
паровые и газовые турбины для электростанций
.pdf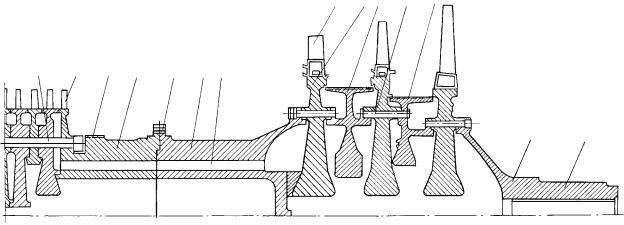
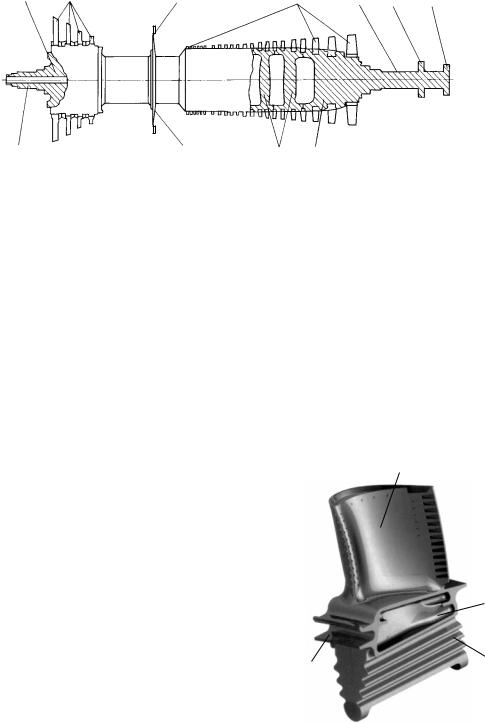
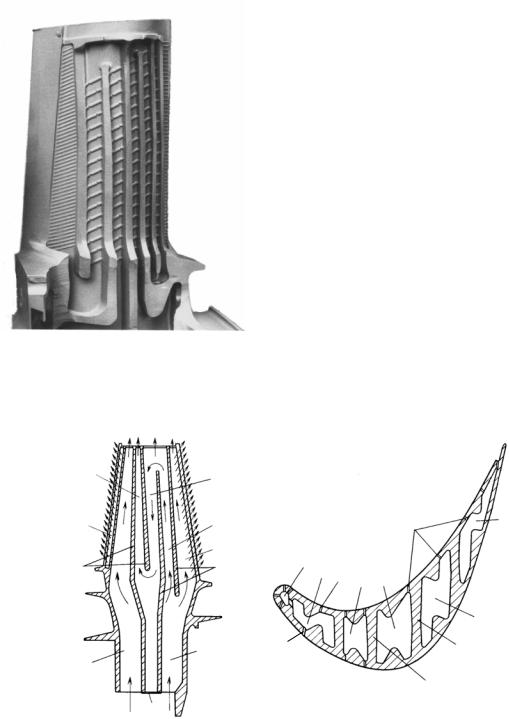
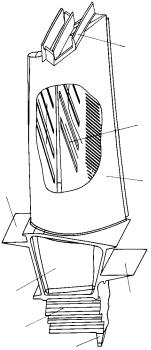
Охлаждающий воздух попадает в лопатку двумя |
|
|
|
|
7 |
|
|
потоками. |
|
|
|
|
|
|
|
Первый поток (примерно 30 % общего расхода |
|
|
|
|
|
|
|
на охлаждение лопатки) поступает в канал 1 (см. |
|
|
|
|
|
|
|
рис. 13.13). Примерно половина этого воздуха идет |
|
|
|
|
|
|
|
в перфорации 10 и 11 в стенках лопатки, остальной |
|
|
|
|
6 |
|
|
|
|
|
|
|
|
||
воздух — в канал 2, а из него — в перфорации, |
|
|
|
|
|
|
|
выполненные на входной кромке. Выходя из этих |
|
|
|
|
|
|
|
отверстий, воздух создает сплошную заградитель- |
|
|
|
|
|
|
|
ную пелену (пленку), отсекающую основной поток |
|
|
2 |
|
1 |
|
|
|
|
|
|
|
|||
|
|
|
|
|
|
|
|
горячих газов от поверхности. Такое охлаждение |
|
|
|
|
|
|
|
называют заградительным или пленочным. |
|
|
|
|
|
|
|
Второй поток охлаждающего воздуха (примерно |
|
|
|
|
|
|
|
70 %) поступает в канал 3 и примерно поровну раз- |
|
|
|
|
|
|
|
водится по каналам 4 и 5. Воздух, протекая через |
|
|
|
|
|
|
|
канал 4 и вытекая из перфораций 9 и щелей в выход- |
|
|
|
|
|
|
|
ной кромке, обеспечивает охлаждение выходной |
|
|
3 |
|
|
|
|
|
|
|
|
|
2 |
|
|
кромки лопатки. Воздух, поступающий в канал 5, |
|
|
|
|
|
||
|
|
|
|
|
|
||
совершает серпантинное движение по каналам 5—7, |
|
|
|
|
|
|
|
вытекает через перфорации 9 в стенках и охлаждает |
|
|
4 |
|
|
|
|
|
|
|
|
|
|
||
среднюю часть лопатки. |
|
|
|
|
5 |
|
|
Перфорации в стенках лопатки представляют |
|
|
|
|
|
|
|
|
|
Рис. 13.14. Рабочая лопатка газовой турбины с интеграль- |
|||||
собой многочисленные |
