
2601
.pdfгде х = НУ/1000.
Анализ современных методов упрочнения материалов показывает, что существует два принципиальных различных направления разработки упрочняющих технологий.
Первое направление. Объёмное упрочнение, которое предполагает обработку материала изделия в целом, при чём упрочнению в данном случае могут подвергаться как ограниченные зоны, так и весь объём. Реализация данного направления осуществляют термической обработкой, легированием, созданием материалом с армированием и г.д.
Второе направление. Поверхностное упрочнение - создание на рабочих поверхностях изделий покрытий, слоев, плёнок, имеющих более высокую твёрдость и износостойкость, чем основной материал. К ним относятся методы физического и химического осаждения покрытий, плазменные и детонационные методы, ионная имплантация, электроискровое легирование и др. Большинство этих методов характеризуются небольшой толщиной упрочняющего слоя( до долей мм). Наибольшая толщина упрочнённого слоя поверхности материала с высокой износостойкостью достигается высокоэнергетическими методами порошковой металлургии (электродуговая и газовая наплавка, электродуговая детализация, детонационное нанесение покрытий и др.)
В табл. 1 приведены данные микроструктуры, химического состава и твёрдости поверхности, упрочнённой плазменной наплавкой. Как видно из табл. 1, плазменная наплавка позволяет получать поверхности с боросодержащей мартенситной и аустенитно-мартенситной микроструктурой с твёрдостью на уровне НУ 580 и выше, что по эмпирической формуле для условия интенсивного изнашивания обеспечит низкое значение относительного износа: менее 0,16.
|
|
|
|
|
|
|
|
Таблица 1 |
||
Химический состав и твёрдость на плавленой поверхности |
||||||||||
|
|
|
|
|
|
|
|
|
|
|
Микроструктура |
|
Химический состав, % |
|
Твердость |
||||||
|
|
|
|
|
|
|
НУ |
|
||
С |
Si |
Мn |
С г |
Мо |
V |
В |
||||
|
|
|
||||||||
1 |
2 |
3 |
4 |
5 |
6 |
7 |
8 |
9 |
|
|
Низколегированная |
0,25 |
1,38 |
0,92 |
2.86 |
0,46 |
- |
- |
250 |
|
|
мартенситная |
0,68 |
0,8 |
1,16 |
2.72 |
- |
0,25 |
- |
705 |
|
|
|
0,3 |
1,47 |
0,46 |
3,91 |
0,5 |
- |
- |
580 |
|
|
|
0,46 |
0,94 |
1,18 |
4,01 |
0,5 |
- |
- |
640 |
|
|
Боросодержащая |
0,9 |
0,95 |
0,75 |
8,25 |
0,52 |
- |
0,27 |
805 |
|
|
мартенситная |
|
|||||||||
|
|
|
|
|
|
|
|
|
|
|
|
|
|
|
|
|
|
Окончание таблицы 1 |
|||
|
|
|
|
|
|
|
|
|
|
|
1 |
2 |
3 |
4 |
5 |
6 |
7 |
8 |
9 |
|
|
|
|
|
|
|
|
|
|
|
|
|
|
|
|
10 |
|
|
|
|
|
|
Аустенитная |
0,74 |
1 |
0,59, |
7,1 |
0,85 |
- |
- |
580 |
|
мартенситная |
|||||||||
|
|
|
|
|
|
|
|
||
Хромистая |
0,25 |
0,83 |
2,46 |
10,78 |
- |
- |
- |
550 |
|
Хромистая |
1,01 |
0,35 |
0,85 |
12,75 |
0,5 |
- |
- |
370 |
|
|
|
|
|
|
|
|
|
|
Таким образом, из имеющихся методов по технологическим показателям для восстановления рабочего элемента техники в настоящее время наиболее перспективно применение плазменной плавки поверхности трения.
Учёт класса стали позволяет прогнозировать после наплавки существенное снижение относительного износа. На основе приведённых исследований рекомендовано использование технологий плазменной наплавки финишного плазменного упрочнения для повышения износостойкости рабочего элемента землеройной техники.
