
Учебное пособие 800655
.pdf
стью и торцом в 3-х кулачковом самоцентрирующем патроне с пневматическим приводом.
10.4. Припуск под черновое точение после отливки (табл. 65)
|
Zв.min |
Rza |
Ta1 |
ρа |
εв |
1000 |
320 70 |
1390 мкм. |
|
|
|
|
1 |
|
1 |
1 |
|
|
|
|
|
|
При обтачивании одной торцевой поверхности векторы |
а1 |
||||||||
|
|
|
|
|
|
|
|
|
|
|
и εв |
имеют одно направление. |
|
|
|
|
|
||||
1 |
|
|
|
|
|
|
|
|
|
|
|
Rza |
Ta1 |
1000 мкм (табл. 52), |
тип производства |
- серий- |
|||||
|
1 |
|
|
|
|
|
|
|
|
|
ный. |
|
|
|
|
|
|
|
|
|
|
|
ρа |
к D |
2 160 |
320 мкм (табл. 46). |
|
|
|
|||
|
1 |
|
|
|
|
|
|
|
|
|
|
εв |
εв.табл. |
(εв.табл. |
0,3) |
100 |
(100 0,3) |
70 мкм |
(табл. |
||
|
1 |
|
|
|
|
|
|
|
|
|
63), так как патрон с пневмоприводом снижает погрешность установки на 20-40%.
εв.табл. 100 мкм, (табл. 63) установка на предварительно обработанную поверхность,.
10.5. Припуск под чистовое точение после чернового точения
(табл. 65)
Zв.min |
|
Rza2 |
Ta2 |
ρа2 |
εв2 |
100 |
0 |
|
4, 2 |
4, 2 108 мкм, |
||||||
R za 2 |
100 мкм, Ta 2 |
0 (табл. 54). |
|
|
|
|||||||||||
Заготовка |
– |
отливка |
|
из |
чугуна, |
2 |
класс точности |
|||||||||
(табл. 46): |
|
|
|
|
|
|
|
|
|
|
|
|
|
|
|
|
ρа |
|
0, 2 |
D |
|
d |
|
0, 2 |
160 |
|
30 |
|
0,320 |
4 мкм. |
|||
2 |
2 |
|
2 |
|
|
2 |
|
|
2 |
|
||||||
|
|
|
|
|
|
|
|
|
|
εв |
|
εв |
Кy |
70 0,06 |
4 мкм (табл. 58). |
||
|
2 |
1 |
1 |
|
|
|
|
10.6. Общие припуски на заготовку. |
|||||||
|
|
|
Z0.min. |
1390 |
108 |
1498 мкм; |
|
|
|
|
Z0.max. |
1990 |
408 |
2398 мкм. |
|
10.7. Общий номинальный припуск [1, с. 64] |
|||||||
Zо.ном |
Z0.min |
H0. |
δД |
1498 |
500 100 1898мкм. |
10.8. Номинальный размер заготовки [1, с. 94]
50

Lз.ном. LД.ном. Zо.ном 100000 1898 101898 мкм.
10.9.Выполненные расчеты сводятся в табл. 45(Г), для которой проводится проверка правильности расчетов по всем технологическим переходам по формуле, приведенной в п. 7.13. Например, для последнего технологического перехода (чистовое точение):
408 мкм = 108 мкм + 400 мкм - 100 мкм.
11.МЕТОДИКА РАСЧЕТА ОБЩЕГО И ОПЕРАЦИОННЫХ ПРИПУСКОВ НА ОБРАБОТКУ ПЛОСКОЙ ПОВЕРХНОСТИ
11.1.Исходные данные: деталь – плита (табл. 43, рис. 16), габаритные размеры 299х160х60 мм. Материал детали СЧ 18. Обработке подлежит поверхность 200х160 мм параллельная основанию
до шероховатости Ra = 2,5 мкм. Необходимо выполнить размер ме-
жду плоскостью и основанием, равный L = 60-0,06 мм. Тип производства - массовый.
11.2.Заготовка – отливка 1 класса точности (табл. 41), массой 15 кг, выбрана по табл. 32. Экономическое обоснование заготовки производится по методике, изложенной в п.2.3.
11.3.Технологический маршрут обработки плоскости 200х160 мм, отстоящей от базовой поверхности на 60 мм, назначается по табл. 67 и состоит из чернового и чистового фрезерования и предварительного шлифования. При фрезеровании заготовка устанавливается предварительно обработанным основанием на пластины (опорные) приспособления с пневматическим приводом. Черновое и чистовое фрезерование осуществляется на двухшпиндельном кару- сельно-фрезерном станке при одной установке детали. При шлифовании заготовка устанавливается на магнитной плите.
