
переработка
.pdfvk.com/club152685050 | vk.com/id446425943
Таблица 6.1 — Влияние группового углеводородного состава
вакуумного газойля на выход продуктов крекинга (катализатор цеолитсодержащий, температура 538°С)
Выход |
|
Сырье |
|
|
|
|
|
продуктов крекинга,% об. |
парафиновое |
нафтеновое |
аромати- |
|
|
|
ческое |
Сухой газ (C1–C2 + Н2) * |
2,6 |
3,2 |
3,4 |
Сжиженный газ С3–С4 |
34,5 |
27,5 |
24,3 |
|
|
|
|
Бензин С3–221 °С |
73 |
70 |
54,2 |
|
|
|
|
Легкий газойль |
5 |
10 |
20 |
Тяжелый газойль |
2 |
5 |
10 |
Кокс * |
4,8 |
5,4 |
6,3 |
* Массовый выход. |
|
|
|
К компонентам, обратимо дезактивирующим катализаторы крекинга,относятполициклическиеароматическиеуглеводороды,смолы,асфальтеныиазотистыесоединениясырья.Обобратимойдезактивирующейспособностисырьяможносудитькосвеннопоплотности,аколи- чественно—пококсуемости,определяемойпоКонрадсону.Какправило, чем выше коксуемость сырья, тем больше выход кокса на катализаторе.
Обычно на установках каталитического крекинга преимущественно перерабатывают типовое сырье (вакуумный газойль 350…500 °С) с коксуемостью не более 0,3…0,5% мас. Если регенератор имеет запас мощности по массе сжигаемого кокса, то может быть использовано сырье с коксуемостью до 2…3% мас. На специальных установках, предназначенных для крекинга остаточного сырья и имеющих системы отвода тепла из регенератора, допускается коксуемость сырья до 5% мас.
Обратимыми ядами для алюмосиликатных катализаторов являются азотистые основания: они прочно адсорбируются на кислотных активных центрах и блокируют их. При одинаковых основных свойствах большее дезактивирующее воздействие на катализатор оказываютазотистыесоединениябольшеймолекулярноймассы.Послевыжига кокса активность отравленного азотистыми основаниями катализатора полностью восстанавливается. Цеолитсодержащие катализаторы, благодаря молекулярно-ситовым свойствам, отравляются азотом в значительно меньшей степени, чем аморфные алюмосиликатные.
Металлоорганические соединения, содержащиеся преимущественно в высококипящих и особенно остаточных фракциях нефти, относят
644
vk.com/club152685050 | vk.com/id446425943
к необратимо дезактивирующим компонентам сырья крекинга.
Блокируя активные центры катализатора, они отрицательно влияют не только на его активность, но и на селективность. Так, по мере увеличения содержания никеля и ванадия, являющихся, как известно, дегидрирующими металлами, в продуктах крекинга интенсивно возрастает выход водорода и сухих газов, а выход бензина существенно снижается.
На установках каталитического крекинга, на которых не предусмотрены специальные приемы по улавливанию или пассивации отравляющего действия металлов, содержание их в сырье нормируется не более 2 г/т.
Для переработки сырья с коксуемостью более 10% мас. и содержанием металлов 10…30 г/т и более требуется обязательная его предварительная подготовка.
6.4.3.Подготовка (облагораживание) сырья каталитического крекинга
С целью снижения содержания металлов и коксогенных компонентов в сырье до такой степени, чтобы его последующая каталитическая переработка была бы более экономична, т.е. при умеренных габаритах регенератора и без чрезмерного расхода дорогостоящего катализатора, осуществляется его подготовка.
Из процессов облагораживания сырья каталитического крекинга в настоящее время широко применяется каталитическая гидроочистка преимущественно вакуумных газойлей и более тяжелого сырья с ограниченным содержанием металлов.
К сырью гидрогенизационных процессов, по сравнению с каталитическим крекингом, не предъявляется столь жестких ограничений по коксуемости, поскольку скорости коксообразования в этих процессах несопоставимы. Однако по содержанию металлов к сырью обоих процессов предъявляются практически одинаковые ограничения, поскольку металлы сырья одинаково необратимо дезактивируют как металлические центры, так и кислотные центры катализаторов.
