
паровые и газовые турбины для электростанций
.pdf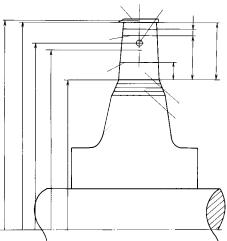
ные воздействия определяют термоциклическую прочность рабочих лопаток.
В условиях воздействия коррозионно-активной среды — загрязненного примесями пара — рабочие лопатки, в особенности лопатки, находящиеся в переходной зоне от перегретого пара к влажному и в условиях первичного влагообразования в паре при статических значительных нагрузках, могут испытывать коррозионное растрескивание под напряжением. Под действием переменных нагрузок в коррозионноактивной среде при колебаниях в рабочих лопатках может наблюдаться коррозионная усталость.
Рабочие лопатки ступеней, находящихся в зоне влажного пара, подвергаются воздействию капель воды, и при этом наблюдается капельно-ударная эрозия рабочих лопаток. Возможна также абразивная эрозия рабочих и сопловых лопаток, возникающая вследствие уноса с паром продуктов коррозии в элементах энергетической установки перед паровой турбиной (в котле, трубопроводах).
При определенных условиях рабочие лопатки подвергаются различным видам коррозии. Различают общую, язвенную коррозию лопаток. Эти виды коррозии поражают не только рабочие лопатки, но и другие элементы тракта. Коррозия возникает преимущественно в период пребывания оборудования в резерве (стояночная коррозия), если не приняты меры по его защите от коррозии.
Растяжение рабочих лопаток. Растягивающее напряжение в произвольном сечении рабочей лопатки (рис. 14.1), вызываемое центробежными
|
|
|
3 |
4 |
1 |
|
|
|
|
F (z1) |
|
dz |
|
|
|
|
|
|
||
|
|
|
|
|
|
|
|
|
|
|
|
1 |
l |
|
|
|
|
|
z |
|
|
|
|
F (z) |
z |
|
|
|
|
|
|
|
|
|
|
|
|
|
|
1 |
|
б |
п |
|
|
|
2 |
|
|
|
|
|
|
||
r |
r |
пр |
ср |
|
|
|
|
|
r |
r |
|
|
|
|
|
|
к |
|
|
|
|
|
|
r |
|
|
|
Рис. 14.1. Схема для определения растягивающих напряже-
ний в рабочих лопатках:
1 — профильная часть; 2 — хвостовик; 3 — периферийный бандаж; 4 — проволочная связь
силами инерции при вращении, определяется очевидным соотношением
σ(z) = N(z)/F(z), |
(14.3) |
где N(z) — растягивающее усилие в сечении с координатой z; F(z) — площадь поперечного сечения с координатой z.
Растягивающее усилие N(z) численно равно суммарной центробежной силе, развиваемой всеми элементами лопатки, находящимися вне сечения F(z), т.е.
N(z) = C + C |
+ C |
, |
(14.4) |
л |
б |
пр |
|
где C — центробежная сила профильной части
л
лопатки, расположенной между сечением площа-
дью F(z) и периферийным сечением площадью F ;
п
C — центробежная сила инерции части бандажа,
б
приходящейся на одну лопатку; C — центробеж-
пр
ная сила инерции проволоки, приходящейся на одну лопатку.
Для определения C (z) найдем вначале центро-
л
бежную силу инерции, действующую на элемент
лопатки длиной dz (см. рис. 14.1):
1
dC = ρω2(r + z )F(z )dz ,
л к 1 1 1
где ρ — плотность материала лопатки; ω — угловая
скорость вращения ротора; r — корневой радиус
к
рабочей лопатки; z — расстояние от корня (пере-
1
менная интегрирования); F(z ) — площадь попереч-
1
ного сечения с координатой z ; dz — длина эле-
1 1
мента лопатки.
Для получения C проинтегрируем dC в преде-
л |
л |
лах от z |
= z до z |
= l, в результате получим |
|
|||
1 |
1 |
|
|
|
|
|
|
|
|
|
l |
|
|
|
Cл(z) = ρω |
2 |
∫F(z |
1)(rк + z1)dz1 . |
(14.5) |
|
|
|
|
|
z |
|
|
Величины C |
и |
C , |
очевидно, выражаются |
|||
|
б |
|
|
пр |
|
|
зависимостями:
C = ρ ω2f t r ;
бб б б б
C |
= ρ ω2f |
t |
r , |
(14.6) |
пр |
пр |
пр пр |
пр |
|
где ρ , ρ — плотности материала связей (соот-
бпр
ветственно бандажа и проволоки); f , f — пло-
б пр
щади поперечного сечения связей; t , t — шаги по
б пр
окружности связей; r , r — радиусы центров
бпр
поперечных сечений связей (см. рис. 14.1).
В общем случае C по (14.5) находят численно
л
после аэродинамического профилирования лопатки и определения зависимости F(z). В случае коротких
441
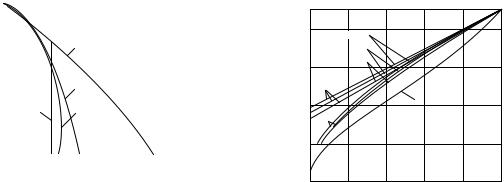
лопаток, т.е. когда d / l > 10…12, обычно F(z) = F =
cр
= const, и тогда напряжения в лопатке без связей
|
|
C (z) |
|
|
l |
|
|
|
||
|
|
|
|
|
|
|
|
|||
σл |
|
л |
|
2 |
∫(rк + z1)dz1 = |
|||||
(z) = |
-------------- |
= ρω |
||||||||
|
|
F |
|
|
|
|
|
|
||
|
|
|
|
|
|
|
z |
|
|
|
|
=ρω2 |
|
|
|
|
|
l2 – z2 |
|
|
|
|
r (l – z) |
|
|
|
||||||
|
+ |
--------------- |
. |
|||||||
|
|
|
|
к |
|
|
|
2 |
|
|
|
|
|
|
|
|
|
|
|
|
|
|
|
|
|
|
|
|
|
|
|
|
После элементарных преобразований получим распределения напряжений в лопатке постоянного сечения по ее длине в виде
σ (z) = σ (1 – ζ)(1 + ζ/θ), |
(14.7) |
л0
где σ — растягивающее напряжение в корневом
0
сечении рабочей лопатки без связей; ζ = z / l; θ = = d / l — обратная веерность рабочего венца; d —
cр |
|
|
|
cр |
средний диаметр рабочего венца. |
|
|||
Величина |
|
|
|
|
|
|
σ = ρω2r l, |
(14.8) |
|
|
|
0 |
cр |
|
где r |
= 0,5(r |
+ r ) — средний радиус рабочего |
||
cр |
п |
к |
|
|
венца (см. рис. 14.1); r , r |
— корневой и перифе- |
|||
|
|
к |
п |
|
рийный радиусы рабочего венца.
Распределение напряжений в этом случае при θ = 3 (длинная лопатка) представлено на рис. 14.2 (кривая 1 ).
