
паровые и газовые турбины для электростанций
.pdfТребуется рассчитать собственные частоты пакета лопа-
ток по формам A , В и A при числе лопаток в пакете j = 6,
0 0 1
проверить вибрационную надежность лопаток.
Решение. Для расчета ν и k предварительно опреде-
бб
Для формы A имеем
0
nz |
50æ32 |
|
1600 |
|
-------н = |
= |
= 1,042 . |
||
fA |
1536 |
|
1536 |
|
0 |
|
|
|
|
ляем:
шаг по бандажу
|
|
π(d |
+ l) |
π(944 + 79) |
|
|
cр |
|
|
t |
б |
= ----------------------- |
= |
----------------------------- = 31,5 мм; |
|
z |
|
102 |
л
момент инерции сечения бандажа (минимальный)
|
|
0,43 |
æ4,4 |
I |
б мин |
= ---------------------- |
= 0,02347 см4. |
|
12 |
Рассчитываем характеристики бандажа:
Отношение n z / fA находится в недопустимом диа-
п
0
пазоне 0,85—1,15 [см. (14.62)], при этом легко увидеть, что в данном случае поправка на влияние вращения на
частоту собственных колебаний пакета по тону A пре-
0
небрежимо мала, в чем рекомендуется убедиться самостоятельно, воспользовавшись зависимостями (14.58), (14.59).
Это означает, что пакет реально находится в резо-
нансе по форме A с кромочным возбуждением.
0
|
|
|
f |
t |
|
0,4æ4,4æ3,15 |
|
|
|
|
|
Для формы В |
|
|
|
|
|
|
|
|
|
|
|
|
||||
|
ν |
|
б б |
|
= 0,148; |
0 |
|
|
|
|
|
|
|
|
|
|
|
|||||||||||
|
= -------- |
|
= ---------------------------------- |
|
|
|
|
|
|
|
|
|
|
|
|
|
|
|
|
|||||||||
|
б |
Fl |
|
4,74æ7,9 |
|
|
|
|
|
|
|
|
|
|
|
|
|
|
|
|
|
|
|
|
||||
|
|
|
|
|
|
|
|
|
|
|
|
|
|
|
|
nz |
|
1600 |
|
|
|
|
|
|
|
|
||
|
|
|
|
j – 1 |
|
I |
l |
|
|
|
|
|
|
-------н = ------------------------------ |
= 0,196…0,195 , |
|
|
|||||||||||
|
|
|
|
|
б мин |
|
|
|
2 |
|
|
fB |
8140…8215 |
|
|
|
|
|
|
|
||||||||
|
k |
= 12 ---------- |
|
H |
б I-------------- |
--- cos |
|
β = |
|
0 |
|
|
|
|
|
|
|
|
|
|
|
|
||||||
|
|
б |
|
|
j |
|
t |
|
|
|
|
|
|
|
|
|
|
|
|
|
|
|
|
|
|
|
||
|
|
|
|
|
|
|
|
η мин |
б |
|
|
|
|
|
|
|
|
|
|
|
|
|
|
|
|
|
|
|
|
|
|
|
|
|
|
|
|
|
|
|
|
|
|
откуда следует, что пакет отстроен от кромочного возбуж- |
|||||||||||||
|
5 |
|
|
0,02347æ7,9 |
|
2 |
|
|
|
|
дения по форме В |
с большим запасом. |
|
|
|
|||||||||||||
--= 12æ6æ0,3 |
-------------------------------1,341æ3, 15 æcos |
|
10 |
|
= 0,1277. |
|
|
0 |
|
|
|
|
|
|
|
|
|
|
|
|||||||||
|
|
|
|
|
|
|
|
|
|
|
|
|
|
|
Аналогично |
убедимся |
в достаточной |
отстройке по |
||||||||||
С учетом ν |
и k |
по графикам, данным на рис. 14.27, |
форме A : |
|
|
|
|
|
|
|
|
|
|
|
|
|
||||||||||||
|
|
б |
|
б |
|
|
|
|
|
|
|
|
|
|
|
|
|
|
|
|
|
|
|
|
|
|
|
|
|
|
|
|
|
|
|
|
|
|
|
|
|
|
|
1 |
|
|
|
|
|
|
|
|
|
|
|
|
|
находим значения ϕ для трех форм колебаний: |
|
|
|
|
|
|
|
|
|
|
|
|
|
|
||||||||||||||
|
|
|
|
|
|
|
|
|
|
|
|
|
|
|
|
|
|
nz |
|
1600 |
|
|
|
|
|
|
|
|
|
|
|
|
|
ϕ(A ) = 0,83; |
|
|
|
|
|
|
|
|
|
н |
|
|
|
|
|
|
|
|
|||||
|
|
|
|
|
|
|
|
|
|
|
|
|
|
|
= 9898 = 0,162 |
|
|
|
|
|
||||||||
|
|
|
|
|
|
|
0 |
|
|
|
|
|
|
|
|
|
|
-------fA |
|
|
|
|
|
|||||
|
|
|
|
ϕ(В ) = 4,4…4,44; |
|
|
|
|
|
|
|
1 |
|
|
|
|
|
|
|
|
|
|
||||||
|
|
|
|
|
|
0 |
|
|
|
|
|
|
|
|
|
|
|
|
|
|
|
|
|
|
|
|
|
|
|
|
|
|
|
|
ϕ(A ) = 5,35. |
|
|
|
|
|
|
— отстройка от резонанса с большим запасом. |
|
|
|||||||||||||
|
|
|
|
|
|
|
1 |
|
|
|
|
|
|
|
|
|
|
|
|
|
|
|
|
|
|
|
|
|
Для определения ψ рассчитываем: |
|
|
|
Проверим отстройку от резонанса при кромочной час- |
||||||||||||||||||||||||
радиус инерции сечения |
|
|
|
|
|
|
тоте 2 n z |
: |
|
|
|
|
|
|
|
|
|
|
|
|
||||||||
|
|
|
|
|
|
н |
|
|
|
|
|
|
|
|
|
|
|
|
|
|||||||||
|
|
|
|
|
|
1 ⁄ 2 |
= 1,341 |
|
|
|
|
|
|
2nz |
|
3200 |
|
|
|
|
|
|
|
|
|
|||
i |
= i |
= |
--------------η мин |
|
|
|
= 0,5319 см; |
|
-----------н = |
= 2,08 — отстроен; |
|
|
||||||||||||||||
|
|
|
I |
|
|
|
|
|
1 ⁄ |
2 |
|
|
|
|
|
|
|
|
|
|
|
|
|
|
|
|
||
η |
мин |
|
|
F |
|
|
|
4,74 |
|
|
|
|
|
|
|
|
|
|
|
|
|
|
|
|
|
|
|
|
|
|
|
|
|
|
|
|
|
|
|
|
|
|
|
|
fA |
|
1536 |
|
|
|
|
|
|
|
|
|
|
|
|
|
|
|
|
|
|
|
|
|
|
|
|
|
|
0 |
|
|
|
|
|
|
|
|
|
|
|
|
гибкость лопатки |
|
|
|
|
|
|
|
|
|
|
|
|
|
|
|
|
|
|
|
|
|
|
||||||
|
|
|
|
|
|
|
|
|
|
|
|
|
|
|
2nz |
3200 |
|
|
|
|
|
|
|
|
|
|
||
|
|
|
|
|
l |
|
|
7,9 |
|
|
|
|
|
|
н |
|
|
|
|
|
|
|
|
|
|
|||
|
|
|
|
|
|
|
|
|
|
|
|
|
|
= 8140…8215 = 0,393…0,389 |
— отстроен; |
|||||||||||||
|
|
|
λ = i--------- |
|
= 0,5319---------------- = 14,85. |
|
-----------fB |
|||||||||||||||||||||
|
|
|
|
мин |
|
|
|
|
|
|
|
|
0 |
|
|
|
|
|
|
|
|
|
|
|
|
|
||
По графику (см. рис. 14.22) с учетом λ = 14,85 опре- |
|
2nz |
|
|
|
|
|
|
|
|
|
|
|
|
||||||||||||||
|
|
|
|
|
|
|
|
|
|
|
|
|
|