11.4.Припуск под черновое фрезерование после отливки
(табл. 65)
Zв.min |
Rza |
Ta1 |
ρа |
εв |
600 500 60 1160 мкм. |
|
1 |
|
1 |
1 |
При фрезеровании одной торцевой поверхности векторы ρа1
и εв1 имеют одно направление.
Rza |
Ta1 600 мкм (табл. 52), тип производства - массовый. |
1 |
51

а |
к |
lмак |
|
2 250 |
500 мкм (табл. 46), |
|
||||||||||
|
1 |
|
|
|
|
|
|
|
|
|
|
|
|
|
|
|
к = 2 мкм/мм (табл. 50), |
|
|
|
|
|
|
|
|
||||||||
εв |
|
60 |
мкм (табл. 61), |
установка предварительно обрабо- |
||||||||||||
1 |
|
|
|
|
|
|
|
|
|
|
|
|
|
|
|
|
танным основанием. |
|
|
|
|
|
|
|
|
|
|
|
|
|
|||
11.5. Припуск под чистовое фрезерование после чернового |
||||||||||||||||
фрезерования (табл. 65) |
|
|
|
|
|
|
|
|
|
|
|
|||||
Zв.min |
Rza2 |
|
Ta2 |
ρа2 |
εв2 |
|
50 |
0 |
30 |
4 |
84 мкм. |
|||||
Rza2 |
50 мкм, |
Ta2 |
0 |
|
(табл. |
54), |
заготовка из чугуна, |
|||||||||
1 класс точности. |
|
|
|
|
|
|
|
|
|
|
|
|
|
|||
ρа |
|
ρа |
Ку1 |
|
500 0,06 |
|
30 мкм (табл. 46, 58), |
|||||||||
|
2 |
1 |
|
|
|
|
|
|
|
|
|
|
|
|
|
|
εв |
|
εв |
Ку1 |
|
60 0,06 |
|
4 мкм, чистовое фрезерование без |
|||||||||
|
2 |
1 |
|
|
|
|
|
|
|
|
|
|
|
|
|
|
перестановки детали после чернового фрезерования. |
||||||||||||||||
11.6. Припуск под предварительное шлифование после чис- |
||||||||||||||||
тового фрезерования (табл. 65) |
|
|
|
|
|
|
|
|
|
|||||||
Zв.мин |
Rza |
3 |
|
Ta3 |
ρа |
3 |
|
εв |
10 |
0 |
20 |
0 30 мкм. |
||||
|
|
|
|
|
|
|
|
|
3 |
|
|
|
|
|
||
Rza |
10 мкм, Ta3 |
0 (табл. 54), |
|
|
|
|
|
|||||||||
|
3 |
|
|
|
|
|
|
|
|
|
|
|
|
|
|
|
ρа |
|
ρа |
Ку2 |
500 0,04 |
|
20 мкм, |
|
|
|
|
||||||
|
3 |
1 |
|
|
|
|
|
|
|
|
|
|
|
|
|
|
εв |
|
0 , установка на магнитной плите не дает погрешности |
||||||||||||||
3 |
|
|
|
|
|
|
|
|
|
|
|
|
|
|
|
|
закрепления. |
|
|
|
|
|
|
|
|
|
|
|
|
|
|
|
|
11.7. Общие припуски на заготовку: |
|
|
|
|
||||||||||||
|
|
|
|
|
Z0.min |
1160 |
84 |
30 |
|
1274 мкм; |
||||||
|
|
|
Z0.max |
1760 |
|
164 |
90 |
|
2014 мкм. |
|||||||
11.8 Общий номинальный припуск [1, с. 64] |
|
|||||||||||||||
Z0.ном. |
Z0.min |
|
H0. |
Д |
1274 |
400 |
60 |
1614 мкм. |
||||||||
11.9. Номинальный размер заготовки [1, с. 94] |
||||||||||||||||
Lз.ном. |
LД .ном. |
Zо.ном |
|
60000 |
1614 |
61614 мкм. |
11.10. Выполненные расчеты сводятся в табл. 45(Д), для которой проводится проверка правильности расчетов по всем технологическим переходам по формуле, приведенной в п. 7.13. Например,
52

для последнего технологического перехода (предварительное шлифование):
90 мкм = 30 мкм + 120 мкм - 60 мкм.