Для снижения растягивающих напряжений при
d / l < 10 лопатки выполняют переменного про-
cр
филя с уменьшающейся от корня к периферии площадью сечения.
Для лопаток средней веерности, т.е. (примерно)
при условии 6 < d / l < 10, применяют линейный
cр
закон изменения площади: |
|
F(z) = F [1 – (1 – a)ζ], |
(14.9) |
к |
|
z/l |
|
|
|
|
|
|
|
|
|
|
|
|
|
|
|
0,8 |
|
|
|
|
|
|
|
|
|
|
1 |
|
|
|
|
|
|
|
|
|
|
|
|
0,6 |
|
|
|
|
|
|
|
|
|
|
2 |
|
|
|
|
0,4 |
|
|
|
|
|
|
|
|
|
|
|
|
|
|
|
|
4 |
|
3 |
|
|
|
|
0,2 |
|
|
|
|
|
||
|
|
|
|
|
|
|
|
|
|
|
|
|
|
|
|
|
|
|
|
|
|
|
|
0 |
0,2 |
0,4 0,6 0,8 / 0 |
|||||
Рис. 14.2. Распределения |
растягивающих напряжений по |
длине лопаток с различными законами изменения площади
сечения при F /F = 0,125, = 3:
пк
1 — постоянная площадь сечения; 2 — линейный закон; 3 —
показательный закон; 4 — лопатка равной прочности
где a = F /F ; F , F — площади поперечного сече-
п к п к
ния лопатки на периферии (z = l) и у корня (z = 0) соответственно.
Для лопаток большой длины, т.е. при d |
/ l < 5…6, |
cр |
|
часто применяется показательный закон: |
|
F(z) = F æaζ. |
(14.10) |
к |
|
Для произвольного закона F(z) вводят понятие коэффициента разгрузки, определяемого отношением
|
k = σ |
/ σ , |
(14.11) |
|
макс |
0 |
|
где σ |
— наибольшее напряжение в лопатке |
||
|
макс |
|
|
переменного сечения; σ — напряжение в корневом
0
сечении лопатки постоянного профиля [см. (14.8)]
при тех же значениях r и l, что и для лопатки
ср
переменного сечения.
Принимая законы — линейный (14.9) и показательный (14.10) и используя общую зависимость
(14.5), можно определить σ |
в лопатке. В каче- |
|
макс |
стве примера на рис. 14.2 показаны распределения растягивающих напряжений при этих законах изменения площади сечения для длинной лопатки с параметрами θ = 3, a = 0,125 в сравнении с лопаткой постоянного сечения. Из сравнения видно, что для рассматриваемой длинной лопатки, у которой площадь поперечного сечения в 8 раз меньше площади корневого сечения, максимальное растягива-
ющее напряжение составляет σ |
= 0,5σ |
для |
|
|
макс |
0 |
|
линейного закона и σ |
≈ 0,4σ |
для показатель- |
|
|
макс |
0 |
|
ного закона, т.е. в 2 и 2,5 раза меньше, чем в лопатке постоянного сечения при тех же значениях
rи l.
ср
На рис. 14.3 представлены графики для определения коэффициента разгрузки, вычисленного указанным способом для практического диапазона параметров a и θ.
k
0,9
0,7
θ =10,0 5,0 2,5
1
3
0,5
2
0,3
0,1
0 |
0,2 |
0,4 |
0,6 |
0,8 Fп/Fк |
Рис. 14.3. Зависимости коэффициента разгрузки от F /F и θ:
п к
1 и 2 — линейный и показательный законы изменения площади
сечения лопаток; 3 — лопатка равной прочности
442
Пользуясь графиками k(a, θ) (рис. 14.3), можно найти максимальное растягивающее напряжение в лопатке переменного сечения по зависимости
|
2 |
|
|
|
σ |
= ρ ω r |
l k (F |
/ F , d |
/ l ). (14.12) |
макс |
cр |
п |
к |
cр |
На рис. 14.2 (линия 4) и 14.3 (кривая 3) показаны данные для так называемой лопатки равной прочности. Так условно называется лопатка, площадь поперечного сечения которой изменяется по следующим законам: на участке
0 ≤ ζ ≤ ζ
*
площадь поперечного сечения определена так, что растягивающее напряжение постоянно, а на участке
ζ ≤ ζ ≤ 1
*
лопатка имеет постоянную площадь поперечного сечения.
Величина ζ — граница участков. Лопатка рав-
*
ной прочности — предельная лопатка, для которой коэффициент разгрузки имеет минимальное значение из всех возможных законов изменения площади сечения по длине лопатки.
На практике реальные законы изменения площади близки к рассмотренным: постоянной площади, линейному или показательному закону.
Определение максимальных растягивающих напряжений в рабочих лопатках паровой турбины становится значимым по крайней мере в двух случаях.
Первый случай связан с проблемой повышения мощности конденсационных и теплофикационных турбин, приходящейся на один поток. Эта проблема рассмотрена в § 5.2.
Учитывая, что ометаемая площадь последней ступени
Ω = 2πr l , |
(14.13) |
|
|
cр |
|
и используя (14.12), получаем зависимость |
|
|
Ω = 2πσ |
2 |
|
/ ( k ρ ω ), |
(14.14) |
макс
из которой следует, что для повышения Ω и, следовательно, мощности, приходящейся на один поток, необходимо: 1) выбирать материалы с максималь-
ным отношением σ / ρ; 2) профилировать рабо-
макс
чие лопатки с минимальным k, для чего следует приближаться насколько это возможно к лопатке равной
прочности и |
выбирать малые значения |
F / F |
= |
|
|
|
|
п к |
|
= 0,1…0,15; |
3) применять |
тихоходные турбины |
с |
|
n = 25 с–1. |
|
|
|
|
н |
|
|
|
|
Максимальные допустимые значения σ |
при- |
|||
|
|
|
макс |
|
нято выбирать по условию |
|
|
|
|
|
σмакс = σ |
0,2 ⁄ ns , |
(14.15) |
где σ — предел текучести материала при рабочей
0,2
температурe; ns — коэффициент запаса по пределу текучести, обычно выбираемый в пределах ns = = 1,5…2,5.
Выбор значений ns обусловлен в основном тем,
что согласно рекомендациям МЭК (Международной электротехнической комиссии) любая турбина без необратимых последствий должна быть способна выдержать кратковременное повышение частоты вращения до n = 1,2 n , где n — номинальная час-
нн
тота вращения. Увеличение частоты вращения в 1,2 раза означает повышениe растягивающих напряжений в любых лопатках (также и в лопатках
со связями) в 1,22 = 1,44 раза. Таким образом, требование ns ≥ 1,5 означает, что при повышении час-
тоты до 1,2 n номинальное напряжение (без учета
н
коэффициента концентрации напряжений в галтелях — переходах от профиля к хвостовику) не достигнет предела текучести материала лопаток. Для гарантии обычно выбирают ns ≥ 2.
