
ТПУ май 2012
.pdf
СИНТЕЗ ТВЕРДЫХ ПОКРЫТИЙ НА ОСНОВЕ ФАЗ СИСТЕМЫ B-C-N Меренков И. С., Виткус Е. В., Хомяков М. Н., Шаяпов В. Р., Суляева В. С.
Институт неорганической химии им. А.В. Николаева СО РАН, г.Новосибирск Новосибирский государственный университет, г. Новосибирск 3 Новосибирский государственный технический университет, г. Новосибирск Институт лазерной физики СО РАН, г. Новосибирск
Современная промышленность, в том числе авиастроение, нуждаются в твердых покрытиях, которые могут использоваться для упрочнения уже использующихся при создании летательных аппаратов металлов и сплавов, например титана и алюминия. В качестве перспективного материала для таких покрытий рассматривается карбонитрид бора BCxNy, уникальные физико-
механические свойства которого известны уже давно [1]. В работах последних лет активно изучаются механические характеристики покрытий BCxNy, исследуется взаимосвязь между параметра-
ми процессов осаждения и физико-химическими свойствами пленок [2]. Пленки и покрытия BCxNy синтезируют как физическими (например, реактивное магнетронное распыление), так и
химическими методами. К последним относится химическое осаждение из газовой фазы (CVD). В качестве исходных веществ традиционно используются смеси галогенидов бора, азота или аммиака и метана. Особенностью настоящей работы является использование, в качестве исходных веществ, борорганических соединений – алкиламинборанов, одновременно содержащих в себе все необходимые для синтеза элементы, а именно бор, углерод и азот.
Экспериментальная часть Целью данной работы является синтез исходного летучего соединения – триэтиламинбора-
на (C2H5)3N BH3 (ТЭАБ) с использованием метода механохимической активации, получение пленок BCxNy на титановых подложках, изучение зависимости свойств пленок, в том числе твер-
дости, от температуры синтеза. Получение покрытий осуществлялось методом химического осаждения из газовой фазы при пониженном давлении в кварцевом реакторе проточного типа. В качестве исходных соединений использовали ТЭАБ и триметиламинборан (CH3)3N BH3 (фирма
MERC).
Результаты и их обсуждение
Была получена серия образцов при различных температурах осаждения от 500 °C до 750 °C в виде пленок BCxNy толщиной 400 – 900 нм на подложках Si(100) и Ti. Для характеризации по-
крытий применялись современные физико-химические методы исследования: эллипсометрия, КР- и ИК-спектроскопия , электронно – дисперсионная спектроскопия, растровая электронная и атомносиловая микроскопии, TXRF-NEXAFS и GIXRS-NEXAFS, наноиндентирование. Установлено, что основными элементами в синтезированных пленках являются бор, углерод, азот, а также кислород, в качестве примеси (<1 ат %). По данным энергодисперсионного анализа с ростом температуры синтеза содержание азота остается постоянным в то время как, содержание углерода увеличивается, а бора уменьшается. Содержание элементов в пленках, синтезированных на кремниевой и титановой подложках одинаково. Определена микротвердость пленок карбонитрида бора методом наноиндентирования. Установлено, что зависимость микротвердости от температуры осаждения проходит через максимум при 650 °C и достигает значения примерно 27 ГПа. Такой характер зависимости связан с изменениями в химическом и фазовом составе пленок, которые заключаются в уменьшении концентрации водородсодержащих связей, увеличении доли свободного графита по мере увеличения температуры осаждения.
Список литературы:
1.Косолапова Т.Я., Макаренко Г.Н. и др. // Порошк. метал. 1971. № 1. С. 27–33. 2.Mannan Md. A., Nagano M. // J. Phys. Chem. Solids. 2009. V. 70. P. 20–25.
ПОЛУЧЕНИЕ ВЫСОКОЭФФЕКТИВНОГО ТЕПЛОИЗОЛЯЦИОННОГО МАТЕРИАЛА НА ОСНОВЕ ДИАТОМОВОГО СТЕКЛА
Мешков А.В.
Национальный исследовательский Томский политехнический университет
В России на отопление жилища расходуется 500-600 кВт∙час на квадратный метр жилой площади (по данным на 2008 г.); в Швеции, Канаде, Норвегии – странах с климатическими усло-
виями близкими к российским – 120-140 кВт∙час/м2. Из этого количества 40 % теряется через стены, 23 – через окна, 10 – через подвал, 18 – через крышу, 14 – через вентиляцию. Тепловая изоляция способна снизить расход топлива на отопление помещений не менее чем на 25 %.
