
книги из ГПНТБ / Монтаж и эксплуатация подшипниковых узлов Е. Г. Рабинер. 1960- 16 Мб
.pdfклассам точности, приведены в каталогах и справочниках по под шипникам качения.
Полученные размеры шейки по каждому сечению не должны выхо
дить за пределы поля допуска для посадки, указанной в чертеже.
Фиг. 13. Схема измерений посадочного места |
вала: |
|
|
/ — III — последовательность измерений по длине; |
1—3 — последо |
|
|
вательность измерений по окружности. |
|
поса |
|
Шейку необходимо измерять в нескольких местах по длине |
|||
дочного места (количество измерений зависит |
от |
длины |
шейки |
и ее диаметра, а также от ответственности узла) и не менее чем в трех местах по окружности, поворачивая при
этом |
мерительный |
инструмент |
на |
120°. |
|
|||||
Примерная схема измерений |
посадочного |
|
||||||||
места вала приведена на фиг. |
13. |
|
|
|||||||
|
Измерения |
в нескольких |
местах дадут |
|
||||||
возможность |
|
установить |
равномерность |
|
||||||
обработки посадочного места по всей длине |
|
|||||||||
и |
выявить |
возможные |
отклонения, а |
|
||||||
именно овальность (dmax — dmin) |
и |
конус |
|
|||||||
ность |
(rfmax — Clmin)- |
ОвЭЛЬНОСТЬ |
ПОСЭДОЧ- |
Фиг. 14. Схема измерений |
||||||
ного |
места |
на |
валу может |
быть |
также |
конусного посадочного места. |
||||
проверена при |
обработке |
вала |
на станке |
|
||||||
и |
проверке |
прямолинейности |
вала в цен |
|
||||||
трах |
(см. фиг. |
19). |
|
|
|
|
|
|
Допускаемые отклонения от правильной геометрической формы посадочных поверхностей валов и отверстий корпусов для подшип ников качения приведены в табл. 8.
Проверка геометрической формы конусного посадочного места
на шейке вала производится по краске при помощи специального калибра или внутреннего кольца подшипника. Насаженный от руки калибр должен плотно прилегать к посадочной шейке вала на поверх*
ности не менее 75% общей ее величины. Калибр следует поворачи
вать на угол ^90°.
Диаметры d2 и шейки вала (фиг. 14) должны изготовляться с отклонениями по посадке скольжения С3а по ОСТу НКМ 1017.
39
Таблица 8
|
|
|
|
|
|
Классы точности |
|
|
|
||
Допускаемые отлонения |
|
подшипников |
|
|
| |
валов1 |
|||||
посадочных мест валов |
|
Н, п и |
в |
| |
А и С |
вз, Вза, в4 |
|||||
и отверстий корпусов |
|
||||||||||
|
|
|
|
|
|
не более |
|
|
|
|
|
По овальности |
|
1 |
допуска |
на |
диа |
1 |
допуска |
на |
диа |
||
|
|
|
у |
— |
|||||||
|
|
|
метр |
в любом |
сечении |
метр |
в |
любом |
сечении |
||
|
|
|
посадочной поверхности |
посадочной поверхности |
|||||||
По конусности (разность |
1 |
допуска на диаметр |
1 |
допуска |
на |
диа |
|||||
диаметров в крайних сече |
— |
— |
|||||||||
ниях |
посадочной |
поверх |
посадочной поверхости |
метр посадочной поверх |
|||||||
ности) |
|
|
|
|
|
|
ности |
|
|
|
|
1 |
Для посадки |
шарико- |
и роликоподшипников на |
закрепительно-стяжных |
(буксовых) втулках.
Допускаемая непрямолинейность образующей конической поверх ности шейки вала приведена в табл. 9.
Радиальное биение конической шейки вала допускается не более
|
|
Таблица 9 |
Наименьший диаметр d2 |
Непрямолинейность |
|
Свыше |
До |
Не более |
80 |
80 |
0,01 |
120 |
0,015 |
|
120 |
180 |
0,020 |
180 |
260 |
0,025 |
260 |
360 |
0,030 |
0,25 допуска на диаметр вала.