Второй случай, когда выбор растягивающих напряжений в рабочих лопатках является значимым, относится к лопаткам первой ступени ЧСД турбины с промежуточным перегревом пара большой мощности (500, 800 и 1200 МВт).
Лопатки эти имеют уже значительную длину (l > 100 мм) и высокую температуру металла (более 520 °С), при которой обнаруживается ползучесть материала. Они должны отвечать требованиям длительной прочности:
σ |
≤ σ |
/ n , |
(14.16) |
макс |
д.п |
д.п |
|
где σ — предел длительной прочности при рабо-
д.н
чей температуре для ресурса τ = 105 или 2æ105 ч
(для P = 0,5); n = 1,3…1,6 — коэффициент запаса
д.п
по длительной прочности для вероятности неразрушения P = 0,5 (см. § 14.4).
Рассмотрим два примера, относящихся к проблеме прочности лопаток при действии растягивающих напряжений в двух названных случаях.
Пример 14.1. На Ермаковской ГРЭС (Казахстан) 5 декабря 1972 г. произошла авария турбоагрегата мощностью 300 МВт с турбиной К-300-23,5, в результате которой валопровод был разрушен в шести сечениях, разрушены были также совмещенный ЦСНД и ЦНД турбины.
Авария началась с отключения от сети системой защиты электрического генератора. При отключении генератора от сети одновременно дается сигнал на закрытие регулирующих и стопорных клапанов, однако эта команда не была выполнена, и валопровод турбоагрегата пошел в разгон с характерным нарастающим гулом.
Впроцессе разгона начали отрываться рабочие лопатки последних ступеней всех трех потоков, пробивая насквозь стенки наружного корпуса ЦНД в районе расположения последних ступеней.
Внекоторый момент разгона нарастающий гул прекратился, машина «притихла». Как выяснилось потом, регулирующие и стопорные клапаны закрылись и начался выбег валопровода.
443
Анализ последствий аварии показал, что в процессе разгона были оборваны многие рабочие лопатки последних ступеней, а именно, в третьем потоке (близком к генератору) оборвалось 35 лопаток, в первом и втором потоках — по 14—15 лопаток.
Разрушение всех лопаток имеет силовой характер, т.е. оно произошло вследствие действия растягивающих усилий в сечениях на расстоянии около 350 мм от корневого. По данным завода-изготовителя, в этом сечении растягивающие напряжения максимальные и при номинальной ско-
рости вращения n = 50 с–1 составляют σ |
≈ 400 МПа |
н |
макс |
(сравните с кривой 3 на рис. 14.2). |
|
Многие лопатки последних ступеней вытянулись на 20—25 мм, некоторые — на 70 мм. На некоторых лопатках появилась шейка — утонение — в наиболее нагруженном сечении, подобно утонению образца при испытаниях материала для определения его механических характеристик.
Рассматриваемые лопатки выполнены из стали 15Х12ВНМФШ.
Основные параметры лопаток следующие: длина
рабочей части l = 1050 мм; средний диаметр d = 2,55 м
ср
(Ω = 8,41 м2); хвостовик елочного типа с торцевой заводкой лопаток, выполненный по дуге окружности; имеется одна демпферная связь на расстоянии около 0,9l от корня.
Хорда лопатки в корневом сечении b ≈ 180 мм, ширина обода диска равна около 230 мм.
Центробежная сила инерции профильной части лопатки составляет 1280 кН (~130 тс), число лопаток на колесе — 104, суммарные напряжения (растяжение + + изгиб) — около 420 МПа.
За счет снятия свисающей выходной кромки в корневом сечении повышен в 2 раза конструктивный предел усталости рабочих лопаток.
По данным контрольных испытаний образцов, изготовленных из материала лопаток, механические характеристики при температуре 20 °С соответствовали техни-
ческим условиям: предел текучести σ = 650…750 МПа,
0,2
предел прочности (временное сопротивление) σ =
в
= 800…900 МПа.
Используя сведения о характере разрушения рабочих лопаток при разгоне ротора, приведенные данные о рабочих напряжениях и механические характеристики материала, требуется установить максимальную частоту вращения, которая была достигнута при разгоне перед тем, как закрылись клапаны.
Решение. Растягивающие напряжения в рабочих лопатках согласно (14.5), (14.6) пропорциональны квадрату частоты вращения, т.е. при произвольной частоте вращения имеем соотношение
|
|
n |
|
2 |
|
σ(n) = σ |
----- |
|
, |
(14.17) |
|
|
н |
n |
|
|
|
|
|
|
|
н
где σ(n) — растягивающее напряжение в любой точке
лопатки при любой частоте вращения n; σ — растягива-
н
ющее напряжение при номинальной частоте n .
н
Применим это соотношение к сечению рабочей лопатки, где номинальное напряжение имеет максималь-
ное значение σ = 400 МПа и где произошло разрушение
н
лопаток при разгоне. В момент разрушения напряжения в лопатках, надо полагать, как раз равнялись, по определе-
нию, временному сопротивлению σ |
= 800…900 МПа |
|||||||
|
|
|
|
|
|
в |
|
|
(для разных лопаток). Полагая в (14.17) σ(n) = σ , σ |
= |
|||||||
|
|
|
|
|
|
|
в |
н |
= 400 МПа и разрешая его относительно n, имеем |
|
|||||||
|
|
|
|
|
σв |
1 ⁄ |
2 |
|
|
|
|
|
|
|
|
|
|
|
n = n |
|
= n |
----- |
. |
|
||
|
|
разр |
н |
σн |
|
|
|
|
Подставляя численные значения, получаем |
|
|||||||
|
|
|
|
800…900 |
1 ⁄ 2 |
|
||
n |
|
= 50 |
------------------------ |
|
= |
|
||
разр |
|
|
|
|||||
|
|
400 |
|
|
||||
|
|
|
|
|
|
=70,7…75 с–1 = 4243…4500 мин–1.
Впроцессе разгона ротора были разрушены далеко не все лопатки. Всего на трех потоках общее число рабочих лопаток более 300, а разрушено было около 65 лопаток. Поэтому можно считать, что частота вращения, достигнутая при разгоне, лежит в пределах
4250 < n < 4500 мин–1,
разр
ближе к меньшему значению.
Отметим, что в данном случае коэффициент запаса по пределу текучести в рабочих лопатках в соответствии с
(14.15) составляет |
|
|
|
|
σ |
650…750 |
|
|
0,2 |
|
|
ns |
= ------------ |
= ------------------------ |
= 1,62…1,87, |
|
σ |
400 |
|
|
макс |
|
|
значение n |
укладываeтся в рекомендуемые пределы, |
||
s |
|
|
|
поэтому лопатка отвечает требованиям кратковременной прочности, что полностью подтверждается результатами случившейся аварии.