111

Среди теплоизоляционных материалов наиболее эффективным по совокупности технических характеристик является пеностекло. Отсутствие надежной технологии, обеспечивающей получение материла с заданными и стабильными свойствами, а также отсутствие дешевого и недефицитного сырья являются основными причинами того, что на сегодняшний день в России нет ни одного крупного промышленного производства этого высокоэффективного теплоизоляционного материала. В связи с этим актуальными являются вопросы по расширению сырьевой базы и разработке технологии для получения перспективного строительного материала – пеностекла.
Последовательность технологических стадий таких как, варка стекла, резкое охлаждение стекломассы и получение стеклокрошки, помол стекла и приготовление пеностекольной шихты, вспенивание и отжиг блоков, обеспечивают получение пеностекла с равномерной мелкопористой структурой, обладающего низким объёмным весом и водопоглощением, при относительно высоких показателях прочности на сжатие. Из-за дефицита стекольных песков, являющихся основным сырьем при варке стекла для производства пеностекла, остро встает вопрос о вовлечении новых распротраненных видов сырьевых материалов, в качестве которых следует рассматривать распространенные опал-кристаболитовые горные породы.
Из всех представителей опал-кристобалитовой группы диатомиты являются наиболее перспективным сырьем для стекольной промышленности, поскольку имеют более стабильный химический состав.
Для проведения исследований выбран диатомит Инзенского месторождения (Ульяновская обл.), имеющий многокомпонентный состав, представленный главным образом стеклообразующим оксидом SiO2 (до 83 %), промежуточным оксидом Al2O3 (до 6 %) и модификаторами (Fe2O3, R2O, RO). Согласно выбранному составу стекла проведен расчет рецепта шихты, из которой сва-
рено стекло. Варку осуществляли в корундовых тиглях объемом 500 см3, в муфельной печи при максимальной температуре 1350 °С. Полученный стеклогранулят измельчали и смешивали с газо-
образователем до удельной поверхности 850 м2/кг.
Полученную пеностекольную смесь загружали в необходимом количестве в жаропрочные металлические формы 160×160×110, предварительно смазанные каолином, уплотняли до одинаковой высоты. Формы плотно накрывали подогнанными крышками и помещали в печь с подогревом пода до температуры 600 °С, повышая температуру до 840 °С, со скоростью и выдержкой при максимальной температуре в течение 20-30 минут. Формы охлаждали до комнатной температуры. Основные физико-механические характеристики пеностекла, полученного на основе диатомового стекла, приведены в таблице. Образцы обладают закрытой равномерной мелкопористой структурой, по свойствам и макроструктуре не уступают промышленному пеностеклу Foamglas ведущего мирового производителя Pittsburgh Corning.
Таблица 1. Физико-механические характеристики пеностекла на основе диатомового сырья
Характеристики полученного на основе диатомита пеностекло
Свойства |
Значения |
Плотность, кг/м3 |
125-135 |
Прочность при сжатии, МПа |
0,7-1,1 |
Коэффициент теплопроводности, Вт/(м∙К) |
0,05-0,055 |
Водопоглощение, % (об.) |
3-5 |
Таким образом, проведенные исследования, подтверждают целесообразность использования диатомитов в качестве основного сырья для варки стекла, на основе которого можно получать качественное пеностекло, обладающее малым объемным весом и водопоглощением, при высоких прочностных показателях.
ПЛАЗМОДИНАМИЧЕСКИЙ СИНТЕЗ НАНОДИСПЕРСНОГО КАРБИДА КРЕМНИЯ Никитин Д.С., студент
Национальный исследовательский Томский политехнический университет
Единственным химически стабильным соединением кремния и углерода является карбид кремния, однако при том, что составляющие элементы C и Si являются, пожалуй, самыми распространенными на Земле, SiC был обнаружен лишь в составе чрезвычайно редкого минерала муассанита, впервые обнаруженного в метеорите в каньоне Диавола (Аризона) Анри Муассаном в 1905. Незадолго до этого события в 1893 году молодым американским инженером Эдвардом Ачесоном был осуществлен синтез карборунда (карбида кремния технической чистоты) с помощью электрической графитовой печи [1]. Данный метод основан на явлении испарения и конденсации синтезируемого материала, т.е. явлении сублимации. В простейшем случае через графитовый керн
112

пропускается ток порядка сотен кА, что приводит к выделению Джоулева тепла. Прекурсоры (смесь кремнозема и углерода) закладываются вокруг нагревателя. При нагреве смеси до температур 1600-1800 оС происходит образование SiC и попутное выделение угарного газа CO. Таким образом, метод синтеза карбида кремния, основанный на использовании электропечи Ачесона, отличается простотой в реализации, малыми затратами на процесс синтеза и стоимостью исходных реакционных материалов, что обусловило широкое распространение этого способа в промышленности вплоть до настоящего времени с незначительными изменениями.
