
Сопротивление материалов
..pdf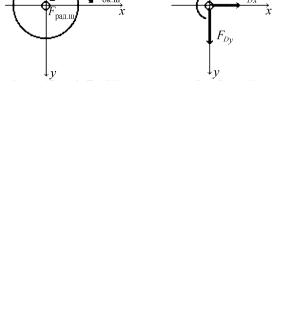
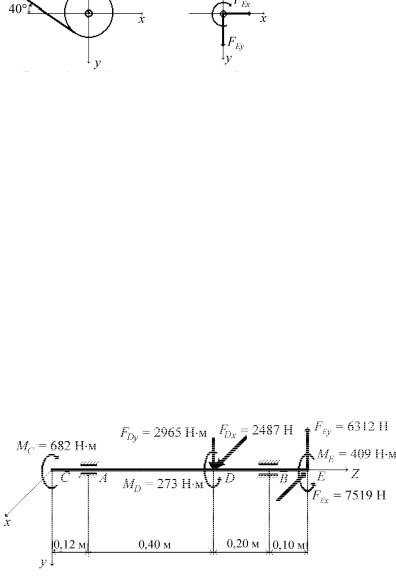
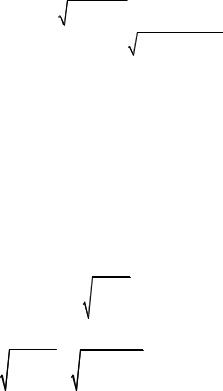

Рис. 11.8. Эпюры внутренних силовых факторов
234
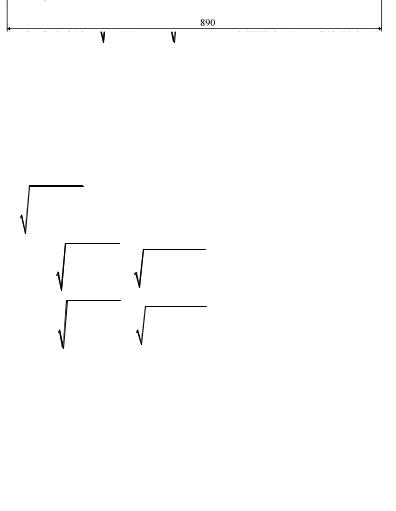
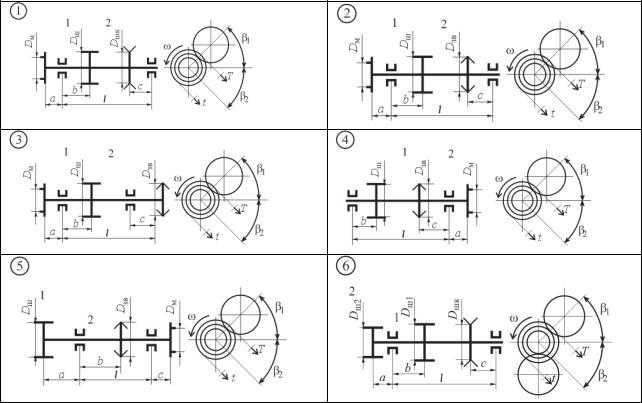
236
Рис. 11.10.
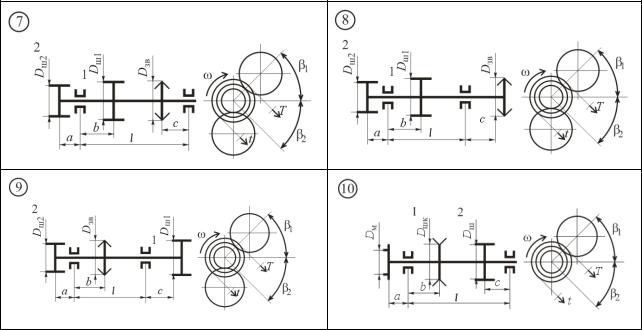
Рис. 11.10. Окончание
237

3. Как записывается условие прочности при изгибе с кручением круглого стержня?
Для лучшего усвоения материала рекомендуется изучить источник [5] (гл. 10, § 10.4).
Контрольная работа № 12
Расчет вала круглого поперечного сечения на прочность при изгибе с кручением
Рассчитать стальной вал на прочность при совместном действии изгиба и кручения. Мощность подводится к валу от электродвигателя посредством муфты, а снимается через зубчатую передачу посредством шестерни 1 и ременной или цепной передачи 2.
Схемы вала и расположения передач приведены на рис. 11.10. Числовые данные принять по табл. 11.1.
Содержание и порядок выполнения работы
1.Вычертить схему вала и схему расположения передач с указанием численных значений заданных величин.
2.Определить усилия в элементах передач и привести их
кцентру вала, разложив по двум взаимно перпендикулярным плоскостям.
3.Построить эпюры крутящих моментов и изгибающих моментов в выбранных взаимно перпендикулярных плоскостях.
4.Построить эпюру суммарных изгибающих моментов.
5.Построить эпюру расчетных моментов, используя четвертую теорию прочности.
6.Произвести ориентировочный расчет диаметра вала из
условия прочности, приняв [σ]= [σnт], ([n] – предварительный
коэффициент запаса, [n] = 4…5) и округлить его значение до ближайшего стандартного размера по ГОСТ 6636–69.
7. Дать эскиз вала.