Пример 14.2. Для рабочих лопаток первой ступени ротора СД турбины К-500-23,5 известны следующие дан-
ные: |
|
|
|
|
|
|
|
материал лопаток — сталь 15Х12ВНМФШ (ЭИ802); |
|
||||||
средний радиус рабочих лопаток r |
= 0,635 м; |
|
|
||||
|
|
ср |
|
|
|
|
|
длина рабочей части l = 0,12 м; |
|
|
|
|
|
||
площадь |
корневого |
поперечного |
сечения |
F |
= |
||
|
|
|
|
|
|
к |
|
= 17,86æ10 – 4 м2; |
|
|
|
|
|
|
|
площадь периферийного поперечного |
сечения F |
= |
|||||
|
|
|
|
|
|
п |
|
= 0,5F ; |
|
|
|
|
|
|
|
к |
|
|
|
|
|
|
|
площадь поперечного сечения бандажа f |
= 4,8æ10–4 м2; |
||||||
|
|
|
|
б |
|
|
|
радиус центра тяжести сечения бандажа r |
= 0,698 м; |
||||||
|
|
|
|
б |
|
|
|
число рабочих лопаток на колесе z |
= 76; |
|
|
|
|||
|
|
л |
|
|
|
|
|
плотность |
материала |
лопатки и бандажа |
ρ = |
ρ |
= |
||
|
|
|
|
|
|
б |
|
= 7850 кг/м3; предел длительной прочности материала лопатки при
температуре T = 550 °С на ресурс τ = 105 ч σ > 160 МПа
д.п
(по справочникам для стали, термически обработанной на
σ= 500 МПа).
0,2
444
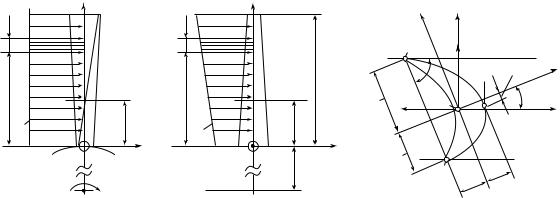
Требуется: а) определить максимальное растягивающее напряжение в корневом сечении рабочей лопатки; б) найти коэффициент запаса по длительной прочности для этого сечения.
Решение. Рассчитаем напряжение в корневом сечении лопатки без учета бандажа по формуле (14.12), где коэффициент разгрузки следует определить по кривой 1 (см. рис. 14.3), предполагая, что площадь сечения лопатки меняется по линейному закону.
Для данного случая F /F = 0,5,
пк
θ= d / l = 2æ0,635/0,12 = 10,58,
cp
c использованием этих данных по рис. 14.3 находим k = 0,755.
Теперь по (14.12) получаем
σ= kρω2r l = 0,755æ7850æ(314,16)2æ0,635æ0,12 =
макс |
cр |
|
|
|
|
=44,6æ106 Па = 44,6 МПа. |
|||
Центробежная сила бандажа |
по формуле (14.6) |
|||
с некоторым ее преобразованием составляет |
||||
|
|
2π |
|
|
|
C |
= ------ ρ(ωr )2f |
= |
|
|
б |
z |
б |
б |
|
|
|
|
л
2π
=------ æ7850 (314,16æ0,698)2æ4,8æ10–4 = 14 979 Н. 76
Дополнительное напряжение в корневом сечении от центробежной силы бандажа
Δσ = C /F = 14 979/(17,86æ10–4) =
бб к
= 8,4æ106 Па = 8,4 МПа.
Полное растягивающее напряжение в корневом сечении
σ= σ + Δσ = 44,6 + 8,4 = 53,0 МПа.
рмакс б
Рассчитаем коэффициент запаса по длительной прочности по (14.16)
n= σ ⁄ σ > 160 ⁄ 53 > 3 .
д.п д.п р
Коэффициент запаса по длительной прочности существенно выше нормативного, равного 1,3—1,6. Кроме того,
значения σ |
> 160 МПа относятся к температуре |
|
д.п |
металла 550 °С. В действительности температура материала лопатки составляет примерно 520 °С, поэтому длительная прочность рабочих лопаток первой ступени ротора СД турбины К-500-23,5 ХТЗ обеспечена с боль-
шим запасом: n > 3 (при этом не учитывается влияние
д.п
концентрации напряжений в галтельном переходе от профиля к хвостовику).
Изгиб рабочих лопаток. Рабочие лопатки подвергаются действию аэродинамических поперечных сил, вызывающих их изгиб. Как уже отмечалось, аэродинамические силы, действующие на рабочие лопатки, имеют стационарные и переменные составляющие. Также уже отмечалось, что для прочности рабочих лопаток особенно значимы переменные (быстро меняющиеся) воздействия, так как именно они вызывают колебания и усталостные поломки рабочих лопаток.
Стационарные аэродинамические усилия хотя и влияют на кратковременную прочность рабочих лопаток, но это влияние мало и, как правило, не является значимым. Между тем, напряжения стационарного изгиба представляются существенными характеристиками прочности, потому что переменные аэродинамические усилия и переменные напряжения в рабочих лопатках оказываются прямо пропорциональны статическим изгибным напряжениям. Поэтому следует рассмотреть способ определения напряжений изгиба лопатки за счет стационарных аэродинамических сил.
На рис. 14.4 показаны окружные и осевые аэродинамические усилия, действующие на рабочую лопатку (без связей — для простоты рассмотрения). Погонные нагрузки в окружном qx(z) и осевом qy(z)
направлениях определяются в результате теплового
|
z |
1 |
|
dz |
|
1 |
|
z |
|
qx |
z |
|
|
|
x |
|
|
|
а) |
|
z |
1 |
|
dz |
|
|
l |
1 |
2 |
z |
|
|
|
|
z |
|
qy |
|
y |
|
к |
|
r |
|
б) |
|
y |
|
|
|
2 |
– |
|
|
|
My |
|
|
|
|
a |
3 |
– |
3 |
|
|
|
|||
|
y |
|
||
– |
|
|
|
|
Mx |
0 |
|
|
|
|
|
|
||
|
|
|
|
x |
– 1 a
1 |
|
|
|
3 |
|
|
|
|
|
– 1 |
|
в)
Рис. 14.4. Аэродинамические (паровые, газовые) усилия, действующие на рабочую лопатку:
а — окружные усилия q ; б — осевые усилия q ; в — профиль рабочей лопатки в сечении z
x |
y |
445

расчета ступени турбины (см. § 2.3) и могут быть представлены в виде:
|
q |
|
= ρ w |
|
(w |
|
|
– w |
)t ; |
(14.18) |
|||
|
|
x |
|
2 |
2a |
|
1u |
|
2u |
2 |
|
|
|
q |
= ρ w |
|
(w |
– w |
|
)t |
+ (p |
– p )t , |
(14.19) |
||||
y |
2 2a |
1a |
|
2a |
|
2 |
|
1 |
2 2 |
|
где ρ — плотность рабочей среды за рабочими лопат-
2
ками; w a, w u — осевая и окружная составляющие
1 1
относительной скорости потока перед рабочими
лопатками; w a, w u — осевая и окружная составляю-
2 2
щие относительной скорости потока за рабочими лопатками; p , p — статическое давление соответ-
12
ственно перед рабочими лопатками и за ними. Предположив нагрузки qx(z) и qy(z) известными
из теплового расчета, найдем изгибающие моменты в произвольном сечении лопатки z: My(z) — под
действием нагрузки qx и Mx(z) — под действием нагрузки qy (см. рис. 14.4, а, б) по зависимостям:
l
My(z) = |
∫qx(z |
1)(z |
1 |
– z)dz |
1 |
; |
(14.20) |
|
z |
|
|
|
|
|
|
|
l |
|
|
|
|
|
|
Mx(z) = |
∫qy(z |
1)(z |
1 |
– z)dz |
1 |
, |
(14.21) |
|
z |
|
|
|
|
|
|
где My(z) — изгибающий момент в сечении z относительно оси y; Mx(z) — изгибающий момент в сечении z относительно оси x (см. рис. 14.4, в).