Необходимо отметить следующие достоинства комбинированной каталитической переработки с предварительной гидроочисткой сырья крекинга:
—существенно снижается содержание сернистых и азотистых соединений во всех жидких продуктах каталитического крекинга и содержание оксидов серы в газах регенерации, в результате отпадает необходимость в их облагораживании и снижаются выбросы вредных газов в атмосферу;
645
vk.com/club152685050 | vk.com/id446425943
—полициклические ароматические углеводороды и смолы сырья при гидроочистке подвергаются частичному гидрокрекингу с образованием алкилароматических углеводородов с меньшим числом колец, врезультатеснижаетсякоксообразованиевпроцессекаталитического крекинга;
—существенно снижается содержание металлов в гидроочищенном сырье, что снижает расход катализаторов крекинга;
—при каталитическом крекинге гидроочищенного сырья (табл. 6.2) увеличивается выход целевых (более высокого качества) продуктов и снижается выход газойлей и кокса.
Таблица 6.2 — |
Влияние гидроочистки на материальный баланс |
|||||
|
|
каталитического крекинга вакуумных газойлей |
||||
|
|
|
|
|
|
|
|
|
|
Фракция 350…500°С |
Фракция 350…580°С |
||
|
|
|
|
|
||
Выход продуктов, % мас. |
исходная, |
гидроочи- |
исходная, |
гидроочи- |
||
|
|
|
S = 1,6% |
щенная, |
S = 1,7% |
щенная, |
|
|
|
S = 0,2% |
S = 0,32% |
||
Газ до С4, |
|
|
18,7 |
20 |
21,9 |
19,5 |
в т.ч. |
С1–С2 |
|
3,4 |
2,7 |
5,9 |
3,1 |
|
∑С3 |
|
6,1 |
7 |
6,8 |
5,8 |
|
∑С4 |
|
9,3 |
10,3 |
9,2 |
10,6 |
Бензин С5–195°С |
|
40,1 |
46,7 |
38,6 |
42,9 |
|
Легкий газойль (195…270°С) |
5,7 |
4,5 |
7,2 |
12,2 |
||
|
|
|
|
|
||
Тяжелый газойль (>270°С) |
28,3 |
23 |
24,5 |
17,9 |
||
|
|
|
|
|
|
|
Кокс и потери |
|
7,2 |
5,8 |
7,8 |
7,5 |
|
|
|
|
|
|
|
|
Кнедостаткам комбинированной переработки следует отнести увеличение капитальных и эксплуатационных затрат и возможность переработки сырья с ограниченным содержанием металлов.
Кнекаталитическим процессам подготовки сырья к каталитическому крекингу (а также гидрокрекингу) не предъявляются таковые ограничения по содержанию металлов, что позволяет значительно расширить ресурсы сырья за счет вовлечения остаточных видов сырья. Но они характеризуются повышенными капитальными и эксплуатационными затратами, из-за чего сдерживается их широкое применение
всовременной нефтепереработке.
Из внедренных в промышленном масштабе в нефтепереработке методов некаталитической подготовки остаточных видов сырья следует отметить процессы сольвентной и термоадсорбционной деасфальтизации и деметаллизации.
646
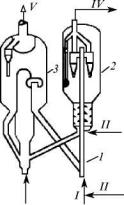
vk.com/club152685050 | vk.com/id446425943
Сольвентная деасфальтизация с использованием в качестве раство- рителейпропана,бутана,пентанаилилегкогобензина(С5–С6)основана на технологии подобной пропановой деасфальтизации гудронов, применяемой в производстве смазочных масел. В этих процессах наряду с деасфальтизацией и обессмоливанием достигаются одновременно деметаллизация, а также частичное обессеривание и деазотирование тяжелых нефтяных остатков (ТНО), что существенно облегчает последующую их каталитическую переработку. Как более совершенные ирентабельныеможноотметитьпроцессы«РОЗЕ»фирмы«Керр-Мак- ти» и «Демекс» фирмы «ЮОП», проводимые при сверхкритических температуре и давлении, что значительно снижает их энергоемкость,
атакже процесс «Добен» (деасфальтизация бензином), разработанный сотрудниками БашНИИ НП, в котором использование в качестве растворителя легкой бензиновой фракции позволяет снизить кратность растворитель : ТНО, уменьшить размеры аппаратов, потребление энергии и, следовательно, капитальные и эксплуатационные затраты.
