
3535
.pdf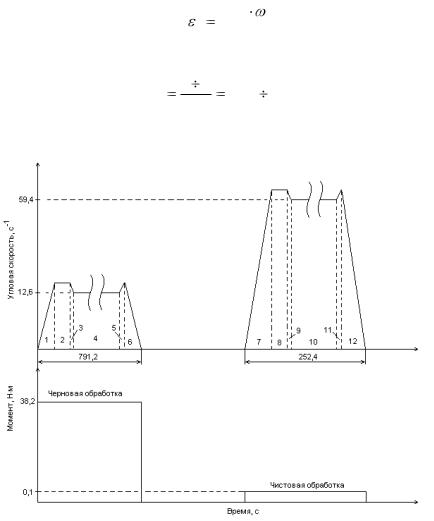
Рекомендуемое время разгона привода главного движения, согласно /8/, tпп=2÷4 с.
Допустимое ускорение определим по формуле /8/
|
0,63 |
с |
, |
(1.53) |
|
|
|||
д |
Т |
|
||
|
|
|
||
|
|
|
|
где ωс – статическая угловая скорость, с-1; Т=tпп/3 – постоянная времени пуска, с;
2 4 Т 0,67 1,3 (с).
3
По найденным значениям стоится нагрузочная диаграмма и тахограмма исполнительного органа привода главного движения при черновой и чистовой обработке (рис. 1.10).
Рис. 1.10. Тахограмма и нагрузочная диаграмма исполнительного органа привода главного движения:
1 – разгон двигателя; 2 – холостой ход; 3 – врезание инструмента; 4 – обработка; 5 – отвод инструмента; 6 – торможение двигателя; 7 – разгон двигателя; 8 – холостой ход; 9– врезание инструмента; 10 – обработка; 11 – отвод инструмента;
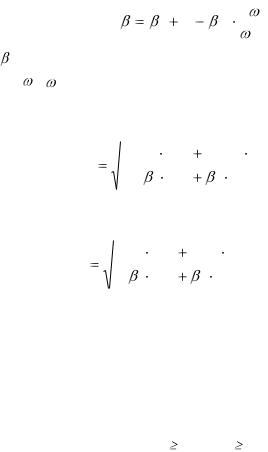
12 – торможение двигателя
По графикам (рис.1.10) строится нагрузочная диаграмма P(t). При построении графика P(t) в связи с большим различием длительности переходных процессов и режима обработки детали можно полагать, что основную долю вносят статические моменты.
Если выбираемый двигатель самовентилируемый, то при работе на скорости ниже номинальной необходимо определить коэффициенты ухудшения теплоотдачи для каждого режима работы по формуле /9/
|
|
|
|
|
|
0 |
|
(1 |
0 ) |
|
|
|
|
|
, |
|
|
(1.54) |
||
|
|
|
|
|
|
|
|
|
|
|
|
|
|
|||||||
|
|
|
|
|
|
|
|
|
|
|
|
|
|
ном |
|
|
|
|||
где 0 |
- коэффициент ухудшения теплоотдачи при неподвижном |
|
||||||||||||||||||
роторе; |
, ном – соответственно значения угловых скоростей для |
|||||||||||||||||||
режима работы и номинальная скорость двигателя. |
|
|
|
|||||||||||||||||
Тогда эквивалентный момент за цикл составит |
|
|||||||||||||||||||
|
|
|
|
|
|
|
|
|
|
|
|
|
|
|
|
|
|
|
|
|
|
|
|
|
М 2 |
|
|
t |
черн |
|
М |
2 |
|
|
t |
чист |
|
|
|
||
|
М |
|
|
черн |
|
|
|
чист |
|
, |
(1.55) |
|||||||||
|
э |
|
|
tчерн |
|
|
tчист |
|
|
|
||||||||||
|
|
|
|
|
1 |
|
2 |
|
|
|
|
|
|
|||||||
а эквивалентная мощность за цикл /6/ будет равна |
|
|||||||||||||||||||
|
|
|
|
|
|
|
|
|
|
|
|
|
|
|
|
|
|
|
||
|
|
|
P2 |
t |
|
|
|
P2 |
t |
|
|
|
|
|
|
|
|
|
||
|
P |
|
|
черн |
|
черн |
чист |
|
чист |
, |
|
|
(1.56) |
|||||||
|
|
|
|
|
|
|
|
|
|
|
|
|
|
|||||||
|
э |
|
|
|
tчерн |
|
tчист |
|
|
|
|
|
|
|
||||||
|
|
1 |
2 |
|
|
|
|
|
|
|
При выборе номинального момента двигателя учитывают коэффициент запаса
Мрасч= kз·Мэкв,
где kз=1,1 – коэффициент запаса.
