
переработка
.pdfvk.com/club152685050 | vk.com/id446425943
между термическим крекингом и каталитическим гидрокрекингом, так называемых гидротермических процессов. Их проводят в среде водорода, но без применения катализаторов гидрокрекинга. Очевидно, что гидротермические процессы будут несколько ограничены глубиной гидропереработки, но лишены ограничений в отношении содержания металловвТНО.Дляниххарактернысредниемеждутермическимкрекингом и гидрокрекингом показатели качества продуктов и капитальных
иэксплуатационных затрат. Аналоги современных гидротермических процессов использовались еще перед Второй мировой войной для ожижения углей, при этом содержащиеся в них металлы частично выполняли роль катализаторов гидрокрекинга. К гидротермическим процессам можно отнести гидровисбрекинг, гидропиролиз, дина-крекинг
идонорно-сольвентный крекинг.
Гидровисбрекинг имеет сходство как с висбрекингом, так и с каталитическимгидрокрекингом,очемсвидетельствуетназваниепроцесса. Процессосуществляютбезкатализаторасрециркуляциейводородапри примерно тех же температуре и времени контакта, что и гидрокрекинг. Процесс проводят без значительного коксообразования только при высоком давлении, поскольку при этом увеличивается растворимость водорода в нефтяных остатках и скорость реакций гидровисбрекинга. Так, процесс гидровисбрекинга фирмы «Лурги» осуществляется при температуре 380…420°С и давлении 12…15 МПа. Степень превращения гудронасоставляет60…66%мас.Процессиспытанвмасштабепилотной установки. Данных по их материальному балансу и качеству продуктов не сообщается.
В настоящее время в БашНИИ НП разработан отечественный вариант гидровисбрекинга. В результате проведенных на пилотной установке исследований на гудроне западно-сибирской нефти установлено, что процесс целесообразно проводить при следующих оптимальных значениях технологических параметров: температура — 500°С, давление — 5 МПа, кратность циркуляции водорода — 750 нм3/нм3 сырья и объемная скорость сырья — 0,3 ч–1. Получен следующий материальный баланс процесса,% маc.: газ — 11,0; бензин — 6,3; легкий газойль (160...340°С)—25,2иостаток>340°С—53,5.Потреблениеводородасо- ставляет около 1% маc. Остаток гидровисбрекинга (> 340°С) содержит 1,2% маc. серы (в исходном гудроне 2,3% маc.) и может использоваться как котельное топливо М100 (ВУ80 °С = 16).
Гидропиролизпроводят, как и термический пиролиз, при повышенных температуре (> 500°С) и давлении (> 10 МПа) и времени контакта от нескольких секунд до одной минуты, но в среде водорода. Одной
804
vk.com/club152685050 | vk.com/id446425943
из модификаций гидропиролиза является процесс дина-крекинг, разработанный фирмой «Хайдрокарбон Рисерч».
Дина-крекингпозволяет перерабатывать разнообразное остаточное сырьесвысокойкоксуемостьюибольшимсодержаниемметаллов,азота и серы. Процесс проводят в трехсекционном реакторе с псевдоожиженным слоем и внутренней рециркуляцией инертного микросферического адсорбента. В верхней секции реактора при температуре примерно 540°С и давлении около 2,8 МПа осуществляют собственно гидропиролиз тяжелого сырья. Носитель с осажденным коксом через зону отпаривания подают в нижнюю секцию реактора, где проводят газификацию кокса парокислородной смесью при температуре около 1000°С
собразованием водородсодержащего газа (смесь СО и Н2). Последний через отпарную секцию поступает в верхний слой теплоносителя, обеспечивая необходимую для протекания реакций гидропиролиза (гидрокрекинга) концентрацию водорода. Таким образом, в данном процессе гидротермолиз сырья осуществляют без подачи водорода извне. Регенерированныйтеплоноситель-адсорбентдалеепневмотранспортом подают в верхнюю секцию реактора.