отверстия (иногда более |
|
|
|
|
|
|
|
|
ным бандажом: |
|
|
|
||
600) небольшого диаметра (0,5—0,6 мм). |
|
|
|
|
|
|
|
|
|
1 — профильная часть; 2 — полки для радиального уплот- |
|||||
Таким образом, в рассмотренной конструкции |
нения; 3 — промежуточный элемент; 4 — елочный хвостовик; |
||||||
лопатки реализовано конвективно-пленочное охлаж- |
5 — стопор осевого смещения лопатки в диске; 6 — вихревая |
||||||
дение. Оно используется в одной-двух первых ступе- |
матрица; 7 — интегральный периферийный бандаж |
|
|||||
нях газовой турбины, где температура газов высокая. |
|
|
|
|
|
|
|
В последующих ступенях применяется только кон- |
ток газовых турбин используются высокопрочные |
||||||
вективное охлаждение воздухом через внутренние |
сплавы на основе никеля (см. ниже). Лопатки изго- |
||||||
|
|
|
|
|
|
||
каналы с выбросом нагретого воздуха через выход- |
тавливают точным литьем по выплавляемым моде- |
||||||
|
|
|
|
|
|
||
ную кромку и отверстия в торце профиля. |
лям в вакууме в целях исключения вредного влия- |
||||||
Рабочие лопатки последней ступени, работаю- |
ния |
на |
материал |
лопатки |
кислорода |
и азота, |
|
|
|
|
|
|
|
||
щие при сравнительно |
низких температурах, не |
содержащихся в воздухе. При обычной технологии |
|||||
|
|
|
|
|
|
||
охлаждаются, так как используемые материалы поз- |
литья |
такого рода |
металл |
отливаемой |
лопатки |
||
|
|
|
|
|
|
||
воляют этого не делать. |
|
затвердевает в направлении от поверхности лопатки |
|||||
|
|
|
|
|
|
|
|
На рис. 13.13 показана рабочая лопатка, не |
к ее оси и приобретает кристаллическую структуру. |
||||||
|
|
|
|
|
|
||
имеющая периферийного бандажа. Такие лопатки |
Каждый из кристаллов при этом обладает разными |
