
Технологии органического и нефтехимического синтеза
..pdf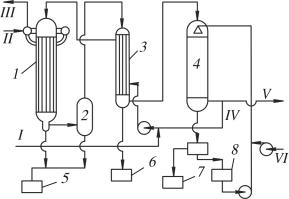
теплообменник вводят в реактор в количестве 500–700 м3 на 1 м3 катализатора в час. В реактор загружают 40 м3 катализатора состава 100 – Fe + 5 – Cu + 5 – K2О + 25 – SiO2. Катализатор работает непрерывно в течение 9–12 мес с постепенным повышением температуры от 220 до 250 °С, обеспечивая конверсию синтез-газа 65–73 %. Производительность одного реактора составляет 250 т/сут углеводородов С2 и выше.
Рис. 10.2. Принципиальная технологическая схема высокопроизводительного синтеза Фишера – Тропша на железном катализаторе: 1 – реактор; 2 – мультициклон; 3 – теплообменник; 4 – конденсатор; 5 – сборник парафина; 6 – сборник высококипящих углеводородов; 7 – сборник легких углеводородов; 8 – сборник реакционной воды. Потоки: I – синтез-газ; II – питательная вода; III – пар; IV – цирку-
лирующий газ; V – остаточный газ; VI – щелочь
Условия работы промышленных установок синтеза Фишера – Тропша в газовой фазе со стационарным катализатором и состав получаемых продуктов приведены в табл. 10.3.
Синтез в газовой фазе в потоке взвешенного катализатора.
На заводе «Сасол-1» реализована также технология синтеза в газовой фазе в потоке взвешенного железного катализатора. Установка мощностью 180 тыс. т/год работает с 1956 г. Технология разработана фирмой Kеllog. Принципиальная схема такого процесса показана на рис. 10.3.
211
Таблица 1 0 . 3
Работа промышленных установок синтеза Фишера – Тропша в газовой фазе со стационарным катализатором
|
Кобальтовый |
Железный |
Высоко- |
||
Показатели |
катализатор |
катализатор, |
производитель- |
||
При |
При |
присреднем |
ныйжелезный |
||
процесса |
|||||
атомсферном |
среднем |
давлении |
катализатор |
||
|
|||||
|
давлении |
давлении |
|
|
|
Давление, МПа |
0,03 |
0,7–1,2 |
1–1,2 |
2,3–2,5 |
|
Температура, °С |
175–230 |
180–210 |
190–230 |
220–250 |
|
Объемнаяскорость, ч–1 |
70–100 |
100–10 |
100–110 |
500–700 |
|
ОтношениеН2 : СО |
2 |
2 |
1,25 |
1,3–2 |
|
висходномгазе |
|||||
|
|
|
|
||
Числоступеней |
2 |
3 |
2 |
1 |
|
Продолжительностьра- |
4–6 |
6–7 |
12 |
9–12 |
|
ботыкатализатора, мес |
|||||
|
|
|
|
||
Степеньпревращения |
|
|
|
|
|
синтез-газа(водну |
70–85 |
78–86 |
60–85 |
63–75 |
|
ступень), % |
|
|
|
|
|
Производительность |
|
|
|
|
|
катализаторапо≥С2, |
150–160 |
190 |
210 |
1250 |
|
кг/м3 · сут |
|
|
|
|
|
Суммарныйвыход≥С2 |
160–190 |
150–160 |
160–185 |
140 |
|
на1 м3 СО+ Н2, г |
|||||
Составпродуктовсин- |
|
|
|
|
|
теза, мас. %, фракция: |
|
|
|
|
|
С1–С4 |
20–30 |
10–12 |
6–7 |
12–14 |
|
30–170 °С |
30–32 |
18–20 |
19–20 |
15–20 |
|
170–270 °С |
|
|
|
|
|
18–20 |
32–33 |
33–34 |
12–15 |
||
270–320 °С |
|
|
|
|
|
32–35 |
13–17 |
16–17 |
3–5 |
||
≥320 °С |
|
|
|
|
|
– |
32–34 |
20–23 |
8–36 |
||
|
Синтез-газ (Н2 : СО = (2,2–2,4) : 1), полученный газификацией угля по методу «Lurgi», смешивают с концентрированным остаточным газом в соотношении (2–2,5) : 1 и вводят в реактор (высота 36 м, диаметр 2,2 м) противотоком к катализатору. Количество газа составляет 90–100 тыс. м3/ч, количество циркулирующего катализатора 130–140 т (скорость циркуляции около 8 тыс. т/ч). Синтез проводят при температуре 310–350 °С и давлении 2–3 МПа. Продукты реакции
212
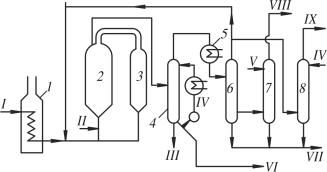
Рис. 10.3. Принципиальная технологическая схема синтеза Фишера – Тропша в газовой фазе в потоке взвешенного катализатора: 1 – подогреватель; 2 – реактор; 3 – холодильник; 4 – колоннасепаратор; 5 – конденсатор; 6 – разделительная колонна; 7 – колонна для промывки бензина; 8 – колонна для промывки газа. Потоки: I – синтез-газ; II – ввод свежего катализатора; III – суспензия катализатора; IV – циркулирующее масло; V – вода; VI – вода и водорастворимые продукты; VII – тяжелое масло;
VIII – бензин; IX – отходящий газ
и катализатор поступают в колонну-сепаратор, оборудованную циклонами для отделения катализатора.
