
паровые и газовые турбины для электростанций
.pdf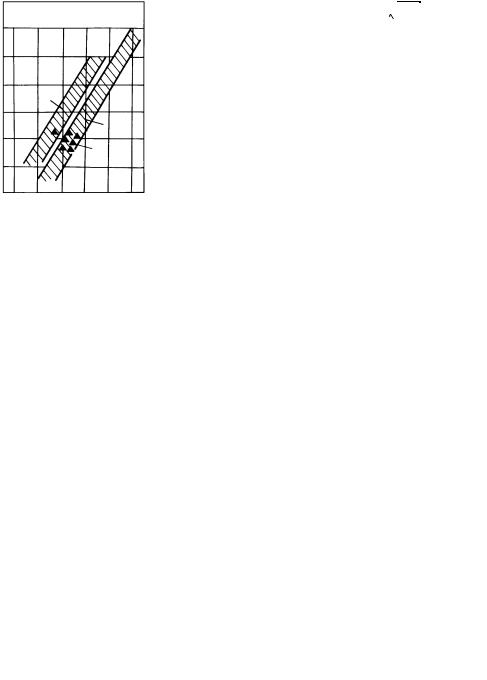
этап — постепенное увеличение трещины до кри-
тического размера l , третий этап — быстрое (со
кр
скоростью звука в материале) развитие трещины, приводящее к разрушению детали.
Инкубационный период в первую очередь зависит от напряжений. На рис. 14.44 по данным фирмы АВВ показано влияние напряжений и среды на инкубационный период для дисковой стали марки 20Х3НМ. На рисунке представлены также отечественные опытные данные по оценке инкубационного периода для дисков ступеней турбин типов Т-50-12,8 и Т-100-12,8 производства ТМЗ. Анализ проведен для большого числа дисков, находившихся в экс-
плуатации, и характеризует уровень τ , а также
инк
косвенно отражает коррозионную активность среды в реальных условиях эксплуатации. Как видно, для названных дисков инкубационный период находится в пределах 30—100 тыс. ч.
При заданных напряжениях второй важный параметр — скорость распространения трещин при КРН — существенно зависит от термообработки и
конкретно от предела текучести материала σ , на
0,2
который производится термообработка. Влияние
σна скорость распространения трещин представ-
0,2
лено на рис. 14.45 (по данным фирмы АВВ). Там же приведены данные обследования дисков отечественных турбин, из которых следует, что скорость распространения трещин в условиях эксплуатации турбин Т-50-12,8 и Т-100-12,8 составляет порядка
v = 10–10 м/с.
Третий важный параметр — критический размер
трещины l — определяется, во-первых, уровнем
кр
номинальных напряжений и, во-вторых, коэффициентом вязкости разрушения Kс. Связь между ними
%инк, ч 105
21
104
|
|
|
– 3 |
|
|
|
103 |
|
|
|
|
|
|
0,3 |
0,4 |
0,5 |
0,6 |
0,8 |
1,0 |
1,2 |
|
|
|
|
|
/ 0,2 |
Рис. 14.44. Инкубационный период для дисковой стали марки
20Х3НМ:
1 — в среде чистого пара; 2 — в 28—35 %-ном растворе NaCl
(1 и 2 — по данным фирмы ABB); 3 — опытные точки по экс-
плуатационным данным для серии турбин
представима в виде основного соотношения механики разрушения
μσ πl = Kc , (14.88)
кр
где μ — некоторый безразмерный коэффициент, зависящий в первую очередь от формы детали и формы и типа трещины, а также от относительного размера трещины; σ — номинальное растягивающее напряжение, перпендикулярное плоскости трещины.
Коэффициент вязкости разрушения Kс — харак-
теристика материала, определяемая экспериментально и приводимая в справочниках по свойствам материалов. Он зависит также от вида напряженного состояния. Минимальное значение Kс наблю-
дается для плоской деформации, в этом случае
коэффициент обозначается K с.
I
В практике эксплуатации теплофикационных турбин трещинообразование возникло в массовом количестве в середине 80-х годов прошлого столетия после того, как введенные турбины Т-50 и Т-100 отработали 30—100 тыс. ч.
Проведенные обстоятельные исследования показали, что для повышения трещиностойкости дисков надлежит применять следующие меры:
снижение концентрации напряжений, в частности отказ от осевых шпонок и применение торцевых шпонок;
применение сталей с пониженным пределом текучести;
поддержание чистоты пара на нормативном уровне;
vп, м/c |
|
|
|
10–5 |
|
= 30…60 МПаæм1/2 |
|
K |
Ic |
||
10–6 |
|
|
|
|
|
|
|
10–7 |
|
|
|
10–8 |
|
|
|
10–9 |
|
2 |
|
|
|
|
|
|
|
|
1 |
10–10 |
|
|
3 |
|
|
|
|
10–11 |
|
|
|
10–12 |
|
|
1200 0,2, МПа |
400 |
800 |
Рис. 14.45. Скорость роста трещины при коррозионном рас-
трескивании под напряжением стали марки 20Х2Н1М при
различном значении предела текучести в двух средах:
1 — испытания образцов в деаэрированной воде при 100 °С;
2 — испытания в 28 %-ном аэрированном растворе NaOH при
110 °С; 3 — опытные точки по эксплуатационным данным для
серии турбин
481
ввод добавок — пленкообразующих веществ, например октадециламина (ОДА), для отмыва поверхностей и защиты их от коррозионно-актив- ных отложений;
местная подача перегретого пара в камеры перед дисками и за ними в целях предотвращения контакта поверхностей дисков с коррозионно-актив- ными растворами в зоне фазового перехода.
В периоды остановки турбины производится проверка дисков, рабочих лопаток и хвостовых соединений в целях обнаружения трещин в них, для чего существуют различные методы, в частности метод ультразвуковой дефектоскопии, позволяющий обнаруживать поверхностные и глубинные трещины размером не менее 3 мм.
Наилучшим способом повышения надежности турбин при обнаружении трещин в дисках является замена поврежденных деталей на новые. Тем не менее разработаны и применяются методы ремонта поврежденных дисков. В некоторых случаях производят выборку металла в месте трещины. Возможности и способы ремонта деталей с трещинами регламентируются циркулярами.