Смысл зависимости (14.20) определяется тем, что под интегралом записан момент от элементар-
ной нагрузки qx(z )dz на плече z – z, где z —
1 1 1 1
переменная интегрирования, и он должен быть вычислен в пределах от z до l. Аналогично записано и второе соотношение для момента Mx(z) [см.
(14.21)].
Окружное усилие qx(z) для всех реальных ступе-
ней обычно близко к постоянному значению по длине лопатки, осевое усилие qy(z) для лопаток
большой вeерности существенно переменно и возрастает от корня к периферии в основном вслед-
ствие влияния второго члена, в котором как p – p ,
1 2
так и t растут от корня к периферии. Для ступеней
2
с лопатками умеренной длины (θ > 10…12) допустимо не только qx, но также и qy считать величиной
постоянной, вычисленной по параметрам для среднего радиуса. При этом по (14.20), (14.21) найдем изгибающие моменты в корневом сечении (z = 0):
l |
|
My к = ∫qx(z1)dz1 = qxl2 ⁄ 2 = Rul ⁄ 2 ; |
(14.22) |
0 |
|
Mx к = qyl2 ⁄ 2 = Ral ⁄ 2 , |
(14.23) |
где Ru, Ra — окружное и осевое усилия, действую-
щие на рабочую лопатку, |
|
|
|
|
|
|
Ru = qx l; Ra = qy l. |
(14.24) |
|||
Окружное усилие Ru можно определить из соот- |
|||||
ношения для мощности ступени |
|
||||
|
N = R |
u |
u |
z , |
|
|
о.л |
cр |
л |
|
|
где u |
= ω r — окружная скорость на среднем |
||||
ср |
ср |
|
|
|
|
радиусе ступени; z — число лопаток на колесе.
л
Учитывая (14.22) и (14.23), имеем
|
N |
l |
|
о.л |
|
My к = |
---------------- . |
|
|
2u |
z |
|
ср |
л |
Здесь N — мощность ступени «на ободе лопа-
о.л
ток».
Если учесть дополнительные потери от утечек и
влажности, то вместо |
N |
следует |
использовать |
|
|
|
о.л |
|
|
мощность Ni за вычетом этих потерь. Тогда |
||||
|
|
Nil |
|
|
M ′ |
= |
---------------- . |
(14.25) |
|
y к |
|
2u |
z |
|
|
|
|
||
|
|
ср |
л |
|
Для определения изгибных напряжений в любом поперечном сечении z необходимо вначале найти изгибающие моменты относительно центральных главных осей η и ξ (см. рис. 14.4, в). Моменты M ,
|
|
|
|
|
|
|
|
η |
M получаем, проектируя векторы-моменты |
|
|
|
|||||
M y и |
||||||||
|
ξ |
|
|
|
|
|
|
|
|
|
|
|
|
|
|||
M x на центральные главные оси η и ξ: |
|
|
|
|||||
|
|
M = M |
cosβ + M |
sinβ; |
|
|
|
|
|
|
η |
y |
x |
|
(14.26) |
||
|
|
|
|
|
Mξ = Mysinβ – Mxcosβ,
где β — угол между осью x и главной осью ξ.
С достаточной точностью можно принимать, что центральная главная ось η параллельна линии, соединяющей точки 1 и 2, т.е. примерно параллельна направлению хорды профиля. Положитель-
ное направление векторов-моментов M y и M x
(см. рис. 14.4, в) соответствует следующему правилу: изгибающий момент в сечении лопатки (с внешним направлением оси z) считается положительным, когда он обусловлен положительной силой, действующей на отсеченную часть лопатки.
При описанных условиях изгибающие напряжения в любой точке сечения лопатки в соответствии с правилом сопротивления материалов определяются по закону косого изгиба стержня по зависимости
|
|
M |
M |
|
|
|
|
η |
ξ |
|
|
σ |
и |
= – ------- |
ξ + ------- |
η , |
(14.27) |
|
I |
I |
|
|
|
|
|
η |
ξ |
|
|
где η, ξ — координаты точки сечения лопатки, для
которой вычисляются напряжения изгиба; I , I —
η ξ
моменты инерции сечения профиля лопатки отно-
446
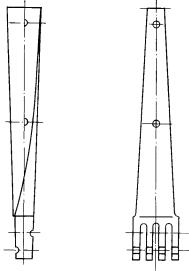
сительно центральных главных осей η и ξ. Часто используются обозначения (см. табл. 3.1)
I |
= I |
, I = I |
. |
η |
мин |
ξ |
макс |
Обычно напряжения изгиба определяют в трех «опасных» точках 1, 2 и 3 (см. рис. 14.4, в).
В точках 1 и 2 имеем растягивающие (положительные) напряжения статического изгиба, в точке 3 — сжимающие (отрицательные) напряжения статического изгиба. Как правило, наибольшие напряжения изгиба наблюдаются в точке 1, так как для этой точки складываются положительные напряжения
изгиба, вызываемые моментами M и M .
η ξ
В точке 2 момент M вызывает положительные
η
напряжения, а момент M — отрицательные напря-
ξ
жения. По общей формуле (14.27) для точки 1 имеем
|
|
M |
|
M |
|
|
|
η |
|
ξ |
|
|
σ = |
W--------------- |
– |
----------------- , |
(14.28) |
|
и1 |
|
W |
|
|
|
|
мин1 |
|
макс1 |
|
где |
|
|
|
|
|
|
I |
|
|
|
I |
|
|
мин |
|
|
макс |
W |
= – ---------- |
, W |
= – |
----------- (14.29) |
|
|
мин1 |
ξ |
макс1 |
η |
|
|
|
|
|
||
|
|
1 |
|
|
1 |
— моменты сопротивления для точки 1, значения
Wдля некоторых типовых профилей даны в
мин1
табл. 3.1.
