
Учебное пособие 800655
.pdf
Переход 5. Зенкерование фаски в центральном отверстии зенковкой 10, основное время работы которой является расчетным и определяется по формуле (14), табл. 4.
T10 0, 00021 70 30 0, 0441 мин расчетное.
Переход 6. Развертывание черновое центрального отверстия инструментом 11, основное время работы которого является расчетным и определяется по формуле (15), табл. 4.
T11 0,00043 60 30 0,744 мин расчетное.
Переход 7. Развертывание чистовое центрального отверстия инструментом 12, основное время работы которого является расчетным и определяется по формуле (16), табл. 4.
T12 0,00086 60 30 1,548 мин расчетное.
Основное время обработки детали на токарно-револьверном станке, определяется как сумма расчетных времен всех переходов.
TO.T P T2 |
T6 T8 |
T9 |
T10 T11 |
T12 ; |
TO.T P 0, 2088 |
0,36 |
0,378 |
0,819 |
0, 0441 |
0,774 1,548 4,132 мин .
Штучно-калькуляционное время обработки детали на токар- но-револьверном станке
|
TШК .Т Р |
К ТО.Т Р ; |
||
Т ШК .Т |
Р 1, 665 4,132 |
6,88 мин |
||
Коэффициент |
К |
находится как среднее значение из табл. 3: |
||
|
|
|
|
|
К |
|
(1,98 |
1,35) / 2 |
1,665. |
|
|
|
|
1.3.2. Операция 010. Автоматно-токарная черновая (рис.6). При рабочем движении поперечного суппорта протачивается
кольцевая канавка инструментом 13 и черновая подрезка двух торцевых поверхностей инструментами 14 и 15. При рабочем движении продольного суппорта обтачивается начерно наружная цилиндрическая поверхность инструментом 16. Все инструменты работают одновременно и основное время работы определяется по формулам (7),(4),(1), табл. 4. Время работы инструментом 18 – расчетное, как перекрывающее время работы других инструментов
T13 0,00063 (1102 962 ) 1,82 мин расчетное ТА Т черн ;
10
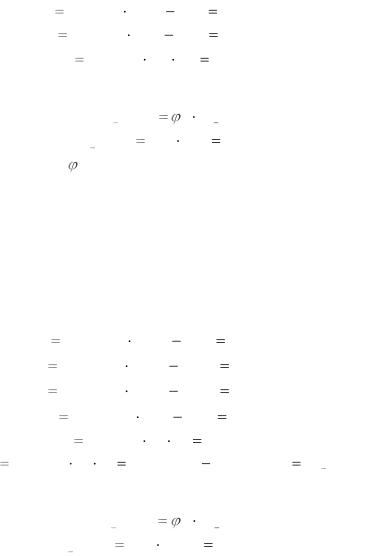
T 0, 00037 (1102 |
802 ) 0, 2109 мин ; |
14 |
|
T |
0,00037 (802 602 ) |
0,1036 мин ; |
15 |
|
|
Т16 |
0, 00017 (80 15) |
0, 204 мин . |
Штучно-калькуляционное время черновой обработки детали на многорезцовом полуавтомате
|
ТШК . А Т .ЧЕРН . |
К Т А Т .ЧЕРН .; |
|
TШК . А Т .ЧЕРН . 1,88 1,82 3, 42 мин. |
|||
Значение |
К |
определяется из табл. 3. |
|
|
|
|
1.3.3. Операция 015. Автоматно-токарная чистовая (рис.7). При рабочем движении поперечного суппорта обтачиваются
четыре наружные фаски инструментами 17,18,19,20. При рабочем движении продольного суппорта растачивается фаска в отверстии инструментом 21 и начисто обтачивается наружная цилиндрическая поверхность инструментом 22. Все инструменты работают одновременно и основное время их работы определяется по формулам (5),(11),(3), табл. 4. Время работы инструмента 22 принято расчетным, как большее
Т |
0,000052 (1002 |
942 ) |
0,0605 мин ; |
17 |
|
|
|
Т |
0,000052 (1102 |
1042 ) |
0,0668 мин ; |
18 |
|
|
|
Т |
|
0,000052 (1102 |
1042 ) |
0,0668 мин ; |
|
19 |
|
|
|
|
|
Т |
20 |
0,000052 (802 |
742 ) |
0,048 мин ; |
|
|
|
|
|
|
|
|
Т21 0,00018 60 30 |
0,0324 мин ; |
|||
Т22 0, 00017 80 15 0, 204 мин |
расчетное Т А Т .ЧИСТ . |
Штучно-калькуляционное время чистовой обработки детали на многорезцовом полуавтомате
ТШК . А Т .ЧИСТ . |
К Т А Т .ЧИСТ . ; |
ТШК . А Т .ЧИСТ . 1,88 |
0, 204 0,38352 мин. |
1.3.4. Операция 020. Агрегатно-сверлильная (рис.9).