Резьба на концах кони ческих шеек валов выпол няется по 2-му классу точ ности, ОСТ НКТП1256. (с 1/1 1960 г. вводится новый
ГОСТ 9253-59).
Волнистость посадочных поверхностей шеек валов про веряется лекальной линей кой по световой щели. Более точно выявить неровности на
поверхности посадочных мест |
можно |
при помощи |
лекальной |
|
линейки по краске. Для этого длинную узкую грань |
точной |
|||
лекальной линейки покрывают |
тонким |
слоем краски, после чего |
||
прикладывают ее к поверхности шейки |
в продольном направлении |
|||
и, слегка нажимая на линейку, |
перемещают ее вдоль шейки. |
Затем |
||
линейку снимают и по следам |
краски |
на шейке определяют со |
||
стояние ее поверхности. |
|
|
|
|
Ни в коем случае не следует допускать к монтажу валы с посадоч |
||||
ными местами, имеющими овальность, |
конусность, |
выпуклость |
||
и впадины больше установленного допуском предела, а |
также валы |
|||
с грубо обработанными посадочными местами. |
|
|
Подшипник должен плотно охватывать вал, чтобы сохранялась необходимая посадка во время эксплуатации.
40

подшипника вместо необходимой посадки с натягом. Этот подшипник
разрушился и почернел из-за сильного нагрева, в результате кото рого получился отпуск металла. Посадочная поверхность внутрен
него кольца покрылась круговыми задирами.
В тех случаях, когда шейка не подвергается закалке, следы сколь
жения |
придают ей вид гладко отполированной поверхности |
|
(фиг. |
16, |
б). |
|
|
В практике нередки случаи, когды валы с чрезмерно ослаблен ными посадочными местами допускают к монтажу, ошибочно думая, что осевое крепление подшипника гайкой или иным способом предо хранит внутреннее кольцо от проворачивания. Этого делать не сле
дует, так как осевое крепление внутреннего кольца подшипника, свободно сидящего на валу, не устраняет опасности отставания
кольца по валу при его вращении, а следовательно, и описанных
выше последствий.
Нельзя также допускать к монтажу валы, шейки которых имеют больший диаметр, чем это предусмотрено по чертежу, так как посадка ’подшипника может получиться с чрезмерным натягом. При посадке с чрезмерным натягом внутренние кольца подшипников ввиду сравнительно малой толщины их стенок расширяются, вследствие этого радиальный зазор между телами качения и кольцами подшип ника (внутренним и наружным) соответственно уменьшится и может произойти заклинивание тел качения, т. е. зазор будет полностью устранен, а ролики или шарики окажутся зажатыми между коль цами. Такой подшипник будет иметь очень тугой ход, сильно нагре ваться и быстро разрушится.
Особенно большое влияние это явление оказывает на радиальные
шарикоподшипники, которые имеют сравнительно малый радиаль ный зазор. По экспериментальным данным увеличение диамётра
внутреннего кольца составляет около 0,7 величины посадочного натяга, а усадка вала — около 0,3 натяга; уменьшение, диаметра наружного кольца составляет около 0,4 натяга, а расширение кор пуса — около 0,6 натяга.
В случае необходимости частого демонтажа подшипника, что
иногда вызывается особыми условиями работы узла, конструкторы назначают более слабые посадки, чем при нормальных условиях.
Если в этих условиях требуется смонтировать подшипник на вал
несколько большего диаметра, чем это предусмотрено по чертежу, то частый монтаж и демонтаж подшипников, особенно больших габаритных размеров, будет значительно усложнен; поэтому необ ходимо строго придерживаться обусловленных чертежом размеров
идопусков. К монтажу следует допускать только проверенные валы,
укоторых посадочные места обработаны точно по указанным в рабо чих чертежах размерам и допускам.
