
3535
.pdf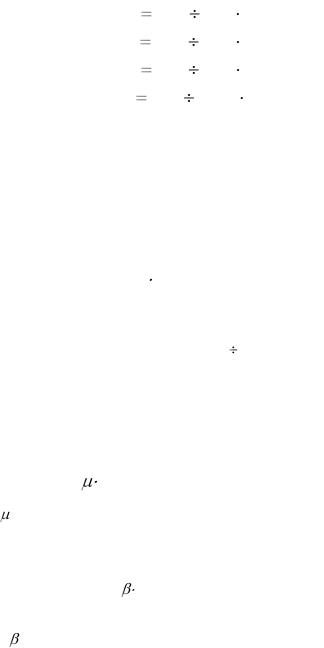
Fhчерн |
(0,6 |
0,8) |
Fzчерн , |
Fvчерн |
(0,6 |
0,7) |
Fzчерн , |
Fyчерн |
(0,3 |
0,4) |
Fzчерн , |
Fxчерн |
(0,5 |
0,55) |
Fzчерн . |
Горизонтальная составляющая силы резания Fhчерн, Н, определяет усилие, которое необходимо приложить для осуществления рабочей подачи.
Для линейного перемещения салазок шпинделя двигатель подачи должен обеспечивать усилие подачи Fпод, Н, которое в равно сумме усилия резания, трения и прилипания /5/
|
Fпод=k Fh+F тр+Fпр, |
(1.108) |
где |
Fh – горизонтальная составляющая усилия резания, |
|
Н; |
|
|
|
k – коэффициент запаса, k = 1,2 1,5; |
|
|
Fтр – усилие трения стола о направляющие, Н; |
|
|
Fпр – усилие прилипания, Н. |
|
|
Усилие трения салазок шпинделя |
определяется их |
массой и массой привода главного движения m, кг,
составляющими усилия резания Fy |
и Fz, направленными |
|
нормально к направляющим, Н |
|
|
|
Fтр= (g·m+ Fv+Fz ) |
(1.109) |
где |
– коэффициент трения стола о направляющие; |
|
|
g – ускорение свободного падения, g = 9,8 м/с2. |
|
|
Усилие прилипания возникает при трогании салазок с |
|
места в начале движения |
|
|
|
Fпр= Sпр |
(1.110) |
где |
Sпр – площадь поверхности прилегания, см2; |
|
|
– удельное усилие прилипания, 0,5 Н/см2 /5/. |
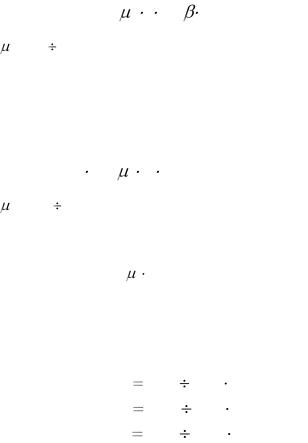
Все составляющие усилия подачи одновременно не действуют, подача производится вхолостую до начала процесса резания. Поэтому при определении нагрузки двигателя подачи рассматривают отдельно два характерных режима его работы: трогание с места и рабочую подачу.
При трогании с места (режим холостого хода) действуют только усилие трения от массы перемещающихся частей механизма подачи и усилие прилипания, возникающее в начале трогания. Усилие подачи при трогании салазок шпинделя
|
Fтр= т g m+ Sпр |
(1.111) |
где |
т=0,2 0,3 – коэффициент трения в направляющих |
|
при трогании с места /5/. |
|
При рабочей подаче в процессе резания, когда салазки шпинделя уже движутся с установившейся скоростью, усилие подачи определяется усилием резания и трения по формуле
|
Fпод=k Fx+ д (g m+Fy+Fz |
(1.112) |
где |
д=0,05 0,15 – коэффициент трения в направляющих |
|
при движении, k =1,5 – коэффициент запаса /5/. |
|
|
|
На быстром ходу усилие определяют по формуле |
|
|
Fпод.бх= д g·m |
(1.113) |
Значения составляющих силы резания при попутном несимметричном фрезеровании
торцевой фрезой находят из /11/:
Fhчист |
(0,2 |
0,3) Fzчист , |
Fvчист |
(0,9 |
1,0) Fzчист , |
Fyчист |
(0,3 |
0,4) Fzчист , |
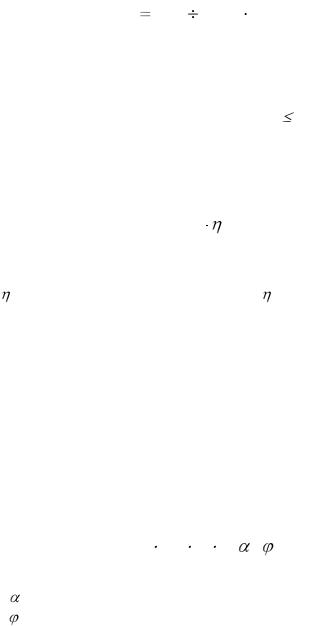
Fxчист (0,5 0,55) Fzчист .
