
Выбор абразивных инструментов и режимов резания для высокоэффективно
..pdfДанным способом обрабатываются гладкие цилиндрические поверхности простых деталей-штифтов, пальцев, роликов, штоков, подшипниковых колец в крупносерийном и массовом производстве. При обработке ступенчатых деталей небольшой длины применяют врезное бесцентровое шлифование – цапфы крестовин, стержни клапанов, сферические пальцы и др.
1.2.5. Глубинное шлифование
Глубинное шлифование обеспечивает большую глубину резания и малую продольную подачу детали. По скорости съема металла этот метод часто превосходит другие методы абразивной и лезвийной обработки, но сохраняет при этом все преимущества шлифования: высокую геометрическую точность, малую шероховатость и т.д. Величина слоя металла, удаляемого при глубинном шлифовании за один проход, достигает 5–10 мм, а величина продольной подачи детали изменяется от 50 до 2000 мм/мин и более и зависит от типа обрабатываемого материала, глубины резания, характеристики абразивного инструмента, вида СОЖ и способа ее подачи, требований к качеству обрабатываемых поверхностей. При увеличении глубины резания в контакте с заготовкой участвует большее число зерен, чем при маятниковом шлифовании, поэтому нагрузка на единичное режущее зерно уменьшается, а производительность, т.е. режущая способность, увеличивается.
Наибольшее применение этот метод нашел при обработке различных профильных поверхностей лопаток газотурбинных двигателей и жаропрочных литейных сплавов на никелевой основе (рис. 17– 19). На ОАО «Пермский моторный завод» на станках фирмы «ЭлбШлифф» обрабатываются различные профильные замковые поверхности более 90 деталей ГТД. Кроме того, на предприятии установлены универсальные станки с ЧПУ для глубинного шлифования (модели ЛШ-220 и ЛШ-233 Липецкого станкозавода). Специальные шлифовальные станки имеют более высокую жесткость, мощность и точность, чем универсальные станки. Они оснащены многокоординатными системами ЧПУ, а также рядом систем и устройств, стабилизирующих технологический процесс. К ним относятся системы
31
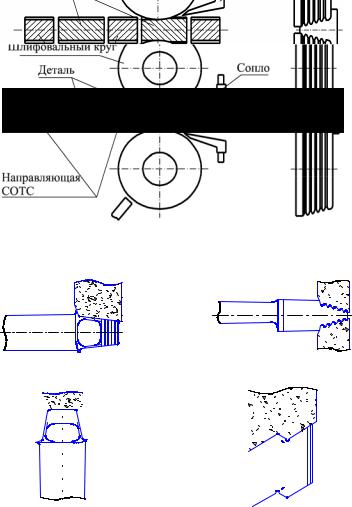
высоконапорной подачи СОЖ, охлаждения и очистки СОЖ, автоматического поддержания постоянной скорости резания, динамической балансировки и автоматической правки кругов и т.д.
