
3535
.pdf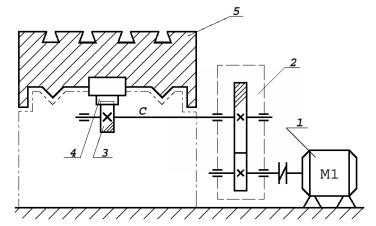
Рис. 1.2. Кинематическая схема продольнострогального станка
Движение от электродвигателя М1 через редуктор 2 и вал с жесткостью упругой деформации С передается на шестерню 3, связанную с реечной шестерней 4, осуществляющей возвратнопоступательное движение стола 5.
Технологический процесс обработки детали
Скорость перемещения стола относительно резца при рабочем ходе называют скоростью резания. Она зависит от вида обработки и материала изделия. Различают черновую и чистовую обработку детали, которые отличаются скоростью и глубиной резания.
Врезание резца в изделие и выход из него производится на пониженных (V1=2-15 м/мин). Допускается наименьшая скорость прямого хода до 4-6 м/мин. Максимальная скорость резания Vmax не превосходит V2=75-120 м/мин. Скорость обратного хода V3 находится в пределах 15-120 м/мин. Отношение скоростей обратного и рабочего ходов характеризуется коэффициентом Кз. При строгании подачу S и глубину резания R принимают в зависимости от вида обработки:
S1=1-7 мм/двойной ход, R1=6-30 мм – для черновой;
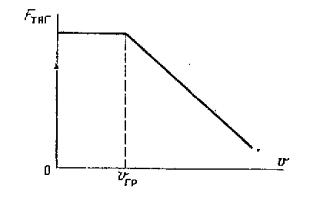
S2=10-30 мм/двойной ход, R2=0,05-0,3 мм – для чистовой /3/.
Технологические условия нагрузки характеризуются зависимостью мощности или момента нагрузки от скорости. В главном приводе продольно-строгального станка регулирование скорости осуществляется частично при постоянстве мощности, а частично – при постоянстве
момента (рис. 1.3).
Рис 1.3. График нагрузки главного привода продольно-строгального станка
До граничной скорости регулирование осуществляется при постоянстве момента, а выше граничной, когда тяговое усилие падает, мощность резания остается постоянной.
Значение граничной скорости определяется механической прочностью станка.
Глубина резания определяется припуском на обработку.
Припуск всегда экономичнее удалять за один рабочий ход. Глубина резания существенно влияет на силы резания и при обработке заготовок малой жесткости, корпусных деталей и т. д. Необходимо стремиться к небольшим силам резания. Силы резания также влияют на точность и параметры качества обрабатываемой поверхности. При удалении повышенных припусков и обработке на станках небольшой мощности припуск разбивают на две части, а иногда и больше.
В главных электроприводах металлорежущих станков полезным является усилие резания. Оно зависит от режимов

резания (глубины, подачи, скорости), материала обрабатываемого изделия и режущих свойств инструмента. На продольно-строгальных станках двигатель должен развивать еще дополнительное усилие, преодолевающее усилие трения в направляющих стола. Общая нагрузка на приводе в установившимся режиме при резании определяется тяговым усилием, равным сумме усилий резания и трения. На холостом ходу оно равно только усилию трения.
Нагрузочная диаграмма рабочего механизма не учитывает динамические нагрузки в переходных процессах. Для механизмов, рассчитанных на работу в длительном режиме S1 или с редкими пусками (торможениями), влияние динамических нагрузок учитывается коэффициентом запаса Кзап при определении расчетной мощности двигателя. Однако в механизмах с возвратно-поступательным движением, которые характеризуются повторяющимися циклами с частотой до 1200-1800 циклов в час, необходимо учитывать возникающие в переходных процессах дополнительные нагрузки. Для этого следует найти величины динамических моментов (усилий), зависящих от суммарного момента инерции Jсум привода и допустимых
ускорений адоп.
