
Технологии органического и нефтехимического синтеза
..pdfГлава 5
ПРОИЗВОДСТВО КИСЛОРОДСОДЕРЖАЩИХ ПРОДУКТОВ НА ОСНОВЕ ОКСИДА УГЛЕРОДА
ИВОДОРОДА
5.1.ПРОИЗВОДСТВО КИСЛОРОДСОДЕРЖАЩИХ
НЕФТЕПРОДУКТОВ НА ОСНОВЕ ОКСИДА УГЛЕРОДА И ВОДОРОДА
Еще в начале XX в. было установлено, что при взаимодействии СО и Н2 в присутствии катализатора можно получить различные углеводороды. Так, в 1902 г. Собатье получил метан на металлическом Ni:
СО + Н2 ↔ СН4 + Н2О |
(5.1) |
В 1908 г. Орлов показал возможности получения на Ni–Cd-ката- лизаторе углеводородов с большей молекулярной массой, чем СН4:
2СО + 4Н2 ↔ СН2=СН2 + 2Н2О; |
(5.2) |
2СО + 5Н2 ↔ СН3–СН3 + 2Н2О |
(5.3) |
В1942 г. Фишер и Тропш разработали метод получения смеси углеводородов и кислородсодержащих соединений при давлении 10–15 МПа и температуре 360–420 °С в присутствии Fe-содержащего катализатора, промотированного КОН. На Со-содержащем катализаторе при давлении 3 МПа и температуре 200 °С получались преимущественно углеводороды. На основе этого метода в 1930-х гг. в Германии было организовано производство синтетического топлива.
Вдальнейшем было показано, что на Zn–Cr-катализаторе из СО
иН2 можно получить метанол по реакции
СО + Н2 ↔ СН3ОН |
(5.4) |
121
Внастоящее время это основной метод получения метанола
впромышленности.
В1970–80-х гг. интерес к синтезам на основе СО и Н2 вновь возрос. Это связано с мировым энергетическим кризисом 1970-х гг., а также с тем, что мировые запасы угля примерно в 6 раз превышают
мировые запасы нефти и газа. Кроме того, СО и Н2 можно получать газификацией из возобновляемых видов сырья (биомасса, отходы сельского хозяйства, городские отходы).
Исследования показали, что из СО и Н2 можно производить целую гамму различных органических соединений: парафиновые, олефиновые, ароматические углеводороды различной молекулярной массы, разнообразные кислородсодержащие соединения (спирты, альдегиды, кислоты и др.).
5.2. ПРОИЗВОДСТВО СИНТЕЗ-ГАЗА
Смесь СО и Н2 принято называть синтез-газом. Получать его можно из различных видов сырья, в частности из каменного угля, бытовых и сельскохозяйственных отходов. Однако в настоящее время его в основном получают из углеводородного сырья (природных и попутных газов, бензинов, мазута).
Основной метод получения синтез-газа – каталитическая конверсия углеводородного сырья водяным паром при высокой температуре. При этом могут протекать следующие реакции:
СН4 + Н2О ↔ СО + 3Н2; |
(5.5) |
СО + Н2О ↔ СО2 + Н2; |
(5.6) |
СН4 + СО2 ↔ 2СО + 2Н2; |
(5.7) |
СН4 + 0,5О2 ↔ СО + 2Н2 |
(5.8) |
Все реакции обратимы и идут с увеличением объема. (5.5) и (5.7) – эндотермичны, (5.6) и (5.8) – экзотермичны. Выходы продуктов близки к равновесным.
122
Различают три разновидности каталитической конверсии углеводородов:
–конверсия водяным паром;
–конверсия смесью водяного пара и СО2;
–конверсия смесью водяного пара с кислородом.
Конверсию водяным паром с СО2 применяют с целью получения синтез-газа с повышенным содержанием СО (смесь используется в производстве метанола, в оксосинтезе). Соотношение СН4 : СО2 может составлять 0,3 : 1 и более. Содержание СО в синтез-газе можно регулировать и меняя соотношение Н2О и СН4 в ходе конверсии.
