
книги / Сварка в машиностроении. Т. 3
.pdfи *> 900* Сопутствующий подогрев в основном замедляет ш30о» Изменения t> 9Ü0
^ 5бо и до30о по-разному влияют на структуру и сопротивляемость стали трещинам в зависимости от состава й характера ее сварочной анизотермической диаграммы превращения аустенита [24]. Для углеродистых и низколегированных сталей, не содержащих карбидообразующих элементов, с низкой устойчивостью аусте нита при температурах перлитного превращения (стали 45, 20Г2, 18Г2ФА и др.) наиболее важным является показатель tt;650. Это объясняется тем, что практи чески для всех способов сварки, повышая q/v и вводя подогрев, изменением а>5Б0 можно получить перлитную или заданную смешанную структуру, стойкую против трещин. Влияние t> 900 незначительно, так как связанные с ним процессы гомо
генизации и роста зерна успевают завершиться за короткое время и не поддаются регулированию тепловыми воздействиями. Для среднеуглеродистых среднелеги рованных сталей, содержащих карбидообразующие элементы, с высокой устой чивостью аустенита при температурах перлитного и бейнитного превращения (ЗОХГСНА, 42Х2ГСНМА, 43ХЗСНМФА и др.), при сварке в широком диапазоне тепловых режимов характерно мартенситное превращение аустенита. Для этих сталей рекомендуется сопутствующий подогрев до температур несколько выше конца мартенситного превращения с целью уменьшения доаоо и обеспечения само-
отпуска мартенсита. Важным является уменьшение / > 900, поскольку высоко
температурные процессы замедлены в связи с наличием карбидов в исходной структуре и имеется возможность регулирования величины зерна и однородности аустенита. Поэтому рекомендуется применять концентрированные источники тепла и многослойную сварку и не рекомендуется предварительный подогрев. Для низкоуглеродистых среднелегированных сталей с повышенным содержанием никеля (12ХН4МДА, 18Х2НЗМДА и др.), имеющих высокую устойчивость аусте нита при температурах перлитного превращения, при сварке в широком диапазоне тепловых режимов характерно превращение в области нижнего бейнита и частично в области мартенсита. Эти стали занимают промежуточное положение по сравне нию с рассмотренными выше группами сталей. При их сварке рекомендуется умеренный подогрев до 100— 150 °С, не вызывающий существенного увеличения t > ооо и вместе с тем понижающий ку550 с целью смещения бейнитного превраще ния в область более высоких температур и уменьшения количества мартенситной составляющей. Полезен сопутствующий подогрев для самоотпуска мартенситной составляющей и удаления диффузионного водорода из сварного соединения. Отпуск сварных соединений проводят главным образом для среднеуглеродистых среднелегированных сталей при температурах 300—650 °С. Важным является время начала отпуска после сварки, которое составляет от 0,5 до 2 ч. При назна чении температуры сопутствующего подогрева и отпуска необходимо учитывать возможность развития процессов отпускной хрупкости и термического старения.
'2. Предварительная термическая обработка стали с целью получения в ис ходной структуре устойчивых коагулированных легированного цементита и спе циальных карбидов. Такой термической обработкой может быть отжиг на зернис тый перлит при Т « Ас} — 25 °С в течение 4— 16 ч в зависимости от содержания углерода и карбидообразующих элементов [21]. Отжиг является эффективным способом повышения сопротивляемости трещинам для сталей, содержащих С > 0 ,3 0 % , и карбидообразующих элементов (Сг, Mo, W, V и др.) в сумме более 1%. При сварке замедленное растворение карбидов ограничивает рост зерна и снижает степень гомогенизации аустенита, что повышает начало превращения аустенита на 100—200 °С и обусловливает образование бейнитно-мартенситной структуры вместо мартенситной.
