
Технологии органического и нефтехимического синтеза
..pdf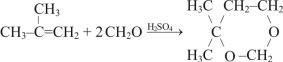
4.2.2. Разделение углеводородов С5
Разделение контактного газа первой и второй стадий дегидрирования изопентана и изопентенов аналогично процессу разделения контактного газа дегидрирования н-бутана и н-бутенов. Путем сочетания процессов абсорбции и ректификации можно выделить фракции С5 из контактного газа, однако разделение между собой углеводородов С5 удается только за счет применения экстрактивной дистилляции вследствие близости температур кипения разделяемых углеводородов. При этом в качестве экстрагентов используют: N-метилпирролидон, диметилформамид, диметилсульфолан.
Процесс разделения фракции С5 экстрактивной дистилляцией аналогичен процессам разделения углеводородов С4. В связи с тем что изопрен после выделения идет на полимеризацию в присутствии комплексных металлорганических катализаторов, его необходимо тщательно отмывать от следов экстрагента.
При экстрактивной дистилляции вместе с изопреном поглощаются и другие диены (пиперилен и циклопентадиен). Очистка изопрена от них проводится четкой ректификацией, однако процесс энергоемкий, таккакприходитсяотгонятьизопренотболеевысококипящихпримесей.
От ацетиленовых углеводородов изопрен очищают селективным гидрированием над никелевым катализатором.
4.2.3.Получение изопрена из 2-метилпропена
иформальдегида
Этот метод разработан в нашей стране Н.С. Немцовым. Метод освоен в промышленном масштабе. Процесс двухстадийный.
Первая стадия – конденсация 2-метилпропена с формальдегидом с образованием 4,4-диметил-1,3-диоксана по реакции:
(4.6)
111
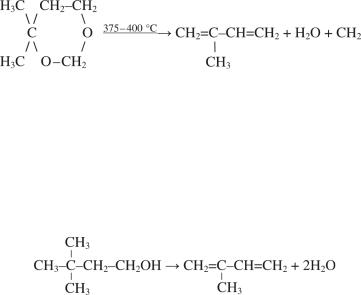
Реакцияпротекает притемпературе70–90 °Сидавлении1–1,6 МПа, катализатор – серная кислота. Выход 4,4-диметил-1,3-диоксана достигает 66–68 %, при конверсии 2-метилпропена – 88–92 %, формальдегида – 92–96 %.
Образуется на данной стадии и ряд побочных продуктов: карбинолы, метилаль, диоксановые спирты, диолы, эфиры и др. Особенно много образуется триметилкарбинола (СН3)3СОН (15 %) и 3-метил-
бутандиола-1,3 (5–7,5 %):
CH׀ 3
CH׀ 2–CH2–C–CH׀ 3
OH OH
Вторая стадия представляет собой газофазное каталитическое расщепление 4,4-диметил-1,3-диоксана с образованием изопрена:
(4.7)
Катализатор процесса – фосфорная кислота на алюмосиликате (оксид алюминия с 25 % оксида кремния), смесь фосфатов и другие вещества кислотного характера. Разбавление водяным паром 1 : 2. Глубина расщепления – до 90 %, выход изопрена 83–84 % от разложенного и 70–75 % от пропущенного диоксана.
3-метилбутандиол-1,3 в указанных условиях также превращается в изопрен:
(4.8)
112
В продуктах второй стадии наряду с изопреном содержатся: 2-метилпропен (10–12 %), продукты уплотнения, незначительные количества циклопентадиена (0,0002 %), формальдегид (86–99 % от стихоометрии).
В качестве сырья для получения изопрена используется изобутан – изобутиленовая фракция, содержащая не менее 40 % 2-метилпропена, не более 0,0005 % серы и 0,001 % ацетиленовых углеводородов.
Формалин должен содержать 37 % формальдегида и не более 1 % метанола.
Рассмотрим принципиальную технологическую схему процесса получения и расщепления диоксана (рис. 4.7).