||||||
|
|
|
|
|
|
||
используют в первой ступени, в которой затрудни- |
механическими и физическими свойствами в разных |
||||||
|
|
|
|
|
|
||
тельно организовать его охлаждение. В остальных |
направлениях, однако из-за их хаотичного располо- |
||||||
|
|
|
|
|
|
||
ступенях, как правило, |
рабочие лопатки выпол- |
жения свойства металла лопатки в целом оказыва- |
|||||
|
|
|
|
|
|
||
няют с периферийным |
интегральным бандажом, |
ются одинаковыми во всех направлениях. Поэтому |
|||||
|
|
|
|
|
|
||
обеспечивающим дополнительное демпфирование |
такую структуру называют равноосной. Ее слабым |
||||||
|
|
|
|
|
|
||
на стыках полок бандажа и уменьшающим пери- |
местом |
являются границы (стыки) кристаллов. В |
|||||
|
|
|
|
|
|
||
ферийную утечку. Пример такой лопатки показан |
результате длительная прочность такого |
металла, |
|||||
|
|
|
|
|
|
||
на рис. 13.14. |
|
особенно при повышенных температурах, оказыва- |
|||||
|
|
|
|
|
|
|
|
|
|
ется недостаточной. |
|
|
|
||
Сопротивление рабочих лопаток высоким меха- |
|
|
|
|
|
|
|
ническим нагрузкам, вызванным вращением, изги- |
Стремление к уменьшению вредного влияния |
||||||
бом под действием аэродинамических сил, а также |
границ кристаллов привело к появлению новой тех- |
||||||
неравномерным нагревом и в условиях высоких |
нологии литья, при использовании которой также |
||||||
температур зависит в первую очередь от используе- |
возникает кристаллическая структура, однако сами |
||||||
мого материала и его структуры. Для рабочих лопа- |
кристаллы в лопатке формируются в виде столби- |
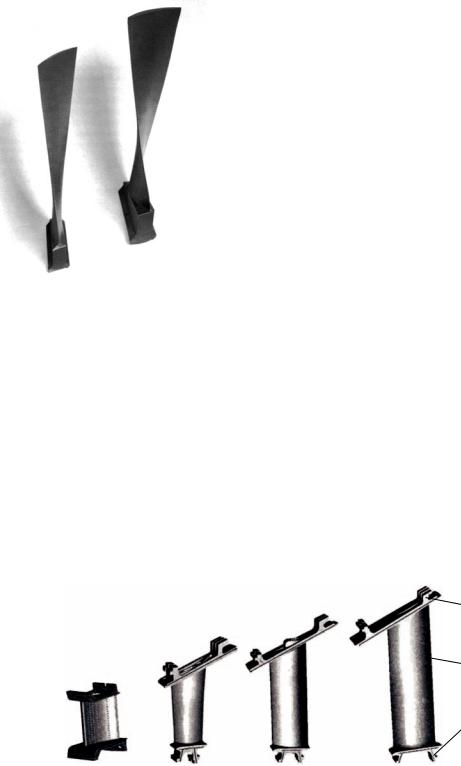
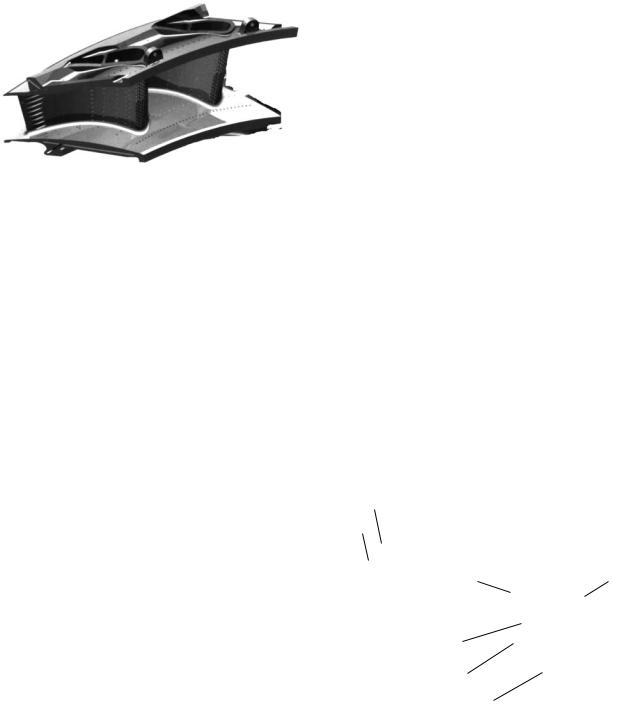
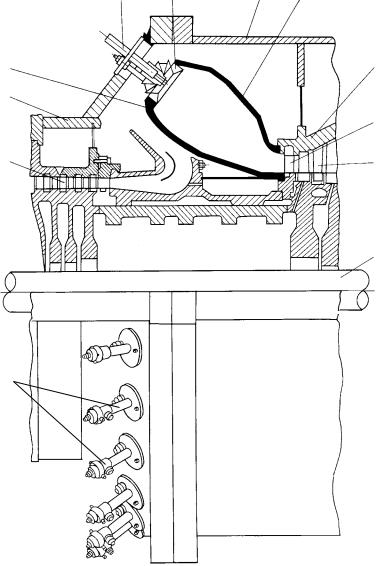
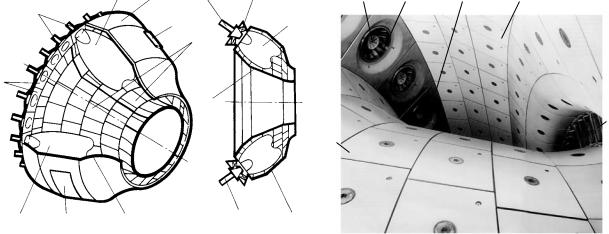