При выборе двигателя его параметры должны удовлетворять следующим неравенствам:
Mном Мэкв,, Рном Рэкв.
Расчет мощности двигателя электропривода продольной подачи
Расчет мощности двигателя при черновой обработке
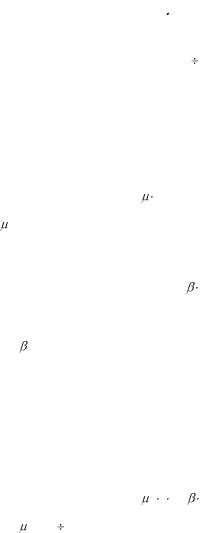
Двигатель подачи обеспечивает усилие Fпод, необходимое для линейного перемещения стола, которое в общем случае равно сумме усилия резания, трения и прилипания /5/
|
Fпод=k Fx+F тр+Fпр, |
(1.57) |
где |
Fx – составляющая усилия резания в направлении подачи, Н; |
|
|
k – коэффициент запаса, k=1,2 1,5; |
|
|
Fтр – усилие трения стола о направляющие, Н; |
|
|
Fпр – усилие прилипания, Н. |
|
|
Усилие трения стола о направляющие определяется |
массой |
перемещающихся механизмов подачи m (масса перемещаемого органа привода вместе с деталью и инструментальным механизмом) и составляющими усилия резания Fy и Fz , направленными нормально к направляющим (Н)
Fтр= (g·m+Fy+Fz), |
(1.58) |
где – коэффициент трения стола о направляющие; g – ускорение свободного падения, g=9,8 м/с2.
Усилие прилипания возникает при трогании стола с места в начале движения
Fпр= Sпр, |
(1.59) |
где Sпр – площадь поверхности прилегания направляющих стола, взаимно трущихся с направляющими салазок, см2;
– удельное усилие прилипания, принимаемое 0,5 Н/см2 /5/.
Все составляющие усилия подачи одновременно не действуют, подача производится вхолостую до начала процесса резания. Поэтому при определении нагрузки двигателя подачи рассматривают отдельно два характерных режима его работы: трогание с места и рабочую подачу.
При трогании с места (режим холостого хода) действуют только усилие трения от массы перемещающихся частей механизма подачи и усилие прилипания, возникающее в начале трогания. Усилие подачи при трогании стола
|
Fтр= т g m+ Sпр, , |
(1.60) |
где |
т=0,2 0,3 – коэффициент трения в направляющих при |
|
трогании стола с места. |
|
При рабочей подаче в процессе резания, когда стол уже движется с установившейся скоростью, усилие подачи определяется усилием резания и трения по формуле
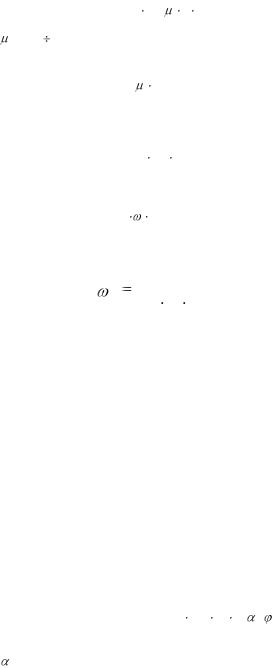
|
|
Fпод. д=k Fx+ д (g m+Fy+Fz), |
(1.61) |
|||
где |
д=0,05 |
0,15 – коэффициент трения в направляющих при |
|
|||
движении стола; |
k=1,4 – коэффициент запаса /5/. |
|
||||
|
На холостом ходу усилие подачи равно |
|
||||
|
|
Fпод.хх= д g·m. |
|
(1.62) |
||
|
Мощность подачи определяется усилием, преодолеваемым |
|||||
приводом подачи Fпод и скоростью vпод по формуле |
|
|||||
|
|
Рпод=Fпод vпод 10-3. |
|
(1.63) |
||
|
Скорость подачи (м/с), определяется подачей и угловой |
|||||
скоростью изделия |
|
|
|
|
||
|
|
vпод=s |
и 10-3, |
|
(1.64) |
|
где |
s=0,5 мм/об – величина подачи при черновой обработке. |
|
||||
|
Угловая скорость изделия равна |
|
|
|||
|
|
|
VU |
|
. |
(1.65) |
|
|
И |
0,5 D 60 |
|||
|
|
|
|
|
Аналогично рассчитывается мощности двигателя продольной подачи при чистовой обработке. При расчѐте следует учитывать диаметр заготовки после черновой обработки, материал резца для чистовой обработки, глубину резания t при подаче s, период стойкости резца.
