
3535
.pdf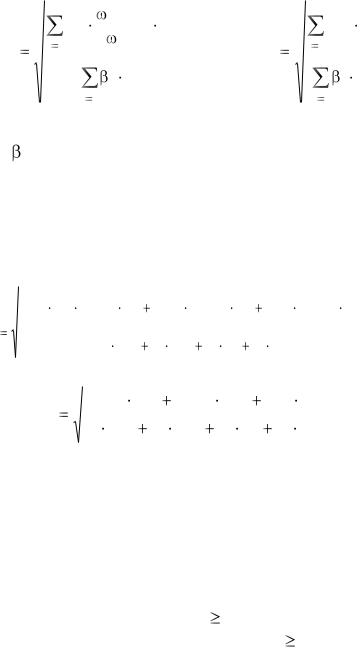
m |
|
|
|
|
m |
|
|
(P |
ном |
)2 t |
i |
|
M 2 |
t |
i |
|
|||||||
i |
|
|
|
i |
|
P |
|
i 1 |
i |
,(1.92); M |
|
i 1 |
, |
|
экв |
|
m |
|
|
экв |
m |
|
|
|
|
|
|
|
|
|
||
|
|
i |
t i |
|
|
i |
t i |
|
|
|
i 1 |
|
|
|
i 1 |
|
|
|
|
|
|
|
|
(1.93) |
||
где |
i – коэффициент ухудшения теплоотдачи на |
i-ом интервале, соответствующий значению угловой скорости на этом интервале.
По формулам (1.92) и (1.93) находим значения
эквивалентной |
|
мощности |
и |
|
|
эквивалентного |
|||||||||||||||||||||||||||
момента: |
|
|
|
|
|
|
|
|
|
|
|
|
|
|
|
|
|
|
|
|
|
|
|
|
|
|
|
|
|
|
|
||
|
|
|
|
|
|
|
|
|
|
|
|
|
|
|
|
|
|
|
|
|
|
|
|
|
|
|
|
|
|
|
|
||
|
|
(M |
|
ω |
|
ωном |
) |
2 |
t |
|
|
|
(Р |
|
ωном |
) |
2 |
|
t |
|
(Р |
|
ωном |
) |
2 |
t |
|
|
|
||||
|
|
тр |
xx |
|
ωxx |
|
бх[ |
черн |
ωчерн |
|
|
черн |
чист |
ωчист |
|
чист |
|||||||||||||||||
|
|
|
|
|
|
|
|
|
|
|
|
|
|
|
|
|
|||||||||||||||||
Pэкв |
|
|
|
|
|
|
|
|
|
|
|
|
|
|
|
|
|
|
|
|
|
|
|
|
, |
||||||||
|
|
|
|
|
β1 t черн β2 |
t чист |
β3 |
|
tбх |
β |
4 tси |
|
|
|
|
|
|
|
|
||||||||||||||
|
|
|
|
|
|
|
|
|
|
|
|
|
|
|
|
|
|
||||||||||||||||
|
|
|
|
|
|
|
|
|
|
|
|
|
|
|
|
|
|
|
|
|
|
|
|
|
|
|
|
|
|
|
|
||
|
|
|
|
|
|
|
M |
2 |
|
|
t |
черн |
М |
2 |
|
t |
чист |
М 2 |
t |
d |
|
|
|
|
|
|
|
|
|||||
|
|
M экв |
|
|
|
черн |
|
|
|
|
чист |
|
|
|
хх |
|
. |
|
|
|
|
|
|
||||||||||
|
|
|
|
β1 |
tчерн |
|
|
β2 |
tчист |
β3 |
|
tбх |
|
β4 |
t |
си |
|
|
|
|
|
|
|||||||||||
|
|
|
|
|
|
|
|
|
|
|
|
|
|
|
|
|
|
|
|||||||||||||||
При выборе номинального момента двигателя учтем |
|||||||||||||||||||||||||||||||||
коэффициент запаса |
|
|
|
|
|
|
|
|
|
|
|
|
|
|
|
|
|
|
|
|
|
|
|
|
|
|
|||||||
|
|
|
|
|
|
|
|
|
|
|
|
Мрасч=kз·Мэкв, |
|
|
|
|
|
|
|
|
(1.94) |
где kз=1,1 – коэффициент запаса.
