
Технологии органического и нефтехимического синтеза
..pdfТретбутилгидропероксид и дитретбутилпероксид находят применение в промышленности в качестве инициаторов радикальной полимеризации и вулканизации полиолефиновых каучуков.
6.3. ЖИДКОФАЗНОЕ ОКИСЛЕНИЕ НАСЫЩЕННЫХ УГЛЕВОДОРОДОВ
Большинство промышленных процессов получения кислородсодержащих продуктов (спиртов, кислот, гидропероксидов, фенола, ацетона и др.) проводят в жидкой фазе. При этом в ряде процессов вместо растворимых солевых катализаторов для инициирования реакции окисления к окисляющемуся углеводороду добавляют продукты окисления (оксидат), полученные в самом процессе. Содержащиеся в оксидате альдегиды, кетоны, спирты и другие соединения под воздействием кислорода значительно легче, чем исходный углеводород, образуют свободные радикалы, а это, в свою очередь, существенно повышает скорость зарождения цепи, снижает период индукции. Такое инициирование цепи используется и в процессе жидкофазного окисления н-бутана и легких фракций прямогонного бензина.
6.3.1. Окисление насыщенных углеводородов (н-бутана, фракции С5–С8 прямогонного бензина)
внизкомолекулярные кислоты
Впоследние годы в мире наблюдается рост производства низкомолекулярных кислот (особенно уксусной). Последнюю, в частности, получают различными методами:
– жидкофазным окислением н-бутана и н-парафинов С5–С8;
– жидкофазным окислением ацетальдегида;
– жидкофазным карбонилированием метанола;
– газофазным окислением этанола и ферментивными процессами. Более 50 % уксусной кислоты в мире получают жидкофазным
окислением н-бутана и н-парафинов С5–С8.
151
6.3.1.1. Окисление н-бутана в уксусную кислоту
Процесс жидкофазного окисления н-бутана ведут в растворе уксусной кислоты и продуктов реакции, возвращаемых в реактор вместе с непрореагировавшим бутаном.
Сырьем для получения уксусной кислоты является выделяемый из бутан-бутеновой фракции н-бутан (чистота 96 %).
В нем ограничивается содержание: пропана (не более 0,5 %), изобутана (не более 2 %), углеводородов С5 и выше (не более 1 %), сернистых соединений (не более 0,005 %), полное отсутствие 2-метил- пропена.
Примесь изобутана способствует увеличению выхода ацетона и метилацетата. При наличии непредельных снижается выход уксусной кислоты за счет образования гликольдиацетатов и возрастания количества продуктов полного окисления.
Процесс окисления идет при температуре 140–170 °С и давлении 5,1 МПа, массовом соотношении свежий н-бутан: возвратный н-бутан: воздух = (1–1,5) : 2 : (10–12) и подаче с возвратным н-бутаном продуктов окисления в количестве 10 % от суммарного количества н-бутана.
Рассмотрим технологическую схему процесса (рис. 6.1). Согласно схеме свежий жидкий н-бутан подается в смеситель 1,
куда поступает возвратный н-бутан (рециркулят) из емкости 11
икислый н-бутан из емкости 19. Смесь продуктов, пройдя теплообменник 2, где она нагревается до температуры 140–150 °С, поступает в нижнюю часть реактора окисления 5. Свежий воздух и кислородсодержащий газ из скруббера 20 смешиваются в аппарате 3, смесь нагревается в подогревателе 4 и тремя потоками подается в реактор окисления 5 (колонного типа). В реактор вмонтированы змеевики для съема тепла и распределительное устройство для воздуха.
Реакция окисления сопровождается выделением большого количества тепла (до 20 900 кДж на 1 кг н-бутана). Съем тепла осуществляется перегретой водой, циркулирующей по замкнутому циклу: сборник 9, насос 7, змеевики реактора окисления, холодильник 6
иснова сборник.
