
Прикладная математика механика и процессы управления
..pdfУДК 539.319
А.Д. Тиунова, Е.В. Кузнецова
Пермский национальный исследовательский политехнический университет
ТЕХНОЛОГИЧЕСКИЕ ОСТАТОЧНЫЕ НАПРЯЖЕНИЯ В ПРОЦЕССЕ ПРЕССОВАНИЯ ОСЕСИММЕТРИЧНЫХ ЦИЛИНДРИЧЕСКИХ ИЗДЕЛИЙ
Рассмотрены процессы формирования технологических остаточных напряжений при прессовании осесимметричных цилиндрических изделий. В общем случае деформированное состояние при прессовании заготовки неравномерно, причем главные деформации удлинения растут от осевых слоев к периферийным и от переднего конца к заднему. Условия прессования определяют деформированное состояние деталей, которое во всех элементарных объемах характеризуется двумя главными деформациями укорочения и одной главной деформацией удлинения. Таким образом, зная параметры прессования, можно прогнозировать уровень и распределение остаточных напряжений по сечению пресс-заготовки.
Ключевые слова: остаточные напряжения, прессование, цилиндрические металлоизделия, деформированное состояние.
A.D. Tiunova, E.V. Kuznetsova
Perm National Research Polytechnic University
TECHNOLOGICAL RESIDUAL STRESSES
DURING AXIAL-SYMMETRIC CYLINDRICAL
WORKPIECES EXTRUSION
Technological residual stresses forming processes during axial-symmetric cylindrical workpieces extrusion are considered at this article. Generally, state of strain during blank extrusion is irregular and principal extension strains increase from axial layer to peripheral and from front end to rear one. Extrusion conditions determine components state of strain which is defined by two principal extension strains and one principal contraction strain at all volume elements. Hence, if you know extrusion parameters you can predict rate and residual stress distribution in workpiece profile.
Keywords: residual stresses, extrusion, cylindrical metal special ties, state of strain.
81
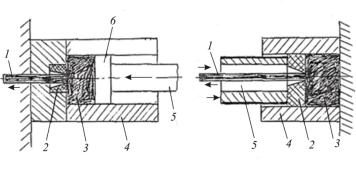
При прессовании металл исходной заготовки (чаще всего цилиндрической формы), помещенный в замкнутый объем – контейнер, подвергается высокому давлению и выдавливается сквозь отверстие, принимая его форму.
Технологический процесс прессования включает следующие операции:
–подготовка заготовки к прессованию (разрезка, предварительное обтачивание на станке, так как качество поверхности заготовки оказывает влияние на качество и точность профиля);
–нагрев заготовки с последующей очисткой от окалины;
–укладка заготовки в контейнер;
–непосредственно процесс прессования;
–отделка изделия (отделение пресс-остатка, разрезка). Прессование производится на гидравлических прессах с вер-
тикальным или горизонтальным расположением плунжера мощностью до 10 000 т.
Существует два вида прессования: прямое и обратное.
а |
б |
Рис. 1. Схема прессования: а – прямое прессование; б – обратное прессование; 1 – заготовка; 2 – матрица (фильера);
3 – нагретый слиток металла; 4 – цилиндр (контейнер); 5 – пуансон [1]
Прямое прессование (рис. 1, а): нагретый слиток 3 цилиндрической формы помещают в толстостенный цилиндр 4 (контейнер); с другой стороны контейнера закрепляется матрица 2, имею-
82

щая отверстие необходимой формы. Давление на металл передается пуансоном 5, и металл начинает течь через отверстие в шайбе.
При обратном прессовании (рис. 1, б) в контейнер 4 входит не пресс-шайба, а полый пуансон с матрицей 2 на конце. Матрица давит на заготовку 1, и металл течет в отверстие матрицы навстречу движению пуансона.