В переходных процессах пуск и реверсирование двигателя выполняют с максимальным быстродействием и допустимыми динамическими нагрузками в передачах редуктора. Допустимое ускорение адоп принимают в пределах от 0,8 до 1 м/с2. Скорость резания (м/мин) рассчитывается по формуле /4/
Vпр |
|
Cv |
|
|
Kv, |
(1.1) |
|
|
|
|
|
|
|||
|
m |
x |
|
y |
|||
T |
t |
|
s |
|
|
|
где Т – стойкость резца, мин; t – глубина резания, мм; s – подача (поперечная) резца, мм/дв.ход;
Кv – поправочный коэффициент (усредненное значение Kv=0.85); Cv, x, y, m – коэффициент и показатели степени, выбираемые
согласно табл. 1.1 режима резания.
Таблица 1.1

Значения коэффициента и показателей степени в формуле определения скорости строгания
Материал |
Подача |
Коэффициент и показатели |
||||
мм/дв. ход. |
степени |
|
|
|
||
обработки |
|
|
|
|||
|
Cv |
|
X |
Y |
M |
|
|
|
|
||||
|
до 0,3 |
420 |
|
|
0,2 |
|
Углеродистая сталь |
0,3-0,7 |
350 |
|
0,15 |
0,35 |
0,2 |
|
более 0,7 |
320 |
|
|
0,45 |
|
Серый чугун |
до 0,4 |
292 |
|
0,15 |
0,2 |
0,2 |
более 0,4 |
243 |
|
0,4 |
|||
|
|
|
|
|||
Ковкий чугун |
до 0,4 |
317 |
|
0,15 |
0,2 |
0,2 |
более 0,4 |
215 |
|
0,4 |
|||
|
|
|
|
|||
Медные сплавы |
до 0,2 |
270 |
|
0,12 |
0,25 |
0,23 |
более 0,2 |
182 |
|
0,3 |
|||
|
|
|
|
|||
Алюминиевые |
до 0,2 |
485 |
|
0,12 |
0,25 |
0,28 |
сплавы и силумин |
более 0,2 |
328 |
|
0,5 |
||
|
|
|
Затем по эмпирической формуле рассчитывается сила резания Fz (Н)
Fz 10Cpt x s yVпрn Kp, |
(1.2) |
где Vпр – скорость резания, вычисленная по (1.1), м/мин; Кр – поправочный коэффициент (усреднено Кр=1.1 );
Cp, x, y, n – коэффициенты и показатели степени, выбираемые по табл. 1.2 режимов резания.
Таблица 1.2 Значения коэффициента и показателей степени в формуле
определения сила резания Fz (1.2)
Материал |
Материал |
Коэффициент и показатели степени |
||||
обработки |
резца |
Cр |
X |
Y |
M |
|
Углеродистая |
тв. сплав |
300 |
1 |
0,75 |
-0,15 - 0 |
|
сталь |
б-р сталь |
200 |
||||
|
|
|
||||
Серый чугун |
до 0,4 |
92 |
1 |
0,75 |
0 |
|
более 0,4 |
158 |
1 |
||||
|
|
|
||||
Ковкий чугун |
до 0,4 |
81 |
1 |
0,75 |
0 |
|
более 0,4 |
||||||
|
|
|
|
|
||
Медные |
до 0,2 |
55 |
1 |
0,66 |
0 |
|
сплавы |
более 0,2 |
|||||
|
|
|
|
Алюминиевые |
до 0,2 |
|
|
|
|
|
|
|
|
|
|
||
сплавы и |
|
40 |
1 |
0,75 |
0 |
|
более 0,2 |
||||||
силумин |
|
|
|
|
||
|
|
|
|
|
||
|
|
|
|
|
|
Нагрузка привода при прямом ходе стола определяется тяговым усилием, который находится как сумма составляющих усилия резания и усилия трения, действующего при движении стола в направляющих.