Отвод тепла осуществляют при помощи двух холодильников, через которые циркулирует масло. Срок службы катализатора составляет 42–45 сут. Установка имеет три реактора, каждый из которых дает 60 тыс. т продуктов в год.
Отличительной особенностью процесса в потоке взвешенного катализатора является высокое содержание олефинов во фракции ≥ С3 (60–85 %). Селективность по олефинам С2–С4 может быть повышена до 46 % при ужесточении рабочих условий.
Во фракции жидких углеводородов (С6–С11) содержатся преимущественно α-олефины (66–76 %).
Технология синтеза Фишера – Тропша в потоке взвешенного катализатора положена в основу строительства нового завода в ЮАР – «Сасол-2». В составе установки «Сасол-2» проектируется
213
восемь реакторов мощностью 150 тыс. т/год каждый. Сннтез-газ (1,1 млн нм3/ч) будут получать в 36 генераторах «Lurgi». Годовая выработка основной продукции должна составить (тыс. т/год): моторных топлив – 1400–1500, этилена – 160–180, смол – 287, различных химикатов – 50, кислородсодержащих продуктов – 200, аммиака –
100, серы – 75–90.
10.3. ПЕРСПЕКТИВЫРАЗВИТИЯПРОЦЕССАФИШЕРА – ТРОПША
Технико-экономическая оценка процесса Фишера – Тропша свидетельствует о том, что он в ближайшие 10–15 лет вряд ли сможет конкурировать с процессами нефтепереработки с целью получения моторного топлива. Однако в решении современной проблемы замены нефтяного сырья угольным роль процесса Фишера – Тропша трудно переоценить. С точки зрения экономики перспективы синтеза Фишера – Тропша становятся более благоприятными, если ориентироваться не на производство моторных топлив, а на сырье для нефтехимии и химической промышленности – этилен, пропилен, бутилены, ароматические углеводороды, α-олефины С5–С11, кислородсодержащие соединения.
Существующие промышленные процессы позволят получать широкий набор продуктов с различным содержанием олефинов в отдельных фракциях. Однако даже эти процессы могут быть рентабельными в районах, располагающих запасами дешевого угля, если обеспечить высокую удельную производительность и повысить селективность. Поэтому одним из направлений развития синтеза Фишера – Тропша будет совершенствование известных способов и катализаторов, создание новых комбинированных схем с целью производства наиболее ценных продуктов. Другим перспективным направлением должна стать разработка катализаторов нового типа и на их основе новых селективных процессов. В качестве примера следует упомянуть новые катализаторы гидрирования СО на основе высококремнеземных цеолитов типа ZSM, содержащих переходные металлы или их оксиды.
Глава 11
ПРОИЗВОДСТВО КАРБОНОВЫХ КИСЛОТ И ИХ ПРОИЗВОДНЫХ
Карбоновые кислоты являются ценными промышленными продуктами и находят широкое практическое применение. Крупнотоннажными продуктами нефтехимии являются муравьиная, уксусная, пропионовая кислоты, жирные кислоты С4–С20.
11.1. ПРОИЗВОДСТВО МУРАВЬИНОЙ КИСЛОТЫ
Основное количество вырабатываемой НСООН потребляется в текстильной промышленности для крашения и обработки тканей (40 %), для производства химикатов и фармацевтических препаратов (40 %), на дубление и обработку кожи (12 %). Находят практическое применение и производные муравьиной кислоты: формамид используется для производства HCN, в качестве растворителя при производстве лекарств, формиаты щелочных металлов используются в текстильной и кожевенной промышленности, щелочноземельных металлов – при изготовлении катодов, в качестве пестицидов, пищевых консервантов, отвердителей бетона. Метилформиат является инсектицидом; этиловый, изоамиловый, бензиловый эфиры – хорошими растворителями для ацетилцеллюлозы, нитроцеллюлозы, смол, лаков, типографских красок и др.
