
Outlook / Логистика 2013 дневники
.pdf
Корректировка плана-маршрута |
|
|
|
|
||
Оптимизация по результатам проверки |
|
|
|
|||
|
Ф1 |
Ф2 |
Ф3 |
|
Ф4 |
Предл. |
|
4 |
3 |
5 |
— |
6 |
|
|
+ |
|
|
|
|
|
Т1 |
|
|
100-50= |
100 |
||
50 |
|
|
||||
|
|
|
50 |
|
||
|
8 |
2 |
4 |
|
7 |
|
Т2 |
|
100 |
75 |
|
25 |
200 |
|
|
|
|
|||
|
1 |
2 |
2 |
|
1 |
|
Т3 |
— |
|
|
+ |
35+50 |
85 |
50-50=0 |
|
|
|
|||
|
|
|
|
|
||
|
|
|
|
=85 |
|
|
|
|
|
|
|
|
|
Спрос |
50 |
100 |
75 |
|
160 |
S=385 |

Проверка нового плана-маршрута на оптимальность
|
Ф1 |
Ф2 |
Ф3 |
Ф4 |
Предл. |
1. Потенциалы для |
|
|||||
|
заполненных ячеек: |
|
||||||||||
|
|
|
|
|
|
|
|
|
|
|
||
|
|
4 |
|
3 |
|
5 |
|
6 |
|
Р11 = U1+V1 = C11 = 4 |
|
|
Т1 |
50 |
|
|
|
|
50 |
100 |
|
||||
|
|
|
|
Р14 = U1+V4 = C14 = 6 |
|
|||||||
|
|
|
|
|
|
|
||||||
|
|
|
|
|
|
|
|
|
|
P22 = U2+V2 = C22 = 2 |
|
|
Т2 |
|
8 |
|
2 |
|
4 |
|
7 |
200 |
P23 = U2+V3 = C23 = 4 |
|
|
|
|
|
|
|
||||||||
|
|
100 |
75 |
25 |
P24 = U2+V4 = C24 = 7 |
|
||||||
|
|
|
|
P34 = U3+V4 = C34 = 1 |
|
|||||||
|
|
|
|
|
|
|
|
|
|
|
||
Т3 |
|
1 |
|
2 |
|
2 |
|
1 |
85 |
Находим |
U1 = 0 |
V1 = 4 |
|
|
|
|
|
|
85 |
||||||
|
|
|
|
|
|
|
|
все Ui и Vj |
U2 = 1 |
V2 = 1 |
||
Спрос |
50 |
100 |
75 |
160 |
S=385 |
|
U3 = -5 |
V3 = 3 |
||||
|
|
V4 = 6 |
||||||||||
|
|
|
|
|
|
|
|
|
|
|
|
2. Разница ( ) потенциала и «тарифа» для незаполненных ячеек
=Р12 - C12 = U1+V2 - C12 = 0+4-4 = 0
=Р13 - C13 = U1+V3 - C13 = 0+3-5 = -2 <0
=Р21 - C21 = U2+V1 - C21 = 1+4-8 = -3 <0
=Р31 - C31 = U3+V1 - C31 = -5+4-1 = -2 <0
=Р32 - C32 = U3+V2 - C32 = -5+1-1 = -5 <0
=Р33 - C33 = U3+V3 - C33 = -5+3-1 = -3 <0
Все <0 или =0
Все потенциалы незаполненных ячеек меньше «тарифов» на их использование
План-маршрут оптимален
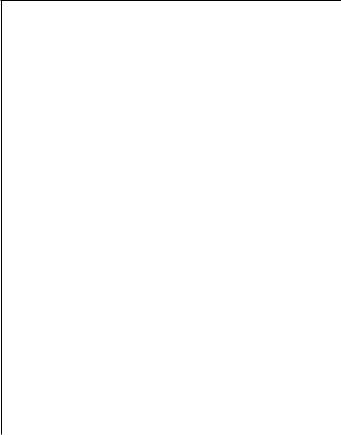
Управленческие решения на основе транспортных задач:
Планирование внутрипроизводственных
транспортных потоков
Планирование внешних транспортных потоков
предприятия
Создание планов сбыта продукции
Расчет потребности в ресурсах на реализацию транспортировки
Выбор схемы сбыта или снабжения предприятия (подразделения)

