
Выбор абразивных инструментов и режимов резания для высокоэффективно
..pdfшероховатости. Во-вторых, силы сцепления между металлом покрытия и смолой выше, чем между алмазом и смолой.
Механизм физико-химического взаимодействия между фенолформальдегидной смолой (связующим) и металлом заключается
вабсорбции гидроксильных групп на поверхности и их взаимодействия с атомами металла, его оксидами и гидроксидами. Это приводит к увеличению подвижности полимерных цепей и тем самым повышению энергии взаимодействия на границе связка–металл. Таким образом, увеличение поверхности контакта связка – металлизированное зерно, повышение энергии взаимодействия на границе контакта обеспечивают лучшее удержание зерен в связке.
Повышение термостойкости алмазоносного слоя с металлизированными зернами обусловлено тем, что слой покрытия, отводя часть тепла от кристалла алмаза, уменьшает температуру на границе покры- тия-связки, что благоприятносказывается на стойкости инструмента.
Эксперименты по шлифованию различных видов сплавов алмазными кругами на органических связках показали, что при использовании в кругах металлизированного алмазного порошка достигается снижение удельного расхода алмаза при увеличении производительности обработки в 1,4–1,7 раза. Особенно эффективным является применение металлизированных алмазов в органических связках при работе кругов на повышенных режимах.
Рекомендации по применению алмазных порошков и микропорошков из различных марок синтетических алмазов для изготовления различных инструментов приведены в табл. 13.
Коэффициент трения алмаза по металлам и твердым сплавам
в1,3–1,5 раза ниже, чем у электрокорунда и карбида кремния. Это уменьшает работу процесса и тем самым теплонапряженность процесса шлифования, что позволяет получать высокое качество обрабатываемой поверхности.
Другим важным преимуществом алмазов по сравнению с обычными абразивами является их высокая температуро- и теплопроводность (на порядок выше, чем у карбида кремния) и низкая теплоемкость. Благодаря этому теплота, выделяемая в процессе шлифования, не аккумулируется на режущей кромке зерна, а быстро отводится в глубь зерна, чтоспособствуетуменьшениютемпературы в зонерезания.
131
|
|
|
Таблица 1 3 |
|
Область применения алмазных порошков |
||
|
|
|
|
Марка |
Характеристика |
|
Рекомендуемая область применения |
алмазного |
|
||
порошка |
|
|
|
|
|
|
Микропорошки |
АСМ |
Из синтетических |
|
Изготовление инструмента на металлических и |
|
алмазов нормаль- |
|
органических связках, паст, суспензий. Для до- |
|
ной абразивной |
|
водки и полирования деталей машин и приборов |
|
способности |
|
из твердых сплавов, чугуна, керамики, стекла, |
|
|
|
полупроводниковых материалов |
АСН |
Из синтетических |
|
Изготовлениеинструментанаметаллическихи |
|
алмазов повышен- |
|
органическихсвязках, паст, суспензий. Длядоводки |
|
ной абразивной |
|
иполированиятвердыхисверхтвердыхтруднооб- |
|
способности |
|
рабатываемыхматериалов, корунда, керамики, ал- |
|
|
|
мазов, драгоценныхиполудрагоценныхкамней |
|
|
|
Субмикропорошки |
АСМ5 |
Из синтетических |
|
Изготовление паст, суспензий, а также при- |
|
алмазов зернисто- |
|
менение в свободном состоянии для финишной |
|
стью: 1/0,5; 0,5/0; |
|
полировки твердых материалов, корунда, кера- |
|
0,3/0 мкм |
|
мики, алмазов, драгоценных камней и полупро- |
|
|
|
водниковых материалов |
В связи с этим меньше нагревается как алмазное зерно, так и обрабатываемая поверхность. Кроме того, при алмазном шлифовании, вследствие высокой теплопроводности зерен, значительное количество теплоты уходит из зоны резания в круг, что существенно снижает температуру обрабатываемой детали. По сравнению с зернами обычных абразивных материалов, зерна синтетических алмазов имеют значительно меньшие радиусы округления вершин, меньшие углы выступов, большее число острых углов на зерне.