Далее определяются расчетная и действительная скорости резания при чистовой обработке, рассчитываются тангенциальная составляющая и усилие подачи при чистовой обработке. Определяется частота вращения шпинделя, соответствующая найденной скорости резания, и скорость подачи при чистовой обработке. Полученные данные позволяют определить мощность подачи при чистовой обработке.
Расчет статического момента двигателя продольной подачи
Статический момент определяется усилием, передаваемым в направлении подачи при установившемся движении органа станка. От усилия подачи на валу ходового винта стола возникает момент Мхв /5/
Мхв=0,5 Fпод dср tg( + ), |
(1.66) |
где dср– средний диаметр ходового винта, мм;
– угол наклона резьбы ходового винта, град;
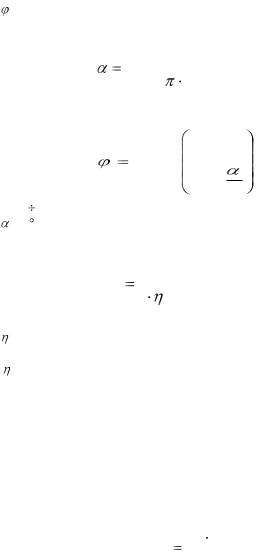
– угол трения резьбы, град.
Угол наклона резьбы ходового винта определяется диаметром винта и шагом его нарезки по формуле /5/
arctg |
t |
|
|
|
, |
(1.67) |
|
|
|||
|
dср |
|
где t– шаг ходового винта, мм.
Угол трения резьбы, в соответствие с /10/, равен
arctg |
f |
, |
(1.68) |
|
|||
|
|
cos 2
где f=0,1 0,3 – коэффициент трения; =45 – угол наклона резьбы.
Вращающий момент на валу ходового винта определяет момент статического сопротивления на валу двигателя подачи
М с |
|
М хв |
, |
(1.69) |
|
i |
пер |
||||
|
|
|
|||
|
|
|
|
где i – передаточное отношение от двигателя к ходовому винту; пер – КПД передач от двигателя к ходовому винту.
По рекомендации /11/ КПД передачи винт-гайка качения без натяга =0,95. Затем находят величины статических моментов, соответствующие режимам трогания, холостого хода, режиму резания при черновой и чистовой обработке.
Линейное ускорение стола, в соответствии с /5/, принимают а=0,8
м/с2.
Построение тахограммы и нагрузочной диаграммы исполнительного органа привода продольной подачи
Время обработки детали (с) при черновом точении найдем по формуле
tчерн |
60 l |
, |
(1.70) |
|
|||
|
vчерн |
|
где l – длина заготовки, м;
vчерн – скорость при черновом точении, м/мин. При чистовой обработке
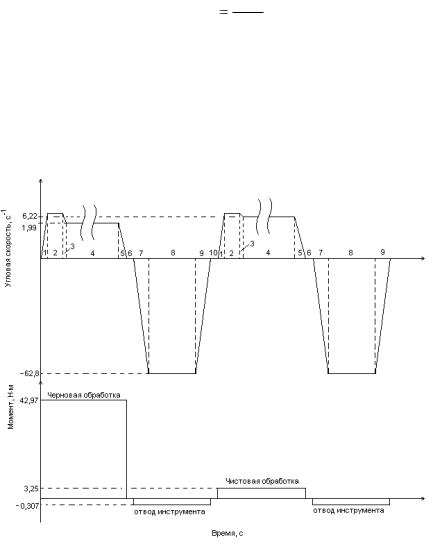
60 l
tчист vчист .