Конверсию смесью водяного пара и кислорода ведут при использовании тяжелого углеводородного сырья (мазута).
В качестве катализатора конверсии СН4 применяют NiO, осажденный на α-Al2O3, в частности, отечественный катализатор ГИАП-5 представляет собой цилиндры или кольца, содержащие 5–25 % NiO на α-Al2O3 + промоторы (γ-Al2O3, MgO, щелочные добавки).
Направляемый на конверсию газ (сырье) не должен содержать сернистые и непредельные соединения. Первые дают сероводород, который отравляет катализатор, переводя его в NiS – неактивное
вданном процессе соединение; непредельные дают кокс на поверхности катализатора.
Каталитическую конверсию метана проводят при температуре
800–900 °С и мольном соотношении Н2О : СН4 от 2 : 1 до 6 : 1. Процессы ведут в трубчатых реакторах с однорядными вертикальными экранами двухстороннего облучения. В трубах находится катализатор. Трубы объединяются коллекторами, расположенными в верхней и нижней частях печи.
Парокислородную конверсию углеводородного сырья проводят
ввертикальных цилиндрических конверторах, изготовляемых из углеродистой стали, футерованных изнутри огнеупорным кирпичом (температура 1500 °С). Катализатор располагается на специальных решетках.
Рассмотрим технологическую схему паровой каталитической конверсии углеводородного сырья (рис. 5.1).
123
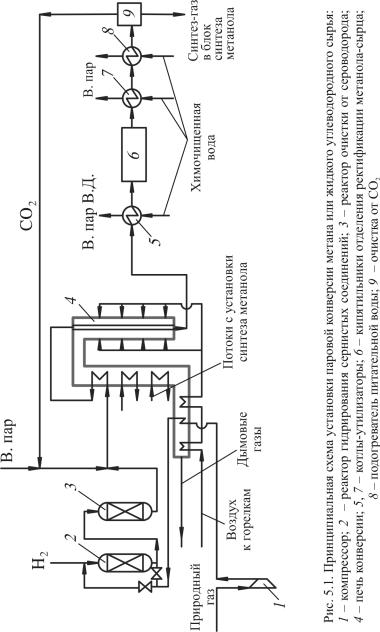
124
Согласно схеме углеводородный газ компримируется в компрессоре 1 до давления 2,3–2,5 МПа, подогревается в дымоходе печи конверсии 4 (за счет тепла дымовых газов) и идет на очистку от сернистых соединений. В случае необходимости направляется в реактор гидрирования 2 для перевода сернистых соединений в H2S. Далее сырье идет в реактор 3, где обессеривание идет на ZnO при температуре 400 °С. Если сырье не требует гидроочистки, оно сразу идет
вреактор 3, затем смешивается с водяным паром (при необходимо-
сти с СО2) и подогревается в камере конвекции за счет тепла дымовых газов до температуры 500–550 °С. После этого сырье поступает
врадиантные трубы печи 4, заполненные Ni катализатором. На выходе из радиантных труб температура составляет 850–880 °С. Дымовые газы из радиантных труб идут в камеру конвекции, где подогревается сырье, воздух – к горелкам, образуется пар высокого давления. Далее дымовые газы отсасываются дымососом и выбрасываются
вдымовую трубу.
Получаемый синтез-газ проходит котлы-утилизаторы 5 и 7, где генерируется пар высокого и низкого давления, и кипятильник 6. Далее он идет в подогреватель питательной воды котлов-утилизаторов 8, направляется в блок очистки от СО2 9, а затем на синтез. СО2 идет на конверсию, смешиваясь с водяным паром.
Если в качестве сырья используют тяжелые нефтяные остатки (мазут) или уголь, их подвергают газификации путем парокислородной конверсии. После этого проводят частичную конверсию СО с использованием сероустойчивого катализатора. Далее синтез-газ подвергается очистке отH2S иизбытка СО2.
