
Учебное пособие 800655
.pdf4. МЕТОДЫ ПОЛУЧЕНИЯ ЗАГОТОВОК Заготовки деталей машин получают литьем, обработкой дав-
лением, резкой сортового и профильного проката, а также комбинированными способами, представленными ниже по данным источника
[7, с. 154-164].
4.1.Получение заготовок литьѐм. Характеристики методов получения литых заготовок приводятся в табл. 32 . Методы 2,3,4,5 и 8-й в настоящее время хорошо механизированы, а методы 6,7,9,10 и 11-й частично или полностью автоматизированы. Часовая производительность методов: 11-го до 1000 мелких отливок , 10-го до 30 отливок и 9-го 15 отливок. При автоматизации 6-го метода можно получать до 450 полуформ в час. Наиболее высокий коэффициент использования металла (порядка 0,9 и выше) можно получить при использовании методов 7,8 и 11-го (без учета потерь металла на литники), а также методов 6,9 и 10-го (коэффициент использования металла 0,8-0,9). При центробежном литье литники отсутствуют, но на внутренней поверхности полой заготовки приходится снимать большой припуск. Коэффициент использования металла при других методах литья составляет 0,6-0,8. Перспективно применение нового метода литья по газифицируемым (выжигаемым) моделям из пенополистирола. Этот метод сокращает маршрут технологического процесса изготовления заготовок; по сравнению с литьем по выплавляемым моделям он позволяет получать более крупные точные отливки весом до 5 Т, шероховатость поверхности до 4-5-го классов и точность до 5-7-го классов по OCT. Прогрессивна штамповка заготовок из жидкого металла. Еѐ преимущества: нет литниковой системы, достаточно высокая точность (5-7 класс) и шероховатость (3-5-й классы) поверхности, возможность получения тонких стенок (от 0,5 мм). Припуски на механическую обработку литых заготовок приведены в табл. 39-40.
4.2.Получение заготовок обработкой давлением. Характеристики методов получения заготовок давлением даны в табл. 33. Из приведѐнных методов наиболее полно автоматизированы методы 3,6,7,10,11,12-й. В меньшей степени автоматизирован цикл получения заготовок методами 1 и 2-м. Наиболее производительны методы 10 и 11-й (до 350 шт/мин) При штамповке небольших заготовок на молотах и прессах достигается производительность до 1000 шт/ч.
30
Наименее производительны методы 1 и 2-ой. Наиболее высокий коэффициент использования металла - порядка 0,9 обеспечивается при использовании методов 6,7 и 9-го (отсутствие облоя и малые штамповые углы) и особенно при использовании методов 10, 11 и 12-го. В последнем случае коэффициент использования металла приближается к единице (заклепки, болты и пр.)
Самый короткий цикл формообразующих операций (без очистки и термической обработки) дают методы 6,7,9,10 и 11-й.
Перспективно применение метода электровысадки, при котором предварительно обработанную на станке заготовку подвергают местному нагреву пропусканием через нее тока низкого напряжения в течение 2 - 3 с. По достижении температуры 900-1000 0С происходит формирование заготовки в штампе пресса. Заготовки получают без окалины по 2-3-му классам точности. Припуски на механическую обработку штампованных заготовок приведены в табл. 42.
4.2.1. Холодной листовой штамповкой получают кожухи, крышки, колпаки, щитки, диски. Исходным материалом служат листовой металл и лента. Для восстановления пластических свойств деформированного металла после штамповки вытяжкой применяют отжиг. Холодная штамповка является высокопроизводительным технологическим методом.
Очень эффективны при листовой штамповке групповые штампы (целесообразны при партии деталей 70-80 шт).
Точность листовой штамповки в совмещенном штампе (0,02- 0.08), последовательном
(0,10-0,30) и раздельном
(0,30- 0,50) мм. Для свободных размеров холодноштампованных деталей может быть выдержан 7-й класс точности.
Для формообразования листовых деталей толщиной до 6 мм
иразмером до 2 м в серийном производстве применяют также беспреоссовую гидровзрывную и электрогидравлическую штамповку. В этом случае штамп состоит из одной матрицы. Точность профиля штамповки при диаметре 2 м достигает 2-3 мм.