Время перемещения инструмента в исходное положение tип определяется при моменте Мс хх и скорости перемещения vип.
Время полного цикла tц (с):
tц=tчерн+tчист+2·tип,
Тахограмма исполнительного органа привода продольной подачи, совмещенная с нагрузочной диаграммой, приведена на рис. 1.11.
Рис. 1.11. Тахограмма и нагрузочная диаграмма исполнительного органа привода продольной подачи:
1 – разгон двигателя; 2 – холостой ход; 3 – врезание инструмента; 4 – обработка; 5 – торможение двигателя; 6 – отвод инструмента; 7 – разгон
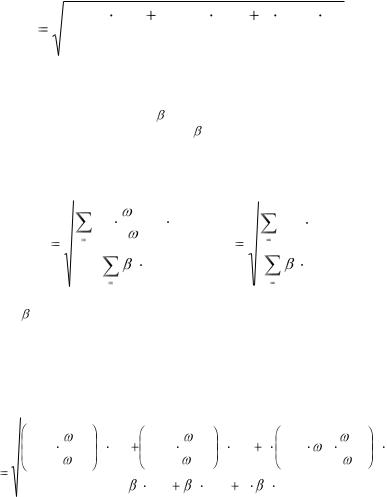
двигателя; 8 – отвод инструмента в исходное положение; 9 – торможение; 10 – подвод инструмента
Найдем значение эквивалентного момента за цикл Мэкв (Н·м) по формуле
|
|
|
|
М 2 |
|
t |
черн |
|
М |
2 |
|
t |
чист |
2 М 2 |
|
|
|
t |
ип |
|
|
|
|
|
|||||||||||
M |
|
|
|
|
|
с под |
|
|
|
|
|
счист |
|
|
с хх |
|
|
|
|
|
|
|
|||||||||||||
экв |
|
|
|
|
|
|
|
|
|
tц |
|
|
|
|
|
|
|
|
|
|
|
|
. |
(1.71) |
|
|
|||||||||
|
|
|
|
|
|
|
|
|
|
|
|
|
|
|
|
|
|
|
|
|
|
|
|
|
|
|
|
|
|
|
|
|
|
||
Для двигателей, работающих с переменной скоростью, (при |
|
|
|||||||||||||||||||||||||||||||||
отсутствии независимой вентиляции) необходимо учитывать ухудшение |
|
|
|||||||||||||||||||||||||||||||||
теплоотдачи при понижении скорости. Коэффициент ухудшения |
|
|
|||||||||||||||||||||||||||||||||
теплоотдачи будет меняться от |
0 (коэффициент ухудшения теплоотдачи |
|
|
||||||||||||||||||||||||||||||||
при неподвижном роторе) до |
н=1 |
|
(коэффициент |
|
|
|
ухудшения |
|
|
||||||||||||||||||||||||||
теплоотдачи при номинальной частоте) |
/9/. |
|
|
|
|
|
|
|
|
|
|
|
|
|
|
|
|||||||||||||||||||
С учетом коэффициента ухудшения теплоотдачи (1.54) |
|
|
|||||||||||||||||||||||||||||||||
эквивалентные мощность и момент равны: |
|
|
|
|
|
|
|
|
|
|
|
|
|
|
|
|
|||||||||||||||||||
|
|
|
|
|
|
|
|
|
|
|
|
|
|
|
|
|
|
|
|
|
|
|
|
|
|
|
|
|
|
|
|
|
|
|
|
|
|
|
|
|
|
m |
|
|
|
|
)2 |
|
|
|
|
|
|
|
|
|
|
m |
|
|
|
|
|
|
|
|
|
|
|
|
|
|
|
|
|
|
|
|
(P |
|
ном |
t |
|
|
|