|
|
|
3200 |
|
|
|
|
|
|
|
|
|
||
|
|
|
|
|
|
|
|
|
|
|
|
|
|
|
|
н |
|
|
|
|
|
|
|
|
|
|
||
деляем |
|
|
|
|
|
|
|
|
|
|
|
|
|
|
|
fA |
= 9898 = 0,323 — отстроен. |
|
|
|||||||||
|
|
|
|
|
|
ψ = 0,785. |
|
|
|
|
|
|
|
|
|
|||||||||||||
|
|
|
|
|
|
|
|
|
|
|
|
|
1 |
|
|
|
|
|
|
|
|
|
|
|
|
|||
В соответствии с (14.54) имеем |
|
|
|
|
|
|
Для обеспечения вибрационной надежности венец |
|||||||||||||||||||||
|
|
|
|
|
|
|
|
|
|
|
|
|
|
|
||||||||||||||
|
|
|
|
|
|
0,56 EIмин |
1 ⁄ 2 |
|
|
должен быть отстроен |
|
от |
резонанса |
|
по форме |
A0, что |
||||||||||||
|
|
|
f = ψϕ---------- |
|
------------- |
|
|
= |
|
|
|
|
|
|
|
|
|
|
|
|
|
|
|
|
||||
|
|
|
|
|
|
l |
2 |
ρF |
|
|
|
|
|
вполне возможно за счет изменения f |
A |
либо z |
н |
в ту или |
||||||||||
|
|
|
|
|
|
|
|
|
|
|
|
|
|
|
|
|
|
|
|
|
|
|
0 |
|
|
|||
|
|
|
|
|
|
11 |
|
|
–8 |
|
1 ⁄ 2 |
|
иную сторону на 15—20 %. При этом за счет больших |
|||||||||||||||
|
0,56 1,89æ10 |
æ1,341æ10 |
|
|
|
|
|
|
|
|
|
|
|
|
|
|
|
|
|
|
|
|||||||
= ψϕ |
|
|
|
|
|
|
|
|
|
|
|
|
= ψϕæ2356,9 . |
запасов отстройки по формам В , A |
(при частоте как nz , |
|||||||||||||
------------------------------------------------------------ |
|
|
|
|
|
|
|
|
|
|
|
|
|
|
|
0 |
|
1 |
|
|
|
|
н |
|||||
0,0792 |
|
7750æ4,74æ10–4 |
|
|
|
|
|
так и 2nz ) не будут нарушены. |
|
|
|
|
|
|
|
|||||||||||||
|
|
|
|
|
|
|
|
|
|
|
|
|
|
|
н |
|
|
|
|
|
|
|
|
|
|
|
|
|
Подставляя значения ϕ и ψ (при этом принимаем, что |
Определим динамические напряжения в корневых |
|||||||||||||||||||||||||||
ψ одинаково для всех трех форм), получаем: |
сечениях рабочих лопаток рассматриваемого венца в |
|||||||||||||||||||||||||||
|
fA |
= 0,785æ0,83æ2356,9 = 1536 Гц; |
условиях резонанса по форме A . Для расчета по формуле |
|||||||||||||||||||||||||
|
|
|
|
|
|
|
0 |
|
|
|
|
= C = 0,415 |
||||||||||||||||
|
0 |
|
|
|
|
|
|
|
|
|
|
|
|
|
(14.64) найдем входящие в нее величины: C |
|||||||||||||
|
|
|
|
|
|
|
|
|
|
|
|
|
|
|
|
|
|
|
|
|
|
|
|
|
|
m |
|
1 |
fB |
= 0,785(4,4…4,44)æ2356,9 = 8140…8215 Гц; |
(см. рис. 14.33); |
η = 0,08 (см. рис. 14.34); |
кр |
= 0,1 (по |
|||||||||||||||||||||||
0 |
|
|
|
|
|
|
|
|
|
|
|
|
|
|
k |
|||||||||||||
|
fA |
= 0,785æ5,35æ2356,9 = 9898 Гц. |
оценке). С учетом (14.70) имеем |
|
|
|
|
|
|
|
||||||||||||||||||
|
1 |
|
|
|
|
|
|
|
|
|
|
|
|
|
|
|
|
|
|
|
|
|
|
|
|
|
|
|
Проверим отстройку пакета от резонансов при колеба- |
|
|
|
|
|
0,1 |
|
|
|
|
|
|
|
|||||||||||||||
σ = 2πæ0,415 |
|
χσ |
|
= 3,26χσ |
|
|
||||||||||||||||||||||
ниях по формам A , В |
|
и A |
|
с кромочными частотами nz . |
----------- |
|
. |
(14.72) |
||||||||||||||||||||
|
|
|
д |
|
|
|
0, 08 |
ст |
|
|
ст |
|
|
|||||||||||||||
|
|
|
0 |
|
0 |
1 |
|
|
|
|
|
|
н |
|
|
|
|
|
|
|
|
|
|
|
|
|
|
471
Для оценки σ примем значение мощности ступени
ст
N = 7 МВт. Тогда рабочее усилие на одну лопатку опре-
0i |
|
|
|
|
|
делим из условия Рu = N |
/ z |
, где u — окружная ско- |
|||
|
0 i |
л |
|
|
|
рость лопаток на среднем радиусе d |
/ 2. Учитывая, что |
||||
|
|
|
ср |
|
|
изгибающий момент в корневом сечении лопаток M = |
|||||
|
|
|
|
|
изг |
= Pl / 2 = N l / ( 2 z |
u), имеем номинальное напряжение |
||||
0 i |
л |
|
|
|
|
изгиба в корневом сечении |
|
|
|
|
|
|
Mизг |
|
N0il |
|
|
σ |
= ---------------- |
= ---------------------------- , |
(14.73) |
||
ст |
W |
2W |
z u |
|
|
|
мин н |
|
мин н |
л |
|
где W — минимальный момент сопротивления про-
мин н
филя натурной лопатки. По табл. 3.1 для нашего профиля Р-30-21А при ширине В = 25 мм (b = 25,6 мм) имеем
м1
W= 0,234 см3.
мин м
Пересчет |
на |
натурное |
значение |
В = 40 мм |
||||
|
|
|
|
|
|
|
|
н |
(см. рис. 14.36) дает |
|
|
|
|
|
|||
|
|
|
3 |
|
|
|
|
|
|
Bн |
|
|
= |
40 |
3 |
= 0,9585 см4. |
|
W |
= |
------ |
W |
|
----- |
æ0,234 |
||
|
Bм |
|
мин м |
|
25 |
|
|
|
|
мин н |
|
|
|
|
|
|
Окружная скорость на среднем радиусе
u = d ω/2 = 0,944æ314,16/2 = 148,28 м/с. cр
Подставляя найденные величины (в системе СИ) в (14.73), получаем
7æ106 |
æ0,079 |
σ = --------------------------------------------------------------------------- |
= |
ст 2æ0,9585æ10–6æ102æ148,28 = 1,907æ107 Па = 19,07 МПа.
Расчет пакетного множителя по (14.68) проводим для условия резонанса k = z :
|
|
|
н |
sin(πjz |
⁄ z |
) |
sin(πæ6æ32 ⁄ 102) |
н |
л |
|
|
χ = j--------------------------------sin(πz |
⁄ z |
) = -----------------------------------------------6sin(πæ32 ⁄ 102) = –0,061. |
нл
Сиспользованием (14.72) получаем амплитуду динамических напряжений в лопатках резонирующего пакета:
σ = 3,26æ0,061æ19,07 = 3,8 МПа.