Процесс прессования характеризуется такими основными параметрами, как коэффициент вытяжки, степень деформации и скорость истечения металла из очка матрицы:
1. Коэффициент вытяжки λ определяют как отношение площади сечения контейнера Fк к площади сечения всех отверстий матрицы Fм:
|
Fк |
|
Fм . |
(1) |
2. Степень деформации равна отношению разницы площадей сечений контейнера Fк:
|
Fк Fм |
100 %. |
(2) |
|
Fк |
||||
|
|
|
3. Интегральный показатель деформации является суммой бесконечно малых деформаций, претерпеваемых рассматриваемым элементом и составляющих его конечную относительную деформацию:
i ln . |
(3) |
4. Скорость истечения металла v из очка матрицы пропорциональна коэффициенту вытяжки λ и определяется по формуле
v |
F V |
V , |
(4) |
к Fм |
где V – скорость прессования (скорость движения пуансона). К основным преимуществам прессования относятся:
– возможность обработки металлов, которые из-за низкой пластичности другими методами обработать невозможно;
83
–возможность получения практически любого профиля поперечного сечения;
–получение широкого сортамента изделий на одном и том же прессовом оборудовании с заменой только матрицы;
–высокая производительность (до 2–3 м/мин).
Недостатки прессования:
–повышенный расход металла на единицу изделия из-за потерь в виде пресс-остатка;
–появление в некоторых случаях заметной неравномерности механических свойств по длине и поперечному сечению изделия;
–высокая стоимость и низкая стойкость прессового инстру-
мента;
–высокая энергоемкость.
Технологические остаточные напряжения в процессе прессования осесимметричных цилиндрических изделий оказывают на материал изделия такое же воздействие, как напряжения, вызываемые эксплуатационной нагрузкой, поэтому причины появления остаточных напряжений и методы их минимизации требуют детального изучения.
Остаточными напряжениями называются напряжения, су-
ществующие в деталях при отсутствии внешних воздействий (силовых и температурных). Обычно эти напряжения остаются в деталях по окончании процесса их изготовления.
При проведении технологического процесса преобразование временных напряжений в остаточные происходит только в том случае, если выполняются следующие условия:
–временные напряжения, вызванные различными причинами, должны быть неравномерно распределенными в объеме материала;
–в наиболее напряженных местах временные напряжения должны превысить предел текучести (вынужденной эластичности, рекристаллизации) материала;
–фазы гетерофазных материалов должны иметь различные термоупругие свойства; в материале детали должны быть заморожены неравновесные конформации макромолекул [2].
В общем случае деформированное состояние при прессовании заготовки неравномерно, причем главные деформации удлинения
84
растут от осевых слоев к периферийным и от переднего конца к заднему. Условия прессования определяют деформированное состояние деталей, которое во всех элементарных объемах характеризуется двумя главными деформациями укорочения и одной главной деформацией удлинения. Все эти деформации неодинаковы и по поперечному сечению, и по длине изделия. Только круглые прутки при прессовании их из круглого сечения заготовки отличаются осесимметричным деформированным состоянием.
Поскольку пресс-изделия после выхода из пластической зоны, как правило, не подвергаются воздействию внешних сил, неравномерность деформированного состояния является основной причиной возникновения остаточных напряжений. Такие напряжения могут возникнуть в деталях и в результате неравномерности температур на отдельных участках пластической зоны. Исходя из этого можно считать, что напряженное состояние в момент выхода из пластической зоны определяется главным образом остаточными напряжениями, возникшими вследствие неравномерности деформаций. После выхода заготовки из матричного канала в центральных слоях возникают остаточные продольные напряжения сжатия, а в периферийных – остаточные продольные напряжения растяжения.
Характер распределения остаточных продольных напряжений на отпрессованном (без дальнейшей обработки) круглом прутке может быть представлен схемой, приведенной на рис. 2, а. Возникновение в периферийных слоях остаточных продольных растягивающих напряжений подтверждается формой изгиба поверхностных слоев при образовании поверхностных трещин в процессе прессования.
