
Engineering and Manufacturing for Biotechnology - Marcel Hofman & Philippe Thonart
.pdf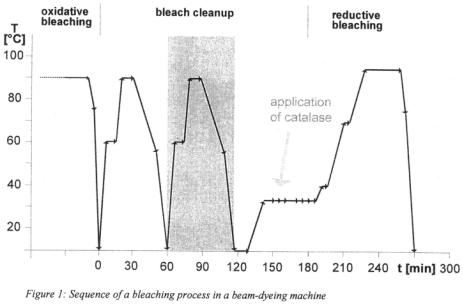
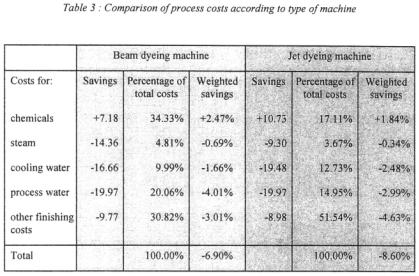
ENZYME STABILITY AND STABILISATION : APPLICATIONS AND CASE STUDIES.
DR. GUIDO A. DRAGO* AND DR. TIM D. GIBSON.
Applied Enzyme Technology Ltd, 175 Woodhouse Lane, Leeds, LS2 3AR, UK. Telephone: +44-113-233-3030 FAX: 44-113-233-2593 e-mail
G.A. Drago@leeds.ac.uk. (* Corresponding author)
Summary
The stabilisation of enzymes is of great importance in many applications. The two main types of stability may be defined as: 1) Storage or Shelf Stability and 2) Operational
Stability. The first relates to the stability of enzymes when stored as a dehydrated preparation, a solution or immobilised and is particularly concerned with retention of activity over time. The second generally relates to the retention of activity of an enzyme when in use. Both types of enzyme stability will be discussed using case studies from the analytical field (alkaline phosphatase, alcohol oxidase, acetylcholine-esterase and a recombinant luciferase) and enzyme based biosterilisers (peroxidases). The introduction of an electrophoretic technique for predicting protein-polymer interactions will be described. In addition, stabilisation using covalent immobilisation of pre-stabilised enzyme complexes will be presented using glucose oxidase as an example and a brief discussion on the likely factors influencing stability of enzymes is included.
1. Introduction
The stabilisation of enzymes is of great importance in a variety of applications. Enzymes are used in the fields of biocatalysis, analytical chemistry, food processing, environmental treatment, detergent manufacture, biosensor production for medical diagnostics and other measuring applications, to name but a few. In all these areas the retention of the biological activity of the enzyme molecule is paramount, and this depends on stabilisation of the biological structure of the enzyme. In most cases, the actual mechanism of stabilisation of enzymes is a little understood phenomena. As enzyme structures are solved, reaction mechanisms are understood and the mechanisms of protein folding and deactivation are worked out, the mechanisms of enzyme
361
M. Hofman and P. Thonart (eds.), Engineering and Manufacturing for Biotechnology, 361–376. © 2001 Kluwer Academic Publishers. Printed in the Netherlands.
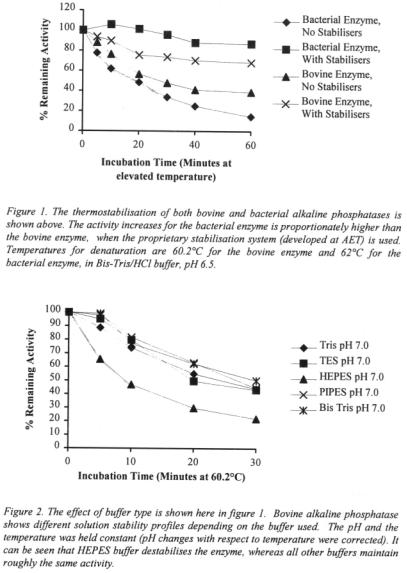