Проверка выбранного режима резания по использованию мощности на шпинделе станка
Мощность, затрачиваемая на резание, должна быть меньше или равна мощности на шпинделе N Nшп, где N – эффективная мощность резания, кВт; Nшп – допустимая мощность на шпинделе, определяемая по мощности привода.
Мощность на шпинделе определится по формуле
Nшп = Nэ |
(1.114) |
где Nэ– мощность электродвигателя привода |
главного |
движения резания, кВт; |
|
– КПД механизмов привода станка, = 0,85. |
|
Расчет статического и динамического моментов
Общий вращающий момент двигателя М складывается
из статического Мс и динамического моментов Мд |
|
||
|
М=Мс+Мд. |
|
(1.115) |
Статический |
момент |
определяется |
усилием, |
передаваемым в направлении подачи при установившемся движении органа станка.
От усилия подачи на валу ходового винта подачи
возникает момент Мхв /5/ |
|
Мхв=0,5 Fпод dср tg( + ), |
(1.116) |
где dср – средний диаметр ходового винта, мм;
–угол наклона резьбы ходового винта, град;
–угол трения резьбы, град.
Угол наклона резьбы ходового винта определяется диаметром винта и шагом его нарезки по формуле
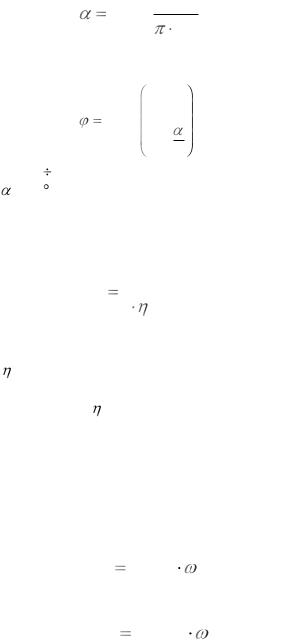
t
arctg , (1.117)
dср
где t – шаг ходового винта, мм. Угол трения резьбы равен
arctg |
f |
, |
(1.118) |
|
|
cos 2
где f = 0,1 0,15 – коэффициент трения /10/; = 30 – угол наклона резьбы.
Вращающий момент на валу ходового винта определяет момент статического сопротивления на валу двигателя подачи
М |
|
|
М хв |
, |
(1.119) |
с |
i |
|
|||
|
|
|
|
||
|
|
пер |
|
|
|
|
|
|
|
|
где i – передаточное отношение от двигателя к ходовому винту;
пер – КПД передач от двигателя к ходовому винту. По рекомендации /5/ КПД передачи винт-гайка
качения c натягом =0,85. Найдем величины статических моментов, соответствующие режимам трогания, холостому ходу режиму резания при черновой и чистовой обработке. Для этого подставим соответствующие величины в формулу
(1.119).
Мощность черновой обработки Pчерн , Вт, равна
произведению момента, развиваемого двигателем на его скорость при черновой обработке
P |
M |
счерн |
1 |
, |
|
(1.120) |
|
черн |
|
|
|
|
|||
Мощность чистовой обработки P |
, Вт, равна |
||||||
|
|
|
|
|
|
чист |
|
P |
M |
счист |
|
2 |
, |
(1.121) |
|
чист |
|
|
|
|
|
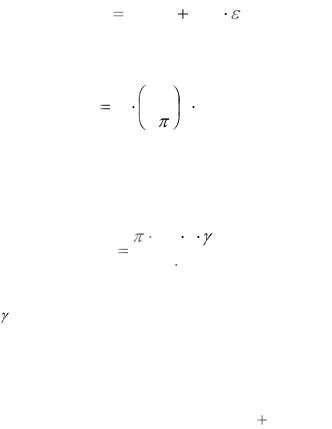
Динамический момент на двигателе определяется суммарным моментом инерции механизма, приведенным к валу двигателя Jмех пр, и собственным моментом инерции двигателя Jдв.
