используется потенциал ЛеннардаДжонса, который описывает взаимодействие ван-дер-Ваальса.
Из-за высокой сложности уравнения Ньютона для системы частиц для его решения были использованы численные методы, а именно многошаговый алгоритм Верле, имеющий глобальную погрешность третьего порядка для координаты и второго порядка для скорости. [3]
Компьютерный эксперимент. Структуру всей работы можно отразить с помощью следующей блок-схемы (рис.2)
127

Рис. 2 Структура проекта Рис. 3 Программа визуализации Вся работы состоит из двух главных программ: Программа 1 – используется для расчетов
координат, путем интегрирования вышеописанного потенциала, термодинамических параметров на каждом шагу; Программа 2 (рис.3) – используется для визуализирования полученных данных от Программы 1. Программа 2 имеет свой интерфейс, меню, доступ с помощью горячих клавиш к основным контроллам, возможность манипулирования с визуализированными данными, в виде обычного видеоплеера.
Входными данными для Программы 1 является файл с начальными условиями эксперимента, а также расположения атомов и скорости, для Программы 2 входными данными являются выходные данные от Программы 1, т.е. файл с конфигурацией и бинарный файл с записью координат на каждом шаге итерации.
Таким образом, меняя начальные условия для расчетов можно производить различные эксперименты в области наноматериалов:
•исследование свойств и характеристик материалов;
•исследование возможности существования новых структур материалов, а также их возможные свойства и характеристики;
•манипулирование с уже открытыми материалами, их возможными сочетаниями, на возможность изменения из физических характеристик;
•разработка новых технологий.
Данная разработка, в частности, в настоящий момент используется для исследования возможности существования некоторых новых структур материалов или структур из различных комбинаций уже открытых материалов, и их возможные свойства и области применения.
Заключение. Производство углеродных наноструктур и экспериментальное изучение их свойств – сложно и затратно. Компьютерное моделирование в данном случае лучший вариант, чтобы получить более глубокий взгляд на проблему. Углеродные наноматериалы обладают превосходными свойствами, и потенциал их использования безграничен.
В заключение, хотелось бы отметить, что возрастающая роль атомного моделирования углеродных наноструктур это инструмент для разработки новых материалов и технологий, потому что через моделирование мы идем к эксперименту по разработки новых технологий и приложений, включающих углеродные наноструктуры.
Список литературы:
1.Brenner, D. W., 1990, “Empirical Potential for Hydrocarbons for Use in Simulating the Chemical Vapor Deposition of Diamond Films,” Phys. Rev. B, 42-15, 9458-9471.
2.Tersoff, J., 1986, "New Empirical Model for the Structural Properties of Silicon," Phys. Rev. Lett., 56-6, 632-635.
3.Maruyama, S. and Yamaguchi, Y., 1995b, "A Molecular Dynamics Simulation for the Formation Mechanism of Fullerene," Therm. Sci. & Engng., 3-3,105-109.
ИССЛЕДОВАНИЕ ФИЗИКО-ХИМИЧЕСКИХ ХАРАКТЕРИСТИК КРИСТАЛЛИЧЕСКИХ МИКРОСТРУКТУР В ПРОЦЕССЕ ХИМИЧЕСКИХ ВЗАИМОДЕЙСТВИЙ И ФОРМИРОВАНИЯ
ВГЕТЕРОГЕННЫХ СИСТЕМАХ СЛОЖНЫХ КЛАСТЕРНЫХ ФОСФАТОВ
САММОНИЙНЫМИ СОЛЯМИ В ПРИСУТСТВИИ МЕТИЛЕНДИМОЧЕВИНЫ Усманов С., Тойпасова У.М., Толкын Б., Козыбакова Э.Б., Кабылбек К.