152
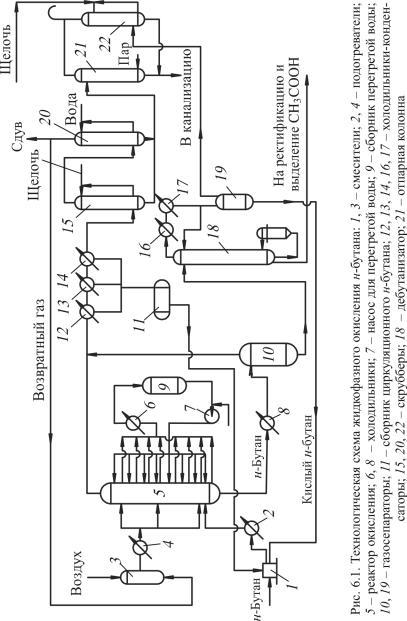
153
Отходящая из верхней части реактора 5 парогазовая смесь направляется на конденсацию в систему водяных и рассольных кон- денсаторов-холодильников 12, 13, 14, откуда конденсат самотеком сливается в емкость 11. Смесь паров и газов, несконденсировавшихся в конденсаторе 14, поступает на нейтрализацию кислых продуктов в скруббер 15, орошаемый 2–5%-м раствором щелочи, а затем на промывку водой в скруббер 20. Промытая паровоздушная смесь частично идет на смешение со свежим воздухом, частично на отдувку. Промывная жидкость из скрубберов 15 и 20 поступает в отпарную колонну 21, где отпариваются органические примеси, сбрасываемые на факел; вода идет в канализацию.
Оксидат, содержащий уксусную кислоту (43 %), МЭК (10 %), этилацетат (8–9 %) и другие продукты, из нижней части реактора 5 через холодильник 8 поступает в сепаратор 10. Выделившийся там газ присоединяется к парогазовой смеси, отходящей из верхней части реактора 5. Жидкость из сепаратора 10 после снижения давления до 0,2 МПа поступает в дебутанизатор 18, где отгоняется н-бутан, растворенный в продуктах окисления. Часть н-бутана после конденсации паров возвращается на орошение в колонну 18, остальное количество (кислый н-бутан) через сепаратор 19 подается в смеситель 1. Несконденсировавшиеся газы из сепаратора 19 нейтрализуются щелочью в скруббере 22, после чего сбрасываются на факел.
Кубовая жидкость из колонны 18 направляется на ректификацию в систему колонн, где происходит выделение концентрированной (99–100 %) и технической (85 %) уксусной кислоты, муравьиной кислоты (86,5 %) и двух фракций – ацетоно-метилацетатной (23 % ацетона и 68 % метилацетата, температура выкипания 56 °С) и мети- лэтилкетон-этилацетатной (МЭК 45,8 %, этилацетат 38,3 %, температура выкипания 57–88 °С).
Из 1 т н-бутана получается 1,6 т полезных кислородсодержащих продуктов, в том числе 872 кг уксусной кислоты и 190 кг МЭКа.
Кпреимуществам процесса относятся: одностадийность, непрерывность и дешевизна сырья и окислителя.
Кнедостаткам относятся: высокая коррозионность среды и образование побочных продуктов.
154
6.3.1.2.Окисление фракции С5–С8 прямогонного бензина
внизкомолекулярные кислоты
Низкомолекулярные кислоты образуются в достаточно больших количествах только при окислении насыщенных углеводородов не выше С8. При повышении молекулярной массы углеводорода в основном образуются кислоты с большей молекулярной массой, чем муравьиная, уксусная, пропионовая и янтарная (С1–С4).
В используемом сырье (фракция бензина С5–С8) нормируется сера (не более 0,06 %) и содержание углеводородов С5–С8 (не менее
78,5–85,0 %).
Процесс проводится при температуре 160–195 °С и давлении 5,1 МПа в реакторе из нержавеющей стали.
В качестве основных продуктов получаются: уксусная (80–81 %), муравьиная (12–15 %), пропионовая (5–8 %), янтарная (3–10 %) кислоты и многочисленные кислородсодержащие примеси. В связи с этим выделение целевых продуктов – низкомолекулярных кислот – представляет весьма сложную задачу. Это делают путем выделения нейтральных кислородсодержащих продуктов в виде азеотропа с водой. Отгоняемые затем нейтральные кислородсодержащие соединения возвращаются на окисление.