Mд (Jмехпр Jдв ) . |
(1.122) |
Момент инерции линейно-перемещающегося узла (кг·м2), приведенный к валу двигателя, равен согласно /5/
|
t |
2 |
1 |
|
|
J m |
|
, |
(1.123) |
||
2 |
|
i2 |
|||
|
|
|
|
где m – масса узла станка;
i – передаточное отношение коробки подач.
Момент инерции винта, приведенный к валу двигателя Jв.пр , рассчитывается по формуле
|
d 4 |
l |
|
|
Jв пр |
ср |
|
, |
(1.124) |
32 i2 |
где dср– средний диаметр винта, м; l – длина винта, м; =7700 кг/м3 – плотность стали.
Суммарный момент инерции механизма, приведенный к валу двигателя, равен
Jмех пр=Jст пр+Jв пр, |
|
|
(1.125) |
|
Коэффициент отношения масс |
g= |
J1 |
J2 |
не должен |
|
J1 |
|||
|
|
|
|
превышать 1,2 – 2. Здесь J1 – момент инерции двигателя, J2
– момент инерции механизма, приведенный к валу двигателя.
Тогда при g=1,2 приближенно можно принять Jдв =5 J2. Линейное ускорение салазок шпинделя а = 0,8 м/с2.
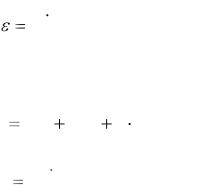
При линейном законе движения ускорение двигателя равно
а i
|
(1.126) |
|
t |
||
|
Динамический момент вычисляем по формуле (1.122). Время цикла работы привода подачи равно (с)
tц tчерн tчист 4 tбх , |
(1.127) |
Время обработки детали на станке, с,
t |
|
60 Lдет |
, |
(1.128) |
о |
|
|||
|
sm |
|
||
|
|
|
По формуле (1.128) с учетом параметров резания определяется время черновой и чистовой обработки детали на станке.
Время работы двигателя в режиме быстрого хода определяется длиной детали и скоростью
быстрого хода.
По найденным значениям момента и скорости в процессе обработки детали строятся нагрузочная диаграмма (рис. 1.20) и тахограмма (рис. 1.21) привода подачи при торцевом фрезеровании.
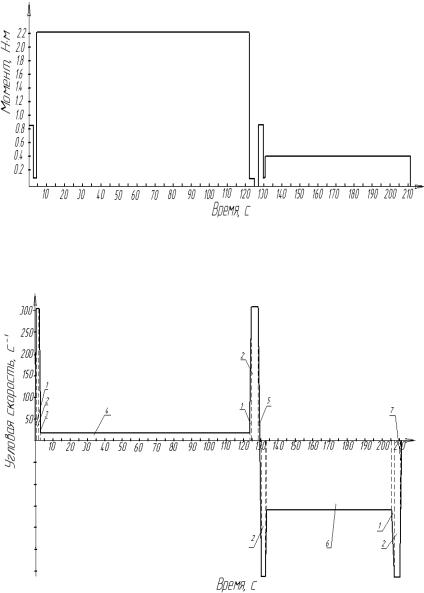
Рис. 1.20. Нагрузочная диаграмма привода подачи при торцевом фрезеровании
Рис. 1.21. Тахограмма привода подачи при торцевом фрезеровании:
1 – разгон двигателя; 2 – быстрый ход; 3 – врезание фрезы;
4 – черновое фрезерование; 5– реверс двигателя; 6 – чистовое фрезерование; 7 – торможение
Расчет мощности электродвигателя привода подачи при торцевом фрезеровании принципиально не отличается в случае
фрезерования цилиндрическими фрезами.
Двигатель должен проходить по нагреву для полученной диаграммы нагрузки методом средних потерь для случая асинхронного двигателя и методом эквивалентных значений, если применяется ДПТ с регулированием скорости.
Двигатель должен также проходить по допустимой
кратковременной перегрузке Мmax≤ mдМном, где Мmax- максимально возможный в рабочем цикле момент, Мном -
номинальный момент выбранного двигателя; mд - коэффициент допустимой перегрузки.
