
Выбор абразивных инструментов и режимов резания для высокоэффективно
..pdfF46, степени твердости СМ2, номером структуры 7, на керамической связке К5ПГ, с рабочей скоростью 35 м/с, класс точности А, 1-го класса неуравновешенности.
Пример 2: 1 400×4×32 14А F30 41(S) БУ 80 м/с 2 кл.
ГОСТ 21963–82. Условное обозначение отрезного круга типа 1 наружным диаметром 400 мм, высотой 4 мм, диаметром посадочного отверстия 32 мм, из нормального электрокорунда марки 14А, зернистости F30, со звуковым индексом 41(S), на бакелитовой связке (Б), с упрочняющими элементами (У), с рабочей скоростью 80 м/с, 2-го класса неуравновешенности для резки металла.
В последнее время в маркировке кругов произошли изменения. Примечания:
1.Маркировка кругов диаметром 40 мм и менее наносится на коробку или упаковку.
2.Номер партии и класс неуравновешенности допускается наносить на обратной стороне круга.
3.Маркировку кругов типа 2, 6, 11, 12 и 14 и на кругах диаметром свыше 40 до 200 мм допускается наносить на периферии круга.
4.Маркасвязки ненаносится на кругах диаметром80 мми менее.
5.Размер круга, обозначение стандарта и номер партии не наносится на кругах диаметром 250 мм и менее.
6.Рабочая скорость не наносится на кругах диаметром менее
100 мм.
7.На кругах с рабочей скоростью более 50 м/с должны быть нанесены цветные полосы: желтая означает круги с рабочей скоростью 60 м/с, красная – 80 м/с, зеленая – 100 м/с, синяяи зеленая – 120 м/с.
8.На отрезных кругах также рекомендовано наносить буквенное обозначение, указывающее на то, какой материал рекомендуется разрезать этим кругом: М – металл; НМ – неметалл. На импортных отрезных кругах указывается словами разрезаемый материал: «металл», «сталь», «камень» и т.д.
Маркировка алмазных шлифовальных кругов производится сле-
дующим образом. Указывается форма, основные размеры круга и алмазоносного слоя (рис. 50), зернистость, связка, концентрация и ко-
91
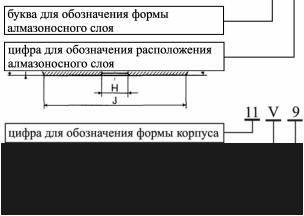
личество алмазов в круге (в каратах), а также наименование пред- приятия-изготовителя или его товарный знак, номер круга и год его изготовления.
Рис. 50. Обозначение и маркировка алмазных и эльборовых кругов
Например, в круге АЧК 150×10×3×32 с характеристикой АС2 10 Б1 2 29 №8-90 маркировка имеет следующие значения: АЧК – алмазный круг чашечный, конический; 150 – наружный диаметр круга, мм; 10 – зернистость алмазного порошка; Б1 – связка бакелитовая первая (с наполнителем из карбида бора); 2 – относительная концентрация алмазов в алмазоносном слое, % (цифрами 1, 2,..., 6 обозначается соответственно 25, 50, 75, 100, 125 и 150%-я концентрация); 29 – содержание алмазного порошка, карат; 8 – заводской номер круга; 90 – год изготовления круга.
Инструмент, изготовленный из эльбора, маркируется подобно алмазному. Например, маркировка ЛЧК 150×10×3×32 Л10 Б1 6 58 № 43-90 читается так: чашечный круг диаметром 150 мм с рабочим слоем высотой 10 мм и толщиной 3 мм, диаметр посадочного отверстия 32 мм, эльборовое зерно (Л), зернистость 10, связка Б1, концентрация 150 %, количество эльбора в круге 58 каратов; 43 – заводской номер круга; 90 – год изготовления круга. Концентрация 100 % в эльборовых кругах не указывается.
92
Согласно ГОСТ Р 52781–2007 (ИСО 525:1999, ИСО 603-1:1999, ИСО 603-6:1999, ИСО 13942:2000) с 01.01.2009 г. введена новая мар-
кировка кругов российских производителей абразивов. Эта маркировка соответствует международным стандартам по абразивам. Прежний ГОСТ 2424–83 с 2009 г. утратил силу. Согласно новому ГОСТ Р 52781–2007 в условных обозначениях кругов типов 2 и 37 указывают размеры D × T × W; кругов остальных типов – D × T × Н.