Три трехшпиндельные силовые головки работают одновременно. Три инструмента 23 одной из головок сверлят три отверстия
11

7 мм на одной из позиций. Три инструмента 24 другой головки зенкеруют три фаски 1 450 на другой позиции. Три инструмента 25 третьей головки нарезают резьбу M 8 в трех отверстиях на следующей позиции. Основное время работы инструментов находится по формулам (12),(14),(35), табл. 4. Время работы инструментов 23 расчетное, как наибольшее.
|
Т23 0, 00052 |
7 |
20 |
0, 0728 мин |
|
расчетное |
Т А С ; |
|||||||||
|
|
Т24 |
0,00021 10 1 |
0,0021 мин ; |
|
|||||||||||
|
|
Т25 |
|
0, 0004 8 17 |
0, 0544 мин . |
|
||||||||||
|
Штучно-калькуляционное время агрегатно-сверлильной опе- |
|||||||||||||||
рации |
|
|
|
|
|
|
|
|
|
|
|
|
|
|
|
|
|
Т ШК . А С |
К |
|
Т А С ;Т ШК . А С |
1,51 0, 0728 |
0,1099 мин |
||||||||||
|
Значение |
к |
определяется из табл. 3. |
|
|
|
|
|||||||||
|
|
|
|
|
|
|
|
|
|
|
|
|
|
|
|
|
|
1.3.5. Операция 025. Круглошлифовальная чистовая по 3 |
|||||||||||||||
классу точности (рис.8). |
|
|
|
|
|
|
|
|
|
|
||||||
|
Основное время работы инструмента 26 находится по фор- |
|||||||||||||||
муле (9), табл. 4. |
|
|
|
|
|
|
|
|
|
|
|
|
|
|
||
|
Т26 |
0, 00010 100 15 |
0,15 мин |
расчетное |
ТК . Ш . |
|||||||||||
|
Штучно-калькуляционное время на круглое шлифование |
|||||||||||||||
Т ШК .К . Ш . |
К |
ТК . Ш . ;ТШК .К . Ш . |
1,825 |
0,15 |
|
0, 27375 мин |
||||||||||
|
Значение |
К |
определяется из табл. 3, [6, с.173]. |
|
||||||||||||
|
1.3.6. Ориентировочно, в п.1.2, тип производства определен |
|||||||||||||||
как |
среднесерийный, |
|
|
для |
|
|
|
которого |
принято |
|||||||
FM |
334,5; KB |
1,3; |
|
H |
0,8 . |
По |
формуле |
(1.6) |
находится |
|||||||
DM |
48000 /12 |
4000 штук. |
|
|
|
|
|
|
|
|
|
|||||
|
Подставляются известные значения в уравнение (1.4) |
|||||||||||||||
|
|
ОР.М . |
60 |
334,5 1,3 |
0,8 |
|
5, 2182 |
|
(1.7) |
|||||||
|
|
|
|
|
|
|
|
|
|
|
|
|
||||
|
|
|
ТШК |
4000 |
|
|
|
ТШК |
|
|
||||||
|
|
|
|
|
|
|
|
|
|
|
|
12

Подстановкой в уравнение (1.7) штучно-калькуляционных времен, рассчитанных в п.1.3.1 – 1.3.5 определяется, какое число закрепленных операций выполняет каждый станок.
Токарно-револьверный
5, 2182 ОР.М .Т Р 6,88 0, 758 .
Многорезцовый полуавтомат черновой
ОР.М .А Т .ЧЕРН . |
5, 2182 |
1,526 . |
|
|
|||
3, 42 |
|||
|
|
Многорезцовый полуавтомат чистовой
5, 2182 ОР.М .А Т .ЧИСТ . 0,38352 13, 606 .
