
Выбор абразивных инструментов и режимов резания для высокоэффективно
..pdf5.6.Выбор зернистости абразивного инструмента
взависимости от вида обработки
При выборе инструмента для операции абразивной обработки существенное значение имеет его зернистость. Зернистость выбирается в зависимости от следующих факторов:
1)количества снимаемого при обработке материала;
2)требуемого класса шероховатости и точности обработки поверхности;
3)физических свойств обрабатываемого материала;
4)требуемой в автоматическом цикле шлифования стойкости кругов между правками.
Крупнозернистые инструменты применяются:
при обдирочных и предварительных операциях с большой глубиной резания, когда удаляются большие припуски;
при работе на станках большой мощности и жесткости;
при обработке материалов, которые вызывают заполнение пор круга и засаливание его поверхности, например, при обработке латуни, меди, алюминия;
при большой площади контакта круга с обрабатываемой деталью, например при использовании высоких кругов, при плоском шлифовании торцом круга, при внутреннем шлифовании.
Средне- и мелкозернистые инструменты применяются:
для получения шероховатости Ra = 0,32…0,03;
при обработке закаленных сталей и твердых сплавов;
при окончательном шлифовании, заточке и доводке инструментов;
при высоких требованиях к точности обрабатываемого профиля детали.
Рекомендации по выбору зернистости абразивных инструментов для различных видов обработки приведены в табл. 30.
С уменьшением размера абразивных зерен повышается их режущая способность за счет возрастания числа зерен на единице рабочей поверхности, уменьшения радиусов округления зерен, меньшего износа отдельных зерен. Однако уменьшение размера зерен приводит
161
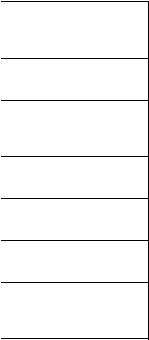
к значительному уменьшению пор круга, что вызывает необходимость снижения глубины шлифования и величины снимаемого на операции припуска. Чем мельче абразивные зерна в инструменте, тем меньше в единицу времени снимается материала с обрабатываемой детали.
Таблица 3 0
Зернистость абразивных инструментов для различных видов обработки
№ п/п |
Вид обработки |
Зернистость инструмента |
|
|
FEPA (ГОСТ) |
1 |
Обдирочные операции: зачистка заготовок, от- |
F22–F10 (80–320) |
|
ливок, поковок, штамповочных деталей |
F36–F22 (50–80) |
2 |
Плоское шлифование торцом круга, заточка |
|
|
средних и крупных резцов, правка абразивного |
|
|
инструмента, отрезка |
F46–F36 (40–50) |
3 |
Предварительное и комбинированное шлифова- |
|
|
ние (предварительное и окончательное шлифо- |
|
|
вание выполняется без съема изделия со стан- |
|
|
ка), заточка режущего инструмента |
F90–F46 (16–40) |
4 |
Чистовое шлифование, обработка профильных |
|
|
поверхностей, заточка мелкого инструмента, |
|
|
шлифование хрупких материалов |
F180–F100 (6–12) |
5 |
Отделочноешлифование, доводкатвердыхспла- |
|
|
вов, доводкарежущегоинструмента, предвари- |
|
|
тельноехонингование, заточкатонкихлезвий |
F220–F180 (4–6) |
6 |
Отделочное шлифование металлов, стекла, |
|
|
мрамора и т.п., резьбошлифование, чистовое |
|
|
шлифование |
F230(М50) и мельче |
7 |
Суперфиниширование, окончательное хонинго- |
|
|
вание, доводка тонких лезвий и мерительных |
|
|
поверхностей калибров, резьбошлифование |
|
|
изделий с мелким шагом |
|
В настоящее время все более широкое применение находят абразивные инструменты так называемых промежуточных (F70, F54) зернистостей. Применение шлифкругов зернистостью F54, вместо шлифкругов зернистостью F46, позволяет повысить стойкость круга до 60 % и снизить шероховатость поверхности. Таким образом, рациональное сочетание режима обработки, правки инструмента и его зернистости позволяет получать высокие точность и качество обработки поверхности, разную стойкость кругов между правками.