Пример 1: Круг 2 300×80×48 14А F54 L7 V50 м/с 2 кл.
ГОСТ Р 52781–2007. Условное обозначение круга типа 2 наружным диаметром D = 300 мм, высотой Т = 80 мм, шириной рабочей части W = 48 мм, из нормального электрокорунда марки 14А, зернистостью F54, твердостью L, номером структуры 7, на керамической связке V, с предельной рабочей скоростью 50 м/с, 2-го класса неуравновешенности.
Пример 2: Круг 1 300×20×76,2 25А F60 K6 V40 м/с 2 кл.
ГОСТ Р 52781–2007. Условное обозначение круга типа 1 наружным диаметром D = 300 мм, высотой Т = 20 мм, диаметром посадочного отверстия Н = 76,2 мм, из белого электрокорунда марки 25А, зернистостью F60, твердостью K, номером структуры 6, на керамической связке V, с предельной рабочей скоростью 40 м/с, 2-го класса неуравновешенности.
Вопросы для самопроверки
1.Что включает в себя понятие «характеристика абразивных инструментов»?
2.Назовите основные определения и виды абразивных инстру-
ментов.
3.Перечислите виды применяемых абразивных материалов.
4.Чем отличаются естественные абразивные материалы от искусственных абразивных материалов?
5.Назовите свойства и область применения сверхтвердых инструментальных материалов.
6.Как обозначаются условно абразивные материалы?
93
7.Что такое зернистость абразивных материалов?
8.Какие типы связок применяются для абразивных инструментов?
9.Что такое твердость абразивного инструмента?
10.Что называется структурой абразивных инструментов?
11.Назовите основные типы шлифовальных кругов.
12.Перечислите основные правила маркировки абразивного инструмента.
94
ГЛАВА 3. КРАТКИЕ СВЕДЕНИЯ О ТЕХНОЛОГИИ ИЗГОТОВЛЕНИЯ АБРАЗИВНОГО ИНСТРУМЕНТА
3.1. Изготовление абразивных инструментов на керамической связке
Керамические связки изготавливаются из смеси глин или каолина, полевого шпата и (или) пегматита, борного стекла, талька и других минеральных материалов. Все материалы, идущие на изготовление связок, измельчаются до крупности 40 мкм на специальном помольном оборудовании и гомогенизируются в смесителе (миксере) в определенном соотношении, с получением определенной огнеупорности и химического состава.
Далее приготавливается формовочная смесь, состоящая, в соответствии с рецептурой, из определенного количества абразивного зерна, связки, увлажнителя и (при необходимости) клеящей добавки. Смешивание производится в течение определенного времени в специальных смесительных машинах. Формовочная смесь после приготовления пропускается через грохот с нужными сетками для устранения комков, посторонних частиц и подается к формовочным агрегатам. Формование заготовок производится в специальных прессформах на формовочных агрегатах, созданных на базе гидравлических либо механических прессов. После дозировки, укладки и прессования заготовки кругов на металлических или асбоцементных плитах поступают на сушку. В ряде случаев формообразование производится методами вибропрессования, экструдирования или литья заготовок на специальном оборудовании.
Сушка заготовок производится в сушильных агрегатах периодического или непрерывного действия при t = 90…100 С. Допускается естественная сушка для заготовок малых размеров. После сушки заготовки устанавливаются на печные вагонетки и подаются в туннельные, щелевые или камерные печи, где производится окончательная термообработка заготовок при температуре 1220–1280 С. После
95
обжига практически весь абразивный инструмент подвергается механической обработке (наружный диаметр, отверстия и торцевые поверхности) на специальных станках. Далее производится калибровка, маркировка, контроль инструмента на соответствие норматив- но-технической документации и упаковка продукции.
