
Выбор абразивных инструментов и режимов резания для высокоэффективно
..pdf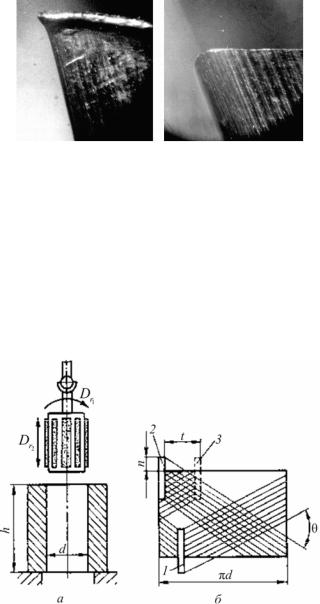
аб
Рис. 29. Вид острой кромки детали до обработки ПАЩ (а) и после обработки ПАЩ (б)
Рекомендуется применять волокна в тех случаях, когда необходимо удалять заусенцы и/или придавать радиусы кромкам без негативного воздействия на геометрические допуски деталей.
1.2.10. Хонингование
Хонингование – это процесс внутренней абразивной обработки цилиндрических отверстий с помощью специального абразивного инструмента – хона (рис. 30, а). Абразивный инструмент хон пред-
Рис. 30. Схема процесса хонингования отверстий (а)
и следы обработки на развертке внутренней поверхности (б)
41
ставляет собой набор абразивных брусков, расположенных на периферии шпинделя и совершающих возвратно-поступательное движение с большой частотой. Особенность процесса хонингования заключается в незначительном съеме припуска, но с обеспечением высокой точности и качества поверхности: отклонение от круглости менее 1 мкм, волнистость менее 0,5 мкм, отклонение от цилиндричности и прямолинейности образующей менее 2–5 мкм, шерохова-
тость Ra = 0,02…0,16 мкм.
Хонинговальные бруски изготавливаются из обычных абразивов, алмазов и новых сверхтвердых материалов. При хонинговании совмещаются вращательное и возвратно-поступательное движения инструмента, благодаря чему создается характерная сетка, как следствие перемещения абразивных зерен по винтовой линии (рис. 30, б). Совмещение движений дает возможность эффективно исправлять отклонения от правильной геометрической формы отверстий (конусность, овальность, корсетность, бочкообразность). К преимуществам процесса следует отнести также и то, что хонингование увеличивает срок службы трущихся пар по сравнению с другими методами окончательной обработки. Стойкость хонингованных поверхностей на 25 % выше, чем обработанных другими методами. При хонинговании инструмент и деталь самоустанавливаются, что обеспечивает высокую точность обрабатываемых отверстий. При этом также отпадает необходимость правки инструмента, а припускимогут бытьсведены до минимума.
Абразивный инструмент хон (рис. 31) представляет собой набор абразивных брусков, расположенных на периферии шпинделя и совершающих возвратно-поступательное движение с большой частотой. Хонинговальные бруски изготавливаются из обычных абразивов и новых сверхтвердых материалов. При обработке деталей из стали и чугуна в качестве СОЖ применяют керосин или смесь керосина с веретенным маслом (10–20 %). При использовании алмазных хонинговальных брусков часто применяют в качестве СОЖ обычную воду, в которую добавляют различные (как правило, синтетические) вещества, предотвращающие коррозию обрабатываемой детали и самого станка. Использование водных растворов оправдывается более высокой плотностью воды (по сравнению с маслами и керосином), а следовательно, и более
42
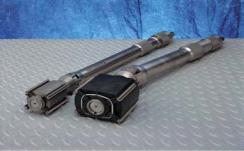
интенсивным отводом тепла, что является одним из важнейших требований, предъявляемых к СОЖ. При этом водные растворы более экологичныи менее вредныдляоператорастанка.
Рис. 31. Общий вид хонинговальных головок
Наибольшее распространение в машиностроении нашел процесс алмазного хонингования. Алмазное хонингование является прогрессивным процессом современного крупносерийного и массового производства. Высокая размерная стойкость алмазных брусков, значительное снижение температур и усилий резания по сравнению с обычным абразивным хонингованием позволили автоматизировать процессы обработки, активизировать контроль, повысить точность и производительность обработки, а самое главное – увеличить долговечность ответственных деталей машин и механизмов. Алмазное хонингование применяется при обработке блоков цилиндров, гильз и втулок автомобильных, тракторных, мотоциклетных и судовых двигателей, цилиндров компрессоров, насосов, деталей станков, холодильников, шатунов, шестерен и др.
1.2.11. Суперфиниширование
Суперфиниширование – это шлифование валов с помощью абразивных брусков при малом съеме металла (10–12 мкм на диаметр) для достижения шероховатости Ra = 0,16…0,02 мкм. Процесс осуществляется при малых окружных скоростях изделия (8–40 м/мин), малых давлениях мелкозернистых брусков (1,5–3 кгс/см2) при их колебательном движении с частотой от 500–600 до 2000–3000 двойных ходов в минуту с амплитудой 2–5 мм (рис. 32). Процесс суперфини-
43

ширования часто осуществляется на модернизированных универсальных токарно-винторезных станках. Деталь устанавливается в шпиндель станка, а головка с брусками – на место резцедержателя.