д
Найденное значение динамических напряжений весьма низкое, оно существенно меньше предела усталости материала лопаток: при рабочей температуре (около
400 °С) для стали марки 20Х13 имеем σ ≈ 300 МПа.
–1
Малые динамические напряжения получены за счет эффекта пакетирования (малого значения пакетного множителя χ, что достигнуто выбором числа лопаток в пакете j = 6). Число лопаток равно оптимальному, рассчитываемому по формуле (14.71):
j = iæ102/32 = 3,1875 i ≈ 3 i, при i = 2 j |
= 6. |
опт |
опт |
Выполненный анализ показал, что лопаточный венец десятой ступени соответствует условиям вибрационной
надежности по формам тангенциальных колебаний A , В
0 0
и A от кромочного возбуждения с частотами nz и 2nz .
1 |
н |
н |
При этом по формам В , A он отстроен от резонансов. По
01
форме A венец отстроен от резонанса при частоте 2nz , но
0 |
н |
находится в резонансе с кромочной частотой nz . Однако и
н
для формы A надежность обеспечена за счет оптималь-
0
ного пакетирования, позволившего снизить динамические напряжения до допустимого (с большим запасом) уровня.
Для полной вибрационной надежности следует выполнить анализ колебаний пакетов венца по изгибно-
крутильным формам A , A , A . Читателю рекоменду-
00 01 02
ется выполнить этот анализ самостоятельно, использовав в качестве подсказки пример 14.6.
Пример 14.9. Требуется оценить динамические номинальные (без учета концентрации) напряжения в корневом сечении рабочих лопаток регулирующей ступени при полностью открытом одном клапане и дать ориентировочную оценку вибрационной надежности лопаток.
Известны следующие данные:
собственная частота колебаний пакета (средняя) по
форме A fA = 4400 Гц;
0
0
разброс частот пакетов на колесе составляет ±15 %;
число лопаток на колеса z = 66;
л
число лопаток в пакете j = 3;
бандажи — цельнофрезерованные; лопатки сварены по бандажам и хвостовикам электронным лучом.
Коэффициент демпфирования принимаем η = 0,005 по оценке для 12 %-ной хромистой стали.
Параметры бандажа следующие: k = 0,05; ν = 0,3
б б
(определены при предварительном расчете, как в примере 14.8).
Изгибающие напряжения σ = 15 МПа (приняты в
ст
соответствии с нормами).
Решение. Напряжения при резонансе определяем по
(14.64), для чего находим С (см. рис. 14.33) по заданным m
k= 0,05 и ν = 0,3:
бб
C = 0,4; m
резонансную гармонику для среднего пакета
k = fA ⁄ n = 4400 ⁄ 50 = 88 ;
0
пакетный множитель для среднего пакета [см. (14.68)]
sin(πæ3æ88 ⁄ 66) |
sin(πæ4) |
|
χ = --------------------------------------------3sin(πæ88 ⁄ 66) |
= 3---------------------------------------sin(πæ88 ⁄ 66) |
= 0. |
Для пакета со средней частотой fA |
пакетный множи- |
|
|
0 |
|
тель равен нулю, этот пакет не колеблется, несмотря на наличие резонанса.
Однако вследствие разброса частот ±15 % необходимо рассчитать резонансные напряжения для пакетов, частота
которых располагается внутри интервала f = (1 ± 0,15) fA .
д
|
|
|
0 |
Для наименее жесткого пакета на колесе частота |
|||
составит f мин = (1 – 0,15) f |
A |
= 0,85æ4400 = 3740 Гц и |
|
д |
|
|
|
|
|
|
0 |
соответствующая гармоника будет иметь номер |
|||
k |
= f мин ⁄ n = 3740 ⁄ 50 ≈ 75 . |
||
мин |
д |
|
|
472
Для наиболее жесткого пакета |
на колесе f макс = |
|
д |
= (1 + 0,15) fA = 1,15æ4400 = 5060 |
Гц и номер соответ- |
0 |
|
ствующей гармоники |
|
k= f макс ⁄ n = 5060 ⁄ 50 ≈ 101 .
Таким образом, на рассматриваемом колесе расположены пакеты, резонирующие с возбуждающими гармони-
ческими силами кратностью от k |
до k |
, т.е. воз- |
мин |
макс |
|
можны резонансы с k = 75, 76, …, 100, 101. |
|
Для определения амплитуды резонансных напряжений следует произвести расчет по зависимости (14.64), в
|
|
п |
парц |
|
которой интенсивности гармоник |
k |
= χ k |
[см. |
|
(14.70)], а интенсивности kпарц |
2 |
|
|
|
= ----- |
[см. (14.66)]. Нужно |
|||
|
πk |
|
|
|
выполнить расчет для k = 75…101 и установить максимальное значение динамического напряжения. Оно будет относиться к наиболее «неблагополучному» пакету на данном колесе и будет определять его вибрационную надежность. Неблагополучным будет тот пакет, для кото-
|
парц |
|
рого произведение |
χ k |
имеет максимальное абсолют- |
ное значение. |
|
|
Из (14.70) с учетом (14.66), (14.68) для данного при-
мера имеем |
|
|
|
sin(πkæ3 ⁄ 66) |
2 |
|
|
kп = ------------------------------------ |
----- . |
|
|
3 sin(πk ⁄ 66) |
πk |
|
|
Для наименее жесткого пакета |
|
|
|
sin(πæ75æ3 ⁄ 66) |
2 |
|
|
kп = -------------------------------------------- |
------------- |
= |
|
3sin(πæ75 ⁄ 66) |
πæ75 |
|
|
= 0,7699æ8,488æ10–3 = 6,54æ10–3. |
|||
Для наиболее жесткого пакета |
|
|
|
sin(πæ101æ3 ⁄ 66) |
2 |
|
|
kп = ----------------------------------------------- |
---------------- |
= |
|
3 sin(πæ101 ⁄ 66) |
πæ101 |
|
= (–0,3213)æ6,303æ10–3 = –2,03æ10–3.
Можно убедиться, что все промежуточные значения
пk в диапазоне k от 75 до 101 находятся в интервале
полученных значений |
kп(kмин) и kп(kмакс) . |
Поэтому |
|
самым |
неблагополучным является наименее |
жесткий |
|
пакет, для которого kп |
достигает максимального значе- |
||
ния п |
= 6,54æ10–3. |
|
|
k |
макс |
|
|
Для него и рассчитаем значение динамического напряжения по (14.64):
|
6,54æ10–3 |
|
σ = 2πæ0,4æ15æ-------------------------- |
= 49,3 МПа. |
|
д |
0, 005 |
|
У лопаток в месте примыкания профиля к хвостовику всегда имеется концентрация напряжений. Коэффициент
концентрации k в случае отсутствия свисающих кромок
σ
может быть выдержан не выше k = 3. Оценивая эффек-
σ
тивное напряжение σ = k σ ≈ 150 МПа и принимая пре-
aσ д
дел усталости σ = 300 МПа (для стали марки
–1
15Х12ВМФ (ЭИ802) при температуре 500 °С), ориентировочно получаем коэффициент запаса усталостной прочности
|
σ |
300 |
|
|
–1 |
|
|
na |
= -------- |
= -------- |
= 2, |
|
σa |
150 |
|
что для стационарных турбин следует считать допусти-
мым (хотя n и не регламентировано в ПТЭ). Отметим, a
что для судовых и авиационных турбин обычно прини-
мают nсудa = 3 и nавиацa ≥ 4 соответственно. В случае
судовых и авиационных турбин значения σ принято a
определять не расчетом, а экспериментально на моделях или натурных объектах, так как расчет из-за его приближенности может дать погрешность, неприемлемую для ответственных двигателей.
