
2601
.pdf3) Немаловажным фактором влияющим на эксплуатационную надежность тахографа является место его установки. Меньшим поломкам подвергаются Тахографы, установленные в верхней панели кабины.
Библиографический список
1.Кузнецов Е.С. Техническая эксплуатация автомобилей: Учебник для вузов. - 3-е изд., перераб. и доп. / Е. С. Кузнецов, В. П. Воронов, А. П Болдин и др.; Под
ред. Е. С. Кузнецова / Издательство: М.: Транспорт, 1991. - 413 с.
2.РД 37.001.246-92 Установка тахографа на автотранспортном средстве. Тех-
нические требования.
3.РД 37.001.247-92 Установка тахографа на автотранспортном средстве. Ме-
тоды проверки.
УДК 621.81.004.63:621.81.004.67
ПОВЫШЕНИЕ ЭКСПЛУАТАЦИОННЫХ СВОЙСТВ ДЕТАЛЕЙ МАШИН ПРИ ВОССТАНОВЛЕНИИ
С.Н. Филимонов, магистрант; С.А. Балановский, магистрант; М.М. Лучко, магистрант
Омский государственный технический университет
При выполнении ремонта транспортных и технологических машин особое внимание при восстановлении уделяют высоконагруженным деталям двигателей, ходовой части, трансмиссии и других узлов и агрегатов, работающих при повышенных напряжениях, в условиях вибрационных нагрузок, при повышенных температурах.
Задачи восстановления таких деталей включают:
восстановление размеров изношенных поверхностей;
обеспечение заданных эксплуатационных свойств поверхностей и материала поверхностного слоя.
В большинстве случаев целью решения исполненных задач является обеспечение эксплуатационных свойств деталей, уровень которых близок
ксвойствам новых деталей.
Вместе с тем, учитывая широкие возможности технологического воздействия на поверхности и на материал поверхностного слоя детали, с помощью такого воздействия можно решать задачи повышения эксплуатационных свойств восстанавливаемых деталей.
В наиболее общем виде схема формирования многоуровневого слоя при восстановлении приведена на рис.1
На этапах удаления дефектного слоя (рис.1а), нанесения восстановительного слоя (рис. 1б), размерной и модифицирующей обработки (рис. 1в) обеспечена широкая возможность использования современных методов технологического воздействия на рассматриваемый многоуровневый слой.
60
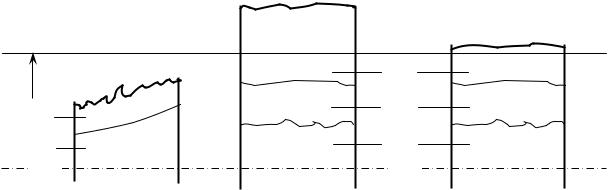
Для нанесения восстановительного слоя были исследованы возможности плазменного напыления.
N
1
2
5
4
3
2
а |
б |
в |
Рис. 1. Схема многоуровневого поверхностного слоя при восстановлении детали: а, б, в – этапы формирования слоя: состояние изношенной детали, после нанесения восстановительного слоя, на завершении процесса восстановления. 1 – измененный изнашиваемый слой; 2 – основа материала детали; 3 – подслой; 4 – основной восстанови-
тельный слой; 5 – защитное покрытие.
В процессе восстановления деталей имеет место неоднократное нанесение, снятие поверхностного слоя и формирование новых поверхностей. При этом расчет размерных цепей, назначение величины наносимых и удаляемых поверхностных слоев, определение пооперационных припусков и решение других технологических задач было предложено выполнять с помощью предложенной обобщенной схемы изменения поверхностного слоя деталей при восстановлении и параметров этого слоя. Отдельные указанные параметры приведены в табл. 1.
