
Технологии органического и нефтехимического синтеза
..pdfГлава 7
ПРОИЗВОДСТВО КИСЛОРОДСОДЕРЖАЩИХ ПРОДУКТОВ ОКИСЛЕНИЕМ НЕНАСЫЩЕННЫХ УГЛЕВОДОРОДОВ
Прямое окисление ненасыщенных углеводородов (в основном С2–С4) осуществляется в промышленности в основном для получения оксидов олефинов, альдегидов (формальдегида, кротонового альдегида и др.), кетонов, карбоновых кислот и их производных.
По сравнению с насыщенными углеводородами окисление ненасыщенных идет более селективно с образованием одного целевого продукта.
7.1. ОКИСЛЕНИЕ НЕНАСЫЩЕННЫХ УГЛЕВОДОРОДОВ
ВОКСИДЫ ОЛЕФИНОВ. ПОЛУЧЕНИЕ ЭТИЛЕНОКСИДА
ИПРОПИЛЕНОКСИДА
Рост производства этилен- и пропиленоксидов стимулируется расширением области их применения при получении растворителей, ПАВ, пластификаторов, антифризов, полиуретанов и других продуктов.
Наиболее простой метод получения оксидов из непредельных – это присоединение кислорода по двойной связи олефина.
7.1.1. Производство этиленоксида
Этиленоксид– это один из наиболее крупнотоннажных продуктов нефтесинтеза. Основная область его применения – получение этиленгликоля, который используется, в свою очередь, для производства антифриза, полиэфирных смол, волокон, пленок. Из этиленоксида получают ПАВ, эфиры гликолей, этаноламины, некоторые виды каучуков.
161
Получают этиленоксид по реакции |
|
СН2=СН2 +0,5O2→ Н2С–СН2 |
(7.1) |
\ / |
|
O |
|
Одновременно протекают следующие побочные реакции: |
|
а) окисление этилена до СО2 и Н2О; |
|
б) с образованием ацетальдегида: |
|
Н2=СН2 + 0,5О2 → СН3СНО; |
(7.2) |
в) с получением формальдегида: |
|
СН2=СН2 + О2 → 2НСНО |
(7.3) |
Процесс окисления этилена в этиленоксид ведут на серебряном катализаторе (единственный применяемый в промышленности в различных модификациях). На активность и селективность серебряного катализатора оказывают влияние метод его приготовления и используемые промоторы. Серебро наносят на Аl2О3, корунд, силикагель, пемзу. На свойства катализатора влияют степень дисперсности серебра, размер и форма кристаллов. В качестве промоторов применяют хлорпроизводные, соединения серы, селена, фосфора, бария, кальция, алюминия, золота, калия, рубидия и др.
Температура процесса лежит в пределах 200–300 °С. Ниже 200 °С мала скорость процесса, выше 300 °С превалируют реакции глубокого окисления.
7.1.1.1. Технологические особенности процесса
При получении этиленоксида в качестве окислителя применяют кислород или воздух.
Используемый в процессе серебряный катализатор легко отравляется различными примесями (сернистые соединения, ацетилен и др.). В связи с этим как этилен, так и окислитель должны быть очищены от химических и механических примесей, так как в этом
162
случае возрастает срок службы катализатора. В частности, при синтезе применяют этилен с чистотой 98–99,5–99,9 %. Содержание сернистых соединений (в перерасчете на серу) не должно превышать 0,0001 об. %, ацетилена – 0,001 об. %. Количество мехпримесей в воздухе не должно превышать 0,007 мг/м3.
Для достижения требуемых параметров по чистоте этилен и воздух подвергают очистке: от соединений серы промывают щелочью, водой, пропускают через адсорбер с активированным углем; ацетилен удаляют либо селективным гидрированием, либо с помощью оксида меди с осаждением ацетиленидов меди.
Процесс окисления этилена ведут в две или три стадии с рециркуляцией этилена и низкой степенью окисления его на каждой ступени, так как при повышении степени превращения снижается селективность и увеличивается выделение тепла. В случае использования воздуха в качестве окислителя после ступени абсорбции этиленоксида из контактного газа производят сброс инертных примесей.
Процесс абсорбции этиленоксида ведут водой под давлением. Насыщенный абсорбент отправляют на отпарку. Отогнанную смесь этиленоксида и диоксида углерода подвергают ректификации для выделения чистого этиленоксида.
Процесс осуществляют при температуре 250–270 °С. Состав смеси определяется пределами взрываемости (3–3,4 об. % этилена в воздухе). Обычно концентрация этилена не превышает 4 об. %, кислорода – 7 об. %. Давление в процессе 2,5–3,5 МПа. Катализатор – серебряный, срок службы которого составляет 6–9 лет. В оптимальных условиях конверсия этилена находится в пределах 30–50 %, селективность 60–75 %.
7.1.1.2. Аппаратурное оформление процесса
Основная трудность процесса получения этиленоксида– необходимостьотводатепла, таккакприперегревевозрастаетвыходСО2 иН2О.