4. ЭЛЕКТРОПРИВОД НАСОСНЫХ УСТАНОВОК
Насосы являются одним из наиболее распространѐнных видов машин с разнообразным конструктивным исполнением.
Насосы представляют собой гидравлические машины, предназначенные для перемещения жидкости под напором. Таким образом, поток жидкости на выходе из насоса обладает большей энергией, чем на входе в него.
Преобразуя механическую энергию приводного двигателя в механическую энергию движущейся жидкости, насосы поднимают еѐ на определѐнную высоту, подают на необходимое расстояние в горизонтальной плоскости или заставляют циркулировать в какой-либо замкнутой системе /27/.
Выполняя одну или несколько указанных функций,
насосы входят в состав основного оборудования насосных
станций или установок.
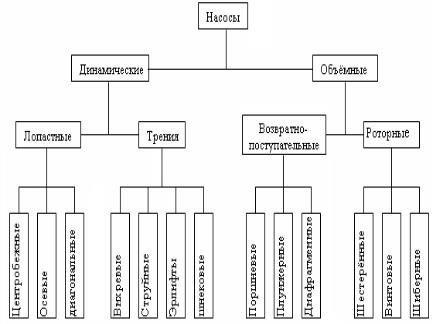
История возникновения и развития насосов показывает, что первоначально они предназначались исключительно для подъѐма воды. Однако в настоящее время область их применения настолько широка и разнообразна, что определение насоса как машины для перекачивания воды было бы односторонним. Помимо водоснабжения и канализации городов, промышленных предприятий и электростанций насосы применяются для орошения и осушения земель, гидроаккумулирования энергии, транспортирования материалов. Существуют питательные насосы котельных установок тепловых электростанций, судовые насосы, насосы для нефтяной, химической, бумажной, пищевой и других отраслей промышленности.
4.1.Классификация насосов
Сточки зрения различия в принципе действия все существующие насосы могут быть разделены на два вида: динамические и объѐмные
(рис. 4.1).
В динамических насосах жидкость движется под силовым воздействием в камере постоянного объѐма, сообщающейся с подводящими и отводящими устройствами. В зависимости от вида силового воздействия на жидкость динамические насосы, в свою очередь, делятся на лопастные и насосы трения.
Рис.4.1. Классификация насосов
Объѐмные насосы работают по принципу вытеснения жидкости из камеры за счѐт уменьшения еѐ объѐма. Периодическое изменение объѐма камеры происходит за счѐт возвратно-поступательного или вращательного движения рабочего органа насоса. Попеременное заполнение камеры перекачиваемой жидкостью и еѐ опорожнение обеспечиваются клапанными устройствами входного и выходного патрубков насоса.
Классификация по конструктивному исполнению приведена в табл. 4.1 /27/.
|
|
|
|
|
Таблица 4.1 |
||
|
Классификация насосов по конструктивному исполнению |
|
|
||||
|
|
|
|
||||
№ |
Название насоса |
Конструктивное исполнение и |
|
||||
|
|
|
особенности |
|
|
||
1 |
2 |
|
|
3 |
|
|
|
1 |
Горизонтальный |
Ось вращения рабочих органов, |
|||||
|
|
например |
|
рабочих |
колес, |
||
|
|
расположена |
горизонтально |
вне |
|||
|
|
зависимости |
от |
расположения |
оси |
||
|
|
привода или передачи. |
|
|
|||
2 |
Вертикальный |
Ось вращения |
|
рабочих |
органов |
||
|
|
расположена вертикально. |
|
|
|||
3 |
Консольный |
Рабочие органы |
расположены |
на |
|||
|
|
консольной части вала. |
|
|
|||
4 |
Моноблочный |
Рабочие органы расположены на валу |
|||||
|
|
двигателя. |
|
|
|
|
|
5 |
С выносными |
Подшипниковые опоры изолированы |
|||||
|
опорами |
от перекачиваемой среды. |
|
|
|||
6 |
С внутренними |
Подшипниковые |
|
|
опоры |
||
|
опорами |
соприкасаются |
с |
перекачиваемой |
|||
|
|
жидкостью. |
|
|
|
|
|
7 |
С осевым входом |
Жидкость подводится в направлении |
|||||
|
|
оси рабочих органов. |
|
|
|||
8 |
С боковым входом |
Жидкость подводится в направлении, |
|||||
|
|
перпендикулярном |
оси |
рабочих |
|||
|
|
органов. |
|
|
|
|
|