Параметры деталей |
Таблица 1 |
|
|
|
|
Наименование параметров поверхностей и поверхностного слоя дета- |
Обозна- |
лей при восстановлении |
чение |
Подготовка под нанесение слоя |
|
Толщина слоя, связанная с неравномерным износом поверхности, для |
|
выравнивания толщины наносимого слоя |
Hи |
Глубина дефектного слоя, сформированного после нанесения слоя и его |
|
термообработки |
Hд |
Размерная и отделочная обработка после нанесения слоя |
|
Геометрические отклонения обрабатываемых поверхностей относи- |
Е (с, сл) |
тельно базовых (систематические, случайные) |
|
Суммарные погрешности установки детали (систематические, случай- |
ΔXY (с, сл) |
ные) |
|
Суммарные погрешности обработки детали (систематические, случай- |
ΔXO(с, сл) |
ные) |
|
Толщина нанесенного слоя после размерной обработки |
Нг |
Глубина поверхностного слоя, измененного размерной обработкой |
Но |
Толщина слоя, снятого размерной обработкой |
НС |
61
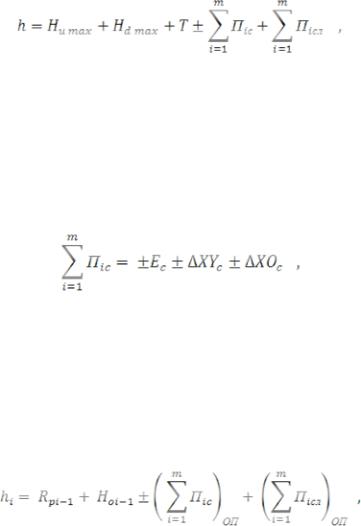
Окончание таблицы 1
Глубина поверхностного дефектного слоя после предыдущей обработки |
Нoi-1 |
Шероховатость поверхности после окончательной обработки нанесен- |
Rp |
ного слоя |
|
Шероховатость поверхности после предыдущей размерной обработки |
Rpi-1 |
нанесенного слоя |
|
В общем случае применительно к условиям обработки поршня при одностороннем снятии припуска на размерную обработку, связанную с подготовкой поверхности под нанесение восстановительного слоя, может быть определен зависимостью:
(1)
где T – допуск на размер; Пiс – результирующая систематических погрешностей, связанных с геометрическими отклонениями обрабатываемых поверхностей относительно базовых, а также с погрешностями установки и обработки детали; Пiсл – результирующая случайных погрешностей, связанная с теми же отклонениями и погрешностями; m – число соответствующих геометрических отклонений и погрешностей.
В зависимости (1) результирующую систематических погрешностей определяют по формуле:
(2)
где положительные и отрицательные значения слагаемых назначают, когда направление действия отклонений и погрешностей соответственно совпадает или противоположно направлению увеличения припуска h.
Аналогично формуле (2) определяют результирующую случайных погрешностей. При этом слагаемым придают только положительные значения. В случае удаления припуска h на нескольких операциях (переходах) припуск на очередной операции (переходе) можно определить следующим образом:
(3)
где два последних слагаемых соответствуют результирующим систематических и случайных погрешностей на рассматриваемой операции (переходе).
Установлено, что обеспечение повышенных эксплуатационных свойств деталей в процессе восстановления может быть достигнуто за счет подбора состава порошковых материалов, используемых для напыления.
При выборе материала наносимого слоя для поршней из алюминиевых сплавов установлены преимущества алюмосиликатного состава, со-
62
держащего 40% Al2O3 и 60% SiO2, а для подслоя использован Mо. Наряду с другими преимуществами выбор указанного состава определен его каталитической активностью к продуктам горения в камере сгорания двигателя.
Испытания в эксплуатации поршней двигателей модели Д50, 11Д45 и других, прошедших восстановление по указанной технологии с нанесением каталитического алюмосиликатного покрытия, показали повышение ряда их эксплуатационных характеристик вследствие улучшения процесса сгорания топлива. Так, установлено снижение отложения нагара на 2040%, снижение скорости изнашивания втулки цилиндра на 15-25%, уменьшение расхода топлива на 3-4%.