Рис. 17. Схема обработки елочного хвостовика лопатки на станке SS13
|
|
|
а |
|
|
|
|
|
|
|
б |
|||
|
|
|
|
|
|
|
|
|
|
|
|
|
|
|
|
|
|
|
|
|
|
|
|
|
|
|
|
|
|
|
|
|
|
|
|
|
|
|
|
|
|
|
|
|
|
|
|
|
|
|
|
|
|
|
|
|
|
|
|
|
|
|
|
|
|
|
|
|
|
|
|
|
|
|
|
|
|
|
|
|
|
|
|
|
|
|
|
|
|
|
|
|
|
|
|
|
|
|
|
|
|
|
|
|
|
|
|
|
|
|
|
|
|
|
|
|
|
|
|
|
|
|
|
|
|
|
|
|
|
|
|
|
|
|
|
|
|
|
|
|
|
|
|
|
|
|
|
|
|
|
|
|
|
|
|
|
|
|
|
|
|
|
|
|
|
|
|
|
|
|
|
|
|
|
|
|
|
|
|
|
|
|
|
|
|
|
|
|
|
|
|
|
|
|
в |
г |
Рис. 18. Схемы обработки различных поверхностей хвостовиков и полок лопаток турбин методом глубинного шлифования на станках SS13L (б) и ЛШ220 (а, в, г)
32
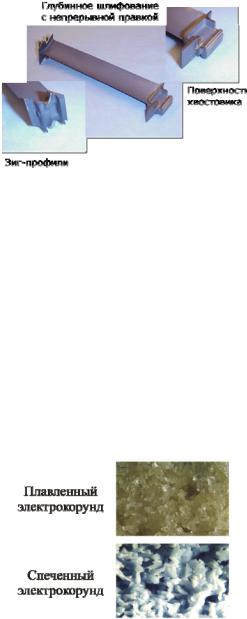
Рис. 19. Общий вид деталей, обрабатываемых глубинным шлифованием
Прямым следствием обработки с большой глубиной резания является увеличенная длина дуги контакта шлифовального круга с деталью, что приводит к возрастанию мощности и сил резания, общей тепловой напряженности в зоне резания. Поэтому большое внимание уделяется интенсивному отводу тепла из зоны резания с помощью высоконапорной подачи CОЖ. В качестве СОЖ используется 3%-ный раствор эмульсола «Пермол-6» производствазавода смазок иСОЖ (г. Пермь).
Для глубинного шлифования применяются специальные высокопористые шлифовальные круги диаметром 450–500 мм отечественных и зарубежных фирм. Крупные поры в кругах образуются в процессе изготовления при выгорании или выплавлении специальных порообразователей (перлит, фруктовая косточка, нафталин и др.) (рис. 20). В порах круга собираются стружка и шлам, которые затем
Рис. 20. Общий вид структуры высокопористых кругов
33
вымываются наружу под действием высоконапорной струи СОЖ и центробежной силы при вращении кругов. Правящие алмазные ролики изготавливаются с высокой точностью корпуса, посадочных отверстий, наружного профиля. Так, биение торцов корпуса и наружного диаметра профиля допускается в пределах 0,002–0,005 мм.
1.2.6. Высокоскоростное шлифование
Шлифование со скоростями 60–100 м/с и более называется скоростным и высокоскоростным шлифованием. При такой скорости шлифования уменьшается удельная нагрузка на каждое зерно, повышается стойкость кругов. Повышение подачи при скоростном шлифовании в 2–4 раза существенно увеличивает производительность обработки. При этом снижается и высота микронеровностей. Для высокоскоростного шлифования применяются специальные жесткие станки и шлифовальные круги с большой прочностью на разрыв. Получившие распространение у нас и за рубежом новые технологические процессы (глубинное шлифование с повышенной глубиной резания до tô 20 30 ì ì ; высокоскоростное шлифование при
V 60 150 ì ñ и более; интенсивное профильное шлифование
с непрерывной правкой алмазными роликами и др.) потребовали создания нового оборудования с повышенными техническими характеристиками (увеличенные подачи, мощность приводов, жесткость всех узлов, применение систем ЧПУ с ЭВМ), разработки соответствующих абразивно-алмазных инструментов и способов их контроля и испытаний на базе автоматизированных испытательных комплексов, оснащенных современной электронной аппаратурой.
1.2.7.Профильное шлифование
Кпрофильным методам шлифования относятся процессы резьбошлифования однониточными и многониточными кругами, зубошлифование методом копирования профильным кругом и методами обкатки червячными или тарельчатыми кругами (рис. 21). Метод копирования применяется и при шлицешлифовании дна и боков шлицев одним или двумя кругами.
