
паровые и газовые турбины для электростанций
.pdfроторов ВД и СД. В настоящее время в России имеется возможность производить поковки роторов диаметром более 2 м, поэтому технологических ограничений не существует.
Ступени газовых турбин вследствие больших
(Gv) не имеют жестких ограничений по высотам
г
лопаток, диаметры d ступеней газовых турбин
cр
ограничиваются практически только условиями прочности и могут быть выбраны и выбираются существенно большими (например, в 2 раза и более), чем диаметры первых ступеней паровых турбин.
Итак, малоступенчатость газовых турбин обусловлена, во-первых, меньшим общим их теплоперепадом, во-вторых, большими значениями оптимального теплоперепада ступени газовой турбины.
3. Экономичность ГТУ существенно зависит от КПД турбины η : изменение η на 1 % ведет к
т |
т |
изменению в ту же сторону КПД ГТУ на 2—3 % (см. § 12.3), а не на 1 %, как это происходит в паротурбинной установке, т.е. повышение экономичности газовой турбины дает относительно больший эффект, чем повышение КПД паровых турбин. Поэтому при проектировании газовой турбины применяются совершенные методы газодинамического расчета пространственного потока, позволяющие выбрать оптимальные формы и минимизировать аэродинамические потери в элементах проточной части — сопловых и рабочих решетках, входных и выходных патрубках. При создании газовых турбин широко используются испытания моделей — физическое моделирование элементов газодинамического тракта и системы охлаждения газовой турбины.
Для достижения высокой экономичности в газовых турбинах регулирующие клапаны в проточной части, регулирующие ступени, парциальный подвод среды не применяются. Для регулирования расхода газа используются иные, более совершенные (экономичные) способы (см. § 13.5).
Снижение потерь с выходной скоростью достигается установкой диффузора за последней ступенью газовой турбины, обычно используют диффузоры с осевым выходом и оптимальным углом раскрытия.
13.2. ОСНОВНЫЕ УЗЛЫ И УСТРОЙСТВО ГТУ
Рассмотрим устройство ГТУ на примере ГТЭ-160, производимой ЛМЗ по лицензии, приобретенной у «Сименс», и обозначаемой как SGT5-2000Е или V94.2 (табл. 13.1). В России эти ГТУ установлены в составе двух дубль-блоков ПГУ-450Т на СевероЗападной ТЭЦ Санкт-Петербурга и одного дубльблока на Калининградской ТЭЦ-2. Этими же ГТУ комплектуются ПГУ-450Т московских ТЭЦ-21 и ТЭЦ-27.
На рис. 13.1 показан продольный разрез ГТУ V94.2 с закрытой нижней частью.
Ротор ГТУ состоит из концевых частей и дисков компрессора и турбины, соединяемых хиртами (рис. 13.2) и центральным стяжным болтом 6. Цилиндрический проставок 11 позволяет разместить между компрессором ВК и турбиной ГТ выходной диффузор компрессора и входной патрубок подвода газа к соплам первой ступени газовой турбины (см. рис. 13.1).
Ротор ГТУ укладывается в два опорных подшипника 1 и 10 (см. рис. 13.1), которые с помощью силовых стоек крепятся соответственно к корпусу выходного диффузора и входному конфузору компрессора.
Корпус ГТУ состоит из следующих частей: корпуса компрессора с входным патрубком; средней силовой части 6; выходного патрубка 11. По бокам средней части 6 с помощью фланцев крепятся две камеры сгорания КС, одна из которых изображена на рис. 13.1. С правой стороны силовой части устанавливается одна обойма 8, в которую помещаются сопловые аппараты всех четырех ступеней газовой турбины.
К вертикальному фланцу левой стороны средней части крепится корпус части высокого давления компрессора. В этот корпус помещаются две обоймы 5 (см. рис. 13.1), в расточки которых устанавливаются направляющие лопатки компрессора. Пространство между обоймами и стенкой корпуса компрессора используется для организации сброса и отборов воздуха.
На входе в компрессор устанавливается входной направляющий аппарат 2 (см. рис. 13.1), лопатки которого синхронно поворачиваются кольцом, привод которого осуществляется тягой 17 и электродвигателем 18.
Силовой корпус ГТУ устанавливается на две пары опор 19 и 13. Опоры 19, расположенные по сторонам корпуса, неподвижны и поддерживают корпус в районе фланца горизонтального разъема. Опоры 13, основания которых также жестко закреплены в бетонной плите, включают в себя по три гибких стержня 12, на верхние части которых устанавливается внешний корпус ГТУ. При пусках стержни свободно изгибаются и не препятствуют тепловым расширениям корпуса ГТУ.