Аналогично для точек 2 и 3 получим зависимости:
|
M |
M |
|
|
|
|
η |
ξ |
|
|
|
σ = --------------- |
+ ---------------- |
; |
|
|
|
и2 |
W |
W |
|
|
|
|
мин2 |
макс2 |
|
|
|
|
|
|
|
|
(14.30) |
|
M |
M |
|
|
|
ηξ
σ= – --------------- – ---------------- ,
и3 W W
мин3 макс3
где
Wмин2 = – Iмин ⁄ ξ2; |
Wмакс2 = Iмакс ⁄ η2; |
|
||||
|
|
|
|
|
|
(14.31) |
W |
= I ⁄ ξ ; W |
= –I |
⁄ η . |
|
|
|
мин3 |
мин 3 |
макс3 |
макс |
3 |
|
|
Значения I, W, F в справочниках относятся к определенному характерному размеру профиля
(чаще всего к определенному размеру хорды b ).
м
Если масштаб профиля m = b /b , где b , b —
н м |
н м |
размер хорды истинного и модельного профиля соответственно, то геометрические характеристики профиля с модельных значений на истинные (натурные) пересчитываются по очевидным соотношениям:
I = m4I ; |
W = m3W ; |
F = m2F ; |
|||
н |
м |
н |
м |
н |
м |
здесь индексами «н» и «м» отмечены соответственно натурные и модельные моменты инерции, моменты сопротивления, площади сечения.
Определение статических напряжений аэродинамического изгиба выполняется для того, чтобы про-
извести сравнение их с допустимыми напряжениями на изгиб. Последние установлены в стационарном турбостроении как одна из мер обеспечения вибрационной надежности рабочих лопаток. Принимается, что изгибные напряжения должны удовлетворять условию
σ ≤ σ , |
(14.32) |
ии.д
где σ — напряжение аэродинамического изгиба в
и
опасной точке 1, 2 или 3, рассчитанное по приве-
денным формулам (14.28)—(14.30); σ — допус-
и.д
каемое напряжение на изгиб.
Многолетний опыт эксплуатации паровых турбин позволил установить следующие допускаемые напряжения на изгиб: для активных ступеней с пол-
ным подводом пара σ ≤ 30…35 МПа; для реак-
и.д
тивных ступеней с полным подводом пара σ ≤
и.д
≤ 70…100 МПа; для ступеней с парциальным подводом пара (в частности, для регулирующих ступе-
ней) σ ≤ 10…15 МПа.
и.д
Причины выбора столь малых допускаемых напряжений на изгиб будут рассмотрены в параграфе, посвященном колебаниям и усталости лопаток.
Определение напряжений статического изгиба в рабочих лопатках рассмотрим на конкретном примере.
Пример 14.3. Последняя ступень ЦНД турбины
Т-100/120-12,8 ТМЗ с рабочей лопаткой размерами d = cр
= 1,915 м, l = 0,55 м (рис. 14.5) имеет следующие характеристики при номинальном конденсационном режиме:
мощность ступени с учетом потерь от утечек и влаж-
ности N = 4315 кВт; i
давление перед ступенью p = 20,9 кПа;
0
Рис. 14.5. Эскиз рабочей лопатки последней ступени ЦНД
турбины Т-110/120-12,8 ТМЗ
447
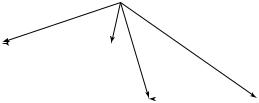
давление за соплами на среднем радиусе p = 13,93 кПа;
1
давление за ступенью p = 5,64 кПа;
2
плотность пара ρ = 0,04515 кг/м3.
2
Треугольники скоростей на среднем радиусе определяются следующими значениями составляющих:
w= 24 м/с;
1u
w= –386 м/с;
2u
w= 113,5 м/с;
1a
w= 270,5 м/с;
2a
u= ωr = 300,8 м/с.
cр cр
Треугольники скоростей представлены на рис. 14.6.
Число рабочих лопаток на колесе z = 94.
л
Геометрические параметры корневого сечения рабочей лопатки следующие.
Угол поворота корневого сечения (угол между осями x и ξ, см. рис. 14.4, в) β = 2,3°.
Моменты инерции
I= I = 10,827æ10–8 м4,
мин η
I= I = 93,766æ10–8 м4.
макс ξ
Координаты «опасных» точек 1, 2, 3 (см. рис. 14.4)
–ξ |
= 22,9æ10–3 м, |
–η |
= 57,283æ10–3 м, |
|
1 |
1 |
|
–ξ |
= 23,303æ10–3 м, |
η |
= 52,780æ10–3 м, |
|
2 |
2 |
|
ξ |
= 16,0æ10–3 м, |
η |
= 0. |
|
3 |
3 |
|
Требуется рассчитать |
напряжения статического |
изгиба в «опасных» точках.
Решение. Рассчитаем изгибающие моменты в корне-
вом сечении рабочей лопатки. Изгибающий момент M
у к
найдем по зависимости (14.25): |
|
|
||
Nil |
4315æ103æ0,55 |
|
|
|
My к = --------------- |
= ---------------------------------------- |
= 42 |
Нæм. |
|
2u |
z |
2æ300,8æ94 |
|
|
|
ср л |
|
|
|
Изгибающий |
момент M рассчитаем |
по формуле |
||
|
|
х к |
|
|
(14.23), полученной в предположении, что усилие q (z)
|
|
|
|
|
|
|
|
y |
постоянно и равно усилию на среднем радиусе: q |
= q . |
|||||||
|
|
|
|
|
|
y |
|
y cр |
Для этого по (14.19) получим |
|
|
|
|
||||
|
q = ρ w (w – w )t + (p – p )t = |
|
|
|||||
|
y |
2 2a 1a |
2a 2 |
1 2 2 |
|
|
||
|
= 0,04515æ270,5(113,5 – 270,5)æ0,064 + |
|
|
|||||
c1 |
w |
1 |
|
|
|
|
|
|
|
|
|
|
|
|
|
|
|
|
u |
|
|
|
|
|
|
|
|
|
|
|
c |
2 |
|
w2 |
|
|
|
|
|
|
|
|
|
u
Рис. 14.6. Треугольники скоростей на среднем радиусе лопа-
ток, u = 301 м/с
+ (13,93 – 5,64)æ103æ0,064 = –122,7 + 530,6 = 407,9 Н/м,
|
πd |
cр = |
πæ1,915 |
|
где |
t = ---------- |
= 0,064. |
||
|
z |
|
94 |
|
2
л
По (14.23) найдем
M = qyl2 ⁄ 2 = 407,9æ0,552 ⁄ 2 = 61,7 Нæм. x к
Рассчитаем изгибающие моменты относительно главных осей ξ, η по формулам (14.26):
M |
= M |
cosβ + M sinβ = |
η к |
у к |
х к |
= 42 cos2,3° + 61,7 sin2,3° = 44,4 Hæм;
M |
= M |
sinβ – M cosβ = |
ξ к |
у к |
х к |
= 42 sin2,3° – 61,7 cos2,3° = –60 Hæм.
