
Технологии органического и нефтехимического синтеза
..pdf
–разделение контактного газа второй стадии дегидрирования абсорбцией иректификацией с выделением бутен-бутадиеновой фракции;
–разделение бутен-бутадиеновой фракции на бутены и бутадиен. Смесь бутенов возвращается на вторую стадию дегидрирования, товарный бутадиен направляется на дальнейшую переработку.
Рассмотрим подробно каждую из стадий дегидрирования.
Дегидрирование н-бутана в н-бутены – первая стадия. На этой стадии применяется алюмохромовый катализатор (Cr2O3 на Аl2О3).
Вкачестве промоторов катализатора применяют оксиды калия,
цезия, магния и др. При этом содержание Сr2О3 доходит от 10 до 40 % от массы катализатора. Ядом для данного катализатора является вода.
Катализатор достаточно селективен, но протекает и ряд побочных реакций, в основном крекинг и изомеризация:
CH3CH2CH2CH3 → CH3CH=CH2 + CH4
P |
(крекинг) (4.2) |
|
CH2=CH2 + C2H6 |
(4.3)
Кроме того, идут реакции уплотнения с образованием кокса. Роль реакций изомеризации невелика, однако накапливающийся в системе 2-метилпропен (изобутилен) требуется удалять.
В процессе дегидрирования н-бутана применяют различные типы реакторов, что связано со способом подвода тепла. В частности, более широкое применение получил (в том числе и в нашей стране)
91
реактор с псевдоожиженным слоем катализатора. Этот реактор имеет ряд преимуществ:
–процесс протекает в изотермических условиях благодаря интенсивному перемешиванию катализатора:
–повышается скорость внутренней диффузии благодаря высокой степени измельчения катализатора;
–интенсифицируются процессы массо- и теплопередачи;
–упрощенное аппаратурное оформление;
–повышенная мощность реакторов (установок).
На установках дегидрирования, оборудованных реакторами псевдоожиженного слоя, дегидрирование и регенерацию катализатора проводят в отдельных аппаратах. В связи с тем, что тепла, образующегося при выжиге кокса, не хватает для нагрева катализатора до требуемой температуры, в регенераторе дополнительно сжигается топливо.
Реактор и регенератор представляют собой секционированные пустотелые аппараты, расположенные соосно один над другим или параллельно. Для секционирования применяются перфорированные провальные решетки (степень перфорации 20–30 %).
Одна из причин снижения активности катализатора – образование
в нем воды за счет его восстановления (сначала Сr+3 переходит в Сr+6,
азатем под действием водорода снова в Сr+3 с выделением трех моле-
кул воды на одну молекулу восстановленного Сr2О3). Выделившаяся вода является ядом для катализатора. Поэтому в регенераторе предусмотрен десорбер-восстановитель, куда подается топливный газ для
восстановления Сr2О3 и азот для десорбции паров воды и кислорода. Тем самым обеспечивается поступление в реактор уже восстановленного катализатора и не происходит отравления его водой.
Рассмотрим принципиальную технологическую схему дегидрирования н-бутана в псевдоожиженном слое катализатора с параллельным расположением реактора и регенератора (рис. 4.1).
Согласно схеме смесь свежей и циркулирующей бутановой фракции после осушки в осушителе 1 молекулярными ситами до содержания воды 0,01–0,001 % проходит через испаритель 2, перегреватель 3 и змеевики закалочного охлаждения реактора 5, после чего
92
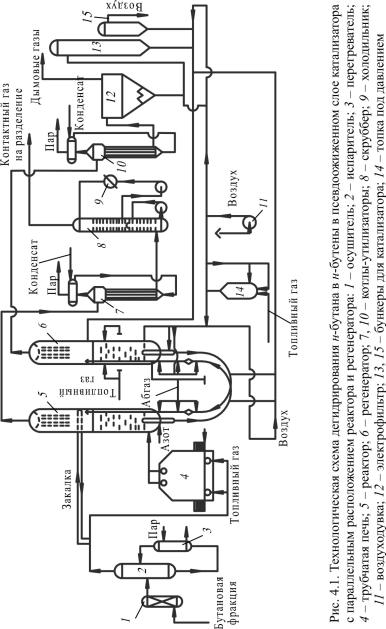
93
направляется в трубчатую печь 4, откуда газ с температурой 550 °С поступает под газораспределительную решетку реактора 5, создавая псевдоожиженный слой и контактируя с регенерированным катализатором.
Из реактора контактный газ поступает в котел-утилизатор 7, где охлаждается до 250 °С. В котле-утилизаторе генерируется водяной пар с давлением 0,6 МПа.
Из котла-утилизатора 7 контактный газ направляется в скруббер 8, где промывается водой и охлаждается до 70 °С. Окончательное охлаждение газа осуществляется в холодильнике 9.
Закоксованный катализатор из реактора 5 проходит десорбер
иидет в регенератор 6 для выжига кокса. Туда же подаются воздух
итопливный газ. Регенерированный катализатор возвращается в реактор 5, а газы регенерации проходят котел-утилизатор 10, электрофильтр 12 и далее уходят в атмосферу.