Водный раствор кислот содержит в своем составе в основном уксусную (47,3 %), а также муравьиную и пропионовую кислоты.
После азеотропной перегонки с изопропиловым спиртом и последующей ректификации получают смесь кислот С1–С3, идущую на разделение. Муравьиная кислота выделяется азеотропной перегонкой с толуолом, уксусная и пропионовая – ректификацией под вакуумом.
6.3.2. Окисление насыщенных углеводородов С10–С20 в спирты
Промышленный процесс окисления насыщенных углеводородов С10–С20 в высшие спирты впервые был разработан и реализован в 1957–58 гг. в нашей стране.
155
Высшие жирные спирты получают в промышленности следующими методами:
1)гидрирование кашалотового жира;
2)гидрирование СЖК и их метиловых и бутиловых эфиров;
3)выделение из вторых неомыляемых производства СЖК;
4)получение спиртов С6–С20 с четным числом углеродных атомов методом олигомеризации этилена в присутствии триэтилалюминия и последующего окисления;
5)прямое окисление насыщенных углеводородов С10–С20 молекулярным кислородом.
Методами 1, 2 и 4 получают первичные спирты, методом 3 – смесь первичных и вторичных спиртов, методом 5 – в основном вторичные спирты.
Высшие жирные спирты применяются для производства ПАВ, моющих средств, присадок к маслам и СОЖам, в текстильной, кожевенной и бумажной промышленности.
А.Н. Башкировым был разработан метод направленного жидко-
фазного окисления жидких насыщенных углеводородов С10–С20 с образованием спиртов. Для защиты целевого продукта от дальнейших окислительных превращений было предложено связывать гидроксильные группы образующихся спиртов борной кислотой:
C12H26 + O2 → CH3(CH2)9CHCH| |
3 + C12H26 → CH3(CH2)9CHCH| |
3 (6.7) |
OOH |
OH |
|
3C12H25OH + H3BO3 → (C12H25O)3B + 3H2O |
(6.8) |
Предотвращение деструкции парафинов в процессе окисления достигается за счет использования газа-окислителя с пониженной концентрацией кислорода.
Окисление производится при температуре 175 °С в присутствии 5%-й борной кислоты азото-кислородной смесью с содержанием кислорода 3–4,5 об. %. Выход спиртов составляет 50–60 %. Данным методом получают вторичные спирты.
156
Сырьем для получения высших жирных спиртов по методу Башкирова служат фракции парафинов нормального строения от 240–270 °С до 330–370 °С, выделенные из фракций дизельного топлива (карбамидная депарафинизация или адсорбция на цеолитах).
Содержание в сырье ароматических углеводородов (особенно нафталина и бутилнафталинов), тормозящих оксиление, не должно превышать 0,5 %. Для приготовления азотокислородной смеси используют отходящий газ процесса, содержащий в основном азот, к которому после очистки от конденсирующихся компонентов добавляют воздух.
Технологический процесс включает следующие основные стадии:
–окисление жидких парафинов в присутствии Н3ВО3;
–отгонка отборнокислых эфиров неокислившихся углеводородов;
–гидролиз борнокислых эфиров;
–омыление и дистилляция вторичных спиртов;
–омыление возвратных углеводородов и отделение от них раствора мыл;
–регенерация борной кислоты.
Рассмотрим технологическую схему процесса (рис. 6.2). Согласно схеме дистиллированный парафин и возвратные углево-
дороды в отношении 1 : 2 нагреваются в теплообменнике 1 до 160 °С и подаются в окислительную колонну 3. Окисление идет в присутствии Н3ВО3, которая поступает из монжуса 2. Степень превращения парафина в кислородсодержащие продукты находится на уровне 45 %.
Отработанный газ из колонны 3 поступает в конденсатор 4, где конденсируются пары легкокипящих продуктов, возвращаемые в колонну 3, охлаждается в холодильнике 5, проходит щелочную и водную промывку в скрубберах 6 и 8, ресивер 7 и после обогащения кислородом воздуха подается в окислительную колонну 3.