На рис. 13.3 показан ротор ГТУ, уложенный в нижнюю половину ее корпуса при сборке ГТУ на сборочном стенде. Хорошо видны выше упомянутые опоры 1 и 6, на которые опирается внешний корпус ГТУ, фланец 5 для присоединения камеры сгорания, рабочие лопатки компрессора 9 и турбины 7, полости 2 между обоймами корпуса компрессора.
401
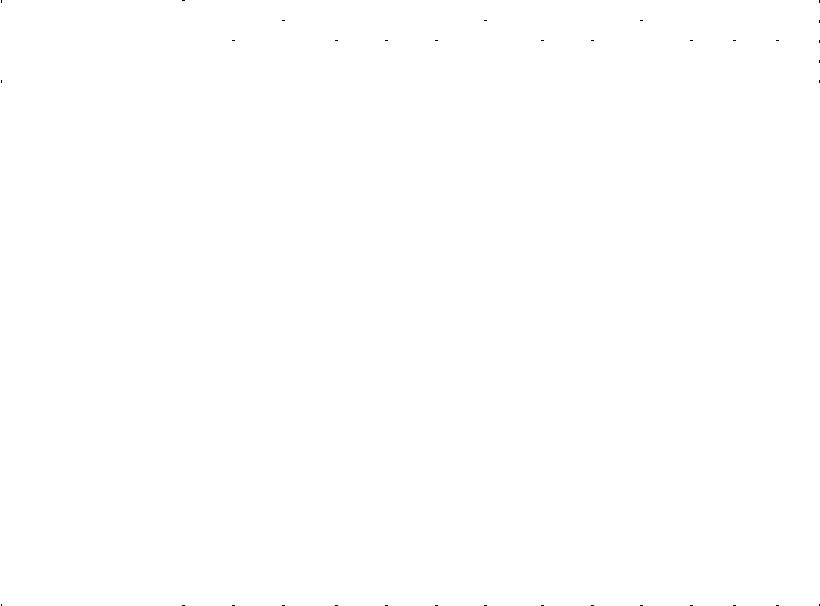
402
Та бл и ц а 13.1. Характеристики ГТУ и соответствующих им ПГУ-У мощностью более 70 МВт
|
|
|
|
|
Фирма-изготовитель (разработчик), тип ГТУ и год выпуска |
|
|
|
|
|||||||
|
|
|
|
|
|
|
|
|
|
|
|
|
|
|
|
|
|
«Альстом» |
|
«Дженерал Электрик» |
|
|
«Мицубиси» |
|
|
«Сименс» |
|
||||||
Показатель |
|
|
|
|
|
|
|
|
|
|
|
|
|
|
|
|
|
GT13E2 |
GT26 |
PG6101FA |
PG9171E |
PG923EC |
PG351FA |
MW701DA |
MW701F |
MW701G |
V64.3A |
V94.2 |
V94.2A |
V94.3A |
|||
|
|
|
|
|
|
|
|
|
|
|
|
|
|
|
|
|
|
1993 |
1994 |
1993 |
|
1987 |
1994 |
1996 |
1992 |
|
1997 |
|
1998 |
1996 |
1987 |
1997 |
1995 |
|
|
|
|
|
|
|
|
|
|
|
|
|
|
|
|
|
Мощность, МВт |
168,0 |
265 |
70,1 |
|
123,4 |
169,2 |
255,6 |
144,1 |
|
270,3 |
|
334,0 |
70,0 |
159,0 |
190,0 |
255,0 |
КПД, % |
35,7 |
38,5 |
34,2 |
|
33,8 |
34,9 |
36,9 |
34,8 |
|
38,2 |
|
39,5 |
36,5 |
34,5 |
36,4 |
38,5 |
Мощность пиковая, МВт |
176,9 |
— |
73,6 |
|
133,0 |
184,7 |
— |
— |
|
— |
|
— |
— |
167,0 |
— |
— |
Отношение давлений компрессора |
14,6 |
30,0 |
15,0 |
|
12,3 |
14,2 |
15,4 |
14,0 |
|
17,0 |
|
21,0 |
16,2 |
11,1 |
14,0 |
17,0 |
Расход воздуха, кг/с |
532,5 |
562,0 |
205,2 |
|
404,1 |
499,0 |
645,6 |
445,4 |
|
652,4 |
|
737,8 |
190,2 |
513,9 |
527,0 |
641,0 |
Частота вращения, мин–1 |
3000 |
3000 |
5254 |
|
3000 |
3000 |
3000 |
3000 |
|
3000 |
|
3000 |
5400 |
3000 |
3000 |
3000 |
Температура газов в турбине, °С: |
|
|
|
|
|
|
|
|
|
|
|
|
|
|
|
|
на входе |
1180 |
1290 |
1290 |
|
1124 |
1204 |
1290 |
1180 |
|
1350 |
|
1410 |
1315 |
1100 |
— |
1315 |
на выходе |
524 |
640 |
589 |
|
538 |
558 |
609 |
536 |
|
586 |
|
587 |
571 |
538 |
570 |
577 |
Возможная выработка теплоты, МВт |
237 |
300 |
105 |
|
186 |
240 |
345 |
204 |
|
328 |
|
360 |
94 |
237 |
260 |
313 |
Масса ГТУ, т |
330 |
335 |
— |
|
863 |
772 |
1090 |
200 |
|
340 |
|
420 |
ПО |
295 |
320 |
330 |
Габаритные размеры, м: |
|
|
|
|
|
|
|
|
|
|
|
|
|
|
|
|
длина |
10,8 |
12,3 |
36,6 |
|
35,1 |
41,2 |
34,2 |
12,5 |
|
17,3 |
|
18,2 |
11,0 |
14,0 |
12,0 |
12,5 |
ширина |
6,4 |
5,0 |
6,1 |
|
23,5 |
16,2 |
7,6 |
5,2 |
|
5,8 |
|
6,2 |
4,0 |
12,5 |
6,0 |
6,1 |
высота |
5,4 |
5,5 |
10,4 |
|
11,9 |
13,7 |
15,2 |
5,2 |
|
5,8 |
|
6,2 |
4,8 |
8,4 |
7,4 |
7,5 |
Мощность ПГУ с одной ГТУ, МВт |
168,0 |
396 |
107,4 |
|
189,2 |
259,3 |
390,8 |
21,5 |
|
399 |
|
484,4 |
101 |
238 |
285 |
380 |
КПД ПГУ с одной ГТУ, % |
49,7 |