Запуск и разогрев системы осуществляется при помощи воздуходувки 11 и топки под давлением 14. Из бункера 13 катализатор транспортируется воздухом в регенератор 6 по системе труб,
ипри помощи пневмоподъемника налаживается циркуляция между реактором и регенератором. После этого катализатор нагревается сначала горячим воздухом, нагнетаемым в регенератор 6 воздуходувкой 11 через топку 14, а затем топливным газом, подаваемым в регенератор.
Впроцессе работы пополнение катализатора в систему идет путем добавки его в регенератор 6 из бункера 15 сжатым воздухом, нагнетаемым воздуходувкой 11.
Транспорт катализатора между реактором и регенератором осуществляется двумя пневмоподъемниками в форме лиры, в которых катализатор аэрируется в нескольких точках по высоте напорного
иподъемного стояков. Такое устройство обеспечивает высокую концентрацию катализатора в пневмоподъемнике при линейной скорости транспортирующего агента 2–3 м/с.
Дегидрирование н-бутенов в бутадиен – вторая стадия. Вто-
рая стадия дегидрирования бутенов проводится при высокой темпе-
94
ратуре и низких парциальных давлениях углеводородного сырья, так как при атмосферном давлении низок выход бутадиена-1,3. Снижение парциального давления достигается за счет разбавления бутенов водяным паром (но не N2, СН4, СО2; из-за увеличения объема контактного газа, подлежащего разделению).
В качестве катализатора на второй стадии дегидрирования применяют катализаторы, содержащие оксиды Fe, Cu, Mg, Zn и другие, а также хромкальцийникельфосфатный катализатор.
Основные побочные реакции: полимеризация бутенов и бутадиена и крекинг бутенов и бутадиена.
Вприсутствии водяного пара идут реакции взаимодействия кокса, откладывающегося на катализаторе, с водой с образованием СО и Н2.
Всвязи с малым временем контакта бутенов и катализатора вторая стадия дегидрирования осуществляется в реакторах со стационарным слоем катализатора. Наиболее распространен за рубежом
ив нашей стране процесс в реакторах адиабатического типа с использованием водяного пара в качестве теплоносителя, т.е. в процессе дегидрирования н-бутенов водяной пар играет роль разбавителя, регенерирующего агента и теплоносителя.
Впроцессе дегидрирования н-бутенов нашли применение два
типа катализаторов: железосодержащие (содержащие Fe2О3, K2СО3, Сr2О3 или Сr2О3, Fе2О3, ZnO, SiO2) и хромкальцийникельфосфатный (Са8Ni(РО4)6, стабилизированный Сr2О3).
Железосодержащие катализаторы характеризуются малым выходом бутадиена за проход (17–19 %), однако могут длительное время работать без регенерации.
Хромкальцийникельфосфатные катализаторы обеспечивают выход бутадиена в 2 раза выше, но имеют короткие циклы дегидрирования из-за быстрого закоксовывания, так как катализатор слабо регенерируется водяным паром.
Рассмотрим принципиальную технологическую схему второй стадии дегидрирования н-бутенов (рис. 4.2).
95
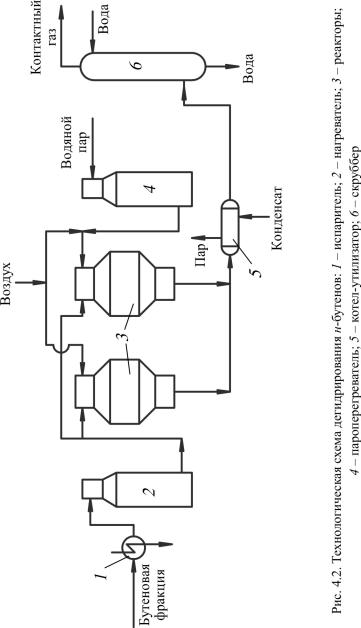
96
Согласно схеме бутадиеновая фракция в смеси с рециркулирующими бутенами в испарителе 1 испаряется и нагревается до 80 °С, проходит через нагреватель 2, где подогревается до 550 °С и поступает
вверхнюю часть реактора 3. Туда же подается водяной пар, перегретый
втрубчатом пароперегревателе 4 до 700–760 °С. В итоге температура
на входе в реактор 3 поддерживается на уровне 650 °С. Пары бутенов и водяной пар смешиваются в верхней части реактора в специальных смесителях инжекционного или диафрагменно-дискового типа.
Реактор представляет собой пустотелый аппарат, в нижней части которого имеется решетка, на которой находится катализатор.
Вторая стадия дегидрирования является весьма энергоемкой: расход топлива в 5 раз выше, чем на первой стадии, из-за необходимости перегрева больших количеств водяного пара.
4.1.1.2. Одностадийное дегидрирование н-бутана
При одностадийном дегидрировании н-бутана упрощается схема производства (исключается первая стадия дегидрирования и разделение продуктов данной стадии). Выход бутадиена при одностадийном дегидрировании составляет 50 % на н-бутан.