12. ДОПУСКИ, ПРИПУСКИ И КУЗНЕЧНЫЕ НАПУСКИ НА ПОКОВКИ СТАЛЬНЫЕ ШТАМПОВАННЫЕ
12.1. Общие требования [14, с. 7-32].
Допуски, припуски и кузнечные напуски устанавливаются в зависимости от конструктивных характеристик поковки, приведенных в табл. 71, и определяются исходя из шероховатости обработанной поверхности детали, изготовляемой из поковки. Для 1-го класса точности Т1 допуски устанавливаются на те функциональные поверхности, которые не подвергаются окончательной обработке.
Расчетная масса поковки определяется как масса подвергаемой деформации поковки или ее частей. В массу поковки не входят масса облоя и перемычки пробитого отверстия.
При высадке поковок на горизонтально-ковочных машинах или местной штамповке на молотах и прессах масса поковки включает массу части стержня, зажатого штампами.
Расчетная масса поковки определяется исходя из ее номинальных размеров.
Ориентировочную величину расчетной массы поковки ( Q )
допускается вычислять по формуле [14, с. 8] |
|
Q = q Кр, |
(12.1) |
где Q – расчетная масса поковки, кг; |
|
q – масса детали, кг;
Кр - расчетный коэффициент, приводится в табл. 78.
Класс точности поковки устанавливается в зависимости от технологического процесса и оборудования для ее изготовления (табл. 77), а также исходя из предъявляемых требований к точности размеров поковки.
Допускаются различные классы точности для разных размеров одной и той же поковки. При этом класс точности определяется
53
по преобладающему числу размеров одного класса точности, предусмотренному чертежом поковки.
Класс точности, группа стали, степень сложности должны быть указаны на чертеже поковки.
Исходный индекс для последующего назначения основных припусков, допусков и допускаемых отклонений определяется в зависимости от массы, марки стали, степени сложности и класса точности поковки (табл. 73).
Для определения исходного индекса по табл. 73 в графе «Масса поковки» находят соответствующую данной массе строку и, смещаясь по горизонтали вправо или по утолщенным наклонным линиям вправо вниз до пересечения с вертикальными линиями, соответствующими заданным значениям группы стали М, степени сложности С, класса точности Т, устанавливают исходный индекс
(от 1 до 23).
Примеры (табл. 31):
1.Масса поковки 0,5 кг, (определяется по формуле 12.1) группа стали М1 (табл. 71); степень сложности С1 (рис. 17, 18), класс точности Т2 (табл. 77).
Исходный индекс – 3 (табл. 72).
2.Масса поковки 1,5 кг, (определяется по формуле 12.1) группа стали М3 (табл. 71); степень сложности С2(рис. 17, 18), класс точности Т1 (табл. 77).
Исходный индекс – 6 (табл. 72).
Исходный индекс должен быть указан на чертеже поковки. Припуск на механическую обработку включает основной, а
также дополнительные припуски, учитывающие отклонения формы поковки. Величины припусков следует назначать на одну сторону номинального размера поковки.
Основные припуски на механическую обработку поковок в зависимости от исходного индекса, линейных размеров и шероховатости поверхности детали устанавливаются по табл. 74.
Припуски на толщину поковки, подвергаемой холодной или горячей калибровке, и поле допуска устанавливаются по формулам
12.21-12.23.
Дополнительные припуски, учитывающие смещение поковки, изогнутость, отклонения от плоскостности и прямолинейности,
54

межцентрового и межосевого расстояний, угловых размеров, определяются исходя из формы поковки и технологии ее изготовления по формулам 12.2-12.6 и 12.19.
В зависимости от класса точности Т устанавливаются дополнительные припуски на механическую обработку.
Разрешается округлять линейные размеры поковки с точностью до 0,5 мм.
При назначении величины припуска на поверхность, положение которой определяется двумя и более размерами поковки, устанавливается наибольшее значение припуска для данной поверхности.
Дополнительный припуск, мм, учитывающий смещение по
поверхности разъема штампов, при массе поковок Q = 1,0 |
10 кг и |
классе точности Т = 1 5 для поверхности разъема: |
|
плоской |
|
Zп = 0,007 + 0,008 Q + 0,015 Т + 0,003 Q Т, |
(12.2) |
симметрично изогнутой |
|
Zси = 0,03 + 0,019 Q + 0,047 Т + 0,003 Q Т, |
(12.3) |
несимметрично изогнутой |
|
Zни = 0,17 + 0,0028 Q + 0,017 Т + 0,008 Q Т, |
(12.4) |
Результат, полученный по формулам 12.2-12.4 округлить до десятых долей мм.