Библиографический список
1.Винокуров Г.Г., Яковлева С.П., Кычкин А.К., Васильева М.И., Стручков Н.Ф., Федо-
ров М.В. Изменение структуры и изнашивание породоразрушающего элемента бульдозера при эксплуатации в условиях севера. // Металлы. -№5.-2009.-С.74-80.
2.Сорокин В.Г., Волосникова А.В., Вяткин С.А. и др. Марочник сталей и сплавов. -М:
Машиностроение, 1089.-640с.
3.Лахтин Ю.М. Основы металлоповедения. -М.: Металлургия, 1988.-320 с.
4.Виноградов В.Н., Сорокин Г.М., Колокольников М.Г. Абразивное изнашивание. —
М.: Машиностроение, 1990.-224 с.
5.Крагельский И.В., Добычин М.Н., Комбалов В.С. Основы расчетов на трение и износ. -М.: Машиностроение, 1977.-526 с.
6.Справочник по триботехнике. / Под общ. ред. М. Хебды, А.В. Чичинадзе. В. 3. т. 1 Теоретические основы. - М.: Машиностроение, 1989.- 400 с.
7.Хасуи А., Моригаки О. Наплавка и напыление. -М .: Машиностроение, 1985.240с.
УДК 629.083
ОБЕСПЕЧЕНИЕ НАДЕЖНОСТИ АВТОМОБИЛЕЙ В ПРОЦЕССЕ РЕМОНТА
В.И. Гурдин, д-р. техн. наук, профессор; А.В. Бердюгин, аспирант Сибирская государственная автомобильно-дорожная академия
Изучение надежности автомобилей и их агрегатов позволяет обосновано подходить к планированию производства по изготовлению новых деталей, используемых вместо негодных, и повышению долговечности деталей путем конструктивных и технологических мероприятий в процессе проектирования и изготовления, а при ремонте - к применению наиболее рациональных способов восстановления деталей и высококачественной сборки [1].
11

Рассмотрим причины, вызывающие снижение надежности отремонтированных автомобилей по сравнению с новыми, и пути ее повышения.
Взаключительной фазе капитального ремонта сборка автомобилей и их агрегатов производиться с использованием деталей, во-первых, с допустимым износом, имеющих различную остаточную долговечность, во-вторых, восстановленных разными способами, и имеющих различную приданную им долговечность, в-третьих, вновь изготовленных или из числа запасных, и имеющих примерно одинаковую сообщенную им долговечность.
Таким образом, надежность капитально отремонтированного автомобиля зависит от надежности каждого из основных агрегатов, отличающихся различной долговечностью, которая в свою очередь зависит от надежности огромного количества их деталей, имеющих различную долговечностью.
Впроцессе эксплуатации могут возникать в капитально отремонтированных автомобилях внезапные отказы, вызываемые увеличением внешних нагрузок, превышающих расчетные [2].
Таким образом, детали отремонтированных агрегатов автомобилей могут иметь не только отказы по причине естественного изнашивания (износные отказы), но и внезапные отказы, появляющиеся совместно.
Совместная вероятность безотказной работы деталей. Вероятность безотказной работы детали с учетом износных и внезапных отказов в период работы от начала эксплуатации (t = 0) отремонтированного автомобиля до следующего капитального ремонта (t = ТМ) определяется [3]
p(t) e t |
p(TM ) |
pb (t) pu (t) , |
(1) |
|
p(0) |
||||
|
|
|
где рв (t) - вероятность безотказной работы по внезапным отказам;
ри (t) - вероятность безотказной работы по износным отказам, которая определяется [3] как
|
|
|
1 |
|
|
|
|
(t t |
0 )2 |
dt , |
(2) |
|
pu |
(t) |
|
|
|
e |
2 2 |
||||||
|
|
|
||||||||||
|
|
|
|
|||||||||
|
2 |
|
|
|
||||||||
|
|
|
|
|
t |
|
|
|
|
|
где t0 - среднее значение долговечности детали.