Пример 14.15. При инспекции диска обнаружена трещина в зоне осевого шпоночного паза (см. рис. 14.41,
зона 1). Номинальные напряжения в этом месте |
σ = |
|
θ |
= 510 МПа, предел текучести материала диска |
(сталь |
34ХН3М) σ = 850 МПа, коэффициент вязкости разру-
0,2
шения K = |
136 МПаæм1/2. Глубина трещины l |
= |
Iс |
|
нач |
= 10 мм. |
|
|
Требуется |
ориентировочно определить критический |
размер трещины l и время достижения трещиной кри-
|
|
|
|
кр |
|
|
|
|
|
|
|
|
|
тического размера. |
|
|
|
|
|
|
|
|
|
||||
|
Решение. Приняв оценочно μ = 1 и K = K |
= 136, из |
|||||||||||
|
|
|
|
|
|
|
|
|
|
|
с |
|
Iс |
условия (14.88) найдем критический размер: |
|
||||||||||||
|
|
|
|
|
1 ⁄ 2 |
|
|
|
|
|
|
|
|
|
|
|
1 |
KIc |
|
1 |
|
136 |
|
1 ⁄ 2 |
|
|
|
|
|
l = |
-- |
------- |
= |
-- |
-------- |
= 0,164 м. |
|||||
|
|
|
|
||||||||||
|
|
π |
|
π |
510 |
||||||||
|
|
кр |
σθ |
|
|
|
|
|
|||||
|
|
|
|
|
|
|
|
|
|
|
|
|
|
|
Оценив по рис. 14.45 скорость распространения тре- |
||||||||||||
щины v = 10–10 м/с, вычислим время до разрушения: |
|||||||||||||
|
l |
– l |
|
0,164 – 0,01 |
|
|
|
|
|
|
|||
|
кр |
нач |
|
|
|
10 |
|
|
|||||
τ |
= -------------------- = ----------------------------- |
= 0,154æ10 |
|
с ≈ 428 тыс. ч. |
|||||||||
|
разр |
v |
|
10–10 |
|
|
|
|
|
|
|
|
|
|
|
|
|
|
|
|
|
|
|
|
Приняв коэффициент запаса по времени порядка 10, придем к заключению, что диск с такой трещиной можно эксплуатировать в течение около 50 тыс. ч.
При проведении анализа ситуации с трещинообразованием в 80-х годах были случаи обнаружения трещин глубиной до 20 мм. При этом ни один диск не разрушился. Консервативно, учитывая результаты проверки, можно считать глубину трещины 20 мм допустимой.
Если это так, то рассматриваемый диск с трещиной
l= 10 мм можно эксплуатировать в течение дополни-
нач
тельного периода 482
0,02 – 0,01 8 τ = -------------------------- = 10 с ≈ 28 тыс. ч.
доп 10–10
Вследствие значительных повреждений турбины в случае разрушения одного диска (как показал опыт эксплуатации английской ТЭС Hincly-Point) обычно предпочитают не доверять ориентировочным оценкам остающейся долговечности и заменять диски при трещинах глубиной более 10 мм, а иногда и при меньшей их глубине.
Трещинообразование в роторах низкого дав-
ления в зонах фазового перехода. Как было ранее отмечено, переменные изгибные напряжения от собственного веса при правильном монтаже и нормальных условиях эксплуатации имеют столь малое значение (амплитуду), что не должны представлять опасность возникновения усталости. Однако реальные нештатные условия могут существенно повлиять на прочность роторов и привести к многочисленным их повреждениям.
Характерным примером такой осложненной ситуации является трещинообразование в ряде роторов турбин типа ПТ-135/160-12,8 (и некоторых других).
Во время проведения в июле 2003 г. ремонта комбинированного ротора среднего-низкого давления (РСНД) турбины этого типа на Волжской ТЭЦ была обнаружена кольцевая трещина на валу сборной части ротора между дисками последней и предпоследней ступеней. Часть НД — три последние ступени турбины ПТ-135 унифицированы почти полностью с одним потоком турбины Т-250/300-23,5, чертеж отсека которой изображен на рис. 11.1. Различие отсеков в сравниваемых турбинах состоит только в том, что рабочие лопатки последних ступеней имеют разную длину рабочей части: у турбины Т-250 она составляет 940 мм, а у турбины ПТ-135 — 830 мм (получена подрезкой лопатки длиной 940 мм).
До момента обнаружения трещины турбина имела наработку 184 тыс. ч и число пусков 114. Кольцевая трещина глубиной более 35 мм начиналась от угла канавки под упорное кольцо между предпоследним и последним дисками.
В последующее время (около двух лет) при инспекции 19 турбин этого типа на 11 из них были обнаружены аналогичные трещины различной глубины (до и более 25 мм). В одном случае на Карагандинской ТЭЦ на одной из турбин этого типа была обнаружена кольцевая трещина, занимавшая более 90 % поперечного сечения. Ротор после выемки и установки его на козлы разломился по этой трещине. Турбина имела наработку 154 тыс. ч.
На рис. 14.46 показан РСНД, трещины образовывались в первую очередь в канавках вала между дисками 24-й и 25-й ступеней, в нескольких слу-
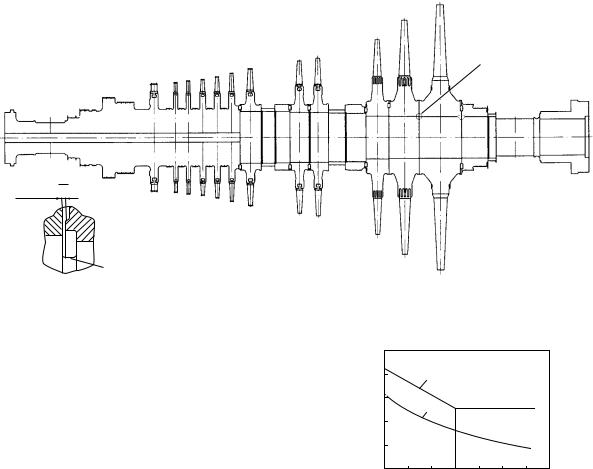
A
A
0,15—0,20
1
Рис. 14.46. Ротор турбины ПТ-135/160-12,8:
A — места возникновения и развития трещин; 1 — канавка вала (разъемное кольцо не показано)
чаях трещины были обнаружены в канавках за диском последней ступени.
Из 11 роторов с трещинами — шесть забракованы, один разрушился на козлах, четыре отремонтированы. В восьми турбинах трещины в РСНД не обнаружены. В числе неповрежденных турбин были такие, у которых наработка составляла от 83 до 172 тыс. ч.