Большинство марок синтетических алмазов имеют развитую шероховатую поверхность с выступами, углублениями и большим числом режущих кромок на одном зерне. Это позволяет при шлифовании алмазным инструментом с меньшими усилиями и более низкими температурами производить съем обрабатываемого материала.
При алмазной обработке в тонком поверхностном слое твердого сплава формируются остаточные напряжения сжатия, что повышает предел прочности твердых сплавов при изгибе на 15–50 %. В резуль-
132

тате повышается прочность и износостойкость обработанной поверхности, а тем самым и сроки службы деталей и инструмента из твердого сплава.
Выбор охлаждения при алмазном шлифовании. Круги алмазные шлифовальныенаорганическихсвязкахмогутработатьбезохлажденияи с охлаждением. Круги на металлических связках работают только с охлаждением. Для кругов на органических связках применять щелочные растворы СОЖ не рекомендуется. Следует отдавать предпочтение шлифованию с охлаждением, так как при шлифовании с охлаждением шлифовальный круг меньше подвергается износу, и можно применять более жесткие условия обработки и тем самым повысить производительность шлифовки. Кроме этого уменьшается вероятность термического поврежденияобрабатываемойдетали, т.е. появленияприжоговнаней.
В качестве охлаждающих жидкостей для алмазных шлифовальных кругов рекомендуются 1–5%-е эмульсии. Рекомендации по применению СОЖ приведены в табл. 14.
Таблица 1 4 Рекомендуемый состав СОЖ для алмазного шлифования
Вид обработки |
Связка круга |
Рекомендуемый состав СОЖ |
Заточка |
Металлическая 1. |
1,5–3%-я эмульсия из эмульсола НГЛ-205 |
твердосплавного |
или замасливателя БВ. |
|
инструмента |
2. |
2–3%-я эмульсия из эмульсола «Аквол 10», |
|
0,5–1,0%-й раствор кальцинированной соды |
Органическая 1. 3%-я водно-масляная эмульсия масла индустриального.
2.0,5–1,0%-й раствор кальцинированной соды.
3.Эмульсия: 0,4 % триэтаноламина; 0,4 % нитрата натрия 0,3 % тринатрийфосфата; 0,3 % соды кальцинированой; 0,5 % буры; 0,1 % смачивателя ОПТ или ОП10; вода
5.2.5.Выбор кругов из кубического нитрида бора
для различных видов обработки
Выбор кругов из кубического нитрида бора для обработки за-
каленных сталей. При шлифовании закаленных сталей и заточке инструмента из быстрорежущих сталей обычными абразивами в зоне обработки возникают значительные силы резания и высокие темпе-
133
ратуры, достигающие температуры плавления обрабатываемого материала. Это приводит к низкому качеству обработанной поверхности, уменьшению стойкости инструмента из быстрорежущих сталей. Кроме того, обычные абразивные круги имеют низкую стойкость, что вызывает их частую правку и переналадку.
Высокий расход абразивных кругов, низкое качество обработанной поверхности, низкая производительность, запыленность рабочей зоны – основные недостатки примененияобычныхабразивныхкругов.
Более прогрессивной является обработка с применением синтетических сверхтвердых материалов на основе кубического нитрида бора (эльбор, кубонит, гексанит-А).
Кристаллы КНБ обладают повышенной хрупкостью, и в результате скалывания кристаллов при шлифовании режущие кромки постоянно обновляются и тем самым обеспечивается самозатачивание инструмента. Круги из КНБ имеют высокую режущую способность, которая в несколько раз превышает режущую способность кругов из обычных абразивов. Высокая режущая способность кругов из КНБ сохраняется практически до полного их износа. Так же как и алмаз, КНБ отличается от обычных абразивных материалов более высокой теплопроводностью и низкой теплоемкостью, что обеспечивает интенсивный отвод тепла из зоны шлифования. Это позволяет осуществлять процесс шлифования более интенсивно и при этом получать обрабатываемую поверхность изделия без прижогов, фазовых и структурных изменений в поверхностном слое.