3. Применение сварочных материалов с возможно более низкой температурой кристаллизации металла шва [10, 22]. Выбор материалов рекомендуется произво дить по соотношению ЛТ= ТЛш0. м — ТСшм. ш (где Тл,0. м и Тс. м. — температуры ликвидуса основного металла и солидуса металла шва соответственно). При завер шении кристаллизации шва околошовная зона испытывает высокотемпературный перегрев вследствие выделения теплоты затвердевания. При применении свароч-
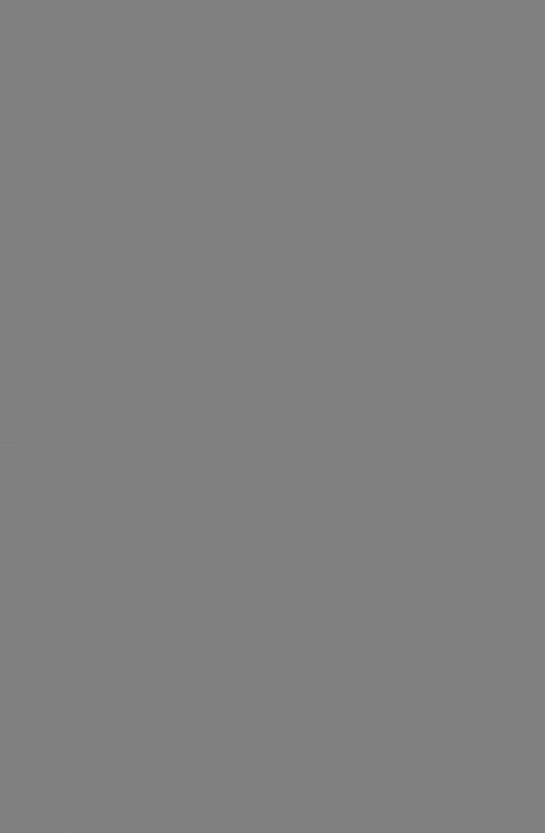
ных материалов с высокой Тс.м. ш перегрев приводит к полному расплавлению участка основного металла у линии сплавления протяженностью один—два зерна (см. рис. 21, а) и последующую полную его гомогенизацию. В результате в этой локальной зоне образуется напряженный низкотемпературный мартенсит без следов самоотпуска с очень низкой сопротивляемостью трещинам (рис. 30, а). При АТ > 8 0 °С отрицательное действие перегрева не проявляется и обеспечи вается высокая сопротивляемость околошовной зоны трещинам. Лучше всех этому соотношению при сварке низко- и среднелегированных сталей удовлетво ряют аустенитные сварочные материалы с большим запасом аустенитности типа 10Х16Н25М6 (ЭА-981/15, ЭА-395), а также высокопрочные легированные матери алы типа 20Х2Г2НМВА (электрод Н-17), 15ХГ2МВ1А (электрод НИАТ-ЗМ). Для определения температур кристаллизации сталей рекомендуется метод термо кинетического анализа применительно к дуговой сварке [8].
4. Снижение содержания водорода в наплавленном металле: 1) прокалкой электродов при 450—480 °С и флюсов при 500—900 °С в течение не менее 3 ч, осушением защитных газов, если их точка росы выше —55°, пропусканием их через осушитель, заполненный силикагелем или другими поглотителями влаги; 2) тщательной очисткой свариваемых кромок и сварочной проволоки от масла, ржавчины и конденсированной влаги; 3) применением при абсолютной влажности воздуха выше 12— 14 г/м3 способов сварки, которые характеризуются минималь ным захватом воздуха дугой; лучшими в этом отношении являются аргонодуговая и сварка под флюсом; 4) замедлением охлаждения сварного соединения путем сопутствующего подогрева и последующего отпуска при 200—300 °С.
5.Снижение уровня сварочных напряжений различными конструктивными
итехнологическими способами, в том числе проковкой, прокаткой и опрессовкой швов и сварных соединений.
СПИСОК ЛИТЕРАТУРЫ
1.Вакуумный метод определения диффузионного водорода применительно к руч ной сварке. /А. М. Левченко. Е. П. Озеров. Г. Л. Петров и др. Труды ЛПИ № 336, 1974,
с.3—6.
2.Винокуров В. А. Сварочные деформации и напряжения. М., Машиностроение, 1968. 233 с.