Отдельные результаты применения плазменного напыления для повышения износостойкости и антифрикционных свойств, а также для улучшения других характеристик приведены в табл. 2. [2]
|
|
|
Таблица 2 |
Эффективность применения плазменных покрытий |
|||
|
|
|
|
Типовые детали ма- |
Обеспечиваемые |
Составы порошко- |
Эффективность при- |
шин и агрегатов |
эксплуатацион- |
вых материалов |
менения деталей с |
|
ные свойства |
|
покрытиями |
Лопатки транспорт- |
Жаро – и эрози- |
Система (Ni-Cr- |
Повышение ресурса в |
1,5 – 2 раза; обеспе- |
|||
ных ГТД |
онная стойкость |
Si)++ антиэррозион- |
чивает ресурс после |
|
|
ные присадки |
восстановления |
|
|
|
|
Камеры сгорания, |
|
Диоксид циркония, |
|
форсунки, сопловые |
Жаро – и эрози- |
Повышение ресурса в |
|
аппараты, сопла |
онная стойкость |
стабилизированный |
2 – 2,5 раза |
транспортных ГТД |
|
окисью магния |
|
|
|
|
|
Шейки коленчатых |
|
Система (Ni-Cr-Si) |
|
и распределитель- |
Износостойкость |
++ (НПГ-80) + тер- |
Увеличение ресурса в |
ных валов, гильзы |
морегулирующий |
2 – 2,5 раза |
|
цилиндров ДВС |
|
порошок |
|
Головки поршней, |
Теплозащитные |
|
Повышение ресурса в |
свойства, улуч- |
|
1,5 – 2 раза; снижение |
|
стенки камеры сго- |
|
||
шение условий |
Диоксид циркония |
расхода топлива на 3 |
|
рания дизельных |
сгорания топ- |
|
– 5% и угара масла на |
двигателей |
|
||
лива |
|
20 – 30% |
|
|
|
||
Диски сцепления, |
|
Бронза (железо) + |
Повышение ресурса в |
тормозных уст- |
Износостойкость |
||
ройств транспорт- |
графит + оксиды |
1,5 – 2 раза |
|
ных машин |
|
|
|
Сочетание обоснованной минимальной толщины наносимого восстановительного слоя с назначением рационального состава порошковых материалов позволяет обеспечить необходимые эксплуатационные свойства восстановленных деталей с минимальным расходом материалов.
63

Библиографический список
1.Восстановление деталей машин: Справочник / Ф.И. Пантелеенко, и др.; под ред. В.П. Иванова М.: Машиностроение, 2003. - 672 с.
2.Вивденко Ю.Н., Супрунов Г.Н. Газотермическое напыление и свойства поверхностного слоя деталей машин./ Военная техника, вооружение и технологии двойного применения: Материалы III международного конгресса (Омск, 7 – 10 июня 2005г.): В 22.
Омск: ОмГТУ, 2005 – 4.I. с 107 – 110.
УДК 629.3.014:66.074.912-024
ВЛИЯНИЕ КАЧЕСТВА СЖИЖЕННОГО УГЛЕВОДОРОДНОГОГАЗА НА НАДЕЖНОСТЬ ЭЛЕМЕНТОВ ГАЗОВОЙ СИСТЕМЫ ПИТАНИЯ
Р.Ю. Филоненко, преподаватель Сибирская государственная автомобильно-дорожная академия
При эксплуатации газобаллонных автомобилей работающих на сжиженном углеводородном газе предусмотрен целый ряд регламентных работ, влияющих на безопасность транспортного средства. Одним из таких видов работ является освидетельствование баллона.
Периодичность технического освидетельствования составляет: 10 лет - для баллонов с толщиной стенки 3 мм и 5 лет - для баллонов с толщиной стенки 2,5 мм.