162
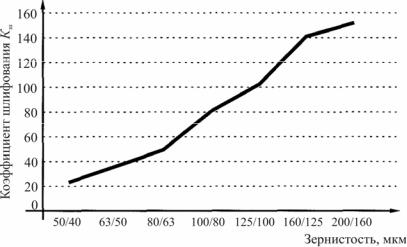
Выбор зернистости алмазных инструментов. Одним из глав-
ных условий абразивной обработки является обеспечение требуемой шероховатости, точности и производительности. Эти условия обеспечиваются правильным подбором зернистости алмазных порошков. Крупные зерна алмазов обеспечивают более высокую режущую способность, т. е. повышается коэффициент шлифования Кш (рис. 72), однако при этом увеличивается и шероховатость обработанной поверхности.
Рис. 72. Влияние зернистости алмазных зерен на коэффициент шлифования (плоское шлифование, органическая связка)
Увеличение зернистости алмазного порошка позволяет повысить производительность процесса обработки. Поэтому для повышения производительности и повышения стойкости кругов следует применять наибольшую зернистость, которая обеспечивает требуемую шероховатость обрабатываемой поверхности. На рис. 73 показано, что чем крупнее зерно, тем больше риски на поверхности.
Рекомендации по выбору зернистости алмазных порошков для различных видов шлифования по отечественным и зарубежным стандартам приведены в табл. 31.
163
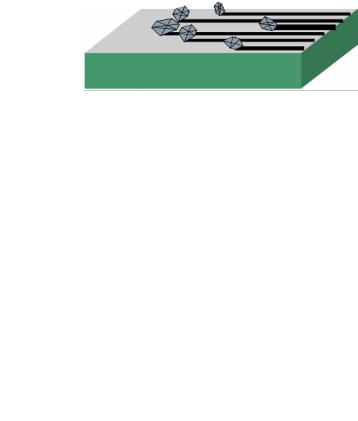
Рис. 73. Влияние зернистости абразивных зерен на высоту микронеровностей при шлифовании
Таблица 3 1
Соответствие зернистости алмазных порошков по ДСТУ 3292–95 зарубежным стандартам и их применение по видам обработки
Вид обработки |
Стандарт Украины |
Международ- |
Стандарт США |
Обозначение |
|
ДСТУ 3292–95, |
ный стандарт |
ANSI В 74-16, |
по FЕРА |
||
|
мкм |
1SО 565, мкм |
меш |
|
|
Черновое |
250/200 |
250/212 |
60/70 |
D 251 |
|
200/160 |
212/180 |
70/80 |
D 213 |
||
шлифование |
|||||
160/125 |
180/150 |
80/100 |
D 181 |
||
|
|||||
Чистовое |
|
150/125 |
100/120 |
D 151 |
|
125/100 |
125/106 |
120/140 |
D126 |
||
шлифование |
|||||
100/80 |
106/90 |
140/170 |
D 107 |
||
|
|||||
Тонкое |
80/63 |
90/75 |
170/200 |
D 91 |
|
шлифование |
|
75/63 |
200/230 |
D 76 |
|
|
63/50 |
63/53 |
230/270 |
D 64 |
|
|
50/40 |
53/45 |
270/325 |
D54 |
|
|
|
45/38 |
325/400 |
D46 |
|
Тонкое |
60/40 |
|
500 |
М 63 |
|
шлифование, |
40/28 |
|
550 |
М 40 |
|
полирование |
28/20 |
|
650 |
М 25 |
|
|
20/14 |
– |
1100 |
М 16 |
|
|
14/10 |
|
1500 |
М 16 |
|
|
10/7 |
|
1700 |
М 10 |
|
|
7/5 |
|
3000 |
М 6.3 |
|
|
5/3 |
|
4000 |
М 4.0 |
Рекомендации по выбору зернистости алмазных кругов при шлифовании и заточке твердосплавных инструментов и изделий в зависимости от вида шлифования и применяемой связки для обеспечения требуемой шероховатости обработанной поверхности приведены в табл. 32.
164
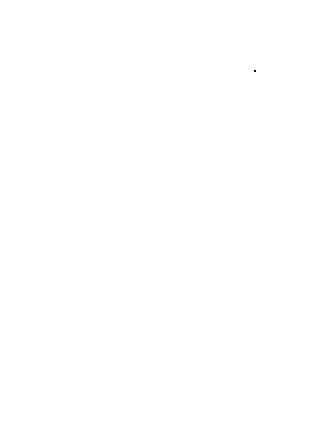
Зернистость кубического нитрида бора в кругах на керамической связке выбирается исходя из требований, предъявляемых к чистоте обрабатываемой поверхности, и находится, как правило, в интервале 200/160– 50/40 мкми125/100–20/14 мкмдлярезьбошлифовальныхкругов.