Лучшим способом доводки посадочных мест вала, оказавшегося слишком большим по размеру, является шлифование. В практике очень часто посадочные места доводят наждачным полотном или напильни ком. Применение этого способа крайне нежелательно, так как, поль
зуясь им, только очень опытный работник может достигнуть удовлетво-
42
рительных результатов, не причинив серьезных повреждений поса дочным местам. Большая часть валов, которые доводятся до нужных размеров наждачным полотном или напильником, не имеет правиль ной цилиндрической формы и правильных размеров. Поэтому если из за особых обстоятельств все же пользуются указанным способом,
то после доводки необходимо тщательно проверить посадочные места по всей длине, чтобы не допустить поврежденный вал к монтажу.
|
Кроме |
проверки |
диаметра |
посадоч |
|||
|
ных мест |
на |
валу, |
нужно также • |
про |
||
|
верять правильность их обработки по |
||||||
|
длине и расстояние между заплечиками |
||||||
В» |
посадочных |
шеек. |
|
неправильная |
|||
Во многих |
случаях |
||||||
|
обработка посадочного места по длине |
||||||
|
может нарушить при сборке компоновку |
||||||
|
сопряженных |
с подшипником |
деталей |
||||
|
узла в части совпадения |
смазочных |
ка- |
Максимальная длина шейки Минимальная длина шейки
Поле
дописка
Фиг. 17. Невозможность регулировки осевой игры
подшипников в результате превышения длины поса дочного места оси ваго нетки.
Фиг. 18. Шаблон для |
проверки длины шейки оси: |
1 |
— риска. |
налов (доступа смазки в подшипник),
возможности установки уплотняющих устройств, регулировки ПОДШИПНИКОВ И Т.'!д.
Особое значение эта проверка имеет в опорах с радиально-упор ными подшипниками регулируемых типов.
На фиг. 17 изображен один из таких примеров: в результате превышения длины размера посадочного места на оси невозможно осуществить регулировку конических подшипников в колесе ваго нетки, так как регулировочная гайка не может поджать внутрен
нее кольцо подшипника. Если не устранить этот дефект, то в зави симости от величины зазора неизбежны ненормальная работа или аварийное разрушение подшипника, а возможно и всего подшипни кового узла. Поэтому в таких случаях вал необходимо подрезать на станке или установить между торцами гайки и подшипника спе циальное кольцо или прокладку. В особо важных случаях длину шейки измеряют специальными шаблонами.
На фиг. 18 показан шаблон с контрольными рисками для изме рения длины шейки оси роликоподшипниковой буксы тендера паро
воза.
43
Для осуществления правильной регулировки у валов зубчатых
передач, работающих на радиально-упорных подшипниках, следует проверять расстояние Ls между упорными заплечиками мест посадки подшипников (фиг. 19).
Фиг. 19. Проверка вала в центрах.
Допуски на |
длину |
между |
упорными |
заплечиками |
приведены |
в табл. 10. |
|
|
|
Таблица 10 |
|
Интервалы длины |
Отклонение |
Интервалы длины |
Отклонение |
||
в мм |
|
в |
мм |
||
|
|
в мм |
|
|
в мм |
свыше |
ДО |
|
свыше |
ДО |
|
50 |
80 |
0,100 |
630 |
710 |
0,310 |
80 |
120 |
0,140 |
710 |
800 |
0,330 |
120 |
180 |
0,160 |
800 |
900 |
0,350 |
180 |
260 |
0,185 |
900 |
1000 |
0,380 |
260 |
360 |
0.215 |
1000 |
1120 |
0,410 |
360 |
500 |
0,250 |
1120 |
1250 |
0,440 |
500 |
560 |
0,270 |
1250 |
1400 |
0,470 |
560 |
630 |
0,290 |
1400 |
1560 |
0,520 |
На практике нередки случаи, |
когда в |
результате |
неправильной |
транспортировки и хранения валы искривляются. |
искривленных |
||
Монтаж подшипников на |
посадочные места |
||
валов вызывает ненормальную |
работу |
подшипников, приводит |
к преждевременному их разрушению и нередко даже к серьезным авариям всего агрегата.
