
3535
.pdf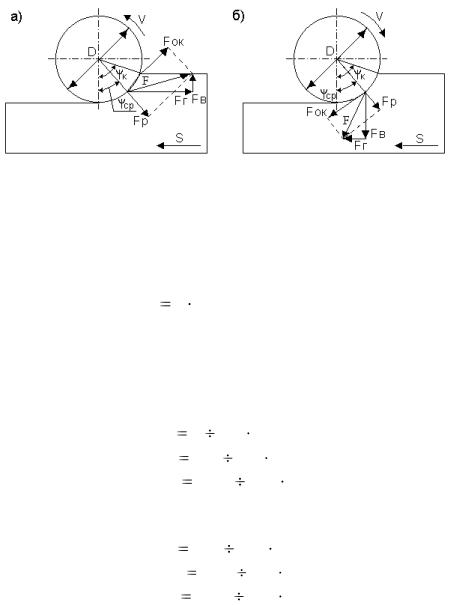
Рис. 1.15. Схемы действия сил при встречном (а) и попутном (б) цилиндрическом фрезеровании
Окружная сила резания равна, кГ, |
|
FOK p Scp , |
(1.80) |
Значения отдельных составляющих силы резания можно определить, зная FOK /11/.
При встречном фрезеровании
цилиндрическими фрезами:
FГ |
(1 1,2) FОК , |
|
|
FВ |
(0,2 |
0,3) FОК , |
|
FР |
(0,35 |
0,4) |
FОК . |
При попутном фрезеровании |
|||
цилиндрическими фрезами |
|||
FГ |
(0,8 |
0,9) FОК , |
|
FВ |
(0,75 |
0,8) |
FОК , |
FР |
(0,35 |
0,4) |
FОК . |
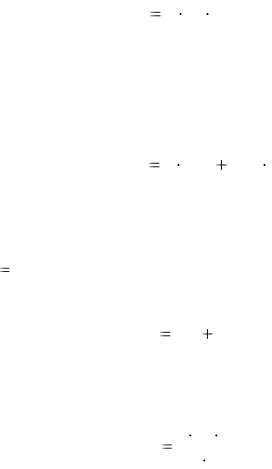
Горизонтальная составляющая силы резания FГ
определяет усилие, которое необходимо приложить к столу станка для осуществления рабочей подачи.
Составляющая усилия подачи от усилия резания при черновом фрезеровании, Н,
Fрез k FГ g , |
(1.81) |
где k – коэффициент запаса (обычно k=1-1.5); g – ускорение свободного падения,
Составляющая усилия подачи от сил трения в направляющих скольжения со смазкой,
Н,
Fтр g (m1 m2 ) fтр , |
(1.82) |
где m1 - масса перемещающегося узла станка, кг; m2 - масса заготовки, кг;
fтр - коэффициент трения скольжения (обычно
fтр 0,1).
Усилие подачи по горизонтальной оси при черновом фрезеровании, Н,
Fпод Fрез Fтр , |
(1.83) |
Скорость вращения двигателя при
черновой обработке, с-1, равна
w1 |
2 sm |
i |
|
|
|
|
, |
(1.84) |
|
60 d |
|
|||
|
|
|
|
где i – передаточное число редуктора.
Подачи при чистовом фрезеровании цилиндрическими фрезами из быстрорежущей стали при параметре шероховатости обрабатываемой поверхности Ra=1.6 мкм
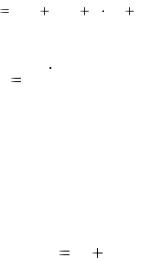
следует брать из диапазона Sz=1,0-3,8 мм в зависимости от диаметра фрезы и типа обрабатываемого материала. Глубина резания при чистовой обработке t=0,1-2 мм /3/.
Расчет ведется в той же последовательности, что и при черновой обработке (формулы 1.77…1.84).
Время цикла работы привода подачи стола определяют по формуле
tц tчерн tчист 2 tбх tси . |
(1.85) |
Время обработки детали на станке, с,
tо |
60 Ld |
. |
(1.86) |
|
sm |
||||
|
|
|
Время работы двигателя в режиме быстрого хода складывается из времени t п - времени
подвода стола с заготовкой к фрезе и t р - времени
перемещения стола в исходное состояние перед началом чистового фрезерования
tбх |
tn |
tp . |
Время смены инструмента tси = 30 с.
Наконец, находят время цикла работы привода подачи по формуле 1.85.
Расчет радиальной и вертикальной составляющей силы резания проводятся аналогично расчету горизонтальной составляющей по методике, изложенной в /11/.
Требования к приводу подачи
Требования к электроприводам и системам управления станками определяются технологией обработки, конструктивными возможностями станка и режущего инструмента.
Основными технологическими требованиями направлены на обеспечение:
-широкого круга технологических режимов обработки
сиспользованием современного режущего инструмента;
-максимальной производительности; наибольшей точности обработки;
-высокой чистоты обрабатываемой поверхности;
-высокой степени повторяемости размеров деталей в обрабатываемой партии (стабильности) /5/.