При выборе двигателя его параметры должны удовлетворять следующим неравенствам /6/:
- по условию нагрева Рном Рэкв;
- по эквивалентному моменту Mном Мэкв;

- по перегрузочной способности Мдв.max Мmax;
- по пусковому моменту Мпуск Мб.х .
При выборе электродвигателя привода подачи необходимо еще руководствоваться и тем, что технологические режимы обработки деталей не постоянны. В зависимости от скорости резания и величины подачи в широком диапазоне меняются и силы резания. Поэтому при проектировании приводов подач продольно–фрезерных станков расчет мощности двигателя необходимо вести по наиболее тяжелым режимам фрезерования и выбирать электродвигатель с номинальной мощностью превышающей среднюю мощность обработки.
Выбор двигателя и системы управления
Исходными данными для выбора привода подачи служат:
-масса перемещаемого органа привода вместе с деталью;
-сила трения в опорах, направляющих и в передаче;
-передаточные отношения механических звеньев привода (коробки передач);
-моменты инерции механических звеньев;
-КПД механических передач;
-скорости быстрого хода и диапазон рабочих подач;
-допустимые для механизмов ускорения;
-циклограмма нагрузки двигателя при работе механизма.
Кроме того, для правильного выбора двигателя необходимо знать законы его регулирования и управления в переходных режимах. Как правило, в механизмах подач регулирование частоты вращения двигателя при постоянном моменте осуществляется изменением напряжения на якоре. Закон управления при разгоне и торможении реализуется системой управления станком. Наиболее распространенными задающими сигналами управления
являются ступенчатый и линейно-изменяющийся, однако возможны и другие формы задающих сигналов.
Система ТП-Д удовлетворяет большинству требований, предъявляемых к приводу подач. Электропривод имеет высокую точность поддержки заданных скоростей, широкий диапазон регулирования и малую инерционность. Система позволяет делать до 1000 включений, торможений и реверсов в час.
Производительность, надежность и экономичность рабочих механизмов в значительной степени зависят от правильного выбора мощности приводного двигателя.
Если выбран электродвигатель большей мощности, чем необходимо по условиям его работы, то увеличиваются капитальные затраты и снижаются КПД. Если мощность двигателя меньше необходимой, то возникает перегрев обмоток, резко снижающий срок службы двигателя.
Двигатель должен развивать момент, уравновешивающий статический момент сопротивления механизма. Во время переходных процессов электродвигатель, кроме того, должен развивать дополнительный момент, преодолевающий динамические нагрузки, обусловленные силами инерции подвижных частей механизма /6/.
В приводах подач станков широко применяются различные двигатели постоянного тока (ДПТ): с пазовым якорем и электромагнитным возбуждением, быстродействующие с гладким и печатным якорями, низкоскоростные высокомоментные двигатели с возбуждением от постоянных магнитов, бесколлекторные ДПТ (вентильные), линейные двигатели /7/.
Низкоскоростные, устанавливаемые непосредственно на ходовой вал двигатели серий 2П, ПБСТ, ПСТ, П и др., обеспечивают большее быстродействие механизма, так как их момент инерции, приведенный к винту, значительно меньше приведенного момента инерции высокоскоростных машин. И, кроме того, в силу своих конструктивных
особенностей низкоскоростные и низковольтные двигатели развивают большие динамические моменты, чем высокоскоростные высоковольтные. Но при этом значительно возрастают габариты и масса двигателя, так как при отсутствии силового редуктора существенно увеличивается момент на валу двигателя.
Электродвигатели подачи фрезерных станков имеют продолжительный режим работы с ПВ 100%, а наличие охлаждающей жидкости, смазки и металлической стружки вызывает необходимость установки двигателей защищенного исполнения.
