
Технологии органического и нефтехимического синтеза
..pdf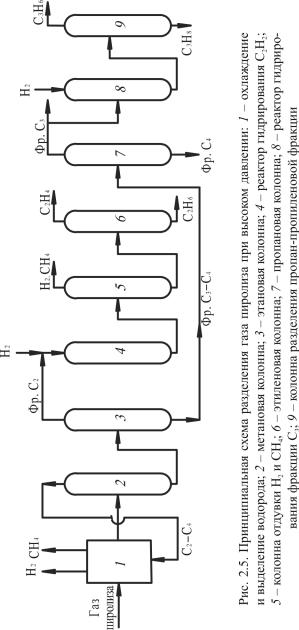
61
Дросселирование – это адиабатическое расширение газа, сопровождающееся изменением температуры, которое обусловлено тем, что энтальпия газа зависит не только от температуры, но и от давления. Дроссельный эффект положительный, если температура газа снижается при дросселировании, и наоборот.
Детандер – газовый двигатель, в котором происходит адиабатическое расширение газов с одновременным совершением внешней работы (перемещение поршня, вращение колеса турбины). При этом газ охлаждается, так как совершаемая газом внешняя работа производится за счет его внутренней энергии.
2.5.3. Очистка этилена
Очистка этилена сводится к удалению из него сероводорода, оксида и диоксида углерода, ацетилена и кислорода.
Сероводород, диоксид углерода и органические сернистые соединения удаляются из этилена за счет промывки газа в скруббере 10%-м раствором NaОН. При этом протекают следующие химические реакции:
Н2S + 2NaОН → Na2S + 2Н2О; |
(2.1) |
СО2 + 2NaОН → Na2СО3 + Н2О; |
(2.2) |
СОS + 4NaОН → Na2СО3 + Na2S + 2Н2О; |
(2.3) |
СS2 + 6NaОН → Na2СО3 + 2Na2S + 3Н2О |
(2.4) |
Существенное снижение содержания сернистых |
соединений |
(до 0,0001 %) и диоксида углерода (до 0,001 %) достигается при двухступенчатой промывке щелочью.
Очистка от ацетилена проводится либо промывкой ацетоном при низких температурах, либо селективным гидрированием. Содержание ацетилена в газе пиролиза колеблется от 0,1 до 1 %. После очистки оно должно быть снижено до 0,001–0,002 %.
62
При промывке газа ацетоном ацетилен растворяется в нем. После этого ацетон регенерируют путем отгонки ацетилена и вновь подают на абсорбцию. При большой мощности установок пиролиза ацетилен можно получать как целевой продукт.
Очистка этилена от ацетилена селективным гидрированием основана на реакции:
СН≡СН + Н2 → СН2=СН2 |
(2.5) |
Условия выбираются такими, чтобы исключить гидрирование этилена. Одновременно с этим этан-этиленовая фракция освобождается от кислорода и оксида углерода по реакциям:
О2 + 2Н2 → 2Н2О; |
(2.6) |
СО + 3Н2 → СН4 + Н2О |
(2.7) |
В качестве катализатора гидрирования применяют никель на кизельгуре, палладий на активированном угле, платину на оксиде алюминия. Условия: температура 100–180–200 °С, давление 2–3 МПа. Процесс идет в реакторах трубчатого или колонного типа.
2.5.4. Выделение и концентрирование пропилена
Для проведения ряда синтезов требуется пропилен высокой чистоты (например, для гидроформилирования), поэтому получаемую в ходе фракционирования пропан-пропиленовую фракцию первоначально очищают от ряда примесей (пропандиена, метилацетилена, сероводорода, диоксида углерода, кислорода и др.).
Удаление сероводорода и диоксида углерода проводят путем промывки щелочью. Пропандиен и метилацетилен удаляют селективным гидрированием. Суммарное их содержание в пропан-пропилено- вой фракции достигает 0,4–0,5 %.
Концентрация пропилена в пропан-пропиленовой фракции доходит до 80 %. Для разделения фракции используют в основном ректифи-
63
кацию, хотя можно также применять и экстрактивную или азеотропную дистилляцию.