Формулу (1) можно использовать только в случае t = 0, т.е. когда деталь новая или восстановленная, но впервые вступила в работу. Если же деталь уже использовалась и имеет наработку и величину износа (деталь с допустимым износом), то вероятность безотказной работы определяется [3]
p(t) e t |
pu (t, t) |
, |
(3) |
, |
|||
|
pu (t ) |
|
где t' - величина наработки.
Средняя долговечность агрегатов, собранных из деталей с допустимым износом без предварительного селективного подбора, меньше долговечности соответствующих агрегатов, собранных из новых деталей.
12
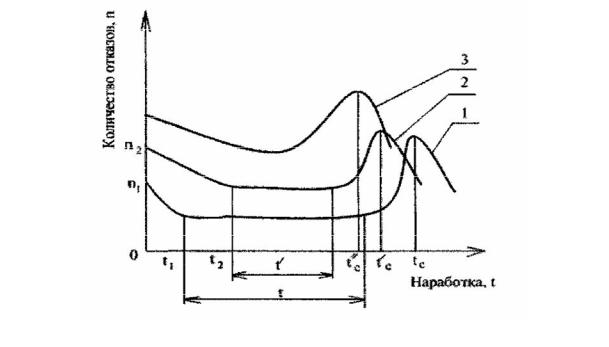
При достижении наработки t'+t0 долговечность деталей будет снижаться вследствие роста величины зазоров в сопряжениях из-за изнашивания.
Анализ распределения долговечности отремонтированных авто-
мобилей. На рис.1 показаны кривые распределения долговечности капитально отремонтированных автомобилей [3]: кривая 1-е выдерживанием требований технологического процесса: в условиях специализированного авторемонтного завода; кривая 2 - с несоблюдением этих требований; кривая 3 - в условиях автотранспортного предприятия.
Величины n1 и n2 характеризуют количество отказов, произошедших по причине капитального ремонта. Вследствие ряда технологических и организационных причин (нерациональный способ восстановления деталей, недостаточность контроля при сборке, отсутствие испытаний ряда узлов и агрегатов и т.д.) число отказов в первый период эксплуатации автомобиля, отремонтированного с несоблюдением требований технологического процесса и технических условий, является большим (кривая 2, см. рис. 1). Возникновение отказов в таком случае происходит в течение более длительного периода времени.
Рис. 1. Схема распределения долговечности отремонтированных автомобилей
Период нормальной эксплуатации, втечение которого производиться устранение возникающих отказов путем проведения технического обслуживания и ремонта автомобилей, становиться меньше по сравнению с периодом нормальной эксплуатации автомобилей, отремонтированных с соблюдением всех требований технологического процесса и технических ус-
ловий (t' <1).
Автомобили, отремонтированные в мелкосерийном ремонтном производстве, не располагающем современными средствами восстановления деталей, оборудованием и технологической оснасткой, имеют все показатели
13
работоспособности, значительно худшие, нежели автомобили, отремонтированные в специализированных ремонтных заводах (t" < t'с, см. рис.1). Участок возникновения отказов таких автомобилей (кривая 3, см. рис. 1) практически переходит в период весьма непродолжительной нормальной эксплуатации, переходящим в область внезапных и износных отказов, наступающих значительно раньше, чем у автомобилей, отремонтированных с отклонением от требований технологического процесса и технических условий (кривая 2, см. рис.1).
Следовательно, высокого качества и эксплуатационной надежности капитального отремонтированных автомобилей можно достичь на специализированных авторемонтных и агрегаторемонтных заводах при соблюдении технологическихпроцессов восстановления деталей и сборки узлов и агрегатов. При этом необходимо осуществление большого количества различных технологических мероприятий, направленно формирующих определенные эксплуатационные свойства восстанавливаемых деталей такие, как качество поверхности, износостойкость, усталостная прочность и обеспечивающих точность сборки.
Библиографический список
1.Малышев Г.А. Основные проблемы авторемонтного производства / Г.А. Малышев II Автомобильный транспорт. - 1993. - №7. - С. 40-42.
2.Расчет деталей машин и конструкций на прочность и долговечность I В.П. Когаев [и др.]. -М.: Машиностроение, 1985. - 224 с.