Не менее важным преимуществом КНБ является его химическая инертность при взаимодействии со сталями. В отличие от алмаза и карбида кремния КНБ инертен к железу вплоть до температуры 1200 °С. Это обстоятельство снижает силы резания, температуру и предотвращает «засаливание» кругов. Низкие температуры в зоне резания кругами из КНБ исключают возможность образования растягивающих напряжений в поверхностном слое и, наоборот, способствуют образованию напряжений сжатия, которые положительно влияют на износостойкость обрабатываемыхдеталейи инструмента.
Несмотря на близость физико-механических свойств алмаза и КНБ, каждый из этих сверхтвердых материалов имеет свою область применения. Например, при обработке твердого сплава Т15К6 удельный расход
134

КНБ превышает удельный расход алмаза в 21 раз, а при шлифовании стали Р18 – в 8,5 раза меньше, чем для алмазных кругов. Очевидно, что для обработки твердого сплава необходимо применять алмазные круги, а дляобработки быстрорежущихсталей – кругиизКНБ.
Инструмент из кубического нитрида бора выпускается на керамической и органической связках. Круги на керамической связке отличаются более прочным закреплением эльбора в слое и высокой стойкостью профиля (табл. 15). Они наиболее распространены и рекомендуются для производительного шлифования, шлифования острых профилей (кромкостойкость) и получения обработанной поверхности высокой точности.
Таблица 1 5
Рекомендуемые режимы работы кругами из эльбора на керамической связке
|
Скорость |
Скорость |
Про- |
Попе- |
Кру- |
Глубина |
||
|
вращения |
вращения |
дольная |
речная |
говая |
шлифова- |
||
Вид обработки |
круга, |
изделия, |
подача, |
подача, |
пода- |
ния, |
||
|
м/с |
м/мин |
м/мин |
мм/ход |
ча, |
мм/дв. |
||
|
м/мин |
ход |
||||||
Круглое наружное |
30–35 |
10–25 |
0,5–1,0 |
– |
– |
|
0,01–0,05 |
|
щлифование |
|
|||||||
|
|
|
|
|
|
|
||
Круглое внутрен- |
8–35 |
10–30 |
0,3–1,0 |
– |
– |
0,002– |
||
нее шлифование |
0,005 |
|||||||
|
|
|
|
|
|
|||
Плоскоешлифование |
30–35 |
– |
8–10 |
0,3–0,6 |
– |
|
0,04–0,10 |
|
(перифериейкруга) |
|
|
|
|
|
|
|
|
Шлифованиерезьбы |
30–45 |
0,2–0,5 |
– |
– |
– |
До 0,4 |
||
Шлифование дол- |
|
|
|
|
|
|
|
|
бяков, шеверов и |
25–35 |
0,5–0,8 |
– |
– |
0,6 |
|
0,03–0,05 |
|
эвольвентного про- |
|
|||||||
|
|
|
|
|
|
|
||
филя зуба |
|
|
|
|
|
|
|
|
Шлифование про- |
25–35 |
0,2–0,4 |
– |
– |
– |
|
0,03–0,05 |
|
филя червячно- |
|
|||||||
модульных фрез |
|
|
|
|
|
|
|
|
Заточкаметаллоре- |
35–40 |
– |
1–2 |
– |
– |
0,03–0,08 |
||
жущегоинструмента |
||||||||
Шлифование про- |
|
|
|
|
|
|
|
|
филя резьбы ходо- |
30–35 |
0,4–0,8 |
– |
– |
– |
0,05–0,10 |
||
вых винтов |
|
|
|
|
|
|
|
|
Шлицешлифование |
25–30 |
– |
2–2,5 |
– |
– |
0,01–0,06 |
135
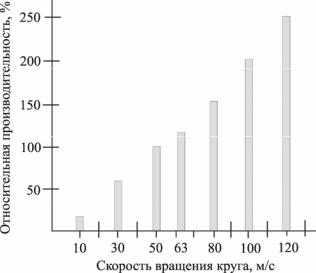
Высокоскоростное шлифование кругами из эльбора на кера-
мической связке. Новым направлением в развитии отечественного производства шлифовального инструмента является освоение выпуска кругов из эльбора на керамической связке для высокоскоростного шлифования (окружная скорость 80–120 м/с).