Изначально карбид кремния представлял особый интерес для абразивной и огнеупорной промышленности ввиду наличия у него сверхтвердости, высокой теплопроводности и износостойкости. В начале XX века, как известно, проводились исследования по изучению полупродниковых свойств вещества. Удивительно при этом, что некоторые фундаментальные электрофизические явления были обнаружены именно на карбидокремниевых кристаллах. Так, при провдении опытов по испытанию первых радиоприемников SiC использовался в качестве детектора [2]. Явление электролюминесценции (фактически реализация первого светодиода) впервые было обнаружено при эксперименте на кристаллах SiC в 1907 году в лаборатории Маркони английским ученым Раундом [3]. Подобные опыты по излучению света, исходящего из кристаллов карбида кремния SiC, были повторены советским изобретателем О.В. Лосевым в НРЛ (Нижегородской радиолаборатории) в 1923 году [4]. Приведенные работы позволили сформулировать главный принцип электролюминесценции полупроводниковых структур - инжекционную рекомбинацию. Во второй половине XX века в связи с интенсивным развитием электроники удалось обнаружить уникальные полупроводниковые свойства карбида кремния (во многом благодаря синтезу монокристаллов SiC методами Лели и ЛЭТИ): широкая запрещенная зона, высокая допустимая напряжённость поля электрического пробоя, теплопроводность, устойчивость к внешним воздействиям (в том числе и к радиационному излучению) [5]. Это позволяет создавать на основе SiC электронные приборы для эксплуатации в особо жестких условиях, а также мощные полупроводниковые ключи.
Еще большего улучшения характеристик возможно ожидать от использования карбида кремния в наноструктурном состоянии, покольку свойства субмикронных и наноматериалов существенно отличаются от свойств крупнокристаллических, крупнозернистых и монокристаллических веществ [6] . Однако сегодня ни один из методов синтеза наноразмерных порошков SiC не нашел промышленного применения из-за определенных трудностей, связанных с недостаточной дисперсностью получаемого продукта, его загрязненностью примесями, а также высокими энергозатратами процесса синтеза.
В предлагаемой работе исследуется принципиальная возможность реализации синтеза наноразмерного SiC продукта в гиперскоростной струе электроразрядной плазмы, истекающей из коаксиального магнитоплазменного ускорителя, общий вид которого изображен на рис. 1. Данный способ позволяет реализовать экстремальные энергетические параметры, необходимые для соединения атомов кремния и углерода. Конструкция ускорителя включает в себя центральный электрод и электрод-ствол. Исходный материал в виде смеси порошков кремния и аморфного углерода, предварительно измельченных до размеров порядка десятков микрон, в соотношении 7:3 общей засыпался в канал формирования плазменной структуры (4). При подведении к ускорителю разности потенциалов происходит возникновение плазменной перемычки и движение сверхзвуковой струи углерод-кремниевой плазмы вдоль ускорительного канала электрода-ствола в камеруреактор, заполненную аргоном при давлении в 1 атм.
Рис. 1. Общий вид коаксиального магнитоплазменного ускорителя
Электропитание ускорителя осуществлялось от емкостного накопителя энергии. Зарядное напряжение было принято равным 3 кВ, емкость конденсаторных батарей 6 мФ. При проведении
113
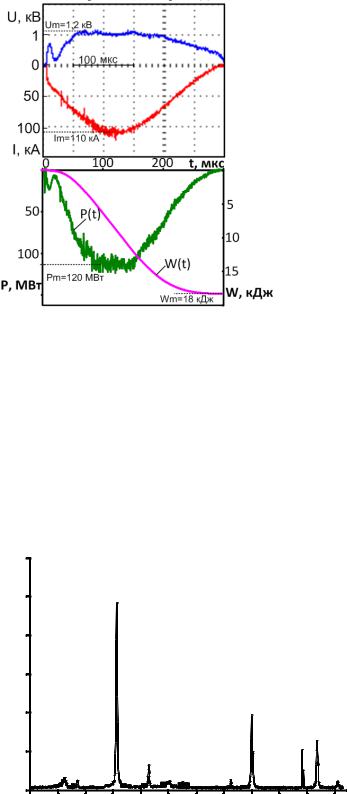
эксперимента с помощью полученных осциллограмм и расчетных кривых (рис. 2) были определены значения напряжения и тока на плазменной перемычке (соответственно 1,16 кВ и 101 кА), мощность электрического разряда (115 кВт) и выделившаяся в процессе опыта эксперимента энергия (18 кДж).