Первичной причиной появления трещин в канавках, несомненно, явились переменные напряжения, вызванные изгибающим моментом от собственного веса ротора. Трещинообразование наблюдалось в зоне фазового перехода, трещины имели усталостное происхождение, поэтому повреждения обусловлены коррозионной усталостью. Галтели кольцевых канавок создавали концентраторы напряжений.
Кривая долговечности коррозионной усталости в отличие от обычной кривой для сталей в нейтральных средах не имеет явно выраженного предела усталости, или предел усталости появляется при зна-
чительно бóльших числах циклов N (108—109), его
p
значение ниже обычного предела усталости для соответствующего материала в нейтральной среде и существенно зависит от состава и концентрации коррозионно-активных веществ в рабочей среде.
Снижение усталостной прочности материала в коррозионно-активных средах происходит вследствие адсорбции и диффузии коррозионно-активных примесей в поверхностный слой детали.
–1, МПа |
|
|
|
|
|
|
|
500 |
|
|
|
|
|
|
|
400 |
|
1 |
|
|
|
|
|
300 |
|
2 |
|
|
|
|
|
|
|
|
|
|
|
|
|
200 |
|
|
|
|
|
|
|
100 |
|
|
|
|
|
|
|
0 |
|
|
|
|
|
|
|
104 |
105 |
106 |
107 |
108 |
109 |
1010 |
Np |
Рис. 14.47. Характеристики усталости стали в нейтральной
и коррозионно-активной средах:
1 — испытания на воздухе; 2 — испытания в коррозионно-
активной среде
На рис. 14.47 дано качественное сравнение кривых долговечности для материала в нейтральной и коррозионно-активной средах.
Пример 14.16. Попробуем оценить усталостную прочность РСНД турбины ПТ-135 по условиям для сечения с канавкой под упорное кольцо между дисками 24-й и 25-й ступеней под действием циклических напряжений от собственного веса ротора в предположении нейтральной среды, штатного монтажа.
Заданы следующие величины (рис. 14.48):
масса ротора 30 700 кг; длина ротора L = 6,860 м;
расстояние от правой опоры до рассматриваемого
сечения l = 1,226 м;
п
диаметр вала по дну канавки d = 0,475 м;
к
483
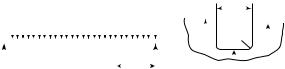
диаметры вала слева и справа от канавки d = 0,493 м,
л
d = 0,490 м.
п
На рис. 14.48 показана упрощенная схема нагружения вала за счет собственного веса: весовая нагрузка принимается равномерной, моменты от концевых частей (муфт) не учитываются.
Решение. Рассчитаем погонную нагрузку от собс-
твенного веса: |
|
|
|
|
|
|
G |
30 700æ9,81 |
|
||
|
q = --- |
= ------------------------------- = 43 902 |
Н/м. |
||
|
|
L |
|
6,86 |
|
Значения реакций при принятых предположениях |
|||||
составляют |
|
|
|
|
|
|
|
|
G |
30 700æ9,81 |
|
R |
= R |
= --- |
= ------------------------------- = 150 |
584 H. |
|
|
1 |
2 |
2 |
2 |
|
Изгибающий момент в сечении I—I |
|
||||
|
ql2 |
|
|
|
|
|
п |
= 150 584æ1,226 – 0,5æ43 902æ1,2262 = |
|||
M = R l |
– ------- |
||||
2 п |
2 |
|
|
|
|
= 151 622 Нæм.
Момент сопротивления по диаметру дна канавки (влиянием центрального канала пренебрегаем)
3
πdк πæ0,4753
W = -------- = ----------------------- = 0,01052 м3. 32 32
Номинальное напряжение изгиба в сечении I—I
M 151 622
σ= ---- = ------------------- = 14,413æ106 Па ≈ 14,4 МПа.
нW 0,01052
Теоретический коэффициент концентрации по разным данным:
α = 2,4…2,7.
σ
Принимаем максимальное значение α = 2,7. Ампли-
σ
туда переменного напряжения в месте концентрации σ = α σ = 2,7æ14,4 = 38,9 МПа.
аσ н
Для стали Р2М при σ = 680 МПа оценим предел
0,2
усталости по минимуму
σ |
= 0,3σ |
= 204 МПа. |
–1 |
|
0,2 |
Коэффициент запаса по пределу усталости |
||
|
σ |
204 |
|
–1 |
|
nf |
= -------- = ---------- = 5,24. |
|
|
σa |
38,9 |
В расчете величина σ |
принималась по максимуму, а |
|
|
а |
|
предел усталости — по минимальной оценке. Следова-
|
|
|
|
|
|
|
|
|
|
|
|
|
|
|
|
|
|
|
|
|
|
|
|
|
|
|
|
|
|
|
|
|
|
|
18 |
|
|
|
|
|
|
|
|
|
|
|
|
|
|
|
|
|
|
|
|
|
|
|
I |
|
|
|
|
|
|
|
|
|
|
|
|
|
r3 |
|
|
||||
|
|
|
|
|
|
|
|
|
|
|
|
|
|
|
|
|
|
|
|
|
|
|
|||||||||||||||||
|
|
|
|
|
|
|
|
|
|
|
|
|
|
|
|
|
|
|
|
|
|
|
|
|
|
|
|
|
|
|
|
|
|
|
|
|
|
||
|
|
|
|
|
|
|
|
|
|
|
|
|
|
|
|
|
|
|
|
|
|
|
|
|
|
|
|
|
|
|
|
|
|
|
|
|
|
||
|
|
|
|
|
|
|
|
|
|
|
|
|
|
|
|
|
|
|
|
|
|
|
|
|
|
|
|
|
|
|
|
|
|
|
|
||||
|
R1 |
I |
|
|
lп |
|
R2 |
|
|
|
|
|
|
|
|||||||||||||||||||||||||
|
|
|
|
|
|
|
|
|
|
|
|||||||||||||||||||||||||||||
|
|
|
|
|
|
|
|
|
|
|
|||||||||||||||||||||||||||||
|
|
|
|
|
|
|
|
|
|
|
|
|
|
||||||||||||||||||||||||||
|
|
|
|
|
|
|
|
|
|
|
|
|
|
a) |
|
|
|
|
|
|
|
|
|
|
|
|
|
493 |
|
|
475 |
б ) |
490 |
|
|||||
|
|
|
|
|
|
|
|
|
|
|
|
|
|
|
|
|
|
|
|
|
|
|
|
|
|
|
|
|
|
|
|
|
Рис. 14.48. К расчету статического изгиба ротора:
а — схема нагружения ротора; б — размеры канавки и вала
тельно, коэффициент запаса n ≥ 5,24, т.е. более чем f
достаточный при принятых нами идеальных условиях.