34
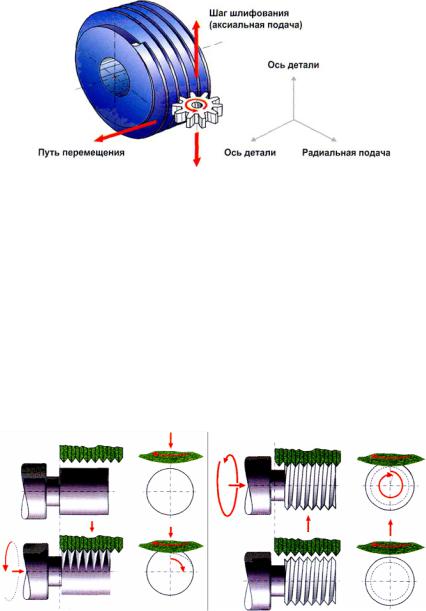
Рис. 21. Зубошлифование методом частичной обкатки
При профильном шлифовании методом копирования или врезания в качестве величины поперечной подачи принимается периметр в поперечном сечении шлифуемого контура в зоне контакта между шлифовальным кругом и заготовкой, который, по мере изменения глубины резания от прохода к проходу, может меняться, что повлечет за собой и изменение сил резания и требуемой мощности привода. При этом на разных участках переменного профиля должны меняться и режимы шлифования.
Резьбошлифование методом врезания многониточными про-
фильными кругами. При помощи правки шлифовальный круг формуется согласно профилю резьбы. Таким образом профили резьбы
Рис. 22. Схема профильного резьбошлифования методом врезания
35
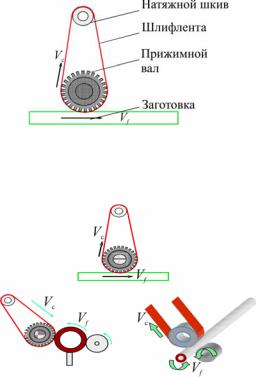
автоматически получают необходимую форму (рис. 22). Вследствие развития процесса правки с контурным управлением с использованием КЧПУ данный метод приобретает все большую популярность.
1.2.8. Ленточное шлифование
Ленточное шлифование – это чистовая обработка деталей с помощью шлифовальных непрерывных лент различной длины. Обработка заготовок проводится на специальных ленточно-шлифовальных станках по схеме на рис. 23. Шлифовальная лента с нанесенным абразивом натягивается между прижимным резиновым роликом и натяжным ведущим шкивом, движется со скоростью резания Vс и снимает необходимый припуск с заготовки. При этом заготовка движется относительно контактногоролика сопределеннойподачей Vf.
Рис. 23. Схема ленточного шлифования заготовок
Ленточное шлифование применяется при плоской, круглой, бесцентровой и профильной обработке с подачей по схемам на рис. 24.
Рис. 24. Схемы ленточного плоского и бесцентрового шлифования
36
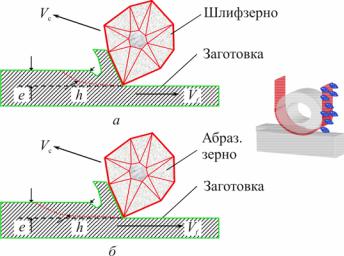
Рис. 25. Увеличениеразмеровснимаемойстружкиприувеличенииподачизаготовки:
а– Vf мала, h мала; б– Vf высока, h велика
Сувеличением подачи детали Vf длина стружки h значительно увеличивается, а с увеличением скорости ленты Vс толщина стружки уменьшается (рис. 25).
1.2.9. Полирование деталей
Полирование – это процесс окончательной чистовой абразивной обработки с целью получения гладкой поверхности с малой шероховатостью. Часто это бывает безразмерная обработка для придания деталям товарного вида, а также для уменьшения концентраторов напряжений в виде оставшихся от предыдущих операций рисок на поверхности. Наиболее наглядным примером может служить процесс полирования профиля пера лопаток компрессора газотурбинных двигателей, который является директивной обязательной операцией при окончательной обработке лопаток. В связи с большой сложностью формы пера лопаток в нашей стране и за рубежом на моторостроительных предприятиях эта операция чаще всего выполняется полировщиками вручную с применением различных абразивных инструментов (рис. 26). С целью сокращения объема ручных полироваль-
37
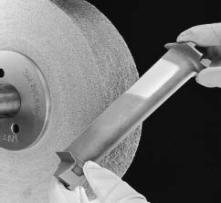
ных работ в последнее время внедряется точная фрезерная обработка и точное ленточное шлифование профиля пера лопаток на станках с ЧПУ. Однако эти операции только уменьшают припуски на полировку, но не решают основные вопросы обеспечения требуемого качества поверхностного слоя лопаток: окончательной точности в пределах 0,01 мм, шероховатости Ra≤0,32 мкм, отсутствия глубоких рисок и шлифовочных прижогов, обеспечения благоприятных остаточных напряжений, минимального наклепа и, как результат, высокой усталостной прочности лопаток.