Процесс дина-крекинга характеризуется высоким выходом газов
смалымсодержаниемолефиновибензина,заметнымгидрообессериваниемдистиллятовигидрированиемдиенов.Примерныйматериальный баланс процесса при переработке гудрона калифорнийской нефти по варианту с рециркуляцией средних дистиллятов (в% мас.) следующий:
топливный газ — 32,5 , нафта (С5–204°С) — 43,3; средние дистилляты
(204…371°С) — 4,4, тяжелые дистилляты (> 371°С) — 24,3. Действует демонстрационная установка мощностью около 250 тыс. т/год. Предполагается строительство промышленной установки мощностью около 2,6 млн т/год.
Донорно-сольвентные процессы основаны на использовании тех-
нологии, применявшейся ранее для ожижения углей, а в 1950-х гг. — в процессе «Варга» (ВНР). Это — гидрокрекинг средних дистиллятов в присутствии донора водорода и катализатора одноразового пользования.ВнастоящеевремяразличнымифирмамиСШАиКанадыразработано несколько вариантов донорно-сольвентных процессов под разны- миназваниями:донорно-сольвентныйвисбрекинг(«Лурги»),донорная переработка битуминозных углей («Галф Канада»), донорно-сольвент- ный крекинг («Петро-Канада»), донорный висбрекинг («Эксон») и др. В этих процессах ТНО смешивают с растворителем (сольвентом) — донором водорода, в качестве которого чаще используют фракции нафтеновых углеводородов, реже — чистые нафтены (например, тетралин),
805
vk.com/club152685050 | vk.com/id446425943
которые обладают способностью легко подвергаться каталитическому гидрированию. Таким образом, смешиваемый компонент выполняет одновременнодвефункции:хорошегорастворителятяжелыхнефтяных остатков и донора водорода.
В донорно-сольвентном процессе фирмы «Галф Канада» гудрон (>500°С) тяжелой или битуминозной нефти смешивают с донором водорода при давлении 3,5…5,6 МПа и подают в трубчатую печь, где нагревают до температуры 410…460°С, и далее — в выносной реактор (кокинг-камера), где выдерживают в течение определенного времени. Продукты донорно-сольвентного крекинга затем подвергают фракционированиювсепаратореиатмосфернойколонненагаз,нафтуисредние дистилляты. Последние после гидрирования в специальном блоке по обычнойтехнологиивприсутствиистандартныхкатализаторовподают нарециркуляциювкачестведонораводорода.Остатокатмосфернойколонны направляют на вакуумную перегонку с получением вакуумного газойля и остатка. На пилотной установке донорно-сольвентного крекинга гудрона получен следующий выход продуктов,% мас: газ — 5,2; нафта — 23,7; атмосферный газойль — 7,7; вакуумный газойль — 30; вакуумный остаток — 33,1.
8.5.12.Краткие сведения об экстракционных процессах облагораживания моторных топлив
Наряду с гидрокаталитическими процессами в нефтепереработке достаточно широкое применение нашли экстракционные процессы
сцелевым назначением деформатизации топливных фракций, а также извлечениеизнихсероорганическихсоединений,преждевсегосульфидов. Сероорганические соединения, содержащиеся в нефтях, в гидрокаталитических процессах превращаются в сероводород и углеводороды ипреимущественносжигаютсякаксоставнаячастьтоплив,загрязняяатмосферу.Болееэффективноихизвлечениеииспользованиедляпроизводстваконцентратовсульфидов,сульфоксидовисульфонов,которыемогут применятьсявомногихобластяхпромышленности,ипреждевсеговгидрометаллургииприобогащениимногихредкихиблагородныхметаллов.
Всвязи с ужесточением экологических требований к моторным топливам по содержанию в них ароматических углеводородов практический интерес представляет применение экстракционных процессов
сцелью деароматизации бензолсодержащих фракций катализаторов риформинга, гидроочищенных реактивных и дизельных топлив. Экономической эффективности комбинированных гидрокаталитических и экстракционных процессов облагораживания топливных фракций
806
vk.com/club152685050 | vk.com/id446425943
будет благоприятствовать использование выделенных ароматических концентратов как ценного нефтехимического сырья.