Вдействительности, как отмечалось, на разных станциях при одинаковых штатных условиях результаты инспекции показали совершенно разные повреждения роторов — от полного отсутствия трещин до развития трещин по всему сечению ротора.
Вчисле причин этого на первом месте следует считать разные степени загрязнения пара коррозионноактивными веществами, далее — различия в качестве монтажа и вибрационных напряжениях, т.е. в качестве эксплуатации (балансировка и пр.).
Вчисле факторов, способствующих возникновению и развитию кольцевых трещин, следует отметить недостаточную отстройку валопровода турбин ПТ-135/165-12,8 от крутильных колебаний по отношению к крутильным возбуждениям с частотой 2n = 100 Гц. По свидетельству Е.В. Урьева, одна из форм (третья) крутильных колебаний валопровода имеет частоту (по расчету УТЗ), практически совпадающую с частотой возбуждения 100 Гц, и при этом в опасном сечении (между 24-й и 25-й ступенями) имеет место максимум крутящего момента при колебаниях.
Длительная прочность цельнокованых роторов. Цельнокованые роторы высокого и среднего давления при температуре свежего и перегретого пара около 540 °С имеют в высокотемпературной части температуру металла свыше 500 °С (до 525— 530 °С). При значительных напряжениях, обусловленных вращением, низколегированные стали, из которых изготавливаются цельнокованые роторы, подвержены ползучести. В условиях развития ползучести материал повреждается во времени, в нем появляются поры, превращающиеся в микро-, а затем и макротрещины. Макротрещина может подрастать, достигать критического размера, при котором произойдет мгновенное разрушение детали по сечению с критической трещиной.
В практике паротурбостроения бывали случаи разрушения цельнокованых роторов вследствие ползучести по описанному механизму.
Процесс разрушения детали вследствие действия ползучести, подобно разрушению при КРН, можно разделить на три периода.
Первый период — инкубационный — от момента нагружения до появления трещины порядка размера зерна; второй период — развитие трещины до критического размера; третий мгновенный период — до разрушения детали.
Прочность материала в условиях ползучести
характеризуется пределом длительной прочности σ ,
д.п
определение которому дано ранее. Опытные значе-
ния σ получают при испытании серии цилиндри-
д.п
ческих образцов из данного материала при различных, но постоянных во времени значениях нагрузки
484
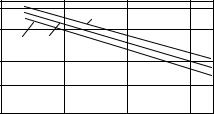
(напряжений) при различной (но также постоянной во времени) температуре. Как характеристика данного материала предел длительной прочности есть
функция двух величин: времени до разрушения t и
р
температуры металла при испытаниях T, °С:
σ |
= f (t , T ). |
(14.89) |
д.п |
р |
|
Опытные данные вида (14.89) приведены в справочниках по свойствам сталей. Зависимость (14.89) часто аппроксимируют функцией
|
–b |
|
|
t |
= Bσ |
, |
(14.90) |
р
где B, b — постоянные (не зависят от напряжения),
зависящие от температуры; σ = σ — предел дли-
д.п
тельной прочности.
Итак, смысл зависимости (14.89) или (14.90) состоит в следующем: образец из данного материала при растягивающем постоянном напряжении σ при постоянной температуре Т, °С, разрушится
через t часов.
р
Под «данным» материалом подразумевается материал (сталь) определенного химического состава и после определенной термообработки.
Совершенно очевидно, что если серию образцов (например, 10—20 образцов) подвергнуть испытаниям на длительную прочность при одинаковом для всех образцов напряжении σ и одинаковой темпера-
туре Т, °С, то время до разрушения t у разных
р
образцов серии вообще будет различным вследствие естественного разброса их свойств.
Время до разрушения есть величина случайная. Вследствие этого постоянные параметры B, b в детерминированной зависимости (14.90) относятся к некоторым осредненным величинам, которые находят из серий испытаний образцов, применяя для обработки результатов метод наименьших квадратов.
Пример характеристик длительной прочности представлен на рис. 14.49, где показаны: средние
д.п, МПа |
|
|
|
|
|
400 |
3 |
|
525 °C |
|
|
|
|
|
|
||
300 |
|
|
|
|
|
2 |
1 |
|
|
|
|
200 |
|
|
|
|
|
150 |
|
|
|
|
|
102 |
103 |
104 |
105 |
2·105 |
tp, ч |
Рис. 14.49. Зависимость предела длительной прочности от
времени до разрушения для стали Р2М (25Х1М1Ф) при тем-
пературе 525 °С:
1 — средние значения; 2 — нижняя граница полосы разброса;
3 — верхняя граница полосы разброса
значения (найденные методом наименьших квадратов), а также нижняя и верхняя границы полосы разброса опытных данных.
Средние значения соответствуют 50 %-ной вероятности неразрушения (P = 50 %). Смысл понятия вероятности неразрушения P = 50 % следующий. Если взять несколько (100) образцов из данного материала и нагрузить все образцы одинаковым напряжением (например, напряжением σ = = 200 МПа), соответствующим времени до разру-
шения t = 105, то 50 % образцов разрушится через
р
время t > 105 ч, а остальные 50 % — через t < 105 ч, а среднее время до разрушения будет составлять
около 105 ч.
Принято считать, что нижняя граница полосы разброса соответствует вероятности неразрушения P = 99 %, т.е. если взять 100 образцов и нагрузить их некоторым напряжением (σ = 180 МПа), соответствующим времени до разрушения, например,
105 ч (см. рис. 14.49, линия 2), то из 100 образцов
лишь один разрушится через 105 ч, а остальные 99 не разрушатся.
Для оценки длительной прочности цельнокованых роторов требуется сопоставить прочность материала, характеризуемую пределом длительной проч-
ности σ , с некоторой характеристикой напряжен-
д.п
ного состояния ротора в опасных зонах. Сложность выбора характеристики напряженного состояния усугубляется тем, что напряжения в цельнокованом роторе (ЦКР) изменяются во времени вследствие явления ползучести.
Основные опасные зоны в ЦКР находятся в высокотемпературных частях РВД и РСД, т.е. около первых ступеней ЧВД и ЧСД. Эти зоны показаны на рис. 14.50. Они являются зонами концентрации напряжений.