При разделении пропан-пропиленовой фракции используют схемы либо с повышенным давлением (до 2 МПа) и водяным охлаждением, что требует большого числа тарелок и повышенной кратности орошения, либо с применением пропиленового и пропанового тепловых насосов.
Гидрирование пропандиена и метилацетилена идет, как правило, в жидкой фазе (температура 10–15 °С, давление 0,5–1,5 МПа). Катализатор – палладий на оксиде алюминия.
Можно удалять пропандиен и метилацетилен из пропан-пропи- леновой фракции и ректификацией, но требуемое флегмовое число равно 20.
Глава 3
ПРОИЗВОДСТВО УГЛЕВОДОРОДНОГО СЫРЬЯ ДЛЯ ПРОВЕДЕНИЯ СИНТЕЗОВ. ПОЛУЧЕНИЕ ЦИКЛОПАРАФИНОВ, ВЫСШИХ НЕНАСЫЩЕННЫХ И АРОМАТИЧЕСКИХ УГЛЕВОДОРОДОВ
3.1. ПОЛУЧЕНИЕ ВЫСШИХ НЕНАСЫЩЕННЫХ УГЛЕВОДОРОДОВ
Кроме низших (газообразных) олефинов, важным видом углеводородного сырья, используемого при проведении различных синтезов, являются высшие (жидкие) олефины: α-олефины, олефины с внутренней двойной связью, разветвленные олефины.
Жидкие α-олефины с прямой цепью (С8–С20) применяются в основном для производства синтетических моющих средств. Их получают термическим крекингом н-парафинов, а также олигомеризацией этилена на катализаторах Циглера.
Процесс термокрекинга н-парафинов реализован в промышленности и по аппаратурному оформлению аналогичен термокрекингу нефтяного сырья в трубчатых печах.
В качестве сырья при этом применяют как мягкие (фракция 260–370 °С, температура плавления 23 °С), так и твердые (фракция 400–500 °С, температура плавления 62 °С) парафины. Процесс ведут в паровой фазе при температуре 550 °С и небольшом избыточном давлении в присутствии водяного пара. Глубина крекинга за проход не превышает 25–30 %. Предусмотрена рециркуляция непрореагировавшего парафина.
Полученные жидкие фракции крекинга содержат в своем составе до 75 % непредельных углеводородов с открытой цепью. При этом больше олефинов образуется при крекинге мягких парафинов.
65
В частности, фракция 180–240 °С, используемая для алкилирования бензола, содержит 75–83 % α-олефинов, 8–14 % парафинов, 1 % сопряженных диенов, 2–7 % несопряженных диенов, 1,5–2,5 % циклических и1–4 % ароматическихуглеводородов.
α-Олефины также могут быть получены путем олигомеризации этилена на катализаторах Циглера. При этом получается смесь α-олефи- нов, в которой содержится до 50 % целевых α-олефинов С10–С14. Получение α-олефинов идет по следующей схеме:
Al + 3H2C=CH2 + 1,5H2 → Al(C2H5)3 триэтилалюминий; |
(3.1) |
Al(C2H5)3 + 3nH2C=CH2 синтез→ Al[–(C2H4)n–C2H5]3; |
(3.2) |
Al[–(C2H4)n –C2H5]3 замещение→ |
|
→ Al (C2H5)3 + 3H–(C2H4)n–1–HC=CH2 |
(3.3) |
Реакция роста цепи (синтез) протекает при давлении 10 МПа
итемпературе 100–120 °С. Реакция замещения проходит при температуре 250–320 °С и давлении ниже 1 МПа. Реакция ускоряется при введении в систему Ni. Al(C2Н5)3 из смеси выделяют перегонкой
ивозвращают в процесс.
Олефины с внутренней двойной связью в основном применяют для получения альдегидов и спиртов методом оксосинтеза и частично для получения синтетических моющих средств (СМС).