58,5 |
53,2 |
|
52,0 |
54,0 |
56,7 |
51,4 |
|
56,9 |
|
58,0 |
53,7 |
52,1 |
56 |
58 |
Мощность, МВт: |
|
|
|
|
|
|
|
|
|
|
|
|
|
|
|
|
ГТУ |
— |
257 |
69,1 |
|
121,6 |
166,6 |
254,1 |
142,1 |
|
266,1 |
|
328,9 |
67,5 |
154 |
— |
— |
паровой турбины |
— |
140 |
40,1 |
|
70,4 |
96,6 |
141,8 |
70,4 |
|
132,9 |
|
155,5 |
32,0 |
88 |
— |
— |
Наибольшее число ГТУ |
3 |
2 |
2 |
|
2 |
2 |
2 |
3 |
|
2 |
|
2 |
2 |
2 |
2 |
2 |
Мощность ПГУ с ними, МВт |
727,5 |
750 |
218,7 |
|
383,7 |
522,6 |
786,9 |
642,3 |
|
804,7 |
|
972,1 |
203 |
478 |
558 |
760 |
КПД ПГУ с ними, % |
53,5 |
58,2 |
54,1 |
|
52,7 |
54,4 |
57,1 |
51,8 |
|
57,4 |
|
58,2 |
54,0 |
52,3 |
54,4 |
58 |
Мощность, МВт: |
|
|
|
|
|
|
|
|
|
|
|
|
|
|
|
|
всех ГТУ |
477,9 |
465,2 |
138,2 |
|
243,2 |
333,2 |
508,2 |
423,6 |
|
532,2 |
|
657,8 |
135 |
308 |
364 |
510 |
паровой турбины |
249,6 |
260 |
84,0 |
|
146,1 |
197,6 |
289,2 |
218,7 |
|
272,5 |
|
314,3 |
70 |
177 |
205 |
260 |
|
|
|
|
|
|
|
|
|
|
|
|
|
|
|
|
|
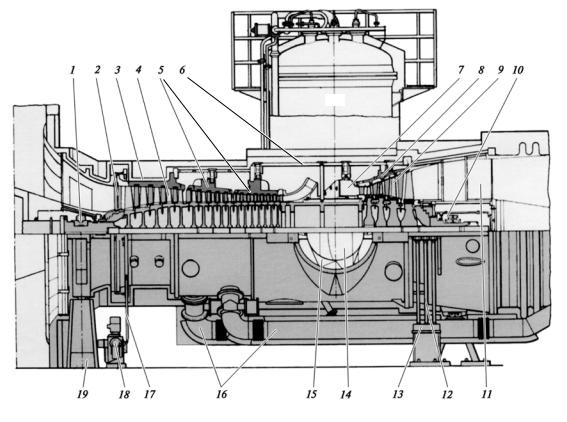
КС
ВК |
|
ГТ |
Рис. 13.1. Продольный разрез ГТУ V94.2:
1 — передний опорно-упорный подшипник ротора ГТУ; 2 — входной направляющий аппарат воздушного компрессора; 3 — передняя
часть корпуса компрессора; 4 — рабочие лопатки воздушного компрессора; 5 — обоймы направляющих аппаратов компрессора; 6 —
средняя силовая часть корпуса ГТУ; 7 — кольцевая полость подвода рабочих газов из камер сгорания к сопловому аппарату первой
ступени газовой турбины; 8 — обойма сопловых аппаратов газовой турбины; 9 — рабочие лопатки газовой турбины; 10 — опорный
подшипник ротора ГТУ; 11 — выходной патрубок ГТУ (диффузор); 12 — гибкие стойки (стержни), обеспечивающие свободное теп-
ловое расширение корпуса ГТУ; 13 — опора гибких стоек; 14 — кольцевая полость, в которой собираются рабочие газы, идущие из
камер сгорания; 15 — кольцевое пространство между пламенной трубой камеры сгорания и ее корпусом для прохода воздуха, иду-
щего от компрессора к горелочному устройству; 16 — обводные воздушные трубопроводы; 17 — тяга привода поворотного кольца,
обеспечивающего поворот лопаток входного направляющего аппарата компрессора; 18 — приводной электродвигатель с редуктором;
19 — передняя (неподвижная) опора ГТУ; ВК — воздушный компрессор; КС — камера сгорания; ГТ — газовая турбина
403
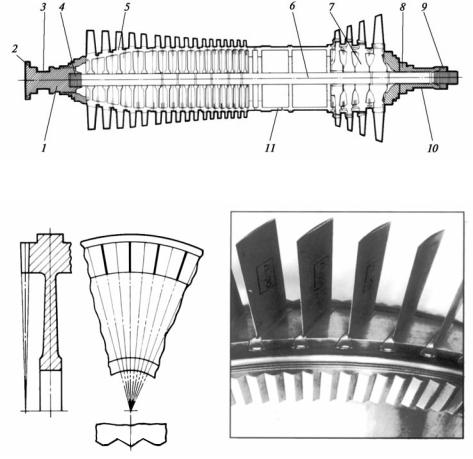
a)
б ) |
в) |
Рис. 13.2. Ротор ГТУ фирмы «Сименс»:
а — общий вид ротора; б — профиль зубьев хиртового соединения; в — диск ротора компрессора с зубьями хиртового соединения;
1 — левая концевая часть ротора; 2 — полумуфта для присоединения проставки, идущей к электрогенератору; 3 — шейка вала
опорно-упорного подшипника; 4 — резьбовое соединение; 5 — облопаченный диск компрессора; 6 — стяжной стержень; 7 — обло-
