
Технологии органического и нефтехимического синтеза
..pdf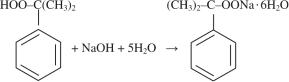
цесс окисления ИПБ оказывает влияние рН среды: скорость реакции возрастает в щелочной среде.
Для окисления ИПБ применяют реакторы: колонного типа, с перемешивающим устройством и эрлифтного типа.
8.4.2. Стадия выделения гидропероксида ИПБ
ГП может быть извлечен из реакционной массы окисления химическими и физическими методами. В первом случае ГП обрабатывают NаОН и переводят в твердую натриевую соль, которую затем отфильтровывают:
(8.7)
От увлеченного осадком маточного раствора соль промывают легким растворителем или растворяют в воде.
Из водно-щелочного раствора ГП выделяют в виде мутного маслянистого слоя путем пропускания через раствор диоксида углерода. В итоге получают 97–98%-й концентрат ГП.
Физический метод выделения ГП сводится к его концентрированию перегонкой. Реакционная масса после окисления подвергается двухступенчатой ректификации под вакуумом для отгонки непрореагировавшего ИПБ и воды. Концентрированный ГП содержит 90–93 % основного вещества.
Физический метод имеет преимущества перед химическим.
Вотечественной практике используют реакторы колонного типа
икаскады реакторов с перемешивающим устройством.
Рассмотрим технологическую схему процесса (рис. 8.3). Согласно схеме смесь свежего и возвратного ИПБ, содержащего
2–3 % ГП, из емкости 6 поступает в теплообменник 3, где нагревается
191
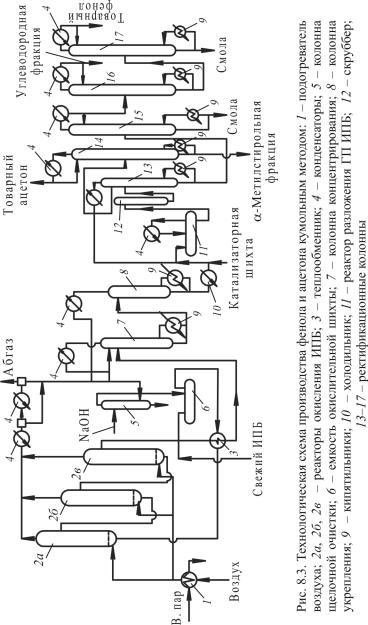
192
за счет тепла реакционной массы окисления, и далее – в первый по ходу реактор 2а. Реакционная масса из каждого реактора направляется в последующий 2б и 2в, а сжатый воздух, нагретый до 110 °С в подогревателе 1, подается в нижнюю часть каждого из трех реакторов.
Давление в реакторах поддерживается на уровне 0,3–0,5 МПа, температура 120–130 °С. Для отвода тепла реакции в каждом реакторе установлены змеевики водяного охлаждения, через которые прокачивается умягченная вода.
Отработанный воздух выводится сверху из каждого реактора и направляется общим потоком в систему конденсаторов 4, охлаждаемых водой и рассолом, где конденсируется ИПБ. Конденсат стекает в колонну промывки щелочью 5.
Реакционная масса окисления из колонны 2в направляется через теплообменник 3 последовательно в колонны концентрирования и укрепления ГП 7 и 8, работающие под вакуумом.
Пары ИПБ из колонн 7 и 8 конденсируются, и после нейтрализации муравьиной кислоты в промывателе 5 изопропилбензол через емкость 6 возвращается на окисление.
8.4.3. Разложение гидропероксида изопропилбензола
Разложение ГП идет под действием серной кислоты с выделением тепла, в связи с чем в реакторе должен быть предусмотрен интенсивный отвод тепла для поддержания оптимальной температуры.
Для предотвращения неконтролируемого процесса (подъем температуры и давления может привести к взрыву) концентрированный ГП разбавляют циркулирующим разбавителем. В качестве разбавителя используют продукты реакции. Разложение ГП идет с использованием реакторов двух типов: адиабатического и изотермического.