Рис. 2. Осциллограммы и расчетные кривые
Вскрытие камеры происходило спустя 1 час после эксперимента для того, чтобы порошок мог осесть. Со стенок камеры был собран ультрадисперсный продукт синтеза серого цвета массой 0,5 г. Осмотр конструкции ускорителя на наличие повреждений и пробоев показал, что установка может нормально функционировать при предлагаемых электрических и энергетических параметрах опыта.
Синтезированный порошок без предварительной обработки был исследован методом XRD (X-ray diffraction) – рентгеновской дифрактометрии – на дифрактометре Shimadzu XRD 7000 (Cu-α излучение) с целью определения фазового состава продукта. Применение программного пакета PowderCell 2.0 вкупе с базой структурных данных PDF 4+ позволило проанализировать дифрактограмму (рис.3). Результаты полнопрофильного структурно-фазового анализа внесены в таблицу 1, откуда видно, что продукт состоит из трех кристаллических фаз: карбида кремния кубической сингонии (пространственная группа F -4 3 m {216}), графита и углеродных луковичных структур (P6-3mc {186}. Как видно из значений ОКР, размеры кристаллитов составляют менее 100 нм, что свидетельствует о нанодисперсности получаемого продукта.
|
6 |
|
|
111 |
|
|
|
|
|
|
|
|
|
|
|
|
|
|
|
|
|
|
|
3 |
|
|
|
SiC(cub) |
|
|
|
|
|
|
|
Интенсивность, усл.ед., *10 |
5 |
|
|
|
|
|
|
|
|
|
|
4 |
|
|
|
|
|
|
SiC(cub) 220 |
|
|
||
3 |
|
|
|
|
|
|
Si(cub) 400 SiC(cub) 311 |
|
|||
2 |
|
Si(cub) 111 |
SiC(cub) 200 |
gC 101 Si(cub) 220 |
|
Si(cub) 311 |
SiC(cub) 222 |
||||
1 |
gC 002 |
|
|||||||||
|
|
||||||||||
|
0 |
|
|
|
|
|
|
|
|
|
|
|
20 |
25 |
30 |
35 |
40 |
45 |
50 |
55 |
60 |
2 , град |
|
Рис.3. Рентгеновская дифрактограмма продукта синтеза |
|
114

Таблица 1. Результаты полнопрофильного анализа картины рентгеновской дифрактограммы ультрадисперсного продукта
|
Кристаллическая |
Содержание, |
% |
Параметр решетки, Å |
ОКР, |
|
|||
|
|
PD |
d/d·103 |
||||||
п/п |
|
фаза |
|
(масс) |
|
эксп. |
F |
nm |
|
|
|
|
|
|
|
|
|
|
|
|
С |
|
gC |
17,08 |
|
а = 2,4482 |
2,4700 |
15,55 |
3,74 |
|
|
|
с = 6,9159 |
6,9700 |
|||||
|
|
P6- |
|
|
|
|
|
||
|
|
|
|
|
а = 2,4207 |
2,4700 |
|
|
|
|
3mc {186} |
Onions |
15,00 |
|
21,08 |
1,58 |
|||
|
|
с = 6,7914 |
6,9000 |
||||||
|
|
|
|
|
|
|
|
||
|
|
SiC(cub) |
67,93 |
|
а = 4,3560 |
4,3480 |
88,93 |
0,91 |
|
|
|
F -4 3 m {216} |
|
||||||
|
|
|
|
|
|
|
|
Присутствие фазы кубического карбида кремния вполне соответствует первоначальным представлениям о возможности синтеза данной фазы предлагаемым способом. Кроме того, содержание в продукте фазы SiC достаточно велико (~ 70 %), что свидетельствует о правильности выбора уровня электрической энергии для подведения к установке.
Также в продукте содержатся углеродсодержащие фазы: графит (gC) и луковичные структуры (Onions). Их наличие обусловлено избыточным количеством углерода в реакции, причиной чего является электроэрозионный износ графитового ствола. При этом, судя по соотношению содержания фаз gC и Onions, образование той или иной фазы в камере равновозможно.
Причиной различия в параметрах кристаллических решеток является наличие некоторых ненулевых значений микронапряжений (Δd/d), обусловленных высокой динамичностью процесса, сравнимой с динамикой детонационных методов.
Собранный порошок был проанализирован также методом просвечивающей электронной микроскопии на дифрактометре Philips SM 12. Светлопольные снимки (А) участков порошка и соответствующие им картины дифракции (Б) и темнопольные снимки в некоторых рефлексах (В, Г) приведены на рис.4 и 5.