Определим моменты сопротивления корневого сечения по формулам (14.29), (14.31):
|
|
|
I |
|
10,827æ10 |
–8 |
|
||||
W |
|
= – |
---------мин = |
|
= 4,728æ10–6 м3; |
||||||
мин1 |
|
ξ |
|
|
|
|
–3 |
|
|||
|
|
|
1 |
|
22,9æ10 |
|
|
|
|
||
|
|
|
I |
|
|
æ10 |
–8 |
||||
W |
= – |
-----------макс = |
93,766-------------------------------- |
|
= 1,6368æ10–5 м3; |
||||||
макс1 |
|
|
η |
|
|
|
|
|
|
–3 |
|
|
|
|
|
|
|
æ10 |
|||||
|
|
|
1 |
|
57,283 |
|
|
||||
|
|
|
I |
|
|
æ10 |
–8 |
||||
W |
|
= – |
---------мин = |
10,827-------------------------------- |
|
= 4,646æ10–6 м3; |
|||||
мин2 |
|
|
ξ |
|
|
|
|
|
|
–3 |
|
|
|
|
2 |
|
23,303 |
æ10 |
|
|
|||
|
|
I |
|
93,766æ10 |
–8 |
|
|||||
W |
|
= -----------макс = |
|
|
|
= 1,7764æ10–5 м3; |
|||||
max2 |
η |
|
|
|
|
–3 |
|
||||
|
|
|
2 |
52,780æ10 |
|
|
|
|
|||
|
|
I |
10,827æ10 |
–8 |
|
||||||
W |
|
= --------- |
мин = |
|
|
= 6,767æ10–6 м3; |
|||||
мин3 |
ξ |
|
|
|
–3 |
|
|
||||
|
|
|
|
|
16,0æ10 |
|
|
||||
|
|
|
3 |
|
|
|
|
|
|
||
|
|
|
|
|
|
I |
|
|
|
|
|
|
|
|
W |
|
= – |
-----------макс = × . |
|||||
|
|
|
макс3 |
η |
|
|
|||||
|
|
|
|
|
|
|
|
||||
|
|
|
|
|
|
|
|
|
3 |
|
Найдем изгибные напряжения в «опасных» точках корневого сечения рабочей лопатки по формулам (14.28),
(14.30): |
|
|
|
|
|
|
|
|
|
M |
|
M |
|
44,4 |
|
60,0 |
|
σ = |
---------------η к |
– |
----------------ξ к |
= |
+ |
= |
||
и1 |
W |
|
W |
|
|
–6 |
|
–5 |
|
|
|
|
|
4,728æ10 |
1,6368æ10 |
||
|
мин1 |
|
макс1 |
|
|
|
= 9,39æ106 + 3,67æ106 = 13,06æ106 Па = 13,06 МПа;
|
M |
|
M |
|
44,4 – |
60,0 = |
||||
σ = |
---------------η к |
+ |
----------------ξ к |
= |
||||||
и2 |
W |
|
W |
|
|
|
–6 |
|
|
–5 |
|
|
|
|
|
|
|
|
|||
|
мин2 |
|
макс2 |
|
4,646 |
æ10 |
|
1,7764 |
æ10 |
|
= 9,56æ106 – 3,38æ106 = 6,18æ106 Па = 6,18 МПа;
|
M |
|
M |
|
44,4 – 0 = |
||
σ = – |
---------------η к |
– |
----------------ξ к |
= – |
|||
и3 |
W |
|
W |
|
|
|
–6 |
|
|
|
|
|
|
æ10 |
|
|
мин3 |
|
макс3 |
|
6,767 |
|
= – 6,56æ106 Па = – 6,56 МПа.
Контрольный расчет изгибных напряжений в лопатке показал, что, как и ожидалось, наибольшие напряжения наблюдаются в точке 1 — на входной кромке профиля.
448
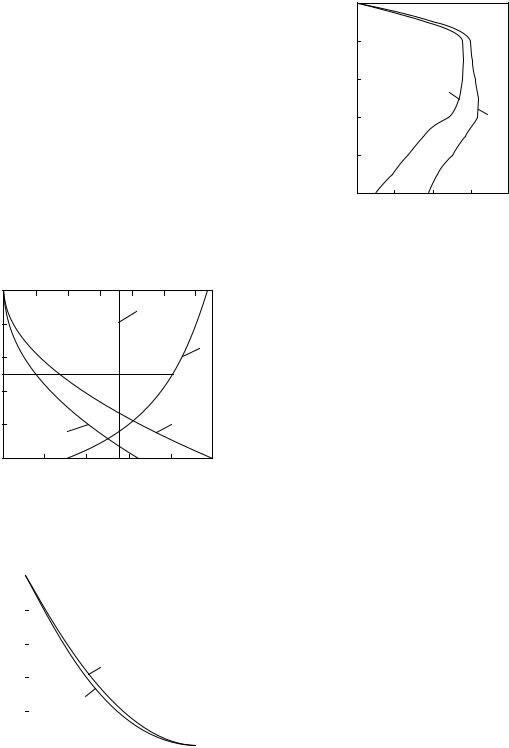
Значение наибольшего изгибного напряжения удов- |
||||||||
летворяет условию (14.32), где для данной рассматривае- |
||||||||
мой ступени σ = 30…35 МПа, так что σ |
|
< σ |
с опре- |
|||||
|
и.д |
|
|
|
|
и1 |
и.д |
|
деленным запасом и по этому показателю лопатка |
||||||||
отвечает условию прочности. |
|
|
|
|
|
|||
Расчет изгибающих моментов в данном примере |
||||||||
выполнен в предположении, что распределение нагрузки |
||||||||
q (z) — равномерное, в то время как более точный расчет |
||||||||
y |
|
|
|
|
|
|
|
|
дает существенно неравномерное распределение осевого |
||||||||
усилия, как показано на рис. 14.7 (кривая 2). Результат |
||||||||
расчета изгибающего момента M (z) по общей зависи- |
||||||||
|
|
|
|
x |
|
|
|
|
мости (14.21) при переменном в соответствии с кривой 2 |
||||||||
усилии q , однако, |
мало |
отличается |
от |
результата при |
||||
|
y |
|
|
|
|
|
|
|
q (z) = const. Поэтому допустимо для лопаток с θ ≈ 3,5 и |
||||||||
y |
|
|
|
|
|
|
|
|
выше рассчитывать изгибные напряжения в корневых |
||||||||
сечениях по значениям момента M |
, определенным по |
|||||||
|
|
|
|
x к |
|
|
|
|
(14.23). На рис. 14.8 представлено сравнение распределе- |
||||||||
z, м |
10 |
20 |
30 |
40 |
50 |
My, Mx, Н·м |
||
0,550 |
|
|
|
|
|
|
|
|
|
|
|
|
1 |
|
|
|
|
|
|
|
|
|
|
|
2 |
|
0,275 |
|
|
|
|
|
|
|
|
|
|
3 |
|
|
|
4 |
|
|
|
|
|
|
|
|
|
|
|
0 |
100 |
200 |
300 |
400 |
qy, qx, Н/м |
Рис. 14.7. Распределения аэродинамических усилий и изги-
бающих моментов по длине лопатки:
1 — q ; 2 — q ; 3 — M ; 4 — M
x |
y |
|
|
y |
|
|
|
x |
|
|
|
|
||
|
My /My к, Mx /Mx к |
|
|
|
|
|
|
|
||||||
|
0,8 |
|
|
|
|
|
|
|
|
|
|
|
|
|
|
|
|
|
|
|
|
|
|
|
|
|
|
|
|
|
0,6 |
|
|
|
|
|
|
|
|
|
|
|
|
|
|
0,4 |
|
|
|
|
|
|
1 |
|
|
|
|
|
|
|
|
|
|
|
|
|
|
|
|
|
|
|
|
|
|
|
|
|
|
2 |
|
|
|
|
|
|
|
|
|
|
0,2 |
|
|
|
|
|
|
|
|
|
|
|
|
|
|
|
|
|
|
|
|
|
|
|
|
|
|
|
|
|
0 |
0,2 |
0,4 |
0,6 |
0,8 |
|
Рис. 14.8. Распределения относительных изгибающих момен-
тов по длине рабочей лопатки:
1 — M / M |
; 2 — M / M |
, а также M / M |
при q (z) = const |
x x к |
y y к |
x x к |
y |
|
|
|
|
0,8 |
|
|
|
0,6 |
|
|
|
|
|
|
2 |
0,4 |
|
|
1 |
0,2 |
|
|
|
0 |
10 |
20 |
30 и, МПа |
Рис. 14.9. Распределения напряжений изгиба по длине
лопатки (l = 960 мм, d = 2,48 м): cр
1 — напряжения в точке 1 (см. рис. 14.4, в); 2 — напря-
жения в точке 2
ний изгибающих моментов, рассчитанных при постоянной и переменной нагрузках q : кривая 1 соответствует
|
y |
значениям M / M |
при переменной нагрузке q (z), кривая |
x x к |
y |
2 получена в предположении, что q (z) = const. y
Из рис. 14.7 (кривая 4) видно, что изгибающий
момент M ≈ 65 Нæм, в то время как по нашему прибли- x к
женному расчету M ≈ 62 Нæм. x к
Погрешность определения момента M составляет xк
около 5 %, а погрешность при расчете напряжений изгиба, например в точке 1, составляет менее 2 %, т.е. несущественна.
