
переработка
.pdfvk.com/club152685050 | vk.com/id446425943
обычновадиабатическомреакторебезотводатеплареакций,поскольку температурный градиент обычно не превышает 10°С.
В реакторах установок гидрообессеривания и гидрокрекинга высококипящих фракций с повышенным содержанием гетеропримесей предусматривается отвод тепла реакций подачей охлажденного ВСГ через распределительные устройства между слоями катализатора.
Регенерация катализатора. В процессе эксплуатации катализатор постепенно теряет свою активность в результате закоксовывания и отложения на его поверхности металлов сырья. Для восстановления первоначальной активности катализатор подвергают регенерации окислительнымвыжигомкокса.Взависимостиотсоставакатализатора применяют газовоздушный или паровоздушный способ регенерации. Цеолитсодержащие катализаторы гидрообессеривания и гидрокрекинга нельзя подвергать паровоздушной регенерации.
Газовоздушную регенерацию обычно проводят смесью инертного газа с воздухом при температуре до 530°С. При этом регенерируемый катализатор ускоряет реакции горения кокса.
Паровоздушную регенерацию проводят смесью, нагретой в печи до температуры начала выжига кокса. Смесь поступает в реактор, где происходит послойный выжиг кокса, после чего газы сбрасывают в дымовую трубу.
8.4.5.Промышленные процессы гидрооблагораживания дистиллятных фракций
Промышленные установки гидрогенизационной переработки нефтяного сырья включают следующие блоки: реакторный, сепарации газопродуктовой смеси свыделением ВСГ, очисткиВСГ от сероводорода, стабилизации гидрогенизата, компрессорную. Установки гидрокрекинга имеют дополнительно фракционирующую колонну.
Установки имеют много общего по аппаратурному оформлению и схемам реакторных блоков, различаются по мощности, размерам аппаратов, технологическому режиму и схемам секций сепарации и стабилизации гидрогенизатов. Установки предварительной гидроочистки бензинов — сырья каталитического риформинга — различаются также вариантом подачи ВСГ: с циркуляцией или без циркуляции – «на проток». На всех остальных типах установок применяется только циркуляционная схема подачи ВСГ.
Схему подачи ВСГ «на проток» применяют только на комбинированных установках гидроочистки и каталитического риформинга (со стационарным слоем катализатора и проводимого под повышенным
774

vk.com/club152685050 | vk.com/id446425943
давлением водорода) прямогонных бензинов с пониженным содержанием сернистых соединений (< 0,1% мас.). Такая схема предусматривает «жесткую связь» по водороду между каталитическим риформингом и гидроочисткой. По этой схеме весь ВСГ риформинга под давлением процесса подают в реакторы гидроочистки. Схема удобна в эксплуатации и более проста по аппаратурному оформлению.
ВсхемесциркуляциейВСГлегкоподдерживатьпостоянноесоотношение водород : сырье. Наличие циркуляционного компрессора позволяетвзависимостиоткачествакатализатораисырья,концентрацииводородавВСГрегулироватьтребуемуюкратностьциркуляцииВСГ,дает возможность проводить газовоздушную регенерацию катализаторов.
Напромышленныхгидрогенизационныхустановкахприменяютдва способа сепарации ВСГ из газопродуктовой смеси: холодная (низкотемпературная) и горячая (высокотемпературная) (рис. 8.11а, б).
|
|
|
|
|
|
|
|
||
|
|
|
|
|
|
|
|
|
|
|
|
|
||
|
|
|
|
|
|
|
|
|
|
|
|
|
|
|
|
|
|
|
Рис. 8.11. Схемы холодной (а) и горячей (б) сепарации ВСГ:
СВД — сепараторы высокого и низкого давления; ГС и ХС — горячий и холодный сепараторы
Холодная сепарация ВСГ применяется на установках гидроочистки бензиновых, керосиновых и иногда дизельных фракций; заключается в охлаждении газопродуктовой смеси, отходящей из реакторов гидроочистки, сначала в теплообменниках, затем в холодильниках (воздушныхиводяных)ивыделенииВСГвсепараторепринизкойтемпературе и высоком давлении. В сепараторе низкого давления выделяют низкомолекулярные углеводородные газы.