В промышленности используют трубчатые реакторы (в трубках – катализатор, а в межтрубном пространстве – теплоноситель – вода под
163
давлением или высококипящие органические жидкости: дифенил, смесь дифенила и дифенилоксида).
Основной недостаток этих реакторов – наличие местных перегревов, что ведет к увеличению выхода СО2 и Н2О и снижению образования этиленоксида.
Реактор и трубопроводы изготовляются из нержавеющей хромоникелевой стали, так как среда чрезвычайно коррозионноактивна. Кроме того, использование хлорсодержащих промоторов (дихлорэтан) при разложении может дать НСl – весьма агрессивное соединение.
Рассмотрим технологическую схему окисления этилена воздухом (рис. 7.1), в которой предусмотрена возможность получения и гликолей при взаимодействии этиленоксида и воды (этиленгликоля) или этиленгликоля и этиленоксида (диэтиленгликоля).
|
Н2С–СН2 + H2O → СН2–СН2 (этиленгликоль); |
(7.4) |
|||
|
\ |
/ |
| |
| |
|
|
O |
O |
O |
|
|
СН2–СН2 + Н2С–СН2 |
→ СН2CH2OCH2CH2 (диэтиленгликоль) |
(7.5) |
|||
| |
| |
\ / |
| |
| |
|
O |
O |
O |
OH |
OH |
|
Согласно схеме воздух поступает на прием компрессора 1, куда направляется и циркулирующий газ из абсорбера 7. Смесь проходит очиститель воздуха 2, смешивается с этиленом и идет в теплообменник 6, и далее направляется в реактор 4, где идет ее окисление с образованием этиленоксида и некоторого количества СО2 и Н2О. Тепло реакции отводится с помощью органического высококипящего теплоносителя, который отдает тепло в котле-утилизаторе 3, где генерируется водяной пар.
Контактный газ из реактора 4 проходит через теплообменник 6, охлаждается и поступает в абсорбционную колонну первой ступени 7, орошаемую водой (или раствором этиленгликоля). Непоглощенный газ из колонны 7 делится на 2 потока. Один поток направляется в виде рецикла на прием компрессора 10, второй (меньший) идет на конечную ступень контактирования. Поскольку в систему поступает
164

165
азот, а при окислении образуется диоксид углерода, эти инертные примеси необходимо вывести из системы. Однако подлежащий отдувке газ содержит непревращенный этилен, который нельзя сбрасывать. Поэтому второй поток газа направляется на конечную ступень контактирования с целью использования содержащегося в нем этилена. Газ проходит теплообменник 6, реактор 8, после чего продукты реакции через тот же теплообменник направляются в абсорбер 9. Непоглощенный в абсорбере газ сбрасывается.
Насыщенный абсорбент из абсорберов 7 и 9 через теплообменник 6 поступает в колонну 10, где отгоняется этиленоксид и легкие газы, а регенерированный абсорбент через теплообменник вновь возвращается в абсорберы 7 и 9. Верхний продукт колонны 10 в отпарной колонне 13 освобождается от газообразных компонентов. Часть остатка колонны 13 идет в колонну 14, где дополнительно освобождается от воды и тяжелых компонентов.
Ректификат колонны 14 представляет собой товарный этиленоксид, который выводится с установки. Другая часть остатка колонны 13 направляется на гидратацию в гидрататор 19 для получения гликолей. Из гидрататора 19 продукт поступает в испаритель 20 для обезвоживания гликолей. Остаток колонны 20 подвергается ректификации в колонне 21 с разделением на МЭГ и смесь ДЭГ и ТЭГ.
При использовании кислорода вместо воздуха отпадает необходимость в хвостовом реакторе и второй ступени контактирования. Этилен, кислород и циркулирующий диоксид углерода в смеси с непрореагировавшим этиленом направляются в реактор 15. Продукты реакции идут в абсорбер 16 для извлечения этиленоксида. Неабсорбированный газ поступает в абсорбер 17, где абсорбируется часть диоксида углерода. Неабсорбированный диоксид углерода компримируется и смешивается с сырьевой смесью. В десорбере 18 отдувается диоксид углерода. Насыщенный абсорбент из абсорбера 16 направляется в отпарную колонну 10. Отпаренный остаток колонны 10 поступает в абсорберы 7 и 9 или 16. В качестве абсорбента используется вода.
166
7.1.2. Производство пропиленоксида
Пропиленоксид так же, как и этиленоксид, относится к крупнотоннажным продуктам. Применяется для получения пропиленгликоля, полимерных продуктов (полипропиленоксидов, полипеноуретанов). Кроме того, важной областью использования пропиленоксида является производство деэмульгаторов (проксанолов, проксаминов) и других неионогенных ПАВ, применяемых для обезвоживания и обессоливания нефти и производства моющих средств.