3.Масино М.А. Повышение долговечности автомобильных деталей при ремонте / М.А.
Масино. - М.: Транспорт, 1992. - 148 с.
УДК 669.14:620
ОЦЕНКА ЭКСПЛУАТАЦИОННОЙ НАДЕЖНОСТИ ДЕТАЛЕЙ ТРАНСПОРТНЫХ МАШИН
А.С. Дариенко, магистранка Сибирская государственная автомобильно-дорожная академия
Одно из важнейших направлений использования механики разрушения в оценке эксплуатационной надежности машин – оценка кинетики субкритического роста трещин в металлах и ресурса изделий при циклическом нагружении. Приемлемой для оценки кратковременной трещиностойкости пластичных металлов и сплавов является концепция критического развития трещин.
При оценке сопротивления хрупкому разрушению с использованием методов механики разрушения все же нельзя полностью решить проблему конструктивной прочности сплавов. В связи с этим необходимо развивать количественные методы оценки сопротивления зарождению трещин в изделиях с гладкой поверхностью, а также при наличии конструктивных
14
концентраторов напряжений с учетом напряженного состояния при статических испытаниях. Они должны быть в арсенале методов оценки характеристик эксплуатационной надежности и конструктивной прочности металлов и сплавов.
Известны работы по созданию аналитических методов оценки коэффициентов эффективности напряжений (КИН) в образцах и изделиях различной конфигурации, особенно решений для определения КИН в цилиндрических образцах с кольцевидной трещиной при испытаниях на изгиб и растяжение. Принимая во внимание высокую стесненность пластической деформации на контуре кольцевой трещины, а также сформулированные критерии автомодельности разрушения цилиндрических образцов, эти данные положены в основу оценки кратковременной трещиностойкости металлов и сплавов. Весьма перспективным оказалось использование интерполяционного подхода к определению КИН, позволяющего оценить их значения для изделий разнообразной конфигурации при практически произвольном характере контура развиваемой трещины.
Основной параметр кратковременной трещиностойкости сталей К1c - это вязкость разрушения. Этому параметру придается большое значение, как важному количественному показателю сопротивления сплавов хрупкому разрушению. Принято считать, что при повышении прочности сталей, достигаемом за счет увеличения содержания углерода, легирования или термического упрочнения, их трещиностойкость понижается.
Для повышения надежности деталей из стали 110Г13Л важное значение имеет увеличение их сопротивления хрупкому разрушению и необходимость снижения порога хладноломкости, что способствует также увеличению долговечности. Одним из реальных способов повышения надежности является уменьшение содержания фосфора в стали, подбор легирующих добавок. Испытания на циклическую трещиностойкость проводились по методике, изложенной в работе [1]. Длину трещины определяли с помощью двух световых микроскопов с ценой деления 0,05 мм. Образцы для испытания на усталость имеют размеры высотой 60мм с основаниями 60 и 15 мм и радиусом при вершине 5 мм. Для испытания на циклическую трещиностойкость использовали плоские образцы размером 6х55 мм с односторонним надрезом. Результаты усталостных испытаний показали существенное влияние легирования стали 110Г13Л на расположение кривых усталости, построенных по моменту появления трещины (длиной около 0,5мм). Так же результаты показали, что на процесс распространения трещины структура стали оказывает менее значительное влияние, чем на процесс накопления усталостных повреждений, предшествующий ее появлению.
Установлено так же, что распространению трещины в марганцовистых аустенитных сталях предшествует интенсивная пластическая дефор-
15
мация, сопровождающаяся появлением устойчивых полос скольжения и образованием субзерен.
Рост трещины в исследуемых сталях сопровождается интенсивно протекающим процессом ветвления магистральной трещины одной или нескольких сепаратных микротрещин, ориентированных в плоскости максимальных нормальных напряжений.
В следствии ликвации легирующих элементов (ванадий, молибден) и выделения карбидов по границам зерен, а также дефектов литья в стали 110Г13Л нередко наблюдаются участки с ослабленными границами зерен, по которым при циклическом нагружении образуется сетка трещин.