Пример расчета трудоемкости развоза груза по транспортному плану-маршруту
|
Ф1 |
Ф2 |
Ф3 |
Ф4 |
Предл. |
||||
|
|
|
|
|
|
|
|
|
|
|
|
4 |
|
3 |
|
5 |
|
6 |
|
Т1 |
50 |
|
|
|
|
50 |
100 |
||
|
|
|
|
|
|
||||
|
|
|
|
|
|
|
|
|
|
Т2 |
|
8 |
|
2 |
|
4 |
|
7 |
200 |
|
|
100 |
75 |
25 |
|||||
|
|
|
|
||||||
|
|
|
|
|
|
|
|
|
|
Т3 |
|
1 |
|
2 |
|
2 |
|
1 |
85 |
|
|
|
|
|
|
85 |
|||
|
|
|
|
|
|
|
|
||
Спрос |
50 |
100 |
75 |
160 |
S=385 |
||||
|
|
|
|
|
|
|
|
|
|
Xij — количество груза, который поставляет i-й источник j-му потребителю
Гр — грузоподъемность транспортной тележки
Cji - «тариф», время перевозки груза от i-го источника к j-му потребителю
Тп-р — время погрукзки-разгрузки одной тележки
Трудоемкость перевозки заготовок:
Тпер = Σ ОКРВВЕРХ( Хij / Гр ) х Cij = (50/25)х4 + (50/25)х6 + (100/25)х2 + (75/25)х4 +
+ (25/25)х7 + ОКРВВЕРХ(85/25)х1 = 2х4 +2х6 + 4х2 + 3х4 + 1х7 + 4х1 = 51 ч-мин
Трудоемкость погрузки-разгрузки:
Тп-р = Σ ОКРВВЕРХ( Хij / Гр ) х Тп-р = (2+2+4+3+1+7+4) х 3 = 23х3=69 ч-мин.
Общая трудоемкость:
Т=Тпер + Тп-р = 51+69 = 120 ч-мин или 2 человеко-часа
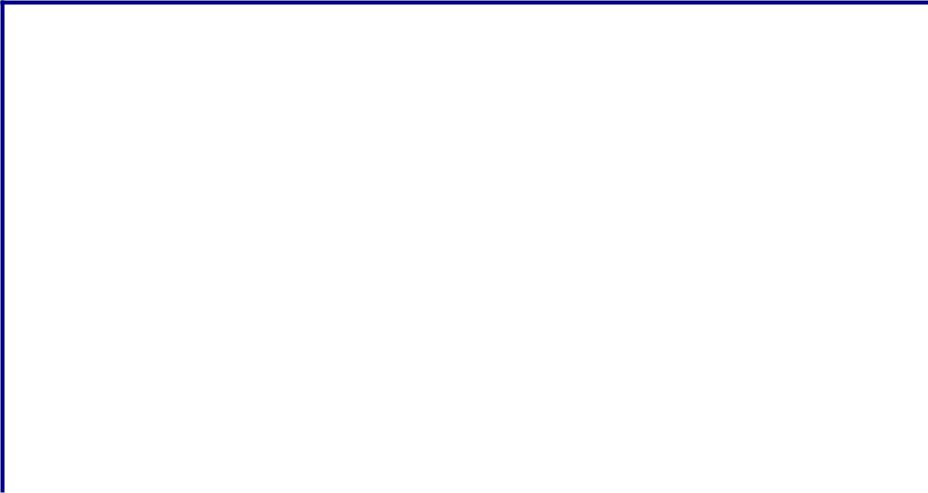
2.Составление расписания последовательной обработки партии различных деталей на двух и более машинах при помощи АЛГОРИТМА ДЖОНСОНА
Каждая работа состоит из операций: обработка детали на первом станке, затем на втором станке и т.д.
Временем перехода между операциями пренебрегают как незначительным Каждая операция должна быть завершена прежде, чем начнется следующая
1.Формируют таблицу исходных данных, где указывают время обработки каждой детали обрабатываемой партии на каждой машине
2.Время обработки детали на первой машине выстраивается по возрастанию таким образом, чтобы время обработки на последующих машинах шло по убыванию. Таким образом, общее время обработки всех деталей партии на первой (первых) машине будет компенсировать простои ожидания обработки на второй (последующих) машине
Оптимизация осуществляется путем взаимной перестановки деталей партии в расписании. В конечном итоге получают оптимальное расписание обработки партии деталей с минимальными простоями машин

Пример применения алгоритма Джонсона при составлении оптимального расписания последовательной обработки партии из шести различных деталей на двух станках
Данные о времени обработки деталей:
№ детали |
1 |
2 |
3 |
4 |
5 |
6 |
Время обработки |
|
|
|
|
|
|
детали на первом |
8 |
6 |
3 |
5 |
10 |
2 |
станке, мин. |
|
|
|
|
|
|
Время обработки |
3 |
4 |
7 |
4 |
2 |
5 |
детали на втором |
||||||
станке, мин. |
|
|
|
|
|
|
Перед проведением оптимизации была составлена временная диаграмма обработки деталей при неоптимальном (исходном, по порядку) расписании обработки партии