Таблица 3 2
Выбор зернистости алмазного круга при шлифовании и заточке твердосплавных инструментов и изделий
Типы и марки связок |
Рекомендуемый |
Шероховатость обработанной поверхно- |
||||
|
|
диапазон зерни- |
|
сти Ra, мкм |
|
|
|
|
стостей |
при торцевом |
приплоском |
при круг- |
|
|
|
|
шлифовании |
шлифовании |
лом шли- |
|
|
|
|
и заточке |
периферией |
фовании |
|
|
|
|
|
круга |
|
|
|
|
Органические связки |
|
|
|
|
Органические |
200/160–100/80 |
0,63–0,16 |
1,0–0,32 |
1,0–0,32 |
||
В1-01, В1-04, |
80/63–50/40 |
0,32–0,16 |
0,63–0,20 |
0,63–0,20 |
||
В1-13, В1-02 |
|
|
|
|
|
|
Органические (алмазы |
|
|
|
|
|
|
с покрытием) В2-01, |
125/100–50/40 |
0,32–0,10 |
0,63–0,16 |
0,80–0,20 |
||
В1-04, В1-13, В1-01 |
|
|
|
|
|
|
Органические (алмазы |
|
|
|
|
|
|
с покрытием) В2-01, |
125/100–20/14 |
0,32–0,05 |
0,50–0,10 |
0,63–0,125 |
||
В1-13, В1-02, В1-01 |
|
|
|
|
|
|
|
|
Металлические связки |
|
|
|
|
Металлические повы- |
|
200/160–125/100 |
1,0–0,32 |
1,25–0,63 |
1,25–0,63 |
|
шенной производи- |
|
100/80–80/63 |
0,50–0,16 |
1,0–0,32 |
1,25–0,40 |
|
тельности М2-01, М3- |
|
63/50–50/40 |
0,32–0,16 |
0,63–0,16 |
0,63–0,32 |
|
04, М-300 |
|
|
|
|
|
|
Металлические |
250/200–125/100 |
1,0–0,32 |
1,25–0,63 |
1,25–0,63 |
||
повышенной стойкости |
100/80–80/63 |
0,50–0,16 |
1,0–0,32 |
1,25–0,40 |
||
М2-01, М1-01, М3-04, |
63/50–50/40 |
0,32–0,16 |
0,63–0,16 |
0,63–0,32 |
|
|
М2-30, М3-08, М-300 |
|
|
|
|
|
|
Связ |
ки для электролитического шлифования |
|
|
|||
Металлические повы- |
200/160–125/100 |
1,25–0,32 |
2,0–0,63 |
2,0–0,63 |
||
шенной производи- |
100/80–80/63 |
0,63–0,20 |
1,25–0,63 |
1,25–0,63 |
|
|
тельности М1-01 |
|
|
|
|
|
|
Металлические повы- |
200/160–125/100 |
1,25–0,32 |
2,0–0,63 |
2,0–0,63 |
||
шенной стойкости |
100/80–80/63 |
0,63–0,20 |
1,25–0,63 |
1,25–0,63 |
|
|
М2-01, М1-01, М3-08 |
|
|||||
|
|
|
|
|
||
Органические В1-13, |
160/125–100/80 |
0,50–0,1 |
0,63–0,16 |
0,63–0,16 |
||
В1-11П, В1-01 |
80/63–50/40 |
0,16–0,05 |
0,32–0,08 |
0,32–0,08 |
|
165
5.7. Выбор формы и размеров абразивных инструментов
Форма и размеры абразивных инструментов определяются в зависимости от конструкции и назначения станка, его размеров, конструкции крепежного приспособления, формы и размеров обрабатываемых деталей, а также площади контакта инструмента с обрабатываемыми поверхностями деталей.
Как пример, можно привести типы абразивного инструмента для различных видов абразивной обработки.
Обдирочное шлифование – снятие больших припусков крупнозернистыми кругами прямого профиля типа 1 (ПП), реже 5 и 36 (ПВ, ПР и ПН), а также чашечными кругами типа 11(ЧК).
Отрезка (разрезка, резка) – разрезание материала кругами типа 41 и 42. Абразивная резка является в настоящее время самым производительным видом среди других видов резания.
Круглое шлифование – процесс шлифования детали во время ее вращения в центрах или в патроне, кругами типа 1, 5, 7, 23 и др. (ПП, ПВ, ПВК и ПВДК).