3.Выбор технологии сварки, обеспечивающей стойкость сварных соединений про
тив образования холодных трещин. /Э. |
Л. |
Макаров, В. Ф. Чабуркин, Л. С. Лившиц |
|
в др. — Сварочное производство, 1972, |
Nb |
8. с. 30—32 |
|
4. |
Горячие трещины при сварке жаропрочных сплавов. /М. X. Шоршоров, А. А. Еро |
||
хин, Т. |
А. Чернышова. М., Машиностроение, 1973. 223 с. |
б.Зимина Л. Н. Свариваемые жаропрочные никелевые сплавы и принципы их леги
рования. — Металловедение и термическая обработка металлов. 1977. № 11, с. 2—7.
6.Козлов Р. А. Водород при сварке корпусных сталей. Л., Судостроение, 1969.
175 с.
7.Конищев Б. П., Полынин Г. Е., Якушин Б. Ф. Оценка стойкости металла про
тив образования и развития горячих трещин при сварке. — Сварочное производство, 1977, № 7. с. 12-13.
8.Макаров Э. Л., Меньшинин С. В. Устройство для определения температуры кри сталлизации сплапов при дуговой сварке. — Автоматическая сварка, 1975, № 3, с. 47—49.
9.Макаров Э. Л. Природа разрушения при образовании «холодных» трещин в вы сокопрочных закаливающихся сталях при сварке. Труды МВТУ № 248. Прогрессивная
технология конструкционных материалов. 1977, с. 85— 105.
10.Макаров Э. Л., Федоров В. Г. К вопросу о выборе электродных материалов для сварки высокопрочных сталей. Труды МВТУ № 167. Прогрессивная технология конструк ционных материалов. 1973, с. 104—108.
11.Макаров Э. Л. Микроскопическая химическая неоднородность в сварных соеди нениях среднелегированных сталей. Труды МВТУ № 202. Прогрессивная технология
конструкционных материалов. |
1976, |
с. 92— 103. |
12. Макаров Э. Л., Лазько В. Е. Сравнительная оценка свариваемости среднелеги |
||
рованных сталей. — Сварочное |
производство, 1977, № 12, с. 29—31. |
|
13. Морочко В. П., Сорокин Л. И., |
Панов Ю. П. Влияние режима электроннолучевой |
сварки жаропрочных никелевых сплавов на их склонность к образованию горячих тре щин. Материалы конференции «Электроннолучевая сварка». МДНТП, 1978, с. 120— 124.
14. Новиков H. Н., Макаров Э. Л., Калмыков В. С. Методы и результаты исследова ний технологической прочности при сварке на образцах с имитацией сварочного термоде формационного цикла. Сб. МВТУ № 248. Прогрессивная технология конструкционных материалов. 1977, о. 66—84.
15.Носовский Б. И., Якушин Б. Ф., Прохоров H. Н. Влияние сварочного цикла на прочность аустенитных сталей при рабочих температурах. — Сварочное производство, 1972, Ня 3. с. 1 -3 .
16.Оценка стойкости металла шва против образования горячих трещин при сварке магистральных трубопроводов. /В. Ф. Чабуркин, Jl. С. Лившиц, А. С. Рахманов и др. —
Сварочное производство, 1972, Ht 2, |
с. 13—17. |
17. Повышение технологической |
прочности при сварке под флюсом за счет введения |
порошкообразного присадочного металла. / — г>. Ф. Якушин, И. И. Ивочкин, Ю. А. Чер
нов и др. — Сварочное |
производство, 1974, N? 10, с. |
16—17. |
18. Прохоров H. Н., |
Якушин Б. Ф., Бардокин Е. В. |
Количественная оценка склонно' |
стн металла околошовной зоны сварных соединений к разрушению при повторном на греве. Известия вузов, 1976, Ня 11, с. 141 —144.
19.Прохоров H. Н. Физические процессы в металлах при сварке. T. 11. М., Металлур гия, 1976, с. 599.