3.2. Изготовление абразивных инструментов на бакелитовой связке
Составляющие абразивного инструмента на бакелитовой связке, а именно абразивный материал, фенолформальдегидная смола
вжидком (бакелит) и порошкообразном виде (пульвербакелит) с наполнителями (криолит, гипс, пирит, антимонит и др.) дозируются в определенном рецептом соотношении и порядке в смеситель. В ряде случаев жидкий бакелит заменяется на другие увлажнители, в частности, фурфурол. Приготовление формовочной смеси производится
вспециальных смесителях (чаще двухстадийных). Приготовленная смесь протирается через сито протирочной машины. В ряде случаев для придания постоянных по времени свойств смесь «вылеживается»
втечение нескольких часов при комнатной температуре (операция «старение массы»), затем вновь пропускается через сито. Прессование заготовок производится в специальных пресс-формах на формовочных агрегатах (в основном, на базе гидравлических прессов). Дозирование и укладка формовочной смеси в пресс-форму производят-
ся вручную или механически. Прессование производится при высоких удельных давлениях – от 200 до 500 кгс/см2. При прессовании армированных стеклосеткой кругов укладка массы производится послойно с перекладкой дисками из стеклосетки (марки СПАП – БЖ, М и др.). Количество дисков в кругах зависит от толщины и диаметра кругов и может составлять от 1–3 (в отрезных кругах) до 6–10 (в обдирочных кругах). При изготовлении обдирочных кругов для упрочнения используются металлические кольца – от 1 до 3 шт. в круге.
Термообработка (бакелизация) заготовок производится в камерных или туннельных печах, имеющих специальное название – бакелизаторы.
Время термообработки от 6 до 36 ч. Конечная температура 180–200 С. После термообработки, при необходимости, абразивный инструмент подвергается механической обработке (наружный диаметр, отверстия
96
и торцевые поверхности) на специальных станках. Далее производится калибровка, маркировка, контроль инструмента на соответствие норма- тивно-техническойдокументациииупаковкапродукции.
3.3. Изготовление абразивных инструментов на вулканитовой и глифталевой связке
Вулканитовые связки – это многокомпонентные композиции на основе синтетических каучуков. В состав входят: вулканизирующий агент-сера, органические ускорители и вулканизаторы (каптакс, тиурам и др.), наполнители (окислы металлов, соли, синтетические смолы и т.д.), мягчители. Связка и формовочная смесь готовится на специальном смесительном оборудовании: вальцах или смесительных машинах (аналоги применяемых в резиновой промышленности). Изготовление связки представляет собой процесс смешивания каучука с другими компонентами до однородного состояния.
Формование заготовок кругов производится двумя способами:
1)прокаткой массы на вальцах и вырубкой заготовок;
2)прессованием кругов в пресс-формах из сыпучей порошкообразной смеси, приготовленной в смесительных машинах и разрыхленной в специальных рыхлителях типа дезинтегратора. Заготовки кругов подвергаются термообработке (вулканизации) в течение 6–16 ч, ко-
нечная температура 160–180 С в камерных или туннельных вулканизаторах. После вулканизации круги подвергаются механической обработке. Далее производится калибровка, маркировка, контроль инструмента на соответствие нормативно-технической документации и упаковка продукции.
Глифталевая связка – это продукт взаимодействия глицерина с фталевым ангидридом (порошкообразной формы) и увлажнитель – жидкий бакелит. Технология изготовления инструмента аналогична технологии изготовления на бакелитовой связке.
3.4. Инструменты на основе вспененного поливинилформаля (поропластовые)
Процесс изготовления заключается в механическом вспенивании композиции, состоящей из водного раствора поливинилового спирта, абразивного зерна, формалина, а также кислого катализатора, вспени-
97
вающих агентов и других добавок в мешалках особой конструкции. Вспененная масса разливается в формы. Термообработка осуществляется при температуре 50–80 оС в течение 5–8 ч. Отвердевшие в результате термообработки заготовки отмываются от непрореагировавших продуктов реакции в специальных отжимных прессах с проточной водой, отжимаются и сушатся до постоянного веса. Затем изделия подвергают резке и механической обработке. Далее производятся калибровка, маркировка, контроль инструмента на соответствие нормативно-техничес- койдокументациииупаковка продукции.
3.5. Краткая технология производства шлифовальной шкурки
Методы нанесения абразивного материала делятся на гравитационный, электростатический, суспензионный.
Гравитационный метод – абразив наносится под действием гравитации простой насыпкой или под действием силы электромагнитного притяжения.
Электростатический метод – абразивный материал наносится в электростатическом поле, которое ориентирует шлифзерно перпендикулярно к поверхности основы и внедряет их в связующее.