Впроцессах термоадсорбционной деасфальтизации (ТАД) облагораживание ТНО достигается за счет частичных термодеструктивных превращений углеводородов и гетеросоединений сырья и последующей адсорбции образовавшихся смол, асфальтенов и карбоидов,
атакже металлов, сернистых и азотистых
соединений на поверхности дешевых адсорбентов. В отличие от сольвентной деасфальтизации, в процессах ТАД ТНО не образуется такого трудноутилизируемого продукта, как асфальтит.
Извнедренныхвнефтепереработкупромышленных процессов ТАД ТНО следует отметить установку APT, а из рекомендо- ванныхквнедрению—процессы3Dфирмы Барко, АКО ВНИИНП.
APT – процесс ТАД ТНО с высокими коксуемостью и содержанием металлов, разработан в США и пущен в 1983 г. в эксплуатацию мощностью около 2,5 млн т/год. Процесс осуществляется на установке, аналогичной установке каталитического крекинга с лифт-реактором (рис. 6.1).
Реакторный блок установки APT состоит из лифт-реактора 1 с бункером-отстой-
Рис. 6.1. Схема реакторного блока установки АРТ:
1 — лифт-реактор; 2 — бункер-от- стойник;3—регенератор;I—сырье; II — водяной пар; III — воздух; IV — продукты ТАД; V — дымовые газы
647
vk.com/club152685050 | vk.com/id446425943
ником 2, где при температуре 480…590 °С и очень коротком времени контакта асфальтены и гетеросоединения частично крекированного сырья сорбируются на специальном широкопористом микросферическом адсорбенте (арткат) с малыми удельной поверхностью и каталитической активностью; регенератора 3, в котором выжигается кокс, отлагающийся на адсорбенте. В процессе APT удаление металлов достигает свыше 95%, а серы и азота — 50…85%, при этом реакции крекинга протекают в минимальной степени (адсорбент не обладает крекирующей активностью). Примерный выход (в% об.) продуктов APT при ТАД гудронасоставляет:газыС3–С4 —3…8;нафта—13…17;легкийгазойль— 13…17; тяжелый газойль — 53…56 и кокс — 7…11% мас. Смесь легкого итяжелогогазойлейснезначительнымсодержаниемметалловявляется качественным сырьем каталитического крекинга, где выход бензина достигает более 42% мас. (табл. 6.3).
Таблица 6.3 — Показатели работы различных процессов подготовки
остаточного сырья для каталитического крекинга
|
Гидро- |
Сольвентная |
|
ТАД |
|||
|
обессе- |
деасфальтизация гудрона |
|||||
Показатель |
гудрона |
||||||
ривание |
|
|
|
|
|||
|
|
|
|
|
АРТ |
||
|
мазута |
пропаном |
бутаном |
|
Розе |
||
|
|
|
|||||
|
|
|
|
|
|
|
|
Выход облагороженного |
|
|
|
|
|
|
|
продукта: |
|
|
|
|
|
|
|
% мас. |
— |
45 |
81 |
|
80 |
71,3 |
|
% об. |
— |
— |
— |
|
82,8 |
— |
|
Плотность, г/см3: |
|
|
|
|
|
|
|
сырья |
— |
0,969 |
0,969 |
|
1,002 |
0,953 |
|
продукта |
— |
0,89 |
0,937 |
|
0,995 |
— |
|
Коксуемость,% мас.: |
|
|
|
|
|
|
|
сырья |
— |
16,4 |
16,4 |
|
20,8 |
9 |
|
продукта |
— |
1,6 |
7,1 |
|
13 |
6,9 |
|
Содержание Ni+V, г/т: |
|
|
|
|
|
|
|
в сырье |
41,5 |
80 |
80 |
|
90,8 |
102 |
|
в продукте |
1,5 |
2,5 |
14 |
|
29 |
9,5 |
|
Содержание серы, % мас.: |
|
|
|
|
|
|
|
в сырье |
1,5 |
4 |
4 |
|
4 |
1,6 |
|
в продукте |
0,1 |
2,5 |
3,5 |
|
3,6 |
0,85 |
Вслучаеприменениянекаталитическихпроцессовоблагораживания ТНОвозможнатрехступенчатаяпереработкаостаточногосырьяпосхеме: деасфальтизация гудрона (сольвентная или термоадсорбционная) →гидрообессеривание смеси деасфальтизата и вакуумного газойля → каталитический крекинг гидрогенизата.