Агрегатно-сверлильный
ОР.М .А С |
5, 2182 |
47, 481. |
|
|
|||
0,1099 |
|||
|
|
Круглошлифовальный
ОР.М .К Ш |
5, 2182 |
19, 062 . |
|
|
|||
0, 27375 |
|||
|
|
Число различных операций равняется сумме всех операций закрепленных за рабочими местами – станками, применяемыми в техпроцессе
|
5 |
|
|
|
|
|
|
О |
ОР.М .Р |
ОР.М .Т Р |
ОР.М .А Т .ЧЕРН . |
ОР.М .А Т .ЧИСТ . |
|||
|
Р 1 |
|
|
|
|
|
|
|
|
ОР.М . А С |
|
ОР.М .К Ш ; |
|
||
О |
0,758 |
1,526 |
13,606 |
47, 481 |
19,062 |
82, 433 . |
Коэффициент закрепления операций определяется по формуле (1.3) и соответствует среднесерийному типу производства п.1.3.
КЗ.О. |
О |
; |
КЗ.О. |
82, 433 |
16, 49 |
|
Р |
5 |
|||||
|
|
|
|
13
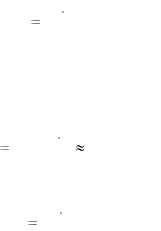
Число рабочих мест (станков) Р = 5 (станки: токарноревольверный, многорезцовый полуавтомат черновой, многорезцовый полуавтомат чистовой, агрегатно-сверлильный, круглошлифовальный).
1.3.7. В серийном производстве изготовление деталей осуществляется партиями. Определение оптимального количества деталей в партии производится по формуле [1, с. 22]
n |
N a |
(1.8) |
|
|
|||
F |
|||
|
|
где n – количество деталей в партии для одновременного запуска, шт.; N – годовая программа выпуска деталей, шт.; a - число дней, на которое надо иметь запас деталей на складе для крупных деталей 2-3 дня, для мелких 5-10 дней; F – число рабочих дней в году (принимать 253 дня)
n |
48000 |
5 |
950 шт. |
|
|
||
253 |
|
||
|
|
|
При проектировании поточного производства следует определить такт выпуска t, мин. по формуле [1, с.21]
t |
60 Ф |
(1.9) |
|
|
|||
N |
|||
|
|
где Ф – действительный годовой фонд времени работы оборудования, ч. [1, с.23, табл.3 и 5]; N – годовая программа выпуска деталей, шт.
1.4. Этап 3. Окончательное определение типа производства по коэффициенту закрепления операций выполняется после разработки операционного технологического процесса, расчета режимов резания и технического нормирования. Расчет производится по методике, изложенной в п.1.3, но вместо укрупненных нормативов используется штучно-калькуляционное время, полученное расчетным путем.
14

2. МЕТОДИКА НАЗНАЧЕНИЯ И ЭКОНОМИЧЕСКОЕ ОБОСНОВАНИЕ ВЫБОРА ЗАГОТОВКИ
Заготовки деталей машин выполняют из проката, давлением и в виде отливок. Характеристика и область применения сортового и специального проката приведены в п. 4.3, заготовок, выполненных давлением, в п. 4.2, а литых заготовок в п. 4.1 [7, с. 154-164].
2.1.Исходные данные. Деталь – втулка (рис. 1). Материал сталь 45. Годовая программа N=48000 шт. Тип производства - среднесерийный. Необходимо определить стоимость заготовок, выполненных из проката, давлением и литьем (рис. 4).
2.2.Стоимость заготовки полученной из проката определяется по формуле источника [2, с. 48]
|
M Q S |
(Q |
q) |
|
SОТХ |
|
(2.1) |
|||||||
|
1000 |
|
||||||||||||
M |
6,5069 0,12 |
(6,5069 |
1,646) |
14, 4 |
0,71 р. |
|||||||||
1000 |
||||||||||||||
|
|
|
|
|
|
|
|
|
|
|
|
|
||
Масса заготовки из проката, кг |
|
|
|
|
|
|
||||||||
Q |
VЗ.П . ; |
Q |
7850 0.0008289 6,51 кг . |
|||||||||||
Плотность стали |
|
7850 кг |
м |
3 , табл. 2. |
|
|||||||||
|
|
|
|
|
|
|
|
|
|
|
|
|
||
Объем заготовки из проката, м3 |
|
|
|
|
|
|
||||||||
|
|
|
|
|
D2 |
|
|
|
|
|
|
|
||
|
V |
( |
З.П . |
) |
h |
|
|
; |
|
|
||||
|
|
|
|
|
|
|||||||||
|
З.П . |
|
|
4 |
|
|
З.П . |
|
|
|
||||
|
|
|
|
|
|
|
|
|
|
|
|
|
||
V |
3,14 ( |
0,122 |
) 0, 07333 |
|
0, 0008289 м3 |
|||||||||
|
|
|||||||||||||
З.П . |
4 |
|
|
|
|
|
|
|
|
|
|
|
||
|
|
|
|
|
|
|
|
|
|
|
|
Диаметр заготовки из проката с учетом припуска на обработку черновым и чистовым обтачиванием и шлифованием, мм.