Институт химических наук им.А.Б.Бектурова
128
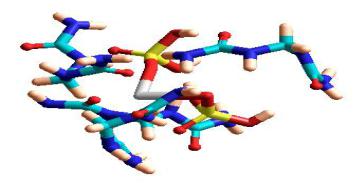
Высокая влагоемкость, мелиоративные, комплексообразующие свойства мочевиноформальдегидных соединений, особенно метиленмочевин – метилендимочевины (МДМ), диметилентримочевины (ДМТМ) и триметилентетрамочевины (ТМТМ) открывают большие перспективы использования их для повышения коэффициента использования пентаоксида фосфора и улучшения физико-химических, товарных и агрохимических характеристик туков, получаемых по бескислотной технологии на базе фосфатного сырья [1-3].
В задачу исследования входило: исследование взаимной растворимости компонентов и химического взаимодействия в водносолевой системе трикальцийфосфат-сульфат аммония (хлорид аммония, нитрат аммония)-метилендимочевина при 30°С и 75°С; определение фазового состава в системе метилендимочевина-дигидрофосфат-вода, идентификация новых соединений; молекулярное моделирование структуры комплекса. Установлено, что в системе Ca3(PO4)2 – (NH4)2SO4 – H2O, содержащего 30,0 мас. % метилендимочевины от массы (NH4)2SO4 при концентрации сульфата аммония 41,35 мас. % растворимость Ca3(PO4)2 при температуре 30°С в 17,3 раза превышает его растворимости в чистой воде, а при 75°С – 32,5 раза.
Определено, что в системе Ca3(PO4)2 – NH4NO3 – H2O, содержащего 30,0 мас. % метилендимочевины от массы NH4NO3 при концентрации нитрата аммония 34,25 мас. % растворимость Ca3(PO4)2 при температуре 30°С в 3,8 раза превышает его растворимости в чистой воде, а при 75°С
– 8 раза.
Изотермическим методом физико-химического анализа в системе МДМ-ДГФСа-вода при 30°С установлены области кристаллизации инконгурентно растворимых соединений включения 10МДМ·ДГФСа и двойного соединения 4МДМ·ДГФСа.
Рассмотренные изменения ИК-спектра соединения 10МДМ·ДГФСа относительно исходных компонентов весьма сходны с наблюдаемыми при образовании аддуктов мочевины.
Между каркасом, построенным из молекул МДМ, которая играет роль «хозяина» и молекулами ДГФСа – «гостями» действуют ван-дер-ваальсовые силы и это стабилизирует структуру образовавшегося соединения включения.
Методами молекулярной механики OPLS и полуэмпирическим методом квантовой химии РМ3 рассчитана электронная структура комплекса из 4 молекул метилендимочевины и дигидрофосфата кальция в газовой фазе (рис.1) в периодическом ящике с участием 390 молекул воды. В результате расчета молекулы воды перераспределены так, чтобы уменьшить напряжения, возникшие при первоначальном заполнении ячейки. Отрицательное значение потенциальной энергии молекул воды свидетельствует о том, что основной вклад в энергию дают невалентные взаимодействия.
Рисунок 1. Молекулярная структура комплекса 4 молекул метилен-димочевины с дигидрофосфатом кальция
Таким образом, результаты исследования показали, что активация фосфоритов с азотными удобрениями в смеси с метиленмочевинами приводит к переводу неусвояемой формы Р2О5 в усвояемую для растений форму. При количестве метилендимочевины 10 мас. % наблюдается большее содержание цитратнорастворимого пента-оксида фосфора, а при количестве 20 мас. % - водорастворимого пента-оксида фосфора.
Список литературы:
1.Вольфкович С.И., Соломонова Н.Л. и др. Синтез азотных и сложных удобрений замедленного действия на основе карбамида // М.: НИУИФ, 1959. – Ч. 1, Вып. 166. – С. 48-51.
2.Вольфкович С.И. Полимерные удобрения // ЖПХ. 1972. № 11. С. 2361-2370.
3.Тарханова Л.С. Физико-химические исследования состава и комплексообразующей способности сложных удобрений длительного действия; дисс…канд.хим.наук. – Чирчик, 1974. –167 с.
129
ВЛИЯНИЕ АРМИРУЮЩЕГО НАПОЛНИТЕЛЯ НА СВОЙСТВА АЛЮМОСИЛИКАТНОЙ КЕРАМИКИ
Усова З.Ю.
Национальный исследовательский Томский политехнический университет
Упрочнение материала путем введения армирующего наполнителя (игольчатых кристаллов, волокон, нитевидных кристаллов) в матрицу с целью сдерживания хрупкого разрушения материала является привлекательным способом упрочнения, так как не имеет ограничений по типу используемых материалов. Такой метод применяется для упрочнения металлов и полимеров, но роль волокнистого материала в случае использования его для упрочнения керамического материала отлична от той функции, которую он выполняет в случае использования его для упрочнения полимерных материалов или металлов. Разница возникает из-за того, что материалы матрицы имеют разные характеристики. Полимеры и большинство металлов обладают меньшей жесткостью, чем керамика. За счет того, что волокна обладают большей жесткостью, чем матрица, происходит распределение нагрузки на армирующий наполнитель через матрицу. Тем самым повышенные механические свойства армирующего наполнителя используются для улучшения прочности композита в целом. Ситуация с керамическими композитами противоположна: керамическая матрица является более жесткой по сравнению с жесткостью армирующего наполнителя. В этом случае армирующий наполнитель и матрица выполняют роли, отличные от классических композитных материалов. Жестокость всего композита определяется жесткостью матрицы, роль армирующего наполнителя в данном случае заключается в том, чтобы уменьшать хрупкость керамической матрицы. Предполагается, что волокнистый наполнитель должен сдерживать хрупкое разрушение матрицы и развитие трещин [1].
В данной работе в качестве керамической матрицы использовался природный обогащенный боксит (Yixing, Китай) химический состав приведен в таблице 1. В качестве упрочняющей добавки в составы масс был введен природный минерал волластонит - обладающий ярок выраженным игольчатым габитусом кристаллов (марки ВП-03 Верхне-Бодамского месторождения с габитусом (соотношение L:D 10:1).
Волластонит вводился в состав сырого и предварительного обожженного боксита. Образцы обжигались при температуре 1450°С и 1500°С с выдержкой при конечно температуре 2 часа. Методом РФА было подтверждено наличие фазы волластонита в конечном продукте (температура плавления чистого волластонита 1544°С).
Таблица 1. Химический состав боксита “Yixing”
|
Al2O3 |
SiO2 |
MgO |
CaO |
TiO2 |
FeO |
H2O |
|
Содержание, |
78,57 |
3,76 |
0,6 |
0,26 |
2,17 |
0,58 |
14,08 |
|
мас. % |
||||||||
|
|
|
|
|
|
|
Таблица 2. Свойства образцов с добавкой волластонита
Содержание волластони- |
0 мас. % |
|
1,5 мас. % |
|
та |
|
|
||
|
|
|
|
|
Тобж1/Тобж2 |
усж., МПа |
p, г/см3 |
sсж., МПа |
p, г/см3 |
1450°С |
133 |
2,25 |
149 |
2,31 |
1500°С |
243 |
2,60 |
252 |
2,59 |
1100°C/1450°С |
104 |
2,16 |
169 |
2,33 |
1100°C/1500°С |
162 |
2,27 |
217 |
2,60 |
Показано, что во всех случаях введение волластонита приводит к увеличению прочности образцов, эффект наиболее выражен в случае введения волластонита в предварительно обожженный боксит. Выявлено, что введение волластонита не приводит к существенному изменению плотности образцов. Таким образом, является целесообразным применение волластонита в технологии производства керамических материалов.
Дальнейшая работа должна быть направлена на исследование свойств получаемой алюмосиликатной керамики, а также изучение влияния количества и дисперсности армирующего наполнителя на свойства конечного продукта.
Список литературы:
1. Bunsell A., Berger M. Fine ceramic fibers. Dekker, Technology& Engineering, 1999. C. 303.
130