В промышленности муравьиную кислоту получают жидкофазным окислением бутана или легкой бензиновой фракции, гидролизом формамида, из СО, метанола и NH3, гидролизом метилформиата, ацидолизом солей НСООН. Разрабатываются такие процессы, как прямой синтез из СО и воды, парофазная каталитическая дегидрогенизация метанола, синтез формамида из СО и аммиака.
215
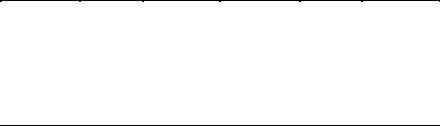
11.1.1. Синтез НСООН через формамид
Процесс является трехстадийным. В первой стадии проводят карбонилирование метанола в присутствии щелочного катализатора в метилформиат по уравнению
СН3ОН + СО ↔ НСООСН3, ∆Н298 = –29,3 кДж/моль. (11.1)
Условия реакции на этой стадии (температуру, давление) выбирают с учетом термодинамических и кинетических факторов, поскольку реакция является равновесной. На практике процесс проводят со степенью конверсии метанола невыше 70 % (табл. 11.1).
Таблица 1 1 . 1
Влияние температуры и давления на карбонилирование метанола в присутствии метилата натрия
Температу- |
Давление, |
Равновесное |
ра, °С |
кПа |
превращение |
|
|
метанола, |
|
|
мас. % |
80 |
1960 |
20 |
80 |
3920 |
40 |
80 |
5880 |
62 |
80 |
7840 |
85 |
|
|
|
Температу- |
Давление, |
Равновесное |
ра, °С |
кПа |
превращение |
|
|
метанола, |
|
|
мас. % |
100 |
1960 |
10 |
100 |
3920 |
20 |
100 |
5880 |
35 |
100 |
7840 |
52 |
|
|
|
В последующих стадиях метилформиат превращают в формамид, из которого при обработке H2SO4 получают НСООН и сульфат аммония:
НСООСН3 + NH3 → HCONH2 + CH3OH, |
(11.2) |
∆Н298 = –71,2 кДж/моль, |
|
2HCONH2 + H2SО4 + 2Н2О → 2НСООН + (NH4)2SO4, |
(11.3) |
∆Н298 = –100,5 кДж/моль. |
|
Технологическая схема этого процесса показана на рис. 11.1. Метанол и СО после осушки подают в реактор, работающий при
216
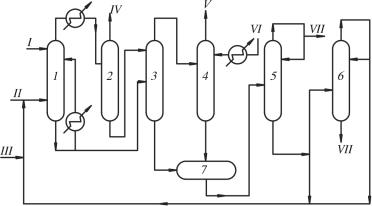
температуре 80 °С и давлении 4,5 МПа. Одновременно вводят катализатор со скоростью, обеспечивающей его концентрацию в реакционной смеси, равную 2 мас. %. Степень превращения СО 95 %, метанола 30 %. Выход метилформиата на прореагировавший метанол 99 %, объемная производительность реактора равна 800 г/ч на 1 дм3 объема. Продукты реакции направляют в газожидкостный сепаратор, где для удаления примесей проводят продувку СО. Отходящие газы из сепаратора промывают в скруббере холодным метанолом. Жидкую фазу из сепаратора и скруббера направляют в колонну выделения метилформиата. Метанол, содержащий катализатор, большей частью возвращают в реактор, а частично направляют в колонну для отделения высококипящих продуктов и дезактивированного катализатора.
Рис. 11.1. Принципиальная технологическая схема получения метилформиата карбонилированием метанола: 1 – реактор карбонилирования; 2 – газожидкостный сепаратор; 3 – колонна выделения; 4 – скруббер; 5 – колонна выделения метилформиата; 6 – колонна отделения высококипящих фракций; 7 – приемный резервуар. Потоки: I – СО; II – метанол; III – катализатор; IV – продувка СО; V – СО на рециркуляцию; VI – метанол;
VII – метилформиат
217
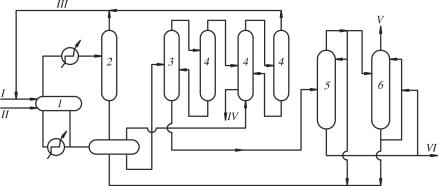
Полученный метилформиат направляют на стадию получения формамида (рис. 11.2). Метилацетат и аммиак подают в реактор, работающий при 65 °С и давлении 1,3 МПа. Теплота реакции отводится циркулирующей реакционной смесью через внешний теплообменник. Жидкие продукты реакции направляются в промежуточный сборник, а поток паров из верхней части реактора – в конденсатор, где отделяют метанол. В колонне отгонки легких фракций формамид отделяют от аммиака, метанола и метилформиата и направляют в колонну доочистки.
