
Технологии органического и нефтехимического синтеза
..pdfдвухкамерных печей с многопоточными змеевиками позволяет существенно увеличить производительность печей пиролиза. Каждая секция змеевика (1 поток) состоит из нескольких труб (4–12 шт.), соединенных калачами. Температурные компенсации труб при этом устраняются за счет закрепления одного конца труб и свободного перемещения другого. Для обогрева печей используются настенные беспламенные или подовые факельные горелки. Реакционный змеевик печи выполняют из жаропрочной нержавеющей стали (например, Х25Н35 и др.). Длина труб составляет 6–16 м, диаметр – 76–150 мм.
Для повышения значения коэффициента теплоотдачи и уменьшения коксовых отложений на стенках труб массовая скорость сырьевого потока должна лежать в пределах 100–120 кг/(м2 с). Ограничение вводится только по скорости паров на выходе из печи (не свыше 300 м/с) с целью исключения абразивного износа аппаратуры и трубопроводов.
Перепад давления в радиантном змеевике не должен превышать 0,1–0,15 МПа. С целью снижения потери напора применяют трубы переменного диаметра – с меньшего на больший, так как по мере прохождения сырья по трубам и его расщепления увеличивается объем паров и потеря напора максимальна.
Удаление кокса со стенок труб змеевика осуществляют через каждые 40–80 сут работы паровоздушным методом. Для снижения коксообразования применяют ингибиторы (например, карбонат калия).
На выход и состав продуктов пиролиза большое влияние оказывает распределение температур по длине радиантного змеевика, регулирование которого можно проводить с помощью горелок. Температурные кривые могут быть выпуклыми, прямолинейными и вогнутыми. При вогнутой кривой меньше выход этилена, но больше пропилена и углеводородов С4, так как реакционная смесь мало времени находится в зоне высоких температур. При выпуклой кривой, наоборот, выше выход этилена (рис. 2.3).
51
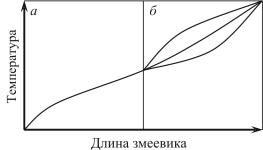
Рис. 2.3. Температурныйпрофильпечного змеевика: а – конвекционная камера; б– радиантная камера
Существует понятие фактора профиля, который характеризует жесткость процесса:
Фактор профиля =
= ∆t последней трети змеевика/∆t всей зоны реакции.
Чем меньше фактор профиля, тем жестче режим, а значит, выше выход этилена.
Селективность процесса пиролиза газообразного сырья определяется отношением Σ(Н2 + СН4)/С2Н4. Чем меньше отношение, тем выше селективность процесса.
Для жидкого сырья селективность определяется отношениями:
С3Н6/С2Н4 или С4Н6/С2Н4.
Селективность процесса пиролиза зависит, в первую очередь, от характеристик исходного сырья и жесткости процесса.
2.3.4. Устройство закалочно-испарительного аппарата
Закалочно-испарительный аппарат (ЗИА) представляет собой трубчатый теплообменник. Продукты реакции поступают в трубное пространство, а в межтрубное пространство – химически очищенная вода. Это связано с тем, что при прохождении продуктов пиролиза на стенках ЗИА накапливается кокс, который удаляется из трубок
52
специальными шарошками под высоким давлением. Кроме того, в трубках можно создать более высокие линейные скорости, а значит, более высокие коэффициенты теплопередачи и уменьшить время закалки. В свою очередь, это способствует меньшему отложению кокса, а значит, увеличивает межремонтный пробег.
Во избежание полного закоксовывания трубок ЗИА температура на выходе из ЗИА должна быть выше температуры конденсации самых тяжелых фракций смолы. Время пребывания паров в ЗИА должно быть меньше 0,1 с.
Дозакалка продуктов пиролиза (см. рис. 2.2) идет в узле впрыска тяжелой смолы 6. Благодаря большим линейным скоростям вся конденсирующаяся тяжелая смола выносится в колонну первичного фракционирования 7.