648
vk.com/club152685050 | vk.com/id446425943
Целевым назначением процесса 3D (дискриминационной деструктивной дистилляции) является подготовка нефтяных остатков (тяжелых нефтей, мазутов, гудронов, битуминозных нефтей) для последующейкаталитическойпереработкипутемжесткоготермоадсорбционного крекинга в реакционной системе с ультракоротким временем контакта (доли секунды) циркулирующего адсорбента (контакта) с нагретым диспергированным сырьем. В отличие от APT в процессе 3D вместо лифт-реактора используется реактор нового поколения, в котором осуществляется исключительно малое время контакта сырья с адсорбентом на коротком горизонтальном участке трубы на входе в сепаратор циклонного типа. Эксплуатационные испытания демонстрационной установки показали, что выход и качество продуктов 3D выше, чем у процесса APT.
Процесс АКО (адсорбционно-контактная очистка) разрабатывался во ВНИИНП в 1980–1990-х гг. и испытан в широком масштабе, предназначен для глубокой очистки нефтяных остатков от нежелательных примесей;поаппаратурномуоформлениюреакционнойсистемы(лифтреакторного типа) аналогичен процессу APT. В качестве адсорбента используется природный мелкозернистый каолин (Аl2О3 ·2SiO2 ·2Н2О). Типичный режим процесса: массовая скорость подачи сырья — 20 ч–1; время контактирования — 0,5 с; температура в реакторе — 520°С. Врезультатеочисткимазутапроисходитудалениетяжелыхметалловна 95…98%, серы — на 35…45, азота — на 50…60, а коксуемость снижается на 75…80% мас. Процесс АКО характеризуется низкими выходами газа и бензина (5…6 и 6…8% мас. соответственно ) и высокими выходами газойлевой фракции (порядка 80% мас.). Выход кокса составляет 125% от коксуемости сырья по Кондрадсону. Тяжелый газойль и широкая газойлевая фракция являются качественным сырьем каталитического крекинга после предварительной гидроочистки. Применяемый в процессе адсорбент позволяет полностью исключить выбросы оксидов серы с газами регенерации.
6.4.4. Катализаторы крекинга
Катализаторы современных крупнотоннажных процессов каталитического крекинга, осуществляемых при высоких температурах (500…800 °С)врежимеинтенсивного массоитеплообменаваппаратах с движущимся или псевдоожиженным слоем катализатора, должны обладать не только высокими активностью, селективностью и термостабильностью,ноиудовлетворятьповышеннымтребованиямкнимпорегенерационным,механическиминекоторымдругимэксплуатационным
649
vk.com/club152685050 | vk.com/id446425943
свойствам. Промышленные катализаторы крекинга представляют собой в этой связи сложные многокомпонентные системы, состоящие:
1)из матрицы (носителя);
2)активного компонента — цеолита;
3)вспомогательных активных и неактивных добавок.
Матрицакатализаторовкрекингавыполняет функции как носи-
теля — поверхности, на которой затем диспергируют основной активный компонент — цеолит и вспомогательные добавки, так и слабого кислотного катализатора предварительного (первичного) крекирования высокомолекулярного исходного нефтяного сырья. В качестве материала матрицы современных катализаторов крекинга преимущественно применяют синтетический аморфный алюмосиликат с высокой удельной поверхностью и оптимальной поровой структурой, обеспечивающей доступ для крупных молекул крекируемого сырья.
Аморфные алюмосиликаты являлись основными промышленными катализаторами крекинга до разработки цеолитсодержащих катализаторов.Синтезируютсяонипривзаимодействиирастворов,содержащих оксиды алюминия и кремния, например жидкого стекла Na2O·3SiO2 и сернокислого алюминия Al2(SO4)3. Химический состав аморфного алюмосиликата может быть выражен формулой Na2O(Al2O3 ·xSiО2) где х — число молей SiO2 на 1 моль Al2O3. Обычно в промышленных аморфных алюмосиликатах содержание оксида алюминия находится в пределах 6…30% мас.