Экстракционная деароматизация головной фракции катали-
зата риформинга. Процесс разработан и внедрен в ПО «Киришнефтеоргсинтез». В качестве экстрагента используется смесь ТЭГ и 15% сульфолана. Массовое соотношение экстрагент : сырье (6,5…8) : 1. Экстракция осуществляется при комнатной температуре. Степень извлечения аренов составляет 96…98%, в т.ч. бензола — более 99%.
Экстракционная деароматизация реактивного топлива. Как наиболее эффективный экстрагент в этом процессе используется смесь ацетонитрила и н-пентана. Массовое соотношение растворитель ацетонитрил : сырье — 3 : 1, пентан : сырье — 1 : 1. Содержание аренов в сырье 20%, в рафинате ≈10%. Выход рафината — 87%. Ароматический концентрат процесса рекомендован для использования в качестве растворителя типа «Нефрас». Высота некоптящего пламени рафината повысилась с 19 до 30 мм. Как достоинство процесса можно отметить одновременную десульфиризацию реактивного топлива, прежде всего удаление бензотиофенов, трудноудаляемых при гидроочистке.
Экстракционноеоблагораживаниедизельнойфракции.Вкачестве наиболее эффективного экстрагента рекомендована смесь полярного расворителя метилцеллозольфа (2-метоксиэтанол) и неполярного — пентана. Температура экстракции — 30°С. Массовое соотношенеи экстрагента — метилцеллозольф:сырье — 5:1, пропан:сырье — 1:1.
Содержание агентов снижается от 25% в сырье до ≈10% в рафинате. Степень извлечения сернистых соединений составляетс 50%. Легче всего экстрагируются трудноудаляемые в процессах гидроочистки гомологи тиофена.
8.6.Особенности конструкций технологического оборудования гидрокаталитических процессов
Наиболее сложным оборудованием и аппаратурой гидрокаталитических процессов оснащены реакторные блоки гидроочистки и риформинга. Наиболее важными аппаратами являются реакторы, а также многокамерные печи. Остальное оборудование (теплообменники, ки- пятильники,конденсаторы-холодильникиидр.)аналогичноприменяе- мому в нефтепереработке. Особенностью работы оборудования и аппаратуры реакторных блоков являются высокие температура и давление, а также присутствие водорода при жестком режиме.
Реакторы установок гидроочистки и каталитического риформинга работают в условиях химической и электрохимической коррозии,
807
vk.com/club152685050 | vk.com/id446425943
а также механического износа металла аппаратов катализатором. Химическая коррозия реакторов обусловлена содержанием в высокотемпературных газовых потоках сероводорода и водорода, а электрохимическая коррозия — содержанием в циркулирующих дымовых газах регенерации паров воды и двуокиси серы.
Сероводородная коррозия металла аппаратов реакторного блока установок тем сильнее, чем больше концентрация серы в сырье и чем выше содержание сероводорода в циркулирующем газе.
Водород, циркулирующий в системе реакторного блока, вызывает межкристаллитную коррозию металла, сопровождающуюся снижением его прочности и увеличением хрупкости. Межкристаллитное растрескивание, образование раковин и вздутий в металле оборудования под действием водорода усиливаются при повышении температуры и давления в системе.
Сульфиднаякоррозияпрактическипротекаеточеньмедленно,однако продукты коррозии засоряют катализатор, забивают поры между таблетками,атакжетрубытеплообменников,чтонарушаеттехнологический режим процесса гидроочистки, ухудшает теплопередачу и приводиткнедопустимомувозрастаниюгидравлическогосопротивления.По возникновению большого перепада давления между входом в реактор и выходом из него часто судят о степени сульфидной коррозии.
Реактор и катализатор засоряются также из-за присутствия в газовых потоках кислорода, хлоридов и азотсодержащих соединений. Кислород способствует окислению сернистых соединений, поэтому его концентрация в циркулирующем газе должна быть ограничена (0,0002…0,0006%). Хлориды и азотсодержащие соединения при взаимодействии с водородом образуют соответственно хлористый водород и аммиак, которые, связываясь, превращаются в хлористый аммоний, выпадающий в виде осадка. Осадок удаляют периодической промывкой, для чего в процессе эксплуатации установки по ходу продуктов реакции от реактора до сепаратора в систему впрыскивают воду. Промывку продолжают до тех пор, пока перепад давления не уменьшится до значения, определенного технологической картой.