Для повышения вибрационной надежности лопаток парциальной ступени имеются следующие меры — увеличение хорды профиля; уменьшение значения разброса собственных частот; соединение между собой пакетов демпферными вставками. Вторая мера сопряжена с повышением точности изготовления пакетов и тщательности сборки их на колесе.
Читателю предлагается самостоятельно установить коэффициент запаса усталостной прочности лопаток регулирующей ступени, если благодаря усовершенствованию технологии изготовления и сборки удалось снизить разброс частот пакетов до нормы ±4 % при прочих тех же условиях.
14.4. ПРОЧНОСТЬ РОТОРОВ
Рассмотрим основы прочности роторов турбомашин (турбин, компрессоров) под воздействием: статического кручения; изгиба от собственного веса; центробежных сил инерции при умеренных и повышенных температурах и в условиях коррозионноактивной среды; температурных полей при переходных режимах работы.
Сопоставление напряженно-деформированного состояния при названных воздействиях с характеристиками прочности материала дает представление о надежности роторов и факторах, определяющих ресурс.
Кручение роторов. Крутящий момент создается на колесе каждой ступени турбомашины, суммируется и в конечном сечении передается приводимой машине.
На рис. 14.37 представлено распределение кру-
тящего момента M по длине валопровода турбоаг-
кр
регата. Максимальное значение крутящего момента достигается на участке вала между роторами низкого давления (РНД) и генератора (РГ) и составляет
M = Nе / ω, (14.74)
кр 0
473
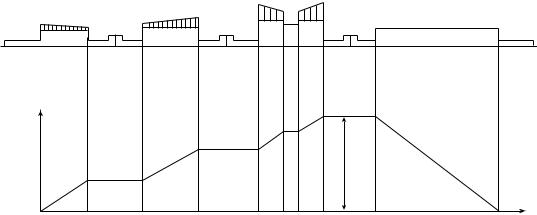
|
РНД |
|
РВД |
РСД |
|
РГ |
||
|
||
Mкр |
|
|
|
кр0 |
|
|
M |
|
|
z |
|
Рис. 14.37. Распределение крутящего момента по длине валопровода турбоагрегата |
где Nе — эффективная мощность на валу турбины,
передаваемая электрическому генератору; ω — угловая скорость ротора.
Крутящий момент вызывает напряжения в элементах ротора, значимыми являются напряжения кручения в шейках роторов, и, как правило, максимальными — напряжения в шейках РНД и РГ, где крутящий момент имеет максимальное значение [см. (14.74)].
Номинальное касательное напряжение в шейке ротора турбины определяется по формуле сопротивления материалов
M
|
|
кр0 |
|
|
τ |
= |
------------ |
, |
(14.75) |
|
0 |
W |
|
|
кр
где W — момент сопротивления кручению шейки,
кр
|
|
|
3 |
|
|
|
4 |
|
|
|
|
πdш |
d0 |
|
|
||
|
|
|
|
|
|
|||
W |
|
= |
---------- |
1 |
------ |
; |
(14.76) |
|
кр |
16 |
– |
|
|||||
|
|
|
dш |
|
|
здесь d — диаметр шейки РНД; d — диаметр
ш |
0 |
центрального канала.
На прочих участках валопровода, кроме участка РНД—РГ, напряжения кручения, как правило, малы.
Ответственными элементами валопровода являются муфты (см. п. 11.1.1). Напряженно-деформи- рованное состояние полумуфт и стяжных болтов определяется специальным расчетом для каждого типа турбин. Оно, как и напряжения в шейках валов, должно отвечать условиям прочности как при номинальных, так и при чрезвычайных режимах турбоагрегата, например при режимах короткого замыкания, повторного автоматического включения (см. § 14.5).
Для оценки напряжений в шейке вала рассмотрим пример.
Пример 14.10. Рассчитать номинальные касательные напряжения в шейке РНД турбины Т-250/300-23,5 ТМЗ на участке между РНД и РГ (см. рис. 11.1) и оценить запас статической прочности при кручении в условиях конденсационного режима турбины.
Материал вала — сталь 34ХНЗМА, имеющая характе-
ристики при температуре 20 °С : σ |
≥ 700 МПа; σ ≥ |
0,2 |
в |
≥ 820 МПа; поперечное сужение при разрыве ψ ≥ 0,4
(≥ 40 %). Диаметр шейки d = 436 мм, диаметр централь-
ш
ного отверстия вала d = 130 мм.
0
Решение. Найдем номинальный крутящий момент в шейке по (14.74):
M= N /ω = 300æ106/314,16 = 0,9549æ106 Нæм.
кр 0 |
e |
|
|
|
|
|
|
|
|
Определим момент сопротивления кручению по |
|||||||||
(14.76): |
|
|
|
|
|
|
|
|
|
|
|
|
πæ0,4363 |
|
|
|
130 |
4 |
|
|
W |
|
= ----------------------- |
1 – |
|
|
= |
||
|
|
|
|
-------- |
|
||||
|
|
кр |
16 |
|
436 |
|
|||
= 0,016274æ(1 – 0,087904) = 0,016145 м3. |
|||||||||
Рассчитаем |
касательные |
|
напряжения (напряжения |
||||||
кручения) на периферии шейки по (14.75): |
τ = 0,9549æ106/0,016145 = 59,1452æ106 Па ≈ 59 МПа.
0
По третьей теории прочности пересчитаем предел
текучести при сдвиге |
|
|
|
1 |
|
τ |
= -- |
σ = 350 МПа. |
0,2 |
2 |
0,2 |
Определим запас прочности по статическим напряже- |
||
ниям кручения: |
|
|
n = τ |
/τ = 350/59 = 5,93, |
|
s |
0,2 |
0 |
т.е. действующие при конденсационном режиме турбины номинальные напряжения кручения примерно в 6 раз меньше предела текучести материала при кручении, т.е. запас прочности при номинальном режиме турбины
474
вполне достаточный. Действительные напряжения кручения будут больше номинальных вследствие концентрации напряжений в галтели перехода от шейки к валу.
При радиусе скругления в галтели ρ = 10 мм (типичное значение) для нашего случая оказывается, что коэф-
фициент концентрации α ≈ 2,2, так что местное напря-
σ
жение достигает значения
τ= α τ = 2,2æ59 ≈ 130 МПа,
макс |
σ 0 |
а коэффициент запаса по отношению к местному максимальному напряжению кручения составит
n′ = 350/130 ≈ 2,7.
σ
Для номинального режима это вполне достаточный запас, но в чрезвычайном случае (короткое замыкание и пр.) максимальный крутящий момент в хорошо отстроенном валопроводе может в 4—6 раз превышать его номинальное значение. При этих условиях в шейке вала в галтели могут появиться местные пластические деформации. Запасы прочности и надежность ротора в этом случае требуют более строгого расчета и оценки.
Изгиб ротора под действием собственного веса. В процессе монтажа роторы устанавливаются так, чтобы полумуфты перед их соединением были соосны, а торцевые поверхности полумуфт были параллельны. Тогда после соединения полумуфт изгибающие моменты в торцевом сечении при равномерной затяжке болтов будут равными нулю. В условиях вращения валопровода равенство нулю изгибающих моментов в торцевых сечениях муфт сохранится, если не изменится центровка валопровода. Из-за ряда условий эксплуатации — тепловых и силовых деформаций фундамента и опор турбоагрегата — упругая линия валопровода при стационарном режиме работы турбоагрегата отличается от линии при монтаже. В тех случаях, когда эксплуатационные расцентровки существенны, при монтаже валопровода учитывают их влияние. Для этого при монтаже перед сборкой полумуфты устанавливают с монтажным раскрытием так, чтобы в установившемся режиме турбоагрегата торцевые поверхности полумуфт стали параллельны и, следовательно, изгибающие моменты в сечениях стыковки были равны или близки к нулевым значениям.