|
|
|
|
|
|
|
M 2 |
t |
|
|
|
|
|
|
|
|
|
|
|||
|
|
|
|
|
|
i |
|
|
|
|
|
|
i |
|
|
|
|
|
|
|
|||||||||||||||
|
|
|
|
|
|
|
|
i |
|
|
|
|
|
|
|
|
|
|
|
i |
|
|
|
|
|
|
|
|
|||||||
|
|
Pэкв |
i 1 |
|
|
i |
|
|
|
, |
M экв |
i 1 |
|
|
, |
|
|
|
(1.72) |
|
|
||||||||||||||
|
|
|
|
m |
|
|
|
|
|
|
m |
|
|
|
|
|
|
|
|||||||||||||||||
|
|
|
|
|
|
|
|
|
|
i |
ti |
|
|
|
|
|
|
|
|
|
|
|
i |
ti |
|
|
|
|
|
|
|
|
|
|
|
|
|
|
|
|
|
|
|
i |
1 |
|
|
|
|
|
|
|
|
|
|
|
|
|
i |
1 |
|
|
|
|
|
|
|
|
|
|
|
где |
|
i – коэффициент |
ухудшения |
теплоотдачи на |
|
i-ом участке, |
|
|
|||||||||||||||||||||||||||
соответствующий значению угловой скорости на этом участке. |
|
|
|
|
|||||||||||||||||||||||||||||||
Для каждого режима работы определяют коэффициент ухудшения |
|
|
|||||||||||||||||||||||||||||||||
теплоотдачи, который подставляется в формулы эквивалентных |
|
|
|||||||||||||||||||||||||||||||||
мощности и момента. |
|
|
|
|
|
|
|
|
|
|
|
|
|
|
|
|
|
|
|
|
|
|
|
|
|
|
|
|
|||||||
Эквивалентная мощность за цикл |
|
|
|
|
|
|
|
|
|
|
|
|
|
|
|
|
|
||||||||||||||||||
|
|
|
|
|
|
|
|
|
|
|
|
|
|
|
|
|
|
|
|
|
|
|
|
|
|
|
|
|
|
||||||
|
2 |
|
|
|
|
|
|
|
|
|
|
|
2 |
|
|
|
|
|
|
|
|
|
|
|
|
2 |
|
|
|||||||
|
|
Рчерн |
|
|
ном |
|
t черн |
Рчист |
|
|
|
ном |
|
|
t чист |
2 |
M ип |
|
|
|
|
|
|
ном |
tв |
|
|
||||||||
|
|
|
|
|
|
|
|
|
|
|
|
|
|
xx |
|
|
|
||||||||||||||||||
Pэкв |
|
|
|
черн |
|
|
|
|
|
|
|
|
|
чист |
|
|
|
|
|
|
|
|
|
|
|
|
|
xx |
|
, |
|||||
|
|
|
|
|
|
|
|
|
|
|
|
|
|
|
|
|
|
|
|
|
|
|
|
|
|
|
|
|
|
|
|
|
|||
|
|
|
|
|
|
|
|
|
1 |
tчерн |
2 |
tчист |
2 |
|
3 |
tип |
|
|
|
|
|
|
|
|
|
||||||||||
|
|
|
|
|
|
|
|
|
|
|
|
|
|
|
|
|
|
|
|
|
|
Эквивалентный момент за цикл
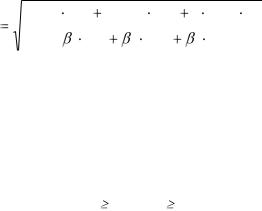
|
|
М 2 |
t |
черн |
М 2 |
t |
чист |
2 М |
2 |
t |
ип |
|
|
M |
|
с под |
|
|
счист |
|
|
с хх |
|
, |
|||
экв |
1 tчерн |
|
tчист |
3 tип |
|
|
|
||||||
|
|
|
2 |
|
|
|
|
При выборе номинального момента двигателя учитывают коэффициент запаса
Мрасч=kз·Мэкв,
где kз=1,1 – коэффициент запаса.