Помимо фрезерования цилиндрическими фрезами широко применяется торцевое фрезерование, особенности которого изложены ниже.
Торцевое фрезерование
В большинстве случаев для обработки плоскостей открытых и углублѐнных применяются торцевые фрезы. При обработке плоскостей этими фрезами, основную работу по удалению припуска выполняют режущие кромки, расположенные на конической и цилиндрической поверхности. Режущие кромки, расположенные на торце, производят как бы зачистку поверхности, поэтому шероховатость обработанной поверхности получается меньше, чем при фрезеровании цилиндрическими фрезами (рис. 1.17). Зуб торцевой фрезы имеет две режущие кромки: главную и вспомогательную.
Диаметр фрезы, для сокращения основного технологического времени и расхода инструментального материала, выбирают с учѐтом жесткости технологической системы, схемы резания, формы и размеров обрабатываемой заготовки.
При торцевом фрезеровании для достижения режимов резания, обеспечивающих наибольшую производительность, диаметр фрезы D, мм должен быть больше ширины фрезерования B, мм /11/
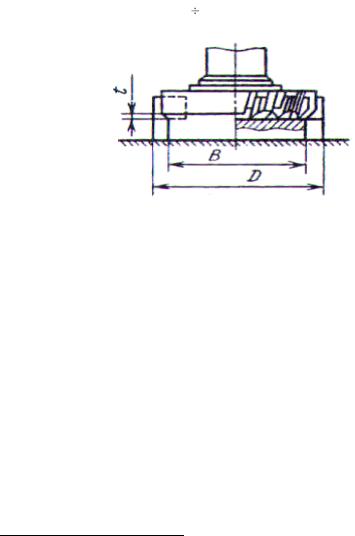
D = (1,25 1,5)·В |
(1.95) |
Рис. 1.17 – Торцевое фрезерование:
t – глубина фрезерования; B – ширина; D – диаметр фрезы
Схемы фрезерования определяются по расположению оси торцевой фрезы заготовки относительно средней линии обрабатываемой поверхности. Различают симметричное и несимметричное торцевое фрезерование
Симметричным называют такое фрезерование, при котором ось торцевой фрезы проходит через среднюю линию обрабатываемой поверхности.
Несимметричным фрезерованием называют такое фрезерование, при котором ось торцевой фрезы смещена относительно средней линии обрабатываемой поверхности.
Несимметричное торцевое фрезерование может быть встречным или попутным. При несимметричном встречном торцевом фрезеровании толщина срезаемого слоя изменяется от некоторой небольшой величины до наибольшей величины, а затем несколько уменьшается. При несимметричном попутном торцевом фрезеровании зуб фрезы начинает работать с толщиной среза, близкой к максимальной.

При торцевом фрезеровании стальных заготовок обязательным является их несимметричное расположение относительно фрезы, при этом:
-для заготовок из конструкционных углеродистых и легированных сталей и заготовок, имеющих корку (черновое фрезерование) сдвиг заготовок;
-в направлении врезания зуба фрезы, чем обеспечивается начало резания при малой толщине срезаемого слоя;
-для заготовок из жаропрочных и коррозийно-стойких сталей и при чистовом фрезеровании сдвиг заготовки - в сторону выхода зуба фрезы из резания, чем обеспечивается выход зуба из резания с минимально возможной толщиной срезаемого слоя.
Несоблюдение указанных правил приводит к значительному снижению стойкости фрезы.
Расчет скорости резания и окружной силы
Данные для расчета /11/:
- заготовка из конструкционной стали с пределом прочности в, МПа;
-ширина фрезерования B, мм;
-торцевая насадная фреза D, мм, со ставными ножами числом z из быстрорежущей стали;
-припуск на обработку h, мм.
Черновое фрезерование (рис.1.18):
-несимметричное встречное, глубина резания t, мм;
-подача на зуб при средней жесткости системы заготовка-приспособление sz=0,06÷0,07 мм/зуб /11/;
-период стойкости фрезы Т, мин.