Горячую сепарацию ВСГ применяют преимущественно на установках гидрообессеривания высококипящих фракций нефти: дизельных топлив, вакуумных газойлей, масляных дистиллятов и парафинов. Газопродуктовуюсмесьпослечастичногоохлаждениявтеплообменниках подают в горячий сепаратор; выделяемые в нем ВСГ и углеводородные газы охлаждают до низкой температуры в воздушных и водяных холодильниках и далее направляют в холодный сепаратор, где отбирают ВСГ с достаточно высокой концентрацией водорода.
Схема холодной сепарации (а) ВСГ, по сравнению с горячей (б), обеспечиваетболеевысокуюконцентрациюводородавВСГ.Основным
775

vk.com/club152685050 | vk.com/id446425943
достоинством варианта горячей сепарации является меньший расход как тепла, так и холода.
Различиевприменяемыхнагидрогенизационныхустановкахсхемах стабилизации гидрогенизатов (отпаркой водяным паром при низком давленииилиподогретымводородсодержащимгазомприповышенном, сподогревомнизастабилизационнойколонныгорячейструейчерезпечь илирибойлером;применительнокгидрообессериваниюмасляныхдис- тиллятов—сдополнительнойразгонкойподвакуумом)обусловливает- ся фракционным составом сырья, ресурсами ВСГ и водяного пара и т.д.
На НПЗ применяют следующие два варианта регенерации насыщенного раствора моноэтаноламина — абсорбента сероочистки ВСГ от H2S: непосредственно на самой установке гидрооблагораживания либо централизо-ванную регенерацию в общезаводском узле. Основным аппаратом гидрогенизацион-
ных установок является реактор со стацио-
нарным слоем катализатора.
Рис. 8.12. Реактор гидроочистки дизельного топлива:
1 — корпус; 2 — распределитель и гаситель потока; 3 — распределительная непровальная тарелка; 4 — фильтрующее устройство; 5 — опорная колосниковая решетка; 6 — коллектор ввода водорода; 7 — фарфоровые шары; 8 —термо- пара
Двухсекционныйреакторагидроочистки дизельного топлива (рис. 8.12) представляет собой вертикальный цилиндрический аппарат с эллиптическими днищами. Корпусреактораизготавливаютиздвухслойной стали 12ХМ и 08Х18Н10Т. Верхний слой катализатора засыпают на колосниковую решетку, а нижний — на фарфоровые шарики,которымизаполняютсферическуючасть нижнего днища. Для отвода избыточного тепла реакций под колосниковой решеткой вмонтирован коллектор для подачи холодного ВСГ. Сырье, подаваемое через штуцер в верхнем днище, равномерно распределяют по всему сечению и сначала для задерживания механических примесей пропускают через фильтрующие устройства, состоящие из сетчатых корзин, погруженные в верхний слой катализатора. Промежутки между корзинами заполняют фарфоровыми шарами. Газосырьевую смесь пропускают через слой катализатора в обеих секциях и по штуцеру нижней секции выводят из реактора.
776
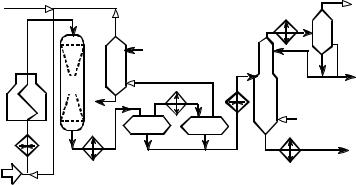
vk.com/club152685050 | vk.com/id446425943
Гидроочистку прямогонных бензиновых фракций осуществляют на секциях гидроочистки установок каталитического риформинга или комбинированных установок ЛК-6у.
Длягидроочисткиреактивныхтопливиспользуютспециализиро-
ванныеустановкитипаЛ-24-9РТ,атакжесекциигидроочисткиКУЛК-6у.
Гидроочистку прямогонных дизельных фракций проводят на установках типа Л-24-6, Л-24-7, ЛЧ-24-7, ЛЧ-24-2000 и секциях гидроочистки КУ ЛК-6у (табл. 8.15).