Удовлетворение всем этим и другим требованиям зависит от характеристик станка и режущего инструмента, мощности главного привода и электромеханических свойств приводов подач и систем управления.
При всем многообразии станков требования, предъявляемые к приводам станков, определяются главным образом не тем, к какой группе относится станок, а для какого движения предназначен привод: главного, подач или вспомогательного. Именно это определяет мощность, способ и диапазон регулирования скорости, необходимую плавность регулирования, требования к жесткости стабильности характеристик, требования к динамике /12/. Полный диапазон регулирования в станках фрезерной группы составляет 100-10000.
В последние годы существенно изменилась конструкция станков вследствие значительного сокращения механической части приводов подач. В ряде случаев стала возможной установка высокомоментных двигателей, имеющих меньшие габаритные размеры по сравнению с обычными двигателями постоянного тока (ДПТ) с электромагнитным возбуждением, непосредственно на ходовой винт. Исключение коробки передач привело не только к сокращению механической части привода, но также и к повышению КПД и снижению момента инерции электромеханического привода. В связи с этим снизилась нагрузка на двигатель при холостых перемещениях и возросла составляющая от резания в общей нагрузке приводов подач. В большинстве современных станков средних размеров нагрузка на двигатель при рабочих

подачах без резания составляет не более (20-30) % номинальной нагрузки. Рост составляющей от сил резания в общей нагрузке на привод подачи увеличил колебание нагрузки на электроприводе подачи при резании, что ужесточило требование к статической и динамической жесткости привода подачи.
Определенные требования к приводу подач накладывается системой числового управления (ЧПУ). В частности, скорость быстрых перемещений зависит от характеристик механической части привода, максимальной частоты сигнала управления приводов от системы ЧПУ /13/, дискретности управления, максимальной частоты вращения приводного электродвигателя, коэффициента редукции передачи от двигателя к механизму, коэффициента усиления по скорости следящего привода и максимального значения ошибки, запоминаемой системой ЧПУ. В соответствии с предельными характеристиками передач винт-гайка качения определяются максимальная требуемая частота вращения двигателя и максимально допустимое ускорение, представляющее отношение максимального вращающего момента к собственному моменту инерции винта. Таким образом, в каждом конкретном случае может быть найдено минимально допустимое время переходного процесса по условиям механической прочности передачи винт-гайка качения.
Для электроприводов подач изменение частоты вращения при набросе и сбросе нагрузки 0,5·Мном относительно уровня 0,5·Мном не должно превышать 100 % при n = 0,001nном и времени восстановления 100 мс. Время реверса под нагрузкой Мном, n = 0,001nном не более 0,5 с /8/.
Cтабильность позиционирования и обработки в значительной степени зависит от стабильности электромеханической системы приводов подач, которая определяется стабильностью ее звеньев и, в первую очередь, привода, датчика положения и системы ЧПУ. Стабильность характеристик комплектного электропривода при
достаточно большом коэффициенте усиления определяется стабильностью входного усилителя и датчика скорости - тахогенератора. Именно поэтому в большинстве широкорегулируемых приводов, выпускаемых ведущими зарубежными электротехническими фирмами, применяются высокостабильные входные полупроводниковые усилители и устанавливаются серебряные щетки на тахогенераторе. Порядок величин, характеризующих допустимые нестабильности входного сигнала и сигнала обратной связи, можно определить из следующих рассуждений. В большинстве систем ЧПУ ошибке в 10 мм соответствует сигнал управления приводом, приблизительно равный 10 В. Таким образом, нестабильности сигнала в 1 мВ соответствует ошибка 1 мкм. А так как нестабильность привода подачи является лишь составляющей и общей доле нестабильности позиционирования и обработки, то можно судить об исключительно высоких требованиях к стабильности характеристик регулируемого электропривода.
Электроприводы подач должны обеспечить требуемый режим резания при обработке различных деталей. Значение подач должны обеспечить требуемую шероховатость поверхности, высокую стойкость инструмента, а также производительность станка. На стойкость инструмента большое влияние оказывает скорость резания, а не подача, поэтому при выборе подачи главным является качество обработанной поверхности. Электропривод подач должен обеспечить наибольшие величины ускорений. Это достигается применением быстродействующего привода и снижением приведенного момента инерции механизма подач. При проектировании следует добиваться уменьшения сил в направляющих, в передачах, в опорах и обеспечение плавности перемещения рабочих органов при малых скоростях и скачкообразном изменении скорости; исключение резонансов элементов механизма подач и всей системы электропривода.
Двигатель должен проходить по нагреву для полученной диаграммы нагрузки методом средних потерь для случая асинхронного двигателя и методом эквивалентных значений, если применяется ДПТ с регулированием скорости;
Двигатель должен также проходить по допустимой
кратковременной перегрузке Мmax≤ mдМном, где Мmax- максимально возможный в рабочем цикле момент, Мном -
номинальный момент выбранного двигателя; mд - коэффициент допустимой перегрузки.