Fтяг = Fz+Fтр = Fz+Ктр·[Fy+g·(mст+mдет)], |
(1.3) |
где Fтяг – тяговое усилие; |
|
Fy – вертикальная составляющая силы резания, Fy=0.4Fz; |
|
Ктр – коэффициент трения, Ктр=0,05-0,08; |
|
g – ускорение свободного падения, м/с-2 ; |
|
mст – масса движущейся части стола, кг; |
|
mдет – масса детали (максимальная), кг. |
|
При обратном ходе стола резец поднимается, и на |
|
привод действует только усилие трения |
|
Fох = Fтр = Ктр·[Fy+g·(mст+mдет )] |
(1.4) |
где Fох – усилие при обратном ходе стола, Н. |
|
Требования к электроприводу
Привод должен обеспечивать большой вращающий момент при малых скоростях обработки (черновая обработка).
Привод должен быть реверсивным с малым временем переходных процессов, малой колебательностью и перерегулированием. Скорость должна регулироваться в зависимости от вида обработки. В установившихся режимах электропривод должен обеспечивать жесткие механические характеристики во всем диапазоне регулирования скорости с изменением скорости не более 5% при колебании нагрузки от нуля до номинальной.
Диапазон регулирования скорости D при поступательном главном движении определяется
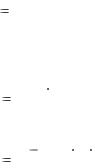
отношением максимальной Vmax и минимальной Vmin линейными скоростями движения и достигает D=30 /5/.
Режим работы электропривода – продолжительный, с частыми реверсами.
Предъявляемым требованиям достаточно полно соответствуют приводы постоянного тока. Они обладают широким диапазоном регулирования скорости с довольно жесткой механической характеристикой. В целях получения широкого диапазона скоростей вращения необходимо осуществлять двухзонное управление электродвигателем: по полю двигателя и по току якоря.
Нагрузочная диаграмма и тахограмма механизма передвижения стола
Расчет усилий и скоростей рабочей машины осуществляют в соответствии с выполнением технологического режима. Участок перед врезанием, когда двигатель работает вхолостую, принимают равным пяти процентам от длины стола
= 0,05·L. |
(1.5) |
Процесс врезания происходит при минимальной скорости Vmin , а
далее осуществляется разгон привода до скорости резания Vрезания. Рассчитаем время работы станка на отдельных участках нагрузочной
диаграммы при различных режимах резания.
Черновая обработка. Прямой ход
Время разгона стола до скорости врезания Vmin
t |
Vmin |
, |
(1.6) |
|
|||
1 |
адоп |
|
|
|
|
где адоп – допустимое линейное ускорение м/с 2.
Время прохождения расстояния =0,05·L
t2 |
0,05 L |
. |
(1.7) |
|
|||
|
Vmin |
|
Время движения стола при резании с Vmin
t3 |
L 0,05 L 2 |
. |
(1.8) |
|
|||
|
Vmin |
|
Время движения стола с Vmin после выхода резца из заготовки
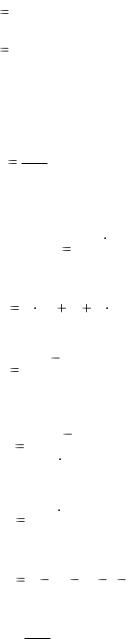
t4 t2 .
Время, необходимое для снижения скорости до 0 t5 t1 .