Принципиальнаятехнологическаясхемаустановкигидроочистки дизельного топлива ЛЧ-24-2000 приведена на рис. 8.13. Цирку-
ляционный ВСГ смешивают с сырьем, смесь нагревают в сырьевых теплообменниках и в трубчатой печи П-1 до температуры реакции и подают в реактор Р-1. После реактора газопродуктовую смесь частично охлаждают в сырьевых теплообменниках (до температуры 210…230°С) и направляют в секцию горячей сепарации ВСГ, состоящую из сепараторов С-1 и С-2. ВСГ, выводимый из холодного сепаратора С-2, после очистки МЭА в абсорбере К-2подают на циркуляцию. Гидрогенизаты горячего и холодного сепараторов смешивают и направляют на стабилизационную колонну К-1, где подачей подогретого в П-1 отдувочного ВСГ из очищенного продукта удаляют углеводородные газы и отгон (бензин).
|
|
|
|
|
|
|
|
|
|
|
|
|
|
|
|
|
|
|
|
|
|
|
|
|
|
|
|
|
|
|
|
|
|
|
|
|
|
||
|
|
|
|
|
|
|
|
Рис. 8.13. Принципиальная технологическая схема установки гидроочистки дизельного топлива ЛЧ-24-2000:
I — сырье; II — свежий ВСГ; III — гидрогенизат; IV — бензин; V — углеводородный газ на очистку; VI — отдувочный ВСГ; VII — регенерированный МЭА; VIII — раствор МЭА на регенерацию
Ниже приводится материальный баланс установок гидроочистки бензина (I), керосина (II), дизельного топлива (III) и гидрообессеривания вакуумного дистиллята — сырья каталитического крекин-
га (IV).
777

vk.com/club152685050 | vk.com/id446425943
|
I |
II |
III |
IV |
Взято,%: |
|
|
|
|
сырье |
100,00 |
100,00 |
100,00 |
100,00 |
водород 100%-й на реакцию* |
0,15 |
0,25 |
0,40 |
0,65 |
всего |
100,15 |
100,25 |
100,40 |
100,65 |
Получено,%: |
|
|
|
|
гидроочищенное топливо |
99,00 |
97,90 |
96,90 |
86,75 |
дизельная фракция |
— |
— |
— |
9,2 |
отгон |
— |
1,10 |
1,3 |
1,3 |
углеводородный газ |
0,65 |
0,65 |
0,60 |
1,5 |
сероводород |
— |
0,20 |
1,2 |
1,5 |
потери |
0,5 |
0,4 |
0,4 |
0,4 |
всего |
100,15 |
100,25 |
100,40 |
100,65 |
* Общий расход с учетом потерь на растворение.
Таблица 8.15 — Основные режимные параметры и показатели
промышленных установок гидроочистки дизельных топлив
Показатель |
Л-24-6 |
Л-24-7 |
Секция |
ЛЧ-24- |
|
ЛЧ-24-7 |
ГО ЛК-6у |
2000 |
|||
Мощность по сырью, тыс. т/год: |
900 |
1200 |
2000 |
2000 |
|
проектная |
|||||
1200…1500 |
1500…2000 |
2000 |
2000 |
||
фактическая |
|||||
|
|
|
|
||
Давление в реакторе, МПа |
2,8…3,7 |
2,8…4,0 |
5,2…5,5 |
|
|
5,0 |
|||||
Температура в реакторе,°С |
340…400 |
340…400 |
350…400 |
360…400 |
|
Кратность циркуляции ВСГ, м3/м3 |
250…300 |
200…350 |
350…500 |
|
|
250 |
|||||
Объемная скорость сырья, т–1 |
3…5 |
3…5 |
4,3 |
4,5 |
|
Выход стабильного гидрогенизата, |
|
|
|
|
|
% мас. |
95,3 |
97,0 |
95,3 |
97 |
|
Содержание серы,% мас.: |
|
|
|
|
|
|
|
|
|
||
в сырье |
0,6…1,6 |
0,6…1,6 |
0,6…1,6 |
0,8 |
|
в гидрогенизате |
0,1…0,2 |
0,1…0,2 |
0,12…0,16 |
0,15 |
|
|
|
|
|
|
Расход водорода,% мас.