Согласно схеме изобутан-изобутиленовая фракция направляется в нижнюю часть второго реактора 1 (спаренного), туда же поступает и серная кислота. Смесь свежего и возвратного формалина подвергается очистке и поступает в верхнюю часть первого реактора 1. Реакционная масса из реактора 1 направляется на нейтрализацию и отмывку от формальдегида в нейтрализатор 2, а затем в отстойник 3. Углеводородный слой из отстойника 3 подается в колонну 4 для выделения бу- тан-бутиленовой фракции, которая в колонне 5 разделяется на изобу- тан-изобутиленовую фракцию и бутены-2. Далее в колоннах 6 и 7 из углеводородного слоя отгоняются метилаль-метанольная фракция и триметилкарбинол. В колонне 8 идет отгонка 4,4-диметил-1,3-дио- ксана от высококипящих компонентов.
Водный слой из аппаратов 2 и 3 нейтрализуется щелочью, после чего в колонне 10 отгоняются низкокипящие органические соединения. Ректификат из колонны 10, состоящий из метилаля, метанола, триметилкарбинола и диоксана, присоединяется к углеводородному слою, а остаток – водный слой – направляется в колонны 11 и 12 для выделения возвратного формалина. Диоксан из колонны 8 вместе с возвратным диоксаном поступает на расщепление в реакторы второй стадии 13, куда подается водяной пар и Н3РО4.
Продукты реакции подвергаются ректификации. В колонне 16 выделяются высококипящие продукты, а в колонне 17 – изобутилен. Колонна 18 служит для очистки изопрена от высококипящих побочных
113
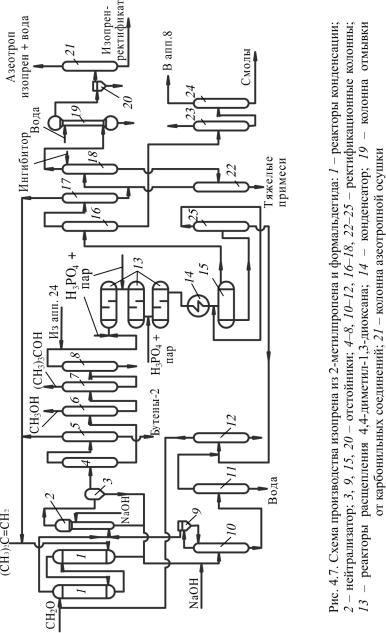
114

продуктов (доочистка). В колонне 19 проводится отмывка карбонильных соединений, в колонне 21 – азеотропная осушка. В колонне 22 идет дополнительное выделение изопрена-сырца из остатка колонны 18. В колоннах 23 и 24 из высококипящих продуктов, выделенных в колонне 16, извлекают непревращенный диоксан. Остатки из колонн 22 и 24 содержат ряд ценных кислородсодержащих продуктов.
Технологическое оформление первой стадии процесса определяется необходимостью вести процесс при высокой концентрации 2-метилпропена. Это обеспечивается применением реактора идеального вытеснения. Для отвода тепла применяют реактор трубчатого типа. 2-Метилпропен иформальдегид подаются в реактор противотоком.
Вторая стадия расщепления диоксана идет с поглощением тепла. Для подвода тепла применяют реакторы полочного типа со стационарным слоем катализатора. В качестве теплоносителя используется перегретый водяной пар, подаваемый в реактор ступенчато, что обеспечивает почти изотермический режим.
Регенерация катализатора осуществляется каждые 5–6 ч в начале работы катализатора и каждые 2–3 ч в конце его работы.
Продолжительность циклов работы и регенерации катализатора одинакова. Активность катализатора со временем падает из-за отложения кокса (регенерация проводится каждые 3 ч).
4.3. ПРОИЗВОДСТВО ИЗОБУТИЛЕНА
Изобутилен используется при производстве бутилкаучука (сополимера с 2–3 % пропена), полиизобутилена.
Существуют различные методы получения изобутилена. В частности, один из них – дегидратация изобутанола:
(4.9)
Более выгодно получать изобутилен из бутан-бутеновой фракции газов крекинга. При этом из-за близости температур кипения смесь бутенов разделяют химическими методами.