Черновая обработка. Обратный ход
Время разгона стола до скорости обратного хода Vобр после реверса
t6 Vобр . адоп
Расстояние, проходимое столом за время t1 при разгоне до скорости Vmin
|
|
|
|
а |
t 2 |
|
||||
|
|
S1 |
|
|
|
доп |
1 |
|
. |
|
|
|
|
|
|
2 |
|
|
|||
|
|
|
|
|
|
|
|
|
||
Следовательно, ход стола |
|
|
|
|
|
|
|
|
|
|
S |
2 S1 |
L |
|
2 . |
|
|||||
Время замедления стола до Vmin |
|
|
|
|
|
|
|
|
||
t8 |
Vобр |
Vmin |
. |
|
|
|
||||
|
|
|
|
|
|
|
||||
|
|
aдоп |
|
|
|
|
|
|||
Расстояние, проходимое столом за время t8 |
|
|
|
|||||||
|
2 |
|
|
|
2 |
|
|
|
||
S8 |
Vобр |
Vmin |
. |
|
|
|||||
|
2 адоп |
|
|
|||||||
|
|
|
|
|
||||||
Расстояние, проходимое столом за время t6 |
|
|
|
|||||||
|
|
а |
t 2 |
|
|
|
|
|
||
S6 |
|
доп |
6 |
|
|
. |
|
|
|
|
2 |
|
|
|
|
|
|
|
|||
|
|
|
|
|
|
|
|
|
||
Расстояние, проходимое столом с скоростью Vобр |
||||||||||
S7 |
S S6 |
S1 |
l S8 . |
Время прохождения столом расстояния S7
t7 S7 .
Vобр
(1.9)
(1.10)
(1.11)
(1.12)
(1.13)
(1.14)
(1.15)
(1.16)
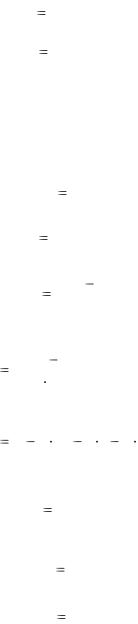
Время движение стола после реверса с Vmin t9 t2 .
Время снижения скорости стола от Vmin до 0
t10 t1 .
По полученным данным построим тахограмму (рис. 1.4 ), где
t1’=t1; t2’=t1’+t2; t3’=t2’+t3; t4’=t3’+t4; t5’=t4’+t5; t6’=t5’+t6; t7’=t6’+t7; t8’=t7’+t8; t9’=t8’+t9; t10’ =t9’+t10=tчернц.цикла .
Чистовая обработка. Прямой ход
Время разгона стола от 0 до Vmin
|
|
|
t11 |
t1 . |
|
|
|
|
Время движения стола с минимальной скоростью Vmin |
|
|||||||
|
|
t12 |
t2 . |
|
|
|
|
|
Время разгона стола до скорости чистовой обработки Vmax |
|
|||||||
|
|
t |
|
Vmax |
|
Vmin |
. |
(1.17) |
|
|
|
|
|
||||
|
13 |
|
адоп |
|
||||
|
|
|
|
|
||||
Расстояние, проходимое столом за время t13 |
|
|||||||
|
|
|
2 |
Vmin |
2 |
|
|
|
S13 |
Vmax |
|
. |
|
(1.18) |
|||
|
2 адоп |
|
|
|||||
|
|
|
|
|
|
|||
Расстояние, проходимое столом со скоростью Vmax |
|
|||||||
S14 S |
2 |
S1 |
2 l 2 S13 . |
(1.19) |
||||
Время прохождения расстояния S14 |
|
|
|
|
||||
|
|
t |
|
S14 |
. |
(1.20) |
||
|
|
|
|
|||||
|
14 |
|
Vmax |
|
|
|
|
|
|
|
|
|
|
|
|
|
|
Время замедления стола от Vmax до Vmin |
|
|||||||
|
|
t15 |
t13 . |
|
||||
Время движения стола с минимальной скоростью Vmin |
|
|||||||
|
|
|
t16 |
t12 |
|
|
|
|
Время снижения скорости стола от Vmin до 0
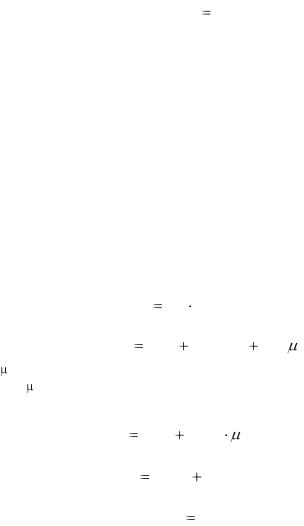
t17 t11 .