Все это должно учитываться при оценке надежности узлов машины, изготовленных из марганцовистых сталей.
Библиографический список
1. Леонтьев, А. Н. /Повышение конструктивной прочности машин на основе создания оптимального структурного состояния сплава./ А. Н. Леонтьев, Ю. К. Корзунин, В. П. Расщупкин.// Вестник академии военных наук, 2009. №3 (28). С. 355-356.
УДК 621.352.6
ПРЕДПОСЫЛКИ К УЛУЧШЕНИЮ СМАЗЫВАЮЩИХ СВОЙСТВ ДИЗЕЛЬНЫХ ТОПЛИВ
П.В. Дрюпин, аспирант Омский государственный аграрный университет
Впоследние 20-30 лет ведется активная работа, направленная на поиск топлив, способных в будущем заменить моторные топлива нефтяного происхождения, в частности дизельное топливо. Это связанно с ухудшением экологической обстановки и осознанием того факта, что мировые запасы нефти ограничены. На данный момент наибольшую популярность завоевали топлива растительного происхождения. К ним можно отнести натуральные растительные масла (рапсовое, соевое, кокосовое, пальмовое и т.п.) и биодизельное топливо, которое является продуктом переработки этих масел.
ВЕвропейских странах для производства топлив, наибольшей популярностью пользуется рапсовое масло, его жирно-кислотный состав представлен ниже см. (табл. 1) [2].
|
|
Таблица 1 |
|
|
Средний жирнокислотный состав рапсового масла |
||
|
|
|
|
Название кислот и химическая формула |
Рапсовое масло (состав, %) |
|
|
|
|
|
|
С 12:0 |
Лауриновая С12Н24О2 |
0,01 |
|
16 |
|
|

С 14:0 |
Миристиновая С14Н28О2 |
0,05 |
С 15:0 |
Пентадекановая С15Н30О2 |
0,02 |
|
|
|
С 16:0 |
Пальмитиновая С16Н32О2 |
4,75 |
С 16:1 |
Пальмитолеиновая С16Н30О2 |
0,2 |
С 17:0 |
Маргариновая С17 Н34О2 |
0,04 |
С 17:1 |
Маргаринолеиновая С17 Н32О2 |
0,06 |
С 18:0 |
Стеариновая С18Н36О2 |
1,9 |
С 18:1 |
Олеиновая С18Н34О2 |
59,53 |
С 18:2 |
Линолевая С18Н32О2 |
21,36 |
С 18:3 |
Линоленовая С18Н30О2 |
9,27 |
С 20:0 |
Арахиновая С20 Н40О2 |
0,67 |
С 20:1 |
Гонделиновая С20 Н38О2 |
1,35 |
|
|
|
С 20:2 |
Эйкозадиеновая С20 Н36О2 |
0,14 |
С 22:0 |
Бегеновая С22 Н44О2 |
0,06 |
С 22:1 |
Эруковая С22 Н42О2 |
0,15 |
С 24:0 |
Лигноцериновая С24 Н48О2 |
0,13 |
С 24:1 |
НервоноваяС24 Н46О2 |
0,12 |
Из таблицы 1 видно, что наибольшую концентрацию в рапсовом масле имеет олеиновая кислота.
В настоящее время известно большое количество способов производства биодизельного топлива из растительных масел. В основном все они основаны на переэтерификации триглицеридов масел одноатомными спиртами (метанол, этанол, бутанол и т.д.) в присутствии основных катализаторов (гидроксид натрия, калия). Реакция получения метиловых эфиров жирных кислот, т.е. биодизельного топлива (см. рис. 1).
Рис. 1. Реакция получения метиловых эфиров жирных кислот: 1 – молекула триглицерида (R – общее обозначение для радикалов жирных кислот); 2 – молекула метилового спирта; 3 – молекула глицерина; 4 – метиловый эфир жирной кислоты
Беря во внимание тот факт, что в рапсовом масле преобладает олеиновая кислота, дальнейшие рассуждения будут строиться на примере этой жирной кислоты.