2.4. НАЗНАЧЕНИЕ И ВЛИЯНИЕ ОСНОВНЫХ ТЕХНОЛОГИЧЕСКИХ ПАРАМЕТРОВ ПРОЦЕССА ПИРОЛИЗА (ТЕМПЕРАТУРЫ, ДАВЛЕНИЯ, ВРЕМЕНИ, СОСТАВА СЫРЬЯ, ВОДЯНОГО ПАРА)
Глубина процесса пиролиза определяется тремя факторами: температурой, временем контакта и парциальным давлением углеводородов. Для процесса наиболее благоприятны высокая температура, малое время контакта и малое парциальное давление углеводородов.
Обычно температура на входе сырьевой смеси в реактор (реакционную зону) составляет 500–600–650 °С, так как при этих температурах не происходит существенного разложения сырьевой смеси в конвекционной секции печи. Для минимального образования побочных продуктов скорость подогрева сырья в реакционной зоне должна возрастать от входа к выходу одновременно с повышением температуры сырьевой смеси.
Этого достигают, регулируя подвод тепла по длине реакционного змеевика.
53
При повышении давления в реакционной зоне увеличивается содержание в продуктах реакции н-парафинов и ароматических углеводородов, а содержание олефинов уменьшается. Обычно давление на выходе из реакционного змеевика печи составляет 0,03–0,12 МПа (лучше меньше).
Для снижения парциального давления углеводородов сырье разбавляют водяным паром. При этом с повышением степени разбавления сырья водяным паром растет выход этилена. Кроме того, водяной пар снижает коксообразование и повышает скорость (линейную) движения газосырьевой смеси в печи. Однако чрезмерное разбавление сырья водяным паром имеет и отрицательные последствия: повышается расход тепла, расход охлаждающей воды, количество загрязненных сточных вод.
В современные трубчатые печи подается до 0,6 кг водяного пара на 1 кг бензина, для тяжелых видов сырья количество водяного пара может возрастать до 1 кг и более на 1 кг сырья, для газообразного сырья – снижаться до 0,2–0,3 кг на 1 кг сырья.
На состав продуктов пиролиза существенное влияние оказывает углеводородный состав исходного сырья.
Изопарафины за счет наличия большого числа метильных групп дают мало этилена, но при этом образуется много бутадиена.
Нафтены (например, циклогексан) дают мало пропилена и метана, меньше этилена, но много бутадиена.
Ароматические углеводороды обладают очень высокой термической стабильностью и почти не образуют этилена. Моноциклическая ароматика является балластом и характеризуется большим выходом кокса, однако не тормозит пиролиза парафинов. Полициклическая ароматика, наоборот, тормозит пиролиз парафинов с образованием газообразных олефинов.
н-Парафины – наиболее благоприятное сырье для пиролиза. Самый высокий выход этилена наблюдается при пиролизе этана. Из пропана и бутана образуется меньше этилена, но возрастает выход пропилена и метана.
54
При повышении молекулярной массы н-парафинов их термическая стабильность снижается, и выход этилена вновь возрастает.
2.5. РАЗДЕЛЕНИЕ ПРОДУКТОВ ПИРОЛИЗА. ПОЛУЧЕНИЕ ЭТИЛЕНА, ПРОПИЛЕНА И ДРУГИХ ПРОДУКТОВ
При пиролизе углеводородного сырья наряду с газообразными образуются и жидкие продукты (смолы пиролиза). Причем выход смолы пиролиза существенно зависит от углеводородного состава исходного сырья. В случае газообразного сырья выход смолы пиролиза находится на уровне 2–8 мас. %. При использовании более тяжелых видов сырья выход смол возрастает и может достигать 40 мас. %. В связи с этим смолы пиролиза не рассматривают как отходы производства, а стараются квалифицированно переработать. В частности, при переработке из них получают бензол, толуол, ксилолы, циклопентадиен, циклопентен, изопрен, стирол, нафталин, нефтеполимерные смолы, сырье для производства техуглерода, растворители, специальные масла.
Так, легкая смола пиролиза (температура выкипания до 200 °С) содержит нафталин и его гомологи, тетралин, конденсированные ароматические углеводороды.
Смолу пиролиза первоначально разделяют на легкую и тяжелую, каждая из которых перерабатывается отдельно. Как правило, легкую смолу делят на фракции: С5 (из нее выделяют изопрен, циклопентадиен); 70–130 °С (ее гидрируют и выделяют из нее бензол); 130–190 °С (после ее гидрирования из нее выделяют ксилолы и сольвент).
Из тяжелой смолы выделяют, в первую очередь, нафталин и полимерные смолы. Переработка тяжелой смолы возможна и по другим направлениям.
55
2.5.1. Разделение газообразных продуктов
После колонны первичного фракционирования и водной промывки газ пиролиза поступает на разделение. Этилен из газообразных продуктов выделяют при низких температурах и высоких давлениях. Перед фракционированием газ предварительно компримируют. После компримирования проводят осушку газа. Она необходима, так как газообразные углеводороды при низких температурах и высоких давлениях образуют с водой гидраты, которые могут отлагаться на стенках трубопроводов и аппаратуры, вызывая их забивание и нарушение работы газофракционирующей установки. При этом осушку газа проводят после компримирования, так как при повышенном давлении
ипониженной температуре часть водяных паров конденсируется
ина осушку поступает газ с меньшим содержанием влаги.
Газ, как правило, компримируют до 2–4,5 МПа в 4–5-ступен- чатых трубокомпрессорах. Температура газа между ступенями компрессии не должна превышать 100–110 °С, чтобы предотвратить полимеризацию олефиновых, диеновых и ацетиленовых углеводородов.
После каждой ступени компримирования газ подвергают охлаждению и сепарации для отделения сконденсированных углеводородов и воды. Промежуточное охлаждение осуществляют водой (27–30 °С) или пропиленом (от минус 15 до минус 16 °С). Ниже минус 15 °С газ не охлаждают, так как могут образоваться гидраты.
Для надежной работы газофракционирующей установки точка росы газа не должна превышать минус 65 – минус 70 °С. На современных установках для осушки газа применяют твердые адсорбенты (цеолиты). Осушку проводят в периодически работающих колоннах с циклом работы 24–36 ч. На осушку подают охлажденный газ (температура 5–15 °С), так как при повышении температуры осушки влагоемкость адсорбента снижается. Во избежание забивания пор адсорбента и его дезактивации перед осушкой газ освобождают от тяжелых углеводородов и влаги.
56
Компримирование и межступенчатая сепарация конденсата могут осуществляться по разным схемам:
–все конденсаты из межступенчатых сепараторов подаются
водин общий сепаратор, а затем в отпарную колонну;
–конденсат из каждого сепаратора подают в последующий, что способствует более полной конденсации тяжелых углеводородов. Затем конденсат направляют в колонну отгона легких углеводородов, а газ подвергают дополнительному фракционированию;
–дросселирование и подача конденсата в сепаратор предыдущей ступени. В этом случае от конденсата полнее отделятся легкие углеводороды.
Рассмотрим одну из разновидностей схем компримирования
иосушки газа пиролиза (рис. 2.4).
Согласно схеме газ пиролиза через холодильник 1 поступает
всепаратор 2, где отделяется тяжелый конденсат. Далее газ проходит последовательно I–V ступени компрессоров. После каждой ступени газ охлаждается в холодильниках 3 и сепарируется в сепараторах 4–8. Конденсат из сепаратора 2 насосом 13 подается в водоотделитель 14, а газ идет на I ступень компрессии. Компримированный газ охлаждается в межступенчатых холодильниках 3 и поступает в сепаратор 4, куда поступает и конденсат из сепаратора 5. Конденсат из сепаратора 4 поступает в водоотделитель 14, откуда углеводородный конденсат
иводный слой раздельно подаются в колонну водной промывки установки пиролиза. Т.е. в колонну водной промывки направляются конденсаты I–III ступеней компрессии.
Далее газ проходит II и III ступени компрессии, холодильники, сепараторы 5 и 6 соответственно и идет на щелочную очистку от диоксида углерода и сероводорода, после чего возвращается на IV ступень компрессии и по той же схеме проходит соответствующие холодильники и сепараторы.