Необходимо, чтобы оси поверхностей посадочных мест строго совпадали с осью вращения вала. Поэтому перед проверкой поса дочных мест следует проверять прямолинейность валов (особенно
длинных).
Если в результате проверки будет установлено, что вал не отве чает требованиям прямолинейности или посадочные места в резуль тате неправильной обработки имеют эксцентричность, то такие валы
44
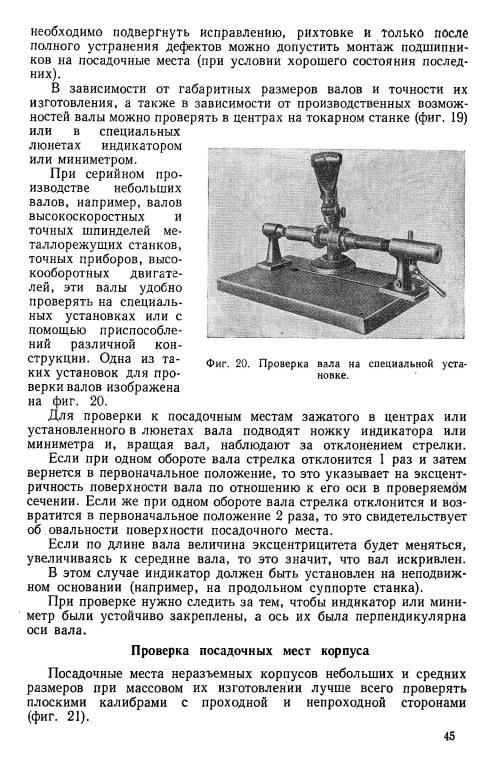
При измерении проходная сторона калибра должна свободно
проходить в отверстие корпуса, а непроходная совсем не должна входить в те части корпуса, которые служат местом посадки под шипников.
В остальных случаях для измерения следует использовать инди
каторный нутромер или штихмасс. |
При |
значительных |
диаметрах |
||||
|
|
расточки, как, например, |
|||||
|
|
посадочных мест |
подшипни |
||||
|
|
ков |
в |
подушках прокатных |
|||
|
|
станов, для измерений при |
|||||
|
|
меняются сборные штихмассы |
|||||
|
|
различной |
конструкции. |
||||
|
|
Для |
выявления |
оваль |
|||
|
|
ности |
и |
конусности |
поса |
||
|
|
дочные места, подобно шей |
|||||
Фиг. |
Проверка посадочного отверстия |
кам валов, необходимо изме |
|||||
21.корпуса плоским калибром. |
рять в нескольких местах по |
||||||
|
|
длине посадочного места в за |
|||||
|
|
висимости от длины и диа |
|||||
|
|
метра |
расточки и |
не |
менее |
||
чем в трех местах по окружности, поворачивая при этом |
меритель |
||||||
ный |
инструмент каждый раз на 120°. |
|
|
|
|
|
Полученные размеры по каждому сечению не должны выходить за пределы поля допуска для посадки, указанной в чертеже корпуса.
$2
Фиг. 22. Схема измерений посадочного места корпуса:
/, II и III— последовательность измерений по длине; 1—3 — по следовательность измерений по окружности.
Примерная схема измерений посадочных мест корпуса приведена на фиг. 22.
Допускаемые отклонения от правильной геометрической формы посадочных поверхностей отверстий корпусов для подшипников качения приведены в табл. 8.
Волнистость посадочных мест корпусов проверяется при помощи лекальной линейки или по краске, описанным выше способом.
46
Отверстия малых диаметров могут быть измерены также при помощи набора специальных телескопических штихмассов и микро метра.
Телескопический штихмасс по конструкции весьма прост и может быть изготовлен почти в любом инструментальном цехе (фиг. 23).
При |
измерении отверстия |
предварительно |
ГГ: |
|||
сжатый стержень штихмасса |
вводится |
в него |
||||
и закрепляется стопором |
(фиг. 24, |
а), |
затем |
' ! ' |
||
при помощи микрометра определяется факти- |
Е |
|||||
ческий |
диаметр отверстия |
(фиг. 24, б). |
|
s
Фиг. 23. Телескопический штихмасс для измерения отверстий небольших диаметров.