Количество потоков
Тип реактора аксиальный
Тип сепарации
Способ стабилизации
Наличие секции регенерации МЭА
0,4 |
0,35 |
0,42 |
0,4 |
1 |
|
|
|
2 |
1 |
1 |
|
|
|
|
|
БиметалФутероБиметалБиметал- лический ванный лический лический
Г |
X |
X |
Г |
|
ВСГ |
ВСГ |
Водяной |
ВСГ |
|
пар |
||||
|
|
|
||
+ |
|
— |
|
|
+ |
+ |
|||
|
|
|
|
778

vk.com/club152685050 | vk.com/id446425943
Гидроочистка вакуумных дистиллятов. Вакуумные дистилляты являются традиционным сырьем для процессов каталитического крекинга и гидрокрекинга. Качество вакуумных газойлей определяется глубинойотбораичеткостьюректификациимазута.Вакуумныегазойли 350...500°Спрактическинесодержатметаллоорганическихсоединений и асфальтенов, а их коксуемость обычно не превышает 0,2%. С повышением tк.к. до 540...560°С коксуемость возрастает в 4...10 раз, содержание металлов — в 3...4 раза, серы — на 20...45%. Влияние содержащихся в сырье металлов, азотистых соединений и серы проявляется в снижении активности работы катализатора за счет отложения кокса и необратимого отравления металлами.
Гидроочистка вакуумного газойля 350...500°С не представляет значительных трудностей и проводится в условиях и на оборудовании, аналогичных применяемым для гидроочистки дизельных топлив. При давлении 4...5 МПа, температуре 360...410°С и объемной скорости сы- рья1...1,5ч–1 достигается89...94%-яглубинаобессеривания;содержание азота снижается на 20...30%, металлов — на 75...85%, а коксуемость — на 65...70%. Гидроочистку тяжелых дистиллятов деструктивных процессов (коксования, висбрекинга) обычно проводят в смеси с прямогонными дистиллятами в количестве до 30%.
Гидроочистка масляных рафинатов применяется в основном для осветления и улучшения их стабильности против окисления; одновременно уменьшается их коксуемость и содержание серы (глубина обессеривания — 30...40%); индекс вязкости несколько увеличивается (на 1...2 единицы); температура застывания масла повышается на1...3°С.Выходбазовыхмаселдистиллятныхиостаточныхрафинатов составляет более 97% мас.
Типовые установки гидроочистки масел и парафинов (типа Г-24/1 производительностью 360 тыс. т/год) включают до пяти технологическихпотоков.Установкигидроочисткимаселотличаютсяотгидроочистки дизельных топлив только способом стабилизации гидрогенизата: отгонкауглеводородныхгазовипаровбензинаосуществляетсяподачей водяного пара; затем стабильное масло подвергается осушке в вакуумной колонне под давлением 13,3 кПа.
Технологический режим процесса гидроочистки масляных рафинатов следующий:
Катализатор |
АКМ или АНМ |
Температура в реакторе,°С |
280…325 |
Давление в реакторе, МПа |
3,5…4,0 |
779
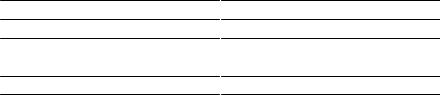
vk.com/club152685050 | vk.com/id446425943
Объемная скорость подачи сырья, ч–1 |
1,5…3,0 |
Кратность циркуляции ВСГ, м3/м3 |
|
для дистиллятного рафината |
250…300 |
остаточного |
500…600 |
Содержание Н2 в ВСГ,% об. |
75…85 |
8.4.6. Процессы гидрооблагораживания нефтяных остатков
Всовременной мировой нефтепереработке наиболее актуальной
исложной проблемой является облагораживание (деметаллизация, деасфальтизация и обессеривание) и каталитическая переработка (каталитический крекинг, гидрокрекинг) нефтяных остатков — гудронов
имазутов, потенциальное содержание которых в нефтях большинства месторождений составляет 20…55%.