8.6.1. Реакторы гидроочистки дизельных топлив
Каталитическую гидроочистку дизельных топлив применяют для уменьшения содержания в них серы до 0,2%мас. и ниже, для повышения их термической стабильности и улучшения других свойств. Процессгидроочисткисопровождаетсяреакцияминасыщенияолефиновых углеводородов и деструктивной гидрогенизации сернистых, кислород-
808
vk.com/club152685050 | vk.com/id446425943
ных и азотных соединений с образованием парафиновых углеводородов, сероводорода, воды и аммиака.
Гидроочистка осуществляется в присутствии водородсодержащего газа при температуре 360…425°С и давлении 2…5 МПа: Степень обессеривания и глубина гидрирования непредельных соединений повышаютсясростомтемпературыидавленияпроцесса,атакжесувеличением кратности циркуляции водородсодержащего газа. Для ускорения процесса применяют различные катализаторы, однако особенно часто — алюмокобальтомолибденовый таблетированный катализатор.
Реакции гидрирования протекают с выделением тепла, избыток которого отводят с помощью хладоагентов (холодного циркуляционного газа, сырья или гидрогенизата).
На отечественных заводах гидроочистку дизельных топлив сернистых нефтей осуществляют на двухблочных установках, реакторные блоки которых работают следующим образом. Сырье после смешения с очищенным циркуляционным газом и свежим техническим водородом нагревают сначала в теплообменниках, затем в трубчатой печи (до 360…380°С) и направляют в реакторы. По мере снижения активности катализатора температуру подогрева сырья повышают. При этом необходимоследитьзатем,чтобымаксимальнаятемпературавзонереакции не превышала 435°С. В противном случае ускоряется закоксовывание поверхностикатализатораиповышаетсягазообразование, являющееся результатом термического крекинга сырья.
Газопродуктовый поток, представляющий собой смесь паров гидрогенизата, газов реакции, сероводорода и циркуляционного газа, поступает из реакторов в сепаратор после предварительного охлаждения
втеплообменникахисекционныххолодильникахдо50°С.Всепараторе смесьгазовипаровпридавлении4,5МПа,разделяетсянагидрогенизат и циркуляционный газ, которые далее перерабатывают в соответствующих аппаратах.
Отработанныйкатализаторвконцереакциисодержит10…13%(мас.) кокса и до 7% мас. серы. Активность катализаторавосстанавливают путем окислительной газовоздушной регенерации. Перед регенерацией систему продувают под давлением 0,8 МПа инертным газом, который затем удаляют из аппарата через вытяжную трубу. Газы регенерации содержат до 0,2% об. двуокиси серы. Процесс восстановления катализатораначинаютсвыжиганиякоксагазамипритемпературе420…430°С и давлении 4 МПа и заканчивают прокаливанием катализатора
втечениечетырехчасовпритемпературе520…550°Сидавлении2МПа. Чтобы сохранить прочность металла коммуникационных труб при
809

vk.com/club152685050 | vk.com/id446425943
Рис.8.16. Политропический реактор установки гидроочистки дизельных топлив: 1 — корпус; 2 — футеровка; 3 —катализа- тор; 4 — опорное кольцо; 5 – штуцеры для термопары;6—выводгазосырьевойсмеси; 7 — днище; 8 — нижний штуцер; 9 — муфта для манометра; 10 — ввод охлаждающего газа; 11 — опора; 12 — штуцер для предохранительного клапана; 13 — воздушник; 14 — люк; 15 — штуцер ввода газосырьевой смеси; 16 — съемная колосниковая решетка; 17 — опорный перфорированный лист
высокой температуре, давление в процессе прокаливания постепенно снижают. Продолжительность выжигания составляет 48…60 ч в зависимости от количества кокса и серы.