Рис. 11.2. Принципиальная технологическая схема получения формамида аммонолизом метилформиата: 1 – реактор; 2 – уравнительный резервуар; 3 – колонна отгонки легких фракций; 4 – колонны выделения метанола; 5 – колонна доочистки; 6 – скруббер. Потоки: I – метилформиат; II – аммиак; III – рецир-
кулирующий NН3; IV – метанол; V – отдув; VI – формамид
В последней стадии проводят гидролиз формамида (рис. 11.3). В реактор непрерывно вводят в равных количествах формамид и68–74%-юH2SO4. ТеплотуреакциииспользуютдляиспаренияНСООН. Горячая пульпа, состоящая из сульфата аммония и НСООН, подается во вращающуюся печь. Пары кислоты направляют в колонну, а сульфат аммония выводят из разгрузочного устройства.
218
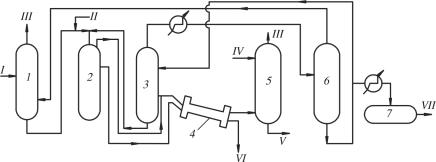
Рис. 11.3. Принципиальная технологическая схема получения НСООН гидролизом формамида: 1 – колонна для приема формамида; 2 – реактор; 3 – колонна выделения НСООН; 4 – вращающаяся печь; 5 – скруббер; 6 – сборник муравьиной кислоты; 7 – товарная емкость. Потоки: I – формамид; II – серная кислота; III – абгазы; IV – вода; V – отработанная вода;
VI – сульфат аммония; VII – НСООН
Выход метилформиата в таком процессе составляет 98 % в расчете на метанол, и 95 % – в расчете на СО. Выход формамида на метилформиат достигает 98 %, а выход НСООН на формамид – 93 %. Расход сырья в кг на 1000 кг НСООН составляет: метанола – 31, СО – 702, NH3 – 314, серной кислоты – 1010.
11.1.2. Синтез муравьиной кислоты гидролизом метилформиата
По способу фирмы Leonard Process муравьиную кислоту получают в две стадии карбонилированием метанола в метилформиат и гидролизом последнего в НСООН. В 1981 г. в Финляндии по этой технологии пущен завод мощностью 20 тыс. т/год.
Стадию карбонилирования метанола осуществляют по технологии, описанной в предыдущем разделе. Для гидролиза метилформиата предложены два варианта: гидролиз с избытком воды, которая затем удаляется перегонкой или НСООН выделяют экстрактивной перегонкой с N-формилморфолином, либо гидролиз осуществляют в присут-
219
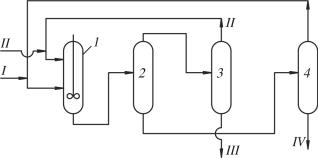
ствии третичного амина (пентилимидазола) со стехиометрическим количеством воды.
Технологическая схема процесса с избытком воды показана на рис. 11.4. Воду и метилформиат непрерывно вводят в реактор, работающий при температуре 80 °С и давлении 2,9 МПа. Гидролиз протекает в жидкой фазе в течение 1 ч. Образующаяся НСООН оказывает на реакцию каталитическое действие. Продукты гидролиза направляют в колонну для отделения водной НСООН. Из верхней части колонны отбирают смесь метанола и метилформиата, которую
Рис. 11.4. Принципиальная технологическая схема получения НСООН гидролизом метилформиата с избытком воды: 1 – реактор; 2 – колонна выделения НСООН; 3 – колонна выделения метанола; 4 – колонна концентрирования НСООН. Потоки: I – вода; II – метилформиат; III – метанол; IV – 82%-я муравьиная
кислота
затем разделяют. Метилформиат возвращают в реактор, а метанол направляют на стадию карбонилирования. Водную НСООН перегоняют в следующей колонне под давлением 0,3 МПа.
11.2. ПОЛУЧЕНИЕ ПРОПИОНОВОЙ КИСЛОТЫ
Одним из промышленных способов получения пропионовой кислоты является карбонилирование этилена (табл. 11.2).
Показано, что пропионовая кислота с селективностью 99 % образуется в мягких условиях (температура 195 °С, давление 7 МПа)
220