Наиболее важными из показателей качества нефтяных остатков как сырья для каталитических процессов, их облагораживания и переработки являются содержание металлов (определяющее степень дезактивации катализатора и его расход) и коксуемость (обусловливающая коксовую нагрузку регенераторов каталитического крекинга или расход водорода в гидрогенизационных процессах). Именно эти показатели были положены в основу принятой за рубежом классификации остаточных видов сырья для процессов каталитического крекинга. По содержанию металлов и коксуемости в соответствии с этой классификацией нефтяные остатки подразделяют на следующие четыре группы:
Группа |
Коксуемость, |
Содержание металлов, |
|
% мас. |
г/т (ррm) |
I |
менее 5 |
Менее 10 |
II |
5…10 |
10…30 |
III |
10…20 |
30…150 |
IV |
Более 20 |
Более 150 |
I.Высококачественное сырье (например, мазут мангышлакской или грозненской нефтей). Его можно перерабатывать без предварительной подготовки на установках ККФ лифтреакторного типа с пассивацией металлов и отводом тепла в регенераторах.
II.Сырье среднего качества. Его можно перерабатывать на установках ККФ последних моделей с двухступенчатым регенератором и отводом избытка тепла без предварительной подго-
780
vk.com/club152685050 | vk.com/id446425943
товки,ноприповышенномрасходеметаллостойкогокатализатора и с пассивацией отравляющего действия металлов сырья.
III и IV. Сырье низкого качества (например, мазуты и гудроны запад- но-сибирской,ромашкинскойиарланскойнефтей).Каталити- ческаяихпереработкатребуетобязательнойпредварительной подготовки — деметаллизации и деасфальтизации.
Вышеприведенная классификация нефтяных остатков применима и для характеристики качества сырья гидрокаталитических процессов, однако применительно к этим процессам важнее содержание металлов, чем коксуемость.
Для переработки мазутов в малосернистое котельное топливо предложены и реализованы следующие методы «непрямого» гидрообессеривания:
—вакуумная (или глубоковакуумная) перегонка мазута с последующим гидрообессериванием вакуумного (глубоковакуумного) газойляисмешениепоследнегосгудроном(содержаниесерывкотельном топливе 1,4…1,8%);
—вакуумная перегонка мазута и деасфальтизация гудрона с последующим обессериванием вакуумного газойля и деасфальтизата и смешение их с остатком деасфальтизации (содержание серы в котельном топливе 0,4–1,4%);
—вакуумная перегонка мазута и деасфальтизация гудрона с последующим гидрообессериванием вакуумного газойля и деасфальтизата и их смешение (содержание серы в котельном топливе составит 0,2…0,3%), остаток деасфальтизации подвергается газификации или раздельной переработке с получением битумов, пеков, связующих, топливного кокса и т.д.
Для обеспечения глубокой безостаточной переработки нефти необходимы либо прямое гидрообессеривание нефтяных остатков с ограниченным содержанием металлов с использованием нескольких типов катализаторов, либо каталитическая переработка с предварительной деметаллизацией и деасфальтизацией гудронов.