Продукты из нижней части колонны 3 подогреваются в подогревателе 10 до температуры не выше 260 °С и поступают в колонну 11 на ректификацию, где при давлении 0,0026 МПа происходит отгонка непрореагировавших углеводородов и кислородсодержащих соединений от борнокислых эфиров. Пары отогнанных продуктов конденсируются в поверхностномконденсаторе9, иконденсатнепрерывноподается
157
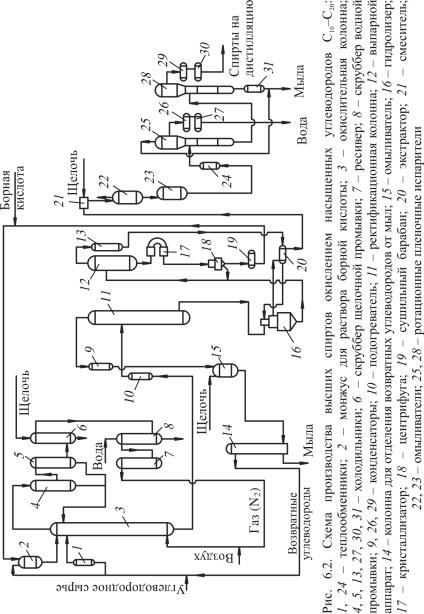
158
вомыливатель 15, где при температуре не выше 100 °С происходит омыливание кислородсодержащих соединений 10–12%-м раствором щелочи. Омыленный продукт из омыливателя 15 подается в колонну 14 для отделения мыл от углеводородов (при температуре 95 °С), возвращаемых наокисление. Мылавыводятся из системы.
Борнокислые эфиры из нижней части колонны 11 через вакуумприемник, где они охлаждаются до 100 °С, поступают на разложение
вгидролизер 16, куда одновременно подается слабый раствор борной кислоты (водный экстракт из экстрактора 20).
При температуре 95–98 °С и тщательном перемешивании в гидролизере идет разложение борнокислых эфиров на спирты и борную кислоту. Раствор борной кислоты из гидролизера 16 подается в выпарной аппарат 12, где идет упаривание раствора борной кислоты
до концентрации 12–18 %. Концентрированный раствор Н3ВО3 поступает в кристаллизатор 17 и далее в центрифугу 18 для выделения
кристаллов борной кислоты. Маточный раствор присоединяется к раствору Н3ВО3 из гидролизера 16, направляемому на упарку. Кристаллическая Н3ВО3 подсушивается в сушильном барабане 19 и возвращается в процесс.
Сырые жирные спирты из гидролизера 16 промываются в горизонтальном экстракторе 20 конденсатом сокового пара выпарного аппарата 12 и направляются через смеситель 21 в омыливатели 22 и 23, в которых идет омыливание содержащихся в них жирных кислот и эфиров.
После омыливания спирты вместе с мылами через теплообменник 24 направляются в ротационные испарители 25 и 28. В первом из них отгоняется вода, во втором – спирты от мыл при температуре 300 °С и давлении 0,012 МПа. Пары спиртов отводятся через конденсатор 29, холодильник 30 на дистилляцию для выделения узких фракций.
Верхний погон из испарителя 25 и кубовый остаток из испарителя 28 выводятся из системы. Эта смесь мыл и нейтральных веществ в соотношении 1 : 1 может применяться в качестве флотореагента фосфоритных руд.
159
В процессе получают спирты С12–С20 (основное количество составляют спирты С14–С18 – 70–80 %). Содержание первичных спир-
тов – 17–25 %, вторичных – 75–83 %.
Достоинство процесса – образование спиртов непосредственно из парафина на первой стадии процесса. Однако схема многостадийна, а получаемые спирты содержат много примесей (диолы, кетоноспирты и др.). Высок расход парафина и реагентов.
Во ВНИИ ПАВ разработан более усовершенствованный процесс: в нем используется парафин более узкого фракционного состава (С13– С15, С13–С17, С14–С16), вводится стадия гидроочистки возвратных углеводородов, спиртов и ректификация последних. Это позволяет повысить качественные характеристики получаемых в процессе спиртов и технико-экономические показатели процесса.