Процесс одностадийного дегидрирования основан на том, что при повышенных температурах и давлении равновесие реакции дегидрирования н-бутана сдвинуто в сторону образования бутадиена-1,3:
С4Н14 С4Н8 + Н2 С4Н6 + 2Н2 |
(4.4) |
Процесс одностадийного дегидрирования идет на алюмохромовом катализаторе. При этом наряду с бутадиеном-1,3 образуется значительное количество бутенов, которые вновь возвращаются в процесс.
Поскольку на дегидрирование поступает смесь н-бутана с н-буте- нами, для процесса существенно, чтобы количество н-бутенов в контактном газе после реактора было не меньше их содержания в исходном газе, иначе будут дегидрироваться только н-бутены, а не будет обеспечена одностадийность процесса.
97
Процесс одностадийного дегидрирования идет при температуре
610–630 °С и давлении 0,015–0,02 МПа.
Процесс проводят в реакторах регенеративного типа. В связи с тем, что применяется алюмохромовый катализатор, разбавление сырья водяным паром исключается и разряжение создается вакуум-компрес- сорами.
Регенеративный тип реакторов обусловливает то, что циклы дегидрирования и регенерации катализатора чередуются в одном и том же реакторе. Выделяющееся при регенерации тепло аккумулируется катализатором и используется при дегидрировании. Однако этого тепла не хватает, и для его компенсации в реактор подводится тепло за счет сжигания топлива и подачи на регенерацию горячего кислородсодержащего газа.
Для улучшения теплообмена между газом и катализатором последний смешивается с инертным теплоносителем, представляющим собой плавленый Al2О3, при массовом соотношении 1 : 3.
Катализатор для одностадийного дегидрирования должен обладать высокой активностью и повышенной прочностью, стабильностью и высокой регенерационной характеристикой. Это связано с тем, что во время чередующихся циклов дегидрирования и регенерации катализатора значительно меняются условия, а циклы регенерации очень короткие.
Рассмотрим принципиальную технологическую схему одностадийного дегидрирования н-бутана (рис. 4.3).
Процесс дегидрирования идет в нескольких группах реакторов (3–8 реакторов в каждой группе). Согласно схеме сырье – бутанбутеновая фракция, содержащая 25–35 % н-бутенов – перегревается в печи 1 до 600–620 °С и поступает в часть реакторов 2, где контактирует с катализатором. Температура процесса колеблется в пределах 590–630 °С в конце и начале цикла дегидрирования. Разряжение создается при помощи двух вакуум-компрессоров.
Контактный газ из реактора 2 поступает на охлаждение и далее идет на разделение. После окончания цикла дегидрирования поток сырья переключается на следующую группу реакторов, а реакторы,
98
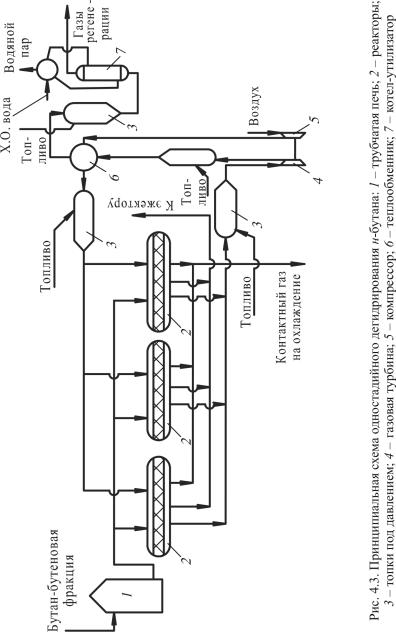
99
бывшие в работе, продуваются для удаления углеводородных паров. После продувки реакторы переключаются на регенерацию топочными газами, содержащими небольшое количество кислорода. Затем идет эвакуация продуктов сгорания пароструйным эжектором, после чего в реакторы вновь начинает поступать поток сырья.
Воздух для регенерации поступает на прием компрессора 5 (давление 0,6 МПа), нагревается в теплообменнике 6 до температуры 520–540 °С, в топке 3 до температуры 630 °С и далее направляется в реактор 2.
Газы регенерации, выходящие из реактора 2, дополнительно нагреваются в топке до температуры, отвечающей рациональному режиму работы газовой турбины 4, из которой охлажденные газы за счет совершения работы с температурой 450 °С поступают в топку 3, нагреваются и далее отдают часть тепла воздуху в теплообменнике 6. После дополнительного подогрева газов регенерации
вследующей топке 3, они используются для генерации водяного пара в котле-утилизаторе 7.
Такая схема позволяет работать без потребления водяного пара и электроэнергии со стороны, но требует повышенного давления
вреакторе в процессе регенерации.
Имеются схемы с пятью, шестью, семью и восьмью реакторами в группе. Переключение реакторов с режима на режим происходит автоматически.
Реакторы представляют собой горизонтальные пустотелые аппараты из стали, футерованные изнутри керамической плиткой. Смесь катализатора и теплоносителя (алунда) насыпается на решетку невысоким слоем. Решетка также выполнена из керамики во избежание коррозии, вызванной восстановительно-окислительной средой при высоких температурах.
Основные достоинства одностадийного процесса:
–более простая схема;
–снижение расходных коэффициентов по сырью;
–уменьшение энергетических затрат.
100