115
Так, при обработке 60–65 % серной кислотой при температуре 35–40 °С изобутилен реагирует с Н2SО4 с образованием третбутилсерной кислоты:
(CH3)2C=CH2 +H2SO4→ (CH3)3COSO2OH, |
(4.10) |
и небольшого количества полимеров за счет протекания побочных реакций.
Гидролиз третбутилсерной кислоты дает третбутанол, который в присутствии серной кислоты дегидратируется в изобутилен:
(CH3)3COSO2OH +H2O→ (CH3)3COH +H2SO4→ (CH3)2C=CH2 + H2O (4.11)
Гидролиз и дегидратация проводятся в колонне-регенераторе, в которую пропускают водяной пар. Из верхней части колонны отбирают изобутилен, который отделяется от примесей и конденсируется.
Из нижней части колонны выходит серная кислота (45 %), которую регенерируют упариванием до 65 %. Выход изобутилена состав-
ляет 90–95 %.
Более совершенным методом выделения изобутилена из бутанбутеновой фракции является его прямая гидратация на катионите КУ-2 в третбутанол (температура 90–100 °С, давление 1–1,5 МПа), который на том же катализаторе при температуре 100–105 °С и давлении 0,34 МПа дегидратирует в изобутилен:
(CH3)2C=CH2 +H2O→ (CH3)3COH –H2O→ (CH3)2C=CH2 (4.12)
Изобутилен может быть выделен из бутан-бутеновой фракции и при помощи низших спиртов (метанола), образующих с изобутиленом эфиры (метилтретбутиловый эфир – МТБЭ). МТБЭ далее разлагается на изобутилен и метанол (катализатор – оксид алюминия, оксиды и сульфаты переходных металлов). Условия: температура 100–300 °С, давление 1 МПа. Для подавления побочных реакций разложение ведут в присутствии водяного пара:
116
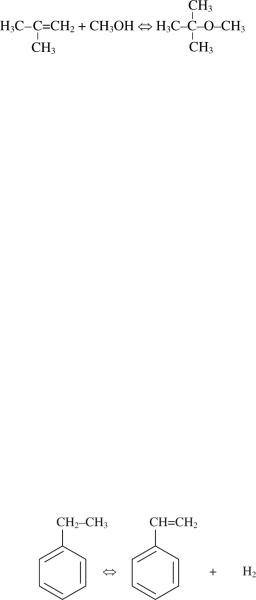
(МТБЭ) (4.13)
В нашей стране изобутилен получают дегидрированием изобутана на алюмохромовом катализаторе при температуре 550–580 °С по реакции:
(СН3)2СНСН3 → (СН3)2С=СН2 + Н2 |
(4.14) |
Процесс идет в псевдоожиженном слое катализатора. Выход изобутилена на изобутан составляет 38–42 %, селективность 80 %. Образующаяся в процессе изобутан-изобутиленовая фракция выделяется из контактного газа абсорбцией и ректификацией, а разделение изобутана и изобутилена происходит при помощи серной кислоты.
4.4. ПРОИЗВОДСТВО СТИРОЛА ДЕГИДРИРОВАНИЕМ АЛКИЛБЕНЗОЛОВ
Стирол и α-метилстирол являются дополнительными мономерами при производстве синтетических каучуков общего назначения. Но основное количество стирола идет на получение полистирола.
Основным промышленным методом производства стирола является дегидрирование этилбензола. Сырьем для производства α-метил- стирола служит изопропилбензол.
Дегидрирование этилбензола и изопропилбензола протекает по реакциям:
(4.15)
117
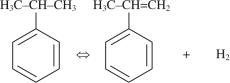
(4.16)
Реакции идут с увеличением объема и поглощением тепла. Следовательно, наиболее благоприятными для них являются повышенная температура и низкие парциальные давления. Для повышения глубины превращения сырья его разбавляют водяным паром.
Одновременно с основной реакцией протекают и побочные – распада и уплотнения. В результате образуются бензол и этилен (в случае этилбензола) и бензол, метилбензол и стирол (в случае изопропилбензола), а кроме того, идет образование этилена, пропилена, метана иэтана.