DЗ.П. |
DД |
(2ZЧЕР. 2ZЧИСТ . |
2ZШЛ . ); |
|
DЗ.П . |
110 |
(5,5 |
2, 0 0,5) |
118 мм |
Припуски 2ZЧЕРН . |
5,5 мм; |
2ZЧИСТ . 2 мм; 2ZШЛ . 0,5 мм |
||
табл. 37, 38. |
|
|
|
|
15
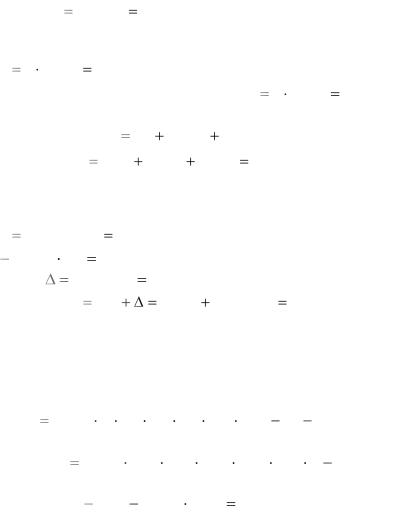
Диаметр заготовки выбирается из табл. 38 ближайший и больший DЗ.П 120 мм 0,12 м . Длинна заготовки h3.1 определя-
ется как длина детали hд =0,05 м, с учетом припуска на отрезку заготовки с двух сторон дисковой пилой на отрезном станке
2ZОТР. |
|
2 |
0, 006 |
|
0, 012 м и припуска на подрезку торцов с двух |
||||||||||||||||||||||
сторон |
|
заготовки, |
после |
|
отрезки |
2ZПОДР. 2 0,003 0,006 м , |
|||||||||||||||||||||
табл. 5. |
|
|
|
|
|
|
|
|
|
|
|
|
|
|
|
|
|
|
|
|
|
|
|
|
|
|
|
|
|
|
|
|
|
|
h3.1. |
|
|
hД |
|
2ZОТР. |
|
2ZПОДР. ; |
|
|
|
|
|
||||||||
|
|
|
|
h3.1. |
0, 05 |
|
|
0, 012 |
|
|
0, 006 |
|
0, 068 м |
|
|||||||||||||
|
Диаметры заготовки из проката и их длины приведены в |
||||||||||||||||||||||||||
табл. 36. Выбирается прокат диаметром DЗ.П. = 0,12 м и длиной L = |
|||||||||||||||||||||||||||
0,88 м. Количество деталей, изготавливаемых из |
такого проката |
||||||||||||||||||||||||||
L / h3.1 |
|
0,88 / 0, 068 12 шт . |
|
|
|
|
|
Остаток |
|
|
составит |
||||||||||||||||
0,88 |
(0,068 12) |
|
0,064 м . На каждую заготовку дополнительно |
||||||||||||||||||||||||
приходится |
|
|
0,064/12 |
|
0,005333 м . Длина заготовки для дета- |
||||||||||||||||||||||
ли составит hЗ.П . |
h3.1. |
|
|
|
0, 068 |
0, 005333 |
0, 07333 м . |
Цена |
|||||||||||||||||||
1 кг материала заготовки S = 0,12 руб, табл. 6. Масса готовой детали |
|||||||||||||||||||||||||||
определена в п.1.2. q = 1,646 кг. Цена 1 т стружки стальной |
Sотх = |
||||||||||||||||||||||||||
14,4 руб, табл. 7. |
|
|
|
|
|
|
|
|
|
|
|
|
|
|
|
|
|
|
|
|
|
||||||
|
2.3. Стоимость заготовок, полученных методами литья, в |
||||||||||||||||||||||||||
рублях, определяется по формуле источника [1, с. 33], |
|
||||||||||||||||||||||||||
S |
|
( |
|
Ci |
Q K |
|
|
K |
|
K |
|
K |
|
K |
|
) |
(Q |
q) |
SОТХ |
|
; (2.2) |
||||||
ЗАГ . |
|
|
|
T |
C |
B |
M |
П |
|
||||||||||||||||||
|
|
1000 |
|
|
|
|
|
|
|
|
|
|
|
1000 |
|
|
|||||||||||
|
|
|
|
|
|
|
|
|
|
|
|
|
|
|
|
|
|
|
|
|
|
||||||
|
|
SЗАГ . |
( |
|
290 |
|
3, 21 1,03 0,83 0,93 1, 21 1) |
|
|
|
|||||||||||||||||
|
|
|
|
|
|
|
|
||||||||||||||||||||
|
|
|
|
|
1000 |
|
|
|
|
|
|
|
|
|
|
|
|
|
|
|
|
|
|
|
|
||
|
|
|
|
|
|
|
(3, 21 |
|
|
|
1,646) |
|
14, 4 |
|
0,87 р . |
|
|
|
|
||||||||
|
|
|
|
|
|
|
|
|
|
1000 |
|
|
|
|
|
||||||||||||
|
|
|
|
|
|
|
|
|
|
|
|
|
|
|
|
|
|
|
|
|
|
|
|
Базовая стоимость 1 т отливок приведена в табл. 8. Для отливок, получаемых в земляных формах и кокилях из чугуна, массой 1-3 кг, 3 класса точности, 3 группы сложности и 3 группы серийности стоимость Сi = 290 р. Масса заготовки определяется по формуле
(1.1).