После выхода пресс-изделия из пластической зоны несколько увеличиваются его поперечные размеры вследствие упругой деформации. В результате возникают радиальные сжимающие напряжения между концентрическими кольцевыми слоями, подобно напряжениям в концентрических трубах, нагруженных внутренним и наружным давлением. Эти напряжения уменьшаются до нуля у поверхностного слоя [3].
На рис. 2, б приведена схема эпюры радиальных напряжений, которые, несмотря на одинаковый знак ввиду симметричного рас-
85

положения, взаимно уравновешиваются. Обе приведенные схемы эпюр распределения продольных и радиальных остаточных напряжений определяют вид эпюры окружных (кольцевых) напряжений. Схема такой эпюры приведена на рис. 2, в и показывает поперечное растяжение в периферийных кольцевых слоях и поперечное сжатие в центральных. Действительно, ввиду возникновения радиальных сжимающих напряжений поперечные напряжения в периферийных кольцевых слоях могут быть только растягивающими. Следовательно, для их уравновешивания необходимо, чтобы поперечные напряжения во внутренних кольцевых слоях были сжимающими.
а б в
Рис. 2. Схемы эпюр: а – продольных; б – радиальных; в – окружных остаточных напряжений круглого отпрессованного
прутка, не подвергавшегося дальнейшей обработке [3]
Изложенные сведения и соображения относятся к напряженному состоянию пресс-изделия в момент выхода его из пластической зоны. При горячем прессовании последующее охлаждение пресс-изделия может изменить описанное напряженное состояние и иногда весьма резко. Так, медленное охлаждение может привести к результатам, аналогичным низкотемпературному отжигу, т.е. к почти полному снятию остаточных напряжений. Такое охлаждение ввиду большой тепловой инерции более вероятно у профилей с небольшими удельными поверхностями.
При прессовании прутков больших диаметров или толстостенных профилей, кроме структурных превращений, изменяющих напряженное состояние, могут возникнуть новые остаточные на-
86
пряжения от неравномерного охлаждения периферийных и центральных слоев.
Быстрое охлаждение периферийных слоев может привести сначала к их укорочению и к увеличению продольных растягивающих напряжений, после чего, под влиянием тепла от внутренних слоев, эти напряжения могут исчезнуть. Затем укорочение внутренних слоев, ввиду их охлаждения, может вызвать продольные сжимающие напряжения в периферийных слоях и растягивающие во внутренних слоях. Это же может наблюдаться и с окружными напряжениями.
Здесь следует иметь в виду влияние диаметра (или толщины стенки). Чем они меньше, тем, очевидно, ниже тепловая инерция, быстрее выравнивание температуры продольных слоев и меньше вероятность возникновения температурных остаточных напряжений. Остаточные напряжения увеличиваются при несимметричных деформациях, поскольку последние вызывают и несимметричные остаточные напряжения.
Итак, основной причиной возникновения технологических остаточных напряжений является неоднородность пластической деформации материала, которая возникает вследствие неоднородного по сечению холодного деформирования, неравномерного распределения температур при нагреве или охлаждении, неравномерности фазовых превращений в изделии и т.п. Таким образом, чтобы при процессе изготовления избежать нежелательных остаточных напряжений либо уменьшить их настолько, чтобы они не отражались на качестве изделий, необходимо знать законы возникновения остаточных напряжений и их зависимость от технологических параметров.
Библиографический список
1.Третьяков А.В., Зюзин В.И. Механические свойства металлов
исплавовпри обработкедавлением. – М.: Металлургия, 1973. – 224 с.
2.Библиотека технической литературы [Электронный ре-
сурс]. – URL: http://delta-grup.ru/bibliot.
87
3. Колмогоров Г.Л., Кузнецова Е.В. О потенциальной энергии остаточных напряжений при осесимметричном деформировании // Вестник Пермского государственного технического университета. Прикладная математика и механика. – 2000. – № 1. – С. 92–98.
Об авторах
Тиунова Анастасия Дмитриевна (Пермь) – студентка ФГБОУ ВО ПНИПУ (614990, г. Пермь, Комсомольский пр., 29, e-mail: 89504546724@mail.ru).