Из пропиленоксида получают глицерин, амиловый спирт, который используется для производства ненасыщенных полиэфиров. Пропиленоксид является низкокипящим растворителем для углеводородов, виниловых полимеров, масел, применяется в качестве промышленного азеотропного агента при разделении смесей пентанов и пентенов с диенами.
Основные методы получения пропиленоксида: а) хлоридный; б) электрохимический;
в) метод эпоксидирования пропилена над кислотами или Н2О2; г) окисление пропилена молекулярным кислородом (процесс идет в газовой или жидкой фазах – сопряженное окисление в присут-
ствии уксусной кислоты); д) окисление пропилена пироксидами углеводородов.
Последний метод относится к основным как в нашей стране, так и за рубежом.
7.1.3. Технология окисления пропилена гидропероксидами углеводородов
Окисление пропилена гидроксидами углеводородов идет в присутствии катализатора. В результате получается пропиленоксид и соответствующий спирт, который может быть использован как таковой или превращен дегидратацией в непредельный углеводород либо последующим гидрированием в исходный углеводород:
167
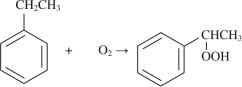
ROOH + CH2=CHCH3 → ROH + H2C–CHCH3
+O2↑ |
↓ –H2O |
(7.6) |
R'CH2CH3 ←+H2__ R'CH=CH2
В качестве эпоксидирующих агентов применяют третбутилгидропероксид, гидропероксиды этилбензола, изопропилбензола, изопентана, изопентена-2 и др. При этом получают 2-метилпропен, стирол, α-метилстирол, изопентен, изопрен.
Так, процесс окисления пропилена гидропероксидом этилбензола с целью получения оксида пропилена и стирола протекает с высокой скоростью в присутствии растворимых катализаторов (солей Со, Мо, Wо, Wa, Ti, Ni и др.). Применяются нафтенаты, ацетилацетонаты, гликоляты этих металлов.
Процесс осуществляют в жидкой фазе, обычно в растворе того углеводорода, из которого был получен гидропероксид при 2–5-крат- ном избытке олефина по отношению к гидропероксиду и 80–110 °С. Давление 2–7 МПа (для поддержания реакционной массы в жидком состоянии). Количество катализатора 0,001–0,005 моль на 1 моль гидропероксида. Время реакции изменяется от 0,3 до 2 ч.
Процесс получения пропиленоксида и стирола эпоксидированием пропилена гидропероксидом этилбензола включает 3 стадии:
1. Получение гидропероксида этилбензола окислением этилбензола:
(7.7)
На этой стадии побочными продуктами являются ацетофенон и метилфенилкарбинал, образующиеся вследствие разложения гидропероксида этилбензола:
168
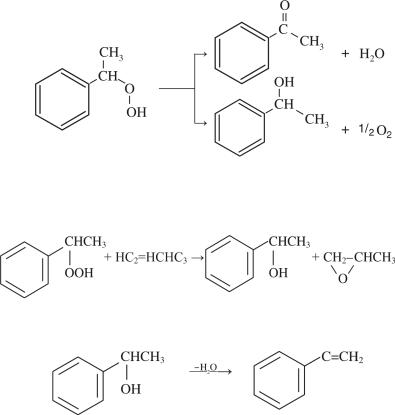
(7.8)
2. Эпоксидирование пропилена гидропероксидом с получением пропиленоксида и метилфенилкарбинола:
(7.9)
3. Получение стирола дегидратацией метилфенилкарбинола:
(7.10)
Рассмотрим технологическую схему процесса (рис. 7.2). Согласно схеме смесь свежего и возвратного этилбензола поступа-
ет на окисление в реактор 1. Окисление идет воздухом при температуре 140 °С и давлении 0,25 МПа в течение 6–4 ч до образования 10–13 % гидропероксида. Одновременно с этим за счет разложения гидропероксида образуются метилфенилкарбинол и ацетофенон. Полученный оксидат после охлаждения подается в колонну эпоксидирования 2, куда поступает свежий и возвратный пропилен и катализаторный раствор (0,6 мол. % растворимых солей Со в расчете на гидропероксид).
169
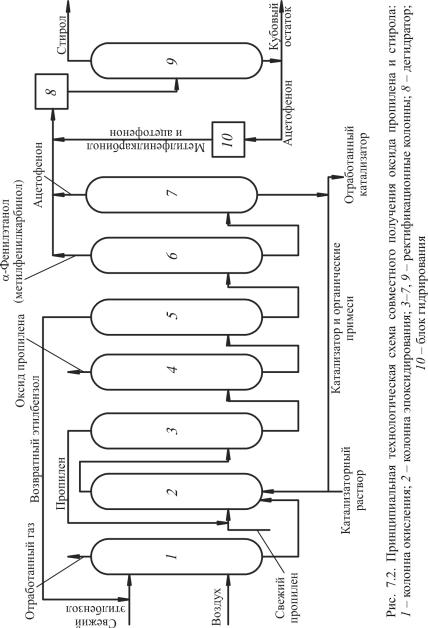
170