Общая продолжительность цикла регенерации катализатора равна 100…150 ч, поэтому данную операцию совмещают во времени с плано- во-предупредительными ремонтами. Периодичность регенерации определяется качеством сырья и глубиной очистки топлива и составляет от трех месяцев до двух лет.
Реакторы устанавливают на железобетонных постаментах таким образом, чтобы обеспечить выгрузку катализатора самотеком через соответствующие люки.
На рис. 8.16 показан политропический(многослойный,многосекционный)реакторустановкигидроочистки дизельных топлив. Он представляет собойвертикальныйцилиндрический аппаратдиаметром1400ммивысотой 14000ммсэллиптическимиднищами. Корпус реактора изготовлен из двухслойной стали 12ХМ + ОХ18Н10Т толщиной 40 мм, штуцеры — из стали Х5М. Изнутри корпус футеруют жаропрочным торкрет-бетоном толщиной обычно 125…200 мм. Футеровка должна быть монолитной и состоять из двух слоев: термоизоляционного
— непосредственно у корпуса и эрозионностойкого — внутреннего.
Состояние футеровки проверяют путемизмерениятемпературыстенок корпуса аппарата поверхностными термопарами.
810
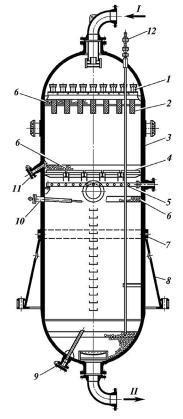
vk.com/club152685050 | vk.com/id446425943
Превышение допустимой температуры (200°С) свидетельствует о нарушении герметичности футеровки на данном участке.
Внутри аппарата имеется шесть съемных колосниковых решеток, на которые насыпан таблетированый алюмокобальтомолибденовый катализатор. Колосники устанавливают на кольцевые опоры, приваренные к корпусу реактора. Все внутренние устройства аппарата выполнены из стали ОХ18Н10Т.
Над каждым слоем катализатора расположен маточник из хромоникелевых труб для подачи охлаждающего циркуляционного газа. Это
позволяет поддерживать в каждой секции |
|
|
необходимую температуру с постепен- |
|
|
ным повышением ее по ходу парогазо- |
|
|
вой смеси. Таким образом, в любой сек- |
|
|
ции протекает адиабатический процесс, |
|
|
а в реакторе в целом — политропический. |
|
|
Таблетированный катализатор в ко- |
|
|
личестве 12 м3 загружают в аппарат через |
|
|
верхний люк диаметром 450 мм, на крыш- |
|
|
ке которого имеется воздушник для отво- |
|
|
да продувочных газов. Над блоком реак- |
|
|
торовсооружаютспециальныеплощадки. |
|
|
С них катализатор по гибкому рукаву |
|
|
засыпают в соответствующую секцию |
|
|
(снизу вверх), где рабочий, находящийся |
|
|
внутри аппарата, соблюдая требования |
|
|
техники безопасности для работы в за- |
|
|
крытых сосудах выравнивает вручную |
|
|
слой катализатора. Газо-сырьевая смесь |
|
|
поступает в верхнюю секцию по штуцеру |
|
|
в верхней части аппарата, последователь- |
|
|
но проходит через слой катализатора во |
|
|
всех секциях и по штуцеру под нижней |
|
|
секцией выводится из реактора. |
|
|
Другим типом реактора для гидроо- |
Рис. 8.17. Реактор гидроочистки |
|
чистки дизельного топлива является ре- |
дизельного топлива с аксиальным |
|
движением сырья: |
||
акторсаксиальнымдвижениемсырья. |
1 — распределительная тарелка; 2 — |
|
Реактор гидроочистки дизельного то- |
фильтрующее устройство; 3 — корпус; |
|
4 — решетка колосниковая;5—коллек- |
||
плива с аксиальным движением сырья |
тор для ввода пара; 6 — фарфоровые |
|
шары; 7 —опорное кольцо; 8 — опора; |
||
(рис. 8.17) имеет корпус 3, изолирован- |
||
9,11—штуцердлявыгрузкикатализато- |
||
ный снаружи. В реакторе размещены два |
ра; 10, 12 — термопары. Потоки: I — сы- |
|
рье; II —продукты реакции |
811
vk.com/club152685050 | vk.com/id446425943
слоя катализатора, через которые сверху вниз проходит сырье. Каждый слой катализатора защищен от динамического воздействия потока среды слоем фарфоровых шаров 6.