Олеиновая кислота имеет следующую структурную формулу:
17
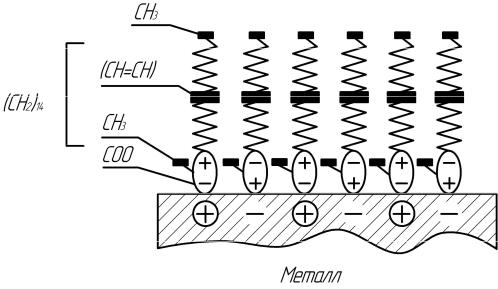
СН3 (СН2 )7 СН СН (СН2 )7 СООН |
(1) |
После прохождения реакции будет получен метиловый эфир олеино- |
|
вой кислоты: |
(2) |
СН3 (СН2 )7 СН СН (СН2 )7 СОО СН3 |
Использование в дизелях чистого рапсового масла затрудняется по причине его большей, по сравнению с дизельным топливом, вязкостью ( в 10 раз). В этой связи, наиболее предпочтительной заменой дизельному топливу является как раз метиловый эфир рапсового масла (биодизельное топливо). Эти эфиры обладают схожими физико-химическими свойствами с дизельным топливом. [1].
Молекула метилового эфира олеиновой кислоты обладает дифильным строением, то есть содержит, как полярную группу СОО, так и неполярный углеводородный радикал (СН2 )n , что относит ее к поверхностно-активным веществам (ПАВ). Эти ПАВ способны образовывать моно и полимолекулярные слои при адсорбции активных молекул на поверхности раздела фаз. В общем случае процесс адсорбции молекул метилового эфира олеиновой кислоты можно описать следующим образом: молекулы адсорбата, приближаясь из объема жидкости к поверхности раздела фаз, испытывают притяжение со стороны этой поверхности, обусловленное действием Ван- дер-ваальсовых сил, и постепенно эта поверхность покрывается адсорбированным слоем молекул см. (рис. 2) [5].
Рис. 2. Схема ориентации молекул метилового эфира олеиновой кислоты при адсорбции на поверхности металла
Полученный мономолекулярный слой резко отличается по своим свойствам от вещества в объеме. Этот слой имеет низкую сдвиговую прочность и большое сопротивление сжатию. Малая толщина образующегося мономолекулярного слоя не может препятствовать упругой и пластической
18

деформации контактирующих тел, но сдвиг происходит именно в этом слое, а не в основном материале, что способствует уменьшению потерь на трение, снижает износ и предотвращает заедание пар трения [3].
От 30 до 50% отказов дизелей приходиться на топливную аппаратуру, из них до 50% - на форсунки и 20-30% на плунжерные пары и нагнетательные клапана [4]. Так как прецизионные детали топливной аппаратуры при работе смазываются дизельным топливом, то повышение его качества является первостепенной задачей. Решение этой задачи позволит повысить надежность работы, как топливной аппаратуры, так и дизеля в целом.
Беря во внимание все вышесказанное об адсорбции полярных молекул и образовании мономолекулярных слоев, обладающих определенными специфическими свойствами, можно предположить, что использование метилового эфира рапсового масла в качестве добавки к дизельному топливу будет способствовать повышению смазывающих свойств последнего. Степень повышения смазывающих свойств полученных смесей будет зависеть от активности молекул и их концентрации в объеме. При низкой концентрации полярных молекул, образующийся адсорбционный слои, изза менее плотной упаковки молекул, будет иметь более низкие трибологические свойства (рис. 3).
Рис. 3. Схема ориентации молекул метилового эфира олеиновой кислоты при малой их концентрации в объеме
Варьируя процентное содержание биодизельного топлива можно добиться улучшения смазывающих свойств, одновременно сохраняя мощностные и экономические показателей дизеля. В итоге это должно привести к повышению долговечности прецизионных деталей топливной аппаратуры. В заключении хотелось бы еще отметить и тот факт, что добавление биодизельного топлива позволит снизить токсичность отработавших газов дизелей, повысив тем самым экологические качества дизельного топлива.
19