Наибольшие изгибающие моменты от собственного веса возникают в роторах примерно посередине пролета, где диаметр вала обычно более 0,5 м. При этом амплитуда переменных напряжений изгиба в условиях вращения вала составляет для середины пролета малое значение, не превышающее обычно 10 МПа. Поскольку предел усталости мате-
риала (такого, например, как Р2МА) σ > 200 МПа,
–1
то коэффициент запаса по пределу усталости nf > 20,
т.е. перемeнные изгибные напряжения от собственного веса не могут вызвать разрушения вала вследствие усталости при нормальных условиях эксплуатации турбины.
Однако в практике эксплуатации наблюдались случаи разрушения вала от переменных изгибных напряжений, но эти случаи относятся к разрушению валов вблизи соединительных муфт, а также в сложных условиях, когда большие переменные напряжения изгиба возникают вследствие значительных расцентровок и переменных напряжений, обусловленных вибрацией.
Трещинообразование вследствие изгиба от собственного веса при сопутствующих осложняющих условиях наблюдалось в роторах НД ряда теплофикационных турбин в зоне фазового перехода.
Прочность вращающихся дисков. Диски являются элементами роторов различной конструкции: сборных, сварных, цельнокованых (см. п. 11.1.1). Основной нагрузкой дисков являются центробежные силы инерции при вращении как самих дисков, так и рабочих лопаток.
Диски сборного ротора ЦНД (см. рис. 11.1) имеют горячую посадку с натягом. Напряжения в таких дисках определяются вращением собственно диска, лопаточной нагрузкой от ЦБС лопаток, передаваемых диску через хвостовые соединения лопаток с диском, контактного давления от посадки диска на вал. Особенно нагруженными являются диски последних ступеней конденсационных паровых турбин, у которых велика лопаточная нагрузка вследствие больших длины и массы рабочих лопаток. Наиболее напряженной в насадных дисках является область на посадочной поверхности ступицы диска. Для снижения напряжений диски выполняют с широкой ступицей.
На рис. 14.38 изображены распределения при рабочей частоте вращения радиального σr и окруж-
ного σ напряжений по радиусу диска одной из ступе-
θ
ней ЦНД конденсационной турбины. Диск посажен на вал с натягом, вследствие чего на поверхности
его расточки при радиусе r = 0,25 м действует кон-
0
тактное напряжение σr0 = –q0. |
|
На периферии диска при радиусе r |
= 0,6 м дей- |
1 |
|
ствуют напряжения σr1, вызываемые |
центробеж- |
ными силами лопаток и частей обода диска, распо-
ложенных вне поверхности радиусом r .
1
Распределение напряжений по радиусу — весьма неравномерное, особенно велики окружные
напряжения на поверхности расточки диска при r = r .
0
Напряжения, данные на рис. 14.38, рассчитаны в предположении равномерного распределения напряжений по толщине.
Существующие и используемые при расчете дисков методики позволяют учитывать неравномерность распределения напряжений по толщине и осевые нормальные и касательные напряжения,
475
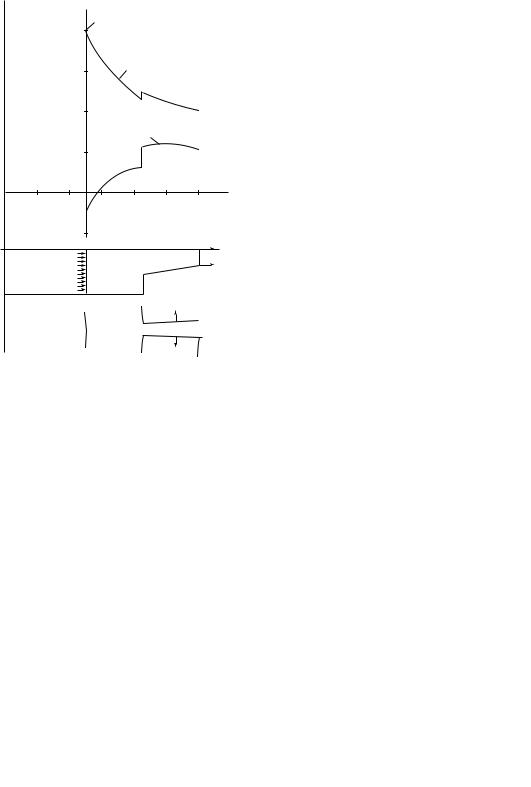
r, , МПа
0
400
300
200
r
100
0,3 |
0,4 |
0,5 |
0,6 r, м |
r0
–100
r1
r0 = –q0
r
r
Рис. 14.38. Распределения напряжений по радиусу насадного
диска РНД
а также напряжения в зонах концентрации — в местах перехода от полотна диска к ступице.
После горячей посадки диска на вал и выравнивания температур диска и вала должно выполняться условие совместности деформаций диска и вала в виде
u – u = u , |
(14.77) |
дв 0
где u — радиальное смещение поверхности рас-
д
точки диска; u (< 0) — радиальное смещение
в
поверхности вала; u = r – r — разница радиусов
0 в д
вала и диска до посадки, называемая натягом (рис. 14.39).
Из условия совместности (14.77), выразив радиальные смещения через напряжения по закону Гука, можно получить основное соотношение посадки в виде:
Eu
|
0 |
|
2 |
|
2 |
|
|
σθ0 – σr0 |
|
|
|
|
|
||
= --------- |
+ 0,25 |
(1 – μ)ρω |
r |
0 |
, |
(14.78) |
|
|
r |
|
|
|
|
|
|
|
0 |
|
|
|
|
|
|
где σ , σr — окружное и радиальное напряжения
θ0 0
на поверхности росточки диска, указанные на рис. 14.38; ρ — плотность материала вала; ω — угловая скорость вала.
Соотношение (14.78) справедливо при любой
частоте вращения в диапазоне 0 ≤ n ≤ n , где n —
ос ос
освобождающая частота вращения. Левая часть
(14.78) σ – σr = 2τ , т.е. представляет собой
θ0 0 макс
удвоенное максимальное касательное напряжение на поверхности расточки диска. Согласно одной из теорий прочности максимальное касательное напряжение является критерием появления пластических деформаций. По этому критерию имеем
коэффициент запаса прочности n в виде
τ
|
τs |
|
σs |
|
n = |
------------ = |
2--------------- |
, |
(14.79) |
τ |
τ |
τ |
|
|
|
макс |
|
макс |
|
где τs — предел текучести при сдвиге; σs — предел текучести при растяжении.
Оценим второй член в правой части (14.78), при-
няв μ = 0,3, ρ = 7800 кг/м3, ω = 314 рад/с, r =
0
= 0,25 м (типичные значения):
0,25(1– μ)ρω2r2 = 0,25 æ0,7æ7800æ(314 æ0,25)2 =
0
= 8,41æ106 Па = 8,41 МПа.
Полученное значение в десятки раз меньше раз-
ницы σ – σr . Например, по рис. 14.38 σ – σr =
θ0 0 θ0 0
= 401 + 46 = 447 МПа, т.е. при изменении частоты вращения поправка меняется от 0 (при ω = 0) до 2 % (при ω = ω ). Это означает, что левая часть
ном |
|
(14.78), т.е. величина τ |
, практически постоянна |
|
макс |
при любой частоте вращения (0 ≤ n ≤ n ). Следова- |
|
|
ос |
тельно, диск с посадкой на валу имеет практически постоянный коэффициент запаса прочности [см. (14.79)]
σsr0 |
|
n ≈ ---------- |
(14.80) |
τ |
Eu |
|
|
|
0 |
|
r0 |
|
rд |
–uв uд
u0
rв
Рис. 14.39. Втулка диска перед посадкой его на вал
476
в диапазоне от нулевой до освобождающей частоты вращения. Это означает, что при работе турбины повышение частоты вращения сверх номинального
значения вплоть до n = n не влияет на прочность
ос
насадных дисков. Кратковременное повышение частоты вращения в эксплуатации неизбежно, например, при опробовании предельных выключателей, сбросах нагрузки и других переходных режимах.