Согласно схеме (см. рис. 8.3) ГП через холодильник 10 направляется в реактор 11 на разложение. Туда же поступает катализатор (50%-й раствор серной кислоты в ацетоне). Разложение осуществляют в избытке ацетона при температуре 60 °С.
193
Тепло реакции разложения ГП отводится путем частичного испарения ацетона. Пары ацетона конденсируются в соответствующем конденсаторе и возвращаются в реактор 11. Продукты разложения из реактора 11 подаются на нейтрализацию в скруббер 12, откуда нейтрализованная масса направляется на ректификацию. В колонне 13 отгоняется ацетон-сырец. Часть его возвращается в колонну 13 на орошение, остальное – в колонну 14, из верхней части которой отбирается товарный ацетон, а с одной из верхних тарелок – ацетон, подаваемый в реактор 11 для разбавления и отвода тепла реакции. Из нижней части колонны 14 отбирается α-метилстирольная фракция.
Остаток колонны 13 направляется в колонну 15, где отгоняется фенол с примесью низкокипящих компонентов (ИПБ и α-метилстирол). Кубовый остаток выводится из системы, а пары после конденсации поступают в колонну 16, из верхней части которой отбирается углеводородная фракция, а из нижней – фенол-сырец, направляемый в колонну 17 для выделения товарного фенола. Куб колонны 17 содержит ацетон, диметилфенилкарбинол, димер α-метилстирола исмолы.
Большое значение в процессе имеет использование побочных продуктов – их реконверсия в фенол. Особенно это относится к фенольной смоле.
По одному из способов фенольную смолу гидрируют метановодородной фракцией на алюмокобальтмолибденовом катализаторе при температуре 350 °С и давлении 4,9 МПа. Далее гидрогенизат подвергается ректификации с выделением ИПБ (до 49 %), фенола (до 23 %) и ЭБ (до 13 %) (проценты приведены на исходную смолу).
По другому методу фенольную смолу подвергают ректификации под вакуумом. При этом происходит частичная деструкция кумилфенола с образованием фенола и α-метилстирола и деполимеризация части димера α-метилстирола. Одновременно диметилфенилкарбинол дегидрируется и превращается в α-метилстирол, который выделяется ректификацией. Выделяют также фенол-сырец, возвращаемый в основную систему ректификации, и ацетофенон.
Глава 9
СИНТЕЗ МЕТАНОЛА
9.1. МЕХАНИЗМ СИНТЕЗА МЕТАНОЛА
Синтез метанола из СО и Н2 на оксиде цинка в качестве катализатора был разработан Патаром в 1921 г.
Промышленное производство синтетического метанола началось с 1923 г. в Германии (осуществлено фирмой «Баденская анилиновая и содовая фабрика» – ВАSF), с 1927 г. – в США и с 1934 г. – в России на Новомосковском химическом комбинате из водяного газа, получаемого газификацией кокса. Процесс проводился под давлением 25–35 МПа на оксидном цинкхромовом катализаторе при температуре
320–380 °С.
В 1960-х гг. в Англии был разработан и освоен промышленный синтез метанола под давлением около 5 МПа на оксидном медьсодержащем катализаторе при температуре 220–310 °С. Обязательным условием хорошей работы низкотемпературного катализатора является наличие в газовой смеси синтеза метанола диоксида углерода (4–5 об. %) для поддержания высокой активности катализатора. При более высоких температурах происходит рекристаллизация катализатора и его активность падает.
Синтез метанола при давлении 5–10 МПа получил наиболее широкое применение, старый метод производства метанола при высоком давлении утрачивает практическое значение.
Имеются сведения о катализаторе синтеза метанола, состоящем из интерметаллида торий– медь, на котором при 6 МПа и 280 °С и объемном соотношении Н2 : СО = 16 : 1 образуется до 40 мол. % метанола.