Современные зарубежные промышленные установки гидрообессеривания нефтяных остатков различаются между собой в основном схемами реакторных блоков, и по этому признаку можно подразделить их на следующие варианты:
1)гидрообессеривание в одном многослойном реакторе с использованием в начале процесса крупнопористых металлоемких катализаторов и затем — катализаторов с высокой гидрообессеривающей активностью;
781
vk.com/club152685050 | vk.com/id446425943
2)гидрообессериваниевдвух-иболееступенчатыхреакторахсостаци- онарным слоем катализатора, из которых головной (предварительный) реактор предназначен для деметаллизации и деасфальтизации сырья на дешевых металлоемких (часто нерегенерируемых) катализатоpax, а последний (или последние) — для гидрообессеривания деметаллизированного сырья;
3)гидрообессеривание в реакторе с трехфазным псевдоожиженным слоем катализатора. Псевдоожиженный слой позволяет обеспечить болееинтенсивноеперемешиваниеконтактирующихфаз,изотермический режим реагирования и поддержание степени конверсии сырья и равновесной активности катализатора на постоянном уровне за счет непрерывного вывода из реактора части катализатора и замены его свежим или регенерированным. Однако из-за существенных недостатков, таких как большие габариты и масса толстостенных реакторов, работающих под высоким давлением водорода, сложность шлюзовой системы ввода и вывода катализаторов, большие капитальные и эксплуатационные расходы, процессы гидрообессеривания и гидрокрекинга в псевдоожиженном слое не получили до сего времени широкого распространения в нефтепереработке.
Из промышленно освоенных процессов оригинальным, наиболее технологически гибким и достаточно эффективным является процесс гидрообессеривания тяжелых нефтяных остатков «Хайвал», разработанный Французским институтом нефти. Принципиальная технологическая схема представлена на рис. 8.14.
Реакторный блок установки состоит из поочередно работающих защитных реакторов Р-1а и Р-1б, двух последовательно работающих основных реакторов Р-2 и Р-3 глубокой гидродеметаллизации и двух последовательноработающихреакторовгидрообессериванияР-4иР-5. ЗащитныереакторыР-1аиР-1бработаютврежимевзаимозаменяемос- ти: когда катализатор в работающем реакторе потеряет свою деметаллизирующую активность, переключают на другой резервный реактор без остановки установки. Продолжительность непрерывной работы реакторов составляет: защитных — 3…4 месяца, а остальных — 1 год.
Исходное сырье (мазуты, гудроны) смешивают с ВСГ, реакционную смесьнагреваютвпечиП-1дотребуемойтемпературыипоследователь- ноподаютвзащитныйиосновныереакторыгидродеметаллизациииреакторы гидрообессеривания. Продукты гидрообессеривания подвергаютгорячейсепарациивгорячемихолодномгазосепараторах,далеестабилизации и фракционированию на атмосферных и вакуумных колоннах. Как катализатор используют модифицированный гидрирующими
782
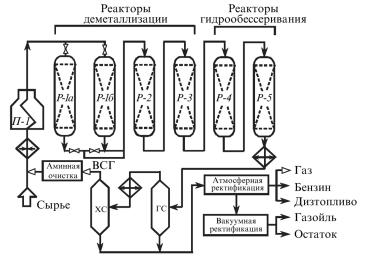
vk.com/club152685050 | vk.com/id446425943
Рис. 8.14. Принципиальная технологическая схема установки гидрообессеривания нефтяных остатков ФИН
металлами оксид алюминия, обладающий высокой металлоемкостью (катализаторимеетшероховатуюповерхностьспорамивформе«ежа»).
8.5. Каталитические процессы гидрокрекинга нефтяного сырья
Гидрокрекинг — каталитический процесс переработки нефтяных дистиллятов и остатков при умеренных температурах и повышенных давлениях водорода на полифункциональных катализаторах, обладающих гидрирующими и кислотными свойствами (а в процессах селективного гидрокрекинга — и ситовым эффектом).
Гидрокрекинг позволяет получать с высокими выходами широкий ассортимент высококачественных нефтепродуктов (сжиженных газов С3–С4, бензина, реактивного и дизельного топлив, компонентов масел) практически из любого нефтяного сырья путем подбора соответствующих катализаторов и технологических условий и является одним из экономически эффективных, гибких и наиболее углубляющих нефтепереработку процессов.
В современной нефтепереработке реализованы следующие типы промышленных процессов гидрокрекинга:
1)гидрокрекинг бензиновых фракций с целью получения легких изопарафиновых углеводородов, представляющих собой ценное сырье для производства синтетического каучука, высокооктановых добавок к автомобильным бензинам;
783