Вверхней части реактора установлена распределительная тарелка 1
спатрубками, под которой размещено фильтрующее устройство 2, состоящее из цилиндрических корзин, погруженных в слой катализатора. Корзины сварены из прутка и обтянуты сбоку и снизу сеткой. Сверху корзины открыты. В корзинах и верхней части слоя катализатора задерживаются продукты коррозии и механические примеси.
Верхний слой катализатора поддерживается колосниковой решеткой 4, на которой уложены два слоя сетки и слой фарфоровых шаров. Впространствемеждуверхниминижнимслоямикатализаторанаходится коллектор 5 для ввода пара. В нижней части реактора размещен слой фарфоровых шаров, служащих опорой для нижнего слоя катализатора иобеспечивающийравномерныйвыводпродуктовреакцииизаппарата. Вверхнемднищеимеютсятриштуцерадляустановкимногозонныхтермопар12,контролирующихтемпературноеполевслоекатализатора,крометого,предусмотренатермопаравсреднейчастиреактора.Катализатор выгружаетсяизверхнегослоячерезштуцер11встенкеаппарата,изнижнего слоя через дренажную трубу и штуцер в нижнем днище 9. В стенке реакторамеждуверхниминижнимслоямикатализатораустановленлюк. В нижней части имеются скобы для удобства обслуживания и ремонта.
8.6.2. Реакторы каталитического риформинга
Реактор(рис.8.18)представляетсобойцилиндрическийвертикальный сосудсшаровымиднищами.При525°Си2…4МПаводородспособствует развитию водородной коррозии металла, вызывающей его трещины ивздутия.Поэтомуи длятеплоизоляции изнутриметаллическуюстенку реактора защищают футеровкой из торкрет-бетона.
Кроме того, внутри реактора устанавливают стальной перфорированный стакан, между стенкой которого и стенкой аппарата имеется газовый слой. Нарушение футеровки приводит к перегреву и разрушению стенки реактора. Поэтому необходимо постоянно контролировать температуру внешней поверхности металла при помощи наружных термопар (не выше 150°С). Для изготовления корпуса и днища реактора применяют сталь марки 09Г2ДТ со специальной закалкой поверхности аппарата или сталь 12ХМ. Внутренняя арматура реактора и присоединительные фасонные патрубки изготовлены из легированных сталей.
На первых установках каталитического риформинга применяли реакторы с аксиальным (вдоль оси аппарата) движением газо-сырьевого
812

vk.com/club152685050 | vk.com/id446425943
Рис. 8.18. Схема реакторов установки с аксиальным вводом сырья:
а — для гидроочистки сырья; б — для риформинга; 1 — зональная термопара; 2 — наружная термопара; 3 — футеровка; 4 — корпус; 5 — фарфоровые шары. Линии: I — сырье; II — продукты реакции; III - выгрузка катализатора; IV — вывод продуктов при эжектировании системы во время регенерации катализатора
потока. Реакторы блока гидроочистки и риформинга (рис. 8.18а) имеют верхнийштуцердлявводаинижний—длявыводапродуктов.Восталь- ныхреакторахриформингаштуцерыдлявводасырьяивыводапродукта находятсявверхуаппарата(рис.8.18б).Катализаторзагружаютваппараты через верхний штуцер и выгружают через нижний. Каждый аппарат оборудован штуцерами для выхода паров при эжектировании системы во время регенерации катализатора. Из-за большого перепада давления (1,3…1,5МПа)вреакторахсаксиальнымдвижениемпотока,впоследнее времясталиприменятьреакторысрадиальнымдвижениемгазо-сырьево- гопотока(реакционнаясмесьдвижетсявреакторечерезслойкатализато-
813