В процессе дегидрирования этилбензола и изопропилбензола в основном используются катализаторы на основе оксидов железа. В частности, отечественныйкатализаторК-22 содержит69–73 мас. % Fe2О3.
Подаваемый в систему водяной пар газифицирует углистые отложения на катализаторе, благодаря чему срок службы катализатора возрастает до 1,5–2 лет без регенерации.
Процесс ведут при температуре 560–580 °С. Аппаратурное оформление процесса дегидрирования этилбензола и изопропилбензола аналогично оформлению процесса дегидрирования бутенов. Чаще всего применяются реакторы адиабатического типа с использованием в качестве теплоносителя перегретого водяного пара.
Рассмотрим работу технологической схемы дегидрирования изопропилбензола (рис. 4.8).
Согласно схеме смесь свежего и возвратного изопропилбензола подается в смесительную камеру 4. Испарение идет в токе водяного пара (50 % от изопропилбензола) за счет тепла контактного газа, поступающего из перегревателя 3.
Испаренный и нагретый до 150 °С изопропилбензол из испарителя 4 поступает в перегреватель 3, где нагревается до 450 °С за счет тепла контактного газа из аппарата 2.
Перегретые пары из перегревателя 3 направляются в смесительную камеру контактного аппарата 2, где они смешиваются с водяным
118
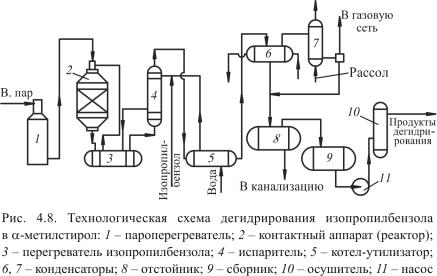
паром, имеющим температуру 675 °С (водяной пар перегревается в трубчатой печи 1).
Парогазовая смесь на входе в реакционную зону контактного аппарата 2 имеет температуру 590 °С, на выходе – 550 °С (реакция эндотермична).
Контактный газ охлаждается в перегревателе 3 и испарителе 4
идалее идет на доохлаждение в котел-утилизатор 5. Затем он поступает в конденсатор 6, где жидкие углеводороды частично конденсируются. Окончательная конденсация происходит в конденсаторе 7 рассолом.
Конденсаты из аппаратов 6 и 7 стекают в отстойник 8, откуда углеводородный слой через сборник 9 подается в осушитель 10 и далее на разделение.
Водный слой из отстойника 8 после дополнительного отстаивания сбрасывается в канализацию. Несконденсировавшиеся углеводородные газы направляются в газовую сеть.
Процесс дегидрирования этилбензола отличается от процесса дегидрирования изопропилбензола только температурным режимом
иналичием аппарата с мешалкой для добавления к стиролу ингибитора полимеризации – гидрохинона (температура 600–615 °С).
119
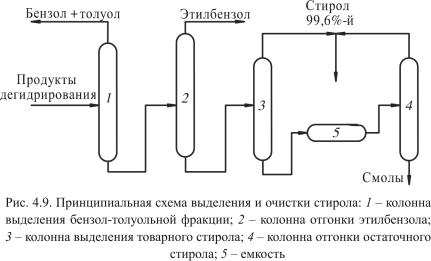
Особенностью стирола является его склонность к самопроизвольной полимеризации, что значительно затрудняет его выделение и очистку. Процесс выделения и очистки идет при невысоких температурах и низком давлении (0,004 МПа) в присутствии ингибитора.
Рассмотрим принципиальную технологическую схему выделения и очистки стирола (рис. 4.9).
Согласно схеме жидкие углеводороды с установки дегидрирования поступают в колонну 1 для удаления бензол-толуольной фракции. Остаток из колонны 1 идет в колонну 2, где отбирается этилбензол. Остаток из колонны 2, представляющий собой смесь стирола и высококипящих примесей, поступает в колонну 3 для отделения стирола. Из верхней части колонны 3 отбирается стирол с чистотой 99,6 %, из нижней части – смола. Смола, в свою очередь, идет в емкость 5 и пропускается через колонну 4 для отгонки остаточного стирола.
Выделение и очистка α-метилстирола проводятся по аналогичной технологии.