паченный диск турбины; 8 — правая концевая часть ротора; 9 — гайка; 10 — шейка вала опорного подшипника; 11 — проставочная
часть
404
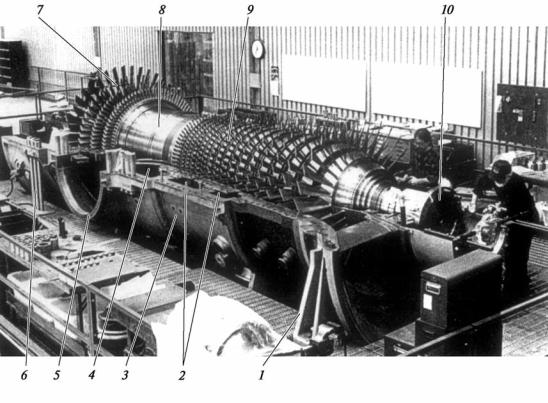
Рис. 13.3. Ротор ГТУ 94.2, уложенный в нижнюю половину корпуса ГТУ:
1 — неподвижная опора корпуса ГТУ; 2 — кольцевые полости между обоймами компрессора; 3 — корпус компрессора; 4 — полость
сбора воздуха после компрессора перед его подачей в камеры сгорания и на охлаждение статорных элементов газовой турбины; 5 —
фланец для присоединения камеры сгорания; 6 — гибкие стойки; 7 — лопатки газовой турбины; 8 — кольцевой элемент, соединя-
ющий роторы компрессора и турбины; 9 — рабочие лопатки компрессора; 10 — фланец присоединения вала-проставки, идущего к
электрогенератору
Газотурбинная установка имеет две камеры сго- |
ная труба выполнена из инконеля — сплава на |
рания, расположенные симметрично относительно |
основе никеля с высоким содержанием хрома. В ее |
оси ГТУ. Разрез по камерам сгорания показан на |
нижней части имеются специальные окна (не пока- |
рис. 13.4. Воздух из выходного патрубка компрес- |
занные на рис. 13.4), через которые подводится вто- |
сора поступает в кольцевое пространство 9 и из |
ричный воздух. Его смешение с продуктами сгора- |
него расходится на две камеры сгорания; затем он |
ния и тщательное перемешивание в переходных |
проходит по кольцевому пространству 1 между кор- |
элементах 15 обеспечивают перед сопловым аппа- |
пусом камеры 2 и пламенной трубой 3 или переход- |
ратом первой ступени газовой турбины температуру |
ными элементами 15. |
газов 1100 °С. Температура за соплами первой сту- |
|
пени при стандартных условиях на входе в комп- |
Пройдя в зазоре между корпусом и пламенной |
|
|
рессор составляет 1050 °С. |
трубой и охладив ее, воздух поступает к восьми |
|
горелочным модулям, к которым подается топливо |
На рис. 13.5 приведена схема горелочного |
(основное топливо — природный газ, резервное — |
модуля, представляющего собой комбинацию трех |
жидкое). Горение происходит на коротком участке |
горелок, т.е. устройств, предназначенных для сжи- |
пламенной трубы, где температура составляет при- |
гания газа, и одной форсунки, служащей для сжига- |
мерно 1450 °С. Относительно низкая температура |
ния жидкого топлива. Такой горелочный модуль |
горения сдерживает образование вредных оксидов |
называется комбинированным. При мощности ГТУ |
азота. Изнутри пламенная труба покрыта термо- |
более 50 % номинальной используется так называе- |
стойкими керамическими плитками, защищающими |
мая горелка с предварительным смешением. Топ- |
ее от действия высокой температуры. Сама пламен- |
ливный газ подается в коллектор 1, а из него — |
405
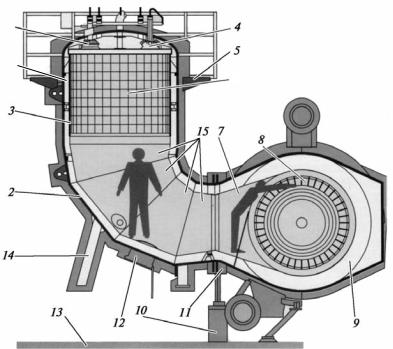
4
1
6
Рис. 13.4. Сочленение камеры сгорания и газовпускной части газовой турбины (правая камера сгорания не показана):
1 — пространство для прохода воздуха от компрессора к горелкам; 2 — корпус камеры сгорания; 3 — пламенная труба; 4 — горе-
лочный модуль; 5 — площадка обслуживания горелок и топливоподающих устройств; 6 — керамические плитки, облицовывающие
внутреннюю поверхность пламенной трубы; 7 — переходной патрубок от камеры сгорания к сопловому аппарату первой ступени
турбины; 8 — сопловые лопатки первой ступени турбины; 9 — сборная выходная камера воздушного компрессора; 10 — дополни-
тельная опора; 11 — фланец присоединения камеры сгорания к корпусу газовой турбины; 12 — люк для прохода обслуживающего
персонала внутрь камеры сгорания; 13 — пол машинного зала ГТУ; 14 — вспомогательная (монтажная) опора камеры сгорания;
15 — переходные элементы от пламенной трубы к переходному патрубку
к многочисленным перфорированным трубкам 6. В кольцевое пространство между трубками подается воздух. Решетка 10 турбулизирует поток, и в результате на выходе из горелки создается однородная смесь топлива и воздуха. Эта смесь поджигается постоянно горящей пилотной («дежурной») горелкой (см. ниже). Горение такой смеси происходит по законам кинетики химических реакций, поэтому его называют кинетическим. Оно происходит сразу во всем объеме и на коротком участке пламенной трубы. Главная особенность горения топлива с предварительным смешением — образование малого количества оксидов азота и монооксида углерода.
Однако горелки с предварительным смешением имеют и недостаток: при малых нагрузках, т.е. при малых расходах топливного газа по отношению к поступающему воздуху (напомним, что так как компрессор имеет постоянную частоту вращения, то расход воздуха можно уменьшить сравнительно
мало только с помощью входного направляющего аппарата компрессора), горение становится неустойчивым. Поэтому горелочный модуль снабжают диффузионной горелкой (без предварительного смешения), работающей при малых нагрузках, в частности при пуске и наборе начальной нагрузки. Через кольцевую полость 3 подается горючий газ, который не успевает полностью смешаться с потоком воздуха VI, а само горение происходит на выходе из горелки в факеле по мере перемешивания топлива и воздуха. Такое горение определяется скоростью диффузии, т.е. механического проникновения топлива в воздух. Поэтому его называют диффузионным, а саму горелку — диффузионной. Горелку, сочетающую в себе горелки с предварительным смешением и диффузионную, часто называют гибридной. Диффузионное горение более устойчиво, чем кинетическое, но характеризуется высоким уровнем вредных выбросов.
Наконец, третья горелка — это пилотная диффузионная горелка, к которой газ подается
406
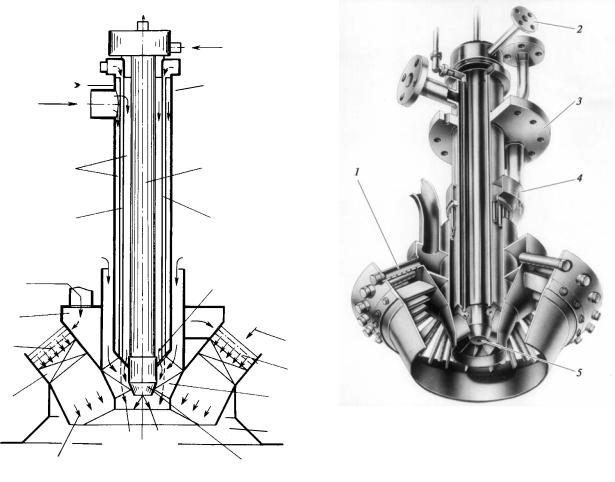
|
|
|
|
X |
|
|
|
|
|
|
IX |
|
VIII |
|
|
|
4 |
|
|
|
|
|
|
V |
|
|
|
||
|
|
|
|
||
|
|
3 |
|
|
5 |
|
|
2 |
|
|
2 |
|
|
|
VI |
|
VI |
I |
|
|
|
XII |
|
|
|
|
|
|
|
1 |
|
|
|
|
|
II |
|
|
|
III |
|
|
|
|
|
|
6 |
10 |
|
|
|
|
7 |
|
|
|
|
|
|
|
|
|
|
|
8 |
|
|
|
VII |
XI |
|
|
IV |
|
Область горения |
9 |
Рис. 13.5. Схема горелочного модуля камеры сгорания:
1 — камера подачи природного газа к основной горелке с пред-
варительным смешением; 2 — трубки подачи природного газа к
пилотной горелке; 3 — кольцевые полости подачи природного
газа к диффузионной горелке; 4 — кольцевая камера подачи при-
родного газа к трубкам, питающим пилотную горелку; 5 —
полый стержень подвода жидкого топлива к форсунке и отвода
его избытка; 6 — полые перфорированные трубки для подачи
газа в зону предварительного смешения; 7 — аксиальные
лопатки; 8 — цилиндрический воротник корпуса камеры сгора-
ния для установки горелочного модуля; 9 — центробежная фор-
сунка; 10 — решетка, обеспечивающая смешение топлива и воз-
духа; I — подача природного газа в камеру раздачи газа к
перфорированным трубкам; II — выход природного газа из тру-
бок; III — подача воздуха для предварительного смешения с топ-
ливом; IV — смесь, готовая к сжиганию; V — подача природного
газа к диффузионной горелке; VI — подача воздуха к диффузи-
онной горелке; VII — выход природного газа из пилотной диф-
фузионной горелки; VIII — топливный газ к пилотной горелке;
IX — жидкое топливо к форсунке; X — отвод избытка жидкого
топлива из форсунки; XI — конус распыливания жидкого топ-
лива; XII — выход основного природного газа из диффузионной
горелки
Рис. 13.6. Внешний вид горелочного модуля камеры сгорания:
1 — перфорированные трубки для подачи газа в зону смеше-
ния с воздухом; 2 — фланец трубопровода подачи жидкого топ-
лива; 3 — фланец крепления горелочного модуля к крышке
пламенной трубы; 4 — коллектор подачи пара (или воды) для
«экологического» впрыска; 5 — форсунка жидкого топлива
по нескольким трубкам 2. Она горит постоянно при работе и горелок с предварительным смешением, и диффузионных.
При работе на жидком топливе используется центробежная форсунка 9. С ее помощью на выходе создается коническая закрученная струя топлива, которая распадается на мелкие капли, смешивается с воздухом и обеспечивает диффузионное горение. К форсунке жидкое топливо подается в постоянном количестве (поток IX), а отводится в разном (поток X). Увеличивая обратный поток, изменяют расход топлива в зону горения.
На рис. l3.6 показана конструкция горелочного модуля. Его закрепляют с помощью фланца 3 на корпусе камеры сгорания. Нижней конической поверхностью модуль свободно входит в отверстия верхней части камеры сгорания. Пользуясь рис. 13.5, легко уяснить назначение отдельных эле-
407
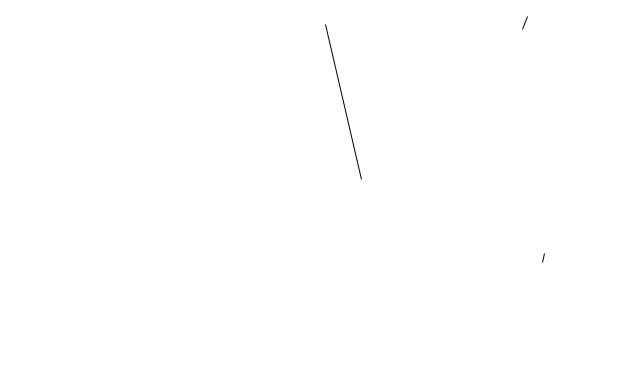
12
Воздух
Воздух от последней ступени компрессора
Газы
3 |
4 5 6 |
a 7 8 |
9 |
|
10 |
11 |
12 |
|
a |
a |
|||||||
|
|
|
|
|
|
б |
|
|
б |
663,95 |
|
б |
|
|
|
|
|
|
175 |
|
|
|
a |
a |
a |
a |
|
|||
1720¾ |
|
|
a |
|
|
|
Воздух от 12-й ступени компрессора
19 18 |
17 |
16 |
15 |
14 |
13 |
Рис. 13.7. Устройство газовой турбины и система ее охлаждения:
1 — выходной патрубок воздушного компрессора; 2 — средняя часть корпуса ГТУ; 3 — газосборник; 4, 6, 8 — охлаждаемые сопловые
аппараты соответственно первой—третьей ступеней; 5, 7 — охлаждаемые рабочие лопатки; 9, 12 — неохлаждаемые рабочие лопатки;
10 — обойма сопловых аппаратов газовой турбины; 11 — неохлаждаемый сопловой аппарат; 13, 14, 16, 17 — диски соответственно
четвертой—первой ступеней; 15 — стяжной болт; 18 — цилиндрическая перегородка, отделяющая воздух, идущий на охлаждение из
двенадцатой и последней ступеней компрессора; 19 — цилиндрический соединительный элемент дисков последней ступени компрес-
сора и первой ступени газовой турбины; а — каналы охлаждающего воздуха; б — кольцевые полости для охлаждающего воздуха
сопловых лопаток
ментов горелочного модуля, представленного на рис. 13.6. Дополнительно на нем показан коллектор 4 подачи пара или воды для так называемого экологического впрыска, предназначенного для подавления оксидов азота при работе на жидком топливе. При этом вместе с подавлением оксидов азота происходит и снижение экономичности.
Устройство газовой турбины и система ее охлаждения представлены на рис. 13.7. Турбина состоит из четырех ступеней.
Сопловые лопатки турбины 4, 6, 8 и 11 выполнены заодно с бандажными полками, с помощью которых они закрепляются в обойме 10, которая, в свою очередь, устанавливается в средней части 2 корпуса ГТУ (см. поз. 6 на рис. 13.1).
Рабочие лопатки 5, 7, 9 и 12 с помощью хвостовиков крепятся на дисках 17, 16, 14 и 13 соответственно. Мощность с диска на диск передается
посредством хиртовых соединений и стяжного болта 15, а с ротора газовой турбины на ротор компрессора и далее на ротор электрогенератора — посредством цилиндрического соединительного элемента 19.
Газы из пламенных труб двух камер сгорания поступают в газосборник 3 и из него — в газовую турбину. Перед газовой турбиной, как указывалось выше, температура газов составляет 1100 °С. После расширения газов в турбине их температура в диапазоне нагрузок 50—100 % должна поддерживаться постоянной и составлять 535 °С. Это обеспечивает надежную и экономичную работу паросиловой установки ПГУ.
В газовой турбине охлаждаются первые пять из восьми венцов. Охлаждение сопловых аппаратов осуществляется воздухом из кольцевых полостей б, в которые он поступает из выходного диффузора 1
408
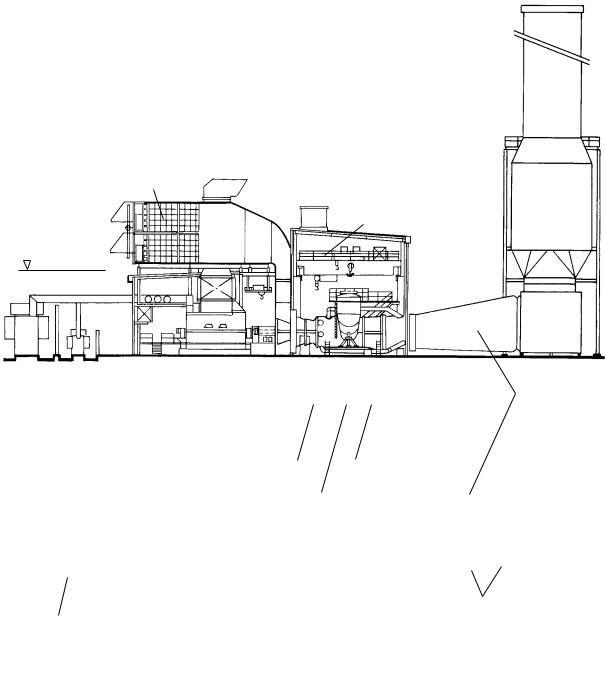
1
2
Около 11 м
4 |
5 |
6 |
8 |
3
7
Около 28 м
9
11
10
Около 70 м
Рис. 13.8. Установка газотурбинного агрегата V94.2 в машинном зале:
1 — КВОУ; 2 — кран для монтажа и обслуживания ГТУ; 3 — электрогенератор; 4 — шахта подачи воздуха к компрессору; 5 —
компрессор; 6 — камера сгорания; 7 — газовая турбина; 8 — переходной диффузор; 9 — маслоохладитель; 10 — щит управле-
ния; 11 — трансформатор
409
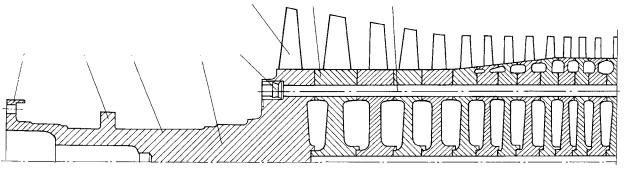
компрессора через каналы а в обойме. Охлаждающий воздух из полостей б направляется внутрь сопловых лопаток и охлаждает их за счет конвекции. Нагретый воздух сбрасывается в проточную часть турбины.
Поступление воздуха в полости б одновременно обеспечивает низкую и равномерную температуру обоймы.
Для охлаждения рабочих лопаток первой ступени используется воздух, отбираемый после последней ступени компрессора. Воздух поступает в кольцевую полость между цилиндрическими перегородкой 18 и элементом 19, а из нее — в каналы а в диске, снабжающие воздухом каждую из рабочих лопаток. Воздух входит в каждую лопатку через отверстия в хвостовике, охлаждает ее и выходит в проточную часть газовой турбины.
Для охлаждения рабочих лопаток второй ступени турбины используется воздух от двенадцатой ступени компрессора, который поступает в кольцевую полость между цилиндрической перегородкой 18 и стяжным центральным болтом 15.
Профильные части рабочих лопаток третьей и четвертой ступеней не охлаждаются, однако охлаждающий воздух из двенадцатой ступени направляется также в пространство между дисками 16 и 14, а также 14 и 13, откуда по каналам а подается к монтажным зазорам в хвостовиках.
Сборка ГТУ производится на турбинном заводе после изготовления в его цехах отдельных деталей и узлов. В отличие от паровой турбины после сборки на заводе ГТУ испытаний не проходит. В результате с турбинного завода на монтажную пло-
щадку ТЭС доставляет несколько отдельно транспортируемых сборочных единиц:
турбогруппа (компрессор и турбина); две камеры сгорания;
маслобак с установленным на нем оборудованием; входной патрубок компрессора; выходной диффузор.
В отличие от паровой турбины ГТУ размещают на ТЭС не на рамном фундаменте, а непосредственно на бетонном основании, установленном на нулевой отметке машинного зала (рис. 13.8). Входную шахту 4 компрессора посредством воздушного короба соединяют с комплектным воздухоочищающим устройством (КВОУ) 1, где происходит тщательная фильтрация воздуха, исключающая износ проточной части компрессора, забивание охлаждающих каналов в рабочих лопатках и другие неприятности. В целях экономии площади КВОУ размещают на крыше здания. К выходному концу вала компрессора присоединяется ротор электрогенератора 3, а к выходному диффузору ГТУ — переходной диффузор, направляющий газы в дымовую трубу или котелутилизатор.
13.3.КОНСТРУКЦИИ ОСНОВНЫХ УЗЛОВ
ИДЕТАЛЕЙ ГТУ
Роторы. Роторы мощных энергетических ГТУ в подавляющем большинстве выполняют сборными из отдельных дисков и концевых частей. На дисках располагают рабочие лопатки компрессора и газовой турбины, а на концевых частях — шейки опорных подшипников и диск упорного подшипника. Пример конструкции такого ротора приведен выше (см. рис. 13.2).
6 |
7 |
8 |
1 |
2 |
3 |
4 |
5 |
Рис. 13.9. Ротор ГТУ М89001FA фирмы «Дженерал Электрик»:
1 — полумуфта для присоединения ротора генератора; 2 — диск упорного подшипника; 3 — шейка вала компрессора под опорный
вкладыш передней опоры; 4 — передняя концевая часть ротора компрессора; 5 — гайка стяжного болта ротора компрессора; 6 —
рабочая лопатка первой ступени компрессора; 7 — диск второй ступени компрессора; 8 — окружной стяжной болт ротора ком-
прессора; 9 — рабочая лопатка последней ступени компрессора; 10 — концевое уплотнение компрессора; 11 — задняя концевая
часть ротора компрессора; 12 — стяжной болт полумуфт компрессора и турбины; 13 — передняя концевая часть ротора турбины;
410