Рис. 32. Схема процесса суперфиниширования вала абразивными брусками
При суперфинишировании полностью удаляется волнистость, уменьшается огранка, удаляется дефектный поверхностный слой металла. После суперфиниширования формируется упрочненный поверхностный слой без структурных изменений, что улучшает эксплуатационные свойства деталей, работающих в условиях трения, скольжения или качения. Рабочим инструментом является абразивная головка с одним-четырьмя абразивными брусками.
1.2.12.Разрезка заготовок и деталей машин абразивными инструментами
Разрезка заготовок и деталей машин с применением специальных абразивных отрезных кругов широко применяется в машиностроении. Заготовка обычно устанавливается в тисках, а отрезной круг вращается с большой скоростью и с определенной поперечной подачей разрезает заготовку в нужном месте. Преимущество этого метода перед другими методами разрезки состоит в высокой производительности разрезки. Кроме того, абразивный отрезной круг может практически разрезать любой труднообрабатываемый материал, что недоступно, например, при разрезке фрезами или ленточными пилами. К недостаткам метода нужно отнести вероятность появления
44

прижогов на торцевой поверхности заготовки и большой расход кругов из-за повышенного их износа. Различные схемы и методы разрезки отрезным кругом представлены на рис. 33.
Рис. 33. Основные способы и схемы разрезки заготовки отрезным абразивным кругом: а – маятниковая отрезка; б – прямая отрезка; в – отрезка с вращением заготовки; г – осциллирующая заготовка
Другим современным методом разрезки с применением абразивов является метод разрезки абразивной эластичной нитью – абразивной пилой (рис. 34). Этот метод применяется в очень сложных условиях – под водой или в космосе. Например, с помощью гибкой абразивной пилы была отрезана носовая часть затонувшей российской подводной лодки «Курск», а также в Мексиканском заливе 2010 году была разрезана американская нефтяная аварийная труба при ликвидации аварии на глубине 1500 м под водой.
Гидроабразивная резка. В настоящее время широкое распространение получила операция разрезки металлов с помощью высоконапорной
45

струи воды с примесью абразивного порошка (рис. 35). Генерируемое впроцессе резания тепло практически мгновенно уносится водой. В результатенепроисходитзаметногоповышениятемпературывзаготовке.
Рис. 34. Общий вид разрезки металла абразивной гибкой нитью – пилой
Рис. 35. Схема работы установки для гидроабразивной резки
Эта характеристика является решающей при обработке особо чувствительных к нагреву материалов. Небольшие сила (1–100 Н) и температура (+60…+90 oС) в зоне резания исключают деформацию
46
заготовки, оплавление и пригорание материала в прилегающей зоне. Ни одна технология, кроме гидроабразивной резки, не может обеспечить отсутствие термического влияния на металл вблизи пропила. Кромки среза не требуют дополнительной обработки. Так как область термовлияния на кромках обработанных деталей отсутствует, гидроабразивная резка позволяет вырезать детали со сложными профилями без дополнительной обработки поверхности реза и достаточно высокой производительностью.
На одной установке можно резать самые разнообразные материалы. Жидкостно-абразивная струя особенно эффективна при обработке многих труднообрабатываемых материалов, таких как, например, титановые сплавы, различные виды высокопрочных керамик и сталей, а также композитных материалов сверхтвердых материалов (высокопрочные сплавы, стекло, керамика, углепластики и другие композитные материалы). При гидроабразивной резке последних не создается разрывов в структуре материала, который таким образом сохраняет свои первоначальные свойства и т.п. С высокой скоростью можно резать самые разнообразные сэндвич-конструкции, так называемые «сэндвичи», которые иными способами не режутся в принципе; можно обрабатывать большие детали сразу «под размер», с высокой точностью, что исключает необходимость последующей мехобработки; можно получать финишную поверхность с шероховатостью Ra = 0,5…1,5 мкм, т.е. во многих случаях отпадает необходимость в дополнительной обработке.
Резка может осуществляться в любых направлениях, по линии любой кривизны и сложности. При обработке можно воспроизводить очень сложные формы или скосы под любым углом.
Струя жидкости по своим техническим возможностям приближается к идеальному точечному инструменту, что позволяет обрабатывать сложный профиль с любым радиусом закругления, поскольку ширина реза составляет 0,18–3,0 мм. При резании хрупкого материала (стекла) гидроабразивная обработка позволяет создавать неповторимые другими технологиями формы и контуры. Водоструйная технология не уступает алмазной резке, когда делаются прямые резы
47
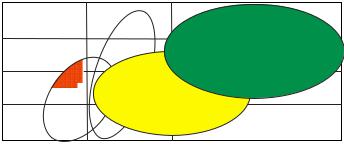
стекла, и тем более никакая другая технология не позволяет получать такие сложные контуры непосредственно в процессе резания.