На рис.3 характерными частицами являются объекты в форме, близкой к несформировавшимся треугольников, и с размерами до 400 нм. Некоторая часть кристаллитов изображена на снимке в поперечном состоянии, что позволяет оценить их толщину – порядка 100 нм. С помощью картины дифракции подобные частицы удалось идентифицировать как принадлежащие к кубической фазе карбиду вольфрама (рефлексы {111} и {222}). В свете этих же рефлексов на другом участке нанопорошка (рис.5) выявлены объекты, подобные изображенным на рис.4, но с менее правильной формой. Аналогичные объекты треугольной формы были найдены в работах [7, 8, 9] и идентифицированы как β-SiC (кубическая фаза). Размер этих частиц колеблется от 700 нм до нескольких микрометров.
Кроме указанного типа частиц имеются образования, гораздо меньшие по размеру (в диапазоне до нескольких десятков нм), не просвечиваемые электронным пучком в свете указанных рефлексов. Эти частицы возможно отнести к наразмерным кремнию или графиту, присутствие которых в порошке в продукте вполне возможно как первоначальных реагентов.
Рис. 4. TEM-снимки продукта синтеза
115
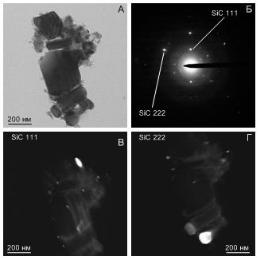
Рис. 4. TEM-снимки продукта синтеза
Таким образом, успешно осуществлен синтез нанодисперсного SiC плазмодинамическим методом в сверхзвуковой плазменной струе, генерированной КМПУ. Продукт, как показал его анализ современными методиками, состоит из фазы карбида кремния кубической сингонии и чисто углеродных структур.
Список литературы:
1. Acheson, G. U.S. Patent 492 767 «Production of artificial crystalline carbonaceous material»,
1893
2.Henry H.C.U.S. Patent 837 616 «Wireless telegraph system», (1906)
3.Round H.J., "A Note on Carborundum," Electrical World, v. 19 (February 9, 1907), p. 309
4.О.В. Лосев, "Светящийся карборундовый детектор и детектирование с кристаллами", Телеграфия и телефония без проводов, 5 (44), с.485, 1927
5.Лучинин В., Таиров Ю. Карбид кремния – алмазоподобный материал с управляемыми наноструктурно-зависимыми свойствами // Наноиндустрия. – 2010. – Вып. 1. – С. 36 - 39.
6.Ремпель А.А. Нанотехнологии, свойства и применение наноструктурированных материалов. // Успехи химии. - 2007. – № 76 (5). – С. 474-500.
7.Raman V. et al. Synthesis of silicon carbide through the sol-gel process from different precursors. // Journal of materials science. – 1995. - V.30 – P.2686-2693.
8.Feng A., Munir Z.A. Effect of an electric field on self-propagating combustion synthesis: Part II. Field-assisted synthesis of β-SiC. // Metallurgical and Materials Transactions B: Process Metallurgy & Mat. Proces. Sci. – 1995. - V.26, No.3– P.587-593.
9.Leparoux S. et al. Synthesis of silicon carbide coating on diamond by microwave heating of diamond and silicon powder: a heteroepitaxial growth. // Scripta Materialia. – 2007. – V.57. – P.595-597.
ОСОБЕННОСТИ СТРУКТУРЫ ЛЕГКОГО БЕТОНА НА ПОРИСТЫХ ЗАПОЛНИТЕЛЯХ Орлов И.А.
Национальный исследовательский Томский политехнический университет
Структура легкого бетона имеет важное функциональное значение при получении материалов с улучшенными эксплуатационными характеристиками. Получение однородной структуры зависит от многих факторов, важнейшими из которых являются качество заполнителей и их зерновой состав, вид и качество вяжущего и добавок, содержание воды в смеси, а также способы и режимы их укладки и уплотнения.
Изучение структуры легкого бетона является основополагающим аспектом в получении высококачественного бетона. Имеется ряд теоретических представлений рассматривающих ее с различных исходных позиций. Среди них наибольшей известностью пользуется теория структуры, предложенная Г. И. Горчаковым [1].
Экспериментальные исследования H. А. Попова показали [2], что лишь слитная структура бетона может обеспечить весь комплекс оптимальных свойств. Бетон плотной структуры предельного уплотнения обладает минимальной теплопроводностью, по сравнению с бетоном обладающим межзерновой пустотностью.
116
Последующее развитие науки о легком бетоне обосновало ряд специфических особенностей этого материала, которые как ставят его в общий ряд применяемых в практике различных бетонов, так и выделяют его в бетон особого вида.
Оценивая структуру бетона вообще и в особенности легкого, необходимо обратить внимание на два основных критерия: однородность и слитность строения. Учитывая, что в легком бетоне капиллярно-пористой структурой является не только цементный камень, но и сам заполнитель, нельзя игнорировать факт миграции воды, как в заполнитель, так и из него. Л. П. Орентлихер обратила внимание на то, что этот процесс протекает по закону маятника [3].