Основными причинами проведения освидетельствования является то, что баллон постоянно находиться под высоким давлением и в составе сжиженного углеводородного газа содержаться примеси, которые вызывают коррозию сосуда тем самым уменьшая толщину его стенок.
Рис. 1. Внутренняя поверхность газового баллона объемом 50 литров после 5 лет эксплуатации
Внешняя поверхность баллона, принимаемого на освидетельствование, должна быть очищена от загрязнений. Газовый баллон должен иметь паспорт, оформленный в соответствие с нормативной документацией. На баллоне должна быть установлена запорно-предохранительная арматура. Наружная поверхность баллона не должна иметь раковин, глубоких рисок,
64
заметных деформаций, выработки в местах крепления и других серьезных повреждений, наличие которых дает право на выбраковку.
Перед проведением освидетельствования необходимо проконтролировать наличие в баллоне остатков газа. При наличии остатков СУГ удалить их через продувочную свечу. После удаления остатков СУГ, внутреннюю поверхность пропарить под давлением 0,14.. .0,15 МПа в течение 25...35 мин. При проведении осмотра наружной и внутренних поверхностей особое внимание уделяется наличию трещин, раковин, вмятин, коррозии, рисок и выработки глубиной более 10 % от номинальной толщины стенки и других серьезных повреждений, наличие которых дает право на выбраковку.
При проведении гидравлических испытаний внутренняя полость баллона должна быть полностью заполнена водой. Наличие воздуха в баллоне недопустимо. При этом перепад температур окружающей среды и воды не должен превышать 5 °С. При давлении 2,5 МПа (25 кгс/см2) выдержать баллон не менее 2 мин. При давлении 1,6 МПа (16 кгс/см2) обстукать молотком сварные соединения и осмотреть наружную поверхность баллона. В сварных соединениях не допускаются трещины всех видов и направлений, расположенные в металле шва, по линии сплавления и в околошовной зоне основного металла. Баллоны считаются выдержавшими гидравлическое испытание, если не обнаружено признаков разрыва, видимых остаточных деформаций обечайки и днищ, течи и потений швов сварных соединений.
Действительная масса баллона определяется из выражения
т = т1-∑тi,
где m1 - масса баллона, полученная первым взвешиванием (до гидроиспытания), кг; ∑mi - суммарная масса всех заглушек, крышки отверстия датчика уровня и сливной пробки, кг. Баллон считается пригодным к эксплуатации, если его действительная масса 0,93mn<m< mn, где mn - номинальная масса баллона, кг. При отклонении m от номинальной на 7 % и более баллон бракуется. Действительный объем баллона в литрах равен V = (т2 –т)/ρ, где т2 - масса баллона с водой, полученная вторым взвешиванием (после гидроиспытания), кг; ρ – плотность воды кг/м3,. Баллон считается пригодным к эксплуатации, если его действительный объем 0,985VH<V< 1,015VН, где VН - номинальный объем баллона, л. При отклонении V от номинального на 1,5 % и более баллон бракуется.
Таким образом можно сделать вывод, что автомобильные газовые баллоны подвержены влиянию агрессивных примесей, содержащихся в газовом топливе. Проведенные исследования сжиженного углеводородного газа и в частности конденсата из редуктора показали следующий состав и свойства примесей (рисунок 2).
65
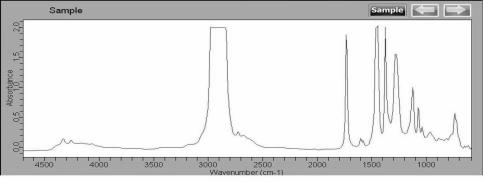
Рис. 2. Спектрограмма компонентного состава конденсата сжиженного углеводородного газа
1.Продукты окисления 52,043 Abs/0,1mm (окисление запредельное, например для моторного масла максимум 25, обычно около 10)
2.Продукты сульфатирования (соединения с группой SO2 и SO3) 34,915 Abs/0,1mm(тоже запредельное, например для моторного масла максимум 23).