Однако даже непродолжительное вращение ротора с частотой, близкой к освобождающей частоте, может привести к последующей увеличенной его вибрации вследствие механической нестабильности, возникающей после ослабления посадки дисков и неравномерного «схватывания» вала дисками при снижении частоты вращения до номинальной.
Механическая нестабильность характерна для роторов с дисками, имеющими широкую ступицу.
Пример 14.11. Диск посажен на вал с натягом u =
0
= 0,5 мм. Требуется определить коэффициент запаса
прочности диска, если r = 0,25 м; E = 2,16æ105 МПа; σ =
0 |
s |
= 680 МПа (сталь 34ХН1М при 20 °С).
Решение. По (14.80) получаем
|
680æ0,25 |
n = |
---------------------------------------------- = 1,574. |
τ |
2,16æ105æ0, 0005 |
|
|
Найденное n |
находится на нижней границе допусти- |
τ |
|
мых значений.
Для каждого диска имеется следующая связь между
натягом u и освобождающей частотой вращения:
0
u |
= r s′ (n |
/n )2/E, |
(14.81) |
0 |
0 θ0 |
ос 0 |
|
где s′ = s – 0,25(1 – μ)ρω2r2 ; s — окружное напря-
θ0 |
θ0 |
0 0 θ0 |
жение на поверхности расточки диска при отсутствии контактного давления при рабочей частоте вращения.
Поскольку s′ для каждого диска есть величина посто-
θ0
янная (определяемая расчетом), то по формуле (14.81) можно определить значение натяга при любой освобождающей частоте, и наоборот.
Формула (14.81) непосредственно следует из (14.78), если последнюю применить к состоянию диска при осво-
бождающей частоте вращения. Полагая в (14.78) ω = ω ,
ос
имеем (по смыслу) контактное напряжение σr = 0,
0
окружное напряжение σ , равное напряжению на поверх-
|
|
θ0 |
|
|
ности |
расточки |
свободно |
вращающегося диска при |
|
ω = ω |
: |
|
|
|
ос |
|
|
|
|
σ (ω ) = σ (ω )(ω /ω )2 = s (ω /ω )2, |
||||
|
θ0 ос |
θ0 0 |
ос 0 |
θ0 ос 0 |
где σ |
(ω ) = s |
— напряжение в свободно вращаю- |
||
θ0 |
0 |
θ0 |
|
|
щемся диске при номинальной скорости ω. Последняя зависимость очевидна: напряжения (любые) в свободно
вращающемся диске пропорциональны квадрату угловой скорости.
Для диска (см. рис. 14.38) получено значение s′ =
θ0
= 315 МПа, и если принять u = 0,5 мм, то из (14.81) найдем
|
|
|
|
0 |
|
|
n |
|
|
|
5 |
|
1 ⁄ 2 |
|
|
|
|
|
||
ос |
|
2,16 |
æ10 |
æ0, 0005 |
|
|
------- |
= |
---------------------------------------------- |
|
= 1,17 . |
||
n |
|
0,25æ315 |
||||
0 |
|
|
|
|
|
|
Обычно принимают определенное значение n /n ≥
ос 0
≥ 1,15 и по нему находят натяг. В соответствии с рекомендацией Международной электротехнической комиссии
следует условие n /n ≥ 1,2.
ос 0
Выполнение рекомендации МЭК в рассматриваемом примере приводит к необходимости увеличения натяга
пропорционально n2 , т.е. до |
u′ = 0,5æ(1,2 ⁄ 1,17)2 = |
ос |
0 |
= 0,526, и к некоторому снижению коэффициента запаса прочности: до величины
n′ = 1,574(1,17 ⁄ 1,2)2 = 1,496.
τ
Из зависимости (14.78) можно получить закон изменения контактного давления при изменении частоты вращения в виде
q |
(n |
⁄ n )2 – (n ⁄ n )2 |
|
||
|
ос 0 |
|
0 |
|
|
----- |
= ------------------------------------------------------ |
|
2 |
|
(0 ≤ n ≤ n ), (14.82) |
q |
|
|
|
ос |
|
0 |
|
(n |
⁄ n ) – 1 |
|
|
|
|
ос |
0 |
|
|
где q — контактное давление на поверхности
посадки при любой частоте n; q — то же при
0
номинальной частоте n = n .
0
Пример 14.12. Для рассматриваемого диска рассчитать контактное давление на поверхности посадки при
остановленном роторе и n /n = 1,2.
ос 0
Решение. Приняв q = 46 МПа, по (14.82) найдем
0
1,22
q = 46------------------ |
= 150 МПа. |
1,22 – 1 |
|
В остановленном роторе контактное давление на |
|
поверхности расточки в |
данном случае более чем в |
3 раза превышает его значение при номинальной частоте вращения.
В дисках сварного ротора (см. рис. 11.5) не делают центральных отверстий, распределение напряжений по радиусу в них наиболее благоприятное из всех типов роторов. Профиль диска может быть выполнен такой формы, что напряжения в нем
постоянны по радиусу и одинаковы: σr = σ = σ —
θ 0
постоянная величина. Соответствующий диск называется диском равного сопротивления. Диски сварных роторов по форме выполняются такими же, что и диск равного сопротивления, или близкими
477
к нему. Профиль диска равного сопротивления выражается зависимостью
ν(1 – r2 |
⁄ r2) |
|
|
h ⁄ h = e |
1 [ν = ρω2r2 |
⁄ (2σ |
) ], (14.83) |
1 |
1 |
|
0 |
где h — текущая толщина диска; h |
— толщина |
||
|
|
1 |
|
диска на периферийном радиусе r ; σ — напряже-
1 0
ние в диске (σr = σ = σ ).
θ0
Сваривание дисков производится по перемычкам, представляющим собой участки цилиндрических оболочек (см. рис. 11.5). Радиусы перемычек выбирают из условия, чтобы радиальное смещение
перемычки u под действием центробежных сил
п
при вращении и радиальное смещение диска в
месте его стыковки с перемычкой u были одина-
д
ковы. Это условие обеспечивает отсутствие изгибающих моментов и перерезывающих сил в перемычке и, следовательно, в сварном шве.
Равенство радиальных смещений перемычки и диска в месте их стыковки запишем в виде
u= u ,
пд
где
u |
σ |
|
ρω2r2 |
|
п |
|
п |
св |
|
r------ = |
-----E = |
-----------------E ; |
(14.84) |
|
св |
|
|
|
|
u |
1 |
|
|
|
д |
|
|
|
|
------ = |
E--- |
(σ |
– μσ ) . |
(14.85) |
r |
0 |
0 |
|
|
|
|
|
св
Здесь r — радиус перемычки (место сварного
св
шва). Приравнивая правые части (14.84), (14.85) и решая получающееся уравнение относительно r ,
|
|
|
|
|
|
|
св |
имеем |
|
|
|
|
|
|
|
|
|
σ |
(1 – μ) |
1 ⁄ 2 |
|
||
|
0 |
|
|
|
|
|
|
r |
= |
------------------------ |
. |
(14.86) |
|||
|
|
|
|
||||
|
св |
|
|
2 |
|
|
|
|
|
|
|
|
|
|
|
|
|
ρω |
|
|
|
||
|
|
|
|
|
|
|
Отметим, что условие u = u , выполненное при
п д
номинальной частоте вращения, остается справедливым при любой частоте, в частности при остановленном роторе, т.е. при выборе места сварного шва по (14.86) он оказывается свободным от изгибающих моментов и перерезывающих сил при любой частоте вращения.