4.2.2. Правку поковок применяют для устранения искривлений и короблений заготовок, которые происходят при обрезке облоя
ипрошивке перемычек, а также от действия остаточных напряжений в их материале.
31
Правку осуществляют в горячем или холодном состоянии. Горячую правку производят на прессе после обрезки облоя и прошивки перемычек; холодную правку - после термической обработки
иочистки поковки от окалины. Во избежание трещин холодную правку поковок производят в отожженном или нормализованном состоянии. Холодная правка в штампах производительнее горячей правки (100-150 шт/ч).
4.3.Получение заготовок из проката. Для получения поковок
инепосредственного изготовления из проката деталей на металлорежущих станках применяет сортовой и фасонной прокат, используя калиброванные прутки и горячекатаную сталь повышенной и обычной точности (табл. 36).
Изготовление деталей из горячекатаной стали, производят
после резки заготовок или непосредственно прутка (табл. 5, 38). Для изготовления деталей соответствующей конфигурации применяют квадратную, шестигранную, полосовую и других профилей стали, а также бесшовные и сварные трубы. Припуски на механическую обработку заготовок из проката приведены в табл. 37.
Заготовки валов часто получают из полосы, которую после разрезки на требуемую длину вальцуют в цилиндр, а шов сваривают на роликовом аппарате. Для получения уступов цилиндр обжимают на гидравлических прессах. Экономия материала при изготовлении валов генераторов достигает 62 %.
4.3.1.Гнутые профили, применяемые для изготовления многих деталей, легки и обладают значительной жесткостью. В конструкциях используют открытые, закрытые и многослойные профили. Форма гнутых профилей может быть приближена к форме отдельных элементов конструкции. Экономию металла (30-70 %) и сокращение времени обработки (20-40 %) можно получить при изготовлении деталей из фасонных труб или труб переменного сечения.
4.3.2.Специальной прокат, применяемый в условиях крупносерийного и массового производства (сельхозмашиностроение, вагоностроение, автомобилестроение), почти полностью исключает механическую обработку, на долю которой остается в основном отрезка, сверление отверстий и зачистка.
4.3.3Правка проката предшествует его резке на мерные заготовки. Последние в ряде случаев также подвергают правке. Правкой
32
уменьшают припуск на последующую механическую обработку заготовки и устраняют поломки зажимных механизмов револьверных станков и автоматов Листовой прокат правят на листоправильных вальцах с точностью 1- 2 мм/м.
Правку круглого проката диаметром 0,25-6 мм, поставляемого в бухтах, производят на правильно-отрезных станках; правка осуществляется роликами, отрезка - ножом по упору; после правки кривизна достигает 0,5-0,7 мм/м. Правку круглого проката диаметром до 120 мм осуществляют на правильно-калибровочных станках: правка производится правильными, а калибровка калибрующими роликами. После правки кривизна достигает для черных прутков 0,5-
0,9 мм/м и обработанных |
0,1-0,2 мм/м. Точность калибровки |
по диаметру достигает |
0,03-0,05 мм. |
Холодную правку на прессах применяют для зацентрованных заготовок. Место и величину искривления определяют индикатором при вращении заготовки на упругих центрах, которые затем опускают, устанавливая заготовку на жесткие опорные призма, и правят; после правки кривизна составляет в зависимости от еѐ диаметра 0,05-0,15 мм/м. Разновидностью этого метода является правка заготовок, установленных в центрах, струбциной вручную.
Правку на накатных станках гладкими плашками применяют для цилиндрических заготовок длиной до 200 мм. При прокатывании заготовки между плоскими гладкими плашками обеспечивается высокая производительность (порядка 60 шт/мин) и точность
0,05-0,10 мм/м.
В результате холодной правки возникают остаточные напряжения в материале заготовки. Поэтому ее не применяют при изготовлении особо ответственных деталей машин.