Гравитационный + электростатический метод нанесения абра-
зива – комбинация вышеописанных методов.
Суспензионный метод – на основу наносится взвешенная смесь связующей смолы или лака с абразивом. Используется только для изготовления шлифшкурки на основе микропорошков.
Поверхность готовой шлифшкурки может обрабатываться стеаратом цинка или стеаратом кальция, рекомендуется для обработки грунтованных поверхностей мебели, кузовов автомобилей, удаления лака с деревянных поверхностей. Это снижает контактную температуру в зоне обработки, увеличивает ресурс шлифшкурки, снижает вероятность прижогов обрабатываемой детали.
Поверхность шлифшкурки может покрываться специальными антистатиками. Это дополнительное покрытие шлифшкурки устраняет статическое электричество, способствует удалению стружки из зоны обработки, предотвращает забивание поверхности шлифшкурки. Чаще всего используется в деревообработке.
98
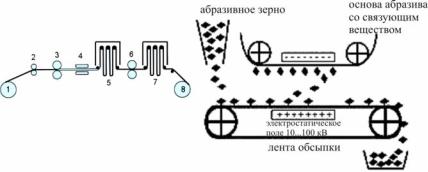
Производство шлифшкурки осуществляется на поточных автоматизированных линиях (рис. 51). Рулон бумаги или аппретированной ткани устанавливается на размоточное устройство (1). Основа проходит через маркировочную машину, где производится нанесение маркировки на нерабочую сторону полотна (2). Далее основа проходит через двухвалковый клеенаносящий механизм (3). Толщина клеевого слоя, наносимого на рабочую поверхность полотна, регулируется изменением зазора между валками. Далее полотно проходит через устройство нанесения шлифзерна (4). В зависимости от зернистости шкурки, линия оборудуется устройством нанесения шлифзерна, действующим по гравитационному или электростатическому принципу. После нанесения шлифзерно вдавливается в клей стальными валками. Плохо закрепленное зерно удаляется с основы отбойниками. Далее основа с абразивным зерном следует в гирляндное сушило (5), после чего поступает во второй клеенаносящий механизм (6), где производится нанесение закрепляющего клеевого слоя. Окончательная сушка шкурки производится во втором гирляндном сушиле (7). Из сушильной камеры полотно поступает на намоточныйстанок(8).
Производственная линия принимает полотно шириной до 1,5 м. Готовая шлифшкурка может быть разрезана так, как это удобно для дальнейшей технологической переработки, или на продольные ленты и полосы.
Рис. 51. Схема и принцип действия электростатической установки по изготовлению шлифовальной шкурки
99
Товарные рулоны шлифшкурки имеют длину от 20 до 50 м и ширину 700–1200 мм. Далее часть шлифшкурки передается для изготовления различных изделий. Шлифовальные бобины получают разрезкой шлифшкурки на бобинорезательной установке. Бесконечные шлифленты получают склейкой концов шлифленты, полученной на бобинорезке. При этом склеиваемые концы предварительно раскраивают и шлифуют (под углом 45 или др.). Прочность клеевого шва контролируется.
Лепестковые круги изготавливаются следующим образом: из шлифшкурки на штампах вырубают заготовки требуемого размера, которые закладываются (набираются) в формы для набора кругов (кондукторы). После чего центральная часть заготовки заполняется эпоксидной смолой с отвердителем и наполнителями. Заготовка лепесткового круга сушится в форме 4 ч при температуре 80–100 С в термошкафу. Затем круг проверяется, маркируется и упаковывается. Помимо скрепляющей центральной части из эпоксидной смолы зачастую, по бокам круга, устанавливаются после заливки смолой металлические скрепляющие фланцы. Листы, диски, полосы различных форм и размеров изготавливаются, в основном, методом вырубки на специальных прессах или других вырубных устройствах. Существуют также методы лазерного раскроя изделий.
Вопросы для самопроверки
1.Назовите особенности изготовления абразивных инструментов на керамической связке.
2.Назовите особенности изготовления абразивных инструментов на бакелитовой связке.
3.Назовите особенности изготовления абразивных инструментов на вулканитовой и глифталевой связках.
4.Назовите особенности изготовления абразивных инструментов на основе вспененного поливинилформаля (поропластовые).
5.Какова технология производства шлифовальной шкурки?
100