Высокая окружная скорость достигается за счет увеличения диаметров шлифовальных кругов, их конструктивных особенностей, а также специального оборудования, уже сориентированного на использование кругов из эльбора для высокоскоростного шлифования. Сокращение времени на обработку не влечет за собой увеличения удельного расхода эльбора. При этом, как показала практика, достигаются наилучшие показатели режущей способности эльбора и, соответственно, производительности обработки (рис. 66). Одними из главных требований, предъявляемых к оборудованию, использующему инструмент из эльбора для высокоскоростного шлифования, являются стабильная, свободная от вибраций конструкция и наличие системы для правки кругов.
Рис. 66. Влияние скорости шлифования на относительную производительность
136
Общие рекомендации по эксплуатации инструмента из эль-
бора. Шлифовальные станки, предназначенные для работы с кругами из эльбора, должны соответствовать станкам высокой точности. Они должны обеспечивать работу при рекомендуемых скоростях круга, возможность применения смазочно-охлаждающей жидкости (СОЖ), возможность автоматических продольной и поперечной подач и подачи на глубину. Биение шпинделей не должно превышать 0,008 мм в осевом и 0,006 мм в радиальном направлениях. Биение круга на шпинделе не должно превышать 0,02 мм.
После установки круга на станок следует произвести правку его рабочей поверхности. В оптимальных условиях резания инструмент из КНБ работает в режиме умеренного самозатачивания, не засаливается и правки для восстановления режущих способностей не требует. Правка инструмента из кубического нитрида бора необходима для восстановления геометрических параметров профиля, а также для первоначального профилирования и устранения биения после установки на станок.
Правка кругов из эльбора осуществляется стандартными алмазными карандашами с неориентированным расположением алмазов. Правка кругов для профильного шлифования производится однокристальным алмазным правящим инструментом (резцами, иглами, алмазами в оправах) при помощи функционирующих на станках стандартных правильных устройств методом точения слоя, содержащего КНБ. Очень эффективна также правка алмазными роликами.
Выбор режимов обработки кругами из СТМ. Режимы обработки оказывают существенное влияние на работоспособность алмазных кругов. Изменяя режимы обработки, можно влиять на производительность процесса, качествообработанной поверхности, стойкостьинструмента.
Выбор скорости резания. Скорость резания Vк (м/с) зависит от диаметра круга и частоты его вращения:
Vк = D N , 60000
где D – диаметр круга, мм; N – частота вращения круга, об/мин.
137
С изменением скорости вращения круга изменяется нагрузка на зерно иэнергия взаимодействия связкис обрабатываемымматериалом.
Общими для всех видов обработки (плоское шлифование, круглое наружное, круглое внутреннее, заточка твердосплавного инструмента) является то, что стойкость кругов (Кш) имеет максимальное значение в определенном интервале скоростей. Зависимость Кш при шлифовании твердого сплава кругами на органических и металлических связках носит экстремальный характер. С увеличением скорости круга Кш повышается, а затем, достигнув максимума, при дальнейшем повышении скорости круга снижается. Такой характер зависимости определяется в основном силами резания и температурами, которые, воздействуя на алмазоносный слой круга, с одной стороны, изменяют характер износа зерен и их устойчивость в связке, с другой стороны, влияют на физико-механические свойства и характер износа самой связки. При небольших скоростях, когда температура в зоне резания невелика, основное влияние оказывают составляющие силы резания, которые в этом случае имеют максимальное значение. С увеличением скорости до оптимальной уменьшаются составляющие силы резания вследствие уменьшения толщины среза, приходящейся на одно зерно. По мере дальнейшего повышения скорости круга, составляющие силы резания изменяются незначительно, но температура в зоне резания интенсивно повышается, что приводит
кснижению механических свойств связки.