При выборе двигателя его параметры должны удовлетворять следующим неравенствам /6/:
Mном Мэкв,, Рном Рэкв.
1.4. Фрезерные станки
Общая характеристика и назначение
Фрезерные станки имеют весьма широкую область применения и разделяются на две основные группы:
-станки общего назначения;
-специализированные.
К первой группе относятся станки консольные и бесконсольные, продольно-фрезерные, станки непрерывного фрезерования (карусельные и барабанные).
Ко второй группе относятся станки копировально-фрезерные, зубофрезерные, резьбофрезерные, шпоночно-фрезерные, шлицефрезерные и др.
Типоразмеры станков характеризуются площадью рабочей (крепежной) поверхности стола или размерами обрабатываемой заготовки (при зубо- и резьбообработке). По указанному признаку станки имеют пять градаций, которые приведены в табл. 1.8.
|
Таблица 1.8 |
|
|
Типоразмеры станков |
|
|
|
|
Размер |
Площадь поверхности стола, мм |
|
0 |
200x800; |
|
1 |
250x1000; |
|
2 |
320x1250; |
|
3 |
400x1600; |
4 |
500x2000. |
Далее приведена классификация фрезерных станков, выпускаемых в России. Фрезерные станки образуют шестую группу металлорежущих станков. В этой группе приведено девять типов станков, кроме того, фрезерные станки входят и в пятую группу зубо- и резьбообрабатывающих станков. Каждый станок имеет свой шифр, первая цифра в котором обозначает группу станка, вторая - его тип:
1- консольные вертикально-фрезерные;
2- непрерывного действия;
3- продольные одностоечные;
4- копировальные и гравировальные;
5- вертикальные бесконсольные (с крестовым столом);
6- продольно-фрезерные;
7- широкоуниверсальные;
8- консольные, горизонтальные;
9- разные.
Третья и при необходимости четвертая цифры обозначают характерные размеры станка. Кроме цифр в обозначение модели станка может входить буква. Если буква стоит между первой и второй цифрами, то это означает, что конструкция станка модифицирована. Если буква стоит в конце шифра станка, то это может означать следующее:
-конструктивную модификацию основной модели;
-различное исполнение станков в зависимости от точности (Н - нормальной точности, П - повышенной, В - высокой, А - особо высокой и С - станки особо точные, называемые мастер - станки);
-различное исполнение с учетом используемой системы управления станком.
Консольно-фрезерные станки - наиболее распространенный тип станков, используемый для фрезерных работ. Отличительная особенность станка -
наличие консоли (кронштейна), несущей стол и перемещающейся по направляющим станины вверх и вниз. В горизонтально-фрезерных станках шпиндель расположен горизонтально, и стол перемешается в трех взаимно перпендикулярных направлениях. Отличие универсальных консольно-фрезерных станков от горизонтальных заключается только в возможности поворота стола относительно вертикальной оси, а широкоуниверсальных фрезерных станков от универсальных - в наличии на станине специального хобота, на торце которого установлена дополнительная головка со шпинделем, поворачивающаяся под углом в любом направлении. Вертикально-фрезерные станки отличаются от горизонтально-фрезерных вертикальным расположением шпинделя и отсутствием хобота.
Фрезерные станки с ЧПУ
Фрезерные станки с ЧПУ предназначены для обработки плоских и пространственных поверхностей заготовок сложной формы. Конструкции фрезерных станков с ЧПУ аналогичны конструкциям традиционных фрезерных станков, отличие от последних заключается в автоматизации перемещений по УП при формообразовании. В основе классификации фрезерных станков с ЧПУ лежат следующие признаки:
-расположение шпинделя (горизонтальное и вертикальное);
-число координатных перемещений стола или фрезерной бабки;
-число используемых инструментов (одноинструментные и многоинструментные);
-способ установки инструментов в шпиндель станка (вручную или автоматически).
По компоновке фрезерные станки с ЧПУ делят на четыре группы:
-вертикально-фрезерные с крестовым столом;