За ходом резки следит точное цифровое программное управление Aliko (ЧПУ/CNC), разработанное фирмой ALIKO. Используемую программу автоматизированного проектирования/производства можно интегрировать с разнообразным программным обеспечением. Станок X-Y ALIKO управляется с помощью интерфейса ALIX на базе Windows. ALIX обладает большим числом функций, упрощающих его использование, таких как задний ход, точная настройка скорости резки и имитация резки. Все важные параметры для резки можно сохранить в специальной библиотеке для последующего использования. Отдельный режущий блок легко подключить к локальной сети предприятия.
Толщина материала, мм
300 |
|
|
150 |
Вода |
Газ |
|
||
|
|
|
20 |
|
|
|
|
Плазма |
1 |
|
Plasma |
Лазер |
|
|
|
|
0,1 1,8 Точность, мм
Рис. 36. Сравнение различных видов разрезки заготовок по точности
По точности реза гидроабразивная резка уступает только лазерной резке, но превосходит плазменную и газовую резку (рис. 36).
1.2.13. Притирка, доводка
Притирка, или доводка, – чистовая, отделочная обработка деталей с целью получения точных размеров (1-й класс и выше) и чистой поверхности, соответствующей Rа<0,1 мкм. Опиливания, зачистки
48
и шабрения поверхностей зачастую бывает недостаточно, чтобы достигнуть достаточно плотного прилегания деталей друг к другу. Поэтому в процессе сборки механизмов слесари прибегают к притирке (доводке) поверхностей с использованием абразивных порошков
ипаст. В процессе притирки деталям сообщается наиболее точный размер за счет снятия очень малого припуска (от 0,01 до 0,05 мм). Поверхность под притирку должна быть тщательно подготовлена. Детали притирают с точностью до 0,001–0,002 мм. Притиркой можно достичь такого плотного прилегания поверхностей, что соединение будет гидронепроницаемым.
Притирку можно производить двумя способами: одной деталью о другую (так притирают в основном криволинейные прилегающие друг к другу поверхности – клапаны, пробки и пр.) или деталью о притир (так доводят фланцы, крышки и пр.). В качестве притиров используются плиты, бруски или другие детали, сделанные из более мягкого материала, чем сами притираемые элементы (например, для притирки стальных деталей используются чугунные притиры, для притирки деталей из цветных металлов – стеклянные притиры). Для достижения высокой точности размеров детали и малой шероховатости ее поверхности применяется обработка с использованием мелкозернистых шлифпорошков, микропорошков и паст. Различают следующие виды притирки: грубая – с применением шлифпорошков зернистостью 28–63, при которой обеспечивается шероховатость обработанной поверхности Ra = 0,80…0,40 мкм; предварительная – с применением микропорошков зернистостью 10–28 для достижения шероховатости обработанной поверхности Rа = 0,2…0,1 мкм; окончательная – для достижения шероховатости обработанной поверхности Rа<0,1 мкм. Применяемые для притирки пасты состоят из абразивных порошков и химически активных веществ, которые ускоряют процесс притирки, образуя на обрабатываемой поверхности мягкую пленку, легко удаляемую абразивными зернами. Притирку наружных
ивнутренних поверхностей выполняют притиром, состоящим из двух и более частей (рис. 37), который устанавливают в державку, обеспечивающую прижим его к обрабатываемой поверхности.
49

Рис. 37. Обработка притирами: а – наружной поверхности: 1 – деталь, 2 – втулкапритир, 3 – жимок, 4 – гайка для затяжки притира; б – внутренней поверхности:
1 – конусная оправка, 2 – притир, 3 – деталь
Притиры изготовляют из закаленной стали, чугуна, латуни и меди. Рабочую поверхность притира покрывают ровным слоем шлифпорошка (с машинным маслом) или пасты. В процессе обработки притир плавно перемещают вдоль вращающейся детали. При этом между притиром и деталью создается небольшой натяг. Если материал притира мягче обрабатываемого материала, то абразивные зерна внедряются в поверхность притира, т.е. происходит шаржирование поверхности; такие притиры лучше обрабатывают поверхность при меньшем расходе шлифпорошка и пасты. Для охлаждения обрабатываемую поверхность смазывают жидким машинным маслом или керосином. Припуск на притирку 0,02–0,005 мм на диаметр. Окружная скорость детали при притирке 10–30 м/мин. Для получения повышенной точности обработки окружную скорость снижают до 5– 6 м/мин, чтобы избежать перегрева детали и искажения ее формы.
Деталь перед притиркой должна иметь шероховатость поверхности Ra = 0,8…0,4 мкм. При чистовой обработке рабочий диаметр притира не должен отличаться от диаметра обрабатываемой поверхности детали более чем на 0,02–0,05 мм. Притирка, как и шабрение, осуществляется в два этапа: предварительная притирка (предназначенные для этого притиры имеют на своей поверхности канавки, ку-
50