Кузнецова Елена Владимировна (Пермь) – доцент кафедры динамики и прочности машин ФГБОУ ВО ПНИПУ (614990,
г. Пермь, Комсомольский пр., 29, e-mail: mellen75@mail.ru).
88
УДК 539.3
Д.С. Дудин, А.С. Шалимов, Е.В. Кузнецова
Пермский национальный исследовательский политехнический университет
ЭКСПЕРИМЕНТАЛЬНЫЕ МЕТОДЫ ОПРЕДЕЛЕНИЯ ОСТАТОЧНЫХ НАПРЯЖЕНИЙ
Рассмотрены самые современные методы определения остаточных напряжений, а именно метод рентгеновской дифракции и метод голографической интерферометрии. Наглядно показаны достоинства и недостатки методов, дано их описание, суть и применение в промышленности. В качестве примера описываются назначение и устройство двух прибо-
ров: Xstress 3000 G3/G3R, Prizm.
Ключевые слова: остаточные напряжения, метод рентгеновской дифракции, метод голографической интерферометрии, метод зондирующей лунки, рентгеновский дифрактометр Xstress 3000 G3/G3R, прибор для измерения остаточных напряжений Prizm, интегральный метод
Schajer.
D.S. Dudin, A.S. Shalimov, E.V. Kuznetsova
Perm National Research Polytechnic University
EXPERIMENTAL METHODS OF DETERMINATION
OF RESIDUAL VOLTAGE
In this article the most modern methods of determination of residual voltage are shown, especially a method of x-ray diffraction and a method of holographic interferometry. The advantages and disadvantages of these methods, their description, their sense and their application in the industry are clearly stated. As an example, there are the functions and structures of two devices: Xstress 3000 G3/G3R, Prizm.
Keywords: residual voltage, method of X-ray diffraction, method of holographic interferometry, method of exploratory crater, X-ray diffractometer Xstress 3000 G3/G3R, device for measuring residual voltage Prizm, cumulative method Schajer.
Применение экспериментальных методов к определению остаточных напряжений. Сейчас, с совершенствованием техноло-
89
гий, возникает особенно важный вопрос – вопрос определения остаточных напряжений. В ходе процесса создания детали с помощью методов пластической деформации в ней возникают остаточные напряжения, которые могут оказывать как положительное, так
иотрицательное влияние. Действительно, иногда остаточные напряжения достигают пределов прочности материала, тем самым разрушая деталь, еще лежащую в этот момент на складе. И наоборот, при благоприятном распределении остаточных напряжений какие-то дефекты в детали могут самозалечиваться, что влияет на характеристики долговечности, прочности и работоспособности данной детали.
Таким образом, качественное измерение остаточных напряжений оберегает нас от дальнейших неблагоприятных результатов. Более того, понимая, как распределены остаточные напряжения, мы можем корректировать методы создания той или иной детали с помощью процессов пластического деформирования. В данной работе рассматриваются самые современные методы определения остаточных напряжений, а именно метод рентгеновской дифракции
иметод голографической интерферометрии, а также некоторые виды экспериментальной аппаратуры, основанные на этих методах.
Метод рентгеновской дифракции. Суть метода рентгенов-
ской дифракции заключается в том, что рентгеновские лучи направляются на образец и отражаются от него. При этом чем плотность материала меньше, тем больше энергии рентгеновских лучей дойдет обратно к регистратору.
Дифракцию рентгеновских лучей на семействе атомных плоскостей (hkI) удобно рассматривать как отражение их от плоскости (hkI). Уравнение Вульфа–Брэгга устанавливает связь между межплоскостным расстоянием d, длиной волны рентгеновского излучения λ и углом дифракции θ (угол между падающим лучом и атомной плоскостью (hkI)):
2d sin n . |
(1) |
Под действием внешней силы s кристаллическая решетка деформируется, тем самым изменяются межплоскостные расстояния d, что приводит к изменению угла дифракции θ. На основании этого о
90