3.Легкие углеводороды 32,933% по весу.
4.Конденсированные спирты 3,914% по весу.
5.Вода 0,0082% по весу (то есть практически нет).
6.Нитрация (соединения групп NO2 и NO3 ) 4,277 Abs/0,1mm
7.Сажа 0,074% по весу. Практически нет.
8.Карбонаты 0,316 Abs/0,1mm.
Испытания проводились на инфракрасном спектрографе Termo Grams ASCII.
Агрессивные примеси, содержащиеся в газовом топливе, активно реагируют с металлом газового баллона и образуют достаточно крупные и твердые частицы окалины и ржавчины, которые попадая в газовую магистраль интенсивно засоряют фильтрующие элементы, снижает надежность газовой системы питания, а при прохождении сквозь фильтр вызывают повышенный износ деталей цилиндро-поршневой группы и газораспределительного механизма.
На сегодняшний день существует несколько способов увеличения ресурса газового баллона:
-улучшение качества газового топлива, отпускаемого на АГЗС;
-применение материалов, устойчивых к воздействию агрессивных примесей;
-выполнение регламентных работ (очистка внутренних поверхностей, обработка ингибирующими составами).
Библиографический список
1 Баллоны стальные сварные для сжиженных углеводородных газов на давление до 1.6
ГОСТ 15860-84 – 18 с.
2 Баллоны стальные сварные для сжиженных углеводородных газов. Правила ремонта и технического освидетельствования ОСТ 153-39.1-003-00 – 13 с.
66
3 Правила устройства и безопасной эксплуатации сосудов работающих под ПБ10-115- 96–140 с.
4 Певнев Н.Г. Техническая эксплуатация газобаллонных автомобилей: Учебное пособие. - Омск: Изд-во СибАДИ, 2002.- 219 с.
УДК 621.439:629.114.5
АНАЛИЗ ЭКСПЛУАТАЦИОННЫХ ЗАТРАТ АВТОМОБИЛЯ С ДВУХТОПЛИВНОЙ СИСТЕМОЙ ПИТАНИЯ
Д.А. Фоменко, аспирант; И.В. Хамов, канд. техн. наук, доцент Сибирская государственная автомобильно-дорожная академия
Цель технического обслуживания (ТО) - поддержание подвижного состава в работоспособном состоянии и надлежащем внешнем виде, уменьшение интенсивности изнашивания деталей, предупреждение отказов и неисправностей, а также выявление их с целью своевременного устранения. ТО является профилактическим мероприятием, проводимым принудительно в плановом порядке через определенные пробеги или время работы подвижного состава.
Газобаллонные автомобили (ГБА) по сравнению с автомобилями, работающими на жидком топливе, имеют ряд особенностей, вызванных наличием у них газовой системы питания, находящейся под давлением. Эти особенности учитываются при организации и проведении ТО, как системы питания, так и автомобиля в целом. Виды ТО ГБА такие же, как и базовых автомобилей без установленного комплекта газобаллонного оборудования (ГБО), но общая трудоемкость работ ТО ГБА выше на 10-15%[2].
Так как ТО ГБА такие же как и базовых автомобилей, за исключением газовой топливной системы, то необходимо вычислить затраты на обслуживание бензиновой и газовой систем питания (на примере развозного автомобиля ГАЗ-3302 «Газель» в условиях г. Омска). Проанализировав рынок г. Омска, была выявлена средняя цена на ТО газовой и бензиновой систем питания, как контрольной части операции, так и исполнительной.
Согласно методу определения периодичности по допустимому значению и закономерности изменения параметра технического состояния, были произведены расчеты и определены пробеги до проведения контрольной части операции, ремонта и очистки, а так же до замены и ремонта элементов газовой и бензиновой систем питания, кратность технических воздействий для элементов газовой и бензиновой систем питания с пробегом автомобиля 100000 км, рассчитаны затраты на выполняемые работы и материалы (таблица 1).