4.3.4. Резку проката на индивидуальные заготовки обычно производят по упору. На пресс-ножницах режут листовой и прутковый материал различного сечения. Резка дает малую точность размера по длине (1-1,5 мм), косой срез и смятие концевых участков заготовки. Для устранения этих дефектов предусматривают дополнительный припуск на подрезку торцов заготовки. Резка на прессножницах весьма производительна. Резка на приводных ножовках наименее производительна, но универсальна. Еѐ преимущества -
33
чистая поверхность реза (3-4-й классы), малый перекос торца заготовки (до 2-2,5 мм на 100 мм диаметра) и малая потеря металла в стружку (толщина ножовочного полотна 1,5-2,5 мм). Для повышения производительности резке подвергают пакет прутков, закрепляемой в призматических тисках.
Резку ленточными пилами применяют для круглых и других прутков. Она производительнее резки ножовками, так как нет обратного хода, и дает более чистую поверхность реза (до 5-го класса) при меньшем отходе металла в стружку.
Резка дисковыми пилами весьма производительна, дает чистый срез (до 4-го класса) и малый перекос торца (до 1,5-2 мм на 100 мм диаметра). При толщине диска 8-12 мм отход металла в стружку относительно велик для коротких заготовок (табл. 5).
Фрикционными дисками режут прокат любых профилей и марок, включая высокопрочные труднообрабатываемые конструкционные стали. Процесс резки основан на использовании теплоты трения, возникающей в месте контакта разрезаемого металла с периферийной частью диска. Температура разрезаемого металла в зоне контакта при этом повышается настолько, что он легко удаляется из пропила в виде пучка искр при незначительном износе фрикционного диска. Поверхность реза шероховатая со следами наплыва металла; еѐ необходимо подвергать повторной обработке.
Резкой отрезными резцами на станках токарного типа получают заготовки из круглого прутка или трубы. Шероховатость реза до 6-го класса, а неперпендикулярность торца до 0,1 мм на 100 мм диаметра. Малый расход металла в стружку, так как ширина лезвия резца составляет 3-5 мм (табл. 5). Это самый эффективный метод резки труб, так как перемещение резца равно толщине стенки трубы.
Анодно-механическую резку производят вращающимся гладким диском (катод), который скользит с небольшим давлением по плоскости реза: струю электролита подают в зазор между прутком и диском. Образующуюся на поверхности прутка (анод) плохо проводящую ток плѐнку удаляют механическим воздействием диска. Твѐрдость и прочность металла заготовки при этом не имеют существенного значения. В качестве электролита применяют водный раствор жидкого стекла, а также соли фосфорной или кремниевой ки-
34

слоты. Этот метод обеспечивает чистую (4-5-классы) и точную поверхность реза.
Резкой абразивными кругами получают заготовки из твѐрдых и труднообрабатываемых материалов (закалѐнная сталь, инструментальные и специальные стали, твѐрдые сплавы). Шероховатость поверхности реза – 6-7-й классы; минимальная ширина кругов 2-3 мм; диаметр200-250 мм.
Газовую (кислородную) резку применяют для листового, полосового и профильного проката, а также для удаления литников и прибылей со стальных отливок. В поверхностном слое реза на глубину 2-5 мм происходит нормализация стали, а при резке высокоуглеродистой стали – закалка, устраняемая последующим отжигом. Поверхность реза обезуглероживается на глубину до 1-1,5 мм.
Газовой резкой по шаблону (копирная резка) можно получать из толстолистовой стали заготовки сложной конфигурации, почти не требующие последующей механической обработки (звѐздочки, фланцы и подобные плоские детали). Точность резки: ручной 1 мм, машинной 0,5 мм, на точных машинах 0,2 мм.
Дуговую электрорезку применяют как для черных, так и для цветных металлов и сплавов. Металл разрезается в результат его расплавления а зоне реза. Метод не обеспечивает такую точность и шероховатость реза, которые получаются при кислородной резке.