Для синтеза метанола предложены также промотированные цинком медные катализаторы Ренея, которые получают выщелачиванием алюминий-медь-цинковых сплавов. Эти катализаторы имеют
195
высокую активность и селективность, приводят к образованию диметилового эфира, что может оказаться благоприятным, если смесь метанола и диметилового эфира используется, например, в производстве бензина по способу «Мобил».
Взаимодействие водорода с оксидами углерода обратимо и протекает с выделением теплоты:
СО + 2Н2 ↔ СН3ОН, |
∆Н298° = –90,3 кДж; |
(9.1) |
СО2 + 3Н2 ↔ СН3ОН + Н2О, |
∆Н298° = –49,4 кДж. |
(9.2) |
Энтальпия реакции взаимодействия монооксида углерода с водородом незначительно возрастает с повышением температуры и давления. Кроме этих реакций, при синтезе метанола протекает и эндотермическая обратимая реакция диоксида углерода и водорода:
СО2 + Н2 ↔ СО + Н2О, |
∆Н298° = –41,0 кДж. (9.3) |
Механизм образования метанола из оксидов углерода и водорода сложен и до конца не выяснен. Достаточно отметить, что в литературе приводится более десяти кинетических уравнений синтеза метанола, отражающих различные схемы механизма процесса.
В течение почти 70 лет механизм синтеза метанола из СО и Н2 (или СО2 и Н2) трактовался как последовательное восстановление оксидов углерода водородом:
СО2 + Н2 ↔ СО + Н2О; |
(9.4) |
СО + 2Н2 ↔ СН3ОН |
(9.5) |
Справедливость этой схемы подтверждалась многочисленными прямыми и косвенными факторами.
Было предложено несколько механизмов образования метанола из СО и Н2 на активных центрах катализатора (М). Например, для цинкхромовых катализаторов предусматривается образование промежуточных гидроксилметила (I) или метоксида (II) по схемам:
М + СО → МСО; |
(9.6) |
2М + Н2 → 2МН; |
(9.7) |
196

МСО + МН → МСНО + М; |
(9.8) |
МСО + МН → МСН2ОМ; |
(9.9) |
МСН2ОН + МН → МСН2ОН + 2М; |
(9.10) |
(I) |
|
МСН2ОН + МН → СН3ОН + 2М; |
(9.11) |
МСНО + МН → СН2О + 2М; |
(9.12) |
СН2О + МН → CH3OM; |
(9.13) |
(II) |
|
СН3ОМ + МН → СН3ОН + 2М |
(9.14) |
Справедливость этих схем подтверждалась многочисленными прямыми и косвенными факторами.
Исследования механизма синтеза метанола, проведенные в нашей стране в 1970–80-х гг., показали, что на оксидных катализаторах, в частности на медьсодержащих, возможно образование метанола также из диоксида углерода, присутствующего в исходной смеси или образующегося по реакции конверсии оксида углерода водой:
СО + Н2О ↔ СО2 + Н2; |
(9.15) |
СО2 + 3Н2 ↔ СН3ОН + Н2О |
(9.16) |
Главными особенностями данной схемы являются окислитель- но-восстановительный характер синтеза метанола и его цикличность.
Полагают, что образование метанола может происходить через стадию образования карбонатных и формиатных комплексов на поверхности медьсодержащего катализатора, обнаруженных спектральными методами:
(9.17)
197
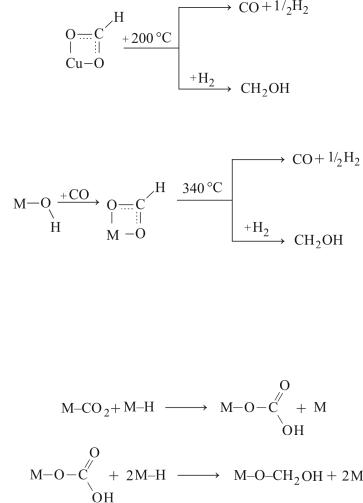
Карбонатные комплексы при гидрировании превращаются в метанол и формиатные комплексы. Формиатные комплексы склонны
краспаду и гидрированию в метанол.