При первоначальном нагружении ротор находится в упругих условиях (как правило). После достижения достаточно высоких температур в роторе начинается процесс перераспределения напряжений: в местах повышенных напряжений происходит их снижение (релаксация); в областях низких напряжений обычно наблюдается некоторое их увеличение. С течением времени происходит изменение напряженного состояния в высокотемпературной части ротора от упругого состояния до
состояния установившейся ползучести. Состояние установившейся ползучести — это такое (предельное, достигаемое через неограниченное время) напряженное состояние, при котором напряжения и скорости деформации в каждой точке детали постоянны во времени. Для примера на рис. 14.51 представлены графики распределения номинальных напряжений σr, σθ, σz и интенсивности напряжений
485
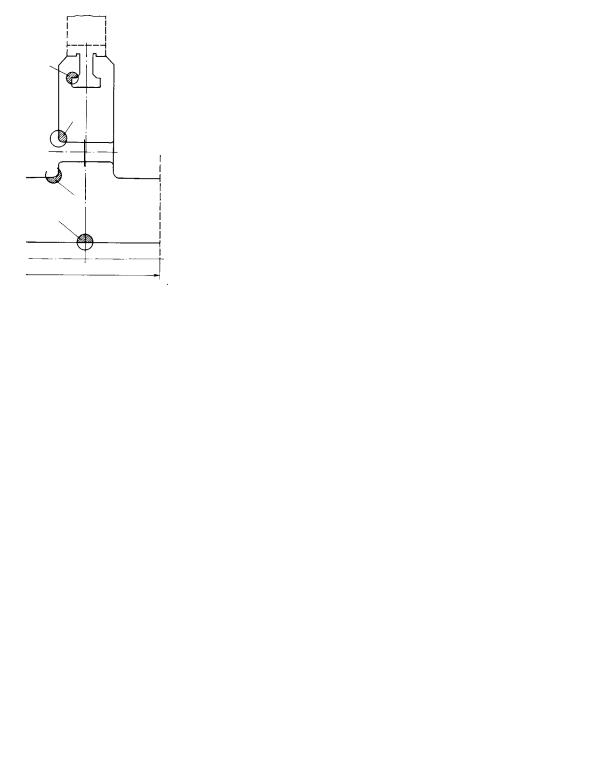
3
4
2
1
h0
Рис. 14.50. Фрагмент цельнокованого ротора с указанием
опасных зон:
1 — поверхность центрального канала ротора вблизи срединной
плоскости первого диска ротора; 2—4 — зоны соответственно
придисковой галтели, обода диска на внутренней галтели паза
для крепления рабочих лопаток, разгрузочных отверстий
σ в срединной плоскости диска для фрагмента
*
РСД турбины К-800-23,5. Напряжения показаны для упругого состояния материала и для состояния установившейся ползучести.
Как видно из рисунка, при перераспределении в
наибольшей степени снижаются напряжения σ , σ
θ *
на поверхности центрального канала.
Так, максимальное напряжение σ снижается от
θ
упр
σ ≈ 160 МПа и стремится к предельному значе-
θ
, МПа |
|
|
, МПа |
|||
150 |
|
|
|
|
|
80 |
|
|
|
|
|
||
|
|
|
|
|
|
|
100 |
|
|
|
|
40 |
|
|
|
|
|
|
|
|
|
|
|
|
|
|
|
50 |
* |
r |
|
|||
|
|
|
|
|||
|
|
|
|
|
||
0 |
|
|
|
z |
0 |
|
|
|
|
|
|
|
|
–50 |
|
|
|
|
|
–40 |
|
0 0,1 |
0,2 0,3 0,4 0,5 r, м |
0 0,1 |
а)
нию σ× ≈ 110 МПа в состоянии установившейся
θ
ползучести. Интенсивность напряжений изменяется
от σупр |
≈ 155 МПа до σ× ≈ 95 МПа. Радиальные |
* |
* |
напряжения σr мало меняются во времени, а осевые напряжения σz несколько возрастают в переходном процессе от упругого к установившемуся состоянию.
Определяющим длительную прочность является (в зависимости от принимаемого критерия
прочности) максимальное напряжение σ = σ |
, |
θ |
макс |
либо интенсивность напряжений σ , либо их комби-
|
|
|
* |
|
нация, например, в виде |
|
|
|
|
|
1 |
|
|
|
σ = --(σ |
|
+ σ ) . |
(14.91) |
|
с |
2 |
макс |
* |
|
Исходя из гипотезы суммирования повреждений материала, претерпевающего переменные во времени напряжения, введено понятие эквивалентного напряжения, определяемого соотношением
1 |
τ |
b |
|
1 ⁄ b |
|
σэ = -- |
∫ [σ(t)] |
|
dt |
, |
(14.92) |
τ |
0 |
|
|
|
|
где τ — общее время работы материала; t — текущее время от начала работы; σ(t) — значимое напряжение (σ , σ или σ ) в зависимости от времени. Напри-
макс * |
с |
мер, на рис. 14.52 дано предполагаемое по расчету изменение во времени максимального напряжения на поверхности центрального канала (см. рис. 14.50, зона 1) для РСД турбины К-800-23,5. Расчет выполнен по одной из гипотез ползучести.
Смысл введенного эквивалентного напряжения
состоит в следующем. Напряжение σ есть постоян-
э
ное напряжение, вызывающее такое же повреждение материала, какое вызывает переменное напря-
r1 = 38,3 МПа
|
|
R 126 |
|
|
|
* |
|
12 |
1 004 |
990 860 |
138 |
780 |
||
r |
|
|
z |
|
|
|
|
135 |
h0 = 307,6 мм
0,2 0,3 0,4 0,5 r, м
б) |
в) |
Рис. 14.51. Распределения по радиусу диска и вала номинальных упругих (а) и в состоянии установившейся ползучести (б)
напряжений для первой ступени ЦСД турбины К-800-23,5; фрагмент РСД (в)
486
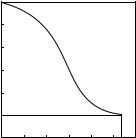
макс, МПа
150
140
130
120
110
0
110 102 103 104 105 t, ч
Рис. 14.52. Изменение максимального напряжения σ |
= σ |
макс |
θ |
на поверхности центрального канала во времени для фраг-
мента РСД
жение σ(t) в опасной точке детали за одинаковое время τ.