Рис. 26. Процесс ручного полирования профиля лопатки турбины ГТД полировальным кругом
Процесс полирования применяется в авиапромышленности, начиная от изготовления турбинных лопаток и кончая ремонтом акриловых и силикатных стекол. В качестве полирующих материалов применяются: нетканые абразивы Скотч-Брайт, структурированные абразивы Тризакт, микроабразивы, суперабразивы, шлифовальные материалы на гибкой основе. Большой выбор типов и степени зернистости абразивов позволяет подобрать нужную агрессивность для получения необходимого качества и производительности как при удалении сварного шва, так и при суперфинишной полировке. Например, объемные абразивы Скотч-Брайт предотвратят «зарезы» при шлифовании и снизят вероятность брака.
38
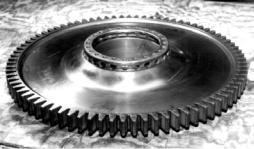
При полировании используется полный спектр абразивов для агрессивного шлифования и придания формы; удаления дефектов
изаусенцев; скругления углов; удаления коррозии и прижогов; зачистки поверхности, подготовки поверхности к покраске, удаления старого покрытия и коррозии.
Скругление и полирование острых кромок деталей полимер-
но-абразивными щетками. Проблема удаления заусенцев и скругления острых кромок наиболее остро стоит при производстве таких сложных и ответственных изделий, как газотурбинные двигатели (ГТД) для авиации и наземных установок. Заусенцы и острые кромки, образующиеся в процессе механической обработки деталей ГТД, удаляются и скругляются до определенного радиуса с целью уменьшения влияния концентраторов напряжений и повышения усталостной прочности обработанных деталей. Наибольшее число этих слесарных операций выполняется вручную с большой трудоемкостью
ис нестабильным качеством.
Снятие заусенцев и скругление острых кромок очень часто проводятся на многочисленных повторяющихся поверхностях различных деталей ГТД, например, обработка более 100 одинаковых кромок вдоль профильных пазов «ласточкин хвост» на дисках компрессоров или вдоль «елочного» профиля в пазах дисков турбин (рис. 27). Большие затруднения вызывает ручное удаление заусенцев из ячеистых сот уплотнительных колец с числом сот до нескольких тысяч при толщине стенок сот 0,05 мм.
Рис. 27. Общий вид диска турбины с елочными пазами, обработанными полимерно-абразивными щетками
39

Образование заусенцев в елочных пазах дисков турбин происходит на операции протягивания. Заусенцы образуются на одной торцевой поверхности диска. Радиусные кромки необходимо получить на обеих торцевых поверхностях. На одной торцевой поверхности необходимо получитьрадиус скругления 0,4 0,2 мм, надругой– 0,8 0,2 мм.
Полимерно-абразивные щетки (ПАЩ) состоят из стабилизированного нейлона и зерен абразива, которые путем экструзии образуют цельное моноволокно. В результате получается гибкая единообразная структура, которая содержит, по весу, примерно 30 % абразива. Абразивные зерна имеются на всех поверхностях волокна. Абразивное действие имеет место, как на торцах волокон, так и на боковых поверхностях (рис. 28). Применение ПАЩ возможно в автоматическом режиме на специальных установках. При применении боковая часть волокна часто трется об обрабатываемую поверхность, действуя при этом наподобие гибкого напильника. Чаще всего волокна применяются для снятия заусенцев.
Рис. 28. Общий вид полимерных щеток с внедренным абразивом
Помимо того, что гибкость волокон делает их идеальными для обработки неплоских поверхностей, она также способствует обработке острых кромок. Удаляя материал, волокна преимущественно оказывают воздействие на заусенцы и острые кромки (рис. 29).
40