При изготовлении поковок по классу точности Т5 с применением пламенного нагрева заготовок допускается увеличение припуска для поковок с массой: до 3,2 г - до 0,5 мм; с 3,2 до 10,0 кг - 0,8 мм; свыше 10,0 кг до 1,0 мм.
Припуски, мм, для классов точности Т на изогнутость и отклонение от плоскостности и прямолинейности, мм, при наибольшем размере поковки L = 100-400 мм,
Zиз = -0,025 + 0,0005 L + 0,0583 Т + 0,0002 L Т. (12.5)
Результат округлить до десятых долей мм.
Припуски, мм, для классов точности Т на отклонение межосевого расстояния L, мм,
Zмр = 0,08 + 0,029 Т + 0,0007 L Т. |
(12.6) |
Результат округлить до десятых долей мм.
55

Минимальная величина радиусов закругления Rmin, мм, при глубине полости ручья штампа h = 10-50 мм, и массе поковки
Q = 1-16 кг,
Rmin = 0,68 + 0,07 Q + 0,025 h. |
(12.7) |
Допуски и допускаемые отклонения линейных размеров поковок назначаются в зависимости от исходного индекса и размеров поковки по табл. 75. Допускаемые отклонения внутренних размеров поковок должны устанавливаться с обратными знаками. Допуски и допускаемые отклонения размеров, отражающие односторонний износ штампов, равны 0,5 величин, приведенных в табл. 75. Допуски и допускаемые отклонения размеров толщины, учитывающие недоштамповку, устанавливаются по наибольшей толщине поковки и распространяются на все размеры ее толщины. Допуск размеров, не указанный на чертеже поковки, принимается равным 1,5 допуска соответствующего размера поковки с равными допускаемыми отклонениями. Для поковок, у которых стержень выходит за пределы штампа и не подвергается деформации, допуск , мм, длины стержня, для классов точности Т принимают:
= Т + 1 (12.8)
Величина допуска длины недеформированного стержня у поковок, полученных двусторонней высадкой, удваивается.
Допускаемая величина смещения по поверхности разъема штампа при плоской поверхности разъема пл, мм, симметрично изогнутой си и несимметрично изогнутой ни представлено в формулах
12.9-12.11
пл = 0,097 |
+ 0,028 |
Q + 0,069 Т + 0,005 Q Т |
(12.9) |
||||
си = 0,06 |
+ 0,039 |
Q + 0,09 |
Т + 0,006 Q Т |
(12.10) |
|||
ни = 0,164 |
+ 0,036 |
Q + 0,092 Т + 0,008 Q Т |
(12.11) |
||||
Допускаемая величина остаточного облоя для плоской по- |
|||||||
верхности разъема опл, мм, симметрично изогнутой |
оси и несиммет- |
||||||
рично изогнутой они представлено в формулах 12.12-12.14 |
|
||||||
опл = 0,158 + 0,042 |
Q + 0,097 |
Т + 0,003 |
Q Т |
(12.12) |
|||
оси = 0,364 |
+ 0,036 |
Q + 0,092 |
Т + 0,008 |
Q Т |
(12.13) |
||
они = 0,467 |
+ 0,033 |
Q + 0,089 |
Т + 0,011 |
Q Т |
(12.14) |
56

Допускаемая величина высоты заусенца на поковке по контуру обрезки облоя не должна превышать: 2 мм – для поковок массой до 1,0 кг включительно; 3 мм свыше 1,0 кг до 5,6 кг включительно; 5 мм свыше 5,6 кг до 50,0 кг включительно; 6 мм свыше 50,0 кг, а при пробивке отверстия эта величина может быть увеличена в 1,3 раза.
Допускаемая величина заусенца hз, мм, образовавшегося по контуру пуансона при штамповке в закрытых штампах (безоблойной), при максимальном радиусе поперечного сечения поковки L до 40 мм, на поверхности разъема штампа и степени сложности поков-
ки С определяется по формуле 12.15, при Q = 3,2 до 20 кг. |
|
hз = -0,38 + 0,119 Q + С. |
(12.15) |
Для L = 40-100 мм к результату расчета по формуле (12.15) прибавить 1 мм. Для L = 100-160 мм к результату расчета по формуле (12.15) прибавить 2 мм. Для L = 160-250 мм к результату расчета по формуле (12.15) прибавить 3 мм, а свыше 250 мм прибавить 4 мм. Для степени сложности С1 подставить степень сложности С2 (т.е. 2). Результат расчета округлить до целого числа.