Влопатках большой веерности напряжения изгиба достигают максимальных значений обычно не в корневом сечении, а на расстоянии (0,6…0,7)l от него.
Вкачестве примера на рис. 14.9 представлены распределения напряжений в точках 1 и 2 для лопатки большой
веерности (d = 2,48 м, l = 0,96 м — типовая лопатка cр
последних ступеней ЦНД турбин ЛМЗ мощностью 300, 500 и 800 МВт).
Влияние связей на изгибные напряжения в рабочих лопатках. Применение конкретной бандажной связи в относительно коротких лопатках
приводит к некоторому снижению момента My и
к
практически не влияет на значение момента Mx .
к
Снижение My за счет бандажа обычно не превы-
к
шает 20 %, и его во многих случаях вообще не принимают во внимание.
Проволочные демпферные связи мало влияют на изгибающие моменты, и в первом приближении их действие можно не учитывать.
Прочность хвостовых соединений рабочих лопаток. Особенность хвостовых соединений рабочих лопаток с ротором (дисками) состоит в том, что
449
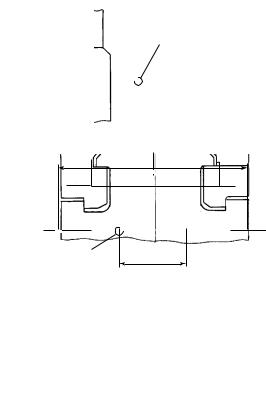
элементы соединения — хвостовики рабочих лопаток и ободья дисков — имеют зоны концентрации напряжений, где местные напряжения существенно выше номинальных напряжений в соответствующих сечениях. Конструкции хвостовиков весьма многообразны, основные типы их представлены на рис. 3.57.
По условиям работы и воздействию лопаток на прочность хвостовиков следует различать три области: 1) высокотемпературную область (более 450 °С), где наблюдается ползучесть; 2) область умеренных температур в отсутствие влияния корро- зионно-активных сред и 3) мигрирующую зону начального влагообразования.
Первая область — лопатки первых ступеней ЦСД, где температура металла лопаток выше 500 °С и наблюдается ползучесть как профильной их части (см. пример 14.2), так и хвостового соединения. При этом прочность хвостовиков оценивается с учетом концентрации напряжений при ползучести.
Условие прочности имеет вид
σ
д.п |
|
n = ------------- ≥ 1,1 , |
(14.33) |
д.п σ
макс
где σ — максимальное эквивалентное напряже-
макс
ние в зоне концентрации; σ — предел длительной
д.п
прочности для материала лопатки при рабочей температуре металла за время ресурса лопаток, обычно
принимаемого равным 105—2 æ105 ч; n — коэф-
д.п
фициент запаса длительной прочности, принимаемый для местных напряжений на уровне около 1,1.
Опасные точки по условию длительной прочности указаны на рис. 14.10, а — для T-образного хвостовика (ЛМЗ), на рис. 14.10, б — для хвостовика типа «наездник» (ХТЗ).
Вторая область — ступени, располагающиеся в температурном диапазоне ниже 500 °С. Для хвостовиков рабочих лопаток этих ступеней прочность оценивается по условию номинальных напряжений и пределу текучести материала. Условие прочности принимается в виде
ns = σs/σ ≥ 1,75…2,0, (14.34)
н
где σs = σ — предел текучести материала лопатки
0,2
при рабочей температуре; σ — суммарное номи-
н
нальное напряжение,
σ = σ + σ ,
н н.р н.и
σ— номинальное напряжение растяжения; σ —
н.р |
н.и |
номинальное напряжение изгиба.
Эти напряжения относятся к опасному сечению, например сечению I—I в хвостовиках (см. рис. 14.10).
Из опыта эксплуатации отечественных турбин следует, что при выполнении условия (14.34) обес-
печивается прочность хвостовых соединений рабочих лопаток.
Третья область — зона начального влагообразования — мигрирует в зависимости от режима работы турбины и обычно занимает несколько последних ступеней ЦСД (турбин без промперегрева) и иногда первые (одну-две) ступени ЦНД. В турбинах АЭС эта область располагается в ступенях ЦНД, где начинает образовываться влажный пар.
В условиях влажной среды при наличии загрязнений в паре при постоянной нагрузке и умеренной температуре (без ползучести) возникает явление — коррозионное растрескивание под напряжением (КРН), представляющее собой процесс зарождения и развития трещины.
Главными определяющими факторами КРН являются: композиционный состав; технология производства детали, термообработка материала; температура эксплуатации; значения (уровень) напряжений и агрессивность окружающей среды. Можно сказать, что возникновение КРН определяется: а) применяемым материалом, б) напряжением и температурой и в) окружающей средой.
A
а)
|
h |
K |
K |
I |
I |
Бh1
б )
Рис. 14.10. Опасные зоны в хвостовиках рабочих лопаток:
а — Т-образный хвостовик; б — хвостовик типа «наездник»;
А, Б — опасные зоны
450