Их получают дегидрированием на Рt-содержащих катализаторах
соответствующих фракций парафинов (С8–С10, С10–С13, С11–С14, С15–С18), полученных выделением на цеолитах и очищенных олеумом для
удаления ароматических и сернистых соединений.
В процессе используют кислотный алюмоплатиновый катализатор, промотированный Li, K, Ge или другими металлами группы германия. Процесс ведут в стационарном слое катализатора (процесс Пекол) с рециркуляцией водородсодержащего газа. Условия процесса: давление 0,3–0,4 МПа, температура 450–500 °С, мольное соотношение водород : сырье равно (6–8) : 1. Продолжительность цикла 30 сут. Конверсия сырья за проход 10 %, селективность по моноолефинам 90 %.
66
Впроцессе получают олефины, имеющие двойную связь преимущественно в средней части углеводородной цепи. Ценным продуктом является и водородсодержащий газ, в котором содержится не менее 95 % водорода.
Вслучае использования получаемых олефинов для алкилирования их не выделяют, а весь продукт используют в процессе. Если же олефины используют в оксосинтезе, то их концентрируют с применением методов адсорбции.
Внастоящее время в производстве ПАВ и СМС применяют также тетрамеры пропилена. Для получения тетрамера проводят олигомеризацию пропилена, содимеризацию с димерами и тримерами
на фосфорно-кислом катализаторе Р2О5 · 2Н2О · SiО2 (твердая фосфорная кислота). Он содержит пирофосфорную кислоту Н4Р2О7 на кизельгуре (природный материал из мелкодисперсного SiО2).
Расход катализатора: 1 кг на 140–150 кг тетрамера. Продолжительность работы катализатора 1200–1300 ч. Процесс протекает по карбоний-ионному механизму.
Процесс олигомеризации пропилена – ступенчатый; при этом последовательно образуются ди-, три-, тетра- и другие олигомеры.
Этот процесс проводят в реакторах типа «труба в трубе», трубки
вкоторых заполнены катализатором. В межтрубном пространстве циркулирует химочищенная вода. Процесс ведут при температуре 180–210 °С на входе в реактор и 225–230 °С на выходе из него и давлении 7–8 МПа. Процесс осуществляют с рециркуляцией низших олигомеров, ввиду чего наблюдается повышенный выход тетрамеров.
3.2. ПОЛУЧЕНИЕ ЦИКЛОПАРАФИНОВ
Из циклопарафинов наибольшее применение в нефтехимии получили циклогексан (сырье для производства полиамидных волокон) и метилциклопентан (как источник получения циклогексана).
Циклогексан получают различными методами:
а) извлечение циклогексана из нефтяных фракций с использованием ректификации и экстрактивной перегонки для нефтей, содержа-
67
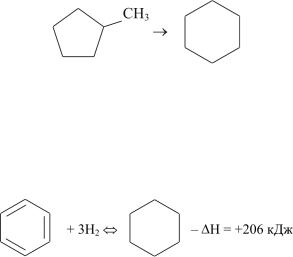
щих большое количество нафтеновых углеводородов в своем составе. Для нефтей Восточных районов характерно небольшое количество нафтенов (5–6 %). Однако большое количество нафтенов содержится вконденсатах, получаемыхизгазовгазоконденсатныхместорождений;
б) получение циклогексана из метилциклопентана путем изомеризации последнего на катализаторе AlCl3, промотированном НСl:
(3.4)
Процесс идет в жидкой фазе при температуре 80 °С. Изомеризации подвергается фракция 66–85 °С, содержащая помимо основных компонентов н-С6Н14, бензол и другие соединения. Для получения циклогексана с чистотой 99 % требуется его дополнительная очистка с использованием экстрактивной перегонки и ректификации;
в) получение циклогексана гидрированием бензола по реакции
(3.5)
Реакция обратима и идет с уменьшением объема и выделением тепла. В связи с этим сдвигу равновесия вправо способствует повышенное давление и умеренные температуры.
Процесс гидрирования бензола может проводиться как в паровой, так и в жидкой фазах. Наиболее распространен жидкофазный процесс.