Временная диаграмма при неоптимальном, исходном расписании обработки деталей
Деталь №1 |
Деталь №3 |
Деталь №5 |
Деталь №2 |
Деталь №4 |
Деталь №6 |
|
|
|
|
|
|
|
|
Время |
|
|
|
|
|
|
|
|
|
8 |
6 |
3 |
5 |
|
10 |
2 |
|
обработки |
|
|
|
|
|
|
|
|
на станке 1 |
3 |
|
4 |
|
7 |
4 |
2 |
5 |
Время |
|
|
обработки |
||||||
|
|
|
|
|
|
|
|
на станке 2 |
8 |
3 |
3 |
Время |
|
|
|
простоев |
Общее время обработки последовательно 6 деталей на двух станках:
8+3+3+4+7+4+3+2+5 = 39 мин.
Их них время простоя оборудования: 8+3+3 = 14 мин.

Оптимизация порядка обработки деталей:
Деталь, не закрепленную за определенным местом, имеющую минимальный элекмент в первой строке, переносим на первое свободное место.
Деталь, не закрепленную за определенным местом, имеющую минимальный элекмент во второй строке, переносим на последнее свободное место.
№ детали |
6 |
3 |
2 |
4 |
1 |
5 |
|
|
|
|
|
|
|
|
|
Время обработки |
2 |
3 |
6 |
5 |
8 |
10 |
|
детали на станке 1, мин. |
|||||||
|
|
|
|
|
|
||
|
|
|
|
|
|
|
|
Время обработки |
5 |
7 |
4 |
4 |
3 |
2 |
|
детали на станке 2, мин. |
|||||||
|
|
|
|
|
|
||
|
|
|
|
|
|
|
Порядок обработки деталей:
Деталь №6 Деталь №3 Деталь №2 Деталь №4 Деталь №1 Деталь №5
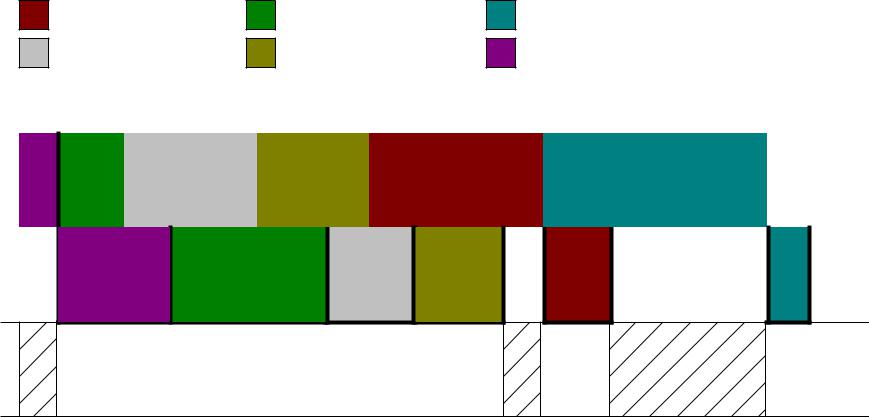
Временная диаграмма при оптимальном расписании обработки деталей
Порядок обработки деталей: Д 6 - Д 3 - Д 2 - Д 4 - Д 1 - Д 5
Деталь №1 |
Деталь №3 |
Деталь №5 |
Деталь №2 |
Деталь №4 |
Деталь №6 |
|
|
|
|
|
|
|
|
|
|
|
|
|
|
Время |
|
|
|
|
|
|
|
|
|
|
|
|
|
|
|
||
|
2 |
3 |
|
|
6 |
|
5 |
|
|
8 |
|
10 |
|
обработки |
|
|
|
|
|
|
|
|
|
|
|
|
|
|
|
на станке 1 |
|
|
|
|
|
|
|
|
|
|
|
|
|
|
|
|
|
|
|
|
5 |
|
7 |
|
4 |
4 |
3 |
2 |
Время |
||||
|
|
|
|
|
обработки |
||||||||||
|
|
|
|
|
|
|
|
|
|
|
|
|
|
на станке 2 |
2 |
2 |
7 |
Время |
|
|
|
простоев |
Общее время обработки последовательно 6 деталей на двух станках: |
До применения оптимизации: 39 минут (из них 14 минут простоя) После применения оптимизации: 2+5+7+4+4+2+3+7+2=36 минут Из них время простоя: 2+2+7 = 11 минут
Оптимизация проведена успешно

II Решение стохастических задач календарного планирования при помощи теории массового обслуживания
Доведение случайной величины, характеризующей работу производственного участка, до некоего среднего значения
Заказы поступают на машины случайным образом
и образуют очередь
Машины имеют приоритет обработки заказов (первый пришел-первый ушел и т.д.), называемый
дисциплиной обслуживания
Дисциплина обслуживания определяет, какой из заказов пойдет на первую освободившуюся машину