Бесцентровое шлифование. Отличается от центрового тем, что обрабатываемые детали получают вращение и шлифуются без крепления в центрах, причем базой является обрабатываемая поверхность. При круглом бесцентровом шлифовании оба круга вращаются в одну сторону с разными скоростями, рабочий круг – со скоростью 30–35 м/с, ведущий – со скоростью, в 60–100 раз меньшей. Опорой для шлифуемой детали является нож со скошенным краем, находящийся между рабочим и ведущими кругами. Нож устанавливается так, чтобы центр детали находился выше или ниже центров кругов. Типы используемых кругов – 1,7 (ПП и ПВД).
Внутреннее шлифование – шлифование отверстий цилиндрической и конической формы. В зависимости от конструкции детали и станка шлифование осуществляется при вращении детали или при неподвижном состоянии. Шлифовальный круг при обработке вращается не только вокруг своей оси со скоростью 20–35 м/с, но и вокруг оси обрабатываемого отверстия с круговой подачей 20–30 м/мин. Типы абразивного инструмента – 1, 5(ПП и ПВ), а также головки различных видов.
166
Плоское шлифование – шлифование плоскостей осуществляется периферией или торцом круга, используются круги типа 1, 2, 7, 6, 11, 36 (ПП, ПВ, ПВД, 1К, ЧК, ЧЦ и ПН), сегменты СП, 1C, 2С, 3С, 4С, 5С, 6С и 8С.
Заточка и доводка режущего инструмента. От заточки и до-
водки режущих инструментов зависят производительность и стоимость обработки деталей, стойкость и расход инструментов. В операции заточки и доводки используются самые разнообразные типы абразивного инструмента – 1,2,3,4,6,7,11,12 и т.д.
Резьбошлифование – шлифование резьбы различных профилей (треугольные, трапециевидные и др.) и шага метчиков, резьбовых калибров, накатных роликов, ходовых винтов металлорежущих станков и измерительных приборов. Используются круги типа 1 и4 (ПП и2П).
Зубошлифование – шлифование зубчатых колес всех видов. Ти-
пы кругов –1, 3,4,14(ПП, 2П, 3Т и 4П).
Шлицешлифование – шлифование шлицев различного профиля: прямоугольных, эвольвентных, трапециевидных и треугольных. Типы – 1,12 (ПП, Т), необходимый профиль придается кругу непосредственно на станке.
Хонингование – процесс доводки абразивными брусками отверстий с шероховатостью Ra = 0,3…0,080 и точности до второго класса. Типы брусков – БК, БХ.
Суперфиниширование – шлифование при малом съеме металла (10–12 мкм на диаметр), для достижения шероховатости Ra = = 0,16…0,02 мкм. Процесс осуществляется при малых окружных скоростях изделия (8–40 м/мин), малых давлениях мелкозернистых брусков (1,5–3 кгс/см2) при их колебательном движении с частотой от 500–600 до 2000–3000 дв. ход/мин с амплитудой 2–5 мм. При суперфинишировании полностью удаляется волнистость, уменьшается огранка, удаляется дефектный поверхностный слой металла. После суперфиниширования формируется упрочненный поверхностный слой без структурных изменений, что улучшает эксплуатационные свойства деталей, работающих в условиях трения, скольжения или качения. Рабочим инструментом является абразивная головка с 1–4 абразивными брусками.
167
Как следует из вышеприведенных данных, наиболее просты по форме и универсальны по применению круги типа 1 (ПП), которые используются для большинства операций.
Тонкие круги – диски типа 41 (Д) – применяются для прорезных работ, шлифования пазов и отрезки материалов.
Круги с выточками представляют собой разновидность кругов типа 1. Выточки предназначены для более прочного крепления во фланцах и лучшего доступа круга к шлифуемому месту. Конические выточки у кругов типов 23,26 (ПВК и ПВДК) помогают также уменьшить площадь соприкосновения боковой поверхности круга с буртиками и фланцами изделий, обрабатываемых на круглошлифовальном станке. Если в уменьшении площади соприкосновения нет необходимости, то для тех же работ применяют круги типов 5 и 7(ПВ
иПВД). Круги типа 5 применяют также для внутреннего шлифования в случае, когда надо подрезать донышко изделия или доработать «в упор».
Круги типов 36, 40 (ПНР и ПН) предназначены для обдирочного
иреже для чистового шлифования. Круги типа 1 (ПР) имеют рифленую рабочую поверхность, и поэтому их применение предпочтительнее там, где существует опасность чрезмерного нагрева обрабатываемого изделия.