Допускаемое наибольшее отклонение от концентричности пробитого в поковке отверстия к, мм, при наибольшем размере поковки L = 100-400 мм и классе точности Т определяется:
к = 0,208 + 0,0004 L + 0,058 Т + 0,001 L Т, (12.16)
к соответствует началу пробивки (со стороны входа пуансона в поковку). В конце пробивки эти отклонения могут быть увеличены на 25 %.
Допускаемые отклонения по изогнутости из, мм, от плоскостности и от прямолинейности для плоских поверхностей при наибольшем размере поковки L = 100-400 мм и классе точности Т определяется:
из = 0,117 + 0,00058 L + 0,083 Т + 0,00047 L Т, (12.17)
В данных величинах не учитываются перепады по высоте, толщине или ширине поковок.
Допуск радиального биения цилиндрических поверхностей не должен превышать удвоенной величины, полученной по формуле
(12.17).
57

Допускаемые отклонения межосевого расстояния |
мо, |
мм, |
при L = 60-400 мм и классе точности Т: |
|
|
мо = (0,063 - 0,0002 L + 0,0015 Т + 0,0008 L Т) |
(12.18) |
|
Допускаемые отклонения межосевого расстояния в поковках |
||
не должны превышать величин, полученных по формуле (12.18). |
|
|
Допускаемое отклонение угловых элементов поковки |
уг, |
|
мин, при длине элемента L = 25-160 мм. |
|
|
уг = (22,685 - 0,0157 L + 28,8 Т + 0,102 L Т) |
(12.19) |
|
Результат округлить с точностью до 1 минуты. |
|
|
Допуск радиусов закруглений R, мм, внутренних и наруж- |
||
ных углов поковок при радиусе закруглений R = 4-16 мм, T=1-5 |
|
|
R = 0,42 - 0,073 R - 0,083 Т + 0,115 R Т) |
(12.20) |
Допускаемые отклонения штампованных уклонов на поковках устанавливаются в пределах 0,25 их номинальной величины.
Штамповочные уклоны не должны превышать величин, установленных в табл. 76.
На поверхностях отверстий в поковках, изготовленных на го- ризонтально-ковочных машинах, штамповочный уклон не должен превышать 30.
У изготовленных на штамповочных молотах и прессах без выталкивателей поковок, имеющих элементы в виде ребра, выступа, реборды с отношением их высоты к ширине не более 2,5, допускается штамповочный уклон до 100 на внешней поверхности и до 120 на внутренней поверхности.
Впадины и углубления в поковке, когда их оси параллельны направлению движения одной из подвижных частей штампа, а диаметр или наименьший поперечный размер не менее 30 мм, выполняют глубиной до 0,8 их диаметра или наименьшего поперечного размера – при изготовлении на молотах и прессах и до трех диаметров – при изготовлении на горизонтально-ковочных машинах.
В поковке выполняют сквозные отверстия при двухстороннем углублении, если при ее изготовлении их оси параллельны направлению движения одной из подвижных частей штампа диаметр сквозного отверстия не менее 30 мм, а толщина поковки в месте пробивки – не более диаметра пробиваемого отверстия.
58
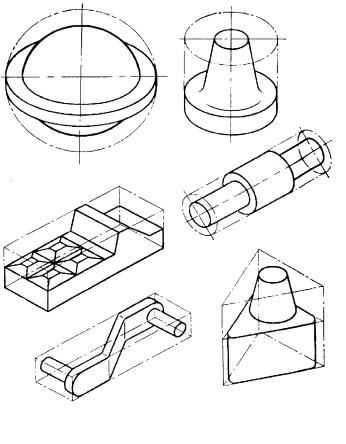
Степень сложности определяют путем вычисления отношения массы (объема) Q поковки к массе (объему) QФ геометриче-
ской фигуры, в которую вписывается форма поковки. Геометрическая фигура может быть шаром, параллелепипедом, цилиндром с перпендикулярными к его оси торцами или прямой правильной призмой (рис. 17).
Рис. 17. Геометрические фигуры
При вычислении отношения QQФ принимают ту из геометрических фигур, масса (объем) которой наименьший.
59