16

Q |
VЗ.Л . ; |
Q 7850 0,0004088 3,21 кг |
Плотность стали |
7850 кг м3 , табл. 2. Объем заготовки, |
при наибольших габаритах детали до 120 мм и номинальном размере 120 мм, определяется с учетом припуска на деталь Z = 4 мм, табл. 40,
и допуска |
на |
наружные |
|
|
цилиндрические |
|
поверхности |
|||
0,8 мм ,отверстие |
0,8 мм и длину |
0,5 мм , табл. |
||||||||
41. |
|
|
|
|
|
|
|
|
|
|
V |
h (R2 |
r2 ) h (R2 |
r2 |
) h (R2 |
r2 ) ; |
|||||
З.Л . |
31 |
31 |
31 |
32 |
32 |
32 |
33 |
33 |
33 |
|
V |
|
3,14 |
0, 015 |
|
(0, 04442 |
|
0, 02562 ) |
|
||
З , Л , |
|
|
|
|
|
|
|
|
|
|
0, 0235 (0, 05942 |
0, 02562 ) |
|
0, 02 (0, 05442 |
0, 02862 ) |
||||||
|
|
|
0, 0004088 м3 ; |
|
|
|
D31
d31
r31
D32
d32
r32 h32
D33
R33
d33
r33
DД1 |
2Z |
; |
D31 |
|
80 |
8 |
0,8 |
88,8 мм |
0, 0888 м ; |
|
|
|
R31 |
0, 0444 м ; |
|
|
|||
d Д1 |
2Z |
; |
d31 |
|
60 |
8 |
0,8 |
51, 2 мм |
0,0512 м; |
0,0256; h31 |
|
15 мм |
0,015 м; |
|
|
||||
D2 |
2Z |
; |
D32 |
110 |
8 |
0,8 |
118,8 мм |
0,1188 м; |
|
|
|
|
R32 |
0, 0594 м; |
|
|
|||
d Д 2 |
2Z |
; d32 |
|
60 |
8 |
0,8 |
51, 2 мм |
0,0512 м; |
|
0,0256 м; |
|
|
|
|
|
|
|
|
|
hД |
2Z |
; |
h32 |
|
15 |
8 |
0,5 |
23,5 мм |
0,0235м |
DД 3 |
2Z |
; |
D33 |
|
100 |
8 |
0,8 |
108,8 мм |
0,1088 м; |
0,0544 м |
|
|
|
|
|
|
|
|
|
d Д 3 |
2Z |
; |
d33 |
|
60 |
8 |
0,8 |
57, 2 мм |
0,0572 м; |
0,0286 м; |
|
|
|
|
|
|
|
|
|
|
|
|
h33 |
20 мм |
0, 02 м |
|
17

Для отливок, получаемых литьем в обычные земляные формы и кокиль, коэффициенты, зависящие от класса точности Кт (табл. 41), группы сложности Кс (табл. 21), массы Кв, марки материала Км, объема производства заготовок Кп, приведены в табл. 9, 10,12, 13,14; для отливок, получаемых литьем по выплавляемым моделям, коэффициенты в табл. 15, 16, 17, 18 ; для отливок, получаемых литьем под давлением, коэффициенты в табл.19, 20; группы серийности приведены в табл. 11 и табл. 20 , а группы сложности в табл. 21 .