Круги типа 4 (2П и 4П) приспособлены главным образом для заточки многорезцовых инструментов, шлифования зубьев шестерен. Круги – кольца типа 2(К), применяемые для плоского шлифования, крепятся в чашечной планшайбе станка каким-либо цементирующим или клеящим веществом. Круги типа ЧЦ используют при заточке инструментов, при плоском шлифовании, иногда – при обработке отверстий, особенно несквозных. В последнем случае применяют круги с более толстыми стенками.
Круги типа 11(ЧК) рекомендуется использовать для заточки инструментов и плоского шлифования, например направляющих станин станков, когда из-за резкого ограничения свободного пространства над обрабатываемой поверхностью нельзя использовать инструменты других форм.
168
Круги-тарелки типов 12–14 (1Т–4Т) применяют в случае еще более резкого ограничения свободного пространства вокруг шлифуемой поверхности. Для заточки и доводки передних граней деталей, например зубьев фрез, лучше использовать круги типа 12(Т), для заточки червячных фрез – круги типа14 (2Т), для обработки зубьев долбяков и зубьев шестерен – круги типа 14 (3Т).
Абразивный инструмент других форм, например сегменты, головки, бруски, предназначены для работы на станках специального назначения.
Сегменты крепятся в патроне и образуют круг с прерывистой кольцевой поверхностью, работающий торцом при плоском шлифовании. Различная форма сегментов обусловлена конструкцией патронов станка. Сегментный круг по сравнению с кольцевым (типа 2) дает некоторое снижение шероховатости поверхности, но позволяет работать с более интенсивными режимами.
Шлифовальные головки сначала крепятся на металлической оправке с помощью клеящего вещества, а затем в патроне, получающем вращение от гибкого вала. С их помощью выполняются операции обработки штампов, матриц, пресс-форм, зачистки отливок, сварных конструкций. Головки типа ГП иногда применяются для внутреннего шлифования.
Для машинной работы (хонингование и суперфиниширование) используют бруски типов БКв, БП, БХ. Остальные типы брусков применяются для ручной работы.
При обработке отверстий диаметр круга Dкр выбирается в зависимости от диаметра отверстия dотв: Dкp = (0,5...0,9)dотв.
Такое соотношение позволяет применять круги оптимальных размеров и создать наиболее рациональный режим шлифования.
Применение кругов различных диаметров и высот определяет эффективность единицы полезно используемого объема абразива и скоростью износа круга. Для малых кругов эти показатели всегда выше, так как нагрузку принимает меньшее количество абразивных зерен, в результате чего они быстрее изнашиваются. Возникает неравномерный износ круга, ухудшается шероховатость поверхности, возможно снижение производительности. Поэтому рекомендуется
169
использовать возможно большие по диаметру и высоте круги, это позволяет работать на жестких режимах. Однако отсутствие достаточного места для размещения более крупных кругов, недостаточная мощность и жесткость стакана, форма обрабатываемой детали (ступенчатые изделия, тонкие и т.п.) могут ограничивать размеры круга.
Выбор размеров шлифовального инструмента из СТМ. На-
ружный диаметр круга следует выбирать максимальным по размеру, с учетом возможностей оборудования, формы и размеров обрабатываемой детали. При этом также необходимо учитывать обеспечение оптимальной скорости обработки. Для внутреннего шлифования наружный диаметр кругов должен быть в пределах 0,4–0,9 диаметра обрабатываемого отверстия, причем, чем больше диаметр отверстия, тем меньше соотношение диаметров. С увеличением диаметра круга увеличивается количество зерен, участвующих в обработке, уменьшается толщина среза, приходящегося на одно зерно, возрастает продолжительность охлаждения зерна и связки, уменьшается длина дуги контакта зерна с обрабатываемой поверхностью. Все эти факторы оказывают положительные влияние на работоспособность инструмента из СТМ, снижается удельный расход СТМ (т.е. повышается стойкость кругов) и увеличивается производительность процесса обработки.
Ширина рабочего слоя круга В (обозначается Т – для кругов типа
1А1 и 14А1, 3А1; W – для 12А2-45º, 12А2-20º, 6А2, 9А3, 4А2, 12R4).
Размер В соответствует ширине контакта рабочего слоя круга с обрабатываемой поверхностью. При изменении ширины круга изменяется площадь контакта круга с деталью. Съем обрабатываемого материала при шлифовании происходит по поверхности контакта. Площадь контакта определяется в основном шириной круга и длиной контакта. Ширина круга должна выбираться в зависимости от размеров обрабатываемой поверхности, мощности и типа станка, условий обработки, наличия или отсутствия охлаждения.
С увеличением глубины шлифования или площади контакта с обрабатываемой поверхностью ширину рабочего слоя выбирают меньшей.
170