20.Прохоров H. Н.. Орлов А. С. Исследование свойств и применимости проб для оценки технологической прочности металлов в процессе кристаллизации при сварке. —
Сварочное производство, |
1970, Ne 12, с. |
39—42. |
|
|
|
21. Технологическая прочность металлов при сварке. Справочник по сварке. T. 111. |
|||||
М., Машиностроение, 1970, с. 504. |
металлов и сплавов плавлением. |
Под ред. |
|||
22. Технология электрической сварки |
|||||
Б. Е. Патока. М., Машиностроение, 1974, с. 768. |
сварке под |
флюсом |
|||
23. Технологическая |
прочность соединения, |
полученного при |
|||
с порошкообразным присадочным металлом стали |
16Г2АФ больших толщин. /Б. Ф. Яку |
||||
шин, В. П. Тихонов, И. И. Ивочкин и др. — Сварочное производство, |
1977, Ht 10, с. 4—7. |
24.Шоршоров М. X. Металловедение стали и сплавов титана. М., Наука, 1964, с. 336.
25.Эйдельштейн В. Е., Якушин Б. Ф., Столбов В. И. Высокотемпературная дефор мация и образование околошовных трещин при сварке сплава типа Ннмоник. — Автома
тическая сварка, 1976, № 11, с. 40—44.
26. Якушин Б. Ф., Чернавский Д. М. Влияние режима сварки на высокотемператур ную деформацию металла шва. — Сварочное производство, 1975, № 6, с. 9—11.
27.Якушин Б. Ф., Мисюров А. И., Фирсова Р. И. Закономерности развития высоко температурных деформаций при сварке. Труды МВТУ На 248. Прогрессивная техноло гия конструкционных материалов. 1977, с. 4—18.
28.Якушин Б. Ф. Определение температурного интервала хрупкости и пластично сти затвердевающего металла шва. Сб. Автоматизация, механизация и технология про
цессов |
сварки. |
М., |
Машиностроение, 1966, с. 213—219. |
|
29. |
Якушин Б. Ф. О достоверности критериев и способов оценки технологической |
|||
прочности |
металлов |
в процессе кристаллизации при сварке. — Сварочное производ |
||
ство, 1971, |
№ |
6, с. |
11 —14. |
|
30. |
Якушин Б. Ф., Тихонов В. П. Получение швов с переменным фазовым составом |
|||
по сечению. — Сварочное производство, 1978, Ня 5, с. 3—6. |
||||
31. |
Якушин Б. Ф. Оценка технологической прочности в зависимости от режимов |
|||
сварки. — Сварочное |
производство, 1969, № 1, с. 19—23. |
|||
32. |
Якушина Г. |
М., Макаров Э. Л., Рыжов H. М. Связь очагов холодных трещин |
||
со структурой |
металла шва высокопрочных сталей. — Сварочное производство, 1973, |
№5, с. 4—6.
33.Elliot D. N. A fractographical examination on lamellar tearing in multlrun fillet
welds. Metal Construction. N 29, 1969, ps. 50—57.
34.Inagakl M. Effects of restraint and hydrogen on root cracking of nigh strength steel welds. Doc. J. J. W. IX — 408—64.
35.Ito Y., Bessyo K. A prediction of welding procedure to avoid heat effected zone cracking. Doc. J. J. W. IX —631—69.
36.Klhara H. Weld cracking tests of high strength steels and electrodes. Welding Journal. N 1, 1962, ps. 36—48.
37.Lundin C. D., Spond D. F. The nature and morphology of fissures in austenitic sta
inless steel weld metals. Welding Journal. N 11, 1976, }s. 356—367.
38.Stern J. L., Qudttrone K. A multiple test approach to the prediction of weldment cracking. Welding Journal. N 5, 1967, ps. 203—216.
39.Tamura H., Watanaba T. Mechanism of liguation cracking in weld heat affected
zone of high strength steel. Trans, of Japan Welding Society, vol. 4., N 2, 1973, ps. 3— 10.
40.The determination of hydrogen in mild and low alloy steel weld metals. Doc. J. J. W P — A — 275—70.
41.Velkov K., Christov S. Technologies skûSka tupého spoja s odstupnovanou tuho stou na zistovanie odolnostl zvarovÿch spojov proti praskavosti za studena. Zvaranie, N 5. 1974, ps. 138-142.