Масса детали q = 1,646 кг, определена в п.1.2. Стоимость 1 т
стружки SОТХ = 14,4 руб, табл. 7 .
2.4. Стоимость заготовки, полученной методами давления, определяется по формуле (2.2), приведенной в п.2.3
SЗАГ |
( |
315 |
2,74 1 0,84 1 1 1) |
(2,74 1,646) |
|
14, 4 |
0,709 р |
|
1000 |
||||||
|
1000 |
|
|
|
Базовая стоимость 1 т штамповок из конструкционной углеродистой стали, массой 2,5-4 кг, 2 класса точности, 2 группы сложности, 2 группы серийности Сi = 315 р. (табл. 8).
Масса заготовки определяется по формуле (1.1)
Q |
VЗ.Ш . ; Q |
7850 0, 00034864 |
2, 74 кг |
|
||
Плотность стали |
|
7850 кг / м3 (табл. 2). |
|
|||
Объем заготовки определяется с учетом основного припуска |
||||||
Z = 2,2 мм, определенного по номограмме (табл. 72-73) и табл. 74 и |
||||||
допуска |
1,12,1 , определенного по (табл. 75). Обозначения символов, |
|||||
приведенных в номограмме, имеются в табл. 71. |
|
|||||
V |
h (R2 |
r2 ) h (R2 |
r2 ) h (R2 |
r 2 ) ; |
||
З.Ш . |
31 31 |
31 |
32 32 |
32 |
33 33 |
33 |
V |
3,14 [0,015 (0,042252 |
0,027252 ) |
0,0215 (0,058252 |
||||||
З.Ш . |
|
|
|
|
|
|
|
|
|
0, 27252 ) 0,02 (0,053252 |
0,030252 )] 0,00034864 м3; |
||||||||
D31 |
DД1 |
2Z |
; |
D31 |
80 |
4, 4 |
2,1 |
86,5 мм |
0,0865 м; |
|
|
|
|
R31 |
0, 04325 м; |
|
|
||
d31 |
d Д1 |
2Z |
; |
d31 |
60 |
4, 4 1,1 |
54,5 мм |
0,0545 м; |
|
|
|
r31 |
0,02725 м; |
h31 |
15 мм |
0,015 м; |
|
18

D32 |
D2 |
2Z |
; |
D32 |
110 |
4, 4 |
2,1 |
116,5 мм |
0,1165 м; |
||
|
|
|
|
R32 0,05825 м; |
|
|
|
||||
d32 |
d Д 2 |
2Z |
; |
d32 |
60 |
4, 4 |
1,1 |
54,5 мм 0,0545 м; |
|||
|
|
|
|
r32 |
0,02725 м; |
|
|
|
|
||
h32 |
hД |
2Z |
; |
h32 |
15 |
4, 4 |
2,1 |
|
21,5 мм |
0,0215 м; |
|
D33 |
DД 3 |
2Z |
; |
D33 |
100 4, 4 |
2,1 |
106,5 мм 0,106,5 м; |
||||
|
|
|
|
R33 |
0,05325 |
м; |
|
|
|
||
d33 |
d Д 3 |
2Z |
; |
d33 |
66 4, 4 1,1 |
|
60,5 мм |
0,0605 м; |
|||
|
|
r33 |
0,03025 м; |
h33 |
20мм |
0,02 м. |
|
Для горячештампованных заготовок коэффициенты, зависящие от класса точности Кт, группы сложности Кс, массы Кв, марки материала Км, определяются по табл. 22,23. Коэффициент, зависящий от объема производства, принимается равным Кп=1, кроме случаев, когда объем производства (годовая программа) превышает значение, указанные в табл. 24. Группа определяется на основании классификации, приведенной на рис. 2 и 3 [1, с. 28-29]. Масса детали q=1,646 кг определена в п.1.2. стоимость 1 т стружки Sотх=14,4 р, табл. 7 .
2.5. Результаты расчета объема, массы и стоимости заготовки, полученной различными методами, приведены в табл. 25. Стоимость получения заготовки из проката и штамповки меньше чем из отливки, однако, вес заготовки из проката наибольший, что требует дополнительных операций для снятия припуска. Окончательно метод получения заготовки назначается после составления маршрутов обработки детали из штамповки и проката и техникоэкономического обоснования.
19