Врезультате размягчения связки снижается прочность удержания зерен в связке и под действием сил резания происходит вырыв отдельных зерен из связки, а остальные подвергаются одновременно абразивному, диффузионному и адгезионному износам. Кроме того, при высоких скоростях усиливается ударный характер воздействия на зерно, что способствует повышенному износу зерен и связки. Все это приводит к снижению стойкости круга при повышенных скоростях круга. Так как оптимальная скорость резания зависит от многих факторов: связки, характеристик алмазоносного слоя, вида и условий обработки, режимов обработки, то для каждого случая существует своя оптимальная скорость круга. Поэтому в рекомендациях по при-
138
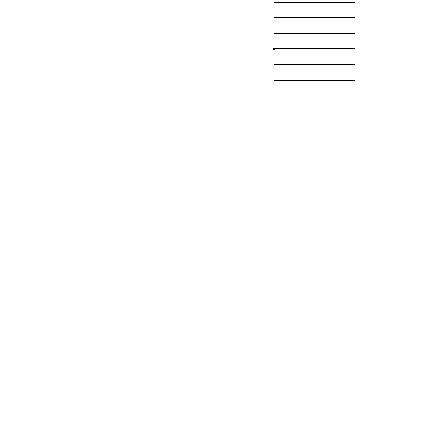
менению алмазных шлифовальных кругов производители указывают интервал рекомендуемых скоростей. При выборе скорости круга необходимо учитывать вид связки. В табл. 16 приведены рекомендации по выбору скорости шлифования твердых сплавов алмазными кругами с различными связками.
Таблица 1 6
Окружная скорость инструмента при шлифовании твердых сплавов, м/с
Вид шлифования |
Органические связки |
Металлические связки |
||
|
с СОЖ |
без СОЖ |
с СОЖ |
без СОЖ |
Плоское |
20–30 |
|
8–12 |
20–25 |
Круглое внутреннее |
10–20 |
8–12 |
12–20 |
|
Круглое наружное |
20–30 |
|
|
12–20 |
Заточка инструмента |
18–28 |
15–22 |
8–12 |
12–20 |
Выбор глубины шлифования, продольной и поперечной пода-
чи. Общим для всех видов шлифования является снижение коэффициента шлифования и повышения производительности с увеличением режимов обработки. При увеличении глубины резания, продольной и поперечной подач возрастает износ алмазных кругов, повышаются силы резания и температура. Прежде всего это объясняется пропорциональным ростом объема снимаемой в единицу времени стружки, увеличением мгновенного сечения среза, ростом составляющих силы резания. Кроме того, повышается доля участия связки в процессе шлифования, т.е. механического трения связки о шлифуемый материал, что приводит к повышенному выделению тепла и ухудшению работы алмазных зерен. При больших значениях глубины резания и подачи нарушается устойчивость алмазных зерен, и они вырываются из связки.
На рис. 67 и 68 приведены зависимости коэффициента шлифования (Кш) от глубины резания, продольной и поперечной подачи при плоском шлифовании твердого сплава алмазным кругом на органической связке.
139

Рис. 67. Зависимость коэффициента шлифования Кш от поперечной подачи (плоское шлифование, связка органическая)
Рис. 68. Зависимость коэффициента шлифования Кш от продольной скорости шлифования (плоское шлифование, связка органическая)
140