На продольно-фрезерных станках привод подачи должен быть реверсивным и обеспечивать широкое регулирование скорости и удовлетворять основным требованиям:
-минимальные габариты двигателя при высоком вращающем моменте; высокая максимальная скорость;
-обеспечение диапазона скоростей подач стола от 10 до 3000 мм/мин;
-значительная перегрузочная способность привода; высокая стабильность характеристик тахогенератора;
-высокое быстродействие и равномерность движения;
-высокая надежность и ремонтопригодность;
-высокая экономичность и малая стоимость.
Как видно из перечисленных, а также многих других требований, совмещение всех их в одном устройстве принципиально невозможно. Поэтому при проектировании электропривода в каждом конкретном случае удовлетворение одним требованиям достигается в ущерб другим /8/.
Нагрузочная диаграмма и тахограмма
Расчет статического момента
Статический момент определяется усилием, передаваемым в направлении подачи при установившемся

движении органа станка. Момент на двигателе от силы резания для передачи рейка-шестерня определяется по формуле
Mст |
Fпод |
d |
, |
(1.87) |
2 i |
|
|||
|
|
|
|
где Fпод – усилие подачи; d – диаметр шестерни; i – передаточное отношение редуктора; - КПД зубчатой
передачи, обычно принимается =0.85 /10/.
При установившемся движении на быстром ходу статический момент равен моменту, создаваемому силами трения.
При черновой обработке статический момент на валу двигателя равен сумме моментов от усилия резания вдоль оси станка и от сил трения в подвижных звеньях механизма
Mст Mрез Mтр , |
(1.88) |
Момент на двигателе от силы резания и от сил трения при чистовой обработке также рассчитывается по (1.88).
Мощность черновой обработки (Вт) равна произведению момента, развиваемого двигателем, на его скорость при черновой обработке
Pчерн Mст1 w1 . |
(1.89) |
Мощность чистовой обработки равна
Pчист M ст 2 w2 . |
(1.90) |
Результаты расчетов целесообразно свести в табл. 1.8.
|
|
|
Таблица 1.8 |
|
|
|
|
Вид |
Скорость |
Момент на |
Мощность |
обработки |
подачи, |
двигателе, Нм |
подачи, Вт |
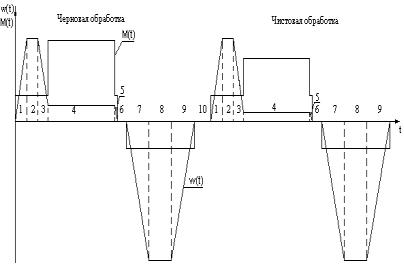
|
мм/мин |
|
|
Черновая |
w1 |
M ст1 |
Pчерн |
Чистовая |
w2 |
M ст 2 |
Pчист |
Примерный вид тахограммы и нагрузочной диаграммы работы привода подачи стола за цикл одного чернового и одного чистового прохода представлен на рис. 1.16. Для их построения использованы ранее проведенные расчеты длительности операций процесса фрезерования и соответствующих им величин статических моментов.
Рис. 1.16 Тахограмма и нагрузочная диаграмма работы электропривода продольной подачи:
1 |
– разгон двигателя; |
2 |
– холостой ход; |
3 |
– снижение скорости и врезание; 4 |
– резание; |
|
5 |
– остановка двигателя; |
6 – отвод инструмента; |
|
7 |
– разгон двигателя в обратную сторону для |
||
возвращения стола на исходную позицию; |
|||
8 |
– холостой ход (скорость быстрых перемещений); |
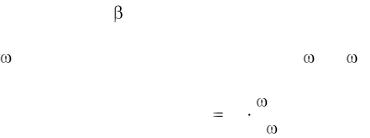
9 – торможение двигателя; 10 – смена инструмента
Расчет предварительной мощности электродвигателя
механизма подачи
По нагрузочной диаграмме M(t) и тахограмме w(t) в дальнейшем рассчитывается нагрузочная диаграмма P(t). Согласно этим нагрузочным диаграммам определяются эквивалентный момент и эквивалентная мощность. Если двигатель самовентилируемый, то его теплоотдача на отдельных интервалах тахограммы различна. Приближенно зависимость коэффициента ухудшения теплоотдачи от угловой скорости можно считать линейной /9/. По формуле (1.54) определяют коэффициент ухудшения теплоотдачи для каждого режима работы: черновая обработка, чистовая обработка, холостой ход, смена инструмента ( 0 ).
Если привести мощность при угловой скорости
i к эквивалентной мощности при |
= ном , то |
|||
используют соотношение |
|
|
|
|
P |
P |
ном |
. |
|
|
|
|||
эi |
i |
|
i
(1.91)
С учетом коэффициента ухудшения теплоотдачи скорректируем эквивалентные мощность и момент по формулам: