
Технологии органического и нефтехимического синтеза
..pdfВ промышленности применяется следующий оптимальный режим синтеза метанола на цинкхромовом катализаторе [(2,5–3,3) ZnO × × ZnCr 2О4]: температура 360–380 °С, давление 30 МПа, объемное соотношение Н2 : СО = 6, объемная скорость газа (35–40) · 103 ч–1; на низкотемпературных медьсодержащих катализаторах (СuО – 52–54; ZnO – 24–28; А12О3 – 5–6 мас. %) температура 260–280 °С, давление
5–10 МПа, объемная скорость газа (5–35) · 103 ч–1, объемное соотно-
шение (Н2 + СО2) : (СО + СО2) = 0,5–5,0.
9.3. ТЕХНОЛОГИЧЕСКИЕ СХЕМЫ ПРОЦЕССА
Промышленные установки синтеза метанола представляют собой крупные агрегаты мощностью 600–900 т/сут. Строятся установки мощностью 1500–2000 т/сут с использованием энерготехнологического принципа максимально возможного использования теплоты химической реакции.
Основным аппаратом блока синтеза является реактор, обычно полочного или трубчатого типа. Подробно реакторы и другая аппаратура установок синтеза метанола описаны в работе [7].
Принципиальная энерготехнологическая схема агрегата синтеза метанола мощностью 900 т/сут показана на рис. 9.1.
Природный газ под давлением 1,2 МПа разделяется на два потока. Первый поток смешивают с продувочными газами синтеза метанола в отношении 8 : 1 и через сепаратор и компрессор направляют в огневой подогреватель и далее в блок очистки от сернистых соединений. Очищенный газ (содержание соединений серы менее 0,5 мг/м3) смешивают с СО2 в соотношении СО2 : СН4 = 0,3–0,35 и с водяным паром в соотношении Н2О : СН4 = 3,0–3,5 и через подогреватель направляют в конвертер. Влажный конвертированный газ поступает в котел-ути- лизатор, где охлаждается до 280 °С, проходит последовательно подогреватели воды, охлаждается и отделяется от конденсата, дожимается компрессором до 5,5 МПа, смешивается с циркуляционным газом и через теплообменник и огневой подогреватель направляется в реактор
201
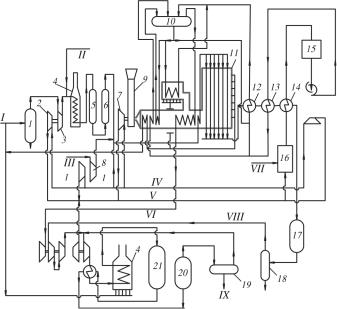
Рис. 9.1. Принципиальная технологическая схема агрегата синтеза метанола мощностью 900 т/сут: 1 – сепаратор; 2 – паровая турбина; 3 – турбокомпрессор природного газа; 4 – огневые подогреватели; 5 – реактор сероочистки; 6 – адсорбер; 7 – паровые турбины; 8 – компрессор СО2; 9 – дымовая труба; 10 – паросборник; 11 – трубчатая печь; 12 – котел-утилизатор; 13 – подогреватель; 14 – экономайзер; 15 – установка деаэрации; 16 – водоподготовка; 17 – воздушный конденсатор; 18 – сепаратор синтез-газа; 19 – сепаратор; 20 – воздушный холодильник колонны синтеза; 21 – колонна синтеза метанола. Потоки: I – природный газ; II – продувочный газ синтеза; III – СО2; IV – пар, 4 МПа; V – пар, 0,4 МПа; VI – пар, 10,4 МПа; VII – вода; VIII – конвертированный газ на синтез;
IX – метанол-сырец
синтеза метанола. Продукты синтеза через теплообменник и воздушный холодильник поступают в сепаратор метанола-сырца. Газ направляют на циркуляцию, а метанол-сырец на дистилляцию.
На рис. 9.2 представлены три типа реакторов синтеза метанола при пониженном давлении (5–10 МПа), различающиеся способами расположения катализатора и охлаждения.
202
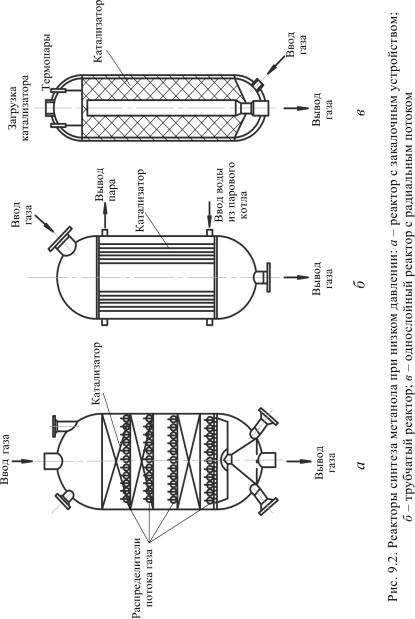
203
В реакторе с закалочными устройствами используется конструкция с несколькими слоями катализатора. Предварительно нагретая смесь рециркулируемого и свежего газа (СО + Н2) подается в различные слои катализатора, разделенные закалочными устройствами для предотвращения перегревов. В большинстве случаев после реактора стоит котел-утилизатор, в котором используется основное количество теплоты реакций.
Втрубчатом реакторе (см. рис. 9.2, б) катализатор, находящийся в трубках, охлаждается водой, поступающей в межтрубное пространство.
Воднослойном реакторе с радиальным потоком (см. рис. 9.2, в) катализатор расположен в виде вертикального кольцевого слоя. Радиальный поток газов, создаваемый в реакторе, обеспечивает незначительное падение давления и позволяет экономить энергию при работе компрессора рециркуляции.
Производство метанола в мире в начале XXI в. составило около 30 млн т в год.
Основной областью применения метанола является получение формальдегида (свыше 40 %). Метанол также используется в синтезе уксусной кислоты, сложных эфиров (в частности, диметилфталата), простых эфиров (МТБЭ, МТАЭ и др.), метилгалогенидов, аминов, ионообменных смол, в качестве растворителя, экстрагента и добавки
кмоторным бензинам. В дополнение к традиционным областям потребления значительными могут стать в будущем потребности в метаноле в новых областях, таких как энергетика, синтез белка, продуцируемого одноклеточными организмами.
Глава 10
ПРОИЗВОДСТВО УГЛЕВОДОРОДОВ ИЗ СИНТЕЗ-ГАЗА (ПРОЦЕСС ФИШЕРА – ТРОПША)
Синтез углеводородов из монооксида углерода и водорода, открытый в 1923 г. Фишером и Тропшем, в промышленных масштабах был осуществлен в конце 1930-х гг. в Германии с целью получения жидких топлив. В 1936–1942 гг. в Германии, Японии, Франции было построено более полутора десятка заводов, на которых применялись кобальтовые катализаторы преимущественно при атмосферном давлении. В 1944 г. производство продуктов по способу Фишера – Тропша в Германии достигло 600 тыс. т/год. В послевоенные годы промышленное производство топлив гидрированием СО сократилось, однако процесс интенсивно изучали в США, Англии, ФРГ, Японии, Индии, а также в Советском Союзе, ПНР. Основное внимание при этом было обращено на разработку новых вариантов технологии и создание новых высокопроизводительных и стабильных катализаторов. В результате в США и ЮАР были пущены новые заводы, на которых при среднем давлении в присутствии железных катализаторов начали выпускать наряду с жидким топливом сжиженный газ, спирты, растворители, твердые парафины.
Всередине 1960-х гг. в связи с интенсивным развитием нефтепереработки и нефтехимии значение способа синтеза углеводородов
из СО и Н2 как способа получения моторных топлив резко упало, что привело к сокращению исследований в этой области.
Внастоящее время интерес к этой реакции как универсальному методу синтеза углеводородов и кислородсодержащих соединений из ненефтяного сырья снова возрос.
Периодически состояние исследований и опытных работ в облас-
ти синтеза углеводородов из СО и H2 освещалось в обстоятельных монографиях и обзорах. Ниже рассмотрены основные промышленные достижения и перспективы развития процесса Фишера – Тропша.
205
10.1. ФИЗИКО-ХИМИЧЕСКИЕ ОСНОВЫ ГИДРИРОВАНИЯ СО
Гидрирование СО с образованием парафиновых и олефиновых углеводородов протекает по уравнениям:
– в случае синтеза парафинов:
nCO + (2n + 1) → CnH2n+2 + nH2O; |
(10.1) |
|
2nCO + (n + 1) → CnH2n+2 + nO2; |
(10.2) |
|
3nCO + (n + 1)H2O → CnH2n+2 + (2n + 1)CO2; |
(10.3) |
|
nCO2 + (3n + 1)H2 → CnH2n+2 + 2nH2O; |
(10.4) |
|
– в случае синтеза олефинов: |
|
|
nCO + 2nН2 |
→ CnH2n + nH2O; |
(10.5) |
2nCO + nН2 |
→ CnH2n + nСO2; |
(10.6) |
3nCO + nН2О → CnH2n + 2nСO2; |
(10.7) |
|
nCO2 + 3nН2 → CnH2n + 2nН2O |
(10.8) |
Основными реакциями, определяющими суммарный процесс, являются:
СО + 2Н2 → [–СН2–] + Н2О, |
∆Н297 = –165,0 кДж, |
(10.9) |
|
СО + Н2О → СО2 + Н2 , |
∆Н297 |
= –39,8 кДж, |
(10.10) |
2СО + Н2 → [–СН2–] + СО2, |
∆Н297 |
= –204,8 кДж, |
(10.11) |
3СО + Н2О → [–СН2–] + 2СО2, |
∆Н297 |
= –244,5 кДж, |
(10.12) |
СО2 + 3Н2 → [–СН2–] + 2Н2О, |
∆Н297 |
= –125,2 кДж. |
(10.13) |
На основании указанных стехиометрических уравнений можно подсчитать теоретически возможный выход углеводородов при гидрировании СО (табл. 10.1).
206

Таблица 1 0 . 1
Теоретический выход углеводородов, полученных гидрированием СО при различных расходных и заданных отношениях СО : Н2
Расходное соотношение |
Выход углеводородов С2 и выше, г/см3 синтез-газа |
||
СО : Н2 |
СО : Н2 = 1 : 2 |
СО : Н2 = 1 : 1 |
СО : Н2 = 2 : 1 |
1 : 2 |
208,5 |
156,3 |
104,3 |
1 : 1 |
138,7 |
208,5 |
138,7 |
2 : 1 |
104,3 |
156,3 |
208,5 |
Побочными реакциями, снижающими теоретически возможный выход углеводородов, являются:
– гидрирование СО в метан:
СО + 3Н2 → СН4 + Н2О, |
∆Н297 |
= –214,8 кДж, |
(10.14) |
или |
|
|
|
2СО + 2Н → СН4 + СО2, |
∆Н297 |
= –254,1 кДж, |
(10.15) |
СО2 + 4Н2 → СН4 + 2Н2О; |
|
|
(10.16) |
– разложение СО по реакции Будуара:
2СО → С + СО2, |
∆Н297 = –134,0 кДж; |
(10.17) |
– образование кислородсодержащих соединений, например спиртов, альдегидов, кетонов, кислот; окисление металла катализаторов водой или СО2.
Промышленные катализаторы. Сначала для синтеза углево-
дородов при давлении 0,1–1,2 МПа применяли кобальтовые катализаторы, в частности 100 – Со + 18 – ThO2 + 200 – кизельгур и 100 – Со + 5 – ThO2 + 8 – MgO кизельгур (массовые части). Основными недостатками этих катализаторов, которые применяли на всех установках атмосферного и низкого давления, являются невысокая производительность, низкая селективность, наличие радиоактивного промотора. Позднее разработаны модифицированные катализаторы, в которых оксиды Mg и Th были заменены на МnО и уменьшено содержание кизельгура. Эти катализаторы позволяли получать высокий выход высокомолекулярных углеводородов и применялись до разработки железных катализаторов.
207

В 1954 г. было обнаружено, что в качестве промоторов Со-ката- лизаторов вместо ThO2 можно использовать ZrO2 или ТiО2. Наиболее активным является катализатор состава 100 – Со + 6 – ZrO2 + 10 – Mg + + 200 – кизельгур, на котором при давлении 1 МПа образуется достаточно селективно твердый парафин (температура плавления 70–98 °С) с выходом 92–116 г/нм3. В 1956 г. были предложены катализаторы состава 100 – Со+ 6–16 – MgO + 250–280 – кизельгур, нашедшие также промышленное применение. Характеристика некоторых промышленных Co-катализаторовсинтезаФишера– Тропшаприведенавтабл. 10.2.
Промышленные железные катализаторы были разработаны в 1950-х гг. для высокопроизводительного синтеза при среднем давлении. По сравнению с кобальтовыми железные катализаторы обладают рядом преимуществ. Они активны и стабильны в широком интервале температур и давлений при различном отношении Н2 : СО в исходном газе, дешевы и легкодоступны, позволяют интенсифицировать процесс синтеза в 10–20 раз.
Железные катализаторы готовят методами осаждения, пропитки, спекания, плавления.
Таблица 1 0 . 2
Промышленные Со-катализаторы гидрирования СО при соотношении Н2 : СО = 2 : 1
Показатели процесса |
|
Катализаторы |
|
|||
I |
II |
III |
IV |
V |
||
|
||||||
Давление, МПа |
0,7 |
0,1 |
0,1 |
1 |
1 |
|
Температура, °С |
190–197 |
182–195 |
190–200 |
190–200 |
190–200 |
|
Объемная скорость, ч–1 |
100–200 |
100 |
100 |
100 |
100 |
|
Конверсия газа, об. % |
50–70 |
69–74 |
74–85 |
78–82 |
74–80 |
|
Выход углеводородов, |
|
|
|
|
|
|
г/нм3: |
|
|
|
|
|
|
С1–С4 |
17–40 |
29–40 |
– |
12–15 |
– |
|
С5 – 320 °С |
82–84 |
96–102 |
67–130 |
40–50 |
72–76 |
|
Парафина > 320 °С |
– |
– |
14–20 |
66–71 |
42–44 |
|
Суммарный выход |
97–124 |
119–142 |
130–190 |
110–125 |
129–132 |
|
углеводородов, г/нм3 |
208
I: 100 – Со + 18 – ТbО2 + 100–200 – кизельгур; II: 100 – Со + 6 – ТhО2 + 12 – МgO + 200 – кизельгур; III: 100 – Co + 6 – ZrO2 + 10 – MgO + 200 – кизельгур; IV: 100 – Co + 6 – ZrO2 + 10 – MgO + 200 – кизельгур; V: 100 – Co + 6–16 – MgO + 250–280 – кизельгур.
10.2. ТЕХНОЛОГИЧЕСКОЕ ОФОРМЛЕНИЕ И УСЛОВИЯ ПРОВЕДЕНИЯ ПРОЦЕССА
Основной проблемой при промышленной реализации процесса Фишера – Тропша является отвод теплоты реакции, составляющей до 10–15 ГДж на 1 кг полученных продуктов. Решение этой задачи во многом зависит от катализатора, целевой направленности процесса, способа осуществления процесса, конструкции реакционного устройства. Этапы развития промышленной технологии процесса Фишера – Тропша подробно описаны.
Внастоящее время в промышленности реализована технология
встационарном слое катализатора, в потоке взвешенного катализатора и в жидкой фазе с суспендированным катализатором.
Синтез в газовой фазе на стационарных катализаторах. Технологические схемы процесса Фишера – Тропша в газовой фазе на стационарном катализаторе, реализованные в различные годы в промышленности, отличаются катализатором, давлением, числом ступеней, наличием или отсутствием циркуляции, нагрузкой по синтез-газу, способами регенерациикатализатора.
Первые промышленные установки с использованием кобальтовых катализаторов при атмосферном давлении, оборудованные пластинчатыми реакторами, работали по схеме «на проток» в две и более ступеней с низкой производительностью и частыми регенерациями.
При переходе на технологию синтеза при повышенном давлении пластинчатые реакторы были заменены на реакторы типа «труба в трубе». Использование, кроме того, рециркуляции газа позволило улучшить теплоотвод, повысить степень превращения реагентов и производительность реактора примерно в 1,5 раза, снизить метанообразование и увеличить срок службы катализатора. Вместо кобальтовых стали широкоприменять железные катализаторы.
209
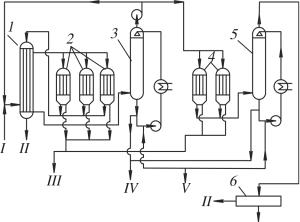
Типичная технологическая схема процесса Фишера – Тропша при среднем давлении показана на рис. 10.1.
Рис. 10.1. Принципиальная технологическая схема синтеза Фишера – Тропша при среднем давлении: 1 – теплообменник; 2 – реакторы первой ступени; 3 – конденсатор первой ступени; 4 – реакторы второй ступени; 5 – конденсатор второй ступени; 6 – установка для очистки газа активированным углем. Потоки: I – свежий синтез-газ; II – отходящий газ после реакции;
III – парафин; IV – масло; V – щелочь
По этой схеме работала установка фирмы Krupp-Kohlechemie. Процесс осуществляли с железным катализатором при температуре 200–215 °С, давлении 1,1 МПа и с нагрузкой по синтез-газу (Н2 : Со =
=1,25 : 1) 100 ч–1. Конверсия в каждой ступени составляла 60 %.
В1952–1954 гг. была разработана новая технология высокопроизводительного процесса при среднем давлении, которая была реализована на заводе «Сасол-1» в ЮАР. На рис. 10.2 показана принципи-
альная технологическая схема высокопроизводительного синтеза в газовой фазе на стационарном железном катализаторе по способу
«Ruhrchemie-Lurgi».
Исходный синтез-газ (СО : Н2 = 1,71 : 1) смешивают в соотношении 1 : 2,5 с циркулирующим газом, компримируют до 2,5 МПа и через
210