Пример 14.13. Определить профиль диска и месторасположение перемычки в сварном роторе при следующих условиях.
Принять в диске равного сопротивления σ = σ |
|
= σ = |
|
|
r |
θ |
0 |
= 250 МПа, что при σ = 500 МПа дает n |
= 2. |
|
|
s |
s |
|
|
Нагрузка от лопаток h σ |
= 10,5 МПаæм, она соот- |
1 |
r1 |
ветствует нагрузке насадного диска (см. рис. 14.38).
Радиус диска r = 0,6 м; ρ = 7800 кг/м3; ω = 314,16 рад/с.
1
Решение. Находим толщину диска сварного ротора на периферии
|
h1σr1 |
|
10,5 |
h′ = |
-------------σ′ |
= |
---------- = 0,042 м = 42 мм. |
1 |
|
250 |
|
|
r1 |
|
|
Предварительно получаем
ν= ρω2r2 ⁄ (2σ ) = 7800æ(314,16æ0,6)2/(500æ106) =
1 0
=0,5543.
По (14.83) определяем толщину диска в центре:
h = h(r = 0) = 0,042 е0,5543 = 0,073 м = 73 мм.
0
Расположение перемычки находим по (14.86), прини-
мая μ = 0,3: |
|
|
|
250æ106 (1 – 0,3) |
1 ⁄ 2 |
r = ----------------------------------------------- |
= 0,477 м. |
|
св |
7800æ314,162 |
|
|
|
Как видно из простого примера, диск сварного ротора можно выполнить тонким при высоком коэффициенте запаса прочности, что достигается отсутствием центральной расточки и посадки диска на вал.
Цельнокованые роторы выполняются, как правило, для ЦВД и ЦСД, где температура пара максимальна. Однако и для ЦНД цельнокованые роторы в последнее время находят все большее распространение (см. рис. 11.6). В случае выполнения ротора без центрального канала он представляет собой вращающийся цилиндр, для которого напряжения выражаются зависимостями:
|
|
|
|
|
2 |
|
|
|
2 |
|
|
|
|
|
|
|
|
σr = σr1 + ar(r1 |
– r |
) |
; |
|
|
|
|
||||||
|
|
|
|
|
|
|
|
|
|
|
|
|
|
|
|
|
|
|
|
|
|
|
|
|
a |
2 |
|
|
|
|
|
|
|
|
|
|
|
|
|
|
|
|
|
||||
|
|
|
|
|
2 |
|
|
|
θ |
|
|
|
|
||
|
|
σθ = σr1 + ar r |
|
– |
----- |
r ; |
|
|
|
||||||
|
|
|
|
|
|
(14.87) |
|||||||||
|
|
1 |
ar |
|
|
||||||||||
|
|
|
|
|
|
|
|
|
|
|
|
|
|
||
|
|
|
|
|
|
|
|
|
|
|
|
|
|
|
|
|
|
|
|
|
|
|
|
|
|
|
|
|
|
|
|
|
|
|
μ |
|
|
|
|
2 |
2 |
|
2 |
|
|
|
|
|
|
σz = |
|
|
|
|
|
|
|
|
|||||
|
|
--------------------- ρω (r1 |
– 2r |
|
), |
|
|
||||||||
|
|
|
4(1 – μ) |
|
|
|
|
|
|
|
|
|
|
|
|
|
|
|
|
|
|
|
|
|
|
|
|
|
|
|
|
|
|
3 – 2μ |
|
a |
θ |
|
|
|
1 + 2μ |
|
|
|
|
||
|
|
ρω2; |
|
|
|
|
|
|
|
|
|||||
гдеa |
|
= --------------------- |
----- |
= |
|
----------------; |
|
r |
— |
радиус |
|||||
|
r |
8(1 – μ) |
|
a |
r |
|
|
|
3 – 2μ |
|
1 |
|
|
||
|
|
|
|
|
|
|
|
|
|
|
|
|
|
|
цилиндра; σr — осредненное радиальное напряже-
1
ние на радиусе r .
1
Пример 14.14. Оценить напряжение в цельнокованом роторе, изображенном на рис. 11.6, в зоне последней ступени, приняв приведенное напряжение в зоне последней
ступени σ = 110 МПа (по оценке); ρ = 7800 кг/м3; r1
μ = 0,3; r = 0,61 м. Оценить запас прочности, если пре-
1
дел текучести материала σ = 500 МПа. s
478
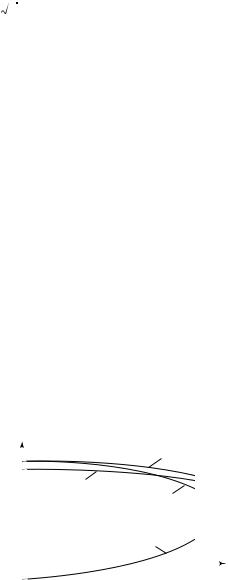
Решение. Подставляя известные величины в формулы (14.87), получаем расчетные соотношения:
r2
σr = 110 + 122,8 1 – ---- ;
r
1
|
|
|
|
|
|
|
|
|
|
2 |
|
r |
|
2 |
|
σ = 110 + 122,8 |
|
|
|
|
|
|
|||||||||
|
1 – |
-- |
|
---- |
|
; |
|||||||||
|
θ |
|
|
|
|
|
|
|
3 |
r |
|
||||
|
|
|
|
|
|
|
|
|
|
|
|
1 |
|
|
|
|
|
|
|
|
|
|
r |
|
2 |
|
|
|
|
|
|
σ |
|
|
|
|
|
|
|
|
|
|
|
|
|||
|
= 30,7 |
|
1 – 2 |
|
---- |
. |
|
|
|
|
|
||||
|
z |
|
|
|
r |
|
|
|
|
|
|
|
|||
|
|
|
|
|
|
|
|
|
|
||||||
|
|
|
|
|
|
|
1 |
|
|
|
|
|
|
|
По полученным зависимостям составим табл. 14.2. В последней строке табл. 14.2 приведены значения интенсивности напряжений, определяемые по зависимости
|
2 |
2 |
2 |
2 1 ⁄ 2 |
σ* |
= -------[(σr – σθ) |
|
+ (σθ – σz) |
+ (σz – σr) ] . |
|
2 |
|
|
|
На рис. 14.40 представлены графики распределений напряжений в цельнокованом роторе, из которых видно, что в цельнокованом роторе без центрального канала напряжения по радиусу меняются достаточно плавно. По одной из теорий прочности критерием является интенсивность напряжений (так называемое октаэдрическое
напряжение). Как видно, σ меняется по радиусу мало, в
*
определенном смысле можно признать, что цельнокованый ротор без центрального канала близок к условиям равнопрочности.