Таблица 1
67
Эксплуатационные затраты на ТО газовой и бензиновой систем питания в расчете на 100000 км
|
|
|
|
|
Технические воздействия |
|
|
|||
|
|
|
|
|
|
|
|
|
|
|
|
|
|
Перио- |
|
|
|
|
|
|
|
|
|
|
дичность, |
|
|
|
Стои- |
|
Периодич- |
Стои- |
|
|
|
км./ |
|
Периодич- |
|
мость |
|
ность,км./ |
мость |
№ |
Элементы |
|
крат- |
Стоимость |
ность,км./ |
|
регу- |
|
кратность, |
ремонта, |
|
ность, |
контроль- |
кратность, |
|
лиров- |
|
ед./цена |
замены |
||
|
|
|
ед./цена |
нойчасти |
|
|
ремонта, |
|||
|
|
|
кон- |
операции, |
ед./цена ре- |
|
кии |
|
замены(с |
(с учетом |
|
|
|
гулировкии |
|
очист- |
|
запча- |
|||
|
|
|
трольной |
СК,руб. |
очистки,руб. |
|
ки,СРО, |
|
учетомзап- |
стей), |
|
|
|
части |
|
|
|
руб. |
|
частей), |
СРЗ, руб. |
|
|
|
операции, |
|
|
|
|
руб. |
||
|
|
|
|
|
|
|
|
|
||
|
|
|
руб. |
|
|
|
|
|
|
|
1 |
2 |
|
3 |
4 |
5 |
|
6 |
|
7 |
8 |
|
|
|
|
|
|
|
|
|
|
|
|
|
|
|
Газовая система питания |
|
|
|
|
||
1 |
Газовые |
|
10000/10/ |
1200 |
15000/6,66/ |
|
2664 |
|
45000/2,22/ |
4218 |
форсунки |
|
120 |
400 |
|
|
1900 |
||||
|
Фильтр |
|
|
|
|
|
|
|
60000/1,66/ |
|
2 |
газа в ре- |
|
- |
- |
- |
|
- |
|
763,6 |
|
|
|
|
460 |
|||||||
|
дукторе |
|
|
|
|
|
|
|
|
|
|
|
|
|
|
|
|
|
|
|
|
|
Фильтр |
|
5000/20/ |
|
|
|
|
|
15000/6,66/ |
|
3 |
тонкой |
|
2000 |
- |
|
- |
|
2331 |
||
|
очистки |
|
100 |
|
|
|
|
|
350 |
|
|
газа |
|
|
|
|
|
|
|
|
|
4 |
Редуктор |
|
15000/ |
1322 |
30000/3,33/ |
|
3330 |
|
60000/1,66/ |
6640 |
|
6,66/200 |
1000 |
|
|
4000 |
|||||
|
Датчик |
|
|
|
|
|
|
|
|
|
5 |
темпера- |
|
10000/10/ |
1500 |
- |
|
- |
|
30000/3,33/ |
1332 |
туры, дав- |
|
150 |
|
|
400 |
|||||
|
ления газа |
|
|
|
|
|
|
|
|
|
|
|
|
|
|
|
|
|
|
|
|
|
Датчик |
|
|
|
|
|
|
|
|
|
6 |
темпера- |
|
15000/ |
999 |
- |
|
- |
|
60000/1,66/ |
1162 |
туры ре- |
6,66/150 |
|
|
700 |
||||||
|
дуктора |
|
|
|
|
|
|
|
|
|
7 |
ЭБУ |
|
25000/4/ |
1200 |
- |
|
- |
|
75000/1,33/ |
9975 |
|
300 |
|
|
7500 |
||||||
|
|
|
|
|
|
|
|
|
||
|
Итого: |
|
8221 |
|
|
5994 |
|
|
26421,6 |
|
|
Бензиновая системапитания [двухтопливная система питания]* |
|
||||||||
|
|
|
|
|
30000/3,33/ |
|
|
|
90000/1,11/ |
|
8 |
ЭБН |
|
15000/ |
999 |
400 |
|
1332 |
|
1500 |
16650 |
|
6,66/150 |
[125000/0,8/ |
|
[320] |
|
[370370/ |
[450] |
|||
|
|
|
|
|
|