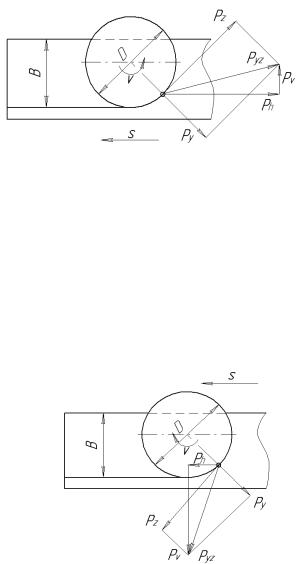
Рис. 1.18. Несимметричное встречное фрезерование
На рис. 1.18 приведены следующие обозначения:
B – ширина фрезерования; D – диаметр фрезы; S – подача; Pz – главная составляющая силы резания (окружная сила); Ph – горизонтальная составляющая (сила подачи); Pv
– вертикальная составляющая; Py – радиальная составляющая.
Чистовое фрезерование (рис. 1.19): несимметричное попутное, глубина резания t=0,2 мм; шероховатость поверхности Ra=3,2 мкм; S=0,5÷1,2 мм/об /3/, подача на зуб Sz=0,086 мм/зуб; период стойкости фрезы Т=180 мин.
Рис. 1.19. Симметричное попутное фрезерование
Скорость резания
Допустимая (расчѐтная) скорость резания V, м/мин определяется по эмпирической формуле
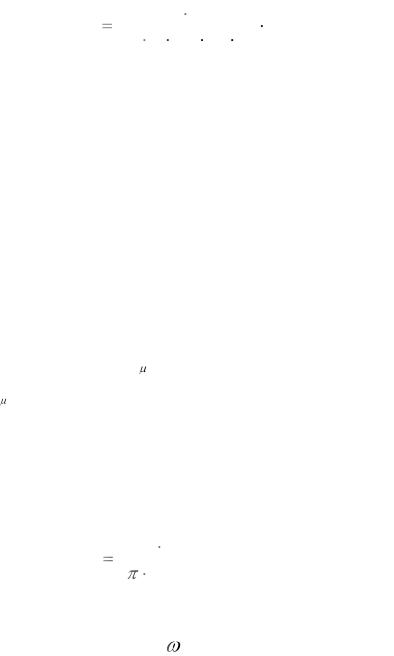
|
V |
Cv |
Dq |
|
kv , |
(1.96) |
|
|
T m t x |
S |
y Bu |
z p |
|||
|
|
|
|
z |
|
|
|
где |
Cv – коэффициент, |
характеризующий |
материал |
заготовки и фрезы;
T – стойкость фрезы (мин); t – глубина резания (мм); Sz – подача на зуб (мм/зуб);
B – ширина фрезерования (мм); Z – число зубьев фрезы;
q, m, x, y, u, p - показатели степени;
kv – общий поправочный коэффициент на изменѐнные условия обработки.
Величины Cv q, m, x, y, u, p приведены в /3/.
Общий поправочный коэффициент Kv, который представляет собой произведение отдельных поправочных коэффициентов, каждый из которых отражает изменение, относительно исходных, отдельных параметров /3/
|
Kv = K v · Kпv · Kиv, |
(1.97) |
где K v |
– коэффициент, учитывающий физико- |
|
механические свойства обрабатываемого материала; |
|
|
Kпv |
– коэффициент, учитывающий состояние |
|
поверхностного слоя заготовки; |
|
Kиv – коэффициент, учитывающий инструментальный материал.