Не менее важной особенностью структуры легкого бетона является повышенное сцепление цементно-песчаной части с пористым заполнителем. Из литературных источников следует, что сила сцепления бетона с пористым заполнителем возрастает в 1,7–2,5 раза по сравнению с плотным щебнем. Сила сцепления цементно-песчаной части с заполнителем в первую очередь влияет на прочностные характеристики бетона. Ю. Е. Корнилович признает три возможных случая прохождения разрушения [4]:
3.по растворной части при неразрушенном заполнителе; 4.по растворной части и по контактной зоне между растворной частью и заполнителем; 5.по заполнителю и растворной части.
Для легкого бетона наиболее характерным является второй и третий вариант. При сравнении тяжелого и легкого бетонов получается, что высокая сила сцепления является не только важной особенностью структуры легкого бетона, она предопределяет иную схему разрушения, чем у тяжелого бетона.
В. М. Москвин в монографии [5] рассматривает механизм разрушения бетона. Он установил, что микротрещины в легком бетоне появляются в зерне заполнителя из-за низкой прочности пористого заполнителя по сравнению с окружающим его цементным раствором и высокой силой сцепления. Микротрещины, например, в зерне керамзита имеются еще до приложения нагрузки, которые увеличиваются в процессе твердения бетона. Заполнитель выполняет двоякую функцию. Она может быть негативной, увеличивая в контактной зоне концентрацию напряжений и стимулируя этим образование микротрещин, и позитивной, поскольку заполнитель задерживает перерастание микротрещин в макротрещины.
Таким образом, изучая структуру легкого бетона, необходимо стремиться к достижению однородности структуры и слитности его строения, что приводит к увеличению прочностных и теплофизических характеристик.
Список литературы:
1. Горчаков Г. И. Состав, структура и свойства цементных бетонов. М.: Стройиздат, 1976.
144 с.
2.Попов Н. А. Новые виды легких бетонов. М.: Стройиздат. 193 с.
3.Орентлихер Л. П. Бетоны на пористых заполнителях в сборных железобетонных конструкциях. М.: Стройиздат, 1988. 136 с.
4.Корнилович Ю.Е. Исследование прочности растворов и бетонов. Киев: Госстройиздат УССР, 1960. 220 с.
5.Москвин В.М., Капкин М.М., Савицкий А.Н., Ярнаковский В.Н. Бетон для строительства в суровых климатических условиях. Л.: Стройиздат, 1973. 172 с.
СОЗДАНИЕ ВОДОСТОЙКИХ МАГНЕЗИАЛЬНЫХ МАТЕРИАЛОВ НА ОСНОВЕ СЕРПЕНТИНИТОВЫХ ПОРОД
Печеркина К.И., Гаппарова К.М.
Национальный исследовательский Томский политехнический университет, г. Томск, Южно-Казахстанский государственный университет им. М. Ауезова, г. Шымкент
При современном уровне и масштабах материального потребления минерального сырья фактор полноты использования и вовлечение в производство вторичных материальных ресурсов имеет первостепенное значение. Разработка и освоение безотходных технологий имеет огромное значение для предприятий ресурсоемких отраслей промышленности. В частности на горнообогатительных комбинатах, предприятиях огнеупорного, металлургического производства, получения солей магния ежегодно образуется более 5,6 млрд.тонн некондиционного природного магнийсодержащего сырья. Это сырье можно использовать для создания магнезиальных вяжущих веществ, которые являются активным компонентом строительных композиционных материалов.
Особую актуальность приобретает вопрос разработки водостойких композиционных магнезиальных вяжущих материалов с вовлечением в производство как местных техногенных, так и природных силикатов магния.
117

Существует несколько видов повышения водостойкости магнезиального вяжущего. Одним из них является введение добавок в состав смешанного магнезиального вещества. Часть добавок используется для повышения водостойкости магнезиального вяжущего, другая часть оказывает влияние на прочностные характеристики магнезиального вяжущего.
В данной работе исследована возможность использования серпентинитовых пород для создания водостойких магнезиальных вяжущих веществ.
При выполнении работы были исследованы в качестве вяжущего материала– каустический магнезит, полученный обжигом магнезита Онотского месторождения, и порошок магнезиальный каустический (ПМК-87), а в качестве добавки использовались магнийсодержащий силикат (серпентинит), химические состав которого представлен в таблице 1, в качестве затворителя использовался раствор сульфата магния.