4.4. Комбинированные методы применяют для изготовления сложных заготовок. При этом рациональным является их расчленение на отдельные простые части, изготовляемые прогрессивными способами, с последующим соединением этих частей сваркой или пайкой в одно целое. Примеры заготовок: листоштампованные детали, соединенные точечной или шовной сваркой (заготовки малых и средних размеров); вырезанные автогеном элементы из листового проката (или отливки), соединѐнные шовной сваркой в крупногабаритные заготовки (фундаментальные кольца гидротурбин, рамы дизелей, станины тяжелых станков); залитые штампованные или механически обработанные заготовки (диафрагмы паровых турбин с залитыми лопатками, армированные отливки); предварительно обработанные поковки или элементы из проката, соединѐнные электрошлаковой сваркой в одну крупную заготовку; средние отливки, соединѐнные термитной сваркой в одну крупную и сложную заготовку.
35

При значительном упрощении технологии изготовления элементов сварной конструкции по сравнению с технологией литья или ковки цельной заготовки сварная заготовка обычно получается более легкой по весу. Еѐ отдельные элементы, находящиеся в наиболее тяжелых условиях, могут быть выполнены из легированной стали.
5. МЕТОДИКА ЭКОНОМИЧЕСКОГО ОБОСНОВАНИЯ ПРИМЕНЕНИЯ СПЕЦИАЛЬНОГО ПРИСПОСОБЛЕНИЯ
Экономическая эффективность применения специального приспособления находится по формуле [1, с.151]
Э |
(Т у |
Т сп |
) |
Сч.з. N |
S |
|
( A B) p. |
(5.1) |
|
|
пр |
||||||||
|
|
шт |
шт |
60 100 |
|
|
|
||
|
|
|
|
|
|
|
|
||
5.1. Штучное время при обработке детали в универсальном |
|||||||||
приспособлении Т у |
|
определяется по методике работы |
[1, с.111.]. |
||||||
шт |
|
|
|
|
|
|
|
|
Если известно штучно – калькуляционное время Тшту = 6,88 (п.1.3.1)
и количество деталей в партии для одновременного запуска n = 950 шт. (п. 1,3,7), то штучное время определяется
Т у |
Т у |
Тп.з. |
, |
(5.2) |
|
||||
шт |
ш.к. |
n |
|
|
|
|
|
Подготовительно – заключительное время Тп.з. находится как сумма времени наладки с индивидуальной установкой шести инструментов, как изображено на операционно-технологической наладке (рис.5). Тпнал.з.. = 53 мин [9, с.148] и времени на получение инструмен-
та и приспособления и сдачу их Тпполуч.з. = 10 мин [9, с.93]
Тп.з. Тпнал.з.. Тпполуч.з.
Тп.з. = 53 + 10 = 63 мин.
Штучное время с применением универсального приспособления по формуле (5.2)
T у |
6,88 |
63 |
6,81 мин. |
|
|||
|
|||
шт |
|
759 |
|
|
|
|
36

5.2. Штучное время с применением универсального приспособления Тшту превышает штучное время с применением специаль-
ного приспособления с пневмоприводом Тштсп на величину разницы
вспомогательных времен, связанных с установкой заготовки массой до 3 кг (п. 2.4). При установке заготовки в универсальном патроне с
креплением ключом ТУ |
0,35 мин [9, |
с.32]. При установке заго- |
|||
|
|
в |
|
|
|
товки |
в специальном патроне |
с применением пневмозажима |
|||
Т сп |
0,17 мин |
[9, с. 32]. |
|
|
|
в |
|
|
|
|
|
|
|
Т сп |
Т у |
(Т у |
Т сп ); |
|
|
шт |
шт |
в |
в |
|
Т сп |
6,81 |
(0,35 |
0,17) |
6,63 мин. |
|
шт |
|
|
|
|
5.3.Часовые затраты по эксплуатации рабочего места опре-
деляются (п.3.14.1.) Сч.з. = 32,67 к/ч.
5.4.Стоимость специального приспособления Sпр определя-
ется по табл.35. Sпр = 50 р.
5.5.Коэффициент амортизации А при сроке окупаемости в два года [1, с.151]. Принимается А = 0,5.
5.6.Коэффициент, учитывающий ремонт и хранение приспо-
собления В = 0,1 0,2 [1, с. 151]. Принимается В = 0,2.