Определим коэффициент запаса по пределу текучести
по состоянию в центре ротора: |
|
|
|
|
|
|||||||
|
|
ns = σ0,2 |
⁄ σ*0 = 500 ⁄ 202,1 ≈ 2,5 , |
|
|
|||||||
что является вполне допустимым (с запасом). |
|
|
||||||||||
Та бл и ц а |
14.2. Напряжения в цельнокованом роторе, МПа |
|||||||||||
|
|
|
|
|
|
|
|
|
|
|
|
|
|
|
|
|
|
|
|
|
r/r |
|
|
|
|
|
|
|
|
|
|
|
|
1 |
|
|
|
|
Напряжение |
|
|
|
|
|
|
|
|
||||
|
|
|
|
|
0 |
|
0,25 |
0,5 |
0,75 |
|
1,0 |
|
|
|
|
|
|
|
|
|
|
|
|
|
|
σ |
|
|
|
|
232,8 |
|
225,1 |
202,1 |
163,7 |
110 |
||
r |
|
|
|
|
|
|||||||
σ |
|
|
|
|
232,8 |
|
227,7 |
212,3 |
186,7 |
150,9 |
||
θ |
|
|
|
|
|
|
|
|
|
|
|
|
σz |
|
|
|
|
30,7 |
|
26,9 |
15,3 |
–3,8 |
–30,7 |
||
σ |
|
|
|
|
202,1 |
|
199,5 |
192,1 |
180,1 |
165,0 |
||
* |
|
|
|
|
|
|
|
|
|
|
|
|
|
|
|
|
|
|
|
|
|
|
|
|
|
r, , z, |
|
|
|
|
|
|
|
|
||||
|
|
|
|
|
|
|||||||
*, МПа |
|
|
|
|
|
|
|
|
||||
|
|
|
|
|
|
|
|
|
||||
|
|
|
|
|
|
|
* |
|
r |
|
|
|
|
|
|
|
|
|
|
|
|
|
|
|
|
|
|
|
|
|
|
|
|
z |
|
|
|
|
|
|
|
|
|
|
|
|
|
|
|
|
|
|
0 |
|
|
|
|
|
|
1 |
r/r1 |
Рис. 14.40. Распределения напряжений в цельнокованом
РНД без центрального канала
Если в цельнокованом роторе выполняется центральный канал (для удаления наименее качественного материала и для контроля качества материала в наиболее рискованной области слитка), то напряженное состояние ротора в зоне центрального канала резко отличается от состояния рассмотренного ротора. На поверхности цент-
рального канала σ = 0, окружное напряжение возрастает r0
примерно вдвое: σ′ = 2σ , осевое напряжение практи-
θ0 θ0
чески не меняется. При этом интенсивность напряжений
на поверхности канала станет σ′ ≈ 451 МПа, и коэффи-
*0
циент запаса будет недопустимо низким:
n′s = 500 ⁄ 451 ≈ 1,1 .
Поэтому РНД с предельно длинными лопатками стремятся выполнять без центрального канала.
Трещиностойкость дисков в условиях коррозионной среды. Коррозионное растрескивание под напряжением роторов паровых турбин проявляется в эксплуатации, как правило, в роторах с насадными дисками, находящимися в зоне фазового перехода от перегретого пара к влажному.
Коррозионное растрескивание под напряжением есть процесс зарождения и развития трещины, протекающий при постоянной нагрузке и умеренной температуре (без ползучести). Главными факторами, определяющими зарождение и развитие трещины, являются композиционный состав и термообработка материала, температура эксплуатации, уровень напряжений и агрессивность окружающей среды.
Для дисковых и роторных сталей существенное влияние на КРН оказывает термообработка. При этом чем выше предел текучести, на который проведена термообработка, тем больше склонность стали к КРН. Причинами преимущественной подверженности КРН насадных дисков являются: вопервых, высокий уровень напряжений в них в таких местах, как зоны посадочной поверхности и особенно шпоночного паза, разгрузочных отверстий в дисках, замковых соединений (рис. 14.41); во-вто- рых, конструктивные особенности роторов, проявляющиеся в том, что в них имеются проходы, в которых движение пара происходит с малыми и переменными скоростями. При переменном режиме работы турбины зона фазового перехода мигрирует по проточной части, некоторые ступени попеременно попадают то в область перегретого, то в область влажного пара. При этом в проходах шпоночных пазов, разгрузочных отверстий, в камерах между дисками и диафрагмами, в щелях замковых соединений происходит попеременное подсушивание и увлажнение поверхностей. Это приводит к концентрированию коррозионно-активных растворов и образованию на поверхностях деталей жидких и твердых пленок, содержащих коррозионно-актив- ные вещества высокой концентрации, вызывающие
479
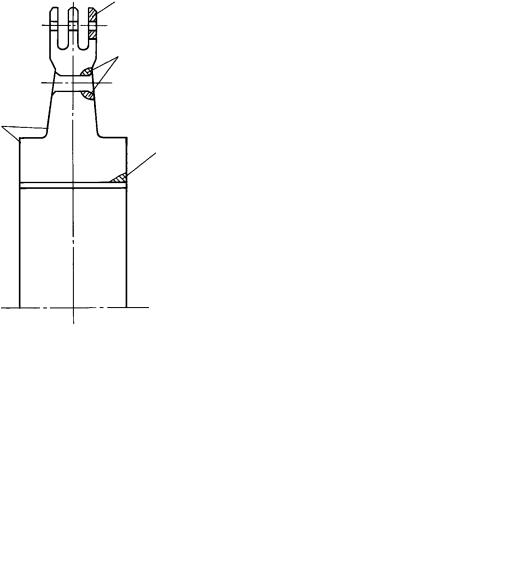
3 |
h, кДж/кг |
2
4
1
Рис. 14.41. Зоны преимущественного трещинообразования в
дисках (по приоритету):
1 — шпоночный паз; 2 — разгрузочные отверстия; 3 — обод
диска около отверстий под заклепки; 4 — поверхность полотна
и ступицы
при высоких напряжениях интенсивный рост коррозионного растрескивания.
Повышение температуры среды вызывает снижение стойкости к коррозионному растрескиванию. Поэтому КРН в дисках наблюдается преимущественно в турбинах без промежуточного перегрева пара. В этих турбинах область фазового перехода располагается в диапазоне температуры 120—140 °С, в то время как в турбинах с промежуточным перегревом эта область лежит в диапазоне 70—80 °С. На рис. 14.42 в h, s-диаграмме показана (заштрихована) зона образования коррозионно-активных растворов высокой концентрации.
Из рисунка видно, что линии расширения пара пересекают зону образования коррозионно-актив- ных растворов при заметно разных температурах в случаях турбин с промежуточным перегревом пара и без него. Основными коррозионно-активными примесями (загрязнениями) являются щелочи (NaOH, KOH), соли (NaCl и др.), кислоты (угольная, кремниевая и др.). Концентрированные растворы этих веществ в виде капель образуются при расширении пара в зоне фазового перехода несколько выше и ниже линии насыщения.
Главными определяемыми параметрами для КРН при конкретной обстановке являются: дли-
2800 |
|
150 |
C |
|
|
|
|
|
|||
|
МПа |
|
|
|
100 C |
|
|
|
|
|
|
0,5 |
|
1 |
|
|
|
|
|
|
|
|
|
2600 |
|
|
|
|
1,0 |
|
|
МПа |
|
|
2 |
|
|
|
|
|
|
|
0,1 |
|
|
МПа |
0,95 |
|
|
|
|
||
|
|
0,02 |
|
||
2400 |
|
|
|
||
|
|
|
|
|
|
|
|
|
|
|
0,90 |
2200 |
|
7,0 |
|
|
7,5 s, кДж/(кгæК) |
6,5 |
|
|
|
Рис. 14.42. Зона образования коррозионно-активных раство-
ров высокой концентрации (заштрихована) и процессы рас-
ширения пара в h, s-диаграмме:
1 — в турбинах без промежуточного перегрева пара; 2 — в тур-
бинах с промежуточным перегревом пара; 1,0; 0,95; 0,90 —
линии постоянной сухости пара
l
lкр
t
I |
II |
III |
Рис. 14.43. Процесс зарождения и развития коррозионной
трещины под напряжением:
I — инкубационный период (трещина отсутствует); II — период
постепенного подрастания трещины при постоянной нагрузке;
III — быстрое распространение трещины до разрушения детали
тельность инкубационного периода τ — времени
инк
от первоначального нагружения детали до появления макротрещины размером порядка диаметра зерна; скорость распространения трещины dl / dt (l — глу-
бина трещины); критический размер трещины l .
кр
В общем случае процесс повреждения детали при КРН можно разделить на три этапа (рис. 14.43). Первый этап — инкубационный период, второй
480