Поэтому условие прочности по состоянию мате-
риала в опасной точке через σ |
запишется в обыч- |
|
|
э |
|
ном (простом) виде |
|
|
σ – σ |
< 0. |
(14.93) |
э |
д.п |
|
Коэффициент запаса по длительной прочности будет иметь вид
n |
|
= σ ⁄ σ . |
(14.94) |
|
|
д.п |
д.п |
э |
|
Строгих норм |
к |
выбору |
n |
не существует. |
|
|
|
д.п |
|
В зависимости от |
тяжести |
последствий аварии |
вследствие исчерпания длительной прочности запас меняется в пределах
n = 1,1…1,6, |
(14.95) |
д.п |
|
если n вычисляют по σ |
с вероятностью нераз- |
д.п |
д.п |
рушения P = 50 %. |
|
Для вероятности P = 99 % следует принять
допустимым n > 1, тем самым будет обеспечено
д.п
условие: из 100 турбин данного типа, наработавших
заданный срок (например, 2æ105 ч), не более чем одна получит в опасной зоне трещину порядка размера зерна, а остальные 99 турбин не будут иметь начальных трещин.
В табл. 14.3 приведены характеристики длительной прочности стали двух марок, из которой выполнены РВД и РСД большинства отечественных турбин.
Данные разных источников по значениям σ не
д.п
совпадают. Приведенные в таблице сведения соответствуют отраслевому стандарту и, по-видимому, соответствуют вероятности неразрушения Р = 50 %.
Пример 14.17. Оценим запас длительной прочности по состоянию на поверхности центрального канала РСД (см. зона 1 на рис. 14.50) при следующих заданных условиях. Температура фрагмента ЦКР считается постоянной
по всему объему и равной 525 °С. Расчетные напряжения во фрагменте представлены на рис. 14.51. Срок службы
ротора τ = 105 ч. |
|
Закон изменения максимального напряжения σ |
= σ |
макс |
θ |
на поверхности центрального канала во времени дан на рис. 14.52.
Показатель в законе длительной прочности (14.90) по оценке наклона прямых, данных на рис. 14.49, можно принять b = 9,5. Для решения задачи необходимо определить эквивалентное напряжение по (14.92), где дан график σ(t) на рис. 14.52. Проведя вычисления, получим:
σ |
= 136 МПа |
для τ = 105; |
|
э |
|
σ |
= 132 МПа |
для τ = 2æ105. |
|
э |
|
Коэффициент запаса по длительной прочности
n= σ ⁄ σ = 181 ⁄ 136 = 1,33,
д.п д.п э
где σ = 181 МПа определено по табл. 14.3 для срока
д.п
службы 105 ч и для температуры металла 525 °С. Полученное значение гарантирует надежность РСД в
зоне центрального канала, так как достаточно, по-види-
мому, иметь n > 1,1…1,3.
д.п
Пример 14.18. В практике отечественного паротурбостроения были разрушения цельнокованого ротора по механизму ползучести. На турбине К-500-23,5 произошло разрушение обода первого диска ротора среднего давления. Фрагмент ротора схематично изображен на рис. 14.53, а, профиль обода — на рис. 14.53, б. Трещина ползучести возникла в переходной галтели М в наиболее напряженной точке сечения I—I со стороны входа пара.
Обрыв участка обода длиной по окружности не более 300 мм произошел после 83 тыс. ч эксплуатации при 252 пусках турбины. Температура металла в месте разрушения составляла примерно 520 °С. Материал ротора — сталь 20ХНЗМВФ (ЭИ-415).
Оценка номинального напряжения в сечении I—I дает
σ = 110…130 МПа (в зависимости от принятых размеров r
лопаток и влияния саморазгрузки обода диска выше сече-
ния I—I). Радиус галтели в зоне М r = 2,5 мм.
1
Та бл и ц а 14.3. Пределы длительной прочности роторных сталей
|
|
σ , МПа, не менее, при |
||
|
|
д.п |
|
|
|
|
времени до разрушения, ч |
||
Марка стали |
Температура, °С |
|
|
|
|
|
1,0æ105 |
1,5æ105 |
2æ105 |
|
|
|
|
|
25Х1М1Ф |
500 |
216 |
210 |
206 |
(Р2М) |
|
|
|
|
|
525 |
181 |
173 |
167 |
|
550 |
147 |
141 |
137 |
|
|
|
|
|
20ХН3МВФ |
500 |
220 |
216 |
213 |
(ЭИ415) |
|
|
|
|
|
525 |
189 |
184 |
181 |
|
550 |
161 |
158 |
155 |
|
|
|
|
|
487
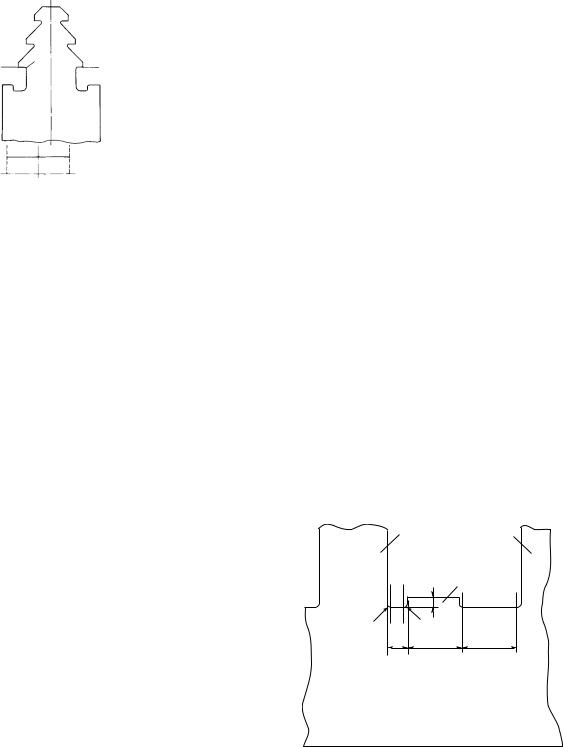
I M I
а) б)
Рис. 14.53. Фрагменты РСД турбины К-500-23,5:
а — фрагмент вала и диск первой ступени; б — обод диска пер-
вой ступени; М — место зарождения трещины ползучести
Попробуем оценить прочность обода диска. Если не учитывать концентрации напряжений в галтели (зона М), то коэффициент запаса по длительной прочности
|
усл |
|
|
nд.п |
= σд.п ⁄ σrI = 195 ⁄ 110 = 1,77, |
где σ |
= 195 МПа найдено интерполяцией данных |
|
|
д.п |
|
табл. 14.3 для t |
= 105 ч на температуру 520 °С; σ — |
|
|
p |
rI |
номинальное (без учета концентрации) растягивающее напряжение в опасном сечении.