5.3. ОКСОСИНТЕЗ. ГИДРОФОРМИЛИРОВАНИЕ ОЛЕФИНОВ
Реакциягидроформилирования(оксосинтеза) былаоткрытав1938 г. Роеленом. Термин же «оксосинтез» относится ко всему технологическому циклу получения альдегидов и соответствующих спиртов, включающему все стадии процесса (гидроформилирование, получение и выделе-
125
ние катализатора, разделение продуктов синтеза и гидрирование альдегидоввсоответствующиеспирты).
В настоящее время ассортимент вырабатываемых промышленностью оксопродуктов превышает 50 наименований: пропанол, бутанолы, спирты С7–С19, изодеканол, тридециловый спирт, адипиновая кислота и многие другие.
Крупнейшие фирмы-производители оксопродуктов: Union Car-
bide, Monsanto, Shell, Mitsubishi и др.
Первая промышленная установка оксосинтеза по производству 2-этилгексанола и изодецилового спирта была пущена в 1948 г. в США. Мировое производство оксопродуктов в настоящее время превышает 7 млн т/год.
Большое количество оксопродуктов производит и Россия – около 400 тыс. т/год.
Из продуктов гидроформилирования наиболее значимые – спирты С3–С19, применяемые в качестве растворителей, стабилизаторов. Оксоспирты применяются при производстве пластификаторов ПВХ, моющих средств, синтетических смазочных масел, фармацевтических препаратов, лакокрасочных покрытий.
Реакция гидроформилирования – присоединение СО и Н2 по двойной связи к олефину. При этом образуются альдегиды н- и изостроения:
RСН=СН2 + СО + Н2 → RСН2СН2СНО; |
(5.9) |
|
RСН=СН2 + СО + Н2 |
→ RСНСН3 |
(5.10) |
|
| |
|
СНО В зависимости от используемого катализатора реакция протека-
ет при температуре 120–200 °С и давлении 1–30 МПа.
Из получаемых альдегидов наибольшее практическое применение имеют продукты нормального, а не изостроения.
126
5.3.1. Катализаторы реакции гидроформилирования
Реакцию гидроформилирования в той или иной степени катализируют соединения Fe, Mn, Ru, Co, Rh и др.
Впромышленности в процессе гидроформилирования получили применение гомогенные системы, содержащие комплексы переходных металлов трех видов:
1) гидрокарбонил кобальта НСо(СО)4;
2) гидрокарбонил кобальта, модифицированный третичными
фосфинами, например трибутилфосфинами НСо(СО)3РБут3; 3) гидрокарбонильные комплексы родия с координированным
третичным фосфином, например, [HRh(CO)(PБут3)3].
Процесс гидроформилирования на катализаторе НСо(СО)4 характеризуется температурой 140–180 °С, давлением 25–30 МПа (соотношение продуктов н- и изостроения (3–4) : 1, из которых 80 % – альдеги-
ды, 10 % – спирты); на катализаторе НСо(СО)3РБут3 процесс протекает при температуре 160–200 °С, давлении 5–10 МПа (соотношение продуктов н- и изостроения составляет (6–8) : 1, из которых 80 % – спирты
и10–20 % – альдегиды); на катализаторе [HRh(CO)(PБут3)3] процесс идет при температуре 80–100 °С, давлении 1,5–2,5 МПа (соотношение продуктов н- и изостроения составляет (15–20) : 1, из которых 96 % – альдегиды).
Внастоящее время 50 % оксопродуктов в мире вырабатывается
с использованием катализатора НСо(СО)4.
Выбор условий проведения процесса гидроформилирования диктуется не термодинамикой, а необходимостью перевода катализа-
тора в активную форму, в частности, Со2(СО)8 в НСо(СО)4, высокое же давление стабилизирует эту активную форму.
Реакция гидроформилирования экзотермична. Скорость реакции пропорциональна концентрации олефина, катализатора и температуре. Зависит она и от строения олефина.
Из большого числа побочных реакций лишь гидрирование протекает параллельно основной реакции:
RСН=СН2 + Н2 → RСН2СН3 |
(5.11) |
127
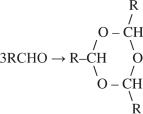
Остальные побочные реакции идут с участием образующихся альдегидов и протекают последовательно по отношению к реакции гидроформилирования.