Аморфные алюмосиликаты обладают ионообменными свойствами, адляприданиякаталитическойактивностиобрабатываютихраствором сернокислогоалюминиядлязамещениякатионовNa+ наАl3+.Высушенные и прокаленные аморфные алюмосиликаты проявляют протонную и апротонную кислотности. При этом по мере повышения температуры прокаливанияпроисходитпревращениепротонныхкислотныхцентров в апротонные.
Активнымкомпонентомкатализаторовкрекингаявляетсяцеолит,
которыйпозволяетосуществлятьвторичныекаталитическиепревращенияуглеводородовсырьясобразованиемконечныхцелевыхпродуктов.
Цеолиты (от греч. цео — кипящий, литос — камень) представляют собой алюмосиликаты с трехмерной кристаллической структурой следующей общей формулы:
Me2/nO·Аl2О3 ·xSiO2 ·уН2О ,
где n — валентность катиона металла Me; х — мольное соотношение оксидов кремния и алюминия, называемое силикатным модулем; у — число молей воды.
650
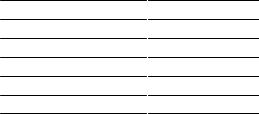
vk.com/club152685050 | vk.com/id446425943
В настоящее время насчитывается несколько десятков разновидностей природных и синтетических цеолитов, отличающихся структурой, типомкатионовMe,силикатныммодулемичисломмолекулкристаллизационной воды. Структура цеолитов характеризуется наличием большого числа полостей, соединенных между собой окнами, или микроканалами, размеры которых сравнимы с размерами реагирующих молекул. Обычно полости имеют больший диаметр, чем каналы (или окна). Например, в цеолите типа шабазит имеется 3·1020 полостей диаметром 11,4Å, в каждую полость которого может поместиться 24 молекулы воды. Диаметр окон шабазита составляет 4,9Å. При нагреве цеолита вода удаляется и образуется ячеистая структура. Удельная поверхность цеолитов достигает 700…1000 м/г. Обезвоженные цеолиты способны избирательноадсорбироватьмолекулыразличныхвеществвзависимости от размеров каналов. Разумеется, если диаметр адсорбируемого вещества больше, чем сечение канала, то оно не может проникнуть во внутренние поры цеолита (ситовой эффект). Так, при диаметре канала (окна) 4Åцеолит не может адсорбировать углеводороды нормального строения, диаметр молекул которых равен =4,9Å.
Обычнотипструктурысинтетическогоцеолитаобозначаютбуквами латинского алфавита А, X, Y, ... L и т.д. Перед буквами ставят химическуюформулукатионаметалла,компенсирующегоотрицательныйзаряд алюминия в алюмосиликате. Например, СаХ означает цеолит типа X в кальциевой обменной форме; LaY, ReY — соответственно лантановая и редкоземельная форма цеолита Y.
Принято подразделять цеолиты в зависимости от величины силикатного модуля х на следующие структурные типы:
Тип цеолита |
х |
Цеолит А |
1,8…2,0 |
Цеолит X |
2,3…3,0 |
Цеолит Y |
3,0…6,0 |
Эрионит (цеолит Т) |
6,0…7,0 |
Морденит |
8,3…10,7 |
Цеолит L |
10,0…35,0 |
За рубежом цеолиты классифицируют иначе: перед буквой, обозначающей тип цеолита, ставят цифру, соответствующую максимальному диаметру молекул (в ангстремах), адсорбируемых данным цеолитом. ПоэтойклассификациицеолитуNaAсоответствуетцеолит4А,цеолиту СаА — 5А, цеолиту NaX — 13Х, цеолиту СаХ — 10Х и т.д.