Без учета концентрации обод имеет запас по длительной прочности существенно больше требуемого. Учтем влияние концентрации напряжений в галтели по зависимости (14.35), использованной ранее для оценки длительной прочности в хвостовике лопатки этой же ступени.
Для галтели типового обода в соответствии с отраслевым стандартом
α = 5,45.
σ
По справочным данным можно принять: n = 2,92. По (14.35) получаем
k× = 5,452 ⁄ 3,92 = 5,450,510204 = 2,375 .
σ
Определяем напряжение в сечении I—I в состоянии установившейся ползучести:
σ× ≈ k σr = 2,375æ110 = 261 МПа.
σ I
Коэффициент запаса по длительной прочности при оценке для состояния установившейся ползучести
n× = σ |
|
⁄ σ× = 195 ⁄ 261 = 0,747. |
д.п |
д.п |
|
Запас прочности |
недостаточен (надо иметь n > 1). |
|
|
|
д.п |
Отметим, что проведенная оценка, по-видимому, завышена,
так как было принято нижнее значение σ и, кроме того, в rI
качестве эквивалентного принято напряжение установив-
×
шейся ползучести. В действительности σ > σ .
э
В рассмотренном случае разрушение обода произошло вследствие неучета при проектировании турбины влияния концентрации напряжений в условиях ползучести.
488
Термоусталость роторов. Повторные переходные режимы турбины, обусловленные пусками — нагружениями и разгружениями — остановками, происходят при изменение параметров пара (температуры и давления) в проточной части турбины и вызывают переменные во времени температурные деформации и температурные напряжения в элементах ротора.
Основными факторами, определяющими уровень температурных напряжений и деформаций на поверхности детали, являются: разность температур подаваемого пара и металла омываемой паром поверхности детали; скорость изменения (закон во времени) этой разности; наличие концентраторов напряжений на поверхности ротора; интенсивность теплоотдачи от пара к поверхности детали. Температурные деформации и напряжения тем выше, чем больше значения этих величин. При определенных сочетаниях факторов в условиях повторных переходных режимов в опасных зонах роторов возникают повторные пластические деформации, которые могут быть причиной появления термоусталостных трещин в роторах.
По условиям появления термоусталостных трещин опасными являются зоны роторов, расположенные около пазов для крепления лопаток, около разгрузочных («тепловых») канавок на поверхности вала в местах расположения лабиринтных уплотнений, зоны перехода от диска к валу в цельнокованых роторах (придисковые галтели), другие галтели на поверхности ротора.
Рассмотрим условия возникновения температурных деформаций и напряжений во фрагменте ротора, изображенного на рис. 14.54, при переходных режи-
3 |
1 |
2
IV III
|
II |
I |
|
h |
|
2 |
1 |
|
l |
m |
H |
|
|
|
|
|
|
|
IV |
III |
II |
I |
|
Рис. 14.54. Фрагмент РВД между регулирующей и второй
ступенями:
1 — диск регулирующей ступени; 2 — диафрагменные уплотне-
ния; 3 — диск второй ступени
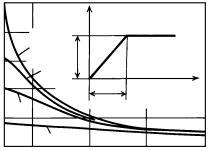
мах турбины в процессе пуска из неостывшего состояния, при стационарном режиме работы и остановке ее в резерв (на конец недели).
В процессе пуска в камеру регулирующей ступени поступает пар, температура которого отличается от температуры металла на поверхности ротора. В самом начале пуска нередко температура пара оказывается ниже температуры металла вследствие того, что пар, подаваемый через перепускные трубы от клапанов в сопловые коробки, охлаждается в них. Это обусловлено тем, что перепускные трубы охлаждаются в период простоя в конце недели значительнее, чем элементы ротора. Однако этот начальный период пуска, когда на ротор воздействует пар пониженной температуры, является кратковременным и неопределяющим. Поэтому примем, что при пуске температура подаваемого пара выше температуры металла ротора. Режимы пуска, нагружения и другие более подробно рассмотрены ниже (см. гл. 15).
Можно считать, что ротор в области, показанной на рис. 14.54, прогрет равномерно и температура металла его в области между сечениями I—I и IV— IV постоянная по всему объему.
При подаче пара в период пуска начнется прогрев ротора, при этом поверхностные слои прогреются достаточно быстро вследствие того, что коэффициент теплоотдачи от пара к поверхности ротора весьма велик в случае как перегретого пара, так и в особенности влажного пара (при пуске турбин АЭС). Прогрев периферийного слоя вызывает температурные деформации металла. Температурные деформации (относительные температурные удлинения) возникают в случае свободного расширения (удлинения) волокон, но волокна на поверхности ротора как в осевом, так и в окружном направлении не являются свободными, они стеснены смежными относительно холодными внутренними областями ротора.
Стесненность температурных удлинений на поверхности ротора обусловливают сжимающие (отрицательные) температурные напряжения и им
соответствующие силовые деформации Δε .
н
При прогреве цилиндрической части ротора температурные напряжения и соответствующие силовые деформации на его поверхности вначале возрастают (по абсолютному значению), в некоторый момент достигают максимума, затем уменьшаются, и при полном прогреве ротора, когда его температура по всему сечению выравнивается, они стремятся к нулю. Наибольший интерес представляют максимальные значения температурных напряжений и деформаций на поверхности ротора в процессе его прогрева.
Для случая прогрева сплошного (упругого) цилиндра получено аналитическое решение для температурных напряжений и деформаций, согласно которому на поверхности цилиндра значения осевых и окружных деформаций равны и для момента их максимума определяются зависимостью
Δε = –ΔεТ s, (14.96)
н
где
Т= αТ (Т – Т ) = αТ Т ; (14.97)
пм0
Т— максимальная температура пара в процессеΔε
п
прогрева; Т — температура металла ротора в
м0
начальный момент пуска; αТ — коэффициент
линейного расширения металла ротора; s — безразмерная силовая деформация в момент максимума (рис. 14.55).
Предположительный график изменения температуры пара в процессе пуска представлен на рис. 14.55, согласно которому подъем температуры
пара до момента τ производится по линейному
0
закону, а затем она остается постоянной. Безразмерное время τ определяется зависимостью
τ = λt ⁄ (r2 |
ρc) , |
(14.98) |
1 |
|
|
где t — время; λ — коэффициент теплопровод-
ности; r — радиус вала (ротора между сечениями
1
I—I и II—II или III—III и IV—IV); ρ — плотность материала; c — удельная теплоемкость материала.
Безразмерное время подъема температуры пара
τ |
= λt |
⁄ (r2 |
ρc) , |
(14.99) |
0 |
0 |
1 |
|
|
где t — время подъема температуры пара при пуске.
0
Как следует из графиков, данных на рис. 14.55, величина s определяется двумя безразмерными параметрами — критериями τ и a, причем τ находится
00
s |
|
T |
|
|
|
|
|
|
|
0,8 |
|
|
|
|
|
4 |
T |
|
|
0,6 |
|
|
|
|
|
|
3 |
|
|
0,4 |
|
|
%0 |
% |
0,2 |
2 |
|
|
|
|
|
|
|
|
|
|
1 |
|
|
0 |
0,2 |
0,6 |
1,0 |
%0 |
Рис. 14.55. Зависимости максимальной безразмерной сило-
вой деформации (безразмерного температурного напряже-
ния) при прогреве сплошного цилиндра от параметров a и τ
0
1 — a = 1; 2 — a = 5; 3 — a = 20; 4 — a = ∞
489
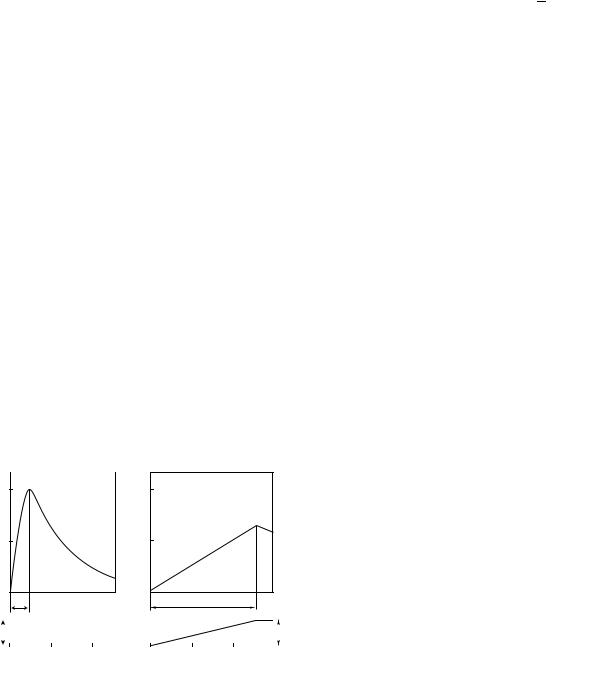
по (14.99), величина a — безразмерный коэффициент теплопередачи от пара к поверхности ротора (число Био) вычисляется по зависимости
αr
1 |
|
a = -------- , |
(14.100) |
λ
где α — коэффициент теплоотдачи ротора.
Согласно упомянутому решению максимальные в процессе прогрева температурные напряжения выражаются в виде
|
|
E |
|
σθ макс |
= σz макс |
= –------------ |
ΔεTs , (14.101) |
|
|
1 – |
μ |
где E — модуль упругости материала ротора; μ — коэффициент Пуассона.
Для примера на рис. 14.56 показаны изменения безразмерного температурного напряжения на поверхности цилиндра
|
|
σ |
(1 – μ) |
σθ = |
θ |
||
(14.102) |
|||
|
|
|
EΔεT |
в процессе пуска при двух условиях изменения температуры пара: а) при подаче в начальный момент пара с температурой, превышающей температуру поверхности на Т, температура пара в дальнейшем остается постоянной; б) при подаче в начальный момент пара с температурой, равной температуре поверхности ротора, в дальнейшем температура пара растет во времени по линейному закону, в момент τ = = 0,5 достигает максимального значения и затем остается постоянной. При этом коэффициент теплоотдачи (число Био а) во времени постоянный: a = 5. Этому значению числа Био по (14.100) для типичных
– |
|
– |
– |
|
– |
|
||
0,4 |
0,4 |
0,2 |
|
0,2 |
|
0 |
%1 |
0 |
%0 |
|
|
|
|
|
|
|
|
|
|
|
T |
|
|
|
|
|
|
|
|
|
T |
|
|
|
|
|
|
|
|
|
||
|
|
|
|
|
|
|
|
|
|
|
0 |
0,2 |
0,4 % |
0 |
0,2 |
0,4 |
% |
|
|||
|
|
а) |
|
|
|
|
б) |
|
|
|
Рис. 14.56. Изменения температурного напряжения на поверх-
ности цилиндра при a = 5:
а — прогрев при постоянной температуре пара; б — прогрев
при линейном (во времени) увеличении температуры пара
чисел r = 0,25 м, λ = 30 Вт/(мæК) соответствует α =
1
= 600 Вт/(м2 æК).
В случае а), как отмечено, температурные напря-
жения и деформации вначале растут, в момент τ = τ
1
достигают максимального значения – σ = s, затем
θ
снижаются и в пределе становятся равными нулю. В случае б) температурные напряжения и деформации растут, достигают максимума в момент τ = 0,5, затем начинают уменьшаться и в пределе стремятся к нулю.
На графиках (см. рис. 14.55) величина s определяет как максимальные силовые температурные деформации, рассчитываемые по (14.96), так и максимальные температурные напряжения, вычисляемые по (14.101).
Как отмечено, эти температурные деформации и напряжения возникают в процессе пуска турбины на поверхности гладкого цилиндра. В реальности на роторе имеются концентраторы напряжений, такие как, например, показанные на рис. 14.54 придисковые галтели в сечениях I—I и IV—IV и галтели в местах перехода от вала к зоне расположения лабиринтных уплотнений — сечения II—II и III—III.
Существенными источниками концентрации напряжений являются так называемые разгрузочные канавки в зонах концевых, средних, а в некоторых случаях и диафрагменных уплотнений. Эти разгрузочные канавки отчетливо видны на роторе ВД турбины Т-250/300-23,5 ТМЗ (см. рис. 11.7).
На рис. 14.57 показана схема участка вала с разгрузочными канавками. Назначение разгрузочных канавок состоит в том, чтобы уменьшить (или даже исключить) тепловой изгиб ротора в случае одностороннего задевания (например, вследствие недопустимой вибрации) гребней сегмента уплотнения о поверхность вала. Одностороннее (не по всей окружности) задевание вызывает односторонний
43
2
2
1
h |
|
|
l
r 1
Рис. 14.57. Схема участка вала с разгрузочными канавками:
1 — вал; 2 — разгрузочные канавки; 3 — сегмент уплотнения;
4 — обойма уплотнения; ρ — радиус скругления канавки
490