Ни в коем случае нельзя допускать к монтажу корпусы, поса дочные места которых имеют овальность или конусность, выходя щие за пределы допусков, указанных на рабочих чертежах, а также
Фиг. 24. Измерение диаметра отверстия:
а — штихмассом; б — микрометром.
корпусы, имеющие ослабленные посадочные места, так как это может резко снизить долговечность подшипника.
Во избежание неправильных показаний мерительный инстру мент перед проверкой посадочных мест следует обязательно прове рять по эталонам-калибрам и в процессе измерения периодически контролировать.
47
Желательно, чтобы при измерении температура мерительного инструмента и измеряемых деталей была одинаковой.
Перед проверкой точности посадочных мест в разъемных корпу
сах необходимо проверить плоскости разъема корпусов. Плоскости разъема должны быть тщательно обработаны и плотно
прилегать одна к другой так, чтобы между ними не было зазора. Плотность прилегания плоскостей разъема проверяется щупом. Для проверки половины корпуса до отказа затягиваются болтами
и затем щупом проверяется стык по всей поверхности его соприкаса
ния |
(фиг. 25). |
Если пластинки |
щупа толщиной 0,03 |
или |
0,05 |
|
|||||||
|
|
|
(в |
зависимости |
от габаритных |
разме |
|||||||
|
|
|
ров и |
степени ответственности данного |
|||||||||
|
|
|
узла) |
проходят |
на |
незначительной |
|||||||
|
|
|
площади |
относительно |
величины |
всей |
|||||||
|
|
|
плоскости разъема, то корпус счи |
||||||||||
|
|
|
тается годным и можно приступить к |
||||||||||
|
|
|
проверке посадочных мест. |
|
|
|
|||||||
|
|
|
|
Если же проверка покажет, что пло |
|||||||||
|
|
|
скости обработаны неудовлетворительно, |
||||||||||
|
|
|
поверхности |
их |
недостаточно |
гладки |
|||||||
|
|
|
и соприкасаются на нескольких незна |
||||||||||
Фиг. 25. Проверка плотности |
чительных площадях, |
то такой |
корпус |
||||||||||
соединения плоскостей разъема |
необходимо |
разобрать |
и |
плоскости |
|||||||||
корпуса при помощи щупа. |
разъема |
пришабрить |
по |
контрольной |
|||||||||
|
|
|
плитке |
под |
краску. |
|
|
в |
резуль |
||||
|
|
|
|
Необходимо учесть, что |
|||||||||
стей |
разъема, |
имеющих |
тате опиливания и шабрения |
плоско- |
|||||||||
дефекты, |
посадочное |
отверстие |
кор |
мм
пуса после скрепления двух его половин болтами может принять
овальную форму вследствие уменьшения его диаметра на величину, соответствующую слою металла, снятого с плоскостей разъема. Поэтому после опиливания или шабрения плоскостей разъема надо пришабрить посадочные места, что допустимо только в том слу
чае, если диаметр посадочного места уменьшился на незначительную величину. Если же диаметр значительно уменьшился вследствие того, что плоскости разъема были сильно повреждены и для их испра вления пришлось снять большой слой металла, то такое посадочное место следует исправлять только на станке.
Часто монтажники проверяют посадочные места в разъемном
корпусе до проверки плотности соединения половин корпуса и,
убедившись в правильности и точности их изготовления, не считают необходимым исправлять посадочное место, даже если после проверки плоскостей разъема последние для исправления были подвергнуты шабрению. В этом случае после установки подшипника в корпус в местах его разъема до полной затяжки соединительных болтов образуется некоторый зазор (фиг. 26).
При сильном затягивании крышки корпуса болтами (что необ
ходимо) наличие такого зазора вызовет деформацию наружного кольца подшипника, т. е. подшипник будет зажат и станет оваль-
48