|||||
|
|
|
|
|
400] |
|
|
|
0,33/1500] |
|
68
Окончание таблицы 1
1 |
2 |
|
3 |
4 |
5 |
6 |
7 |
8 |
|
|
|
5000/20/ |
|
15000/6,66/ |
|
60000/1,66/ |
|
9 |
ЭМФ |
|
200 |
4000 |
800 |
5328 |
2500 |
4150 |
|
[2000/50/ |
[10000] |
[10000/10/ |
[8000] |
[400000/2,5/ |
[6250] |
||
|
|
|
||||||
|
|
|
200] |
|
800] |
|
2500] |
|
|
|
|
|
|
|
|
75000/1,33/ |
|
10 |
ЭБУ |
|
25000/4/ |
800 |
- |
- |
4500 |
5985 |
|
200 |
[250000/ |
[1485] |
|||||
|
|
|
|
|
|
|||
|
|
|
|
|
|
|
0,33/4500] |
|
|
|
|
|
|
|
|
60000/1,66/ |
|
11 |
Датчики |
|
10000/10/ |
1500 |
- |
- |
550 |
913 |
ЭСУД |
|
150 |
[250000/0,4/ |
[220] |
||||
|
|
|
|
|
|
|
550] |
|
|
Фильтр |
|
|
|
|
|
1500/6,66/ |
|
|
|
|
|
|
|
400 |
2664 |
|
12 |
тонкой |
|
- |
- |
- |
- |
||
|
[60000/1,66/ |
[664] |
||||||
|
очистки |
|
|
|
|
|
||
|
|
|
|
|
|
400] |
|
|
|
|
|
|
|
|
|
|
|
|
Фильтр |
|
|
|
|
|
30000/3,33/ |
|
|
|
|
|
|
|
600 |
1998 |
|
13 |
грубой |
|
- |
- |
- |
- |
||
|
[125000/0,8/ |
[480] |
||||||
|
очистки |
|
|
|
|
|
||
|
|
|
|
|
|
600] |
|
|
|
|
|
|
|
|
|
|
|
|
Итого: |
|
7299 |
|
66602 |
|
18550 |
|
|
|
[10000] |
|
[8320] |
|
[10258] |
||
|
|
|
|
|
|
*Учитывая тот факт, что при эксплуатации ГБА бензиновая система питания используется на 25% (заезд в ремонтную зону и выезд из нее после проведения технических воздействий, запуск двигателя в зимнее время (при температуре окружающей среды ниже 0 град. С)[1]), соответственно кратность технических воздействий на элементы бензиновой системы питания относительно плановых ТО изменяется, кроме ЭМФ [3].
После анализа эксплуатационных затрат на обслуживание элементов систем питания, выделим ряд преимуществ, сказывающихся на увеличении срока службы ГБА посравнению с бензиновым[2]:
·увеличение срока службы свечей зажигания - в 1,5 раза;
·увеличение срока службы моторного масла- в 1,4 раза;
·повышение моторесурса двигателя –в 1,6 раза .
Втаблице 2 представлены затраты при эксплуатации автомобиля с пробегом 100000 км, с учетом вышеизложенного.
Расчет затрат на ТО автомобиля с пробегом 100000 км с учетом контрольных, регулировочных, ремонтных работ и определения срока окупаемости ГБО, произведем по следующим формулам:
-для бензиновой системы питания:
ЗТОб= СКб+ СРОб+ СРЗб+ССЖб+СММб+СКРДб,
где ЗТОб – затраты на ТО бензиновой системы питания, руб.;
69