Основные побочные реакции:
– гидрирование альдегидов в спирты:
RСНО + Н2 → RСН2ОН; |
(5.12) |
– альдольная конденсация: |
|
2СН3(СН2)2СНО → СН3(СН2)2СН=С–СНО + Н2О; |
(5.13) |
| |
|
С2Н5 |
|
– образование ацеталей: |
|
RСНО + 2НОСН2R → RСН(ОСН2R)2 + Н2О; |
(5.14) |
– сложноэфирная концентрация: |
|
2RСНО → RСООСН2R; |
(5.15) |
– реакция уплотнения: |
(5.16) |
Поскольку среди продуктов оксосинтеза наиболее предпочтительны продукты с прямой цепью, то при использовании того или иного катализатора определены наиболее оптимальные условия его применения, так как выход продуктов нормального строения зависит от температуры и давления.
В качестве растворителей реакции гидроформилирования обычно используют: толуол, кубовые продукты самого оксопроцесса, простые эфиры, алифатические спирты, кетоны, пентан-гексановую фракцию.
128
5.3.2.Влияние примесей на процесс гидроформилирования
Как олефиновое сырье, так и синтез-газ могут содержать примеси, влияющие на протекание основной реакции. Основные из них: диеновые, ацетиленовые, сернистые и перекисные соединения, кислород, аммиак.
Так, кислород окисляет карбонилы кобальта до СоО (аналогично ведут себя и перекисные соединения):
Со2(СО)8 + О2 → 2СоО + 8СО |
(5.17) |
Несмотря на то, что СоО вновь переходит в условиях процесса в Со2(СО)8:
2СоО + 8СО + 2Н2 → Со2(СО)8 + Н2О, |
(5.18) |
реакция протекает медленно, а это сказывается на скорости самого процесса.
Диеновые и ацетиленовые углеводороды оказывают ингибирующее действие на реакцию гидроформилирования, образуя комплекс диолефина с НСо(СО)4 → С4Н6 НСо(СО)4.
Аналогично ведут себя и ацетиленовые соединения:
RC≡CR + Со(СО)8 → RC–CR + 2CO |
(5.19) |
| | | |
(СО)3Со Со(СО)3
Примеси аммиака образуют с НСо(СО)4 соль, неактивную в реакции гидроформилирования:
NH3 + HCo(CO)4 → NH4Co(CO)4 |
(5.20) |
Сернистые соединения тормозят реакцию гидроформилирования, связывая Со в сульфаты:
129
Co2(CO)8 + 2H2S → 2CoS + 8CO + 2H2; |
(5.21) |
Co2(CO)8 + C2S → 2CoS + 8CO + C |
(5.22) |
До настоящего времени механизм реакции гидроформилирования еще полностью не выяснен. Общепризнанной считается схема механизма, предложенная Бреслоу и Хеком в 1961 г. Согласно данной схеме реакция гидроформилирования протекает по механизму цепного типа, при этом роль активных частиц, ведущих цепь, играют координационно-ненасыщенные соединения.
5.3.3. Реакционные устройства процесса гидроформилирования
Основное требование к реакционным устройствам – это обеспечение минимального выхода побочных продуктов. Максимально это достигается при проведении реакции в реакторе идеального вытеснения, в котором обеспечивается минимальная средняя концентрация альдегидов, а следовательно, создаются условия для минимального образования побочных продуктов.
По способу съема тепла применяемые реакторы делятся:
–на реакторы с внутренним теплосъемом;
–реакторы с внешним теплосъемом;
–реакторы комбинированного типа.
В реакторах с внутренним теплосъемом тепло снимается за счет подачи холодного сырья или продуктов гидроформилирования прямо в зону реакции. Все компоненты реакции подаются в зону реакции сни-
зу (рис. 5.2).
Достоинством аппаратов данного типа является простота конструкции и изготовления, недостатком – повышенный выход побочных продуктов.
Реакторы с внешним теплосъемом (рис. 5.3). Наиболее оп-
тимальны в процессе гидроформилирования колонные аппараты со встроенными трубчатками либо теплообменные аппараты типа
130