238
|
|
|
|
|
|
|
|
|
|
|
|
|
|
Таблица 11.1 |
||
|
|
|
|
|
|
|
|
|
|
|
|
|
|
|
|
|
Но- |
|
|
|
|
|
|
Цифра шифра |
|
|
|
|
|
||||
мер |
1-я |
|
|
2-я |
|
|
|
3-я |
4-я |
5-я |
|
6-я |
|
|||
стро- |
схе- |
|
Размеры, мм |
|
|
Углы, |
Мощ- |
n, |
|
Марка |
Rz, |
|||||
ки |
ма |
|
|
|
|
|
|
|
град |
ность, |
об/мин |
стали |
мк |
|||
|
|
|
|
|
|
|
|
|
|
|
кВт |
|
|
|
|
|
|
|
l |
a |
b |
c |
Dшк |
Dш |
β1 |
β2 |
N |
N1 |
n |
|
|
|
|
|
|
|
|
|
|
(Dзв) |
|
|
|
|
|
|
|
|
|
|
1 |
1 |
460 |
85 |
140 |
95 |
220 |
|
180 |
30 |
60 |
18 |
7 |
220 |
|
50 |
3,2 |
2 |
2 |
540 |
90 |
180 |
110 |
300 |
|
210 |
40 |
70 |
24 |
10 |
300 |
|
55 |
6,3 |
3 |
3 |
600 |
110 |
200 |
120 |
360 |
|
230 |
45 |
120 |
16 |
6 |
320 |
|
60 |
12,5 |
4 |
4 |
500 |
100 |
150 |
100 |
400 |
|
260 |
60 |
200 |
30 |
12 |
400 |
|
20Х |
25 |
5 |
5 |
650 |
120 |
220 |
130 |
450 |
|
300 |
70 |
140 |
26 |
11 |
380 |
|
40Х |
6,3 |
6 |
6 |
720 |
140 |
250 |
140 |
500 |
|
340 |
110 |
30 |
28 |
11 |
450 |
|
45Х |
1,6 |
7 |
7 |
450 |
100 |
130 |
80 |
380 |
|
210 |
80 |
210 |
19 |
7,5 |
280 |
|
40ХН |
12,5 |
8 |
8 |
560 |
110 |
170 |
100 |
400 |
|
190 |
30 |
80 |
14 |
6,2 |
350 |
|
30ХМ |
25 |
9 |
9 |
620 |
120 |
200 |
110 |
380 |
|
220 |
45 |
160 |
22 |
8,4 |
380 |
|
60 |
3,2 |
10 |
10 |
480 |
100 |
120 |
120 |
320 |
|
160 |
120 |
110 |
13 |
5,8 |
230 |
|
40Х |
12,5 |
Примечание. При наличии в схеме вала двух шестерен диаметр меньшей шестерни принять равным 0,5Dш.
ГЛАВА 12. УСТАЛОСТЬ МАТЕРИАЛОВ И ЭЛЕМЕНТОВ КОНСТРУКЦИЙ
12.1. Явление усталости
Усталостью материалов называется процесс образования и развития трещин под действием периодически меняющейся нагрузки.
Различают малоцикловую усталость, при которой наблюдаются заметные пластические деформации, а число циклов до разрушения не превышает 50 000 циклов, и многоцикловую усталость, при которой уровень напряжений может быть значительно ниже пределов упругости или текучести, а число циклов до разрушения составляет от сотен тысяч до десятков миллионов циклов. Но и в этом случае из-за существенной микронеоднородности современных конструкционных материалов зарож-
239
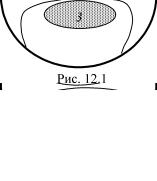
дение трещины усталости связано с локальными повторными пластическими деформациями, протекающими в отдельных структурных элементах материала.
В дальнейшем речь пойдет, в основном, о многоцикловой усталости, при которой разрушение протекает без заметных пластических деформаций на макроуровне и имеет специфический характер. Трещина зарождается, как правило, с поверхности детали в наиболее нагруженных местах (выточках, галтелях, переходах, отверстиях и т.д.) и постепенно распространяется, как бы перерезывая деталь, уменьшая площадь ее рабочего сечения. В процессе развития трещины ее обнаружение крайне затруднительно, так как сама трещина обычно закрыта, а деталь долго сохраняет свою несущую способность. И только когда оставшееся сечение не сможет нести нагрузку, происходит катастрофическое, почти мгновенное разрушение детали.
Статистикой установлено, чтобольше половины катастроф (без учета террористических актов) связано с этим грознымявлением.
При усталостном разрушении на поверхности излома можно выделить три характерные зоны (рис. 12.1): зону зарождения трещины 1, имеющую вид темного пятна, зону ее развития 2, занимающую, как правило, большую часть площади излома и представляющую гладкую поверх-
ность, и так называемую зону долома 3 с зернистой структурой. Соотношение между размерами зон и их конфигурация зависят от вида и уровня нагружения и конструкции детали. Тонкие линии на рис. 12.1 показывают последовательное положение фронта трещины по мере ее распространения.
12.2. Характеристики цикла
Под действием периодически меняющихся нагрузок в опасной точке возникают так же периодически меняющиеся напряжения. Пусть в некоторой детали реализуется линейное напряженное состояние, а нормальные напряжения в опасном сечении
240