651
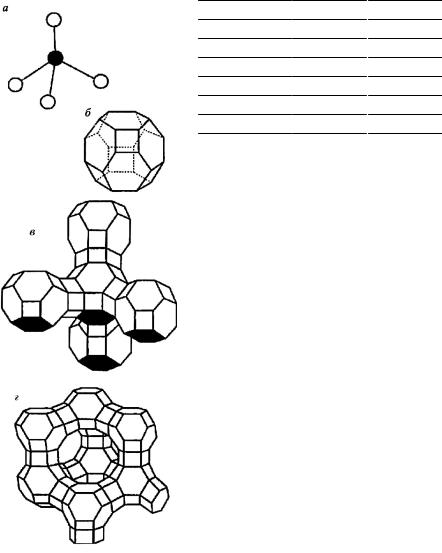
vk.com/club152685050 | vk.com/id446425943
Ниже приводим размеры полостей и окон для некоторых синтетических цеолитов:
Рис. 6.2. Строение цеолитов типа фожазита:
а — тетраэдр; б — содалитовая клетка; в — суперклетка; г — элементарная ячейка
Цеолит |
Диаметр |
|
|
полости |
окон |
||
|
|||
LiA |
12 |
4,4 |
|
Na |
11…12 |
4,0 |
|
КА |
11 |
3,3 |
|
СаА |
11 |
5,0 |
|
NaXиNaY |
11…13 |
9,0 |
|
СаХиСаY |
11…13 |
8,0 |
|
Са-морденит |
7 |
4,0 |
|
Н-морденит |
7 |
6,6 |
Цеолиты типа А, имеющие малые размеры окон (3,3…5 Å) и небольшой силикатный модуль (1,8…2,0), как правило, не используются в каталитических процессах и применяются в качестве адсорбентов. В каталитических процессах, в том числе крекинга нефтяного сырья, наибольшее применение нашли цеолиты типа X и Y — оба аналоги природного фожазита. В последние годы широкое распространение получают высококремнеземные трубчатые цеолиты L с силикатным модулем более 30 (напри-
мер, ZSM).
Первичной основой (структурной единицей) кристаллической решетки цеолитов X и Y является тетраэдр, состоящий из четырех анионов кислорода, которые окружены значительно меньшими по размерам ионами кремния или алюминия (рис. 6.2а). 24 тетраэдра образуют вторичную структурную единицу — усеченный октаэдр (кубооктаэдр, который содержит восемь шестиугольных и шесть квадратных поверхностей), так называемую содалитовую клетку
652
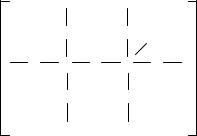
vk.com/club152685050 | vk.com/id446425943
(рис. 6.2б). На следующей ступени структурирования четыре кубооктаэдра объединяются в тетраэдрическую конфигурацию вокруг пятого при помощи шестиугольных призм, образуя суперклетку (рис. 6.2в). В результате объединения множества суперклеток (в фожазите их восемь) в регулярную систему формируется элементарная ячейка цеолита (рис. 6.2г).
Тетраэдры из оксидов кремния и алюминия расположены так, что цеолиты имеют открытые участки структуры. Это и создает систему пор с высокой удельной поверхностью. Химическую формулу первичной структурной единицы — тетраэдров кремния и алюминия — можно представить в виде:
OO Me+
O Si O Al O
OO
Тетраэдры с ионами Si4+ электрически нейтральны, а тетраэдры с ионами трехвалентного алюминия Аl3+ имеют заряд минус единица, который нейтрализуется положительным зарядом катиона Ме+ (сначала катионом Na+, поскольку синтез чаще ведется в щелочной среде, затем в результате катионного обмена — катионами других металлов, катионом NH4 или протоном Н+).
Наличиезаряженныхионовалюминиянаповерхностицеолита(центры Бренстеда) и обусловливает кислотные свойства и, следовательно, его каталитическую активность.
Натриевая форма цеолитов каталитически малоактивна и наименее термостабильна. Оба эти показателя существенно улучшаются при увеличении силикатного модуля цеолитов, а также степени ионного обменана двухвалентныеиособенно натрехвалентные металлы. Среди них более термостабильны цеолиты типа ReY, обладающие к тому же важнымсвойством—высокойкаталитическойактивностью.Благодаря этим достоинствам цеолиты серии ReY как активный компонент катализаторов крекинга получили исключительно широкое применение в мировой нефтепереработке.
Важным этапом в области дальнейшего совершенствования цеолитных катализаторов крекинга явилась разработка (в 1985 г. фирмой
653