В качестве катализатора гидрирования бензола могут применяться металлические и сульфидные катализаторы. Металлические (Рt, Ni) работают при температуре 150–200 °С и давлении 5 МПа. В этих условиях достигается полное превращение бензола в циклогексан. Однако эти катализаторы чувствительны к примесям, в частности к тиофену. Поэтому требуется предварительная очистка бензо-
68
ла. Сульфидные катализаторы (NiS, MoS), наоборот, эффективны только на сернистом бензоле, но требуются более жесткие условия: температура 350–370 °С и давление 30 МПа.
На этих катализаторах не удается добиться полной конверсии бензола в циклогексан, кроме того, идет частичная изомеризация циклогексана в метилциклопентан. Непревращенный бензол и метилциклопентан необходимо отделять от циклогексана, что значительно удорожает процесс.
Аппаратурное оформление процесса определяется необходимостью отвода большого количества тепла (1750 кДж на 1 кг бензола). Для гидрирования используют реакторы с непрерывным и ступенчатым отводом тепла. Реакторы первого типа – трубчатые, напоминающие кожухотрубчатые теплообменники, в трубках которых засыпан катализатор, а в межтрубном пространстве циркулирует конденсат. Тепло отводится за счет испарения конденсата и образования водяного пара. Отвод тепла регулируется давлением (так как оно влияет на температуру кипения, а следовательно, и на испарение конденсата и отвод тепла).
Реакторы со ступенчатым отводом тепла представляют собой аппараты колонного типа. Отвод тепла в этом случае осуществляется либо поддувом холодного водорода между слоями катализатора, либо охлаждением реакционной смеси в выносных холодильниках при циркуляции циклогексана.
Рассмотрим схему гидрирования бензола в жидкой фазе (рис. 3.1), где использован реактор колонного типа, заполненный стационарным слоем платинового катализатора. Тепло отводится циркулирующим циклогексаном. Бензол и циркулирующий циклогексан в смеси с циркуляционным и свежим водородом нагреваются до температуры реакции (250–280 °С) и поступают в реактор 1. Реакционная смесь из реактора 1 направляется в газосепаратор высокого давления 3, откуда водород возвращается в процесс, а часть циклогексана попадает в реактор для регулирования температуры. Остальной циклогексан поступает в газосепаратор низкого давления 4, где отделяются газообразные угле-
69
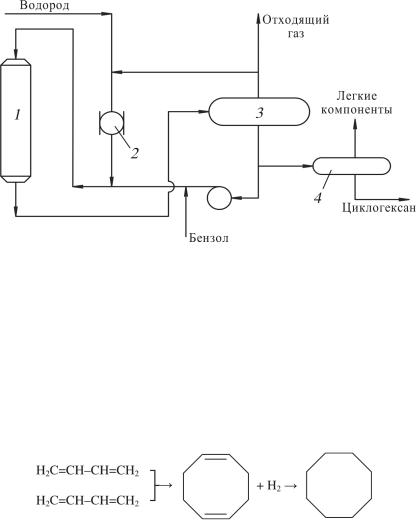
Рис. 3.1. Технологическая схема гидрирования бензола в жидкой фазе: 1 – реактор; 2 – компрессор; 3 – газосепаратор высокого давления; 4 – газосепаратор низкого давления
водороды. На рис. 3.1 2 – компрессор для создания давления (3,5 МПа). Производительность установок от 30 до 120 тыс. т/год.
Циклооктан в настоящее время получают в промышленности циклодимеризацией (в растворителе) бутадиена-1,3 в циклооктадиен-1,5 на катализаторе (С6Н5О)3РNi(Со)4 при температуре 165 °С и давлении 4 МПа с последующим гидрированием последнего (выход 65 %):
(3.6)
Циклододекан получают в промышленности циклотримеризацией бутадиена-1,3 в присутствии комплексного катализатора Al(C2H5)2Cl-TiCl4 в циклододекантриен-1,5,9 с последующим его гидрированием:
70