Чистовая обработка. Обратный ход
Тахограмма обратного хода чистовой обработки аналогичны обратному ходу черновой обработки.
По полученным данным построим тахограмму чистовой
обработки (рис. 1.5), где: t11’=t11; t12’=t11’+t12; t13’=t12’+t13; t14’=t13’+t14; t15’=t14’+t15; t16’=t15’+t16; t17’=t16’+t17; t18’=t17’+t6;
t19’=t18’+t7; t20’=t19’+t8; t21’=t20’+t9; t22’ = t21’+t10=tчист.цикла .
Определение усилий для построения нагрузочной диаграммы
При расчетах нагрузочной диаграммы статический момент нагрузки при врезании и резании принимают постоянным. Все силы рассчитывают по модулю.
Вертикальная составляющая усилия резания вычисляется по формуле /5/
Fy 0,4 Fz max . |
(1.21) |
Сила трения при движении стола по направляющим при резании
Fтр( рез ) (Gст Gдет ) Fy
, (1.22)
где – коэффициент трения стола о направляющие, для тяжелых станков = 0,07.
Сила трения при движении стола по направляющим на холостом
ходу
Fтр( хх ) |
(Gст |
Gдет ) |
. |
(1.23) |
Тяговое усилие при резании |
|
|
|
|
Fтяг( рез ) |
Fz max |
Fтр( рез ) . |
(1.24) |
Сила трения при обратном ходе
Fтр(обр) Fтр( хх ) .
Регулирование скорости от Vmin до граничной скорости Vгр
осуществляется при постоянном моменте, а увеличение скорости с Vгр
до Vmax происходит при постоянной мощности. Принимают Vгр в
диапазоне (20 - 25) м/мин.
Найдѐм усилие резания при чистовой обработке
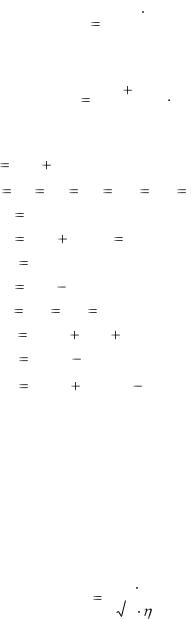
F |
Fz max Vгр |
. |
(1.25) |
|
|||
zччис |
Vmax |
|
|
|
|
Рассчитаем динамическое усилие, обусловленное массами стола и детали при разгоне и торможении привода стола
F |
Gст Gдет |
a . |
(1.26) |
|
|||
дин |
g |
доп |
|
|
|
|
Определим силы, действующие на каждом участке технологического процесса:
F1 Fдин Fтр( хх ) ;
F2 F4 F7 F9 F12 F16 Fтр( хх ) ;
F3 Fтяг ;
F6 Fдин Fтр( хх ) F1 ;
F11 F1 ;
F5 Fдин Fтр( хх ) ;
F8 F10 F17 F5 ;
F13 Fzччис Fдин Fтр( рез ) ;
F14 Fzччис Fтр(тез ) ;
F15 Fzччис Fтр(тез ) Fдин .
Силы, действующие при обратном ходе чистовой обработки, такие же, как и при черновой обработке.
По полученным данным построим нагрузочные диаграммы при черновой (рис. 1.4) и чистовой обработке (рис. 1.5).
Расчет предварительной мощности электропривода
Вычислим эквивалентную мощность за технологический цикл обработки детали. Для этого рассчитаем мощность на отдельных временных участках тахограмм:
1) 0…t1 Разгон до Vmin
P |
(F1 |
) |
Vmin |
. |
(1.27) |
|
|
|
|||
1 |
3 |
|
|
|
|
|
n |
|
|||
|
|
|
|
2) 1…t2 Равномерное движение с Vmin