Конденсат из сепаратора 8 дросселируется, охлаждается и поступает в сепаратор 9. Выделившийся газ возвращается на прием V ступени компрессии, аконденсат вместе с конденсатом изсепаратора 7
57
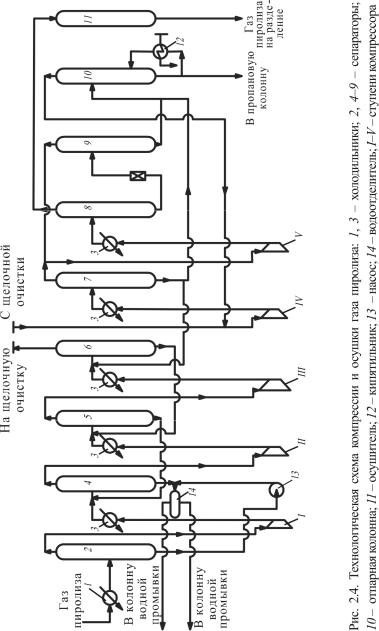
58
направляется в отпарную колонну 10 для выделения легких фракций (легче С3). Пары из колонны 10 направляются на IV ступень компрессии, а остаток – в пропановую колонну газофракционирующей установки.
Газ пиролиза из сепаратора 8 с температурой 15 °С поступает в осушитель 11, которых может быть два или три, работающих поочередно в режиме осушки и регенерации. Регенерация проходит горячим метаном при температуре 220 °С.
2.5.2. Фракционирование газа пиролиза
Для разделения газа пиролиза применяют методы низкотемпературной ректификации с применением аммиачного, метанового, этиленового или пропанового циклов или абсорбционно-ректифика- ционный. При последнем методе все компоненты тяжелее метана выделяют абсорбцией с последующим разделением компонентов низкотемпературной ректификацией. Более экономичным является метод низкотемпературной ректификации.
Как тот, так и другой методы требуют применения холода, с чем и связаны основные затраты. В связи с этим большое значение имеет эффективность и экономичность применяемых холодильных циклов.
Разделение газа пиролиза методом низкотемпературной ректификации (как более экономичным) идет как при высоком, так и при низком давлении.
В случае разделения газа пиролиза при низком давлении (давление 0,127–0,196 МПа, температура минус 120 °С) расширяется интервал температур кипения разделяемых углеводородов. Вследствие этого требуется меньше тарелок, меньше флегмовое число, при одновременном возрастании четкости разделения. Однако для создания низких температур приходится применять метановый холодильный цикл, который требует более сложного оборудования и менее экономичен. Эти установки малопроизводительны, чувствительны к изменению состава газа, их трудно автоматизировать.
59
Как в нашей стране, так и в ряде других стран, в частности вСША,
восновном применяется метод разделения газа пиролиза при высоком давлении(вЗападнойЕвропе– восновномпринизкомдавлении).
Рассмотрим технологическое оформление разделения газа пиролиза при высоком давлении (рис. 2.5).
Согласно схеме компримированный и осушенный газ поступает
вблок охлаждения и выделения водорода 1. Для его охлаждения используют отходящие холодные потоки пропилена, этилена, метана. В результате конденсации углеводородов (метана и выше) удается получить водород чистотой 90–95 %.
Конденсат подается в метановую колонну 2, в которой конденси-
руются углеводороды С2–С4, а из верхней части колонны 2 отбирается метановая фракция с небольшим содержанием водорода. Последняя идет в блок 1.
Углеводороды С2–С4 подаются в этановую колонну 3 для выделения этан-этиленовой фракции, которая идет на селективное гидри-
рование в аппарат 4 с целью удаления ацетилена. Далее фракция С2 поступает в колонну 5 для удаления водорода и метана, после чего разделяется на этилен и этан в колонне 6.
Остаток из колонны 3 – смесь углеводородов С3–С4 – направляется в пропановую колонну 7, из верхней части которой отбирается пропан-пропиленовая фракция. Последняя может выводиться или подвергаться селективному гидрированию для удаления пропандиена и метилацетилена в колонне 8 и последующему разделению на пропилен и пропан в колонне 9.
Технико-экономические показатели схемы низкотемпературного разделения газа пиролиза под высоким давлением в значительной степени определяются энергетическими затратами на создание холода, а они, в свою очередь, зависят от выбранной схемы охлаждения. Это сочетание методов дросселирования, расширения газа в детандере, каскадного охлаждения за счет теплообмена с испаряющимся высококипящим компонентом (например, охлаждение этилена пропаном, метана – этиленом) и др.
60