Таблица 1. Химический состав серпентинита
Содержание оксидов, мас. %
SiO2 |
Al2O3 |
Fe2O3 |
FeO |
CaO+MgO |
MgO |
31,69 |
4,63 |
39,32 |
0,35 |
17,34 |
7,02 |
Серпентинит смешивался с каустическим магнезитом или ПМК-87 в соотношениях от 50 до 70% , полученная смесь затворялась раствором сульфата магния. Образцы для испытаний изготовлялись в форме кубиков размером 20×20×20 мм, которые твердели в условиях воздушной и воз- душно-влажной средах в течении 28 суток.
В зависимости от количества вводимого компонента определялись основные физикомеханические свойства разработанных материалов: сроки схватывания, предел прочности при сжатии, объемную массу, водопоглощение, коэффициент водостойкости.
При введении серпентинита уменьшаются сроки схватывания образцов; значения предела прочности на сжатие варьируется от 12,6 до 25,1 МПа; объемная масса составляет примерно
2 г/см3, водопоглощение образцов не превышает 7%; коэффициент водостойкости 1,0-1,2. Каустический магнезит обжигался при разных температурных режимах и исследовалась ак-
тивность каустического магнезита (m (Mg+)=11,32·10-3 г).
Анализ экспериментальных данных показал, что наибольшей активностью обладают каустический магнезит обожженный при температуре 700 °С в течение 10 минут и порошок магнезитовый каустический, которые использовались в работе для получения смешанного магнезиального вещества с заданными свойствами.
Анализ экспериментальных данных показал, что полученные материалы соответствуют требованиям ГОСТ и могут быть рекомендованы для производства магнезиальных материалов на основе серпентинита.
Работа поддержана грантом РФФИ № 12-03-90902.
Список литературы:
1.Вайвад А.Я. Магнезиальные вяжущие вещества. Рига. 1971. 332 с.
2.Волженский А.В. Минеральные вяжущие вещества. Москва: Стройиздат, 1986. 372 с.
СИНТЕЗ ПЛЕНОК CEO2 С ДОБАВКОЙ SIO2
Пичугина А.А., Халипова О.С.
Национальный исследовательский Томский государственный университет
Пленки оксида церия(IV) на твердотельных подложках нашли применение в создании фоточувствительных элементов для биолюминесцентных сенсорных систем [1]. Сходство кристаллических решеток оксида церия (IV) с оксидом кремния (IV) обеспечивает их лучшую адгезию с кремнием, что приводит к уменьшению плотности поверхностных зарядов и повышению степени отклика вольтамперных характеристик сенсоров. Известные технологии получения таких пленок требуют высоких энергетических затрат и наличие вакуума. В настоящей работе для получения пленок CeO2–SiO2 используется метод химического осаждения вещества из пленкообразующего
раствора (ПОР). Этот метод позволяет снизить энергозатраты и трудоемкость процесса получения оксидных материалов.
Целью работы являлось установление оптимальных температурных режимов получения пленок CeO2 с добавкой SiO2 из ПОР.
118
Пленкообразующие растворы готовили на основе 96 % (масс.) этилового спирта, кристаллогидрата нитрата церия(III) (С=0,15 моль/л), салициловой кислоты ((Sal) С=0,15 моль/л), тетраэтоксисилана ((ТЭОС) С=0,43 моль/л).
Согласно литературным данным [2] , методам вискозиметрии и ИК-спектроскопии формирование пленкообразующей способности раствора идет за счет реакций гидролиза, комплексообразования и поликонденсации:
2SiOCHH 2SiOCHOHOH; |
|||
254 |
2 |
253 |
25 |
2SiOCHOCSiHSiOCHH; |
|||
253 |
|
252 |
2522 |
CeNOHCeNOHNO
33 2 32 3
;
CeNCOHCOHCOe
3264 HNO64 3
3
Рисунок 1. Термический анализ высушенного ПОР Се(NO3)3 – Sal – ТЭОС
Данные процессы приводят к формированию в растворе комплексного соединения нитрата гидроксосалицилата церия(III) и полиэтоксисилана.
Пленки CeO2–SiO2 получали на кремниевых подложках методом центрифугирования на
центрифуге MPW-3410, со скоростью вращения 2000 об./мин. После чего сушили при температуре
60
анализ высушенного ПОР в атмосфере кислорода (синхронный анализатор SТA 449).
Как видно из термограммы, процесс разложения ПОР (рисунок 1) идет в два этапа. Первый этап разложения смеси (0 – 240 °C), согласно литературным данным термодеструкции высушенного спиртового раствора тетраэтоксисилана [2] и раствора кристаллогидрата церия с салициловой кислотой [3], может быть связан с удалением адсорбированных молекул воды и азотной кислоты (два эндо-эффекта, один экзо-эффект). Второй – при температуре более 240 сгоранием салициловой кислоты (экзо-эффект при 301,6 °C) и термодеструкцией полисилоксана (экзо-эффект при 500 °C). По результатам термического и рентгенофазового анализов (дифрактометр XRD – 6000 с CuKa – излучением, с использованием баз данных PCPDFWIN и программы полнопрофильного анализа POWDER CELL) установили, что оксидная система CeO2–SiO2 фор-
мируется при температуре 600
Список литературы:
1.Максимчук Н.В., Шмырева А.Н., Борисов А.В.// Технология и конструирование в электронной аппаратуре. 2010. №5. 6. С. 54–59.
