
58-2020-chast_-2_08.07.2020
.pdf3.Цугленок Н.В., Манасян С.К., Дьяченко О.Г., Книга Ю.А. Подход к повышению эффективности комплексов послеуборочной обработки зерна // Вестн. КрасГАУ, 2009. № 4. С. 193-197.
4.Цугленок Н.В., Манасян С.К., Жуков М.А. Основные факторы и показатели для сравнительной характеристики зерносушилок // Вестн. КрасГАУ, 2010. № 5. С. 114–119.
5.Перекопский А.Н., Могильницкий В.М. Развитие механизации послеуборочной обработки зерна в Северо-Западном регионе России // Механиз. и электриф. сельского хоз-ва. 2012. №3. С. 9.
6.Цугленок Н.В., Манасян С.К., Пиляева О.В., Книга Ю.А., Полубояринов Н.А. Математическое моделирование процесса воздухораспределения в приемно-сушильно-вентиляционных устройствах бункерного типа // Вестн. КрасГАУ, 2009. № 10. С. 116–124.
7.Цугленок Н.В., Манасян С.К., Демский Н.В. Зерносушилки сельскохозяйственного назначения; Краснояр. гос. аграр. ун-т. — Красноярск, 2008. 100 с.
8.Купреенко А.И. Технология энергосберегающей сушки зерна на основе гелиосушильных
установок. – Брянск: БГСХА, 2013. 97 с. 9. Цугленок Н.В., Манасян С.К., Манасян Г.С., Куликов Н.Н. Обоснование автоматизированной системы многосвязного управления процессом сушки зерна // Вестн. КрасГАУ. 2010. № 10. С. 160-165.
10.Галкин А.Д., Галкин В.Д. Машины и оборудование послеуборочной обработки зерна и подготовки семян из влажного комбайнового вороха: рекомендации. - Пермь, 2020. 47 с.
11.Малин Н.И. Энергосберегающая сушка зерна: учебное пособие. – Москва : КолосС, 2004. 240 с.
УДК 669.162.2
Р.Р. Имайкин, Г.А. Мережников – студенты; А.М. Кашфуллин – научный руководитель, доцент, ФГБОУ ВО Пермский ГАТУ, г. Пермь, Россия
АНАЛИЗ СПОСОБОВ ПЕРЕРАБОТКИ ПРОДУКТОВ ДОМЕННОГО ПРОИЗВОДСТВА НА ПРИМЕРЕ КОЛОШНИКОВОГО ГАЗА
Аннотация. Исследованы вредные вещества от доменного производства. Представлен состав колошникового газа, а также как газ образуется во время доменного производства. Представлены схемы очистки колошникового газа.
Ключевые слова: доменная печь, колошниковый газ.
На сегодняшний день во многих городах России, имеется проблема загрязнения окружающей среды. Очень большое влияние на экологию играет доменное производство, а именно его отходы в виде различных газов и шлака. В данной статье, представлены одни из факторов.
Колошниковый газ – отходы в виде газа, образующиеся во время выплавки чугуна в доменных печах. Продукт неполного сгорания углерода и других химических реакций. Химический состав доменного газа может колебаться в широких пределах.
|
|
Таблица |
|
Состав колошникового газа, % |
|
Наименование |
Плавка на каменноугольном коксе |
Плавка на древесном угле |
|
|
|
Углекислый газ CO2 |
4–16 |
9–15 |
Окись углерода CO |
34-25 |
29–25 |
Метан CH4 |
0–0,4 |
1–2 |
Водород H2 |
1–3 |
4–10 |
Азот N2 |
56–59 |
50–54 |
|
161 |
|
Теплота сгорания доменного газа приблизительно 3,6–4,6 МДж/м3 (850– 1100 ккал/м3). При обогащении дутья кислородом содержание азота в газе снижается и соответственно этому возрастает количество других газов (в том числе окислы углерода и водорода), а также теплота сгорания.
Первые анализы доменного газа были сделаны Бунзеном в 1839 году на заводе Фекерхаген [2].
Первые попытки использования доменного газа как топлива на металлургических заводах были проведены французом Фабер дю Фором в 1832 году [2].
В1886 году Ф. Люрман предложил использовать доменный газ для газовых двигателей на воздуходувных станциях. В 1889 году на бельгийском заводе «Серен» была введена в строй первая доменная газовоздушная машина [1].
Сегодня используется на металлургических заводах как топливо в воздухонагревателях, коксовых и мартеновских печах (в смеси с коксовым газом), газовых двигателях, в паровых котлах.
Колошниковый газ токсичен, поэтому требует утилизации.
Влажность доменного газа составляет 3–4 %. Газ такого состава покидает доменную печь с температурой 200–350°С через газоотводы на колошнике доменной печи и называется колошниковый. Он проходит газоочистку и используется в качестве газообразного топлива.
Вдоменной печи газ выполняет функции восстановителя, теплоносителя и науглероживателя железа. Компоненты доменного газа СО и Н2 восстанавливают оксиды железа. Горновой газ покидает зону горения с температурой 2000°С. Поднимаясь вверх в доменной печи он отдаёт тепло двигающемуся навстречу потоку шихты и постепенно остывает. Доменная шихта и продукты плавки, напротив, нагревается до 1450–1500 °С. При температурах ниже 700°С в доменном газе происходит образование сажистого углерода:
2 = 2 + САЖ
Осаждаясь на поверхности свежевосстановленного железа, углерод взаимодействует с ним. В результате содержание углерода в губчатом железе достигает 1,5–2 %, а температура плавления снижается до 1300°С [2].
Колошниковый газ, содержащий до 35 % горючих компонентов и 50–60 г/м3 пыли при работе печи с повышенным давлением на колошнике (и 15–20 г/ м3. – с нормальным давлением), должен быть очищен от пыли перед его отправкой потребителям – на коксовые батареи, на горелки доменных воздухонагревателей и др. – до достижения концентрации пыли не выше 10 мг/ м3. Для очистки газа до столь низких концентраций пыли на металлургических заводах применяют многоступенчатые комбинированные схемы [4].
Как правило, первоначально очистку колошникового газа проводят в сухих пылеуловителях диаметром 5–8 м, в которых осаждаются частички пыли размером 50 мкм и более. В этих аппаратах улавливается 70–90 % пыли, содержащейся в доменном газе, благодаря воздействию сил гравитации и инерционных сил, возника-
162
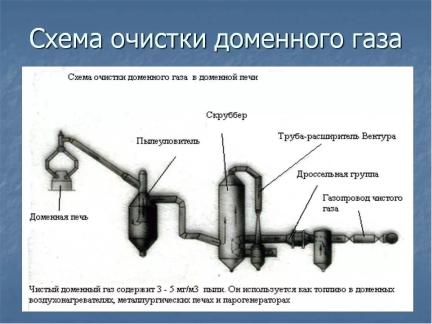
ющих при повороте газового потока на 180 градусов. Пыль из пылеуловителя удаляется при помощи винтового конвейера, смачиваемого водой. Остаточное содержание пыли в доменном газе после грубой очистки не превышает 3–10 г/м куб.
Для второй ступени очистки газа используют системы мокрой очистки. Обычно доменный газ из системы грубой сухой очистки поступает на полутонкую очистку газа, в которой выделяются частички размером 20 мкм и более и газ очищается до остаточного содержания пыли на выходе 0,6–1,6 г/м3. Полутонкую очистку осуществляют в аппаратах мокрого типа – форсуночных полых скрубберах и трубах Вентури.
Газы в доменных скрубберах имеют скорость 1–2 м/с при удельном расходе воды, составляющем 3–6 кг/ м3 газа. Проходящий через скруббер доменный газ охлаждается с 250–300 °С до 40–50 °С и полностью насыщается влагой. Степень очистки газа от пыли в скруббере не превышает 60–70 %.
После скруббера газ в большинстве случаев поступает в двечетыре низконапорные трубы Вентури, скорость газов в горловине которых равна 50–80 м/с при удельном расходе воды 0,2 кг/ м3. Здесь завершается полутонкая очистка газа.
Тонкую очистку колошникового газа, содержащего до 10 мг/м3 пыли, осуществляют в аппаратах 1 класса. В связи с широким внедрением на заводах черной металлургии газорасширительных станций, использующих потенциальную энергию давления доменного газа для выработки электроэнергии в газовых утилизационных бескомпрессорных турбинах (ГУБТ), для тонкой очистки газа обычно применяют аппараты, работающие с малой потерей давления, например мокрый электрофильтр.
Таким образом, в зависимости от наличия или отсутствия ГУБТ, на отечественных заводах обычно применяют две схемы очистки колошниковго газа:
Рисунок. Схема очистки колошникового газа
163
Выбор системы очистки колошникового газа зависит от требуемой степени его чистоты и экономических показателей пылеочистки.
При применении трубы Вентури расходуется около 600–800 кг воды и 10,8– 14,4 МДж электроэнергии на 1000 м3 газа.
За трубой Вентури устанавливают каплеуловитель-сепаратор, которым может быть мокрый циклон, скруббер или канальный сепаратор.
В электрофильтрах для промывки и охлаждения электродов расходуется 0,5–1,5 кг воды и 3,6–4,3 МДж электроэнергии на 1000 м3 газа.
Затраты на устройства для очистки от пыли и газов всех основных источников загрязнения атмосферы доменного цеха, т.е. газов, отводимых при загрузке кокса в бункеры и транспортировании и сортировке руды и кокса перед загрузкой в печь, отводе доменного газа и воды из очистных сооружений и отстойников, составляет примерно 15–20 % суммы всех капиталовложений цеха, включая и все соответствующие вспомогательные службы.
Объем капиталовложений зависит от мощности предприятия и его технической оснащенности. Некоторые устройства используют одновременно для нескольких пылегазоочистных агрегатов (газоходы, отстойники устройства для переработки шлама, вспомогательные агрегаты), благодаря чему объем капиталовложений снижается [4].
Эксплуатационные затраты на очистные сооружения доменного цеха зависят в основном от стоимости электроэнергии, водоснабжения и обслуживания [1].
Литература
1.Воскобойников В.Г., Кудрин В.А., Якушев A.M. Общая металлургия. 6 изд., переработанный и доп. - М., ИКЦ "Академкнига", 2002. 768 с.
2.Готлиб А.Д. Доменный процесс. 2 изд. М., "Металлургия", 1966.
3.Трушко В.Л., Утков В.А., Сивушов А.А. Улучшение экологии доменного производства за счет применения бокситовых красных шламов. Москва: Издательство «Интернет Инжиниринг», 2017. С. 63-65.
4.Корнилов Б.В., Чайка А.Л., Сохацкий А.А., Шостак В.Ю. Исследование влияния параметров колошникового газа и конструкции колошника на вынос пыли. Харьков: Издательство Государственное предприятие «Украинский научно-технический центр металлургической промышленности «Энергосталь»», 2014. С. 59-63.
УДК 631.36
И.В. Ковин, Е.С. Собянин – магистранты; В.Д. Галкин – научный руководитель, профессор, ФГБОУ ВО Пермский ГАТУ, г. Пермь, Россия
ОБЗОР КОНСТРУКЦИЙ АЭРОЖЕЛОБОВ
Аннотация. Целью исследований является выявление направлений совершенствования аэрожелобов. В статье проведен обзор конструкций аэрожелобов. Из обзора выяснено, что недостатками аэрожелобов являются снижение надежности транспортировки зернового вороха высокой влажности зерна, существенная не-
164
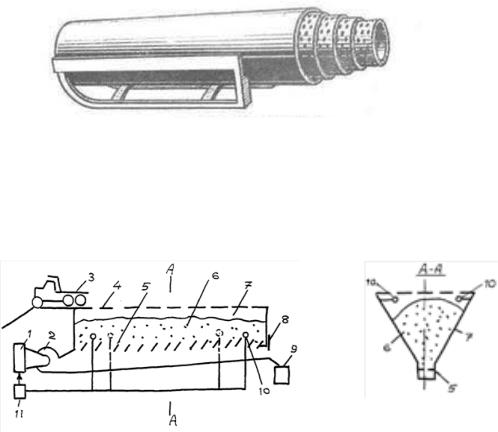
равномерность выгрузки зерна, находящегося на разных участках, высокая энергоемкость и выделение пыли при работе. Поэтому исследования следует направлять на повышение равномерности выгрузки зерна из аэрожелобов, снижение затрат энергии на их работу и обеспечение благоприятных условий обслуживающего персонала.
Ключевые слова. Аэрожелоба, недостатки, пути совершенствования.
Аэрожелоб – это вентиляционная установка, предназначенная для механизированной выгрузки, временного хранения и активного вентилирования зерна.
Рабочим элементом аэрожелоба является воздухораспределительная перегородка, которая делит канал на верхнюю часть – для транспортирования зерна и нижнюю – для подачи воздуха. Воздухораспределительная перегородка устанавливается под углом к горизонтали. Через нее снизу нагнетается воздух в зерновую массу.
Известны различные конструкции аэрожелобов [1,2,3].
Установка телескопическая вентиляционная ТВУ-2 (Рис.1) использу-
ется для вентилирования зерна в складах и на открытых площадках хлебоприемных предприятий, не оборудованных стационарными напольными вентиляционными установками. Она применяется с вентиляторами ВОЭ-5 мощностью 7,5 кВт.
Рисунок 1 – Установка телескопическая вентиляционная ТВУ-2 Известна установка в виде телескопического пневмотранспортера, предна-
значенного для вентилирования зерна при хранении и его выгрузки из хранилища. Она состоит из пяти звеньев, которые можно растягивать в рабочее положение на длину до 10 м. Внутри установки имеется трос, который одним концом закреплен за конец последнего звена, а другой заканчивается петлей для набрасывания на крюк тягового средства при необходимости совмещения звеньев.
1-калорифер, 2-вентилятор , 3-автомобиль, 4-площадка, 5-воздухораспределитель- ная решетка, 6-влажный зерновой ворох, 7-корпус аэрожелоба, 8- заслонка, 9- траспортертер, 10-датчики относительной влажности воздуха, 11-интегратор
Рис. 2. Схема аэрожелоба для вентилирования и сушки зерна и семян
165
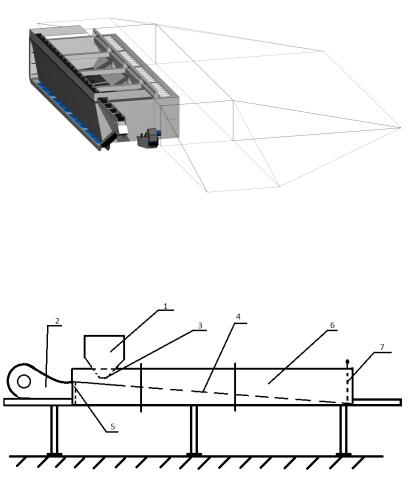
Учеными Всероссийского института механизации А.В. Голубковичем и С.А.Павловым [4] разработан способ вентилирования и сушки зерна наружным и подогретым воздухом с использованием аэрожелоба (Рис2).
Способ позволяет управлять процессом вентилирования и подсушки зерна, в зависимости от относительной влажности воздуха. Однако способ имеет и недостаки, такие как, неравномерность подачи зерна на последующую операцию, в зависимости от расположения материала на аэрожелобе, повышенный расход энергии на эту операцию, пылевыделение при выгрузке материала. Поэтому, исследования, направленные на устранение этих недостатков являются важными и актуальными.
Аэрируемый приемник (Рис.3) влажного зерна [5] разработан для приема и временного хранения влажного зернового вороха. Благодаря большой вместимости и возможности подачи воздуха, он рассчитан на прием зерна влажностью 24-40%, что позволяет исключить порчу зерна и бесперебойно подавать зерновой ворох на очистку и сушку. Однако эта конструкция не вполной мере устраняет основные недостатки аэрожелобов.
Рисунок 3. Аэрируемый приемник влажного зерна Для исследования процесса транспортирования зернового вороха на ка-
федре сельскохозяйственных машин и оборудования Пермского ГАТУ разработана и изготовлена установка.
Рисунок 4. Лабораторная установка 1 – загрузочный бункер, 2 – вентилятор, 3 – затвор, 4 – воздухораспредели-
тельная перегородка, 5 – задвижка, 6 – транспортный желоб сборной конструкции, 7 – задвижка
166
Установка позволяет изменять скорость воздушного потока, угол наклона рабочей поверхности, подачу зернового вороха различной влажности.
Вывод: Одним из эффективных устройств для транспортирования и вентилирования зерна являются аэрожелоба, преимуществом которых состоит в простоте и удобстве выгрузки зерна, отсутствие движущихся деталей и надежности конструкции.
Недостатками аэрожелобов являются снижение надежности транспортировки зернового вороха высокой влажности, существенная неравномерность выгрузки зерна, находящегося на разных участках, высокая энергоемкость и выделение пыли при работе. Поэтому исследования следует направлять на повышение равномерности выгрузки зерна из аэрожелобов, снижение затрат энергии на их работу и обеспечение благоприятных условий обслуживающего персонала.
Литература
1.Зимин Е.М. Рабочий процесс, параметры и режимы работы аэрожелобов для вентилирования и транспортирования влажного, засоренного вороха (теория, конструкция и расчет): автореферат диссертации на соискание ученой степени доктора технических наук / Зимин Евгений Михайлович. – Ленинград; Пушкин, 1990. 33 с.
2.Онхонова Л.О. Научные основы создания и применения универсальных аэрожелобов послеуборочной обработки семян и зерна. – М.: ВИМ, 2000. 250 с.
3.Онхонова Л.О. Аэрожелоб для временного хранения зернового вороха. – М.: Механизация и электрификация сельского хозяйства. 1999. №12. С. 22-23.
4.Патент РФ №23955047 Российская Федерация, МКП F26B3/06 (2010.07). Способ и устройство для сушки зерна и семян: заявлено:01.06.2009; опубл. 20.07.2010/А.В.Голубкович, С.А.Павлов.: заявительГосударственное научное учреждение Всероссийский научно-исследовательский институт механизации сельского хозяйства (ГНУ ВИМ Россельхозакадемии). 4с.
5.Галкин А.Д., Галкин В.Д. Машины и оборудование послеуборочной обработки зерна и подготовки семян из влажного комбайнового вороха: рекомендации. - Пермь, 2020. 47 с.
УДК 631.3:636
Б.Б. Коновалов – студент; Н.В. Трутнев – научный руководитель, доцент,
ФГБОУ ВО Пермский ГАТУ, г. Пермь, Россия
РОБОТИЗАЦИЯ УБОРКИ НАВОЗА ПРИ БЕСПРИВЯЗНОМ СОДЕРЖАНИИ КРУПНОГО РОГАТОГО СКОТА
Аннотация. Рассмотрены вопросы применения роботов для уборки навоза в коровниках со щелевыми полами при беспривязном содержании крупного рогатого скота, расчет производительности робота при обслуживании коровника на 240 голов, при расчете получены данные: время уборки всей территории, количество циклов уборки за суточный период (16 часов).
Ключевые слова: коровник, уборка навоза, щелевой пол, роботизация.
Автоматизированные устройства (роботы) для удаления навоза в коровниках со щелевыми полами позволяют исключить полностью ручной труд при выполнении этого трудоемкого производственного процесса. Роботизация уборки навоза имеет ряд достоинств:
167
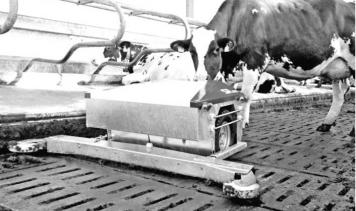
тщательная очистка трудоемких мест;
дистанционное управление с простым обслуживанием при помощи сенсорных датчиков;
беспрерывная работа в течении 16 часов и зарядка - 6 часов;
бесшумная и гуманная работа;
уменьшение количества персонала в коровниках.
Благодаря этому обеспечивается лучшее гигиеническое состояние животноводческого помещения, что является фундаментом чистоты и здоровья животных, а также снижает стоимость конечного продукта, за счет снижения количества ра-
ботников [1, 2, 3, 4].
Основной проблемой внедрения роботизированных систем уборки навоза является наличие решетчатых полов в коровниках, высокая стоимость установки и дорогое сервисное обслуживание.
Наиболее часто используемой системой, в настоящее время, является специализированный мобильный навозоуборочный робот SRone (Рис. 1).
Рис. 1. Навозоуборочный робот SRone
Робот SRone [5] бесшумен, а значит почти исключает беспокойство, стресс и дискомфорт у животных. Быстрая смена резиновых крыльев позволяет уменьшить затраты труда при техническом обслуживании.
Данный мобильный робот имеет стальной корпус, опирающийся на колеса с широкими резиновыми покрышками, которые обеспечивают устойчивость, маневренность и проходимость в труднодоступные места коровника. Движение происходит за счет электропривода, питающегося за счет энергоемких аккумуляторных батарей. На нижней передней части корпуса располагается скрепер, со встроенным предохранителем, который останавливает робота в случае возникновения препятствия на своем пути и он мгновенно меняет траекторию движения. С правой стороны корпуса располагается разъем для подключения робота к зарядному устройству [5].
Другой автоматизированной машиной для уборки навоза является робот JOZ-TECH [6] (Рис. 2). Конструкция этого робота имеет следующие отличия:
168

большой корпус, с интегрированым баком для воды и система опрыскивания, предотвращающая засыхание навоза;
используется не только для уборки в помещении, но и на выгульных площадках;
имеет подъемное устройство для скребка, которое позволяет преодолевать неровности;
роботу можно задать несколько программ, исполняемых в определенной последовательности[6].
Рис. 2. Мобильный робот для уборки навоза JOZ-TECH
Одним из роботов для уборки навоза и чистки полов, имеющих малые размеры, является Lely Discovery [7] (Рис. 3).
Рис. 3. Мобильный робот для уборки навоза Lely Discovery
Робот предназначен для всех видов щелевых полов, и кроме этого может применятся для закрытых полов шириной менее 5 метров. Основными достоинствами робота Lely Discovery являются:
малые размеры, что повышает проходимость и маневренность в помеще-
нии;
наличие пульта дистанционного управления, позволяющего прокладывать маршрут движения;
169
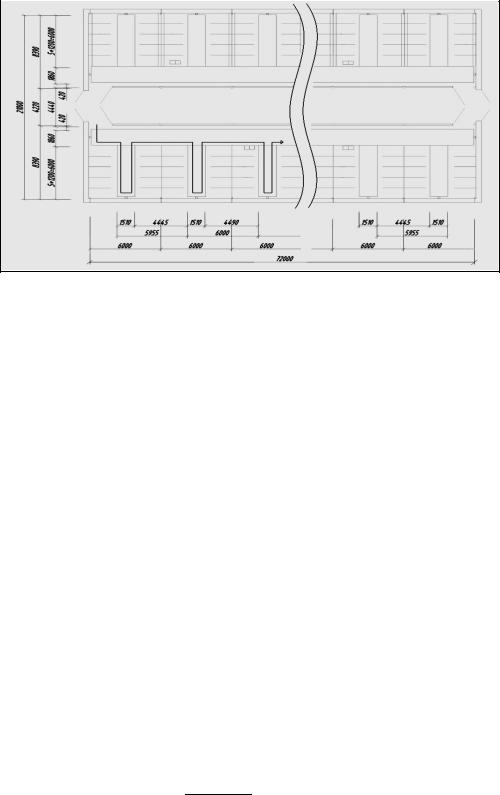
эргономичный дизайн и безопасность робота и животных за счет присутствия горизонтального кольца, имеющего ультразвуковой датчик, который следит за точностью перемещения [7];
На рис. 4 приведен план коровника с щелевыми полами.
Рис. 4. План коровника с щелевыми полами на 240 голов.
Параметры.
Площадь щелевого пола, которую будет очищать робот.
= осн. ∙ осн. ∙ осн.п. + бок. ∙ бок. ∙ бок.п. , мм2;
где – S - площадь щелевого пола, которую будет очищать робот;осн. – длина основного прохода, мм;бок. – длина бокового прохода, мм;
– ширина основного прохода, мм;
– ширина бокового прохода, мм;осн.п. – количество основных проходов, шт.;
– количество боковых проходов, шт.
S=72000·1860·2+6000·1510·24=485 280 000мм2=485,2м2
1.Время уборки всей территории.
2.t=S/V, минут;
3.где – t – время уборки всей территории, мин;
4.V – скорость передвижения робота, м/мин;
5.T=485,2/4=121,3 минут
6.Количество циклов уборки коровника.
ц = /t, циклов,
где - ц – количество циклов уборки помещения; T –время без подзарядки, мин;
960(16ч)
ц = 121,3 = 7,9 циклов.
170