Г л а в а 15
ОРГАНИЗАЦИЯ И ЭКОНОМИКА СВАРОЧНОГО ПРОИЗВОДСТВА
;
ДЛИТЕЛЬНОСТЬ ПРОИЗВОДСТВЕННОГО ЦИКЛА ИЗГОТОВЛЕНИЯ СВАРНЫХ КОНСТРУКЦИЙ (сложного процесса)
Длительность производственного цикла изготовления сварных конструкции (Гц. св. кон) — календарный период времени между запуском в производство исходных материалов (заготовок) и выпуском конструкции в готовом виде. Дли тельность этого цикла складывается из длительностей циклов заготовительных
Тц.заг, обрабатывающих 7 ц. 0бр» сборочных 7 ц. сб, сварочных |
7 Ц. СН, отделочных |
7 Ц. отд и естественных 7 Ц. ест частичных процессов, времени |
на контроле 7 K0Ht |
транспортные Ттр операции и времени межоперационного пролеживания изго
товляемой сварной |
конструкции и |
ее элементов 7 пер: |
Та. св. кон == 7ц.заг + |
Т'ц. обр + Тц. сб + |
Тл. св + Т1иотд + Та. сст+ Tкон + Tтр+ Тпср. |
Длительность производственного цикла сварной конструкции зависит от количества и способа сочетания во времени (последовательный, параллельно последовательный, параллельный) входящих в него простых процессов (рис. 1 и 2).
В производственных условиях (см. рис. 2) простые процессы одного и того же сложного процесса изготовления сварной конструкции сочетаются во времени одновременно тремя указанными выше способами, а 7 Ц. СВ. кон равна максимальной сумме длительностей циклов простых взаимосвязанных процессов:
где 7 Ц/ — длительность производственного цикла i-го простого процесса, входя щего в наибольшую (максимальную) сумму длительностей циклов простых свя занных между собой процессов; m — число процессов, входящих в максимальную по длительности «цепочку» циклов.
Длительность производственного цикла изготовления конструкции М опре деляется суммой длительности циклов по цепочке М — Ус11 — Ь в (рис. 2). Дли
тельность производственного цикла простых процессов зависит от числа и степени одновременности протекания входящих в них операций.
При последовательном способе сочетания операций во времени длительность
производственного цикла (в |
календарных днях) |
||
т |
___ |
m |
|
у |
|||
1 ц. поел---Q |
|||
где ■ ÿ — коэффициент перевода рабочих дней в календарные (257 : 365 « 0,7); |
m — число операций в данном процессе; п — число заготовок (деталей) в партии; /к — штучно-калькуляционное время, мин.; с — число единиц оборудования или рабочих мест, занятых одновременно выполнением данной операции; s — сменность работы; — продолжительность рабочей смены; tw.0 — длительность межоперационных перерывов в сменах; tecT — длительность естественных про цессов, ч.
где |
— операционный |
|
цикл операции, наиболее продолжительной по |
||
длительности выполнения (из |
всех операций процесса). |
||||
|
Параллельный способ получил наибольшее применение при синхронном |
||||
процессе, характеризующемся |
наличием следующего равенства: |
||||
|
^Kl |
|
^КЗ |
_ |
turn _ |
|
C1 |
ca |
^ 5 --- .. |
,. ÇZo |
- i=&Г1 |
|
*3 |
|
cm |
где г — такт поточной линии. Числа от 1 до m при tKи с соответствуют порядко вому номеру операций и рабочих мест поточной линии.
Рис. 3. Длительность производственного цикла при параллельном со четании операций синхронного процесса (в условиях потока)
Длительность производственного цикла синхронного процесса представлена на рис. 3. Длительность цикла обработки каждой из четырех транспортных пар тий (plf р2, р3. р Д на которые разделена изготовляемая партия деталей в лшт, равна
m m m
r u-p= T ,p f* = £ p rc= r£ p c-
1 1 1
Длительность же производственного цикла изготовления партии деталей на потоке Тц. пот определяется по формуле
m |
m— 1 |