Расчетную частоту вращения фрезы определяют по
формуле |
|
|
|
|
n |
1000 v |
, |
(1.98) |
|
D |
||||
|
|
|
||
где n – число оборотов фрезы, об/мин; |
||||
D – диаметр фрезы, мм. |
|
|
||
Угловая скорость фрезы |
|
и , с-1 равна |
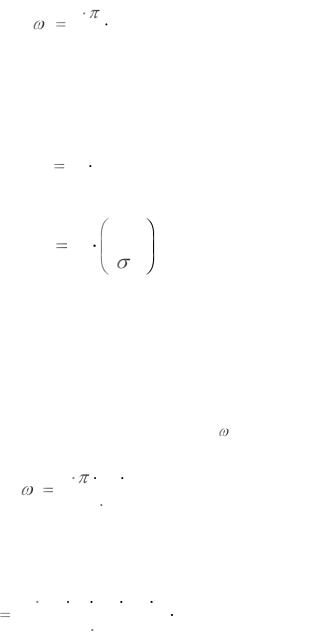
|
2 |
|
|
n . |
|
(1.99) |
|
и |
|
|
|
|
|
||
60 |
|
|
|||||
|
|
|
|
|
|||
|
|
|
|
|
|
||
Минутная подача Sм, мм/мин, находится по формуле |
|||||||
Sм = Sz · Z · n |
|
(1.100) |
|||||
Подача на один оборот фрезы при черновом |
|||||||
фрезеровании, S0 , мм/об, |
|
|
|
|
|
||
S0 |
Sz |
z , |
|
(1.101) |
|||
Коэффициент kмv найдем по формуле /3/ |
|
||||||
|
|
|
750 |
nv |
|
||
kмv |
|
kг |
|
|
|||
|
|
|
|
, |
(1.102) |
||
|
|
|
|
в
где kг – коэффициент, характеризующий группу стали по
обрабатываемости;
nv – показатель степени.
Для конструкционной стали коэффициент kг =1,
показатель степени nv=0.9. Коэффициенты, учитывающие состояние поверхности заготовки и состояние инструментального материала kпv=1 и kиv=1 /3/.
Скорость вращения двигателя 1 , с-1 при
черновой обработке
|
|
2 |
sm |
i |
. |
|
|
|
(1.103) |
||
1 |
|
|
60 t |
|
|
|
|
||||
|
|
|
|
|
|
|
|
||||
|
|
|
|
|
|
|
|
|
|
||
Главная составляющая силы резания Fz, Н, при |
|||||||||||
фрезеровании определяется по формуле |
|
|
|||||||||
10 C |
p |
t x |
S y |
Bu |
z |
|
|
||||
Fz |
|
|
|
|
|
|
|
K p , |
(1.104) |
||
|
|
|
Dq |
nw |
|
|
|
|

где Cp – коэффициент, характеризующий обрабатываемый материал и другие условия;
Kp – общий поправочный коэффициент, представляющий собой произведение коэффициентов, отражающих состояние отдельных параметров, влияющих на величину силы резания
|
|
Kр = K р · Kvр · K р · K р, |
||
|
|
|
|
(1.105) |
где |
K р – коэффициент, учитывающий свойства материала |
|||
обрабатываемой заготовки; |
|
|||
|
Kvр – коэффициент, учитывающий скорость резания; |
|||
|
K р – коэффициент, учитывающий величину переднего |
|||
угла |
; |
|
|
|
|
K р – коэффициент, учитывающий величину угла в |
|||
плане . |
|
|||
|
Для конструкционной стали K р=1, Kvр=1, |
K р=0,94, |
||
K р=1,6. |
|
|||
|
Из /3/ находим значения коэффициента Ср и |
|
||
показателей степеней x , y, u, q, w. |
|
|||
|
Крутящий момент на шпинделе станка (Н·м) |
|
||
|
|
D |
|
|
|
Mкр Fz |
|
, |
(1.106) |
|
2 1000 |
где Fz – главная составляющая силы резания, Н; D – диаметр фрезы, мм.
Мощность резания N, кВт, при фрезеровании рассчитывается по формуле
N |
Fzчерн V |
, . |
(1.107) |
60 1020 |
Значения составляющих силы резания при встречном несимметричном фрезеровании
торцевой фрезой согласно /11/: