
58-2020-chast_-2_08.07.2020
.pdfПриведенные на рисунках 1 и 2 схемы по своей конструкции аналогичны. Отметим основные достоинства и недостатки систем капельного полива растений.
Преимущества капельного полива растения в теплицах [2, 3, 6, 7, 8]:
1.Значительное снижение непродуктивных потерь воды, подаваемой на орошение (наблюдается существенная экономия водных ресурсов в результате меньших потерь на испарение, минимальной инфильтрации и отсутствия поверхностного стока).
2.Уменьшение засоренности полей в связи с высокой степенью очистки воды и локальным увлажнением (предварительная очистка воды исключает попадание семян сорной растительности с поливом, а локальное увлажнение предупреждает прорастание сорняков в неорошаемых междурядьях).
3.Пониженный расход удобрений (ввиду локальной подачах потребного количества).
4.Создание оптимальных условий по температурному режиму активного слоя почвы.
5.Наличия неувлажненной поверхности междурядий (обеспечивает создание необходимых условий для одновременного проведения агротехнических мероприятий).
6. Практически полное отсутствие зависимости капельного способа полива растений от внешних факторов.
7.Значительное снижение затрат энергии на подачу воды (системы работают при низком рабочем давлении от 0,5 до 0,2 ат.).
8.Капельный полив позволяет на 20-50% по сравнению с дождеванием и поверхностными способами полива повысить урожайность возделываемых культур.
Недостатки капельного полива растениий в теплицах [2, 3, 4, 7, 8]:
1.Возможность засорения и выведения из работы капельниц (из-за наличия в поливной воде взвешенных частиц, биологических и механических примесей,
втом числе и частиц плохо растворимых удобрений).
2.Большие первоначальные затраты на развертывание системы капельного орошения.
3.Ограниченные возможности регулирования микроклимата приземного слоя воздуха орошаемых площадей.
4.Вымывание лабильных питательных веществ из увлажняемого слоя почвы и возможность накопления избыточных запасов солей на границе контуров увлажнения.
5.Снижение парусной устойчивости растений садовых культур из-за формирования корневой системы в области стабильного увлажнения.
Вывод: Эффективность капельного способа полива обусловлена уникальностью возможностей данного способа: в первую очередь, непрерывностью подачи воды или водной смеси удобрений в необходимых количествах на протяжение всего онтогенеза растений, а во вторую, существенной экономией ресурсов и
151
уменьшением себестоимости производимой продукции. Проведенный анализ капельного способа полива позволяет говорить о нем как о перспективном, но не об универсальном способе полива растений. Вопрос по конкретной реализации данного способа в тех или иных хозяйствах требует дополнительной проработки.
Литература 1. Кавшин В.И. Научные основы адаптивного садоводства. - М.: Агропромиздат, 1995.
335 с.
2.Ионова З.М., Бойко С.И. Основные достижения в применении капельного орошения. - М., 1985. 66 с.
3.Григоров М.С. Внутрипочвенное орошение. -М.: Колос, 1983. 128 с.
4.Бурмистрова А.Ю. Регулирование водного режима почвы при капельном орошении плодовых питомников в нечерноземной зоне [Текст]: дис. …к.с.-х.н.: 03.02.13, 06.01.02. - М., 2013. 229 с.
5.Ахмедов А.Д., Темерев А.А., Галиуллина Е.Ю. Надежность систем капельного орошения // Известия нижневолжского агроуниверситетского комплекса: наука и профессиональное образование. 2010. №3 (19). С. 84–89.
6.Ахмедов А.Д., Ходяков Е.А., Боровой Е.П., Мазепа М.В. Техника и технология возделывания сельскохозяйственных культур при капельном и внутрипочвенном орошении: Монография. - Волгоград: ИПК ФГОУ ВПО ВГСХА «Нива», 2008. 228 с.
7.Рожнов С.И. Разработка технологии капельного орошения саженцев яблони в условиях Нижнего Поволжья [Текст]: дис. … к. с.-х. н.: 06.01.02. - М., 2004. 204 с.
8.Храбров М.Ю. Ресурсосберегающие технологии и технические средства орошения [Текст]: дис. … д. т. н.: 06.01.02. - М., 2008. 269 с.
УДК 631.347:635.64
К.Д. Дурновцев, Д.А. Тигин, М.Ю. Мясников, И.Л. Нечаев – студенты;
В.Д. Галкин – научный руководитель, профессор, ФБГОУ ВО Пермский ГАТУ, Пермь, Россия
ТЕНДЕНЦИИ СОВЕРШЕНСТВОВАНИЯ ЗЕРНОСУШИЛОК
Аннотация. Целью работы является выявление тенденций совершенствования зерносушилок. На основе обзора исследований основными направлениями совершенствования сушилок зерна и семян являются: обеспечение увеличенной подачи теплоносителя до 6000 м3/т*ч в плотный тонкий движущийся без затрат энергии слой зерна и системой рециркуляции теплоносителя; снабжение сушилок устройством ворошения зерна и отлежки; оснащение сушилок системами очистки высушенного зерна.
Ключевые слова: зерносушилки, тенденции совершенствования.
Процесс сушки состоит из взаимно связанных между собой тепло-физиче- ских явлений: передача тепла от агента сушки к материалу (нагрев зерна); испарение влаги с его поверхности; перемещение влаги к поверхности зерновок и испарение влаги с поверхности. Скорость испарения влаги при сушке зерна зависит от физико-химической структуры зерна и от формы связи влаги с зерном. Чем выше
152
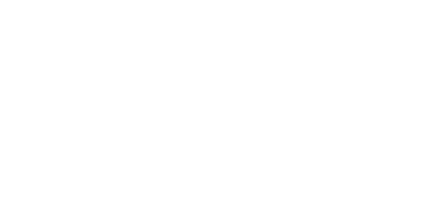
начальная влажность зерна, тем больше скорость сушки на начальном этапе. Затем скорость сушки становится постоянной, а при подсушке поверхности зерна она снижается.
Зерносушилки классифицируют по различным признакам. По принципу действия – прямоточные и противоточные (рециркуляционные). В прямоточных сушилках зерно проходит через сушильную шахту один раз при снижении влажности не более 6%. Зерно, влажностью более 20% пропускают через шахту сушилки 2 и белее раз. Для прямоточных сушилок партии зерна должны быть с одинаковой влажностью. В рециркуляционных сушилках подсушенное зерно смешивается с исходным зерном и возвращается в сушилку. Поэтому в этих сушилках можно высушить зерно с высокой влажностью без лишних затрат. По состоянию зернового слоя сушилки делятся – с плотным неподвижным, движущимся, псевдосжиженным и взвешенным слоем. Наибольшее распространение получили сушилки с гравитационным движущимся слоем зерна. По температуре теплоносителя сушильные установки различают –с подачей в зерно атмосферный воздух при относительной влажности 65%, подогретый теплоноситель и высокотемпературный.
По типу нагрева агента сушки – с прямым нагревом и с использованием теплообменника. По типу воздухораспределительных устройств – с воздухораспределительными коробами, с перфорированными стенками, с направляющими лопатками. По режиму работы – непрерывного и периодического действия. По конструкции сушилки непрерывного действия различают: шахтные, барабанные, камерные, карусельные, колонковые, бункерные, конвейерные, сушилки кипящего слоя и другие. Сушилки периодического действия делятся на: напольные, треугольные, ромбические и другие.
В регионах с повышенной влажностью зернового вороха, поступающего от
зерноуборочныхПроизводительностьпослеуборочнуюкомбайнов на сотовой шилкиобработкудобавляется, большое распрострапо |
- |
нение нашли колонковыепринципузерносушилки«улья(Рис» от.1)4. до 100 т/ч |
|
СоСС-2 |
СоСС-4 |
СоСС-6 |
СоСС-8 |
СоСС-12 |
4 пл.т/ч |
10 пл.т/ч |
15 пл.т/ч |
20 пл.т/ч |
30 пл.т/ч |
33
Рис.1 Колонковые зерносушилки сотового типа, выпускаемые ООО «Техноград»
Достоинствами сушилок являются: высокая скорость сушки, обеспечиваемая тонким (23 см) слоем движущегося зерна при подаче теплоносителя до 6000
153
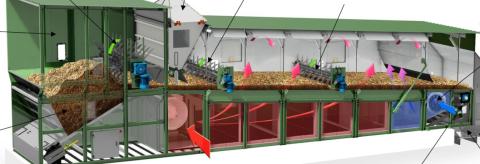
м3 на 1 т зерна в час или на 30 % больше, чем в шахтных сушилках с коробами; повышенная температура теплоносителя (70…75°С) при допустимой температуре нагрева зерна - 40-45°С; низкий расход топлива и электроэнергии в расчёте на 1т зерна за счет наличия зон отлежки, в которые теплоноситель не подаётся ( через каждые 2,0 м интенсивной сушки в «соте» зерно 0,8м движется по зоне отлёжки без подачи теплоносителя); рециркуляция теплоносителя (отработанный теплоноситель с влажностью менее 70% и температурой выше 38 - 40°С по сигналу датчиков автоматически перекидными заслонками направляется в топочное отделение, где вновь проходит через теплогенератор и далее в сушилку, а влажный и холодный отработанный теплоноситель выбрасывается в атмосферу); снижение мощности двигателей вентиляторов для подачи теплоносителя в тонкий слой зерна, по сравнению с шахтными сушилками. Колонковые зерносушилки позволяют: высушивать малую партию зерна (от 3т) независимо от её общей производительности; работать в параллельном (влажность зерна 20…24%) и последовательном (влажность зерна выше 24%) режимах; имеют возможность увеличения производительности сушилки за счёт увеличения количества сушильных сот; обеспечивает очистку высушенного зерна от лёгких примесей, включая щуплое зерно [1].
Конвейерные зерносушилки «Alvan Blanch» типа CD (Рис.2) позволяют удалять из зерна за один проход любой процент влаги.
Рис. 2. Схема рабочего процесса в сушилке «Alvan Blanch»
В отличие от колонковых зерносушилок, зерно перемещается цепочнопланчатым конвейером и в процессе движения сушится, обдуваясь теплоносителем, а затем охлаждается. Система рециркуляции тепла позволяет экономить, по данным производителя, до 30% энергии [3].
Зерносушилки фирмы «Petkus» DS [2] шахтного типа с автоматизированным процессом сушки, поставляются в трех типоразмерах (1500, 2500, 4000) с производительностью от 8 до 70 т/ч (при сушке пшеницы со снятием 4% влаги).
Воздух нагнетается осевыми вентиляторами в верхней части вытяжного воздушного канала. Конструкция разгрузочного устройства позволяет проводить
154
равномерную выгрузку зерна из всего пространства подсушильного бункера. Теплогенератор состоит из корпуса (камера сгорания), горелки с форсункой для жидкого топлива или газа и системы управления и автоматики.
Сушилка предусматривает как прямой нагрев воздуха, так его нагрев через теплообменник; имеет низкое потребление электроэнергии, благодаря применению коробов оптимальной формы и осевых вентиляторов; эффективную самоочистка шахты, благодаря пульсирующему выпуску зерна, при помощи разгрузочного устройства с пневматическим приводом. Теплогенератор располагается внутри кожуха сушилки.
Вывод. Основными направлениями совершенствования сушилок зерна и семян являются: обеспечение увеличенной подачи теплоносителя до 6000 м3/т*ч в плотный тонкий движущийся без затрат энергии слой зерна; системой рециркуляции теплоносителя; снабжение сушилок устройством ворошения зерна и отлежки; оснащать сушилки системами очистки высушенного зерна.
Литература 1.Галкин А.Д., Галкин В.Д. Машины и оборудование послеуборочной обработки зерна и
подготовки семян из влажного комбайнового вороха: рекомендации. - Пермь, 2020. 47 с.
2. Зерносушилка Petkus [В Интернете] // ТРИА Техника дя агробизнеса. - 2020 г. - https://tria-agro.ru/p/339265131-zernosushilka-petkus-nepreryvnogo-deystviya-tipa-dd/.
3.Сушилки конвейерного типа [В Интернете] // Альфа-Трейд Модернизация сельскохозяйственных предприятий. - 2017 г. - https://www.alfatreid.ru/catalog/konveyernye-sushilki/.
4. Зерносушилка Petkus [В Интернете] // ТРИА Техника дя агробизнеса. - 2020 г.. - https://tria-agro.ru/p/339265131-zernosushilka-petkus-nepreryvnogo-deystviya-tipa-dd/.
5.Сушилки конвейерного типа [В Интернете] // Альфа-Трейд Модернизация сельскохозяйственных предприятий. - 2017 г.. - https://www.alfatreid.ru/catalog/konveyernye-sushilki/.
УДК 631.374
Б.Г. Зедымышев, А.Н. Устюгов – магистранты; Н.В. Трутнев – научный руководитель, доцент, ФГБОУ ВО Пермский ГАТУ, г. Пермь, Россия
ОБЗОР КОНСТРУКЦИЙ МАТРИЦ ЭКСПЕРИМЕНТАЛЬНОГО ЗЕРНОВОГО ЭКСТРУДЕРА
Аннотация. Целью в данной статье является обзор конструкций матриц экструдера и их классификация. Приведена экструзионная лабораторная установка и описан ее рабочий процесс., разработаны направления ее совершенствования для выявления зависимости энергоемкости и подачи от конструктивных параметров матриц экструдера.
Ключевые слова: экструзия, зерновой экструдер, классификация матриц
Экструдирование кормов в последнее время все более широко применяется в современных технологиях производства кормов. При экструдировании, зерно
155
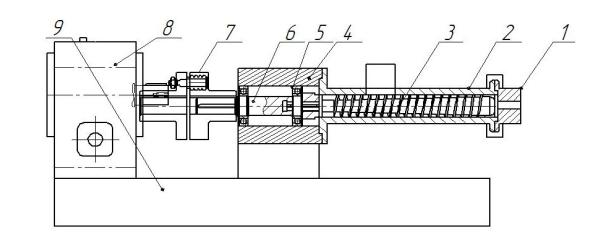
находится под воздействием давления так же температуры и сдвиговых деформаций. В результате происходят глубокие биохимические превращения питательных веществ: разрушение структуры крахмала зерна до глюкозы, изменение структуры клетчатки, происходит стерилизация корма, улучшаются вкусовые качества, а так же нейтрализуются антипитательные вещества. Корма полученные таким способом, усваиваются лучше и способствуют повышенной переваримости питательных веществ организмом КРС, птиц и других животных.
Процесс переработки продуктов путем размягчения или пластификации и придания им формы при продавливании через отверстия специальной матрицы называется экструзией [2].
Изменения, в экструдируемом сырье, зависят от режимов работы и конструктивных параметров экструдера, которые определяет возникающее в этом случае комплексное физико–механическое воздействие на материал. Так же стоит отметить, что в литературных источниках практически отсутствует информация о зависимости кормовых качеств зерновых продуктов от воздействий, оказываемых на них в процессе экструзии.
Изучение влияния физико–механических воздействий на материал, возникающих при экструзии на кормовые качества, является актуальной задачей, решение данной проблемы позволит целенаправленно выбирать конструктивные параметры экструдера и технологические режимы с учетом показателей кормового качества [1].
Одним из способов совершенствование процесса экструдирования является совершенствование конструкции матриц экструдера.
Для этой цели планируется исследования на лабораторном экструдере на кафедре сельскохозяйственных машин и оборудования Пермского ГАТУ. На рисунке 1 изображена схема экструдера.
1 – матрица, 2 – корпус, 3 – шнек, 4 – корпус подщипников, 5 – подшипники, 6 – вал приводной, 7 – муфта, 8 – редуктор с приводом, 9 – рама
Рисунок 1 – Схема экспериментального экструдера
Общий вид экструдера показан на рисунке 2.
156
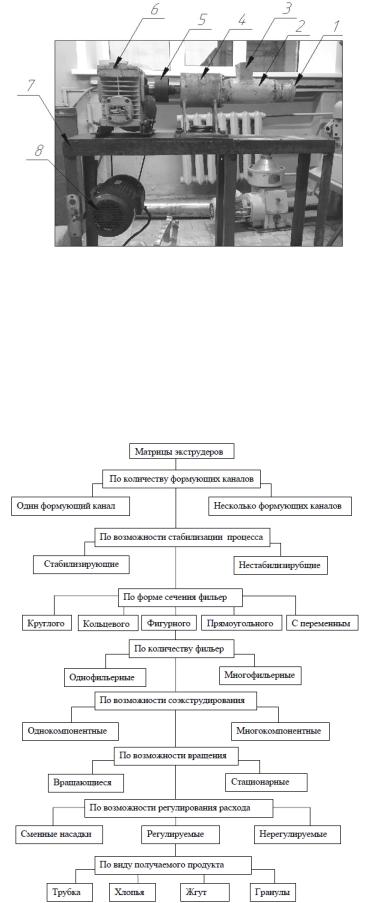
1 – матрица, 2 – корпус, 3 – загрузочная горловина, 4 – корпус подшипников, 5 – муфта, 6 – редуктор с приводом, 7 – рама; 8 – двигатель
Рисунок 2 – Общий вид экспериментального экструдера
Экструдер работает следующим образом: при вращении шнека в корпусе 2 экструдируемый продукт равномерно подается в загрузочную горловину 3 экструдера и направляется прессующим шнеком в сторону матрицы 1. Для перемещения материала необходимо, чтобы трение о материал корпуса 2 было больше трения о витки шнека.
Рисунок 3 – Классификация матриц
157
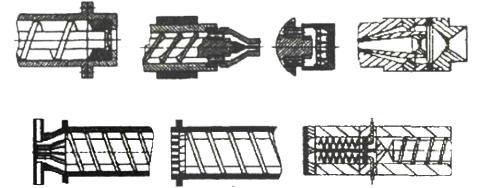
На конечный процесс экструдирования большое влияние оказывает матрица. Для того что бы определить наиболее перспективную конструкцию конфи-
гурацию матрицы для экструдироваиия зерновых материалов был проведена классификация матриц (рисунок 3).
Так же существует множество различных конструкций матриц. На рисунке 4 были приведены наиболее распространенные из них.
а |
б |
в |
г |
д |
е |
|
Рисунок 4. Матрицы экструдеров |
|
На рисунке 4а наконечник формующей головки экструдера сделан в виде цилиндра с диаметром и он равен внутреннему диаметру шнека, на втулке снята фаска, она понижает сопротивление в зазоре матрицы при вдавливании продукта шнеком. Рисунок 4 – б показывает матрицу со сменными формующими насадками они позволяют получать переработанный продукт разных форм. Для лучшей гомогенизации экструдата перед ними устанавливается специальная решётка.
Матрица (рисунок 4 – в). Эта матрица позволяет достигать форм получаемого продукта в виде ядра, окружённого оболочкой, а матрица (рисунок 4 – г) разработана для выравнивания расхода между фильерами, которые изготовлены в виде ввинчивающихся втулок.
Конструкция на рисунке 4 – д была придумана для предотвращения залегания продукта, в ее предматричной зоне расположены лопасти для нагнетания продукта в отверстия матрицы.
Экструзионную головку (рисунок 1.2 – е) разработали для экструдирования сразу нескольких компонентов в зависимости от содержания различных компонентов исходного сырья. Трубки, по которым подаются дополнительные компоненты, так же выполняют функцию турбулизаторов, для лучшего перемешивания всех компонентов.[3]
Выводы Обзор матриц, дает понять что существует множество способов подхода к
решению проблемы изготовления экструдированых кормов, поэтому создание новых конструкций матриц с меньшими затратами и наиболее высокой экономической эффективностью является актуальной.
Литература 1. Исмагилов Р.Р., Ахиярова Л.М. Кормовые качества зерна озимой ржи. – Уфа: Гилем,
2012. 116 с.
158
2.Влияние замены сахара-песка олигофруктозой на изменение реологических показателей бисквитного теста / С.Я. Корячкина [и др.] // Сб. науч. тр. II науч.-практ. конф. «Управление реологическими свойствами пищевых продуктов». - М.: ГОУВПО «МГУПП», 2010. С. 67-70.
3.Зубкова Т.М., Насыров А.Ш. Учет характера движения материала в канале шнека при математическом моделировании экструдирования растительного сырья // Вестник ОГУ. 2003. №1. С. 147-151.
4.Черняев Н.П. Технология комбикормового производства. – М.: Агропромиздат , 1985.
255 с.
УДК: 631.371:631.365.22
В.А. Игошев – магистрант; А.Д. Галкин – научный руководитель, профессор,
ФГБОУ ВО Пермский ГАТУ, г. Пермь, Россия
НАПРАВЛЕНИЯ СНИЖЕНИЯ ЗАТРАТ ЭНЕРГИИ НА СУШКУ ЗЕРНА И СЕМЯН
Аннотация. Целью исследований является выявление путей снижения энергии на сушку зерна и семян. Сушка является наиболее дорогостоящей и энергоемкой операцией послеуборочной обработки зерна и семян. При этом затраты на топливо и электроэнергию могут достигают до 60% от общих затрат, при этом на жидкое топливо приходится более 90% общих энергозатрат. Из обзора исследований установлено, что снижение затрат энергии на сушку зерна можно достичь за счет: использования двухэтапной технологии сушки с применением колонковых зерносушилок, в том числе сотового типа, позволяющих проводить операцию при повышенных расходах агента сушки; использовать системы рециркуляции сушильного агента, позволяющие добиться снижения расхода топлива зерносушилкой до 30 %; применять технологии консервирования фуражного зерна, приводящие к снижению энергозатрат топлива на доведение урожая до состояния, приспособленного к хранению до 40 %; обеспечивать оптимальные режимы работы зерносушилок с использованием автоматических систем управления.
Ключевые слова: зерно, семена, сушка, затраты энергии.
Производство зерна и семян злаковых растений имеют огромное значение в жизни человека, так как продукты питания, выработанные из них, являются важной составной частью пищи человека и имеют большую ценность. Однако, высокий уровень цен на топливные ресурсы ставит жесткие экономические условия для сельскохозяйственных предприятий. К числу одних из наиболее энергозатратных операций относится сушка зерна и семян. В этой связи возникает задача снижения затрат на осуществление этой операции [2].
Для решения этой задачи следует использовать системный подход, основными элементами которого являются: использование более дешевых и эффективных видов местного топлива совместно с совершенствованием конструкции топок
159
и их распылительных устройств; применение более эффективной системы теплоизоляции корпуса зерносушилок для снижения тепловых потерь с окружающей средой, а также внедрение и использование рекуперативных теплообменников, которые используют отработавший агент сушки для передачи части тепла вновь поступающему в сушилку воздуху.
Значительный эффект дает применение систем рециркуляции теплоносителя, предварительного нагрева и фракционирования зерна перед сушкой семенной и продовольственной фракций [1, 2, 11], использование консервантов для хранения фуражной фракции, снижение влажности зерновой массы в сушилках и подачи зерна на воздушно-решѐтные машины с последующим удалением влаги [1, 6,
7, 9].
Важным для снижения себестоимости сушки является применение энергосберегающих способов сушки, например, двухэтапной технологии, а также рациональный выбор оборудования с учетом свойств зернового вороха, теплоизоляция сушилок [10]; применение гелиосушильных установок, использующих аккумуляторы, и позволяющих выполнять технологический процесс в ночное время [1, 5, 8]; наличие системы аспирации в составе зерносушилки [3, 4]; внедрение системы управления, основанной на проведении энергоаудитов, типовых измерений и проверок, обеспечивающей работу по энергообеспечению предприятия, при которой потребляется необходимое, но достаточное для эффективного производства количество энергии [1]; рациональный выбор способа подачи теплоносителя; выполнение настроек зерносушильных установок, проведение технологического обслуживания.
Вывод. Для снижения энергетических затрат на сушку зерна и семян при поступлении на обработку влажного зернового вороха, целесообразно:
-внедрять двухэтапную технологию сушки, позволяющую снизить затраты энергии за счет отлежки и доведения зерна до кондиционной влажности в вентилируемых бункерах с применением колонковых зерносушилок, в том числе сотового типа, позволяющих проводить операцию при повышенных расходах агента сушки;
-использовать системы рециркуляции сушильного агента, позволяющие добиться снижения расхода топлива зерносушилкой до 30 %;
-применять технологии консервирования фуражного зерна, приводящие к снижению энергозатрат топлива на доведение урожая до состояния, приспособленного к хранению, до 40 %:
-обеспечивать оптимальные режимы работы зерносушилок с использованием автоматических систем управления.
Литература 1. Пиляева О.В., Книга Ю.А. Основные направления энергосбережения при эксплуатации
зерноочистительно-сушильных комплексов сельскохозяйственного назначения // Технические науки – от теории к практике: мат-лы XIX междунар. заочн. научно-практич. конф. 20.03.2013 г.
2. Манасян С.К. Принципы конвективной сушки зерна // Вестн. КрасГАУ. 2008. № 6. С.
145-150.
160