2.Борило Л.П. Тонкопленочные неорганические наносистемы. Томск: Томск. ун-та, 2003.
С. 133.
3.Халипова О.С., Кузнецова С.А., Козик В.В.// Ползуновский вестник. 2011. № 4-1. С. 74–
77.
СИНТЕЗ И ИССЛЕДОВАНИЕ МАГНИЙЗАМЕЩЕННОГО ГИДРОКСИАПАТИТА Рассказова Л.А.
Национальный исследовательский Томский государственный университет
Гидроксиапатит (ГА), являясь основным неорганическим компонентом костной ткани, давно представляет интерес для многих ученых в области химии, биохимии и медицины. Природный ГА представляет собой структурный аналог кости, вследствие чего проявляет свойства биосовместимости и самое главное уникальной биоактивности. Это позволяет применять его в составе имплантационных материалов и покрытий. Такой гидроксиапатит содержит ряд физиологически
важных для жизнедеятельности организма ионов (Na+, K+, CO32‾, F‾ и др.), среди которых нема-
ловажное значение имеет ион Mg2+. Ионы магния принимают участие в процессах адгезии клеток и положительно влияют на биологическую совместимость при использовании его в качестве материала для имплантации [2].
В данной работе был проведен синтез обычного (незамещенного) ГА и магнийзамещенного гидроксиапатита (МГА) метом жидкофазного осаждения [2] согласно уравнениям (1) и (2) соответственно:
10Ca(NO3)2+6(NH4)2HPO4+8NH4OH→Ca10(PO4)6(OH)2+20NH4NO3+6H2O (1)
119

(10-x)Ca(NO3)2+xMg(NO3)2+6(NH4)2HPO4+8NH4OH→ (2) Ca10-xMgx(PO4)6(OH)2+20NH4NO3+6H2O, где х=0,1.
Далее образцы были подвергнуты термической обработке при температуре 800 °С в муфельной печи в течение 1 часа.
По полученным на растровом электронном микроскопе ТМ-1000 изображениям методом секущей определялась дисперсность порошков (рис. 1).
Химическим методом были определены значения произведений растворимости полученных порошков (до и после прокаливания) в воде (рН 7) при комнатной температуре по результатам трилонометрического титрования иона кальция (табл. 1).
|
90 |
|
|
,% |
80 |
|
а |
70 |
|
||
|
|
||
частиц |
|
|
|
60 |
|
|
|
50 |
|
|
|
40 |
|
|
|
Количество |
|
|
|
30 |
|
|
|
20 |
|
|
|
10 |
|
|
|
0 |
|
|
|
0 |
50 |
100 150 200 250 300 |
|
|
|
Размер частиц, мкм |
,% |
70 |
|
|
|
|
частиц |
|
|
|
б |
|
60 |
|
|
|
||
50 |
|
|
|
|
|
40 |
|
|
|
|
|
Количество |
|
|
|
|
|
30 |
|
|
|
|
|
20 |
|
|
|
|
|
10 |
|
|
|
|
|
0 |
|
|
|
|
|
0 |
100 |
200 |
300 |
400 |
|
|
Размер частиц, мкм |
||||
|
|
,% |
50 |
|
в |
|
|
|
|||
частиц |
40 |
|
||
|
|
|||
30 |
|
|
||
Количество |
20 |
|
|
|
10 |
|
|
||
0 |
|
|
||
0 |
50 |
100 150 200 250 |
||
|
||||
|
|
Размер частиц, мкм |
,% |
50 |
|
|
|
|
|
|
|
|
|
|
|
г |
||
частиц |
40 |
|
|
|
|
||
30 |
|
|
|
|
|
||
|
|
|
|
|
|
||
Количество |
20 |
|
|
|
|
|
|
10 |
|
|
|
|
|
||
0 |
|
|
|
|
|
||
0 |
50 |
100 |
150 |
200 |
250 |
||
|
|||||||
|
|
Размер частиц, мкм |
Рис. 1. Гистограммы распределения частиц ГА, МГА по размерам:
а – ГА незамещенный; б – ГА незамещенный, прокаленный при температуре Т = 800 °С; в– МГА, х = 0,1; г – МГА, х = 0,1 прокаленный.
120