1.Формиаты, адсорбированные на атомах Сu:
(9.18)
2. Формиаты, адсорбированные на атомах Zn и Аl с участием ОН-группы:
(9.19)
Схему механизма превращения СО2 в СН3ОН с участием Н2 на катализаторе Cu–ZnO/Al2О3 можно представить следующим образом:
СО2 + М ↔ М–СО2; |
(9.20) |
Н2 + 2М ↔ 2М–Н; |
(9.21) |
|
(9.22) |
|
(9.23) |
M–O–CH2OH + M–H → CH3OH + M–O–M |
(9.24) |
198
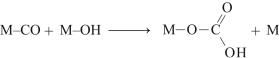
На поверхности катализатора формиаты находятся в монодентатной и бидентатной формах, а реакция образования метанола протекает через лимитирующую стадию гидрирования формиата на меди.
Образование формиатов, возможно, также происходит по реакциям с участием оксида углерода:
М + СО ↔ М–СО; |
(9.25) |
|
(9.26) |
Формиатные комплексы, по-видимому, могут образовываться с различными скоростями из смеси СО2 + Н2 и СО + Н2. Возможно, этими различиями и объясняются разные скорости синтеза СН3ОН из этих смесей на разных катализаторах и в разных условиях.
Возможны и другие схемы механизма образования метанола, так как на поверхности катализатора были обнаружены группы Cu–Н, Сu–ОН, Сu–СО, Сu–СНО. Дальнейшие исследования, по-видимому, дадут однозначный ответ на вопрос о механизме образования метанола из синтез-газа.
9.2. ОСНОВНЫЕ ЗАКОНОМЕРНОСТИ ПРОЦЕССА
Влияние температуры и давления. Цинкхромовые катализаторы работают при температуре 330–400 °С и давлении 20–40 МПа; мед- но-цинковые – при температуре 220–270 °С и давлении 5–10 МПа.
Выбор рабочего давления в указанных диапазонах определяется кроме температуры составом синтез-газа, заданной производительностью и скоростью побочных реакций (в частности, метанообразования); выбор температуры – активностью катализатора и конструкцией реактора.
Влияние объемной скорости синтез-газа. С увеличением объемной скорости синтез-газа, особенно в интервале 10 000–40 000 ч–1, выход
199
метанола и производительность катализатора сначала растут, а затем проходят через максимум.
Влияние рециркуляции газа. Степень превращения синтез-газа за проход через реактор составляет 15–50 %, что определяется положением равновесия реакции образования метанола в выбранных условиях синтеза, продолжительностью контакта и допустимым перепадом температуры по слою катализатора при адиабатическом режиме процесса. Поэтому все промышленные установки работают с рециркуляцией газа после отделения от него воды и метанола. Для определения коэффициента рециркуляции предложена формула
UG |
= U E |
1 + Ф |
|
|
, |
(9.27) |
|
|
|
Са |
|
||||
|
|
|
|
|
|||
|
|
1 + Ф 1 |
− |
|
|
|
|
|
|
|
|
|
|||
|
|
|
|
С0 |
|
|
где UG – общая степень превращения СО; UE – степень превращения СО за проход; Ф – коэффициент рециркуляции;
С0 – концентрация СО во входящем газе, мол. %; Са – концентрация СО в отходящем газе после конденсации воды
и метанола, мол. %.
Рециркуляция позволяет регулировать тепловой режим реактора и состав синтез-газа.
Состав синтез-газа. В процессах высокого давления используют синтез-газ, обогащенный водородом (Н2 : СО = (10–12) : 1). Отимальный состав синтез-газа для процессов низкого давления Н2 : СО≈ 3,5 : 1.
Избыток водорода по отношению к стехиометрическому позволяет повысить скорость реакции, улучшить качество метанола-сырца и ограничить содержание инертных компонентов.
Концентрация СО в синтез-газе составляет 5–25 об. %. Это объясняется тем, что с повышением концентрации СО увеличивается тепловыделение. Содержание СО2 поддерживается в пределах
2–5 об. %.
200