5.7. Экономическая эффективность применения специального приспособления составит:
Э (6,81 6,63) |
32,67 48000 |
50 (0,5 0, 2) 12 р. |
|
60 100 |
|||
|
|
37
6. ОБЩИЕ МЕТОДИЧЕСКИЕ РЕКОМЕНДАЦИИ ПО РАСЧЕТУ ПРИПУСКОВ НА ОБРАБОТКУ ДЕТАЛЕЙ МАШИН
Почти все способы получения заготовок не обеспечивают необходимого качества деталей машин. Требуемая точность и шероховатость деталей достигается механической обработкой. Поверхности заготовок, подлежащие механической обработке, имеют размеры, отличающиеся от размеров детали. Следовательно, наружные поверхности детали должны быть увеличены, а внутренние - уменьшены на величину, снимаемую при механической обработке.
Слой металла, снимаемый при механической обработке, для получения заданной точности и заданной шероховатости поверхности, называется припуском. Припуски подразделяются на промежуточные и общие. Величина припусков оказывает значительное влияние на технико-экономические показатели технологического процесса. Увеличенные припуски требуют дополнительного расхода материала и снижают производительность. При заниженных припусках не удаляется дефектный слой металла.
В машиностроительной промышленности широко применяется опытно-статистический метод назначения припусков.
При этом методе припуски определяются по таблицам, составленным на основе обобщения и систематизации производственных данных передовых предприятий.
Расчетно-аналитический метод определения припусков разработал профессор В.М. Кован. По методу В. М. Кована величина промежуточного припуска должна быть точной, чтобы при удалении этого припуска устранялись погрешности обработки и дефекты поверхностного слоя, полученные на предшествующих операциях, а также погрешности установки обрабатываемой детали, возникающие на выполняемой операции. Величину минимального промежуточного припуска определяют следующие факторы:
1) высота неровностей Rza , полученная на смежной предше-
ствующей операции обработки данной поверхности. Величина Rza
зависит от способа обработки, режимов резания и условий выполнения предшествующей обработки. Так как шероховатость обработанной поверхности обычно колеблется в пределах двух-трех классов,
38
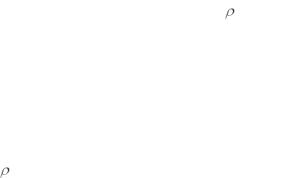
то для расчета припусков на обработку должны быть взяты значения Rza по более грубому классу шероховатости;
2) состояние и глубина поверхностного слоя Ta , полученные
на смежной предшествующей операции. На выполняемой операции этот слой подлежит полному или частичному удалению с заготовки;
3) пространственное отклонение |
a |
в расположении обраба- |
|
|
тываемой поверхности относительно базовых поверхностей заготовки. К пространственным отклонениям относятся кривизна осей, коробление поверхностей, увод и непараллельность осей, неперпендикулярность осей и поверхностей, отклонения от соосности ступеней валов и отверстий, эксцентричность внешних поверхностей относительно отверстий и т. п. Все эти отклонения не связаны с допуском на размер элементарной поверхности и имеют самостоятельное значение. Они учитываются в минимальном припуске в виде слагае-
мого a ;
4) погрешность установки εв , возникающая на выполняемой
операции. При погрешности установки обрабатываемые поверхности заготовок партии не будут занимать одинакового положения на станке. Следовательно, получаемые смещения обрабатываемой поверхности должны быть компенсированы дополнительной составляющей операционного припуска.
Следовательно, общая величина минимального промежуточного (операционного) припуска Zвmin определяется сумми-
рованием величин Rza , Ta , ρa и εв .
При выполнении расчетов припусков необходимо соблюдать следующие рекомендации. Для определения припусков расчетноаналитическим методом использовать формулы, приведенные в табл. 65. Табличные значения допусков и припусков на изготовление поковок имеются в п. 12. Качество торцов поковок представлено в табл. 62.
Суммарное значение пространственных отклонений для различных видов заготовок и механической обработки представлено в табл. 46.
39